
Сборник 70 студ конференции БГТУ
.pdf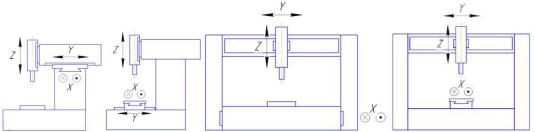
131
Работая над станком на настоящее время достигнуты следующие результаты: приведены в рабочее состояние шаговые двигатели, продольные, поперечные и вертикальные салазки, электрический двигатель, концевые датчики, подсоединены 2 вентилятора, а также была проведена обработка по прямоугольному контуру с применением круговой и линейной интерполяции.
Работа выполнена под руководством зав. каф. «Металлорежущие станки и инструменты» д.т.н., проф. Хандожко А.В.
и доц. каф «Металлорежущие станки и инструменты» Щербакова А.Н.
А.С. Шмат АНАЛИЗ КОМПОНОВОЧНЫХ РЕШЕНИЙ ПРИ ПРОЕКТИРОВАНИИ
ГРАВИРОВАЛЬНО-ФРЕЗЕРНОГО СТАНКА
Объект исследования: Компоновки гравировально-фрезерных станков. Результаты, полученные лично автором: На основании выполненного анализа предложено новое компоновочное решение для разрабатываемого
гравировально-фрезерного станка.
Изучая источники открытой печати, было выявлено четыре основных компоновочных решения гравировально-фрезерных станков. Эти решения можно классифицировать по двум основным критериям: наличие-отсутствие портала; подвижность различных рабочих органов.
Станками с порталом называются станки, имеющие две стойки соединенные балкой (порталом). Все прочие, не подходящие под это описание, являются беспортальными. С точки зрения перемещения рабочих органов компоновки разделяются в зависимости от того, перемещаться ли стол с заготовкой или он статичен.
Рассмотрим компоновки станков.
1.Беспортальная с неподвижным столом. Структурная схема представлена на рисунке 1 а, описывается формулой ОХУZСv.
2.Беспортальная с подвижным столом. Структурная схема представлена на рисунке 1 б, описывается формулой XYOZСv.
3.Портальная с подвижным порталом. Структурная схема представлена на рисунке 1 в, описывается формулой OXYZСv.
4.Портальная с подвижным столом. Структурная схема представлена на рисунке 1 г, описывается формулой XOYZСv.
а) |
б) |
в) |
г) |
Рис. 1. Компоновки гравировально-фрезерных станков: |
|
132
а, б – беспортальные; в, г – портальные Проведем анализ компоновок с точки зрения размеров рабочего
пространства, металлоемкости, жесткости и точности.
Самым большим рабочим пространством обладают портальные компоновки. Благодаря наличию портала, располагающегося на двух стойках, мы получаем большое рабочее поле заготовки. В беспортальных же компоновках, увеличение рабочего пространства заготовки ведет либо к увеличению габаритных размеров станка, либо к увеличению вылета режущего инструмента. В свою очередь это снижает жесткость станка, приводит к увеличению вибраций и снижению точности обработки.
Компоновка станка беспортальная с крестовым столом (рис. 1 б) наиболее экономичная с точки зрения металлоёмкости. Благодаря перемещению стола с заготовкой по двум линейным координатам, требуемая жесткость обеспечивается при малых габаритных размерах. Наиболее затратные портальные компоновки. Из-за наличия крупного основания, двух стоек и портала, на его изготовление потребуется наибольшего количества материала.
Исполнение беспортальное с неподвижным столом (рис.к 1 а) имеет малую жесткость. При максимальном вылете инструмента велика вероятность появления вибраций. Наибольшей жесткостью обладают портальные компоновки, в особенности с неподвижным порталом. Надежно прикреплённый неподвижный портал обладает высокой жесткостью. Стол имеет малые габариты и величины ходов, что также положительно скажется на общей жесткости компоновки.
Погрешности обработки зависят от изменений внешних условий и изменений внутреннего состояния системы. Поэтому точность компоновки можно воспринимать как степень невосприимчивости станка к изменениям этих условий. К внешним условиям можно отнести действие сил резания и веса деталей, а к внутренним - изменениям координат рабочего пространства,
скоторым связано положение подвижных узлов. Противостояние внешним факторам связано с жесткостью конструкции: выше жесткость – выше точность. Следовательно, наиболее точной является компоновка с неподвижным порталом и подвижным столом. Неоднородность рабочего пространства зависит от величины податливостей составляющих узлов станка, что будет определяться конструкцией этих узлов, их жесткостью и точностью.
