
- •ЧАСТЬ 1
- •Список литературы
- •4.3. ПОЛУЧЕНИЕ
- •вр Ed (р — ар) + уарг) + E0NV '
- •Список литературы
- •Список литературы
- •7.2. ОБРАЗЦЫ ДЛЯ ИСПЫТАНИЙ
- •7.4. СДВИГ
- •8.1. Расчетные зависимости для постоянных упругости однонаправленного материала (монослоя)
- •8.2. ТЕРМОУПРУГОСТЬ
- •многослойных композитов
- •ПРИ ПЛОСКОМ НАПРЯЖЕННОМ
- •состоянии
- •8.4. ИЗГИБ МНОГОСЛОЙНЫХ
- •композитов
- •Шсшгьш-
- •[Фасу] = 1.] [ф°] [7\]т; (8.101)
- •Список литературы
- •9.1. КЛАССИФИКАЦИЯ КОМПОЗИТОВ
- •9.2. СТРУКТУРНЫЕ ЭЛЕМЕНТЫ
- •9.5. Приближенные зависимости для расчета упругих характеристик композита с противофазным искривлением волокон
- •9.6. ЧЕТЫРЕХНАПРАВЛЕННЫЕ КОМПОЗИТЫ (4Д)
- •ЧАСТЬ 2
- •1.1. УРАВНЕНИЯ МЕХАНИКИ АНИЗОТРОПНОГО ТЕЛА
- •Список литературы
- •2.1. КОМПОЗИТНЫЕ БАЛКИ
- •2.2. ТОНКОСТЕННЫЕ СТЕРЖНИ
- •2.4. КРУГОВЫЕ КОЛЬЦА
- •Список литературы
- •4.1. СТАТИКА ОБОЛОЧЕК ВРАЩЕНИЯ
- •Му == ^1я8да 4“ &22®у 4~ CiaKx4“ ^ааКу!
- •в.З. АНИЗОТРОПНЫЕ ДИСКИ
- •6.3. Влияние начальных термических напряжений на удельные энергоемкости дисков, образованных намоткой композитов
- •6.4. ХОРДОВЫЕ МАХОВИКИ
- •Список литературы
- •ОСЕСИММЕТРИЧНАЯ ЗАДАЧА
- •8.1. ПРОЕКТИРОВАНИЕ МЕХАНИЧЕСКИХ СОЕДИНЕНИЙ
- •Список литературы
- •« РЕКЛАМА»
- •« РЕКЛАМА»
усилий (особенно сосредоточенных) с одного элемента ца другой [2, 4].
Прочность наиболее распространен ных (клепаных, болтовых, резьбовых) соединений металлических элементов значительно превосходят прочность аналогичных соединений конструкций из композитов. Из-за невысокой проч ности на смятие и срез может быть све ден на снет» весь выигрыш в массе от применения в конструкции компози тов. Если для металлов соотношение характеристик прочности при растя жении ав, смятии асм и срезе тср составляет соответственно 1,0; 1,3;
0 ,7 , |
то |
для композитов |
однонаправ |
ленной |
структуры оно |
равно 1 ,0 : |
|
: 0,4 |
: 0,16. |
|
Малое относительное удлинение ряда композитов (например, для углепла стиков ё = 0 ,5 ~ 1 ,5%) может привести
кместному локальному разрушению композита уже в процессе клепки. Слоистость структуры композитов приводит к перегрузке прилегающих
кклеевым швам слоев и часто вызывает их отрыв или расслоение.
Для полимерных композитов специ
фической проблемой является сохра нение плотности стыка и обеспечение стабильности затяжки болтовых сое динений из-за ползучести и релак сации напряжений в соединении.
Эти и другие особенности следует учитывать при проектировании и вы боре вида соединений и оценке их
прочности.
Конструктивное оформление соеди нений композитных элементов отлича ется большим разнообразием и зави сит как от назначения и предъявляе мых требований, так и от технологиче ских операций, с помощью которых они
выполняются.
Каждое соединение обладает своими особенностями, преимуществами и не достатками и выбор того или иного И8 них при проектировании изделий за висит от ряда факторов — характера и величины нагрузки, размеров дета лей, физико-механических свойств ма териалов, условий эксплуатации, стои мости, технологической реализуемости, а также от специальных требований, например, по герметичности.
Условно факторы, определяющие конструктивно-технологический об
лик проектируемого соединения, мож но объединить в три группы: эксплу атационные, технологические и кон структивные, Взаимосвязь перечислен ных факторов требует комплексного подхода к проблеме проектирования соединений композитов и необходи мости вести этот процесс одновременно с процессом проектирования всей кон струкции.
Любую конструкцию можно рас сматривать как комбинацию листов, балок, стержней, оболочек, труб и других элементов, соединенных вое дино. Комбинируя эти элементы, мож но получить большое количество раз личных по геометрии соединений. Их можно свести к нескольким основ ным видам: стыковым, нахлесточным и угловым. В конструкциях из компо зитов соединительные узлы могут быть образованы с применением как одного из перечисленных видов соеди нений, так и их комбинации.
Элементы, образующие агрегат или изделие, могут быть соединены между собой с помощью клеевой прослойки, механического крепежа (болтов, эаклепок и т. д.), выступов и углублений, имеющихся на поверхностях соеди няемых деталей (например, резьбо вые и клиновые соединения), а также сочетанием названных соединительных элементов (например, клей совместно с болтами, заклепками, резьбой).
Особую группу составляют соеди нения, образуемые непосредственно в в процессе формования композитных изделий. В качестве примера можно привести соединения фланцев, фитин гов, окантовок с такими композитными деталями, как баллоны давления, стержни, трубы.
8.1. ПРОЕКТИРОВАНИЕ МЕХАНИЧЕСКИХ СОЕДИНЕНИЙ
Выбор и обоснование целевой функ ции, с помощью которой возможно оценивать эффективность различных видов соединений, представляют из вестные трудности ввиду многоплано вости задачи.
