
Теория определяющих соотношений. Часть 2. Теория пластичности
.pdf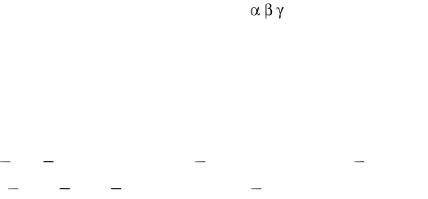
щественно зависят от процессов, предшествующих анализируемому процессу деформирования твердотельного образца, детали или конструкции. Так, свойства сплавов одного химического состава могут существенно отличаться при различных условиях кристаллизации, режимах охлаждения после кристаллизации, возможной термообработки. При этом изменение условий обработки приводит к изменению микроструктуры материала. Именно микроструктура в конечном счете и определяет физико-механические и теплофизические свойства материалов, что еще раз подчеркивает необходимость рассмотрения эволюции микроструктуры при построении определяющих соотношений.
Следует отметить также, что многие кристаллические материалы в зависимости от температуры и напряжений могут существовать в различных кристаллических формах или полиморфных модификациях [46], причем это свойство относится как к «чистым» (однокомпонентным) материалам, так и многокомпонентным. При полиморфных превращениях материалы, не изменяя химического состава, испытывают изменение параметров или даже типа кристаллической решетки; направление процесса перехода определяется термодинамическими условиями устойчивости, записанными обычно в виде условий экстремальности соответствующего (в зависимости от условий сопряжения ТДС с окружающей средой) термодинамического потенциала. Например, при сопряжении ТДС по температуре и термодинамическим параметрам состояния обычно используется свободная энергия Гельмгольца. При отсутствии внешних для ТДС напряжений полиморфные модификации обозначают индексами греческого алфавита , , по мере роста температуры, при которой данная модификация является устойчивой. Для чистых металлов этот переход осуществляется при постоянной температуре, называемой критической (точкой), и сопровождается поглощением (эндотермический) или выделением (экзотермический твердотельный фазовый переход) тепла. Заметим, что это свойство используется при построении фазовых диаграмм (диаграмм состояния), широко используемых в физическом материаловедении, мезо- и микромеханике.
Способность к полиморфным превращениям испытывают такие металлы, как железо (
Feα |
Feβ |
Feγ ), кобальт ( Coα Coβ ), стронций (Srα Srβ ), марганец ( |
Mnα |
Mnβ |
Mnγ Mnδ ), титан ( Tiα Tiβ ) и многие другие, а также неметаллы и хи- |
мические соединения, например, некоторые керамики. В ряде случаев учет полиморфных превращений является необходимым, поскольку служит лидирующим или важным аккомодационным механизмом неупругого деформирования. В литературе для обозначения данного механизма неупругого деформирования и соответствующих моделей материала используется термин «трансформационная пластичность» (или «пластичность превращения»). Особое значение полиморфные превращения имеют при исследовании явления сверхпластичности (трансформационной сверхпластичности), проявляющегося для поликристаллических металлов и керамик и характеризующегося аномально большими для данного материала неупругими деформациями (например, для керамик они могут достигать нескольких десятков процентов).
Процесс полиморфного превращения начинается с образования зародыша новой фазы, как правило, в областях неоднородности – границах зерен и субзерен, характеризующихся высокими концентрациями напряжений. В дальнейшем зародыши новой фазы растут за счет отрыва отдельных атомов или их групп от зерен старой фазы и присоединения к решетке новой фазы; решетка новой фазы имеет вполне определенную ориентацию по отношению к решетке исходной фазы. Заметим, что при фазовом превращении материалы часто испытывают резкое изменение теплофизических и физико-механических свойств (теплоемкости, теплопроводности, удельного объема, модулей упругости и т.д.). При анализе таких процессов необходимо учитывать возникающие внутренние напряжения, способные содействовать или препятствовать процессу превращения.
120
Твердые растворы, химические соединения
Подавляющее большинство конструкционных материалов представляют собой не чистые (однокомпонентные) металлы, а сплавы, состоящие из двух и более компонентов. Добавление даже незначительного количества (от сотых до десятых долей процента) элементов к основному материалу приводит к весьма существенному изменению его макросвойств. Типичными примерами являются стали, основа которых – сплав железа и углерода (конечно, в современных сталях присутствуют и многие другие компоненты). Кроме существенного изменения упругих характеристик, наличие добавочных (к основному металлу) компонентов (примесей, легирующих добавок) приводит к значительному изменению пластических свойств на макроуровне, влияя на механизмы деформирования на мезо- и микроуровнях, о чем более подробно будет говориться ниже. Знание этого влияния представляется необходимым для механиков, специализирующихся в области построения моделей материалов, особенно если речь идет о новых, проектируемых материалах и конструкциях из них.