На основе отличительных особенностей предлагается новое компоновочное решение, представленное на рис. 2. Компоновка портальная,
скрестовым столом и неподвижным порталом, описываемая структурной формулой XYОZСv. Такой вариант при компактных габаритных размерах обладает высокой жесткостью и точностью.
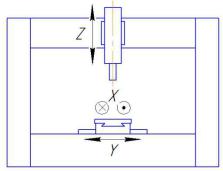
133
Рис. 2. Предлагаемое компоновочное решение гравировальнофрезерного станка
Компоновочное решение легло в основу проектируемого станка, который изготавливается на кафедре «МСиИ» БГТУ.
Работа выполнена под руководством доц. каф. «Металлорежущие станки и инструменты» Л.А. Захарова
ТЕХНОЛОГИЯ МАШИНОСТРОЕНИЯ
Абрамов Р.В, Арутюнян Р.А. НАНОМАТЕРИАЛЫ И НАНОТЕХНОЛОГИИ ДЛЯ
МАШИНОСТРОЕНИЯ
Объект исследования: наноматериалы и нанотехнологии.
Результат, полученный лично автором: проанализировали возможности и достижения в машиностроения.
Наноматериалы - материалы, содержащие структурные элементы, геометрические размеры которых хотя бы в одном измерении не превышают 100 нм, и обладающие качественно новыми свойствами, функциональными и эксплуатационными характеристиками;
Впоследнее время и в России наметились поределённые успехи в практической реализации научных исследований. Так, наноструктурированная продукция инструментального и триботехнического назначения уже сейчас не уступает лучшим зарубежным аналогам.
Вотчете ФЦНТП представлены результаты внедрения в производство ряда изделий с применением НТ, в том числе непосредственно для машиностроения, или которые могут быть применены на предприятиях данной отрасли, в том числе: производство поворотных резцов с наноструктурными кернами для фрезерования асфальтобетонных покрытий дорог, пластов в соле- и угледобыче; пластин режущего инструмента; наноструктурированных гидроштампованных нержавеющих фитингов (крестовины, угольники, переходники). Сортамент-сталь 12X18НЮТ диаметр 6-50 мм, толщина стенки08-2,0 мм.
Заметный прогресс достигнут в области производства ультрадисперсных нанопорошков. Расширяются и области их применения. Так, выпускаемые
134 |
|
концерном «Наноиндустрия» наноразмерные |
порошки на основе |
серпентинитов нашли массовое применение в узлах трения практически всех видов оборудования. Речь идёт о технологии восстановления изношенных узлов и механизмов промышленного оборудования до первоначальных параметров с помощью специальных ремонтно-восстановительных составов (РВС
Эта технология уже используется на таких крупных предприятиях как: в ГУЛ «Мосводоканал», на Московской железной дороге, во ФГУП ММП «Салют», ОАО «Аэроприбор», ОАО «Карчаровский механический завод», на Московском метрополитене, в грузовом аэропорту Шереметьево и др.
Базовые установки и технологии нанесения тонкопленочных (от 10 нм до 50 мкм) наноструктурированных покрытий с использованием высокоскоростного ионноплазменного и вакуумнодугового напыления, разработанные фГУП ВНИИНМАШ имени академика А. А. Бочвара и ООО
«МЭШ плюс», обеспечивают:
•Нанесение многокомпонентных, сложных по составу и структуре материалов, включая наноструктурированные и многослойные покрытия;
•Создание новых материалов в виде покрытий и порошков, включая нанокластерные;
•Снижение стоимости 1 м2 покрытия, нанесенного в вакууме, до стоимости аналогичного покрытия, нанесенного гальваническим путем.
Из данных НМ может быть изготовлена различная уникальная продукция: изделия авиационно-космической техники 5-го поколения, жидкие и твердые смазки для пар трения, суперэффективные химические аккумуляторы для синтеза новых веществ и др. •
Повышение свойств наноструктурированного металла при использовании взамен аналога позволяет:
Снизить расход металла за счёт облегчения массы изделий в связи с
уникальными физикомеханическими свойствами материалов.
Снизить затраты в процессе эксплуатации более легких изделий.
Повысить надежность и срок службы изделий.
Снизить затарты на обработку, например в результате улучшения нггампуемости.
Повысить стойкость инструмента.