Используются различные показатели качества: теоретический kT и эффек тивный &еф ноэффициенты концентра-
Рис. 8.1. Формы разрушения механиче- сеих соединений композитных элементов:
а — разрушение по ослабленному сече нию; б — срез—сдвиг композита; в —
смятие композита; г — срез «силовой точ ки»
ции напряжений, коэффициенты проч ности шва фшв» приведенные затраты. Наиболее общую оценку эффективности соединений проводят с помощью экс пертных «балльных» оценок [2]. Их применение, эффективное лишь на самой ранней стадии выбора видов соединений, не позволяет сделать точ ный количественный анализ.
В практической реализации про цедуры выбора вида соединений КМ и определения их оптимальных пара метров наиболее целесообразным яв ляется применение методики, осно ванной на использовании экспери ментально-теоретических подходов.
На первом этапе определяются экс периментально основные константы прочности композитов на смятие осма, среэ тсра и разрыв ова с учетом направ ления действия внешней нагрузки по отношению к осям симметрии упругих характеристик материала.
На втором этапе проводится теоре тический анализ распределения нанагрузок и напряжений в соединении и выполняется процедура выбора оп тимальных параметров соединений, ис ходя из условия равнопрочности (рис. 8 . 1 ). Так как условие равно прочности соединения
Рс ~ Ро. о = ^см == ^ср = Рср. т
(8. 1)
(где Р0. с, Р см, Яср, Яср. т-—нагрузки, разрушающие образец соответственно по ослабленному сечению, в резуль тате смятия, среза и среза силовой
точки) реализуется неоднозначно, то для выбора наилучшего варианта не обходимо задавать целевую функцию и искать ее экспериментальное зна
чение.
Для наиболее распространенных ви дов соединений клеевых, клее-клепа- ных, клепаных, болтовых и штифтобол товых в качестве целевой функции
целесообразно |
принять функцию |
|
шах. |
д-22- Goa + |
Сар. , (l)/Vr)-® |
"с. М |
* |
|
(8.2) |
Здесь ф (W8) — коэффициент прочно
сти s-ro вида |
соединения; ф (В73) = |
|
= Рс/Р кМ (^с |
~ прочность соедине |
|
ния; |
— |
прочность материала); |
Gcs — увеличение массы конструк ций от соединения; СПра = СТ8 + + EHks — приведенные затраты на выполнение всего объема s-вида соеди нения (CTs — технологическая себе стоимость; kg— капитальные затраты на оборудование для выполнения s-
вида соединения; |
= 0,12ч-0,15 — |
нормативный коэффициент эффектив ности капитальных затрат); йС8 — среднее значение коэффициента запаса прочности соединения; йс. м— сред нее значение коэффициента запаса прочности для материала; т| — коэф
фициент, |
учитывающий стоимость |
|
увеличения |
массы |
конструкции на |
|
|
k |
1 кг, руб/кг; Nr =* |
2 GQ8IGC8 — от- |
|
|
|
1 |
носительный годовой объем выполне ния соединений s-вида для всех кон струкций (k — количество конструкций с s-видом соединений); — коэф фициент, учитывающий масштабный фактор при переходе от расчета проч ности образца к прочности всех соеди нений s-ro вида конструкции:
где оп и m — параметры распределе ния Вейбулла, полученные при ис
пытании образцов; аг — предел проч |
на смятие Р см, прочности на срез ком |
||||||||||||||||||||||
ности образца соединения на разрыв; |
позита Рср и прочности на срез сило |
||||||||||||||||||||||
F8 — площадь зоны соединения об |
вой точки |
Р ср. т, |
выраженные |
через |
|||||||||||||||||||
разца; |
Fa — площадь зоны |
соедине |
геометрические |
|
и |
физико-механиче |
|||||||||||||||||
ния всей |
конструкции. |
|
|
|
|
ские |
параметры |
соединения, |
форми |
||||||||||||||
С учетом введенной целевой функ |
руется |
неполная |
система |
уравнений |
|||||||||||||||||||
ции (8 .2 ) и условия равнопрочности |
для |
определения |
методом |
последова |
|||||||||||||||||||
соединения (8 .1 ) на разрыв по ослаб- |
тельных приближений |
оптимальных |
|||||||||||||||||||||
ленному |
сечению |
Р0. с, |
прочности |
параметров |
|
соединений: |
|
|
|
|
|||||||||||||
|
|
|
|
|
___________________4> (ra)F M |
|
|
____________ |
|
|
|||||||||||||
|
|
|
|
|
|
f i ^ T |
600d |
{ Гс <*' + |
+ |
“ V a )- |
- |
f ( Y « |
- |
У) |
X |
|
|
||||||
|
|
|
|
|
|
|
_____________________1_______________________ |
|
|
|
|
||||||||||||
|
|
|
|
|
|
|
|
|
|
1 |
|
|
|
|
|
с |
|
|
1 |
|
|
|
|
|
|
|
|
|
|
X |
(1 + |
<в)] ) Ф + |
0,001d8Vo. т* |
+ |
|
др8Т)- г— |
; |
|
|
|
|||||||
f = |
l + |
i |
|
qcM a U + |
<й) |
|
На |
рис. |
8.2 |
представлены |
резуль |
||||||||||||
|
|
|
|
|
|
|
таты расчета по предлагаемому алго |
||||||||||||||||
|
|
|
|
|
|
|
|
|
|
|
|||||||||||||
|
|
|
|
|
Z |
n r |
|
, |
|
ритму. В зависимости от механических |
|||||||||||||
|
|
|
|
ilE£)a°ва + <5ш i |
|
свойств КМ и крепежных элементов |
|||||||||||||||||
|
|
|
|
|
«а |
|
|
|
|
|
|||||||||||||
|
|
d _ |
4y ( W 8)QBg |
_t_. |
|
|
оптимальные |
параметры |
|
соединений |
|||||||||||||
|
|
|
|
|
ЯТСр. т |
|
* |
|
|
меняются. |
|
|
|
|
|
|
|
