
Сборник 70 студ конференции БГТУ
.pdf81
Обработка металлических изделий гальваническим методом является одним из наиболее распространенных и востребованных способов нанесения покрытий. С его помощью наносятся защитные или декоративные покрытия. Преимуществами гальванического метода нанесения покрытий являются простота, экономичность процесса, стойкость и долговечность покрытий.
Внастоящее время в промышленности используется несколько основных типов гальванического оборудования, каждый из которых выполняет свой спектр задач. К ним относят:
1. Гальванические ванны;
2. Гальванические линии;
3. Барабаны или роторные установки;
4. Дополнительное оборудование.
Гальванические линии – это промышленные установки, которые объединяют серию ванн и дополнительно оснащены манипуляторами или конвейерными установками для подачи заготовок. Преимущества использования гальванических линий заключается в том, что они обеспечивают автоматизацию процесса и высокую производительность. Гальванические ванны – это установки, предназначенные для нанесения покрытий методом погружения заготовок в емкость с рабочим раствором с дальнейшей гальванической обработкой.
Рассматриваемая линия предназначена для гальванического нанесения полного и локального покрытия на штыри электрических соединителей методом контролируемого погружения в электролит в ленте-заготовке. Лента-заготовка, сматываясь с бобины передающего механизма в процессе покрытия деталей, проходит последовательно через ванны, в которых циркулируют рабочие растворы. При этом выполняются технологические операции, такие как обезжиривание, никелирование, серебрение, травление и другие.
Потребность в значительном росте производства, повышении качества продукции, сокращении энергетических и трудовых ресурсов при производстве продукции диктует необходимость в увеличении объемов тех производств, которые обеспечивают надежную защиту изделий от коррозии, снижение их металлоемкости, улучшение товарного вида.
Врешении этих вопросов существенная роль отводиться гальванотехнике. Автоматизация и механизация процессов нанесения гальванических покрытий позволяют не только повысить производительность труда и улучшить качество покрытий, но и устранить малоэффективный ручной труд, особенно в тяжелых и вредных для человека производственных условиях. Состав и конструкция оборудования зависит от характера технологического процесса, числа видов покрытий, номенклатуры обрабатываемых изделий и ряда специальных требований.
На данный момент устройство гальванической линии локального покрытия представляет собой: основания, на которых установлены каркасы, ванны, в которых производятся технологические операции покрытия деталей, сушильное устройство. Через ванны и сушильное устройство проходит в
82
вертикальном положении лента-заготовка с деталями. Лента подвешена за перфорацию на зубчатых роликах опор. Для прохода ленты-заготовки в торцевых стенках ванн имеются вертикальные щели. В начале линии расположен передающий механизм, с бобины которого лента-заготовка подается в линию. Передающий механизм имеет:
1.Устройство для смотки ленты-заготовки с фрикционным подтормаживанием.
2.Устройство для намотки ленты-прокладки с фрикционной муфтой и регулированием скорости намотки путем изменения числа оборотов двигателя постоянного тока.
В конце линии находится приемный механизм, на бобину которого наматывается лента-заготовка с покрытыми деталями. Приемный механизм имеет:
1.Тянущий механизм с регулируемой скоростью протяжки и намотки на бобину ленты-заготовки путем изменения числа оборотов двигателя постоянного тока.
2.Устройство для смотки ленты-прокладки с фрикционным подтормаживанием.
3.Устройство для счета прошедших линию деталей.
Была разработана структурная схема автоматизированной системы управления величиной погружения ленты-заготовки в электролит, содержащая следующие основные элементы:
-ОВЕН ПЛК 110-60;
-Драйвер управления ШД А4988;
-Контроллер управления SMSD-1,5;
-Датчик положения ленты ИО-102-15;
-Фотоэлектрический датчик уровня жидкости CSS-04A;
-Регулируемый блок питания БП-24-5.
Работа выполнена под руководством доц. каф. «Автоматизированные технологические системы» Д. М. Медведева
Ермаков Е.Г.
МОДЕРНИЗАЦИЯ АВТОМАТИЗИРОВАННОЙ СИСТЕМЫ УПРАВЛЕНИЯ ТЕМПЕРАТУРОЙ ЭЛЕКТРОПЕЧИ ПКМ 4.8.4/11,5
Объект исследования: закалочный комплекс на базе электропечи ПКМ
4.8.4/11,5.
Результаты, полученные лично автором: выделены основные задачи модернизации системы управления, построена функциональная схема системы управления и интерфейс рабочего места оператора.