Всплавах в зависимости от вида физико-химического взаимодействия на атомномолекулярном уровне фазы представляют собой или твердые растворы, или химические соединения. Твердыми растворами называются такие фазы, в которых основной компонент (растворитель) сохраняет свою кристаллическую решетку, а атомы остальных компонент («примеси») располагаются в решетке растворителя, искажая ее параметры. При этом существуют твердые растворы замещения и внедрения. В твердых растворах замещения атомы растворенных компонентов размещаются в узлах кристаллической решетки растворителя («замещают» последние). Известно, что в определенной степени все металлы способны растворяться друг в друге. В некоторых случаях возможно неограниченное растворение одних компонентов в других, тогда сплавы могут образовывать непрерывный ряд твердых растворов. Для этого компоненты должны иметь одинаковый тип кристаллической решетки, различие атомных радиусов не должно превышать 8–15%, компоненты должны принадлежать одной или смежным группам периодической системы элементов (т.е. иметь близкое строение валентной оболочки электронов).
Вобщем случае атомы растворенных компонентов могут хаотически располагаться в узлах решетки растворителя. Однако при определенных режимах термообработки атомы растворенных компонентов могут занять вполне определенные, устойчивые при относительно низких температурах положения в узлах кристаллической решетки растворителя, т.е. образовывать упорядоченные твердые растворы (сверхструктуры). В отличие от химических соединений упорядоченность в сверхструктурах сохраняется только до определенной температуры (точки Курнакова), выше которой фаза превращается в неупорядоченный твердый раствор. Можно рассматривать упорядоченные твердые растворы как промежуточные фазы (между неупорядоченными твердыми растворами и химическими соединениями).
Втвердых растворах внедрения атомы растворенных компонентов размещаются в междоузлиях (пустотах) кристаллической решетки растворителя, стремясь занять наибольшие по объему пустоты. При этом кристаллическая решетка растворителя обычно искажается.
Следует отметить, что атомы растворенных компонент при наличии краевых дислокаций размещаются в растянутых областях под краями экстраплоскостей, создавая при этом достаточно прочные соединения с дислокациями, называемые атмосферами Котрелла. С отрывом дислокаций от атмосфер Котрелла связывают наблюдаемый экспериментально эффект прерывистой пластической деформации (см. гл. 2).
Химические соединения и сходные с ними по свойствам фазы в сплавах отличаются большим разнообразием. Образуемые по законам нормальной валентности химические соеди-
нения компонентов А и В имеют формулу AiBj (i, j – целые числа, не имеющие общего делителя), обладают свойствами и решеткой, отличающимися от свойств и решеток компонентов. Известно большое число соединений металлов друг с другом (интерметаллидов
121
или интерметаллических соединений), связь в таких соединениях обычно металлическая. Широкий класс соединений образуют переходные металлы (Fe, Co, Ni, Ti, Mo и т.д.) с углеродом, азотом, бором и водородом (карбиды, нитриды, бориды и гидриды); обычно они называются фазами внедрения. Из других соединений отметим фазы Лавеса (с формулой AB2, образующихся при отношении атомных радиусов RA:RB = 1.1–1.6; примерами могут служить MgZn2, MgNi2, MgCu2, TiCr2 , TiMn2, TiBe2 и др.) и электронные соединения (имеющие определенные отношения числа валентных электронов к числу атомов; примеры CuZn, Cu3Al, FeAl, Cu5Zn8, CuZn3, Cu3Si и др.). Как видно из приведенной краткой справки, сплавы представляют собой практически неограниченное множество материалов, причем даже несущественное изменение концентрации различных компонентов в сплаве может приводить к весьма заметному различию теплофизических и физико-механических характеристик материала. Иначе говоря, многообразие возможных форм организации материи на микроуровне, атомном и нижележащих уровнях, видов связей микрочастиц в кристаллах, типов кристаллических решеток, различий фазового состава порождает многообразие свойств материала на макроуровне.