|
|
|
|||
|
|
|
|
|
|
|
|
В рассмотренных примера* наиболь |
|||||||||||||||
|
|
|
|
|
|
|
|
|
|
|
|||||||||||||
с — |
^ |
(^д) стваkekj |
t |
, |
п - # |
шей |
эффективностью |
обладают |
за |
||||||||||||||
- ^ с р а О + С О ) * + 0 Л |
клепочные |
и болтозаклепочные соеди |
|||||||||||||||||||||
нения. |
Данная |
|
процедура |
оптимиза |
|||||||||||||||||||
|
|
|
|
|
|
|
kjke |
|
|
|
|||||||||||||
с о = ф ( Г 3); |
|
|
I. |
ции повторялась для различных гео |
|||||||||||||||||||
|
|
|
|
||||||||||||||||||||
В этом случае 7 = |
t/d; d = |
d!d\c = |
метрических и физических параметров |
||||||||||||||||||||
соединений. |
|
|
|
|
|
|
|
|
|
||||||||||||||
= c!d\ |
|
со = |
бу/6 ; 7, d, с, 6 , i — соот |
В диапазоне толщин 1—4 мм ис |
|||||||||||||||||||
ветственно |
геометрические |
парамет |
пользование |
клепаных соединений эф |
|||||||||||||||||||
ры — шаг, диаметр, расстояние до |
фективно, так как оптимальные ре |
||||||||||||||||||||||
кромки, толщина и количество рядов; |
шения находятся в зоне допустимых |
||||||||||||||||||||||
ава> |
Ясма» |
Тсра, |
тср. т— константы |
ограничений. С |
увеличением |
количе |
|||||||||||||||||
прочности в направлениях а соот |
ства |
крепежных |
элементов |
эффектив |
|||||||||||||||||||
ветственно на разрыв, смятие, срез- |
ность |
|
соединений |
резко |
снижается |
||||||||||||||||||
сдвиг КМ и срез силовой точки соот |
вследствие |
роста |
трудоемкости |
изго |
|||||||||||||||||||
ветственно; |
© — степень |
утолщения |
товления и увеличения массы конст |
||||||||||||||||||||
(усиления) краевой зоны; ke, ku ka — |
рукции из-за возрастания толщины и |
||||||||||||||||||||||
коэффициенты, |
учитывающие |
эксцен |
эксцентриситета |
в |
передаче нагрузок |
||||||||||||||||||
триситет приложения нагрузки е, не |
соединений. Оптимальные-геометриче |
||||||||||||||||||||||
равномерность загрузки точек и кон |
ские параметры соединения |
находятся |
|||||||||||||||||||||
центрацию |
напряжений |
около |
от |
на пересечении вертикали, проходящей |
|||||||||||||||||||
верстия; |
уа , |
ус. т — удельная |
плот |
через точку экстремума, и кривых рав |
|||||||||||||||||||
ность соединяемого материала и сило |
нопрочности |
соединений |
для |
соответ |
|||||||||||||||||||
вой точки; ф (JF3) — коэффициент |
ствующего |
вида |
разрушения. |
|
|
||||||||||||||||||
прочности образца. |
|
|
|
|
мето |
Существенно |
|
повысить |
эффектив |
||||||||||||||
Эффективность предлагаемой |
ность соединений при стыке сравни |
||||||||||||||||||||||
дики |
расчета |
оптимальных |
парамет |
тельно |
«толстыXI |
оболочек |
(6 |
^ 8 |
|||||||||||||||
ров соединений и выбора наилучшего |
мм) можно применением штифтоболто |
||||||||||||||||||||||
вида соединений рассмотрим на при |
вых |
|
(ШБС) |
и |
штифтошпилечных |
||||||||||||||||||
мере болтовых и заклепочных соеди |
(ШШС) соединений (рис. 8.3). Оценку |
||||||||||||||||||||||
нений |
|
конструкций |
из |
углепластика. |
эффективности |
и |
выбор |
оптимальных |
fc d |
с w |
<опт ~ 1 |
1о п т = 2 |
|
|
|
Г |
|
|
|
d |
|
|
|
a) |
а) |
5) |
1опт~ 3 |
*опт ~ 2 |
6) г)
Рис. 8.2. Зависимость геометрических параметров соединений из КМ от количества сило вых точек и вида соединения:
а — болтовые; |
б — болтозаклепочные; в — клепаные |
(заклепки не |
материала В-65); |
|||||||
г — клепаные (ааклепки из материала 1Х18Н9Т) |
|
|
|
|
||||||
параметров осуществим с помощью системы уравнений; |
|
|
||||||||
|
|
_____________________ ♦ (р « )^ м |
|
|
||||||
|
|
|
|
{ 2 n R L * y a |
Н |
ni |
(Yin — Yo)} + |
|
||
|
|
|
|
|
|
6- |
|
|
|
|
|
|
|
4 |
n . 2 |
|
2 ) |
|
— Yo) + С пр« (Ч ^ г )- * |
i |
|
|
|
|
|
i = |
l |
|
|
|
|
|
|
Q ,+ |
|
|
|
N , |
Шщap 0 |
— C08<PQ)(n + |
tgyo — Фо) |
||
2X |
|
|
Сф |
- Г - |
Rni |
|
2 tg фо — sin 2 фо |
|||
|
l + - % |
+ |
L m |
|
||||||
do= - |
|
e |
|
|
|
|
|
|||
|
_____ c 6 |
____ ci |
|
|
|
|
|
„ V ° l + 3 *
oBa2nRkt niOcM afce 1
n d % yo l + 3t*
40см^ш
_ |
3 T » + 4 d m6yT c p g |
SfiyTop 0
Здесь Q8 — усилие затяжки штифтов;
0 ,6 Я2 |
|
|
N |
/ |
ля^ 2 \ |
4 |
[ i r ^ y |
— г 5 ) |
С0т — GCM/ACMI CQ — ■
L* = я |
^ 2бУ |
|
6 ( 1 — Vi2V2i ) ’ |
kt = \ + 4МИЗр X
NR
х (1 — COS Уо) (я + tg у0 — ф0)
2 tg Фо — Sin 2ф0 |
’ |
где Сф, сот» CQ — жесткость фланца, отверстия на смятие, болта на растя
жение; L* — краевая зона оболочки; Ет — относительная площадь кон такта фланца (Ет = 0 ,8 ); МИ8Г — из
гибающий |
момент, |
действующий |
на |
фланцевый |
стык; |
Еф, £ lf Е2, |
via, |
v2i, £б — упругие постоянные пакета и болта; Rz — шероховатость поверх ности стыка; ф0 — угол, определяю щий положение нейтральной оси; N — осевая сила; п — количество штифтов в одном ряду; Хр — податливость резь
бы болтов ^ 0 , 8 -g g -- у, /—ко
личество рядов; с — приведенная дли на болтов; GCM— модуль упругости при смятии; Дсм— смешение штифта в от верстии.
