
Сборник 70 студ конференции БГТУ
.pdf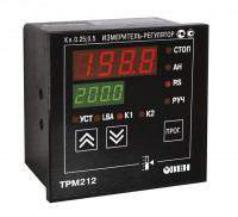
91
Измеритель ПИД-регулятор ОВЕН ТРМ212 для управления задвижками и трехходовыми клапанами с интерфейсом RS-485 (рис. 3).
Рис.3 ПИД-регулятор ОВЕН ТРМ212
Работа выполнена по руководством доц. каф. АТП БГТУ О.Н. Крахмалева
М.В. Костюков РАЗРАБОТКА И ИЗГОТОВЛЕНИЕ ПРИВОДА ГЛАВНОГО
ДВИЖЕНИЯ И НЕСУЩЕЙ СИСТЕМЫ ГРАВИРОВАЛЬНО-ФРЕЗЕРНОГО СТАНКА С ЧПУ
Объект исследования: гравировально-фрезерный станок.
Результаты, полученные лично автором: спроектирована и построена графическая модель, подобран привод главного движения и изготовлены элементы несущей системы гравировально-фрезерного станка.
Из приведённого обзора и анализа различных существующих компоновочных решений гравировально-фрезерных станков, а также на сравнении технических и экономических параметров станков аналогов отечественного и зарубежного производства, была выбрана наиболее рациональная компоновка, положенная в основу проектируемого станка.
Гравировально-фрезерный станок предназначен для обработки различных металлических и неметаллических материалов таких, как: сталь, бронза, пластик, дерево, камень и т.д. Технические характеристики и точность обработки позволят с легкостью использовать данную модель для таких работ, как: рельефная гравировка (гравировка изображений, табличек, штампов для теснения, выжимных печатей); полиграфия (штампы, пломбираторы, выжимные печати); ювелирное дело (инкрустация драгоценностей, изготовлении медалей, значков, брошей и т.д.); электроника (фрезеровка печатных плат) и др.
Рациональная область применения такого оборудования: малый и средний бизнес; учебный процесс (ВУЗы, ССУЗы и т.д.); промышленность
92
(машиностроение, станкостроение и приборостроение), а также домашние мастерские.
Впроцессе проектирования была разработана и построена графическая 3D модель конструкции проектируемого гравировально-фрезерный станка
(рис. 1).
Станок имеет следующую конструкцию. К боковым сторонам основания
(1)крепятся две вертикальные стойки (2) с траверсой (3). На траверсе (3) расположены вертикальные салазки (6) с приводом главного движения (7). Вертикальные салазки (6) имеют возможность передвигаться в вертикальном направлении, совершая подачу по оси Z. На основание (1) установлены продольные (4) и поперечные (5) салазки со столом (8), которые совершают подачу по осям Х и Y. На столе (8) устанавливается обрабатываемая заготовка.
Вкачестве привода главного движения было решено использовать современный электрошпиндель с воздушным охлаждением фирмы GMT
модели AS800. Он позволяет обеспечивать регулировку частоты вращения шпинделя до 24000 мин-1, обладает требуемой мощностью 0,8 кВт, и имеет исполнение переднего конца шпинделя в виде цангового патрона ER16 для закрепления инструментальной оснастки нагружаемой и в аксиальном, и в радиальном направлении, который позволяет установить различный осевой режущий инструмент диаметром до 10мм.
Для возможности регулировки частоты вращения вала электрошпинделя в пределах от 1000 до 24000 мин-1, применяем векторный частотный преобразователь компании «DELTA ELECTRONICS» модели VFD, что позволит подобрать оптимальные режимы резания, характерные для разных условий обработки.
Конструкцию несущей системы станка (рис. 2), имеет основные базовые узлы: основание; две стойки и траверса.
Основание (1) это одна из основных частей станка, на которое монтируется или устанавливается все узлы и элементы станка. Имеет коробчатую форму для возможности установки электрооборудования во внутренней полости.