Дефекты кристаллического строения [51, 56,
58]
«Богатство внутреннего мира» кристаллических материалов не исчерпывается приведенными выше составляющими, относящимися главным образом к «идеальным» кристаллам (монокристаллам или зернам, субзернам в поликристалле). В первую очередь это связано с механизмами неупругого деформирования моно- и поликристаллических материалов. Анализ процесса пластического деформирования показал недостаточность рассмотрения кристаллических материалов как идеальных кристаллов. К настоящему времени в прямых микроскопических исследованиях обнаружены десятки различных видов дефектов. Обычно используемая в ФТТ и физическом материаловедении классификация основана на «размерности» дефектов, точнее – на характерных размерах несовершенств, искажений идеального строения кристаллов, вносимых теми или иными дефектами. В связи с этим классификационным признаком выделяются нульмерные (точечные), одномерные (линейные), двумерные (планарные) и трехмерные (объемные) дефекты. Каждый из этих типов дефектов может вносить свой вклад в деформирование (или в препятствия деформированию) материала, служить «носителем» того или иного основного или аккомодационного механизма деформирования, образовывать дефектные субструктуры, вступать во взаимодействие с другими типами дефектов. В связи с вышесказанным знания о дефектах, их влиянии на процессы деформирования представляются совершенно необходимыми для механиков - «твердотельщиков».
Точечные дефекты вызывают искажение кристаллической решетки на расстояниях нескольких характерных размеров кристаллической ячейки (по каждому из направлений); напряжения и упругие деформации, вызванные наличием точечного дефекта, убывают пропорционально третьей степени расстояния от дефекта, в силу чего эти поля называют близкодействующими. Наиболее важными и распространенными точечными дефектами являются вакансии (узлы с удаленными атомами) и межузельные атомы. При удалении атома из узла в междоузлие (пору) происходит возникновение пары дефектов, называемой (парным) дефектом Френкеля или френкелевской парой. Часто в литературе дефектами Френкеля называют межузельные атомы, а вакансии – дефектами Шоттки. Заметим, что в ионных кристаллах образование френкелевских пар обусловлено требованием сохранения нейтральности кристалла; образование дефектов Шоттки в связи с указанным требованием должно также происходить парами – за счет удаления пар ионов противоположного знака. Энергия, необходимая для образования точечного дефекта, составляет примерно 1–4 эВ,
122

при этом энергия искажения решетки в окрестности межузельного атома существенно превосходит энергию искажения, вызванного вакансией.
Отметим, что одним из механизмов неупругого деформирования является направленная миграция (диффузия) точечных дефектов; в связи с этим следует заметить, что в силу большей энергии искажения решетки в окрестности межузельного атома его энергия миграции значительно ниже (0.16 0.1 эВ) энергии миграции вакансий (1.0 0.5 эВ) [58]. Однако диффузия атомов однокомпонентных материалов (самодиффузия) реализуется обычно за счет вакансионного механизма, поскольку концентрация вакансий на много порядков (например, для меди при 1000оС – на 35) превышает концентрацию межузельных атомов; при этом огромную роль играет наличие других дефектов кристаллической решетки, о которых говорится ниже, особенно дислокаций и границ зерен. Так, коэффициенты диффузии в присутствии дислокаций (так называемой туннельной диффузии) на 4–5 порядков выше, чем коэффициенты диффузии по вакансионному механизму. Миграция примесных атомов замещения (гетеродиффузия) реализуется с большими скоростями в силу значительной упругой энергии искажений, вносимых примесными атомами. С еще большими скоростями в твердых растворах происходит диффузия примесных атомов внедрения в силу малой энергии перехода из одной поры в другую; при этом чем ниже компактность упаковки кристалла, тем выше коэффициент диффузии; например, в ОЦК кристаллах диффузия происходит с большими скоростями, чем в плотноупакованных ГЦК и ГПУ кристаллах. Следует напомнить, что диффузия является термически активируемым процессом, с ростом температуры скорость диффузии возрастает по экспоненциальному закону.
Из термодинамических оценок следует, что равновесная концентрация вакансий в кристаллах отлична от нулевой; иначе говоря, бездефектных (идеальных) кристаллов в природе не существует. Кроме того, с энергетической точки зрения вакансиям выгодно образовывать бивакансии, тривакансии и т.д., вакансионные кластеры. Большие плоские скопления вакансий (в виде дисков) после их схлопывания приводят к образованию дислокационной петли. Избыточная (неравновесная) концентрация вакансий может быть получена при быстром охлаждении кристаллических тел (закалка, например).
В силу высокой энергии образования межузельных атомов (по сравнению с энергией образования вакансий) их равновесная концентрация близка к нулю даже при температурах, близких к температуре плавления. Как и вакансии, межузельные атомы могут образовывать различные устойчивые конфигурации. Для однокомпонентных кристаллов наиболее известными соединениями являются гантели (вытеснение межузельным атомом атома из узла решетки и образование с ним симметричной пары с центром тяжести в узле) и краудионы (цепочки атомов в направлении плотнейшей упаковки, содержащие один лишний атом на 5–10 межатомных расстояний). Подобно вакансиям межузельные атомы могут образовывать плоские скопления (диски), края которых также представляют собой петли дислокаций. Избыточная (неравновесная) концентрация межузельных атомов создается при облучении кристаллов высокоэнергетическими потоками микрочастиц (электронов, протонов и т.д.).