На рис. 8.4 представлены резуль таты расчетов однорядных и двухряд ных ШБС, выполненных с предвари тельной затяжкой болтов и без нее.
Для оболочек, работающих на внут реннее давление и изгиб с автономным обеспечением герметичности, наиболее эффективно использование двухряд ного шва: снижение массы составляет 16 кг. В том случае, когда плотность стыка и герметичность обеспечиваются за счет предварительной затяжки бол тов, существенно возрастает масса изделия, так как возрастают абсо лютные нагрузки на болт при некото ром уменьшении амплитуды перемен-
Рис. 8.3. Конструкции Ш1 мфтоболтовых (а) и илифтошпилечных ((f) соединений
кэу Ш3 dl d$ |
с |
dL |
|
|
|||
/0 JT |
* |
' |
|
|
|
|
|
0,6Н |
* |
- в н 6 |
|
|
|||
0,5 |
5 |
- |
5 |
|
V— |
- |
|
0,4 |
- |
4h |
* |
||||
|
|||||||
|
|
|
|||||
0,3\ |
г |
г; |
|
с |
(*б |
||
|
|
|
|||||
|
|
|
I dut |
|
0, 2\ |
1 |
|
0,1 |
||
|
||
|
___ L |
|
|
а) |
Рис. 8.4. |
Зависимости па |
|
раметров |
ШБС |
от количе |
ства стыковых |
болтов: |
а — однорядный шов (за тяжка отсутствует); б — однорядный шов (затяжка
моментом Мкр); в — двух
рядный шов (эатяжка от сутствует)
i)
|
|
|
б) |
|
|
|
|
|
|
|
ных нагрузок. На рис. 8.5 показаны |
вести |
перерасчет |
жесткостных |
пара |
||||||
метров |
материалов по формуле |
|||||||||
области |
эффективного использования |
|||||||||
различных видов соединений в зави |
|
|
|
|
|
|
||||
симости от изменения толщины соеди |
где k — относительный коэффициент |
|||||||||
няемых |
материалов. |
трудоемкости |
||||||||
В целях сокращения |
пересчета; б*, Е± — толщина и модуль |
|||||||||
расчетов |
эффективности |
различных |
упругости углепластика; |
бм, |
Ем — |
|||||
видов соединений |
для |
материалов, |
толщина и модуль упругости исследу |
|||||||
отличающихся по физико-механиче |
емого |
материала. |
Для |
определения |
||||||
ским свойствам от приведенных на |
оптимальных |
параметров |
для |
вновь |
||||||
рис. 8.2, |
8.4, 8.5, |
необходимо произ |
исследуемого |
материала |
необходимо |
к*-тг
|
|
Области |
« | L |
, |
использования |
|
||
Я |
Клепаные |
Клеевые |
ИЛсоединения соединения
|
|
Клепаные |
|
|
|
соединения |
|
|
в т |
болтовые |
|
4 \ |
|
соединения |
|
" |
1^боли\овые |
||
Клепаные' |
|||
соединения |
|
соедьтения1 |
|
г |
1 1^» |
ГЧЬДО |
|
|
|||
1 |
1 1 \ |
|
|
1 |
1 1 |
|
О |
__ 1_ 1 1 |
* 5 |
6 |
7 S,nn |
|
I |
г 3 |
||||
Рис. 8.5. Области эффективного |
исполь |
||||
зования различных |
видов |
соединений: |
|||
1 — клеевые; |
2 —- клепаные; |
S — клеекле |
|||
паные; |
4 — болтовые |
|
|
|
|
найти |
исходную |
точку |
на |
графике |
|
с помощью |
«приведенной» толщины |
материала бпр — бм£ А Для значений бпр определяются показатели эффек
тивности и сравниваются |
различные |
|
виды |
соединений. |
соединяе |
С |
увеличением толщины |
мых материалов всех видов соединений показатели эффективности снижаются. Это объясняется возрастанием коэф фициента ke и увеличением количе ства рядов в соединении. Для рас сматриваемого материала область эф фективного использования клеевых соединений находится в пределах до 1 , 6 мм толщины соединяемых дета
лей. |
клепаных |
соединений эффек |
||
Для |
||||
тивная |
область |
толщин |
1,5—3,0 |
мм |
и для |
болтовых — более |
3 мм. |
Для |
соединений оболочек с толщиной ма териала б ^ 8 мм целесообразно при менять штифтоболтовые или штифто шпилечные соединения. Таким обра зом критерий эффективности соедине ний, дающий возможность оценить изменение прочности соединения на единицу изменения приведенной мас сы стыка, позволяет производить по следовательный итерационный цикл оптимизации конструкторско-техноло гических параметров соединения и выбор вида соединения, обладающего большой эффективностью.
8 .2 . П РО ЕК ТИ РО В А Н И Е К Л Е Е В Ы Х СОЕДИНЕНИЙ
При изготовлении клеевых соединений композитных элементов основными этапами являются выбор силовой схе мы (вида) соединения и определение его конструктивных параметров.
Наиболее распространенным видом клеевого соединения является соеди нение внахлестку (рис. 8 .6 ) (5]. При ложение нагрузки в плоскости скле енных элементов вызывает появление напряжения сдвига в клеевом слое и на поверхности раздела. На напря женно-деформированное состояние, а следовательно, и на несущую способ ность соединения большое влияние оказывают его конструктивные пара метры.
