
Сопротивление материалов конспект лекций
..pdf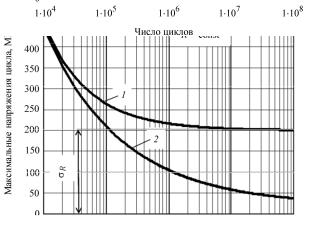
Испытывается серия одинаковых образцов в количестве не менее 10 шт. Первый образец устанавливается на достаточно большом уровне напряжений σ′, и фиксируется число циклов до разрушения (долговечность) N1. Для следующих образцов уровни напряжений последовательно снижаются и определяется их долговечность. В результате испытаний серии образцов получают уровни максимальных напряжений цикла σmax и соответствующие им значения долговечности N.
Результаты испытаний наносят на график, откладывая по оси абсцисс значения долговечности, а по оси ординат – максимальные напряжения цикла. Значения долговечности в одной серии испытаний могут отличаться в сотни и тысячи раз, поэтому по оси абсцисс обычно используют логарифмическую шкалу, а по оси ординат – как логарифмическую, так и равномерную.
График зависимости «долговечность – максимальное напряжение цикла» при фиксированном коэффициенте асимметрии цикла носит название кривой усталости, которая по существу и является характеристикой сопротивления усталости. На рис. 13.5 показаны два типичных вида кривых усталости.
Рис. 13.5
121
Для кривых вида 1 характерным является наличие горизонтальной асимптоты, т.е. наибольшего максимального напряжения цикла, при котором разрушение не наступает за сколь угодно большое число циклов. Такое максимальное напряжение цикла носит название физического предела выносливости и обозначается σR, где индекс R равен коэффициенту асимметрии, при котором проводились испытания (σ–1, σ0, σ0,1 и т.д.). Такими кривыми характеризуются в основном малоуглеродистые стали. Число циклов нагружения, по достижении которого дальнейшие испытания прекращаются, носит название базы испытаний N0. ГОСТом рекомендуется принимать N0 = 107 циклов.
Кривые типа 2 характерны для цветных металлов и сплавов и некоторых легированных сталей. В этом случае определяется так называемый условный предел выносливости, т.е. такое наибольшее максимальное напряжение цикла, при котором разрушение наступает за базу испытаний. При этом база испытаний увеличивается до 108 циклов и более. Условные пределы выносливости обозначаются так же, как и физические, но при этом указывается база испытаний.
Пределы выносливости являются основными механическими характеристиками сопротивления усталости. Результаты усталостных испытаний очень чувствительны к конструктивным, технологическим и внешним факторам. Принято определять пределы выносливости на гладких полированных образцах диаметром 8–12 мм при комнатной температуре в сухой воздушной среде. Чаще всего проводят испытания при R = –1, т.е. определяют σ–1.
13.4. Диаграмма предельных амплитуд и ее схематизация
Опыт показывает, что сопротивление усталости, в частности предел выносливости, сильно зависит от характеристики цикла. Существует несколько методов экспериментального изучения этой зависимости. Один из этих методов заключается в следующем. Испытываются несколько серий образцов при различных значениях среднего напряжения цикла. Для каждой серии путем последовательного изменения амплитуды от образца к образцу определяют максималь-
122

ную амплитуду цикла, при которой не наступает разрушение за базу испытаний. Такая амплитуда называется предельной. График зависимости предельной амплитуды от среднего напряжения цикла носит название диаграммы предельных амплитуд. На рис. 13.6 схематически показана такая диаграмма (кривая 1).
Рис. 13.6
Для большинства материалов с увеличением среднего напряжения цикла в области растяжения предельная амплитуда уменьшается и с приближением его к значению временного сопротивления стремится к нулю. В области сжимающих средних напряжений цикла с увеличением этих напряжений по модулю вначале наблюдается повышение предельной амплитуды цикла, а затем ее снижение. Таким образом, сжимающие статические напряжения в широком диапазоне их значений оказывают благоприятное влияние на сопротивление усталости. Это явление широко используется в технике для повышения прочности деталей машин и элементов конструкций.
