
Сборник 70 студ конференции БГТУ
.pdf151
Нано двуокись кремния.
Наноразмнрный оксид кремния имеет очень большую удельную поверхность. Материал имеет ненасыщенную структуру алкильного типа с различными типами связей. Свойства систем, включающих добавку нано оксида кремния, будут существенна отличаться от тех. же систем, содержащих обычный микронный оксид кремния. По этой причине нано оксид кремнии может широко применяются во многих отраслях промышленности. NSilica-01 и NSilica-02 имеет большую удельную поверхность. Другие продукты этого ряда (от NSilica-U 3 до NSilica-08) отличаются различными методами обработки поверхности порошка.
Нанопорошки соединений магния.
Нано оксид, карбонат и гидроокись магния: белые порошоки, не имеющие запаха, не токсичные. Обладают уникальными свойствами. Могут широко использоваться в электронике, как катализаторы, в керамике, в нефтеперерабатывающей и в текстильной промышленностях, в производстве огнезащитной добавки высокоэффективного типа, для и производства технических тканей.
Все это открывает перспективу эффективного использования субмикронных порошков медных сплавов для продления срока эксплуатации машин и механизмов.
Работа выполнена под руководством доц.каф."Технология машиностроения" Фролова Е.Н. и доц.каф. "Технология машиностроения" Надуваев В.В.
А.Ю. Добрин, К.Н. Пушкарев ТЕХНОЛОГИЧЕСКОЕ ОБЕСПЕЧЕНИЕ ПАРАМЕТРОВ КАЧЕСТВА ФУНКЦИОНАЛЬНЫХ ПОВЕРХНОСТЕЙ ДЕТАЛЕЙ МАШИН ДЛЯ ДОСТИЖЕНИЯ ТРЕБУЕМЫХ ПОКАЗАТЕЛЕЙ НАДЕЖНОСТИ ПРИ РАЗЛИЧНЫХ СОЧЕТАНИЯХ ЭКСПЛУАТАЦИОННЫХ СВОЙСТВ
Объект исследования: рабочие поверхности деталей машин. Результаты, полученные лично автором: разработана подсистема
интегрированной САПР для решения задачи анализа эксплуатационных свойств для обеспечения требуемой долговечности рабочей поверхности.
Эксплуатационные свойства деталей и их соединений определяют основной показатель качества машин – надежность.
Важнейшие эксплуатационные характеристики деталей машин в значительной мере зависят от состояния их поверхностного слоя. Для успешного решения задачи повышения качества машин необходимо рассмотреть теоретические аспекты влияния параметров состояния поверхностного слоя деталей на их эксплуатационные свойства.
Износостойкость является важнейшей эксплуатационной характеристикой деталей машин. Для большинства машин основной

152
причиной отказов является достижение предельно допустимого уровня износа их деталей. Износостойкость в значительной мере зависит от состояния их поверхностного слоя, определяемого параметрами механической обработки при изготовлении.
Некоторые виды основных эксплуатационных свойств деталей машин: Износостойкость определяет способность поверхностных слоев деталей
сопротивляться разрушению. Износ является причиной выхода из строя подавляющего большинства машин (до 80%) и их деталей.
Исследования О.А. Горленко по износостойкости плоских поверхностей производились применительно к направляющим станков. Исследуемая поверхность трения образцов обрабатывалась разными методами и с различной шероховатостью. По результатам экспериментальных исследований строились кривые линейного износа образцов, которые с достаточной точностью аппроксимируются степенной функцией
где S - путь трения, км; α, β - параметры кривой начального износа. Результаты анализа показали, что 70—80% всей вариации показателей
износостойкости связаны с параметрами шероховатости.
Контактная жесткость определяет способность поверхностных слоев деталей, находящихся в контакте, сопротивляться действию сил, стремящихся их деформировать. Она оказывает влияние на качество машиностроительных изделий. Контактная жесткость в значительной степени зависит от качества поверхности сопрягаемых деталей и, следовательно, от технологии их изготовления.
Экспериментальные исследования по установлению связи контактной жесткости плоских стыков с характеристиками качества сопрягаемых поверхностей проводились на образцах из серого чугуна и стали.
Контактные перемещения образцов измерялись как при взаимно параллельном, так и при взаимно перпендикулярном расположении следов обработки на сопрягаемых поверхностях. Цикл нагрузки и разгрузки образцов без их взаимного смещения повторялся десятикратно.