Распределение касательных напря жений %х по длине клеевого шва и
усилий |
в соединяемых элементах |
||||
описывают |
следующие |
выражения: |
|||
|
|
т* ^ |
Nk X |
|
|
|
Гф ch k (х — /) + ( 1 |
— ф) ch k x l . |
|||
Х L |
sh kl |
|
|
||
|
|
N l x ^ N X |
|
||
v f , h a |
— Q + |
( i — Ф)дь**1. |
|||
' ' |
^ |
|
's h kl |
J ’ |
|
|
Nt x ^--N [ l - t | > - |
|
|||
|
ifrchMx — 0 |
+ ( 1 |
—4 >)shfex |
"I |
|
|
|
|
sh kl |
|
J’ |
где |
f t - |
K - F |
( " 5 T + - t ) |
|
(Blt B2— жесткости элементов при рас
тяжении; |
G, |
б —- модуль сдвига и тол |
|
щина клеевой прослойки). |
|||
|
У |
|
____ tв, N |
■ГГ |
|
|
|
|
1 |
|
|
Т |
х |
X |
|
|
|
|
Рис. 8.в. Расчетная схема клеевого нахлесточного соединения
Для элементов одинаковой жесткости (Bi = В2 = В, Ф = 1 /2 ) полученноерешение принимает вид
Nk |
ch k (x — 1/2) |
||
= |
2 |
sh klf2 |
; (8.3) |
|
|||
|
|
N zx---- g— * |
|
- |
|
|
|
1 |
db- |
\ |
* / |
sh kl/2 |
|
||
|
|
|
где k = 1/2G/B6 .
Из равенства (8.3) следует, что ка сательные напряжения по длине клее вого шва распределяются неравно мерно и имеют максимальную вели чину Ттах на концах нахлестки, т. е. при х = 0 и х = /. Из (8.3) имеем
Tmax == —2 |
I , kl |
J . |
~ cth ~ 2" . |
(8.4) |
Величина ттах зависит от параметра kt причем несущая способность соеди нения с увеличением k падает. Входя щее в параметр k отношение G/ 6 ха рактеризует способность клеевой про слойки влючать в работу присоединен ный элемент. Чем выше жесткость клеевой прослойки, тем меньший ее объем оказывается нагруженным, тем выше максимальные напряжения.
Из формулы (8.4) следует, что при увеличении длины нахлестки напряже ние тт ах снижается и, достигнув не которого предела, остается постоян ным. Величину нахлестки, при дости жении которой перестает уменьшаться максимум касательных напряжений, обозначим черев /пр. Поскольку при
I > /пр cth |
« 1 , получим |
Nk ______
:= — = N 1/0/256,
т.е. тШах зависит только от нагрузки
и от упругих характеристик элементов соединений.
Из формул (8.3) можно заключить, что с увеличением длины нахлестки касательные напряжения в ее средней части уменьшаются до нуля. При превышении длины нахлестки ве личины /пр в центре соединения начи
нает развиваться зона, которая не принимает участия в восприятии внеш ней нагрувки. Величину /пр можно определить из условия cth (6 /пр/2 ) » 1 . В результате с учетом б/др/2-3
/пр « 6 1/56/20 .
Неравномерность распределения на пряжений в соединении обычно харак теризуется коэффициентом концентра ции напряжений я, представляющим собой отношение максимального на пряжения в клеевом шве к среднему тср» рассчитанному как частное от деления растягивающей силы на пло щадь шва. Коэффициент концентрации напряжений в нахлесточном соедине нии двух одинаковых элементов.
kl_
2
Анализ напряжений в нахлесточном клеевом соединении элементов различ ной жесткости выявляет еще большую неравномерность распределения ка сательных напряжений в клеевой про слойке. Напряжения сдвига имеют максимумы на концах нахлестки, при чем больший из них расположен со стороны менее жесткого элемента.
При большой длине соединения / ^ ^ /Пр касательные напряжения на концах нахлестки определяются сле дующими приближенными асимптоти ческими зависимостями:
|
|
|
1 f |
В г |
G |
т*=0 = |
NkV = N У |
5 , + 5* |
6 S 2 ’ |
||
|
|
|
|
|
(8.5) |
|
|
= N k(l — у) = |
|
||
- |
,, 1 |
г |
в , |
о ; |
* |
N |
V |
Bl + Bi 65! |
|||
Из равенств |
(8 .6 ) |
видно, |
что уве |
личение жесткости только одного И8 соединяемых элементов уменьшает
прочность соединения.
Напряжения, возникающие в клее вых соединениях при действии внеш них нагрузок, накладываются на на чальные (остаточные) напряжения, по явившиеся в процессе склеивания. Наибольших величин эти остаточные напряжения достигают в случае склей-
вания при повышенных температурах разнородные элементов. Зависимости температурных напряжений в клее вой прослойке и усилий в соединяемых разнородных элементах имеют вид
т |
/ |
вВлВа |
|
|
. |
|
T = V |
6(B l + Bt) t ^ |
~ |
a^ |
e~ * |
||
к г |
|
к г |
5 iZ ? a |
J |
|
|
N I X = |
|
и g ^ |
g ^ t X |
|
||
|
X (<*J --Oj) (l ---в- **), |
(8.6) |
||||
где* = |
У |
\ |
( " В Т + |
- £ - ) ; |
t — перепад температур при охлажде нии после склеивания; В В 2, с^, а2 — соответственно жесткости и тем пературный коэффициент линейного расширения первого и второго соеди няемых элементов. Максимальные ка сательные напряжения возникают на концах нахлестки. Величина тгаах и степень изменяемости т возрастают при увеличении параметра k . Максималь ные остаточные напряжения тем выше, чем тоньше клеевая прослойка, выше ее модуль упругости и меньше раз личие в жесткостях соединяемых ма териалов. Необходимо учитывать так же, что возникающие в соединяемых элементах напряжения могут выз вать изгибание (коробление) соедине ния и тем большее, чем больше разли чие жесткостей элементов. По сравне нию с действительными расчетные оста точные напряжения, как правило, оказываются завышенными, что свя зано с неучетом высокоэластичных и пластических деформаций клеевых прослоек, которые особенно сущест венно проявляются на начальной ста дии охлаждения клеевого соединения. Зависимости (8 .6 ) можно использовать в основном для качественного анализа остаточных напряжений в клеевых соединениях.