Две стойки (2) предназначены для возможности установки траверсы с вертикальными салазками и приводом главного движения на требуемую высоту относительно других узлов.Траверса (3) станка состоит из различных частей: плиты, ребер жесткости, балки и крышек. Плита монтируется на две стойки, и на которую крепиться вертикальные салазки с приводом главного движения. Ребра жесткости крепятся с внутренней стороны плиты траверсы для повышения жёсткости несущей системы. Задняя балка предназначена для обеспечения требуемой жесткости всей траверсы и небольшого противовеса для привода главного движения. Балка крепиться в противоположном направлении плиты на стойках. Крышки крепятся с верхней и нижней стороны траверсы, которые предназначены защиты электропроводки монтируемой во внутренней полости траверсы..
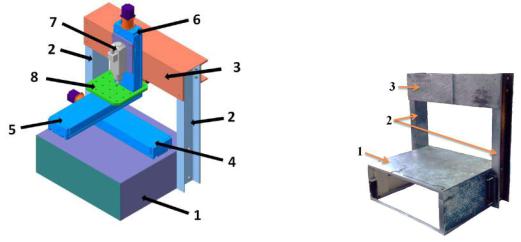
93
Рис. 1. Графическая 3D модель |
Рис. 2. Несущая системы |
гравировально-фрезерного станка |
гравировально-фрезерного станка |
В ходе данной работы была спроектирована и построена графическая 3D модель конструкции станка, на основе которой был изготовлен комплект чертежей. Подобраны и заказаны все покупные изделия. В настоящее время станок проходит стадию изготовления и наладки в условиях кафедры «Металлорежущие станки и инструменты» УНТИ БГТУ.
Работа выполнена под руководством доц. каф. «Металлорежущие станки и инструменты» А.Н. Щербакова
П. С. Левкин АВТОМАТИЗИРОВАННОЕ ПРОФИЛИРОВАНИЕ ЗУБЬЕВ
РЕЗЬБОФРЕЗЫ
Объект исследования: создание профиля резебофрезы с помощью программ на ЭВМ.
Результаты, полученные лично автором: проанализированы существующие способы профилирования резьбофрез, предложена методика профилирования резьбофрезы при помощи программ на ЭВМ.
В настоящее время существует множество способов получения резьбы, одним из которых является резьбофрезерование. Инструментами для этого метода служит резьбофрезы. С целью сохранения идентичности профиля резьбы при переточках фрезы изготавливаются только с затылованными зубьями.
Из-за наличия кольцевых витков теоретический профиль резьбы отличается от действительного. В процессе фрезерования ось заготовки расположена параллельно оси фрезы. Если рассечь заготовку и фрезу плоскостями, перпендикулярными к осям, то в этих сечениях получим для фрезы окружность, а для заготовки архимедову спираль с двумя ветвями.
94
Точка контакта профилей заготовки и фрезы располагается в стороне от центровой линии. Вследствие этого теоретический профиль резьбы фрезы отличается от профиля резьбы. Поэтому необходимо решать задачу профилирования резьбофрез.
При проектировании профиля резьбофрезы используется три основных метода профилирования: аналитический, графический и графоаналитический. Графический метод – прост и нагляден, но не дает высокой точности. Есть несколько способов графического профилирования: метод совмещенных (наложенных) сечений, метод последовательных положений и др. Их часто применяют как контрольные для определения ошибок в расчетах. Аналитический метод – заключается в определении точек профиля инструмента путем решения системы уравнений, описывающих условия контакта инструмента и детали. Существуют точные и приближенные методы. Приближенные применяются в случаях, когда имеющаяся при этом погрешность не выходит за пределы допускаемой. При этом точный профиль инструмента заменяется более простой известной линией. Графоаналитический метод – заключается в том, что ряд параметров определяется расчетом, а некоторые - графическим построением.
Графический метод дает возможность построить профиль зуба фрезы. Поскольку боковая поверхность резьбы образуется движением прямой линии, пересекающей ось и наклонной к ней под определенным углом, то первоначально строят винтовые поверхности , образующие боковые стороны резьбы. Для этой цели строят окружность диаметром d0 (проекция А, рис. 1), равным наружному диаметру резьбы, и концентричную ей окружность диаметром d1, равным внутреннему диаметру резьбы. Большую окружность делят на определенное количество частей и через деления проводят радиальные прямые 0-0’, 1-1’, 2-2’, и т. д. до внутренней окружности.