Изменение взаимного расположения следов обработки на контактирующих поверхностях с параллельного на перпендикулярное ведет к перераспределению значимости влияния отдельных характеристик качества этих поверхностей на контактную жесткость. Если при взаимно параллельном расположении следов обработки на сопрягаемых поверхностях наибольший процент варьирования жесткости связан с высотными характеристиками то при взаимно перпендикулярном расположении следов обработки наибольшее влияние на контактную жесткость оказывает поперечный радиус микронеровностей.
Проведенный корреляционный анализ показал, что между характеристиками качества сопрягаемых плоских поверхностей и их контактной жесткостью существует тесная связь.
Коррозийная стойкость. Одним из важнейших эксплуатационных свойств деталей машин является их коррозионная стойкость.

153
Для экспериментального исследования были изготовлены специальные образцы в виде колец из стали, наружная поверхность которых обрабатывалась различными методами с разной шероховатостью и степенью наклепа.
Для количественной оценки коррозии образцов использовался метод измерение потери в весе прокорродированного металла. Был определен показатель проницаемости
где k — потеря массы за 1 час, г/м2; у — плотность металла. Математическая обработка результатов показала, что 37% вариации
коррозии объясняется изменением характеристик качества поверхности, введенных в анализ.
Анализ результатов экспериментальных исследований убедительно показывает, что обработка деталей машин ППД приводит к снижению их коррозионной стойкости.
Разработана методика количественной оценки изменения эксплуатационных свойств деталей машин в зависимости от комплекса параметров поверхностного слоя при различных методах лезвийной, алмазно-абразивной и отделочно-упрочняющей обработок.
Работа выполнена под руководством зав. каф. "Технология машиностроения", к.т.н., доц. Е.А. Польского
Е.Б. Дружбина ТЕХНОЛОГИЧЕСКОЕ ОБЕСПЕЧЕНИЕ ЭКСПЛУАТАЦИОННЫХ
СВОЙСТВ ДЕТАЛЕЙ УПЛОТНИТЕЛЬНЫХ ЭЛЕМЕНТОВ ТУРБИН
Объект исследования: детали узлов уплотнительных элементов узлов свободных турбин, работающие в условиях линейного износа, подлежащие изготовлению на ремонтных предприятиях ОАО «Газэнергосервис».
Результаты, полученные лично автором: разработан научный подход к нормированию параметров качества и точности рабочих поверхностей деталей уплотнительных элементов узлов свободных турбин, для обеспечения требуемых показателей надежности сборочных узлов для заданных условий эксплуатации.
Износ детали, являющейся ползуном в сопряжении, в соответствие с эпюрой давлений, можно представить
U2 k2 p(l)Vt,
где p(l) – закон распределения давлений по контактирующим поверхностям. После учета распределения давления при интегрировании суммарный
износ в соединении составит

154
|
|
|
P |
12 |
|
|
12 y |
|
|
|
l2 |
|
P |
12 |
|
|
12 y |
|
|
||||||
|
|
|
x |
|
|
|
|
|
x |
|
|
||||||||||||||
U U |
2 |
k |
|
1 |
|
|
x |
|
|
y Vt k |
s |
(x l) |
|
1 |
|
|
l |
|
|
y dl |
|
||||
|
|
2 |
|
|
2 |
|
|
2 |
|
|
2 |
|
|||||||||||||
1 |
1 |
|
|
b |
|
|
a |
|
2 |
|
|
|
|
b |
|
|
a |
|
|
||||||
|
|
|
ab |
|
|
|
|
|
|
|
l |
|
ab |
|
|
|
|
|
. |
||||||
|
|
|
|
|
|
|
|
|
|
|
|
|
|
1 |
|
|
|
|
|
|
|
|
|
|
|
|
|
|
|
|
|
|
|
|
|
|
|
|
|
|
|
|
|
|
|
|
|
|
|
|
Из зависимостей видно, что ползун имеет линейную зависимость износа поверхности, а направляющая деталь – нелинейную. Кроме этого на изнашивание ползуна будет большое влияние оказывать функция φ(x) определяющая допуск отклонения от правильной геометрической формы контактирующих поверхностей.
