
Сборник 70 студ конференции БГТУ
.pdf11
находясь за рулем автомобиля, следует эти факторы отслеживать и не рисковать собственной жизнью и здоровьем. Особенно это относится к случаям чрезмерной торопливости.
Для нас очевидно, что проблемы пешеходов невозможно решить в отрыве от транспортных проблем в целом, однако подход к их решению должен основываться на равенстве прав участников дорожного движения - и водителей и пешеходов на безопасное и, по-возможности, комфортное передвижение по дорогам и улицам городов. Часто необходимы компромиссы, но предлагая решение проблемы необходимо помнить, что во главе приоритетов всегда должна быть человеческая жизнь и здоровье.
Итак, на что следует обратить внимание водителю для предотвращения наезда на пешехода:
1.Остановки общественного транспорта. В непосредственной близости от них пешеходы любят неожиданно появляться на дороге.
2.Притормаживающие на дороге автомобили. Водители часто пропускают пешеходов даже вне пешеходных переходов и если этого вовремя не заметить, можно попасть в неприятное ДТП.
3.Пешеходы, переходящие проезжую часть в темное время суток и не имеющие светоотражающих предметов
Работа выполнена под руководством проф. С.П.Щеца
ДЕТАЛИ МАШИН
Н.Ю. Лапченко
ОЦЕНКА ОСТАТОЧНОГО РЕСУРСА ДЕТАЛЕЙ МАШИН
Объект исследования: остаточный ресурс детали машин. Результаты, проведен анализ современных методов оценки
остаточного ресурса изделий.
З
адача оценки остаточного ресурса эксплуатируемого объекта относится к классу задач индивидуального прогнозирования и включает решение таких задач, как оценка текущего состояния. прогнозирование этого состояния в будущем ,оценка вероятностей наступления отказов ,оценка риска аварийных ситуаций.
Вероятностный метод расчета ресурса.
Работа вероятностного иллюстрирована на рисунке 1 на примере оценки ресурса для различных вероятностных повреждений образцов легкого сплава АМг-6 и стали ЭП-630, испытанных при действии суммы случайных процессов различной интенсивности и подвергающиеся консольному изгибу на электродинамических установках с автоматическим поддержанием реализуемого случайного процесса .

12
Рис.1 Сопротивление усталости образцов
Параметрический метод оценки остаточного ресурса на основе метода неразрушающего контроля.
В основу подхода положен неразрушающий метод текущего контроля (в процессе всего срока службы) по результатам измерения такой магнитной характеристики металла, как коэрцитивная сила (рисунок 2). Подобный подход давно признан в металлургии и машиностроении.
Рис.2 Типовые режимы эксплуатации
Метод оценки ресурса с использованием диффузионного распределения. Для эффективного выборочного контроля необходимо применение
статистических методов, основанных на использовании информации о законах распределения дефектов по поверхности (или объему) оборудования.
Функция этого распределения имеет следующий вид
f t |
t |
|
|
t 2 |
F t DM t; |
|||
|
|
|
exp |
|
; |
|||
|
|
|
2 2 t |
|||||
2 t |
2 t |
|||||||
|
|
|
|
|
||||
|
|
|
|
|
|
|
|
t,v .