Затем слева (проекция Б, рис. 1) от этой окружности строят вторую проекцию резьбы. Для этого проводят первую образующую 0-0’. От обоих концов этой образующей вдоль оси откладывают шаг винтовой линии. Шаг делят на то же число делений, 0-1”; 1”-2”; 2”-3” и т. д. и 0-1’’’; 1’’’-2’’’ и т. д. , на которое разделена окружность. Через эти деления проводят прямые, перпендикулярные к оси. Затем через точки деления окружности параллельно оси проводят прямые 0-0; 1-1; 2-2; и т. д. и 0’-0’; 1’-1’; 2’-2’ ит. д. до пересечения с соответствующими им вертикальными прямыми. Получим ряд точек на левой проекции резьбы и ряд на наружном диаметре 0, 1, 2, 3 и т.д. соответствующих им точек на внутреннем диаметре резьбы 0’, 1’, 2’ и т.д. Соединяя одноименные точки на наружной и внутренней поверхностях, получим винтовую поверхность, определяемую образующими. Таким же образом строят и вторую боковую поверхность. После построения винтовых поверхностей они рассекаются плоскостями 11, 21, 31, 41 и т.д., перпендикулярными к плоскости чертежа, наклоненными к оси под углом φ.
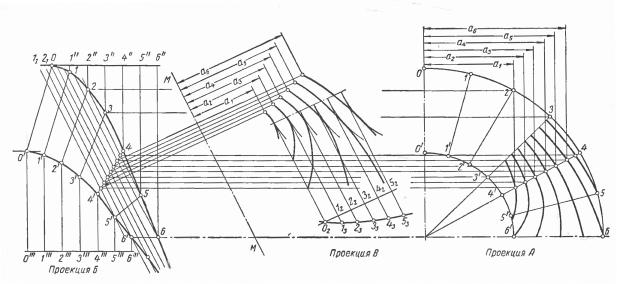
95
РРис. 1. Графический метод профилирования.
Аналитический метод заключается в определении точек профиля ИП путем решения систем уравнений, описывающих условие контакта ИП и Д. Для определения ИП разработан алгоритм: 1) определение угла наклона винтовой поверхности на каждом радиусе в пределах поверхности Д; 2) определение угла на каждом радиусе в пределах поверхности Д; 3) вычисление координат точек контакта на поверхности детали; 4) определение координаты профиля ИП.
При автоматизированном профилировании предлагается расчет координат точек производить с помощью программы Excel или любой подобной программы , потом программе КОМПАС-3D по рассчитанным координатам будет происходить построение профиля резьбофрезы.
Работа выполнена под руководством доц. каф. «Металлорежущие станки и инструменты» Д.В. Левого
А.В. Лохвицкий
РАЗРАБОТКА И ИЗГОТОВЛЕНИЕ УСТРОЙСТВА ДЛЯ БАЛАНСИРОВКИ ИНСТРУМЕНТОВ
Объект исследования: |
устройство для |
балансировки |
дисковых |
|
инструментов |
|
|
|
|
Результаты, полученные лично автором: спроектировано и |
||||
изготовлено |
устройство |
для статической |
балансировки |
дисковых |
инструментов |
|
|
|
|
Кафедрой «Металлорежущие станки и инструменты» проводились исследования по разрезанию пластмасс. Во время экспериментов возникла проблема вибраций. При работе на частотах вращения свыше 5000 мин-1 наблюдались значительные вибрации, которые ухудшали качество обрабатываемой поверхности. Одной из причин возникновения этих
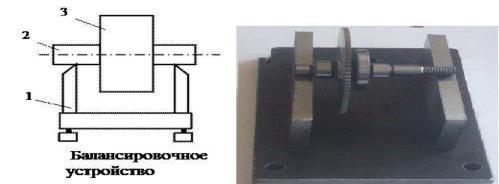
96
вибраций является неуравновешенность инструмента. Балансировка — процесс устранения неуравновешенности.
Существует два вида балансировки : динамическая и статическая.
Динамическая балансировка применяется для устранения неуравновешенности инструмента, имеющего длину L > 0,2D. Для нашего дискового инструмента динамическая балансировка не нужна.
Статическую балансировку рекомендуется проводить при соотношении длины L и диаметра D, равном L/D<0,2 Инструмент имеет центр массы, смещенный относительно оси вращения на какую-то величину. При вращении инструмента с угловой скоростью будет возникать сила инерции . Чтобы ее уравновесить, необходимо создать силу 2, равную силе инерции и направленную в противоположную сторону. Это достигается установкой в плоскости действия силы 2 противовеса на определенное расстоянии от оси вращения.Промышленность выпускает балансировочные устройства для серийных станков. Но для использованных в нашем случае фрез такие устройства не подходят. Поэтому было принято решение о разработке и изготовлении специального балансировочного устройства.