Применение объёмных НМ на металлической основе делает возможным инновационное перевооружение промышленности: авиакосмического, энергетического и транспортного машиностроения,
станкоинструмёнтальной,горнодобывающей, медицинскойпромышленности и ТЭК. Ресурс изделий различного назначения, изготовленных по новой технологии, может увеличиться от 200
до 500%.
В машиностроении уже используются технологии и оборудование для изготовления деталей машин с нанометровой точностью, и в этом направлении-продолжаются дальнейшие исследования: электроискровая и
135
электрохимическая обработка, фрезерование, шлифование, полирование, доводка и др.
Большие возможности для машиностроительных отраслей промышленности в области применения НМ и нанопокрытий представляют имеющиеся и будущие разработки износо-, и коррозионностойких и других функциональных нанопокрытий, а также композитов и других материалов, упрочненных наноразмерными материалами, предназначенных для авиа- и ракетно-космической техники.
Работа выполнена под руководством доц. каф. «Технология машиностроения» Е.Н. Фролов, В.В. Надуваев
Р.В. Абрамов. Л.В.Сахаров.
МЕТОДЫ УЛУЧШЕНИЯ КАЧЕСТВА ПОВЕРХНОСТЕЙ ДЕТАЛЕЙ МАШИН
Объект исследования: эксплуатационные свойства деталей машин. Результат, полученный лично автором: проанализировали методы
улучшения качества поверхностей деталей машин.
Основные эксплуатационные свойства деталей машин – износостойкость, прочность, коррозионная устойчивость в значительной мере определяются состоянием их поверхностного слоя. Существует достаточно большое количество различных технологических методов повышения качества поверхностей деталей. Наиболее распространенными из них являются гальванические и химические методы нанесения покрытий, такие как: хромирование, никелирование, цинкование, лужение, кадмирование, латунирование, меднение, оксидирование, свинцевание.
Технологический процесс изготовления деталей с покрытиями обычно включает следующие операции: механическую обработку для получения поверхностей необходимой точности и чистоты, обезжиривание и травление, промывку, осаждение на рабочую поверхность покрытия, термическую обработку. Неблагоприятным с экологической точки зрения является использование в составе электролитов для травления и нанесения покрытий сильных кислот.
Для решения этой проблемы решили использовать для повышения качества поверхности деталей отделочно-упрочняющую обработку поверхностным пластическим деформированием.
Накатывание, обкатывание и раскатывание осуществляют специальным инструментом, рабочими элементами которого являются шарики или ролики от подшипников или специально изготовленные. При давлении рабочего элемента на обрабатываемую поверхность детали происходит ее локальное пластическое деформирование в месте контакта. Наличие различных вращательных и поступательных движений позволяет обрабатывать различные поверхности (плоские, цилиндрические, фасонные). Обработку
136
ведут на универсальных и специальных станках, станках с ЧПУ, полуавтоматах и автоматах.
Выглаживание производят инструментом, рабочим элементом которого является твердосплавный или алмазный индентор, скользящий по обрабатываемой поверхности. Этим методом можно обрабатывать все виды поверхностей от плоской до фасонной.
Виброобработка - это процесс накатывания, обкатывания, раскатывания шариками или алмазное выглаживание при наличии дополнительного осциллирующего движения рабочего элемента параллельно обрабатываемой поверхности. Варьирование амплитуды и частоты осцилляций рабочего элемента, наряду с изменением других режимов обработки, позволяет создавать на поверхности различные регулярные микрорельефы или системы канавок.
Динамическое упрочнение производят рабочими элементами в свободном состоянии или при их фиксированном положении. В качестве рабочих элементов при свободной обработке применяют дробь и шарики, стальные или стеклянные, при фиксированном положении шарики и ролики подшипников или специальные, в зависимости от обрабатываемой поверхности. При свободной динамической обработке рабочие элементы направляются на обрабатываемую поверхность воздушной струёй с помощью специальных устройств под действием центробежных сил или в вибробункерах.
Сегодня наряду с ранее известными технологиями повышения качества деталей машин широко используются физические методы обработки. Одним из таких методов является лазерная обработка, которая обладает высокой эффективностью и гибкостью управления. Лазерный луч отличается высокой плотностью энергии. Быстрый теплоотвод в глубь металла приводит к возникновению закалочных структур в поверхностном слое. Лазерный луч легко проникает в труднодоступные места, включая внутренние поверхности полых валов и отверстий. Происходит упрочнение тонкого поверхностного слоя.
Часто применяют лазерную обработку в комбинации с другими методами, что дает возможность получить качественно новые свойства поверхностного слоя.