Кроме указанных механизмов образования точечных дефектов их возникновение происходит в процессах неупругого деформирования и связано с эволюцией других типов дефектов. Например, концентрация вакансий примерно пропорциональна интенсивности пластических деформаций.
Дислокации [51, 56, 58]
К числу важнейших «носителей» механизмов неупругого деформирования моно- и поликристаллов относятся одномерные (линейные) дефекты кристаллической решетки – дислокации; без знания этих дефектов, механизмов их возникновения и взаимодействия с другими дефектами невозможно понимание физической природы пластической деформа-
123
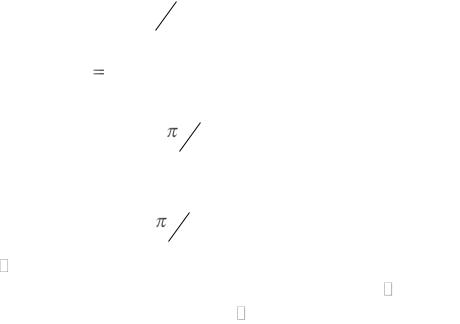
ции и сопровождающих последнюю процессов упрочнения–разупрочнения материалов и других эффектов, наблюдаемых на макроуровне (см. гл. 2).
Существовавшее в начале XX века предположение о сдвиге атомных плоскостей идеального кристалла относительно друг друга как возможном механизме неупругого деформирования столкнулось с огромным расхождением теоретических и экспериментальных данных. Оценки так называемой теоретической прочности были получены различными авторами [56, 58, 76]. Весьма красивый способ определения теоретической прочности на сдвиг был предложен Я.И.Френкелем [56], который рассмотрел сдвиг одной атомной цепочки относительно другой. Пусть d – расстояние между двумя кристаллографическими плоскостями (совпадающими с плоскостью сдвига), а а– расстояние между атомами в направлении сдвига. При малом относительном сдвиге х атомных слоев сдвиговое напряжение определяется законом Гука:
τ = G x |
, |
(3.3) |
d |
|
|
Очевидно, что в силу периодичности расположения атомов в слоях смещение одного слоя относительно другого на величину x a переведет решетку в исходное состояние (при нулевых напряжениях), в силу чего сдвиговые напряжения можно принять в виде синусоиды:
τ = τ sin(2 x |
a |
) , |
(3.4) |
m |
|
|
|
|
|
|
где τm – максимальное сдвиговое напряжение, которое может выдерживать решетка. В предположении малости х/а последнее соотношение можно записать в виде
τ = τ |
|
2 x |
, |
|
(3.5) |
|
m |
a |
|
|
|
|
|
|
|
|
|
Полагая, что a d , и приравнивая правые части (3.3) и (3.5), получаем |
|||||
искомую оценку так называемой теоретической |
прочности: τm |
G/(2π). |
|||
Позднее было получено уточненное значение τm |
G/30. Понятно, что полу- |
ченные оценки являются качественными, позволяющими оценить порядок величины критического напряжения, соответствующего началу пластического деформирования.
Однако эксперименты, проведенные на широком классе отожженных кристаллов различных металлов, показывают, что значения сдвиговых критических напряжений равны (10–6÷10–4)G. Объяснение этому было дано в середине 30-х годов нашего столетия, в первую очередь в практически одновременно опубликованных в 1934 году работах Тейлора, Орована и Поляньи (результаты были получены авторами независимо друг от друга). Отмеченное несоответствие объяснялось цитируемыми авторами и другими исследователями наличием в кристаллах специфических линейных дефектов — дислокаций. В этом случае для осуществления неупругого деформирования нет необходимости одновременно разрушать связи всех соседствующих вдоль плоскости сдвига атомов, достаточно локального разрушения и восстановления таких связей вдоль линии дислокации по эстафетному механизму. Установление такого типа дефектов в качестве основного «носителя» неупругой деформации позволило существенно улучшить соответствие теоретических и экспериментальных данных.
Два основных типа дислокаций – краевые и винтовые. Основной характеристикой дислокации является вектор Бюргерса, определяющий различие замкнутого контура в бездефектном кристалле и замкнутого контура, окружающего линию дислокации (контур Бюргерса).
