
Сборник 70 студ конференции БГТУ
.pdf
141
объектно-ориентированная среда визуального программирования Visual Basic 8.0.
Система даст возможность производить оценку эффективности и обосновывать предлагаемые технологические процессы в более короткие сроки, что позволит разработанной системе занять место в общем цикле подготовки производства.
Данная САПР найдет успешное применение на предприятиях, а также в учебном процессе при подготовке студентов технических специальностей на этапе курсового и дипломного проектирования.
Работа выполнена под руководством доц. каф. «Технология машиностроения» Е.А. Польского, С.В. Сорокина
Д.Е. Васильева, А.В. Орлов НАДЁЖНОСТЬ ТЕХНОЛОГИЧЕСКОГО ОБЕСПЕЧЕНИЯ
ВЫСОТНЫХ ПАРАМЕТРОВ ШЕРОХОВАТОСТИ АЛМАЗНЫМ ВЫГЛАЖИВАНИЕМ
Объект исследования: технологические системы алмазного выглаживания поверхностей.
Результаты, полученные лично автором:надёжность технологического обеспечения высотных параметров шероховатости поверхностей деталей.
Известно, что триботехнические свойства поверхностей во многом определяются параметрами качества поверхностного слоя (ПКПС), которые формируются в процессе обработки и характеризуются достаточной управляемостью за счёт факторов технологических систем (ТС).
По известной методике проф. В.П.Федорова с применением системы компьютерного мониторинга исследована параметрическая надёжность ряда ТС, в том числе надёжность технологического обеспечения параметров шероховатости поверхностей деталей из чугуна СЧ20 алмазным выглаживанием и триботехнических характеристик пар трения-скольжения комбинированной обработкой на основе нанесения износостойких покрытий
иалмазного выглаживания.
Вкачестве показателя рациональности выбора той или иной ТС по критерию параметрической надёжности предлагается максимум вероятности P выполнения задания по случайному параметру качества Y в заданном
интервале:
P Y |
|
|
|
|
|
|
|
max, |
(1) |
Y |
Y;Y |
Y |
где Y - средняя величина регламентируемого параметра качества; - относительная допускаемая величина его изменения (0 1).В качестве исходных данных используются результаты построения имитационных моделей с учётом конструкторских и технологических ограничений.
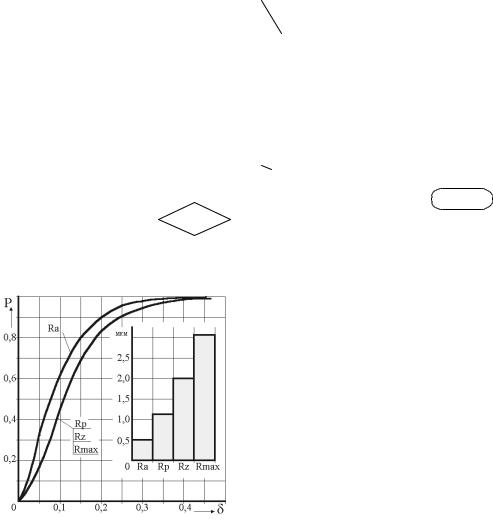
142
При алмазном выглаживании плоских поверхностей из чугуна СЧ20 исследовалось влияние следующих факторов: 1) предварительная обработка торцевым фрезерованием композитом-10 (Raпр = 0,6 – 3,6 мкм); 2) сила алмазного выглаживания (Q = 50 – 250 Н) индентором из синтетического алмаза АСПК радиусом r = 3 мм при наличии СОТС «ИС-30»; 3) подача выглаживания (S = 0,03 – 0,16 мм / об); 4) скорость выглаживания (V = 35 – 85 м / мин). Имитационные модели для исследуемых параметров строились на основе реализации активного эксперимента.
. Например, для параметра Ra ИМ имеет вид:
Ra 0,55Ra0пр,4 V0,22Q0,28 . (2)
Блок-схема расчёта надёжности ТС таким методом показана на рис. 1.