t
Параметры распределения можно определить из следующих соотношений:

13
|
|
|
|
|
|
|
|
|
|
|
|
|
|
|
|
|
|
|
|
|
|
|
t |
|
|
|
|
|
|
|
|
|
|
|
|
||||||||
|
|
|
|
|
|
|
|
R t 1 DM t; ,v |
|
|
|
|
|
|
|
; |
|
|
|
|
|
|
|
|
|
|
|
||||||||||||||||
|
|
|
|
|
|
|
|
|
|
|
|
|
|
|
|
|
|
|
|
|
|
|
|
|
|
||||||||||||||||||
|
|
|
|
|
|
|
|
|
|
|
|
|
|
|
|
|
|
|
|
|
|
|
|
|
t |
|
|
|
|
|
|
|
|
|
|
|
|
||||||
|
|
|
|
|
|
|
|
|
|
|
|
|
|
|
|
|
|
|
|
|
|
|
|
|
|
|
|
|
|
|
|
|
|
|
|
|
|||||||
|
|
|
|
|
2 |
|
|
|
|
|
|
2 |
|
|
2 |
|
|
|
|
|
|
|
|
|
|
|
|
|
|
|
|
|
|
2 |
|
||||||||
|
|
|
|
|
|
|
|
|
|
|
|
|
|
|
|
||||||||||||||||||||||||||||
|
1 |
|
|
|
|
|
|
|
|
|
e2 |
|
|
|
|
|
|
|
|
|
|
|
exp |
|
|
|
|||||||||||||||||
|
2 |
|
|
|
|
2 |
|
|
|
|
|
|
|
|
|
|
|
|
2t2 |
|
|||||||||||||||||||||||
|
|
|
|
|
|
|
|
|
|
||||||||||||||||||||||||||||||||||
|
|
|
|
|
|
|
|
|
|
|
|
|
|
|
|
|
|
|
2 |
|
|
|
|
||||||||||||||||||||
|
|
|
|
|
|
|
|
|
|
|
|
|
|
|
|
|
|
|
|
|
|
|
|
|
|
|
|
|
|
|
|
|
|
|
|
|
|
|
|||||
|
|
|
|
|
|
|
|
|
|
|
|
|
|
|
|
|
|
|
|
|
|
|
|
|
|
|
|
|
|
|
|
|
|
. |
|||||||||
|
|
|
|
|
|
|
|
|
|
|
|
|
|
|
|
|
|
|
|
|
|
|
|
|
|
|
|
|
|
|
|
|
|
|
|
||||||||
|
|
|
|
|
|
|
|
|
|
|
|
|
|
|
|
|
|
|
|
|
|
|
|
|
|
|
|
|
|
|
|
|
|
|
|||||||||
|
|
|
|
|
|
|
|
|
|
|
|
|
|
|
|
|
|
|
|
|
|
|
|
|
|
|
|
|
|
|
|
|
|
|
|
|
|
|
|||||
|
|
|
|
|
|
|
|
|
|
|
|
|
|
|
|
|
|
|
|
|
|
|
|
|
|
|
|
|
|
|
|
|
|
|
|
|
|||||||
|
|
|
|
|
|
|
|
|
|
|
|
|
|
|
|
|
|
|
|
|
|
|
|
|
|
|
|
|
|
|
|
|
|
|
|
|
|
|
|||||
|
|
|
|
|
|
|
|
|
|
|
|
|
|
|
|
|
|
|
|
|
|
|
|
|
|
|
|
|
|
|
|
|
|
||||||||||
Метод определения распределений ресурса по индивидуальным |
|||||||||||||||||||||||||||||||||||||||||||
кривым усталости. |
|
|
|
|
|
|
|
|
|
|
|
|
|
|
|
|
|
|
|
|
|
|
|
|
|
|
|
|
|
|
|
|
|
|
|
|
|
||||||
Остаточный ресурс (рисунок 3) |
оборудование может иметь не только до |
||||||||||||||||||||||||||||||||||||||||||
|
|
|
|
|
|
|
|
|
|
|
|
|
|
|
|
|
|
истечения |
|
|
|
расчетного |
|
|
|
срока |
|||||||||||||||||
|
|
|
|
|
|
|
|
|
|
|
|
|
|
|
|
|
|
службы, но и после него. Это |
|||||||||||||||||||||||||
|
|
|
|
|
|
|
|
|
|
|
|
|
|
|
|
|
|
обусловлено |
|
|
|
|
действующими |
||||||||||||||||||||
|
|
|
|
|
|
|
|
|
|
|
|
|
|
|
|
|
|
нормами |
и |
|
правилами |
|
расчета |
||||||||||||||||||||
|
|
|
|
|
|
|
|
|
|
|
|
|
|
|
|
|
|
сроков |
|
|
службы |
|
оборудования, |
||||||||||||||||||||
|
|
|
|
|
|
|
|
|
|
|
|
|
|
|
|
|
|
предусматривающими обеспечение |
|||||||||||||||||||||||||
|
|
|
|
|
|
|
|
|
|
|
|
|
|
|
|
|
|
прочности |
|
|
|
и |
износостойкости |
||||||||||||||||||||
|
|
|
|
|
|
|
|
|
|
|
|
|
|
|
|
|
|
изделий |
|
|
|
|
|
|
|
|
при |
|
|
наиболее |
|||||||||||||
|
|
|
|
|
|
|
|
|
|
|
|
|
|
|
|
|
|
неблагоприятных |
|
|
|
режимах |
|||||||||||||||||||||
|
|
|
|
|
|
|
|
|
|
|
|
|
|
|
|
|
|
нагружения |
в заданных |
условиях |
|||||||||||||||||||||||
|
|
|
|
|
|
|
|
|
|
|
|
|
|
|
|
|
|
эксплуатации, а также при |
|||||||||||||||||||||||||
Рис.3 Плотность распределения |
|
|
|
минимальных уровнях механических |
|||||||||||||||||||||||||||||||||||||||
|
|
|
характеристик |
|
|
|
конструкционных |
||||||||||||||||||||||||||||||||||||
ресурса металлоконструкции |
|
|
|
|
|
|
|||||||||||||||||||||||||||||||||||||