Часто диаграмма предельных амплитуд дополняется линией, отражающей условие появления пластических деформаций (линия 3). Уравнение этой линии имеет вид
σa + σm = σт
123
ипредставляет собой прямую, наклоненную под углом 45° к оси абсцисс и пересекающую эту ось в точке с координатой, равной пределу текучести материала. Для того чтобы максимальное напряжение в образце не превышало и предел выносливости, и предел текучести, рабочая точка D на диаграмме, координаты которой равны среднему напряжению цикла и его амплитуде соответственно, должна лежать ниже как линии 1, так и линии 3.
Экспериментальное определение достаточного числа точек для построения диаграммы предельных амплитуд является весьма трудоемким и дорогостоящим мероприятием и проводится в крайне редких случаях. Обычно ограничиваются схематизацией этой диаграммы с помощью прямой, проходящей через экспериментально определенные точки при симметричном и отнулевом циклах нагружения (точки А и В). Координаты этих точек соответственно равны (0, σ–1)
и(σ0/2, σ0/2), где σ–1 и σ0 – пределы выносливости при R = –1 и R = 0. Уравнение этой прямой можно записать в виде
σа.пр = σ–1 – ψσσm,
где ψσ – коэффициент чувствительности материала к асимметрии
цикла, ψσ = 2σ−1 −σ0 .
σ0
13.5. Влияние различных факторов на сопротивление усталости
Опыт показывает, что характеристики сопротивления усталости оказываются очень чувствительными к многообразным конструкционным, технологическим и эксплутационным факторам. Из-за большой трудоемкости усталостных испытаний экспериментальные исследования влияния этих факторов проведены в основном при симметричных циклах нагружения. Рассмотрим влияние важнейших из них.
124
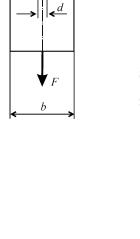
Конструкционные факторы
Детали машин обычно имеют достаточно сложную форму из-за наличия различных конструкционных элементов: галтельных пере-
ходов, шпоночных канавок, выточек, шли- |
|
цов, отверстий и т.п. Теоретически и экспе- |
|
риментально установлено, что в местах рез- |
|
кого изменения размеров и формы детали |
|
происходит локальное повышение напряже- |
|
ний, при этом напряженное состояние стано- |
|
вится, как правило, более сложным. Это яв- |
|
ление называется концентрацией напряже- |
|
ний, а геометрический фактор, вызывающий |
|
это повышение, – концентратором. Влияние |
|
концентраторов на напряженное состояние |
|
весьма значительно. На рис. 13.7 в качест- |
|
ве примера показано распределение нор- |
|
мальных напряжений в пластине с круглым |
|
отверстием, растягиваемой осевой нагруз- |
Рис. 13.7 |
кой F. |
|
Для характеристики влияния концентратора напряжений вводится понятие теоретического коэффициента концентрации напряжений ασ (ατ):
α |
σ |
= |
σmax , |
|
|
|
σн |
|
где σmax – максимальное напряжение в зоне концентратора; σн – номинальное напряжение, рассчитанное по формулам сопротивления материалов.
|
В случае |
пластины с отверстием, показанной на рис. 13.7, |
||
σн = |
|
F |
где h – толщина пластины. |
|
|
|
, |
||
|
(b −d)h |
|||
|
Теоретический коэффициент концентрации напряжений позво- |
ляет вычислять максимальные напряжения через номинальные на-
125
пряжения, этот коэффициент определяется теоретически или экспериментально. Данные о нем приводятся в справочной литературе. В рассматриваемом примере с увеличением ширины пластины по сравнению с диаметром отверстия теоретический коэффициент концентрации напряжений ασ стремится к 3.
Теоретический коэффициент концентрации напряжений зависит от формы детали и вида нагружения и не зависит от свойств материала.
Поскольку процесс зарождения трещин усталости носит локальный характер, концентраторы напряжений оказывают наиболее сильное влияние на снижение сопротивления усталостному разрушению.