124
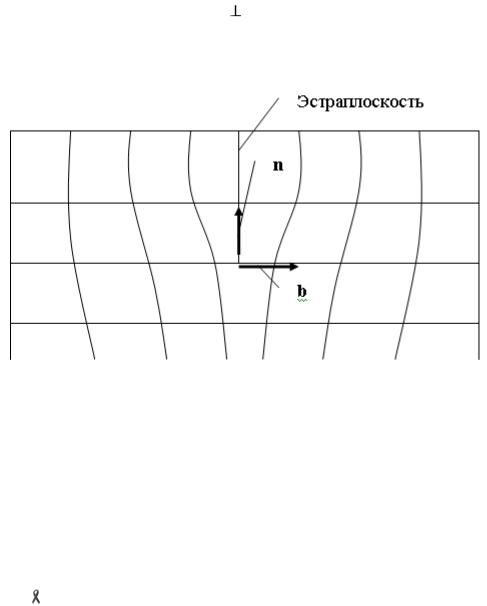
Схематично образование краевой дислокации можно представить следующим образом: в идеальном кристалле делается плоский надрез, в который вставляется лишняя полуплоскость (экстраплоскость), после чего системе дают возможность отрелаксировать (рис.
3.11). После релаксации правильное строение кристалла восстанавливается во всем объеме, за исключением узкой области (с размерами в несколько межатомных расстояний), примыкающей к краю экстраплоскости. Плоскость, перпендикулярная экстраплоскости и определяемая нормалью n, называется плоскостью залегания или плоскостью скольжения краевой дислокации; вектор Бюргерса b краевой дислокации расположен в плоскости залегания и определяет направление возможного движения (скольжения) дислокации. Край экстраплоскости определяет положение линии дислокации, вдоль которой направляется единичный вектор l , так, что тройка является правой тройкой. Плоскость залега-
ния краевой дислокации, таким образом, совпадает с плоскостью (b,l) . В зависимости от расположения экстраплоскости выделяют положительные и отрицательные краевые дислокации, обозначаемые соответственно как и T. Под действием приложенных напряжений краевые дислокации могут скользить в плоскости залегания (в направлении вектора Бюргерса), такое их движение называется консервативным, или двигаться в направлении вектора n (переползать) за счет присоединения к краю экстраплоскости вакансий, такое движение называется неконсервативным.
Рис. 3.11. Схема образования краевой дислокации (линия дислокации перпендикулярна плоскости рисунка)
Винтовую дислокацию схематично вводят обычно следующим образом: в цилиндрическом бездефектном кристалле делается радиальный надрез до оси цилиндра; вдоль пересечения плоскости надреза и боковой поверхности цилиндра края надреза смещаются на одно межатомное расстояние и соединяются, после чего дают системе отрелаксировать. В полученной таким образом конфигурации нарушение правильного строения кристалла сосредоточено в узкой области вблизи оси цилиндра, которая является линией винтовой дислокации и определяется единичным вектором касательной l. Вектор Бюргерса b винтовой дислокации параллелен линии дислокации. В зависимости от направления вектора Бюргерса по соглашению вводятся положительные и отрицательные винтовые дислокации, обозначаемые как g и соответственно.
В реальных кристаллах дислокации в общем случае имеют криволинейную форму, в каждой точке линии дислокации могут присутствовать краевые и винтовые составляющие. Часто дислокации представляют собой замкнутые петли. При этом из ФТТ известны следующие геометрические свойства дис-
125
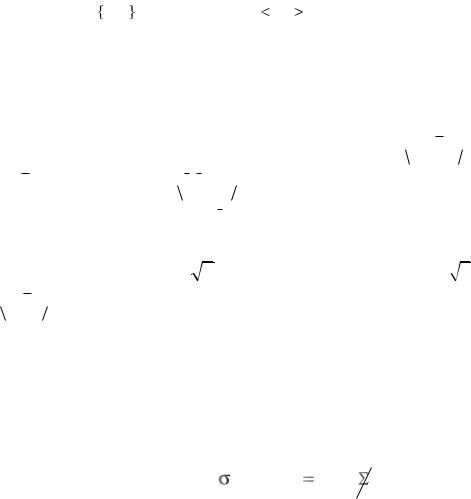
локаций: вектор Бюргерса постоянен в каждой точке данной дислокации; дислокации не могут обрываться в кристалле, они могут либо выходить на поверхность кристалла, либо образовывать замкнутые петли, либо разветвляться; в каждой точке ветвления суммарный вектор Бюргерса исходящих из узла дислокаций равен нулевому вектору.