|
|
|
материалов, |
|
|
обеспечиваемых по |
|||||||||||||||||||||||||||||||||||||
|
|
|
|
|
|
|
|
|
|
|
|
|
|
|
|
|
|
|
государственным стандартам. Фактические режимы нагружения при соблюдении правил эксплуатации оказываются, как правило, менее напряженными, чем расчетные, что снижает интенсивность расходования заложенных запасов (по прочности, износо- и коррозионной стойкости) обеспечивает резерв по остаточному ресурсу оборудования
Работа выполнена по руководством асс. каф. «ДМ»С.А. Олисова
К.А.Мефёд, А.С. Костоглотов ВЛИЯНИЕ МАГНИТНОГО ПОЛЯ НА ПРОЧНОСТЬ
СОЕДИНЕНИЯ С НАТЯГОМ
Объект исследования: прессовое соединение с гарантированным натягом металлических деталей типа вал-втулка.
Результаты, полученные лично автором: проведено несколько экспериментов на прессе, получены данные подтверждающие влияние магнитного поля на силу сцепления вала со втулкой.
В результате экспериментальных исследований было установлено, что наличие магнитного поля в месте контакта вала и втулки повышает их силу

14
сцепления, что приводит к повышению усилия сдвига в осевом направлении вала относительно втулки.
Экспериментальные исследования проводились на нескольких образцах (рис.1) с использованием пресса (рис.2).
Для регистрации осевого усилия сдвига, сближения, силы тока, напряжения на катушке использовалась измерительная система фирмы Л- Кадр LTR-EU-2 с двумя платами LTR212 c АЦП для тензоизмерений и LTR214 c прецизионным АЦП для измерения напряжения, сопротивления или силы тока.
Рис. 1 . Образец |
Рис. 2. Установка для |
|
испытания |
Установлено, что магнитное поле увеличивает силу сцепления вала с втулкой, что приводит к повышению усилия сдвига в осевом направлении вала относительно втулки.
На рис.3 представлен процесс изменения осевого усилия сдвига с наличием магнитного поля и без него.
Рис. 3 . Изменение силы запрессовки
15
Выводы:
Разработана методика проведения эксперимента.
Получены данные подтверждающие влияние магнитного поля на силу сцепления вала со втулкой.
Работа выполнена под руководством проф. кафедры «Детали
машин» А.Г. Стриженка
М.А. Семенькова КОНТАКТНАЯ ЖЕСТКОСТЬ ПЛОСКОГОСТЫКА
Объект исследования: болтовое соединение плоского стыка. Результаты, полученные лично автором: выявлены зависимости
удельной контактной жесткости от параметров качества сопряженных поверхностей.
При проектировании машиностроительных изделий широко используются неподвижные соединения, образованные шероховатыми поверхностями сопрягаемых деталей.
Наиболее широко применяются резьбовые соединения. Микронеровности поверхностей контактирующих деталей в таких соединениях приводят к различию номинальной и фактической площади контакта, которая зависит от давления в стыке.
Это обуславливает специфические механические свойства контактного слоя – области, находящейся около поверхности контакта деталей, толщиной порядка высоты микронеровностей контактирующих поверхностей. В общепринятых методиках расчета резьбовых соединений не учитывается податливость контактного слоя, что приводит к невозможности прогнозирования фреттингостойкости в резьбовом соединении. Большинство исследований по податливости контактного слоя соединений деталей машин посвящено нормальной податливости.