В ряде случаев выходной параметр удается представить в виде трех независимых составляющих:
|
zj (t) 0 f1 g1(t),g2(t),...,gi (t) h t (t) |
|
|
|
||
где: |
0 |
- случайная |
величина, оценивающая начальное качество; |
f |
- |
|
|
1 |
|||||
неслучайная функция |
возмущений; h t и |
(t) - случайные функции, |
оценивающие соответственно влияние медленно протекающих процессов и внезапных случайных флуктуаций параметра.
Пусть z – выходной параметр, полностью определяющий работоспособность объекта. Тогда вероятность безотказной работы в течение наработки T можно трактовать, как вероятность того, что за время T параметр z не выходит за допустимые пределы R1 и R2, т.е.:
P(t) P R1 z R2 T
Вероятность безотказной работы:
T |
T R2 |
(z/t) |
|
|
P(T) 1 q(t)dt 1 |
dzdt |
|||
|
||||
0 |
0 R |
t |
||
|
1 |
|
|
Поведение такого объекта характеризуется постепенными отказами.
Если граница R(t) - случайный процесс с плотностью вероятности 1(R/t),
обычно вводят новую переменную R z. При независимости границы R и выходного параметра, плотность вероятности новой переменной:
( /t) (z/t) 1 z/t dz
Вероятность безотказной работы:
T |
/t |
|
|
P(T) P 0/t T 1 |
d dt |
||
|
|||
0 0 |
t |
||
В ряде случаев, когда отказ в форме выхода параметра состояния за |
определенную границу (выброс) не приводит к значительным отрицательным последствиями, регламентироваться может параметр потока отказов . При
известной плотности совместного распределения параметра состояния z(t) и
скорости его изменения во времени v(t) усредненный параметр потока отказов, определяющий число выбросов за границы в единицу времени:
|
|
|
1 |
T |
|
0 |
|
|
|
|
|
|
(R ,v/t)vdv |
|
R ,v/t vdv dt |
||
|
|
|||||||
|
|
|
T |
2 |
1 |
|
||
|
|
|
0 0 |
|
|
|
155
Таким образом, решение задачи оптимального распределения величины допуска на эксплуатационные звенья сборочной размерной цепи узла и назначение обоснованных требований по качеству поверхности для обеспечения требуемой надежности возможно при условии определения весовых коэффициентов, устанавливающих значимость влияния того или другого эксплуатационного свойства в элементарном прототипе. Назначение весовых коэффициентов при условии максимальной вероятности безотказной работы контактирующей пары является необходимым условием для разработки автоматизированной подсистемы технологического обеспечения надежности машины на этапах анализа размерных связей при конструкторско-технологической подготовке производства.
Rz |
S2 |
|
cу sуру vzру |
HBmaxn |
txру HBminn t Rzисх |
хру |
|
bсдв(2s bсдв) |
R |
||||
8r |
|
НВn |
j |
|
|
32r |
|||||||
|
|
|
|
|
|
|
zв.p |
||||||
|
|
|
|
|
|
ср |
спид |
|
|
|
|
|
|
Ra |
4 S2 32 r cу |
sуру vzру |
HBmaxn |
txру HBminn |
|
t Rzисх хру bсдв(2s bсдв) 32 Rzв.p |
|||||||
|
|
|
|
|
|
160 r НВсрn |
jспид |
|
|||||
|
|
|
|
|
|
|
|
|
По рассчитанной подаче для чистового точения, возможно выбрать необходимый инструмент:
-рассматриваются возможные варианты державки резца и способ ее установки в резцедержатель;
-рассматриваются возможные варианты закрепления пластин и тип выполняемой операции;
-выбирается режущая пластина: форма, размер, геометрия, область применения, марка сплава;
-выбираются (назначаются) оптимальные режимы резания, при которых резец обеспечивает заданные параметры качества поверхности.
Работа выполнена под руководством зав. каф. "Технология машиностроения", к.т.н., доц. Е.А. Польского
И.Ю. Еремин РАЗРАБОТКА АВТОМАТИЗИРОВАННОЙ ПОДСИСТЕМЫ РАСЧЕТА
ПОГРЕШНОСТИ ОБРАБОТКИ, ВЫЗВАННОЙ НЕТОЧНОСТЬЮ РАЗМЕРНОЙ НАСТРОЙКИ СТАНКА
Объект исследования: этап технологической подготовки производства по расчету элементарных составляющих суммарной погрешности обработки деталей машин.
Результаты, полученные лично автором: разработан программный модуль автоматизированной подсистемы расчета погрешности обработки, вызванной неточностью размерной настройки станка.