Несмотря на то, что дислокации не являются равновесными дефектами, в реальных кристаллических материалах всегда присутствует значительное количество дислокаций. Количественной мерой при этом служит плотность дислокаций, определяемая суммарной длиной дислокаций в единице объема. Даже в хорошо отожженных кристаллах плотность дислокаций составляет 105-108 см/см3 (см-2), доходя в деформированных кристаллах до 1012-1014 см-2 (104-106 км в 1 мм3!). Дислокации в кристаллических материалах образуются уже на стадии кристаллизации из расплавов, растворов или газообразной фазы. В процессах термообработки возможными механизмами образования дислокаций (в виде петель) являются диффузионные процессы, приводящие к возникновению дисков вакансий и межузельных атомов.
Отметим, что в кристаллических телах плоскости залегания и ориентация векторов Бюргерса, вдоль которых осуществляется трансляционное движение (скольжение) краевых дислокаций, известны; ими являются наиболее плотно упакованные плоскости и направления. Так, в ГЦК-металлах скольжение краевых дислокаций осуществляется в плоскостях системы 111 по направлениям 110 , соединяющим ближайшие в плоскости плотнейшей упаковки атомы (иначе говоря, в системе скольжения {111}, <110>), итого – 12 систем скольжения (СС). Следует отметить, что при повышенных температурах в некоторых ГЦК кристаллах (например, в алюминии) наблюдается скольжение по трем плоскостям системы {100} по двум направлениям <110>. В ОЦК – решетке трансляционное движение краевых дислокаций осуществляется в плоскостях {110}, {112} или {123} по направлениям <111>, так что полное число СС достигает 48. В ГПУ металлах скольжение
имеет место по базисным плоскостям {0001} в направлении 1 1 2 0
, плоскости
1 1 2 2 по направлению 1 1 2 3
; возможно также скольжение в так называемых
призматических плоскостях 1 0 1 0 . Обозначив через а длину ребра кубической решет-
ки, нетрудно установить, что векторы Бюргерса в ГЦК решетки суть векторы а/2 <110> (модуль вектора Бюргерса a2 ), в ОЦК – а/2 <111> (модуль – a
3
2 ), в ГПУ –
a 1120
(модуль – а; для ГПУ а – длина стороны правильного шестиугольника в базис-
ной плоскости).
Из опытов, активно проводимых с 20-х годов на монокристаллах, известно, что пластическое деформирование осуществляется за счет сдвига одних частей кристалла относительно других при прохождении краевых дислокаций по так называемым активным системам скольжения. При этом было установлено, что условием активации k-й системы скольжения является достижение касательным напряжением в ней некоторого критиче-
ского напряжения τ k |
: |
0 |
|
: n k b k |
τ0k , , |
(3.6) |
|
k |
|
Диада n k b k представляет собой ориентационный тензор k-ой системы скольжения (здесь под b(k) понимается единичный вектор в направлении соответствующего вектора
126
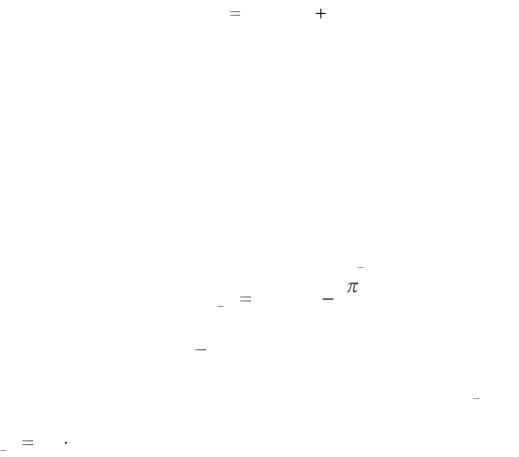
Бюргерса); чаще в литературе в качестве ориентационного тензора M(k) k-й системы используется симметричная часть диадного произведения
|
k |
1 |
|
k k |
k |
|
k |
, |
(3.7) |
M |
|
2 |
n |
b |
b |
n |
|
||
|
|
|
|