Характерной особенностью углового соединения (рис. 8.7) является то, что клеевая прослойка в нем работает на отрыв. В случае, если параметры соединения по длине клеевого слоя не меняются, то, считая основание 2 абсолютно жестким, а клеевую про слойку и элемент 1 —- линейно упру гими и используя уравнение балки
Рис. 8.7. Конструктивная (а) и расчет ная {б) схемы углового соевннения
на упругом основании, можно полу чить следующее выражение для рас пределения нормальных напряжений в клеевой прослойке:
4 г
о = 2 Р у |
£""*** cos ах, |
(8.7) |
где £ к —■ модуль |
упругости |
клея. |
Из равенства (8.7) следует, что мак симальное напряжение реализуется при х = 0 , т. е.
а тах — 2 Р |
3£к |
|
бЕ & |
* |
При увеличении толщины присоеди~ няемого элемента в 1 0 раз максималь ное нормальное напряжение умень шается в 5,7 раз и соответственно увеличивается несущая способность соединения. Влияние жесткости клее вой прослойки (£к/6 ), входящей в выражение (8.7), в соединении рас сматриваемого типа значительно меньше, чем в нахлесточном соедине нии.
Полученные выше результаты соот ветствуют случаю, когда жесткость элемента 2 (см. рис. 8.7) значительно превосходит изгибную жесткость пол ки 1. В случае соединения элементов с соизмеримыми жесткостями распре деление нормальных напряжений в клеевой прослойке и прочность соеди нения существенно зависят от жест кости элемента 2. Уменьшение жест кости основания приводит к значитель ному снижению разрушающей нагруз ки, что связано с изгибом элемента 2 , и появлению дополнительной кон центрации отрывающих напряжений уже на другом конце соединения.
Рассмотренные теоретические зави симости распределения напряжений
в различных соединениях позволяют определить пути создания соединений с уменьшенной концентрацией напря жений. Способы снижения концентра ции напряжений могут быть основаны на изменении жесткости клеевой про слойки или соединяемых элементов по длине соединения, особенно на его на чальных участках. Эффективным спо собом уменьшения концентрации на пряжений в нахлесточном соединении может быть применение комбинации клеев: эластичного (по краям) и более жесткого (в средней части). Такое со четание вызовет появление вторичных максимумов на участках, где изменя ется модуль упругости клеевой про слойки, однако эти пики напряжения не столь велики и опасны, как напря жения, возникающие при склеивании с помощью одного клея. В некоторых случаях выравнивание напряжений в клеевой прослойке может быть осуще ствлено путем изменения ее толщины, например, в нахлесточных соедине ниях, имеющих у кромок утолщенную клеевую прослойку, прочность на сдвиг повышается на 10—15%.
Для снижения концентрации напря жений в нахлесточном соединении широко применяют способы срезания части материала, благодаря чему по вышается деформативность оставшегося приклеиваемого элемента. Последнее обстоятельство приводит к тому, что включение элемента в работу происхо дит более плавно, т. е. снижается кон центрация напряжений.
Считается, что в соединении «на ус» одинаковых элементов концентрация напряжений практически отсутствует (п = 1). При соединении листов, труб, изготовленных из материалов с раз личными упругими свойствами, рас пределение напряжений по длине ско са имеет неравномерный характер. Так, в клеевой прослойке, соединяю щей «на ус» образцы из боропластика и алюминиевого сплава, наиболее на груженной является часть клеевой прослойки у конца скоса более жест кого (борэпоксидного) элемента.
Задавая различные законы изме нения жесткости соединяемых элемен тов, можно получить всевозможные картины распределения касательных напряжений в клеевой прослойке
т. е. добиться положительных резуль татов по снижению неравномерности распределения касательных напряже ний в соединении «на ус» разнородных элементов. Например, применение про точки на более жесткой металлической трубе в соединении ее «на ус» с трубой из стеклопластика привело к повыше нию прочности примерно на 30%. Оптимизацию соединения разнородных элементов все чаще производят с при менением ЭВМ. Рассчитывая с помо щью ЭВМ напряжения в любой точке соединения и варьируя толщиной соеди няемых элементов, можно получить относительно равномерное распреде ление касательных напряжений по всей длине клеевого соединения.
При проектировании врезных нахле сточных соединений необходимо соблю дать требования, вытекающие из анали за соединений: длину ступеней делать переменной, наружные ступени делать длиннее, а внутренние — короче. Это приводит к тому, что максимум касательных напряжений будет на ходиться во внутренней части соеди нения.
В угловых соединениях концентра цию наиболее опасных отрывающих напряжений можно снизить, например, плавным уменьшением толщины при клеиваемой полки по ее длине. Более равномерное распределение напряже ний в клее вследствие уменьшения жесткости склеиваемых кромок уголь ника повышает прочность соединения.
После выбора конфигурации соеди нения на следующем этапе проекти рования следует провести предвари тельное определение размеров с после дующим уточненным анализом на пряженного состояния. Первое пред ставление о размерах соединения мож но получить, исходя из приближенно определенной площади клеевого шва, необходимой для передачи нагрузки F = N/тср или F = N/ocр, где тср = = тв/л1 , оср = ов/п2\ N — расчетное
.усилие; тв, ав — пределы прочности клеевой прослойки при сдвиге и рас тяжении соответственно; nl t n2 — ожи даемые коэффициенты концентрации напряжений.
Полученное таким образом первое приближение может быть улучшено путем последовательных уточнений.
При этом для предварительного ана лиза используются соотношения, при веденные ранее, а окончательный рас чет осуществляется на основе более точных методов. Целесообразно ис пользовать энергетические методы, ме тоды конечных элементов, конечных разностей и сеток, реализуемых на ЭВМ.