Комплекс предназначен для безокислительной закалки легированной, конструкционной, рессорно-пружинной и инструментальной сталей. Для предохранения деталей от окисления и от обезуглероживания применяют безокислительные (защитные) газы, которые вводят в жаропрочный ящик с
83
деталями. В качестве защитных газов в данном закалочном комплексе используется смесь азота с метаном. Существующая система управления данным комплексом, основана на регуляторе температуры «Термодат -10К2»
– он позволяет измерять и регулировать температуру в рабочей камере печи. Для регистрации значений температуры на протяжении всего периода термообработки используется самопищущий прибор «Диск 250». Контроль расхода подаваемого защитного газа осуществляется с помощью ротаметра. Данная система управления является сложной для точного контроля протекания технологического процесса закалки. По результатам исследования существующей системы управления закалочным комплексом были выделены основные задачи модернизации: повышение точности поддержания температуры в рабочем пространстве печи, увеличение производительности, снижение потерь от брака, сокращение потерь от простоев, создание сигнализации о неисправностях, улучшение условий и удобства работы оператора. Построенная функциональная схема системы управления позволяет решить поставленные задачи модернизации. По функциональной схеме рабочее место оператора будет находиться за персональным компьютером, на котором установлен интерфейс системы управления закалочным комплексом, созданный в SCADA системе TRACE MODE. Основные функции регулирования и сбора информации осуществляет микроконтроллер, подключаемый к персональному компьютеру по средствам преобразователя интерфейсов. Связь микроконтроллера с непосредственными элементами управления осуществляется по промышленной сети RS-485. Также предполагается возможность перехода на резервное ручное управление. Создание такой системы управления значительно улучшит эффективность и условие работы оператора, соответственно повысится и качество выпускаемой продукции.
Работа выполнена под руководством ст. преп. каф «Автоматизированные технологические системы» О.П. Чистоклетовой
А.Н. Игнатов
РАЗРАБОТКА ПРОГРАММНОГО МОДУЛЯ ОПРЕДЕЛЕНИЯ ПРОЦЕНТНОГО СОСТАВА КОМПОНЕНТОВ ПО ФОТОГРАФИИ
Объект исследования: нитрид-титановые покрытия.
Результаты полученные лично автором: определены алгоритмы обработки изображения, рассмотрена практическая реализация программного модуля определения процентного состава компонентов в нитрид-титановых покрытиях по фотографии, произведено исследование данных эксперимента взаимосвязи качества поверхностного слоя и износостойкости с условиями электромеханической обработки нитридтитановых покрытий
Развитие техники предполагает применение новых материалов, обладающих специальными свойствами (тугоплавкие, высокопрочные,
84
коррозионностойкие и др.), а также совершенствование технологий упрочнения. Для изучения изменения свойств материалов используется метод изучения изображения микроструктуры материала, полученного при
помощи специального |
оптического или электронного |
микроскопа. В |
последнее время все |
большее распространение и применение находят |
программно-аппаратные комплексы для автоматизации металлографических исследований.
В лаборатории «ПУСК-83» УНТИ БГТУ ведутся работы по изменению свойств материалов методом физического осаждения покрытия (ФОП). Произведены опытные исследования с целью получения эмпирических уравнений взаимосвязи качества поверхностного слоя и износостойкости с условиями электромеханической обработки нитрид-титановых покрытий. Для исследования микроструктуры напыленного покрытия на процент дефектных составляющих в фазе TiN на приборе ПМТ-3М, производилось фотографирование образцов с последующим анализом данных с
применением разработанного программного модуля "PhotoMath". |
|
В качестве входных данных программного модуля |
выступают |
фотографии микроструктуры покрытия до и после электромеханической обработки (ЭМО). Для обработки этих данных используется методологический аппарат компьютерного зрения, в частности - сегментация. Один из основных и простых способов — это построение сегментации с помощью порога. Порог — это признак (свойство, в нашем случае цвет выбранной компоненты), который делит искомое изображение на классы. Операция порогового разделения, которая в результате дает бинарное изображение, называется бинаризацией.
Бинаризация с нижним порогом является наиболее простой операцией, в которой используется только одно значение порога:
0, f (m,n) t f '(m,n)
1, f (m,n) t
Все значения вместо критерия становятся 1, в данном случае 255 (белый) и все значения(амплитуды) пикселей, которые больше порога t — 0 (черный).
Так же возможны другие вариации с порогами, где пропускается только часть данных (средне полосовой фильтр), когда выбранная компонента имеет промежуточный цвет, отличный от фона и других компонент.