В условиях рыночной экономики и активной конкуренции особую остроту для машиностроительных заводов приобретает проблема регулярного обновления продукции, выпуска новых модификаций уже разработанных изделий с тем, чтобы удовлетворить запросы максимального

156
числа потребителей. Прежде чем выпустить новую конкурентоспособную продукцию, необходимо провести большую работу по сбору, накоплению и оперативной обработке информации. Переработка больших объемов информации в настоящее время невозможна без использования ЭВМ.
Область применения систем автоматизированного проектирования (САПР) охватывает сегодня самые различные виды деятельности человека — от расстановки мебели в квартире до проектирования и изготовления интегральных микросхем и современной космической техники. Каждая категория задач технического черчения предъявляет к этим продуктам свои требования, однако наибольшее распространение они получили в машиностроении и архитектуре.
В данном исследовании рассмотрена задача автоматизации расчета составляющей суммарной погрешности обработки, вызванной неточностью размерной настройки станка.
Суммарную погрешность обработки деталей на настроенных станках для диаметральных размеров (чистовое растачивание отверстий) определяют по уравнению:
|
2 |
2 |
2 |
|
2 |
|
|
|
2 |
|
|
|
т |
2 |
, |
|
|
у |
н |
|
1,73 и |
|
1,73 |
ст |
|
1,73 |
|
|
|||||
где У – |
погрешность обработки, вызванная упругими деформациями |
|||||||||||||||
технологической системы под влиянием силы резания; |
Н – |
погрешность |
||||||||||||||
настройки |
станка; |
И |
– |
погрешность, |
вызванная |
размерным |
износом |
|||||||||
инструмента; |
СТ – погрешность, вызванная геометрическими неточностями |
|||||||||||||||
станка; |
Т – погрешность обработки, вызванная температурными |
|||||||||||||||
деформациями технологической системы. |
|
|
|
|
|
|
|
|
|
Таким образом, необходимо определить значения всех элементарных погрешностей.
Под наладкой (настройкой) технологической системы понимают приведение ее в рабочее состояние, пригодное для использования при выполнении технологической операции. Наладка в общем случае включает согласованную установку режущего инструмента, рабочих органов станка, приспособления в положение, которое обеспечивает получение заданного размера с установленным допуском на изготовление. Эти элементы наладки часто называют настройкой технологической системы станка на размер. Кроме этих элементов в наладку входит установка заданного режима обработки путем смены шестерён, установка инструмента в инструментальные магазины и револьверные головки станков, установка программоносителя в считывающее устройство станков с ЧПУ и другие работы.
Взаимное положение элементов технологической системы определяется «установочным размером». При каждом регулировании системы или смене инструмента невозможно обеспечить одно и то же его положение. Поле рассеяния положений инструмента при наладке называют погрешностью наладки станка на размер и обозначают Η. Ориентировочно погрешность
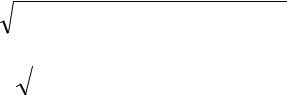
157
наладки можно принять равной разности между предельными значениями
установочного размера. |
|
|
Точно значения Η определяются расчетом. В общем случае |
Η зависит |
|
от погрешности регулирования |
Р положения инструмента |
(по лимбу, |
эталону, жесткому упору и т.п.) |
и погрешности измерения размера детали |
ИЗМ.
Для поверхностей вращения с учетом того, что Η и Р относятся к радиусу, ИЗМ – к диаметру, получим:
H |
|
(KP P)2 (KИ ( ИЗМ / 2))2, |
||
для плоских поверхностей |
|
|
|
|
|
|
|
|
|
H |
|
|
(K P P )2 (K И ИЗМ )2 , |
где КР и КИ – коэффициенты, учитывающие отклонение закона распределения элементарных величин Р и ИЗМ от нормального закона распределения
При использовании автоматизированной системы расчета погрешности настройки станка на размер необходимо выполнять следующие требования:
при открытии программы в главном меню ввести исходные данные. Все поля являются обязательными;
необходимо выбрать данные из предложенных в форме «Метод регулирования»;
для расчета погрешности нажать кнопку «Расчет»;
для представления данных в Microsoft Office Word необходимо нажать кнопку «Отчет»;
для выхода из программы необходимо нажать кнопку «Выход».