8.3. ПРОЕКТИРОВАНИЕ КОМБИНИРОВАННЫХ СОЕДИНЕНИЙ
Комбинированными называются сое динения, образованные одновременно силовыми точками и непрерывным швом. К ним относятся такие соедине ния, как клееболтовые, клеезаклепоч ные, клеерезьбовые и т. п. Применение при сборке элементов одновременно двух методов соединения обусловлено стремлением иметь более прочный в механическом отношении шов, повы сить его ударные и вибрационные ха рактеристики и использовать гермети зирующие свойства клеевых прослоек.
Например, в клепаных самолетных конструкциях клеевая пленка погло щает вибрации, ослабляет действие ударных нагрузок и снижает вероят ность усталостного разрушения. При нагружении комбинированного соеди нения клеевая прослойка воспринимает часть нагрузки, разгружая силовую точку. Такое перераспределение на пряжений уменьшает их концентрацию
уграниц силовой точки, что приводит
кповышению прочности конструкции. В то же время наличие в клеевом шве жестких связей в виде болтов или за клепок устраняет серьезный недоста ток клеевых соединений — низкую работоспособность при неравномер ном отрыве.
Основной задачей при проектирова нии клеемеханических соединений яв ляется определение усилий в силовых точках, напряжений сдвига в клеевом шве и нормальных напряжений в соеди няемыхэлементах. При этом необходимо определить и соотношение нагрузок, воспринимаемых силовыми точками и клеевым швом. Относительно невы сокая прочность клеевых композиций при сдвиге и неравномерность рас
пределения напряжений по длине кле
евых швов приводят к тому, что клеевая прослойка, как правило, вос принимает сравнительно небольшую нагрузку. В связи с этим эффектив ность клеевой прослойки в комбини
рованных соединениях |
возрастает с |
уменьшением толщины |
соединяемых |
элементов. |
необходимо |
При проектировании |
учитывать, что для эффективной ра боты комбинированного соединения деформативность его элементов должна быть примерно одинаковой, однако, как правило, податливость механиче ских (например, клепаных) соедине ний значительно выше, чем клеевых. Для устранения этого недостатка мож но увеличивать количество и жесткость
заклепок |
и |
повышать эластичность |
клеев [1 ]. |
цель применения клеевой |
|
Главная |
||
прослойки |
в |
комбинированных соеди |
нениях заключается в повышении не
столько |
статических, |
сколько динами |
||
ческих |
свойств соединений. |
|||
Особую |
группу |
составляют соеди |
||
нения |
различных |
композитных эле |
||
ментов, |
образуемые |
непосредственно |
||
в процессе |
изготовления последних. |
К этим соединениям относятся заформовка фланцев в различные оболочки
итрубы, фитингов в стержневые труб чатые элементы, соединительных вту лок в лонжероны лопастей вертолетов
ит. п. Перечисленные переходные эле менты (фланцы, фитинги и т. д.), пред назначенные для передачи больших сосредоточенных нагрузок, обычно из готавливаются из металлов и соединя ются с ответными металлическими из делиями традиционными способами.
Проектирование таких соединений заключается в обеспечении совместной работы металлического и композит ного элементов. Обычно объединение композитной и металлической деталей осуществляется за счет выступов и впадин, имеющихся на сопрягаемых поверхностях элементов [4]. Напри мер, конструкция соединения металли ческого фитинга со стержневым труб чатым композитным элементом пока зана на рис. 8 . 8 и представляет собой углубление трапециевидной формы, в котором уложены основные ориенти рованные вдоль оси трубы слои ком позита (ф = 0 ), закрепление которых
|
|
|
|
|
|
|
кой реализуемости данного соединения. |
||||||||||||||
|
|
|
|
|
|
|
Соединения, |
аналогичные |
рассмот |
||||||||||||
|
|
|
|
|
|
|
ренному, применяются и для присты |
||||||||||||||
|
|
|
|
|
|
|
ковки |
законцовок |
к |
тонкостенным |
|||||||||||
|
|
|
|
|
|
|
композитным трубам малого диаметра. |
||||||||||||||
|
|
|
|
|
|
|
Трубы, обычно изготавливаемые на*- |
||||||||||||||
|
|
|
|
|
|
|
моткой тканого или ленточного пре- |
||||||||||||||
|
|
|
|
|
|
|
прега, соединяются |
с металлическими |
|||||||||||||
|
|
|
|
|
|
|
законцовками |
с |
помощью |
|
кольцевых |
||||||||||
|
|
|
|
|
|
|
слоев, материалом которых могут быть |
||||||||||||||
|
|
|
|
|
|
|
пропитанные |
связующие |
нити, |
жгу |
|||||||||||
|
|
|
|
|
|
|
ты или ленты. После отверждения соб |
||||||||||||||
|
|
|
|
|
|
|
ранной таким образом заготовки об |
||||||||||||||
Рис. 8.8. Схема |
соединения |
трубчатого |
разуется |
достаточно прочное соедине |
|||||||||||||||||
композитного стержня (7) с металлической |
ние металлического элемента с трубой. |
||||||||||||||||||||