В настоящей программе используется пороговая бинаризация с предварительной обработкой полученного изображения, что дополнительно повышает различимость исследуемой компоненты:
перевод цветового пространства RGB в оттенки серого (с максимальной разностью между цветовыми компонентами):
Gray = Round( (Max( R,G,B)+ Min (R,G,B))/2);
расширение динамического диапазона оттенков серого (Lmin, Lmax) до максимального (0, 255) для повышения контраста между оттенками серого (эквализация гистограммы):
Gray = Round( 255*(Gray- Lmin)/( Lmax - Lmin));
85
прохождение по изображению медианного фильтра (для исключения мелких дефектов - точки пыли, царапины) - сглаживается исходное изображение;
с целью снижения уровня цифрового шума преобразования при фотогрфировании и повышения локальной контрастности используется Фильтр Гаусса (Gaussian filter) для обработки серого изображения с последующим вычитанием исходного.
Программа PhotoMath может работать в двух режимах работы: автоматическом и ручном. В ручном режиме производится последовательное прохождение каждого этапа действий программы и определение всех необходимых параметров (так называемое первичное обучение). Автоматический режим предназначен для выполнения всех этапов с заранее определенными (в ручном режиме) параметрами, при этом происходит поиск всех файлов в директории " Photo-In" и сохранение результатов в файл
"MemoLog_Date".
Особенностями данной программы являются:
Все настройки программы PhotoMath сохраняются в ini-файле
Каждое действие пользователя записывается в log-файл и служит для анализа результатов работы алгоритмов программы;
Проверка верности распознавания путем наложение полученного разделение компонент на исходное изображение и визуального контроля.
Таким образом, при выполнении поставленной цели определения компонент по фотографии:
Решена задача по автоматизации деятельности сотрудника лаборатории, в которой реализованы все функции, описанные в постановке задачи.
Разработаны и применены комбинированные методы обработки изображения, исходя из свойств реального объекта исследования.
Проведены испытания программного продукта.
Имеется возможность полной автоматизации эксперимента
(управление фотоаппаратом, передача данных и их обработка в автоматическом режиме с выдачей результата в базу данных и построение графиков).
Работа выполнена под руководством доц. каф "АТС" Матлахова В.П.
Е.Н. Кокарева СОВЕРШЕНСТВОВАНИЕ ИНСТРУМЕНТАЛЬНОГО ОБЕСПЕЧЕНИЯ ТЕХНОЛОГИЧЕСКОГО ПРОЦЕССА ЛИТЬЯ ДЕТАЛЕЙ «КРЫШКА» С ЦЕЛЬЮ ПОВЫШЕНИЯ ПРОИЗВОДИТЕЛЬНОСТИ ДЛЯ УСЛОВИЙ
ОАО ПРИБОРНЫЙ ЗАВОД «СИГНАЛ»
Объект исследования: технологический процесс изготовления детали «Крышка» и предлагаемая инструментальная оснастка.
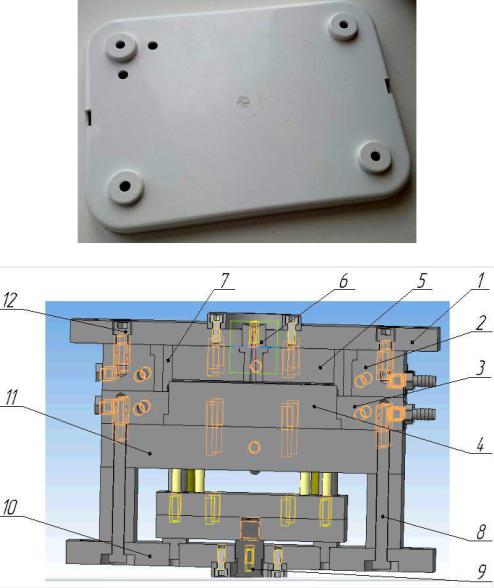
86
Результаты, полученные лично автором: разработан новый вариант технологического процесса изготовления детали «Крышка» и спроектирована инструментальная оснастка в виде стационарной прессформы.
Первоначально деталь «Крышка» для светильника бытового (рис. 1) в размере 180 шт., была изготовлена на съемной пресс-форме в условиях ОАО Приборный завод «Сигнал». После возросшего спроса на светильник, было принято решение о изготовлении 5000 штук в год деталей «Крышка». Так как съемная пресс-форма не дает большей производительности, и приходиться затрачивать много времени на ее изготовление, была спроектирована стационарная пресс-форма (рис. 2).