Были разработаны сборочные чертежи устройства и чертежи деталей. Устройство для статической балансировки включает две призмы (1).
Опорные кромки призм выставляют строго горизонтально и на одинаковой высоте. На призмы устанавливается оправка (2) с балансируемым инструментом (3).
а) б) Рис. 1. Устройство для балансировки. а) схема; б) общий вид
Это устройство для статической балансировки было изготовлено. Кроме этого была разработана методика проведения балансировки. Режущий инструмент крепят на оправке так же, как на шпинделе станка. В исходном состоянии оправку кладут на призмы. Под действием статического момента оправка покатится по призмам, и центр тяжести инструмента переместится в нижнюю точку траектории движения, и будет находиться вблизи точки равновесия. На торцовой поверхности инструмента наносят меловую черту 1, проходящую через центр вращения вертикально, которая примерно показывает положение смещенного центра тяжести. Затем оправку с инструментом поворачивают в любую сторону на 90°. На остановившемся инструменте наносят по радиусу инструмента меловую метку 2,
97
указывающую положение центра тяжести.Операцию проводят еще раз, при этом оправку с инструментом устанавливают на призмах так, чтобы метка 2 находилась в горизонтальной плоскости с другой стороны от оси вращения. После затухания колебательных движений оправки положение равновесия отмечают вертикальной меловой меткой 3 .Далее полагают, что смещенный центр тяжести лежит на линии, являющейся биссектрисой угла, заключенного между метками 2 и 3. Эту линию обозначают меткой 4 называют тяжелой меткой, на ней расположен центр тяжести. Противоположная линия от оси вращения оправки называется легкой.Устранение явной статической неуравновешенности инструмента. Для этого оправку ориентируют на призмах так, чтобы метка 4 находилась в горизонтальной плоскости. К легкой стороне инструмента в удобном месте прикрепляют уравновешивающий груз (кусочки пластилина) такой величины, при котором на оправку с инструментом перестает действовать статический момент. Величину уравновешивающего груза подбирается опытным путем при многократном повторении опыта.
Работа выполнена под руководством профессор. каф «Металлорежущие станки и инструменты» А.В. Хандожко
Н.А. Мехедов ПРИМЕНЕНИЕ МЕТОДА ДВУХ СИСТЕМ КООРДИНАТ,
СВЯЗЫВАЕМЫХ С КАЖДЫМ ЗВЕНОМ МАНИПУЛЯЦИОННЫХ СИСТЕМ РОБОТОВ
Объект исследования: манипуляционные системы роботов. Результаты, полученные автором: проведено исследование метода
двух систем координат, связываемых с каждым звеном манипуляционных систем роботов.
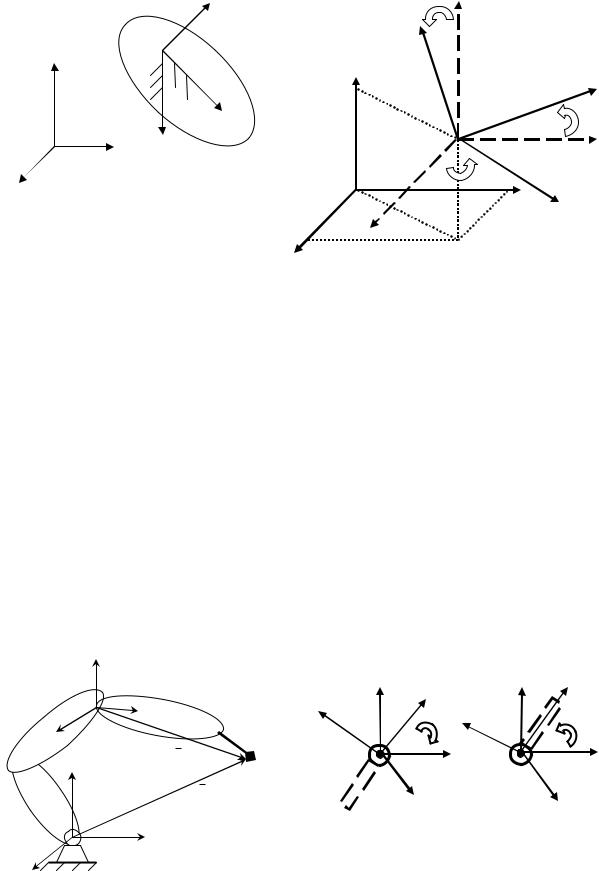
|
|
|
|
98 |
|
|
|
|
Zi |
γ |
|
|
Si |
|
Zi |
|
|
|
|
|
|
||
Z0 |
|
|
|
Z0 |
Yi |
|
|
|
|||
|
|
|
Yi |
β |
|
S0 |
Xi |
|
|
||
|
|
||||
|
|
|
|
||
X0 |
Y0 |
|
|
|
α |
|
|
|
|
||
|
|
|
Zi(0 |
Xi |
|
|
|
|
|
Y0 |
|
Рис. 1 Положение тела в |
|
X(0) |
|||
|
i |
||||
пространстве |