Лазерное воздействие на специально нанесенные материалы используется для получения широкого спектра поверхностных покрытий. Они обладают высокими свойствами и создаются различными видами лазерной обработки: термической, глазурованием, аморфизацией, ударным упрочнением, легированием и наплавкой.
Работа выполнена под руководством доц. каф. «Технология машиностроения» Т.А. Моргаленко

137
Н.А. Богинский РАЗРАБОТКА АВТОМАТИЗИРОВАННОЙ ПОДСИСТЕМЫ
РАСЧЕТА ПОГРЕШНОСТИ ОБРАБОТКИ, ВЫЗВАННОЙ УПРУГИМИ ДЕФОРМАЦИЯМИ ТЕХНОЛОГИЧЕСКОЙ СИСТЕМЫ ПОД ВЛИЯНИЕМ СИЛЫ РЕЗАНИЯ
Объект исследования: этап технологической подготовки производства по расчету элементарных составляющих суммарной погрешности обработки деталей машин.
Результаты, полученные лично автором: разработан программный модуль автоматизированной подсистемы расчета погрешности обработки, вызванной упругими деформациями технологической системы под влиянием силы резания.
Очевидно, что прогресс неуклонно движется вперед, помогая создавать все новые и новые технологии, технологические процессы, происходит автоматизация производства. На фоне всего этого очень важную роль приобретают системы САПР, позволяющие ускорить и упростить работу на промышленном предприятии и добиться более высокой производительности труда.
В данном исследовании рассмотрена задача автоматизации расчета суммарной погрешности обработки для трех вариантов получения элементарной поверхности – наружное чистовое точение заготовок.
Математическое обеспечение любых систем автоматизации проектирования (САПР) по назначению и способам реализации делится на две части. Первую составляют математические методы и построенные на их основе математические модели, описывающие объекты проектирования или их части и параметры объектов.
Суммарную погрешность обработки деталей на настроенных станках для диаметральных размеров определяют по уравнению:
|
2 |
2 |
2 |
2 |
|
2 |
|
|
|
2 |
, |
|
у |
н |
1,73 и |
1,73 |
ст |
|
1,73 |
т |
|||
где У – |
погрешность обработки, вызванная упругими деформациями |
||||||||||
технологической системы под влиянием силы резания; |
Н – погрешность |
||||||||||
настройки |
станка; |
И – погрешность, вызванная размерным износом |
|||||||||
инструмента; |
СТ – погрешность, вызванная геометрическими неточностями |
||||||||||
станка; |
Т – погрешность обработки, вызванная температурными |
||||||||||
деформациями технологической системы. |
|
|
|
|
|
|
|||||
Таким образом, |
необходимо определить значения всех элементарных |
погрешностей. Основной сложностью при проведении расчетов является необходимость постоянного анализа эмпирических данных по точности и жесткости оборудования и выбору справочных материалов из большого числа таблиц и графиков.
138
Для разработанной автоматизированной подсистемы математическое обеспечение САПР представлено виде формул и уравнений для расчета погрешность обработки, вызванная упругими деформациями технологической системы под влиянием силы резания для токарной группы металлорежущего оборудования.
Для возможности применения подсистемы для всех видов оборудования
иинструментальных материалов была решена задача преобразования эмпирических справочных таблиц в математические зависимости, обеспечивающие получения адекватных и значимых результатов для различных вариантов исходных данных.
Вкачестве входных данных пользователь подсистемы должен указать
ивыбрать следующие параметры:
длину детали, мм;
диаметр детали, мм;
приведенный диаметр детали, мм;
диаметр поверхности и квалитет точности обработки после выполнения предыдущего перехода;
модель станочного оборудования;
способ установки заготовки;
материал заготовки.
Помимо этого вводятся основные параметры режимов резания (глубина резания, мм, подача, мм/об, скорость резания, м/мин) и параметры режущей части инструмента (главный угол в плане, град).
Подставляя исходные данные (введенные пользователем) и данные, хранящиеся в соответствующих базах данных в математические модели, предназначенные для расчета минимальных и максимальных значений податливости элементов технологической системы и предельных значений нормальных составляющих усилий резания, получаем значение погрешности обработки, вызванной упругими деформациями технологической системы под влиянием силы резания.