Рис. 1. Деталь «Крышка»
Рис. 2. Стационарная пресс-форма для изготовлении детали «Крышка» Пресс-форма имеет следующие основные узлы и детали: 1 - фланец верхний; 2 - обойма-матрицы; 3 - знакодержатель; 4 - знак (пуансон); 5 - матрица; 6 - втулка литниковая; 7 - вставка; 8 - болт; 9 - шток; 10 - фланец
нижний; 11 - плита опорная; 12 - винт.
87
Принцип работы пресс-формы: через литниковую втулку 6 поступает пресс-материал в оформляющие полости матрицы 5 и знака (пуансона) 4. Обойма матрицы 2, которая держит матрицу 5, соединена с фланцем верхним 1 и крепится с помощью крепежных винтов 12. Аналогичным образом, знакодержатель 3 держит знак (пуансон) 4, который соединен с опорной плитой 11 и крепится с помощью крепежных болтов 8. Вставка 7 и шток 9 непосредственные конструктивные элементы пресс-формы.
В настоящее время разработаны сборочные чертежи пресс-формы и выполняется детальная проработка рабочих чертежей деталей пресс-формы.
Спроектированная стационарная пресс-форма позволит повысить производительность до 5 раз, по сравнению с базовым вариантом съемной пресс-формы, а также снизить себестоимость изготовления детали «Крышка» до 2 раз.
Работа выполнена под руководством доц. каф. «Металлорежущие станки и инструменты» Л.А. Захарова
Д.В. Коржуков ПРОЭКТИРОВАНИЕ АВТОМАТИЗИРОВАННОЙ СИСТЕМЫ
ОХРАННОЙ И ПОЖАРНОЙ СИГНАЛИЗАЦИИ ДЛЯ БЛОК – КОНТЕЙНЕРА
Объект исследования: блок – бокс, системы обеспечения пожарной и охранной безопасности.
Результаты, полученные лично автором: спроектирована охранно – пожарная сигнализация для блок – контейнера, её структурная схема, схема её работы, план схема расположения элементов, подобраны все необходимые датчики, извещатели, замки и видеорегистраторы.
Данный блок - контейнер предназначен для размещения инженерного оборудования (систем энергообеспечения, инженерных систем поддержания микроклимата, телемеханики, связи, оборудования управления запорнорегулирующей арматурой, оборудования электрохимзащиты, оборудования управления АПС, СОУ, оборудования инженерно - технических средств охраны; автоматической установки газового пожаротушения). Расчетный срок службы блок - контейнера - 30 лет. Средний срок службы инженерного оборудования не менее - 10 лет. В данном случае блок - бокс ПКУ с трансфор-матором на узле запорной арматуры (береговом, дистанционно управляемая задвижка). Так же производятся блок - боксы НКУ. Комплектуется низковольтным комплектным устройством и необходимыми инженерными системами, обеспечивающими исправную работу оборудования в различных климатических условия. Блок-бокс ДЭС. Модульное мобильное сооружение для размещения дизельной электростанции. Блок-бокс связи. Блок-контейнер, предназначенный для установок аппаратной связи и оборудованный системами поддержания
88
микроклимата. Блок-бокс операторной. Здание, состоящее из нескольких технических помещений и комнат для персонала, предназначенное для обеспечения работоспособности установленного в нем оборудования.
Перечень требований: документация, опросный лист с требованиями к комплексу технических средств охраны и требованиями к системе обеспечения пожарной безопасности.
Для выполнения данной задачи был проведен анализ опросного листа, требований к комплексу технических средств охраны и к системе обеспечения пожарной безопасности, а так же гостов, норм и правил проектирования охранно-пожарной сигнализации и требований к проектированию систем контроля и управления доступом, таких как Федеральный закон от 22.07.2008. №123 - Ф3 «Технический регламент о требованиях пожарной безопасности», свод правил 5.13130.2009. и т.д.
Были определены функции охранно - пожарной сигнализации, основной из которых является непосредственно сигнализация и извещение, система пожаротушения в данном случае не предусмотрена. А так же управление дымовыми датчиками, электромеханическими замками на дверях, комбинированными инфракрасными извещателями, табло, сиренами, видеорегистраторами, как внутренними, так и по периметру, и передача информации с них в районо - диспечерский пункт, анализ цепи на обрыв и короткое замыкание.
Была разработана структурная схема управления ОПС, где Сигнал 20П - подключение неадресных извещателей, отвечает за охранную сигнализацию (20 шлейфов).
Сигнал 10 - отвечает за пожарную сигнализацию (10 шлейфов). Ск - сухой контакт.
С2000 - КПБ - для управления исполнительными механизмами, свет и звук оповещения. ИГП - источник гарантированного питания. С2000 - СП1 - рэлейный блок (4 реле до 2А и 250В), для управления внешними устройствами. СОКОЛ - 3 - комбинированный датчик. ИО 102 - 26 - магнитоконтактный датчик.