Yi(0) |
|
|||
|
|
|
|
X0 |
|
Для определения положения |
Рис. 2. Линейные и угловые |
||||
твёрдого тела в |
пространстве |
координаты |
|||
необходимо |
указать |
6 координат |
|
|
|
этого тела. |
Это 3 прямоугольные |
|
|
(линейные) координаты любой точки тела и 3- угловые координаты, отражающие ориентацию тела в пространстве. Для этого с телом достаточно связать одну систему координат и определять положение этого тела по координатам начала (Xi(0), Yi(0), Zi(0)), связанной с телом системы координат Si, в базовой (неподвижной) системе координат S0 и трём углам между соответствующими осями базовой и связанной систем координат (рис. 1). Например, такими углами могут быть выбраны углы α, β и γ, соответствующие углам между осями Xi и X0, Yi иY0, Zi и Z0 (рис.2).
Для определения положения многозвенных систем с последовательной структурой используют различные способы связывания систем координат с звеньями (телами) таких систем (рис. 3). В робототехнике наибольшее распространение получил метод Денавита-Хартенберга, названный по именам американских учёных, и детально изложенный в литературе.
Sn
М
rM(n)
S0 rM(0)
Рис.3 Положение многозвенной системы
|
|
X(i-1)* |
|
(i +1)X(i+1) |
Y(i-1)* |
|
qi |
Y(i+1) |
q(i+1) |
|
|
|
|
|
|
|
|
|
Xi* |
|
|
|
|
|
(i -1) |
|
(i) |
Xi |
|
|
Zi*, |
|||
Z(i-1)*, Zi |
|
Рис. 4. Связываемые системы
координат Si(Xi,Yi,Zi) и Si*(Xi*,Yi*,Zi*)
99
В данной работе предложено использовать метод, основанный на использовании двух систем координат, связываемых с каждым звеном манипуляционной системы робота (рис. 4).
Данный метод имеет следующие преимущества:
1. Возможность фиксирования исходной конфигурации манипуляционной системы робота. Это достигается совмещением систем координат S(i-1)* и Si в исходном положении. Реализуется матрицами преобразования однородных координат A(i–1)*,i, i = 1…n при qi=0
|
|
|
cos(βiqi ) |
sin(βiqi ) |
0 |
0 |
|
|
|
A |
|
|
sin(β q ) |
cos(β q ) |
0 |
0 |
|
|
|
* |
|
|
i i |
i i |
1 |
(1 β |
)q |
. |
|
(i 1) |
|
,i |
|
0 |
0 |
|
|||
|
|
|
|
|
|
|
i |
i |
|
|
|
|
0 |
0 |
0 |
1 |
|
||
|
|
|
|
|
|
2. Позволяет разделить параметры описывающие геометрию звеньев манипуляционных систем (неизменяющиеся параметры) и обобщённые координаты (изменяющиеся параметры), отражающие текущую конфигурацию. Неизменяющиеся геометрические параметры (например, длины звеньев) составляют матрицы Ai,i*
|
cos(Xi ,Xi* ) |
cos(Xi ,Yi* ) |
cos(Xi ,Zi* ) |
lxi |
||||||||||||
A |
cos(Y |
|
,X |
* ) |
cos(Y |
|
,Y |
* ) |
cos(Y ,Z |
* ) |
l |
|
|
|||
* |
i |
i |
* ) |
i |
i |
* ) |
i |
i |
* ) |
l |
yi , |
|||||
i,i |
cos(Z |
i |
,X |
cos(Z |
i |
,Y |
cos(Z |
i |
,Z |
zi |
|
|||||
|
|
|
i |
|
|
i |
|
|
i |
|
|
|
||||
|
0 |
|
0 |
|
|
0 |
|
|
1 |
|||||||
|
|
|
|
|
|
|
|
где cos(Xi,Xi*) и т.д. – косинусы углов между соответствующими осями координат; lxi, lyi, lzi – координаты начала системы Si* в системе Si.