Условие (3.7) в литературе обычно называется законом Шмида, устанавливающим момент начала неупругого деформирования при достижении в системе скольжения критического значения касательного напряжения. Для определения начального (без учета деформационного упрочнения) критического напряжения часто используется так называемое (барьерное) напряжение Пайерлса–Набарро, полученное на основе энергетического рассмотрения: в исходном и конечном (после перехода в новое равновесное состояние) атомная решетка с дислокацией имеет минимальную потенциальную энергию. Для перехода требуется преодоление энергетического барьера, зависящего от параметров решетки, типа дислокации и ее вектора Бюргерса. Предполагая зависимость энергии и напряжения сдвига синусоидальной (аналогично модели Я.И.Френкеля, однако период полагается равным вектору Бюргерса), Пайерлс получил следующее выражение для напряжения старта дви-
жения дислокации (напряжение Пайерлса–Набарро τП Н [58]:
τП Н |
2G |
exp( |
2 d |
) , |
(3.8) |
|
|
||||
|
q |
qb |
|
где q = 1 для винтовой и q =1 ν для краевой дислокации, G – модуль упругости, d – расстояние между атомными плоскостями в нормальном по отношению к плоскости
скольжения направлении, ν – коэффициент Пуассона. Напряжение τП Н существенно
зависит от отношения d/b. Например, при отношении d/b=1 τ |
П-Н |
=2.5 10-4G, при d/b=1.5 |
||
|
|
|
|
|
τ |
П Н |
2.1 10-6G. В силу этого плоскостями легкого скольжения являются плотноупако- |
||
|
|
|
|
ванные кристаллографические плоскости, расстояние между которыми является наибольшим. Из (3.8) следует, что при прочих равных условиях τП-Н для винтовых дислокаций
существенно выше (более чем на порядок) стартового напряжения для краевых дислокаций. Следует особо подчеркнуть, что формулы типа (3.8) имеют скорее качественный, чем количественный характер, они правильно отражают основные черты физики процесса, но малопригодны для практических расчетов, производимых механиками. В то же время такого рода соотношения весьма полезны и для механиков, поскольку позволяют установить характер зависимостей, общий вид соотношений, которые затем могут быть скорректированы за счет введения дополнительных параметров, значения коих устанавливаются в соответствующих макроэкспериментах.
При реализации (3.6) в одной системе скольжения говорят об одиночно скольжении. Если кристалл подвергается нагружению, при котором дислокации н чинают скользить в двух или более системах, то говорят о двойном или множестве ном скольжении.
Рассмотрим монокристалл, ориентированный на одиночное скольжение краевых дислокаций в направлении оси x1 в плоскости x1Ox3 (единичная нормаль n ориентирована вдоль оси Ox2). Размеры кристалла вдоль осей x1, x2 и x3 обозначим соответственно через a1, a2 и a3. Тогда прохождение одиночной дислокации с вектором Бюргерса b приводит к сдвигу одной части кристалла относительно другой (в направлении оси х1), величина которого может быть приближенно (в среднем) оценена сдвиговой деформацией
127
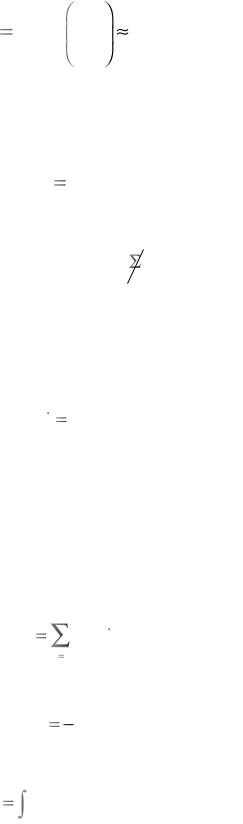
γ arctg |
b |
|
b |
||
|
|
|
|
. |
|
a |
a |
||||
|
2 |
|
2 |
|
|
Если дислокация «прошла» лишь некоторую часть |
a1 кристалла вдоль оси x1, то можно |
принять, что сдвиг составляет часть a1/a1 от введенного выше. Тогда, вводя среднюю длину свободного пробега дислокаций λ и полагая, что подвижными являются n дислокаций данной системы скольжения, определяем величину сдвига следующим соотношением:
γ bρλ , |
(3.9) |
где ρ – плотность подвижных дислокаций (в данном случае ρ=na3/(a1a2a3) = n/(a1a2)). Соотношение (3.9) может быть записано для любой k-ой системы скольжения как
γ(k) = b(k)ρ(k)λ(k) , |
. |
(3.10) |
|
k |
|
Как уже отмечено выше, плотность дислокаций в металлах меняется в широких пределах
– от 105–108 см–2 в отожженных кристаллах до 1012–1014 см–2 в сильно деформированных. Существуют специальные способы термообработки, позволяющие снизить плотность дислокаций до 103 см –2.