Существующие зависимости для оценки касательной податливости контактного слоя не учитывают конструктивных параметров соединения, указываемых на рабочих чертежах деталей. Вследствие этого при разработке нового оборудования расчеты производятся без учета контактной податливости, что вызывает необходимость длительной доводки конструкций по результатам эксплуатации, а также ремонтов, повышающих расходы.
Оценка контактной жесткости проводилась главным образом для станочных приспособлений, когда главным критерием качества являлась точность. Результаты исследований, проведенные ранее, показали, что контактная деформация определяется в основном деформацией волн и шероховатого слоя. При оценке долговечности болтовых соединений важную роль играют податливость самих болтов и жесткость соединяемых

16
элементов. Увеличение податливости болтов осуществляется за счет увеличения длины болтов.
Рост жесткости стыка также приводит к увеличению долговечности. В данном случае эффективным способом увеличения долговечности является исключение мягких прокладок между сопряженными элементами стыка. Не следует при этом игнорировать герметичность стыка.
В соответствии с подходом, излагаемым в курсе «Детали машин», жесткость стыка является условной величиной и определяется так называемыми конусами давления. Этот подход не учитывает контактную жесткость стыка.
Цель работы ‒ установление связи между контактной жесткостью и параметрами качества поверхности.
Методы исследования: методы математического моделирования; методы механики контактного взаимодействия; экспериментальные методы; методы аппроксимации.
Рассматривались два сочетания стальных поверхностей: 1 (поверхности 1 и 1*); 2 (поверхности 2 и 2*).Параметры качества, определяющих волнистость и шероховатость, приняты в мкм следующими:
сочетание 1(Ra1=2,30 ; rw1 =7540; Wz1 =8,9; Ra1*=0,64 ; rw1*=6290; Wz1*=3,6);
сочетание 2 (Ra2=0,92 ;rw2 =3000; Wz2 =6,6; Ra2*=1,20 ; rw2* =3700; Wz2* =9,1).
На основании имеющихся экспериментальных данных для
рассматриваемых сочетаний нагрузка – сближение выявлены зависимости давления в стыке от деформации и контактной жесткости от давления.
Аппроксимация полученных зависимостей имеет вид:
для сочетания 1
для сочетания 2 Анализ полученных зависимостей показал, что на величину контактной
жесткости существенное влияние оказывают параметры качества сопрягаемых поверхностей, особенно радиусы волн поверхности.
Выявленные закономерности, оценивающие податливость плоского стыка, дают возможность разработать методику расчета надежности ответственных болтовых соединений.
Для этого требуется решить следующие задачи:
1)установление обобщенной зависимости жесткости плоского стыка для разных сочетаний;
2)определение составляющих деформации стыка, связанных с волнистостью и шероховатостью.
Работа выполнена под руководством проф. каф. «Детали машин»
Тихомирова В.П.
17
МЕХАНИКА, ДИНАМИКА И ПРОЧНОСТЬ МАШИН
Д.М. Гулак ПРИМЕНЕНИЕ МОДЕЛИ БАЛКИ ТИМОШЕНО В ДИНАМИЧЕСКИХ
ЗАДАЧАХ
Объект исследования: модель балки Тимошенко.
Результаты, полученные лично автором: произведены расчеты, с помощью которых определены собственные частоты колебаний, и произведено сравнение полученных значений с аналитическим решением.
Широко используемая в инженерных расчетах модель балки ЭйлераБернулли, игнорирующая инерцию вращения поперечного сечения и прогибы, обусловленные поперечным сдвигом, имеет ограниченные пределы применения. Эта модель не применима для исследования высокочастотных колебаний, когда расстояние между узлами собственных форм сопоставимо с размерами поперечного сечения, в задачах изгиба коротких балок.
В20-х годах прошлого века С. П. Тимошенко усовершенствовал расчетную схему балки, включив в дифференциальное уравнение поперечных колебаний члены, учитывающие инерцию вращения сечения и прогибы от поперечной силы. Такая модель балки в литературе получила название «балка Тимошенко».
Вданной работе рассмотрены модели балки Эйлера-Бернулли и балки Тимошенко с одинаковыми геометрическими характеристиками.
На языке программирования Fortran была написана программа формирования матриц жесткости и масс для модели балки Тимошенко, с помощью которой в программном комплексе DSMFEM произведен расчет на собственные формы колебаний для исследуемых балок. Результат сравнивался с аналитическим решение, взятым из работ С. П. Тимошенко.