Анализ надёжности технологического обеспечения высотных параметров шероховатости, полученных при средних значениях факторов выглаживания (рис 2.), показывает, что надёжность обеспечения величины Ra выше, чем других высотных параметров для одинаковых .
|
Исходные данные |
|
|
|
1. |
|
Y = f ( o, i, Xi) |
|
|
|||||||
|
|
|
|
2. |
|
M { i}, S { i} |
Оценка параметров |
|||||||||
|
|
|
|
|
|
|
|
|
|
|||||||
|
Расчёт условий |
|
|
|
|
|
|
M {Xi}, S {Xi} |
|
распределения. |
||||||
|
|
обработки |
|
|
|
3. |
|
Ymax, Ymin |
|
Проверка |
||||||
|
|
|
|
|
|
|
статистических гипотез |
|||||||||
|
|
Расчёт N |
|
|
|
4. |
|
Xi max, Xi min |
|
|
|
|||||
|
|
|
|
|
5. |
, a, d |
|
Оценка параметров |
||||||||
|
|
j = 1 |
|
|
|
|
|
|
|
|
|
|||||
|
|
|
|
|
|
|
|
|
|
|
распределения. |
|||||
|
|
|
|
|
|
|
|
|
|
|
|
|
|
|
Проверка |
|
|
Генерация случайных |
|
|
|
|
|
|
|
|
|||||||
|
|
|
|
|
Датчик |
|
|
статистических гипотез |
||||||||
|
параметров модели |
|
|
|
|
|
|
|||||||||
|
|
псевдослучайных |
|
|
|
|
||||||||||
|
|
|
|
|
|
|||||||||||
|
|
Xi, oj, ij |
|
|
|
|
|
чисел |
|
|
Расчёт вероятности |
|||||
|
|
|
|
|
|
|
|
|
|
|
|
|
|
|
безотказной работы ТС |
|
|
|
Расчёт Yj0 |
|
|
Y1, Y2, ... , Yj, ... , YN |
|
||||||||||
|
|
|
|
|
в течение t |
|||||||||||
|
|
|
|
1, 2, ... , j, ... , N |
|
|||||||||||
|
|
j = j + 1 |
|
|
|
|
|
|||||||||
|
|
|
|
|
|
|
|
|
|
|
|
|
||||
|
|
|
|
|
|
|
|
|
|
|
Конец |
|||||
|
да |
нет |
|
|
|
|
|
|
|
|||||||
|
|
|
|
|
|
|
|
|
|
|||||||
|
|
j < N |
|
|
|
|
|
|
|
|
|
|
|
|
||
|
|
|
|
|
|
|
|
|
|
|
|
|
|
Рис.1. Блок-схема расчёта параметрической надёжности технологической системы
Рис. 2. Надёжность обеспечения высотных параметров шероховатости
алмазным выглаживанием
Поэтому, в соответствии с критерием (1), высотные характеристики шероховатости предпочтительнее регламентировать величиной Ra при отсутствии других ограничений.
Сравнение по указанному критерию алмазного выглаживания с накатыванием шариком при идентичных силовых и скоростных факторах показывает предпочтительность применения первого метода.
Анализ надёжности технологического обеспечения высотных параметров шероховатости, полученных при средних значениях факторов выглаживания, показывал, что надёжность обеспечения величины Ra

143
выше, чем других высотных параметров для одинаковых . Поэтому высотные характеристики шероховатости предпочтительнее регламентировать величиной Ra при отсутствии других ограничений.
Сравнение по указанному критерию алмазного выглаживания с накатыванием шариком при идентичных силовых и скоростных факторах показывает предпочтительность применения первого метода.
Итак, с помощью системы компьютерного мониторинга можно осуществлять высокопроизводительные измерения и вычислять ПКПС с высокими требованиями к точности и достоверности полученных результатов.
Работа выполнена под руководством проф .каф."Технология машиностроения" В.П. Федорова и доц .каф."Металловедение и машиностроение" Е.В. Ковалевой
М.К. Власенков РАЗРАБОТКА АВТОМАТИЗИРОВАННОЙ ПОДСИСТЕМЫ РАСЧЕТА
ПОГРЕШНОСТИ ОБРАБОТКИ, ВЫЗВАННОЙ РАЗМЕРНЫМ ИЗНОСОМ РЕЖУЩЕГО ИНСТРУМЕНТА
Объект исследования: этап технологической подготовки производства по расчету элементарных составляющих суммарной погрешности обработки деталей машин.