Разработанная автоматизированная система расчета составляющей суммарной погрешности обработки, вызванной неточностью размерной настройки станка проста и легка в применении. Полученные результаты при выполнении данных исследований весьма актуальны. Автоматизированная система значительно ускоряет работу инженеров технологических отделов машиностроительных предприятий.
Работа выполнена под руководством доц. каф. «Технология машиностроения» Е.А. Польского, С.В. Сорокина
В.А. Камшуков, Г.Н.Мелков ФОРМИРОВАНИЕ ШЕРОХОВАТОСТИ ПЛОСКИХ ПОВЕРХНОСТЕЙТ ДЕТАЛЕЙ МАШИН АЛМАЗНЫМ
ВЫГЛАЖИВАНИЕМ
Объект исследований: обработка плоских поверхностей деталей алмазным выглаживанием
Результаты, полученные лично автором: физико-статистические модели формирования параметров шероховатости .
158
Исследовались возможности технологических систем (ТС) формирования параметров шероховатости плоских поверхностей деталей машин из чугуна СЧ20 с применением инструмента из поликристаллических сверхтвёрдых материалов (АСПК).
Цель исследованийпостроение имитационных моделей формирования параметров в зависимости от условий обработки методом активного многофакторного эксперимента.
В качестве факторов рассматривались как условия предварительной обработки: подача X1 - Sz фрез, скорость X2 - Vфрез, взаимодействие факторов X6 - Sz фрез Vфрез – для предварительного торцевого фрезерования композитом 10, Raисх – шероховатость поверхности после предварительного плоского шлифования периферией абразивного круга; так и режимы АВ – сила выглаживания X3 - Q, подача на индентор X4 - Sz, скорость выглаживания X5 – V, взаимодействие, характеризующее мощность воздействия индентора на поверхность в процессе выглаживания X7 - Q V (X7). Проведение экспериментов с целью построения имитационных моделей формирования параметров качества в ТС "торцевое фрезерование композитом 10 – АВ" осуществлялось при уровнях факторов: Sz фрез = (0,05 – 0,25) мм/зуб; Vфрез = (311 – 622) м/мин; Q = (50 – 150) н; Sz = (0,025 – 0,16) (мм/об); V = (35 – 90) (м/мин). При исследовании технологической управляемости параметрами качества АВ" режимы шлифования выбирались для обеспечения шероховатости Raисх = (0,16 – 0,6) (мкм).
АВ осуществлялось на фрезерном станке FQW-400 с системой управления CNC-Н646 как представителе фрезерных станков с компьютерными системами ЧПУ.
На основе результатов экспериментов построены имитационные модели формирования ряда параметров шероховатости плоских поверхностей деталей из чугуна при указанных условиях: Ra, Rz, Rmax, Rp, Sm, , b, , .
В общем случае имитационные модели формирования параметров шероховатости в ТС АВ плоских поверхностей деталей имеют вид:
а) в случае предварительного торцевого фрезерования:
Yi i0 Sziфрез1 Vфрезi2 Q i3 SziАВ4 VАВi5 Szфрез Vфрез i6 Q V i7 ;
б) в случае предварительного шлифования периферией абразивного круга:
Y |
i0 |
Ra i1 |
Q i2 |
S i3 |
V i4 , |
i |
исх |
|
z |
|
где Yi – элемент множества Yi = {Ra, Rz, Rmax, Rp, Sm, , b, , }; i… –
параметры модели. Так, модель формирования параметра Rp ТС "торцевое фрезерование композитом 10 – АВ" имеет вид:
0,002 0,15 0,49 0,21 0,04 0,51 0,06
Rp 6,67 Szфрез Vфрез Q SzАВ VАВ Szфрез Vфрез Q V
Анализ значений критериев Кохрена, Стьюдента и Фишера показывает, что дисперсии в опытах плана эксперимента однородны, большинство факторов статистически значимы, а модели адекватны экспериментальным данным. Анализ Парето показал высокую согласованность влияния
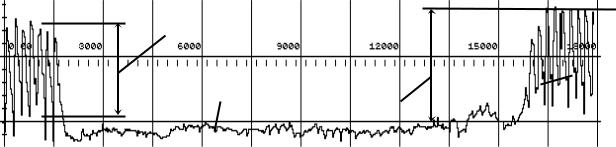
159
взаимодействия X6 = Sz фрез Vфрез на формирование подавляющего большинства рассматриваемых параметров качества поверхности. К основным рычагам "технологического управления" качества следует отнести
факторы X6 – Sz фрез Vфрез, X3 – Q, X4 – Sz, X7 – Q V.Помимо параметров шероховатости строились имитационные модели величины остаточной
деформации поверхности H в направлении действия силы обработки Z, которая должна учитываться при проведении точностных технологических расчётов. Её величина определялась по профилограммам (см.рис.).Установлено, что в ряде случаев остаточные деформации обработанных поверхностей H превышают максимальную величину неровностей Rmax после предварительной обработки фрезерованием. Этот факт можно объяснить уплотнением поверхностных слоёв материала за счёт вытеснения из глубинных слоёв на поверхность свободного графита при увеличении Q.