Принимая плотность дислокаций постоянной и дифференцируя соотношение (3.9), можно для каждой системы скольжения получить выражение для скорости сдвига
γ bρv , |
(3.11) |
где v – средняя скорость движения дислокаций. Следует заметить, что более корректным представляется использование в качестве исходного именно соотношение (3.11), где ρ – плотность подвижных дислокаций в текущий момент деформирования. В этом случае нет необходимости в гипотезе о неизменности плотности подвижных дислокаций. Кроме того, при таком ходе рассуждений точно выполняется аддитивность скоростей сдвигов по различным системам скольжения, принятая ниже. Суммируя скорости сдвига по всем системам скольжения рассматриваемого кристалла, для монокристалла, деформируемого только путем скольжения краевых дислокаций, девиатор тензора деформаций скорости можно определить следующим образом
|
N |
|
d p |
M k γ k . |
(3.12) |
k1
Вобщем случае скольжения и переползания краевых и движения винтовых дислокаций выражения для девиатора деформаций скорости имеет вид
dp Є : N , |
(3.13) |
где Є – тензор (третьего ранга) Леви–Чивиты, N – тензор третьего ранга, определяемый соотношением
N f v l b d l d b . |
(3.14) |
В последнем соотношении f(b, l, r) – функция распределения дислокаций в точке r по параметрам b и l, где l – единичный вектор, направленный вдоль линии дислокации (для винтовой дислокации совпадает с направлением вектора Бюргерса; для краевой дислокации векторы l, b, n составляют правую тройку).
Выше уже отмечалось, что, несмотря на высокую энергию образования дислокаций, в реальных кристаллах в состоянии поставки («недеформированных») всегда наличеству-
128

ют дислокации с плотностью 103–108 см-2. Однако наиболее важными являются источники дислокаций, инициируемые деформацией кристалла (точнее – источники размножения дислокаций). К числу наиболее эффективных из них относятся источники Франка-Рида (закрепление сегментов дислокаций на сильных препятствиях (например, жестких включениях вторичных фаз или достаточно прочных барьерах дислокационной природы) и испускание закрепленным сегментом под действием приложенных напряжений дислокационных петель) и двойное поперечное скольжение винтовых дислокаций (изменение плоскости скольжения винтовой дислокации с последующим переходом в плоскость скольжения, параллельную исходной; механизм подобен механизму Франка-Рида, однако закрепление сегмента дислокации в новой плоскости скольжения осуществляется за счет неподвижных участков дислокации краевой или смешанной ориентации, расположенных в плоскости поперечного скольжения).
Дислокационные реакции
Таким образом, основным механизмом пластического деформирования является движение дислокаций. Казалось бы, при достижении критических напряжений в образце (по крайней мере, монокристаллическом) дальнейшее пластическое деформирование должно продолжаться до каких угодно деформаций при сохраняющейся нагрузке. Однако для большинства металлов и сплавов даже в опытах на монокристаллических образцах обнаруживается, что для продолжающейся пластической деформации требуется увеличивать прикладываемую к образцу нагрузку; иначе говоря, материалы упрочняются в процессе пластического деформирования. В чем причина такого поведения материалов? Оказывается, что «ответственность» за возникновение различных эффектов упрочнения (и многих других эффектов, отмеченных в гл.2) несут различные механизмы взаимодействия дислокаций с другими дефектами – точечными, линейными, поверхностными и объемными. Другими словами, движущиеся дислокации, встречая на своем пути другие дефекты, вступают с ними в реакции, во взаимодействие. В связи с этим понимание указанных процессов является весьма важным для построения ОС, особенно – для развитых пластических деформаций.
Выше рассматривались так называемые полные (или единичные, или совершенные) дислокации с вектором Бюргерса, равным одному из трансляционных векторов решетки, перенос на который (или n-кратный перенос) делает конечное состояние решетки неотличимым от исходного. Однако в типичных металлических кристаллах имеются дислокации с отличными от трансляционных векторами Бюргерса, которые называются частичными дислокациями. Такие частичные дислокации могут взаимодействовать друг с другом с образованием полных дислокаций; напротив, полные дислокации могут диссоциировать на несколько частичных, т.е. частичные дислокации сами могут рассматриваться как продукт реакции дислокаций. Рассмотрим более подробно частичные дислокации на примере ГЦК-кристаллов. В ГЦК решетке имеет место следующее расположение атомов (рис.3.12): первый слой составляют плотноупакованные «шары», позиция которых в проекции на плоскость плотнейшей упаковки (111) обозначена буквой А. Положение центров «шаров» второго слоя в проекции на ту же плоскость обозначены буквой В, третьего – как С, далее соблюдается периодичность (АВС...).
Такое расположение плотноупакованных слоев ГЦК-решетки обозначают как упаковку АВСАВСАВС…. Заметим, что для ГПУ-решетки имеет место периодичность АСАСАС…
.
Предположим, что в кристаллической решетке имеется (полная) краевая дислокация, экстраплоскость которой перпендикулярна плоскости рисунка, ее край совпадает со слоем
В, вектор Бюргерса b ( a2[101] ) перпендикулярен экстраплоскости и расположен в плос-
129