Результаты, полученные лично автором: разработан программный модуль автоматизированной подсистемы расчета погрешности обработки, вызванной размерным износом режущего инструмента.
Современное машиностроительное производство характеризуется как многономенклатурное с частой сменой выпускаемых изделий, повышенной конструктивной сложностью, большим числом оригинальных и уникальных конструкторских решений, реализация которых сопровождается высокими требованиями к качеству, надежности и ресурсу изделий.
Автоматизация проектирования в машиностроительном производстве – часть комплексной проблемы автоматизации инженерного труда во всех сферах функционирования современной производственной системы.
В данном исследовании рассмотрена задача автоматизации расчета составляющей суммарной погрешности обработки, вызванной размерным износом режущего инструмента.
Суммарную погрешность обработки деталей на настроенных станках для диаметральных размеров (чистовое растачивание отверстий) определяют по уравнению:
|
2 |
2 |
|
2 |
|
2 |
|
|
2 |
|
|
т |
2 |
|
у |
|
н |
|
1,73 и |
|
1,73 |
ст |
|
1,73 |
|
||
|
|
|
|
|
|
|
|
|
|
|
|
|
, |

144
где У – погрешность обработки, вызванная упругими деформациями технологической системы под влиянием силы резания; Н – погрешность настройки станка; И – погрешность, вызванная размерным износом инструмента; СТ – погрешность, вызванная геометрическими неточностями станка; Т – погрешность обработки, вызванная температурными деформациями технологической системы.
Таким образом, необходимо определить значения всех элементарных погрешностей.
В процессе работы автоматизированная система расчета погрешности использует следующую математическую базу. Размерный износ инструмента измеряют в направлении нормали к обрабатываемой поверхности и суммируют с другими погрешностями.
LД = vtО
или
LД = (πDlД)/1000S
где D – диаметр обрабатываемой поверхности, мм, lД – длина обрабатываемой поверхности, мм, S – подача, мм/об.
Линейная зависимость размерного износа инструмента от длины пути резания на основном участке позволяет принять за характеристику размерного износа относительный (удельный) износ на 1000 м пути резания
(и0, мкм/км).
Для того чтобы учесть более интенсивное начальное изнашивание на первом участке кривой, условно принято увеличивать полученную расчетом длину пути резания на 1000 м. Приняв по нормативным или экспериментальным данным относительный размерный износ и0 резца для данных условий выполнения операции, определяют учитываемый в суммарной погрешности размерный износ.
На размерный износ влияют материал режущего инструмента, конструкция, геометрия и состояние лезвия, режимы обработки, жесткость системы и другие факторы. Например, зависимость радиального (размерного) износа от времени работы Т (мин), скорости резания v (м/мин) для обработки деталей из стали 45 резцом с пластиной из твердого сплава Т15К6 может быть выражена формулой
L
и 1000и0
Однако в достаточной степени обобщенных зависимостей размерного износа инструмента от указанных факторов пока нет. Поэтому часто, определяя размерный износ для обрабатываемой партии деталей, исходят из ориентировочных значений относительного износа или задаются допустимым для данного вида обработки размерным износом инструмента.
Автоматизированная система работает в следующем порядке. В начале процедуры объявляются все переменные, необходимые для расчета (входные данные и коэффициенты). После этого осуществляется считывание введенных пользователем с клавиатуры данных и передача их в соответствующие переменные. Первым этапом расчета является определение
145
относительного износа. Для этого сначала формируется SQL-запрос, в котором из таблицы material, на основании выбранной из выпадающего списка cmbMaterial марки материала режущей части инструмента, выбирается код типа материала. Затем этот код подставляется в запрос к таблице u0, из которой выбираются значения коэффициента u0. Заключительным этапом выполнения рассматриваемой процедуры является расчет погрешности, вызванной размерным износом режущего инструмента, и вывод на экран окна с результатами расчета.
Разработанная автоматизированная система расчета составляющей суммарной погрешности обработки, вызванной размерным износом режущего инструмента проста и легка в применении, как на предприятиях, так и в учебных целях. Полученные результаты при выполнении данных исследований весьма актуальны в настоящее время и их значение будет увеличиваться в будущем, так как научный прогресс идет вперед, постоянно ускоряя свои шаги. Появляется необходимость в автоматизированных системах для ускорения работы. Автоматизированная система значительно ускоряет работу инженеров и студентов.