Был произведен анализ мест возникновения пожара, в основном пожар возникает по вине эксплуатации, из-за несанкционированного увеличения мощности нагрузки, из - за ошибок монтажа, поэтому пожар может возникнуть как в трансформаторном так и в инженерном отсеке, в шкафах: ШОС, силового распределения, телемеханики, оборудования связи и т.д.
Был произведен анализ всех составляющих опс, и фирм производителей, были выбраны все необходимые извещатели, оповещатели, замки электро - механические, видеокамера, пульт контроля и управления.
Производители и поставщики систем ОПС:
1.Болид - наиболее адаптированная система, выгодная по функциональ - ности, качеству и цене. 2.Рубеж 3.Торговый дом "Тинко" 4.Сигма - ИС 5. Нита.
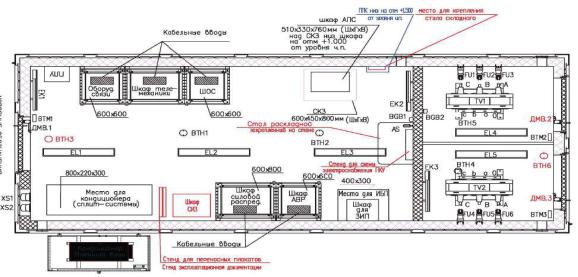
89
Рис. 1. План схема расположения элементов в блок-контейнере.
Работа выполнена под руководством проф. каф. «Автоматизированные технологические системы» О.Н. Федонина
Д.А. Косицын СИСТЕМА АВТОМАТИЧЕСКОГО УПРАВЛЕНИЯ ОХЛАЖДЕНИЕМ
УСТАНОВКИ АРСЕНИД -1М
Объект исследования: установка выращивания кристаллов Арсенид1М. Результаты, полученные лично автором: подбор шарового крана с электроприводом, выбор ПЛК с функцией ПИД-регулирования, термопар, манометра, реле потока.
Гидравлическая система охлаждения установки выращивания кристаллов арсенида галлия включает напорный коллектор, сливной коллектор, контура охлаждения и узел подготовки воды. Система имеет в своем составе шаровые краны с электроприводами, перекрывающими общий поток воды и каждый из контуров отдельно (рис.1).
Давление на магистральном трубопроводе контролируется двумя манометрами. Для визуального наблюдения за протоком воды и сигнализации о наличии заданного расхода, каждый контур имеет индикатор потока.
В сливном коллекторе для контроля температуры воды в каждом контуре и общем сливе установлены термопреобразователи. Давление воды на входе в установку: 2–2.5 атм. Слив закрыт, без разрыва струи. В системе предусмотрен контроль температуры и наличие потока воды в каждом контуре, а так же на входе и выходе установки.
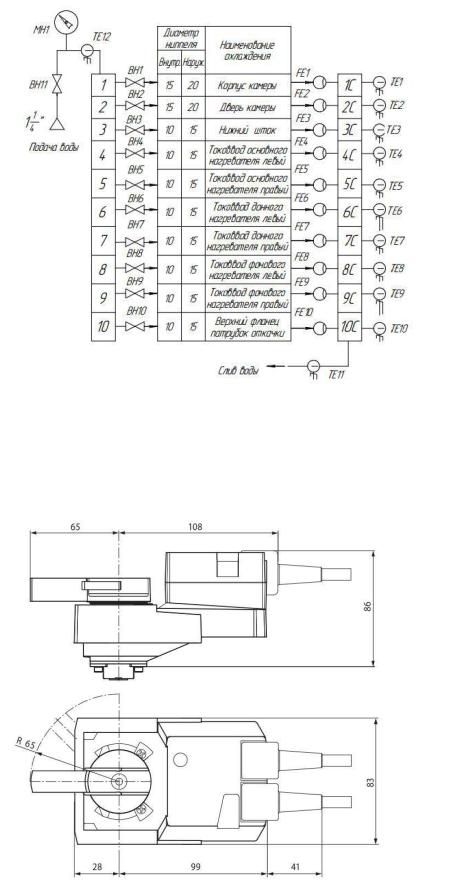
90
Рис. 1. Гидравлическая система установки выращивания кристаллов арсенида галлия.
Выполнен подбор шаровых кранов с электроприводами для управления от ПЛК. Шаровой кран Belimo с электроприводом предназначен для точной
регулировки |
потоков |
воды (рис. |
2). |
Рис.2 Электропривод шарового крана Belimo