Sz фрез = 0,25 мм / зуб; Vфрез = 622 м / мин; Raфр = 11,5 мкм
|
Rmaxфр |
|
|
|
|
|
|
|
|
|
|
|
|
|
|
|
|
|
|
|
|
|
|
|
|
|
|
Raфр |
|
|
|
RaАВ |
|
|
|
||||
H |
|
|
|||||||
|
|
|
|
|
|
|
|
|
|
|
|
|
|
|
|
|
|
|
|
|
|
|
|
|
|
|
|
|
|
Q = 150 н; Sz = 0,025 мм / об; V = 35,2 м / мин; RaАВ = 1 мкм; |
H = 65,4 мкм |
Рис. Типовая профилограмма для определения остаточной деформации поверхности детали из чугуна в ТС "торцевое фрезерования композитом 10 – АВ"
Работа выполнена под руководством проф .каф."Технология машиностроения" В.П. Федорова и доц .каф."Металловедение и машиностроение" Е.В. Ковалевой
Ковалев А.Г., Васильева Д.Е. НАДЁЖНОСТЬ ТЕХНОЛОГИЧЕСКОГО ОБЕСПЕЧЕНИЯ
ПАРАМЕТРОВ ШЕРОХОВАТОСТИ ПОВЕРХНОСТЕЙ ДЕТАЛЕЙ МАШИН
Объект исследования: технологические системы механообработки. Результаты, полученные лично автором: количественные показатели
надёжности технологического обеспечения параметров надёжности и типовая форма их представления.
Известно, что параметры шероховатости (ПШ) оказывают одно из решающих влияний на процессы контактного взаимодействия поверхностей деталей, от которого зависят показатели эксплуатационных свойств (ПЭС) соединений. Это определяет актуальность решения проблемы технологического обеспечения требуемых ПШ. которое достигается путём
160
решения ряда специальных задач, имеющих самостоятельное прикладное значение, назначение и краткое содержание которых можно охарактеризовать следующим образом.
1. Получение количественных моделей формирования параметров шероховатости при обработке в различных технологических системах (ТС) в зависимости от условий обработки с учётом технологической наследственности.
2. Решение задачи определения вероятности выполнения задания ТС по параметрам качества, в том числе по ПШ, то есть задача определения параметрической надёжности ТС (ПНТС). Эта общая задача для всех параметров качества (ПК) обрабатываемых поверхностей, так как они являются случайными величинами.
3.Технологическое обеспечение закономерного изменения ПШ поверхностей деталей. Необходимость решения этой задачи обусловлена тем, что практически в большинстве случаев имеют место нестационарные условия эксплуатации, характеризующиеся неравномерным распределением нагрузок, скоростей относительного скольжения и других возмущающих воздействий по контактирующим поверхностям трибоэлементов.
4.Решение частных задач по исследованию физических процессов отдельных ТС с целью повышения качества обрабатываемых поверхностей. К ним прежде всего относятся: исследование динамики и технологической устойчивости процессов ОУО ППД устройствами упругого действия с получением соответствующих критериев в виде уравнений и номограмм; исследование формирования ПШ в триботехнологических системах с получением соответствующих адекватных имитационных моделей; исследование и физическое моделирование контактирования индентора с обрабатываемой поверхностью в процессе ОУО ППД в зависимости от условий обработки; модернизация морально устаревших, но физически
работоспособных ТС на основе применения современных мехатронных систем ЧПУ.
5. С целью метрологического обеспечения параметров качества, в том числе ПШ, испрльзуется автоматизированная система научных исследований на основе компьютеризации отдельных измерительных модулей.
По результатам расчётов ПНТС (рис.) созданы базы данных по вероятности обеспечения ПШ в заданных интервалах для различных методов обработки.