Работа выполнена под руководством доц. каф. «Технология машиностроения» Е.А. Польского, С.В. Сорокина
Б.Э. Голдобов РАЗРАБОТКА АВТОМАТИЗИРОВАННОЙ ПОДСИСТЕМЫ РАСЧЕТА
ПОГРЕШНОСТИ ОБРАБОТКИ, ВЫЗВАННОЙ ГЕОМЕТРИЧЕСКИМИ НЕТОЧНОСТЯМИ СТАНКА
Объект исследования: этап технологической подготовки производства по расчету элементарных составляющих суммарной погрешности обработки деталей машин.
Результаты, полученные лично автором: разработан программный модуль автоматизированной подсистемы расчета погрешности обработки, вызванной геометрическими неточностями станка.
Создание новой техники в машиностроении происходит в такой последовательности: на основе анализа выпускаемой продукции проектируется новая, обладающая более высокими эстетическими, эксплуатационными или другими свойствами, затем производятся инженерные расчеты и моделирование, технологическая подготовка производства, изготовление и сбыт изделия. При этом мы получаем замкнутый цикл, так как проектирование нового изделия выполняется на базе анализа рынка и данных об эффективности, надежности и сбыте выпускаемых моделей.
Использование САПР позволяет членам проектных групп одновременно работать над изделием с разных сторон: решать задачи стилевого дизайна, проектирования внешнего вида изделия и параллельной поагрегатной разработки изделия. Новое изделие создается в конструкторском

146
подразделении, которое является центральным звеном компьютеризации предприятия. Одновременно группой специалистов различных профилей, работающих над выпуском нового изделия, выполняются все этапы разработки деталей, узлов и сборок, их технологическая проработка.
Изделие начинают изготавливать еще до того, как будет завершен выпуск всей документации, что приводит к значительному сокращению сроков и повышает качество проектирования. Облегчается автоматизированное управление проектами и предприятием на базе электронного документооборота. Любые изменения в любом элементе изделия незамедлительно становятся доступными как для отдельных конструкторов и технологов, так и для целых отделов и организаций на всех этапах создания изделия — благодаря использованию единой базы данных. Таким образом, САПР сокращает время и трудозатраты на проектирование изделия.
В данном исследовании рассмотрена задача автоматизации расчета составляющей суммарной погрешности обработки, вызванной геометрическими неточностями станка.
Суммарную погрешность обработки деталей на настроенных станках для диаметральных размеров (чистовое растачивание отверстий) определяют по уравнению:
|
2 |
2 |
2 |
2 |
|
2 |
|
|
|
2 |
, |
|
у |
н |
1,73 и |
1,73 |
ст |
|
1,73 |
т |
|||
где У – |
погрешность обработки, вызванная упругими деформациями |
||||||||||
технологической системы под влиянием силы резания; |
Н – погрешность |
||||||||||
настройки |
станка; |
И – погрешность, вызванная размерным износом |
|||||||||
инструмента; |
СТ – погрешность, вызванная геометрическими неточностями |
||||||||||
станка; |
Т – погрешность обработки, вызванная температурными |
||||||||||
деформациями технологической системы. |
|
|
|
|
|
|
|||||
Таким образом, |
необходимо определить значения всех элементарных |
погрешностей. Основной сложностью при проведении расчетов является необходимость постоянного анализа эмпирических данных по точности и жесткости оборудования и выбору справочных материалов из большого числа таблиц и графиков. В процессе работы автоматизированной системы расчёта погрешности вызванной геометрической неточностью, были использованы формулы описания прямых в косвенном виде для построения графиков.
Для выполнения расчёта необходимо ввести (выбрать) следующие данные:
тип станка;
параметры вызывающие погрешность;
размеры детали;
класс точности станка.