Опыт показывает, что влияние концентраторов напряжений на сопротивление усталости для разных материалов различно. Для учета этого влияния вводится понятие эффективного коэффициента концентрации напряжений. Он определяется как отношение предела выносливости гладкого лабораторного образца σ–1 (τ–1) к пределу выносливости такого же образца, но с концентратором напряжений σ–1k (τ–1k) и обозначается через Kσ (Kτ):
K |
σ |
= |
σ−1 |
, K |
τ |
= |
τ−1 |
. |
|
|
|||||||
|
|
σ−1k |
|
τ−1k |
Эффективный коэффициент концентрации напряжений зависит от свойств материала и определяется экспериментально. Данные о нем для некоторых материалов, типов концентраторов и видов нагружения можно найти в справочной литературе.
В случае отсутствия таких данных его можно оценить по формулам
Kσ = 1 + q(ασ – 1), Kτ = 1 + q(ατ – 1),
где q – коэффициент чувствительности материала к концентрации напряжений.
126
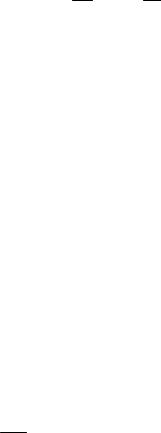
Так, например, для конструкционных сталей q = 0,5…0,7, для закаленных легированных сталей q = 0,7…0,8, а для серого чугуна q = 0. Последний результат объясняется тем, что чугун является высокодефектным материалом, и присущие ему внутренние концентраторы напряжений являются более эффективными, чем внешние.
Зная эффективный коэффициент концентрации напряжений, можно оценить предел выносливости образца с концентратором по формулам
σ−1k = σK−1 , τ−1k = τK−1 .
στ
Качество поверхности
Как уже отмечалось, усталостное разрушение почти всегда начинается с поверхности, точнее, в приповерхностном слое. В связи с этим становится понятным существенное влияние состояния этого слоя на сопротивление усталости. При изготовлении детали именно приповерхностный слой подвержен различного рода воздействиям, могущим существенно изменить свойства этого слоя как в лучшую, так и в худшую сторону.
Одним из основных факторов, влияющих на свойства слоя, является геометрический фактор. Чем выше шероховатость поверхности, тем эффективнее микроконцентраторы напряжений, представляющие собой чередование выступов и впадин профиля поверхности, и соответственно, ниже предел выносливости. Кроме того, на предел выносливости оказывают влияние другие факторы, такие как наклеп, наведение в процессе обработки остаточных напряжений, обезуглероживание приповерхностного слоя или насыщение его ка- кими-либо элементами и т.д.
Влияние геометрического фактора при расчетах на усталость учитывается коэффициентом влияния шероховатости поверхности
KFσ = σ−1F , KFτ = τ−1F , равным отношению пределов выносливости
σ−1 τ−1
127
образцов с данным качеством поверхности к пределу выносливости гладкого полированного образца. Значения этих коэффициентов лежат в следующих пределах: для шлифованных образцов 0,8–0,9, тонкого точения 0,7–0,9, грубого точения, фрезерования – 0,6–0,7. Меньшие значения относятся к материалам высокой прочности. Чем материал более прочный, тем более высокие требования предъявляются к качеству обработки поверхности детали для реализации его резерва прочности.
Влияние различного вида упрочнений поверхностного слоя учитывается коэффициентом влияния поверхностного упрочнения Kv ,
равным отношению пределов выносливости упрочненной и неупрочненной детали. В зависимости от примененного технологического процесса упрочнения этот коэффициент может достигать нескольких единиц.
Размеры детали
Опыты показывают, что с увеличением размеров деталей их предел выносливости уменьшается. Такой характер влияния размеров на характеристики сопротивления усталости носит название масштабного эффекта. Масштабный эффект объясняется статистической теорией и связан с тем, что при прочих равных условиях зарождение усталостной трещины начинается, в первую очередь, в наименее прочных объемах материала (гипотеза слабого звена), а с увеличением объема детали повышается вероятность попадания ослабленных объемов материала в наиболее нагруженные области.