законцовкой (2) |
|
|
|
|
|
Конструктивные |
параметры |
|
рас |
||||||||||||
осуществлено |
с помощью |
кольцевых |
сматриваемого |
соединения |
зависят от |
||||||||||||||||
слоев, |
уложенных |
в оставшуюся не |
эксплуатационных |
и технологических |
|||||||||||||||||
заполненной |
часть |
углубления. |
Бо |
факторов. На начальном этапе проек |
|||||||||||||||||
ковые |
поверхности |
углубления |
пере |
тирования |
можно |
использовать |
|
сле |
|||||||||||||
дают на композитный элемент растяги |
дующие |
эмпирические |
соотношения: |
||||||||||||||||||
вающие и сжимающие усилия. |
Коль |
глубина |
|
канавки |
Я |
= |
|
( 1 -г-1 ,5) Я, |
|||||||||||||
цевые слои препятствуют перемещению |
ее |
длина |
/ |
= |
|
(5 -- 6 ) А, |
углы |
скоса |
|||||||||||||
основных продольных слоев по фитингу |
Of = |
0 2 |
= |
45°, общая толщина компо |
|||||||||||||||||
и способствуют быстрому их включению |
зита в месте заделки (2—2,5) А. Окон |
||||||||||||||||||||
в работу. |
|
|
что получение |
чательные |
конструктивные |
параметры |
|||||||||||||||
Расчеты показывают, |
соединений |
определяются |
|
после |
их |
||||||||||||||||
достаточно |
жесткого |
|
соединения |
чкгчтеоиментальной |
обработки. |
|
|
||||||||||||||
стального фитинга с трубой из угле |
8,4. |
ВЛИЯНИЕ |
ТЕХНОЛОГИИ |
|
|||||||||||||||||
пластика диаметром 0,15 м и толщи |
|
||||||||||||||||||||
ной 5Х 1 0 “ 8 м обеспечивается следую |
НА |
ПРОЧНОСТЬ |
СОЕДИНЕНИЙ |
||||||||||||||||||
щими |
конструктивными |
параметрами |
Экспериментальные исследования проч |
||||||||||||||||||
(см. рис. 8 .8 ): Н « |
5А, |
|
= ЗО-т-450, |
||||||||||||||||||
|
ности |
механических и |
комбинирован |
||||||||||||||||||
сса = |
50-7-60°; длина |
углубления I |
|||||||||||||||||||
ных |
соединений |
углепластиков |
и |
||||||||||||||||||
определяется |
из условий технологичес |
||||||||||||||||||||
|
|
|
|
|
|
|
|
|
|
|
|
|
|
|
О |
0,1 |
0,2 |
0,3 |
Oft |
«р |
|
- г |
- ..........г |
|
|||
Рис. 8.9. Зависимость |
аффективного |
коэффициента |
устало^оЙ |
про кости |
Д |
||||||||
ния |
РНА. от натяга |
Д |
(п /о — коэффициент |
корреляции, |
рав |
» |
СП-б; |
клепа- |
|||||
„ |
N |
г |
□ |
|
__ _ |
пф т.осТ |
О |
- стеклопластик |
|||||
болтовые соединения: |
— стеклопластик |
Вф 1 |
^ *\Л1пластик ВФТ-2СТ, |
* — стекло- |
|||||||||
ные соединения: А |
- |
углепластик КМУ-1У. □ |
ст^_ стеКлоПЛастИк TCV-8/3-BM78 |
||||||||||
пластик КАСТ-В, |
О |
— стеклопластик |
СК-9А, |
V |
|
|
|
|
|
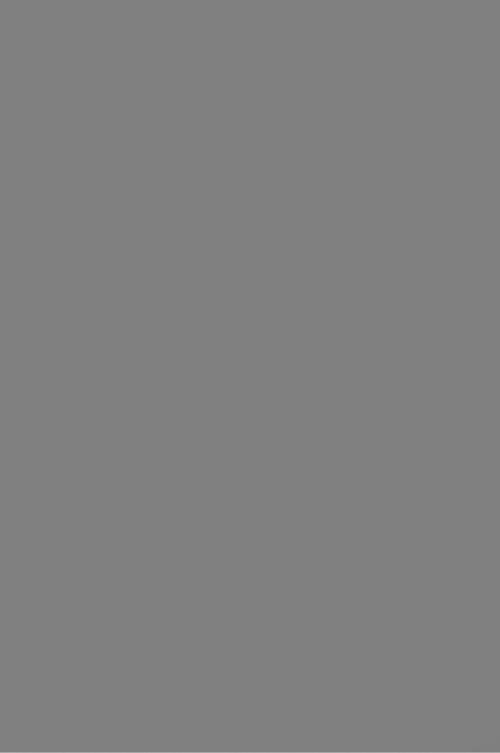
0 0,г 0,4 0,6 0,8 1,0
Ю
Рис. 8.18. Прочность и деформатнвность соединений КМ, усиленных высокопроч ными прослойками:
а — прочность на смятие: 1 — углеродное волокно — ВМН-1+ЭДТ-10; / ' — корд
ная стеклоткань № 156; 2 |
— углеродное |
волокно — ВМН-4+ЭДТ-10; |
2' — ткань |
№ 156, усиленная фольгой; 3 — ВМН-4+ +ЭДТ-10-f-фольга; 4 — ткань ТСУ-8/3-ВМ78+ЭДТ-10-f- боралюминиевая лента; б — влияние ускоренных кли матических испытаний (УКИ) на деформа-
тивность |
соединений |
(углепластик |
||
КМУ-ЗУ + фольга, |
w = |
6%): |
/ - / = |
|
« 20 °С; |
Яр = 18 000 |
Н; |
2 — t |
160 °С; |
Яр * 14 600 Н; 3 - / = 160 ®С; Я =
= 12 100 Н; после УКИ, эквивалентный эксплуатации в 12 лет
Для металлических соединений дол говечность соединений с увеличением натяга растет. Это необходимо прини мать во внимание при проектировании соединений из композитов. Пользуясь обобщенными зависимостями рис. 8.9 и 8 .1 0 , можно определить относитель ное изменение прочности и долговеч ности соединений конструкций из ком позитов, если известны данные по
Рис. 8.14. Влияние длины трещины на остаточную прочность н долговечность пластины из КМУ-1У (с отверстием 0 4 мм и В — 72 мм):
а — статические нагрузки (V = 0,5 м/с);
б — повторно-статические нагрузки (о ==
= 0,9ав)
прочности и долговечности пластин с отверстием и известна величина на тяга болтов или заклепок.
Исследование прочности болтовых соединений при статических и пере менных нагрузках с различной вели чиной предварительной затяжки пока зывает существенное увеличение дол говечности соединений и прочности на смятие. При выборе метода вы полнения соединения композитных конструкций необходимо стремиться сохранять повышенную затяжку бол тов или заклепок и снижать величину натяга. На рис. 8.12 представлены дан ные по изменению долговечности кле паных соединений углепластика мар ки КМУ-1у, полученных разными ме тодами с использованием заклепки из материалов с разной прочностью. Наибольший эффект обеспечивает клепка давлением с раскаткой (кри
вая 3) заклепок из стали |
марки |
1Х18Н9Т с прочностью ов = |
720 МПа. |