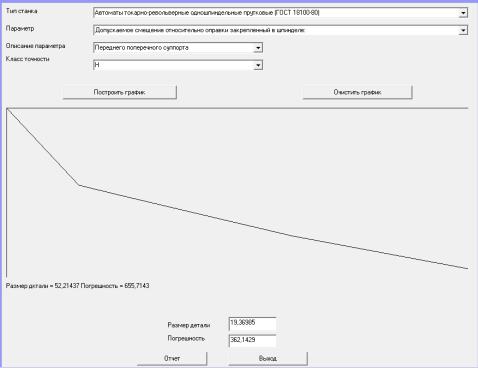
147
В соответствии с введенными данными строится график зависимости погрешности от размеров детали, по которому в соответствии с габаритами заготовки пользователь определяет жесткость оборудования (рис. 1).
Рис. 1. Рабочее окно автоматизированной системы. Разработанная САПР может найти применение на предприятиях, а также
в учебном процессе при подготовке студентов технических специальностей в рамках выполнении курсового и дипломного проектирования
Работа выполнена под руководством доц. каф. «Технология машиностроения» Е.А. Польского, С.В. Сорокина
А.А. Горбачёв ПРОЕКТИРОВАНИЕ ТЕХНОЛОГИЧЕСКОЙ ОСНАСТКИ В
СИСТЕМЕ SOLIDWORKS
Объект исследования: CAD/CAE/CAM-система SOLIDWORKS. Результаты, полученные лично автором: разработаны библиотеки
параметрических прихватов и параметрические модели станочных приспособлений.
SOLIDWORKS – это полнофункциональная 3D CAD/CAE/CAM
система. Основное назначение SOLIDWORKS – обеспечение сквозного процесса проектирования, инженерного анализа и подготовки производства изделий любой сложности, включая создание интерактивной документации.
Система SOLIDWORKS позволяет проектировать и создавать 3Dмодели сборок любого назначения. При этом доступно большое количество
148
приемов проектирования геометрии деталей и их сопряжения в сборочных моделях.
Целью работы являлось знакомство с системой SOLIDWORKS и разработка в ней параметрической модели станочного приспособления для обработки валов.
Станочные приспособления состоят из следующих типов деталей:
установочные элементы;
зажимные элементы;
направляющие элементы;
корпусы;
вспомогательные элементы.
Установочные (опорные) элементы имеют разнообразные конструкции, многие из которых стандартизированы. Эти элементы позволяют обеспечить определенную ориентацию заготовки относительно режущего инструмента.
Зажимные элементы входят в состав системы закрепления заготовок в приспособлении. Силы резания, действующие в процессе обработки, могут нарушить положение, достигнутое при базировании. Они также могут вызвать вибрации детали, которые могут привести к значительным погрешностям обработки и отрицательно действуют на сохранность инструмента, приспособления и станка. Поэтому необходимо надежное крепление детали в приспособлении с помощью различных зажимных устройств. Наиболее распространенными являются винтовые прихваты.
В качестве одной из задач при проектировании станочного приспособления ставилась задача разработки параметрической модели конструкции откидного прихвата. При этом использовались широкие возможности параметризации системы SOLIDWORKS.
Проектирование станочного приспособления выполнялось в следующей последовательности:
1.Разработана схема базирования заготовки. При установке валов наиболее часто применяется набор из двойной направляющей и опорной баз. Для их реализации в конструкции приспособления использованы стандартные призмы.
2.Выбран тип и разработана модель винтового прихвата для закрепления заготовок. В конструкции прихвата использованы стандартные детали: прихваты ГОСТ 4736-69, вилки ГОСТ 4738-67, болты ГОСТ 1472469, гайки ГОСТ 5927-70 и ГОСТ 15524-70, оси ГОСТ 9650-80, шайбы ГОСТ
11371-78, шплинты ГОСТ 397-79.
3.Выполнена табличная параметризация модели деталей и самой сборки откидного прихвата. Это позволило при необходимости быстро изменять его конструкцию.
4.Спроектирована конструкция и разработана модель корпуса, объединившая все ранее выполненные компоненты приспособления в единую систему (см. рис).