При расчетах на прочность масштабный эффект учитывается масштабным коэффициентом Kdσ, Kdτ, равным отношению предела выносливости образца, размер которого соответствует размеру рассчитываемой детали, к пределу выносливости стандартного лабораторного образца. На рис. 13.8 показана типичная зависимость масштабного коэффициента от диаметра круглого вала из углеродистой конструкционной стали средней прочности.
128
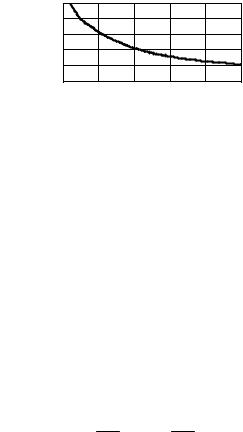
K (d) 1,0 |
|
|
|
|
|
|
d |
0,9 |
|
|
|
|
|
|
|
|
|
|
|
|
|
0,8 |
|
|
|
|
|
|
0,7 |
|
|
|
|
|
|
0,6 |
|
|
|
|
|
|
0,5 |
|
|
|
|
|
|
0 |
40 |
80 |
120 |
160 |
200 |
|
|
|
|
d, мм |
|
|
|
|
|
Рис. 13.8 |
|
|
Масштабный эффект наиболее заметен для деталей малого размера. С увеличением диаметра масштабный эффект затухает, и после достижения диаметром размера 100–150 мм дальнейшее его проявление почти полностью прекращается.
13.6. Определение предела выносливости детали
На практике характеристики сопротивления усталости ответственных деталей определяют экспериментально путем стендовых испытаний деталей или их моделей в условиях, максимально приближенных к условиям эксплуатации.
Приближенная оценка предела выносливости проводится по данным испытаний стандартных гладких лабораторных образцов с учетом влияния на него основных факторов по формулам:
σ−1д = σ−1 , τ−1д = τ−1 ,
Kкσ Kкτ
где σ–1д и τ–1д – пределы выносливости детали; Kkσ и Kkτ – коэффициенты снижения пределов выносливости детали.
В свою очередь, коэффициенты снижения пределов выносливости определяются из выражений:
Kkσ = |
|
Kσ |
+ |
|
1 |
|
−1 |
1 |
|
, |
||
|
|
|
KFσ |
|
|
|||||||
Kdσ |
Kv |
|||||||||||
Kkτ = |
Kτ |
+ |
|
1 |
|
−1 |
1 |
. |
||||
|
|
KFτ |
|
|||||||||
Kdτ |
Kv |
|||||||||||
|
|
|
|
|
|
|
|
129 |
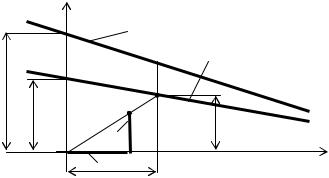
Значения коэффициентов, входящих в эти выражения, для типичных конструктивных элементов и технологических методов обработки, приводятся в справочной литературе.
13.7.Диаграмма предельных амплитуд для детали
Впринципе, диаграмма предельных амплитуд для детали, также как для лабораторных образцов, может быть построена экспериментально. Однако из-за большой трудоемкости усталостных испытаний, как правило, ограничиваются теоретическим построением этой диаграммы, при этом принимается гипотеза о том, что коэффициенты влияния различных факторов, определенные при симметричном цикле нагружения, сохраняют свои значения по отношению к предельным амплитудам. Иными словами, коэффициенты снижения
предельных амплитуд не зависят от среднего напряжения цикла
иравны коэффициенту снижения предела выносливости при симметричном цикле нагружения.
Обратимся к рис. 13.9. Линия 1 представляет собой схематизированную диаграмму предельных амплитуд лабораторных образцов
иописывается уравнением
σ–1
σ–1д
σа.пр = σ–1 – ψσσm.
σа
|
1 |
|
|
|
2 |
|
|
D1 |
|
D |
n |
|
|
|
|
σа.д |
a.д |
|
σ |
|
О |
σm.дσm.дn |
σm |
Рис. 13.9
130