Геометрическая (математическая) модель манипуляционной системы роботов может быть представлена преобразованиями однородных координат
A(i–1),i = A(i–1), (i–1)* A(i–1)*,i,
|
k |
A0,k A0,1A1,2...A(i 1),i Ai,(i 1)...A(k 1),k |
A(i 1),i . |
|
i 1 |
Работа выполнена по руководством доц. каф. АТП БГТУ О.Н. Крахмалева
В.С. Милехин, А.В. Степанов, М. Н. Гриневич РАЗРАБОТКА И ИЗГОТОВЛЕНИЕ РОБОТА ДВИЖУЩЕГОСЯ ПО
ЗАДАННОЙ ЛИНИИ
Объект исследования: робот с автономным типом управления (перемещающийся строго по заданной линии).
Результаты, полученные исследовательской группой: разработана и собрана принципиальная схема робота движущегося по затемненной линии.
В настоящее время большое внимание уделяется разработке мобильных машин с высокой приспособляемостью к движению по сложным
100
траекториям и сложным поверхностям, а также разработка модели «искусственного интеллекта». Возрастает потребность в устройствах, которые могут работать без участия человека, оперативно реагируя на изменяющиеся условия внешней среды. Сегодня можно выделить четыре области, где такие устройства могут быть широко востребованы:
Во-первых, это работа на других планетах и исследование труднодоступных мест на Земле, там, где человек не может находиться долгое время из-за природных опасностей и сурового климата. Здесь устройства должны действовать полностью автономно. Часто управление с Земли невозможно, так как время прохождения сигнала очень велико. Вовторых, автоматизация рутинных работ. Например, транспорт, передвигающийся по стандартному маршруту и выполняющий стандартные действия, может работать без участия человека в автоматическом режиме. Это обеспечивает более надежную и безопасную работу, удешевляет эксплуатацию, повышает эффективность работы и позволяет человеку заняться творческой работой. В-третьих, автоматизация опасных для человека и животных работ. Например, такие роботы могут использоваться для разминирования, разведки, осмотра опасных мест и предметов. В- четвертых, создание автоматизированных устройств, облегчающих работу человека. Когда оператор должен одновременно реагировать на очень большое число быстро изменяющихся параметров среды, ему очень сложно быстро принять правильное решение.
Разработанный нами робот является устройством среднего уровня сложности, но может быстро и достаточно точно передвигаться по темной линии, нанесенной на светлую поверхность. В отличие от других роботов данного типа он содержит значительно большее число элементов, однако выполнен на обычных цифровых логических микросхемах, не требует процедуры программирования и поэтому может оказаться более доступным для повторения начинающими радиолюбителями.
Робот передвигается с помощью двух электродвигателей и постоянно удерживается на линии или рядом с ней. Он снабжен тремя датчиками, определяющими его положение относительно линии, а также элементом памяти, который запоминает информацию о том, в какую сторону произошел съезд. Поэтому, если робот сходит с линии, он быстро возвращается обратно. Центральный датчик собран на светодиоде и фототранзисторе, которые вместе образуют оптопару с открытым оптическим каналом. Левый и правый датчики спроектированы аналогичным образом. Каждый из светодиодов освещает определенный участок поверхности под роботом, а соответствующий фототранзистор принимает отраженный свет. Яркость свечения светодиодов можно регулировать подстроечным резистором, что в свою очередь повлияет на эксплуатационные условия
На коллекторах фототранзисторов напряжение зависит от их освещенности. Когда датчик расположен над линией, от нее отражается незначительная часть светового потока, освещенность фототранзистора мала и на его коллекторе будет напряжение высокого логического уровня. Если