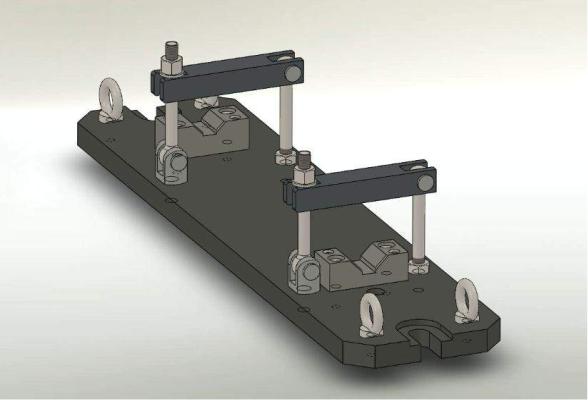
149
Рис. Модель разработанного станочного приспособления
Особенностью разработанной модели приспособления является широкое применение возможностей параметризации системы SOLIDWORKS. Конструкции приспособления можно быстро изменить и настроить под текущую задачу.
Работа выполнена под руководством доц. кафедры «Технология машиностроения» Д.М. Филькина
В.Ю. Данилова, И.Д. Воронина ПРИМЕНЕНИЕ НАНОРАЗМЕРНЫХ ПОРОШКОВ
Объект исследования: субмикронные материалы и композиции нанопорошков.
Результаты, полученные лично автором: проведен анализ повышения надежности деталей машин, работающих в особых условиях, за счет создания модифицированных поверхностных слоев с нанесением нанопокрытий из различных материалов.
Большая часть производимых порошков цветных металлов - это цинковые, медные и изготовленные из ее сплавов. В настоящее время получают. субмикронные порошки меди и ее сплавов со средним размером частиц от 0,01 до 1,0 мкм методом испарения-конденсации в инертном газе. После выполнения исследования наноструктурных превращений стальной поверхности в присутствии субмикронных порошков сплавов меди‚
150
содержащей субмикронный порошок сплава меди, было установлено что при введении между контактирующими поверхностями из стали композиции смазки, возникают реакции, которые приводят к наноструктурньм превращениям этих наружных стальных слоев. Выделенные при этом атомы меди обладают повышенной энергией, поэтому активно взаимодействуют с металлом-подложкой, встраиваясь в его наружные слои. Происходит микромодифицирование поверхности металла и появляется наноструктурное покрытие, обладающее необычным свойством - сочетанием высокой твердости с повышенной пластичностью.
Здесь важно то, что образовавшийся нанокристаллический медьсодержащий пласт в процессе эксплуатации ведет себя как специфическое микропокрытие, защищающее поверхности контакта от трения.
В конце 1980-х годов была создана система получения нанопорошков Fе, Ni, Со и Сu методом термического разложения химических соединений - оксалатов (солей с достаточно низкой температурой разложения). Частицы нанопорошков, образовавшиеся в результате топохимической реакции, имеют значительные искажения кристаллической решетки, что обеспечивает им высокую активность в различных физико-химических процессах.
Для увеличения дисперсности (величины, характеризую щей размер нанопорошков была использована добавка 0,5°/о МgО в виде раствора нитрата магния в этаноле, которым перед восстановлением смачивали исследуемые соли. Полученные порошки металлов имели удельную поверхность, свойственную максимально дисперсным продуктам пиролиза.
Добавим: нами также разработаны конструкцонные порошковые стали с новым композиционным типом структуры: последняя состоит из крупных сферических частиц железноГо порошка, связанных по границам мелкозернистыми прослойками на основе нанопорошковNг - Си сплавов, диффузионно-насыщенных железом и дисперсно-упрочненных включениями 7г02. в итоге проверка показала: эти новинки по прочности и пластичности в 2 - 4 раза превосходят аналогичные по составу, но полученные из смеси традиционны порошков. Кроме того, добавление нанопорошков Nг и Си совместно с углеродом позволило получить порошковую сталь Х71-i2 (содержит 17°/о хрома, 2°/о водорода) с коррозионной стойкостью и механическими свойствами не хуже, чем у обычной литой стали того же состава.
Нано двуокись титана.
Высокочистый нано диоксид титана в анатазной и рутильной форме. Средний размер частиц менее 100нм. Представленные наноразмерные оксиды титана имеют хорошую прозрачность и отличную способность к поглощению ультрафиолетового излучения в длинноволновом и средневолновом диапазонах, в отличие от обычного диоксида титана. Нано оксид титана не растворим в воде, органических кислотах, слабых неорганических кислотах. Растворим в серной и фтористоводородной кислотах, щелочах.