При проектировании маршрута обработки элементарной поверхности необходимо дать заключение, для каждого варианта последовательности технологических переходов, о возможности обеспечения требуемой точности. Единственным критерием позволяющим выбрать тот или иной маршрут обработки является сравнение суммарной погрешности обработки с допуском на выполняемый размер. Поэтому проведенная работа и созданная автоматизированная системы весьма актуальна и востребована. Разработанная программа доступна широкому кругу пользователей, но создавалась в первую очередь для технологов, чтобы помочь им при оценке возможности осуществления обработки детали на станке с заданной точностью. Предполагается, что данная автоматизированная система в дальнейшем будет являться частью более крупной САПР, являющейся комплексным решением для большинства технологических задач. Данную работу также можно использовать в качестве методического пособия при
139
создании аналогичных автоматизированных систем технологической подготовки производства.
Работа выполнена под руководством доц. каф. «Технология машиностроения» Е.А. Польского, С.В. Сорокина
Р.В. Бурыченкова РАЗРАБОТКА АВТОМАТИЗИРОВАННОЙ СИСТЕМЫ
ОПРЕДЕЛЕНИЯ ЭКОНОМИЧЕСКИХ ПОКАЗАТЕЛЕЙ ТЕХНОЛОГИЧЕСКОГО ПРОЦЕССА
Объект исследования: этап технологической подготовки производства по определению наиболее рационального варианта технологического процесса механической обработки деталей машин.
Результаты, полученные лично автором: разработан программный модуль автоматизированной системы расчета технико-экономических показателей участков механических и механосборочных цехов.
В условиях перехода к рыночной экономике особенно возросли требования к сокращению сроков разработки технологии (технологических процессов и средств их оснащения) при улучшении ее качества. При осуществлении мероприятий научно-технического прогресса (НТП), к которым относятся разработка и внедрение новой техники, новых технологических процессов, необходимо давать их экономическую оценку.
При проведении экономических расчетов проектировщик выполняет повторяющиеся циклические вычисления. Кроме этого, необходимо анализировать нормативные данные по коэффициентам нормативной загрузки, величине амортизационных отчислений и др., а также проводить оптимизацию числа единиц оборудования и численности работающих по критерию нормативной загрузки. Проведение этих действий, особенно при анализе нескольких вариантов технологического процесса (ТП), приводит к необоснованно высоким потерям времени и значительно увеличивает срок подготовки производства. Поэтому задача автоматизации проведения технико-экономического сравнения вариантов ТП является достаточно актуальной.
Основной задачей рассматриваемой САПР является выбор оптимального варианта технологического процесса (ТП) по результатам технико-экономического анализа на основе критерия оптимальности (минимальной себестоимости обработки, минимальной технологической себестоимости изготовления детали, минимального цикла, максимального использования оборудования по мощности и т.п.).
Главными пользователями данного объекта проектирования являются инженеры отдела главного технолога (ОГТ), которые смогут использовать разрабатываемую САПР для оценки эффективности новых ТП и обоснованности предлагаемого варианта. Помимо ОГТ данная система
140
может широко использоваться в экономических отделах и службах предприятий.
Разрабатываемая система позволяет решать как прямую задачу, так и обратную.
Прямая задача состоит в определении технико-экономических показателей проектируемого участка на основе входных данных и последовательного выполнения всех процедур программы.
Обратная задача состоит в определении допустимых затрат с целью их окупаемости в заданные сроки.
Входными данными являются:
наименование и обозначение детали;
годовая программа выпуска;
материал и масса детали;
число смен работы;
ТП: базовый, проектный;
вид и масса заготовки.
Для расчета технико-экономических показателей проектируемого участка в системе осуществляется последовательное выполнение следующих процедур:
использования действительного фонда времени работы оборудования;
расчета основной заработной платы производственных рабочих;
расчета капитальных вложений в технологическое оборудование;
расчета капитальных вложений во все виды используемых основных фондов;
расчета штата основных производственных рабочих и фонда оплаты их труда;
формирования сметы общехозяйственных расходов;
составления калькуляции себестоимости изготовления детали;
расчета организационно-экономических показателей спроектированного участка.
После отработки выше перечисленных процедур производится вывод результатов расчета технико-экономических показателей участка на экран. Далее осуществляется формирование отчета – результаты проделанной работы сохраняются в приложении Microsoft Office Word или же отправлены на печать.
Необходимая информация хранится в таблицах базы данных и при необходимости может быть скорректирована в используемой среде Microsoft Office Access.
При разработке автоматизированной системы были использованы математические выражения и зависимости, на основе которых осуществляется работа всех процедур программы.
Вкачестве специального ПО при разработке автоматизированной системы расчета технико-экономических показателей участка была выбрана