Сравнение результатов показало, что для коротких балок в динамических расчетах лучше использовать модель балки Тимошенко. Погрешность расчета данной балки составила два процента, в то время как расчет балки Эйлера-Бернулли дал погрешность более пятидесяти процентов.
Работа выполнена под руководством доц. каф. «Механика и динамика и
прочность машин» А.А. Ольшевского
А.С.Забелин,Ю.Ю.Рыжако ЛАБОРАТОРНАЯ УСТАНОВКА ДЛЯ ОПРЕДЕЛЕНИЯ КРИТИЧЕСКОЙ СИЛЫ ДЛЯ СЖАТОГО СТЕРЖНЯ
Объект исследования: критическая сила для сжатого стержня с начальной погибью и способы ее определения.
Результаты, полученные авторами: лабораторная установка и значение критической силы для сжатого стержня.
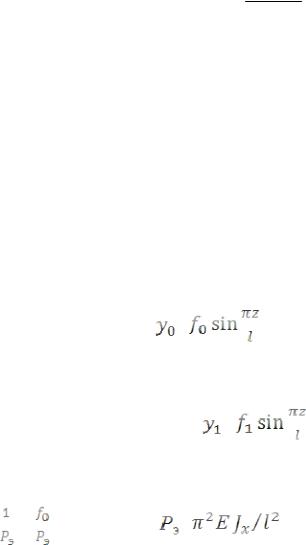
18
Для определения критической силы для сжатого стержня большой гибкости используется формула Эйлера:
Pкр 2EJ2x ,
( l)
где E – модуль упругости материала стержня;
Jx – момент инерции поперечного сечения стержня относительно оси х, относительно которой изгибается стержень при потере устойчивости;
l – длина стержня;
μ – коэффициент приведения длины стержня.
Теоретически стержень сохраняет исходную прямолинейную форму равновесия, если приложенная к нему сила меньше критической. Если сила превышает критическую, он переходит к криволинейной форме равновесия. На практике прогибы сечений стержня наблюдаются при сжимающей силе меньшей критической. Это происходит по двум причинам. Трудно обеспечить приложение силы вдоль оси стержня. Ось стержня имеет начальную погибь.
Уравнение начальной формы оси стержня:
= |
|
(1) |
|
Уравнение для дополнительного прогиба, вызванного действием сжимающей силы Р:
= |
|
(2) |
|
С использованием уравнений (1) и (2) получаем уравнение для определения критической силы
у= |
|
x+ |
|
, |
где = |
, f1 = x, f1/P= y. |
|
|
Для определения критической силы была сделана установка(рис.1). На этой установке к стержню с круглым сечением(диаметр 4мм) прикладывалось несколько значений силы, в диапазоне 150-375 Н. По полученным значениям прогиба стержня построены на графике экспериментальные точки, через которые проведена линияметодом наименьших квадратов(рис.2).
При практическом определении критической силы было получено значение 410Н, а при теоретическом 430Н. Значения критической силы оказались довольно близкими. Лабораторная установка позволила получить корректное значение критической силы.
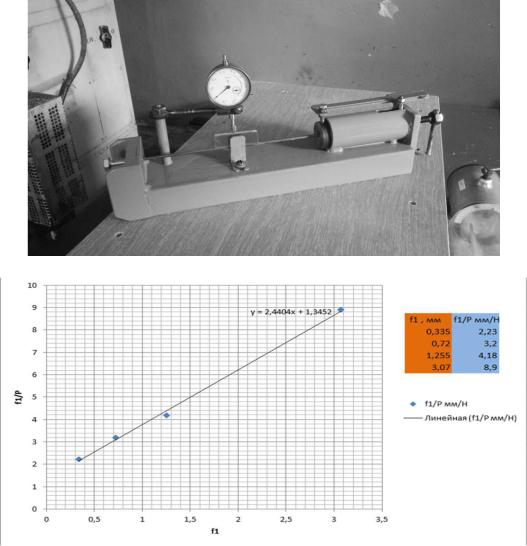
19
Рис.1
Рис.2
Работа выполнена под руководством зав. каф. «Механика и динамика и прочность машин»В.И.Сакало
Е.С. Кожелева ИССЛЕДОВАНИЕ КОЛЕБАНИЙ ОПОРЫ КОНВЕЙЕРА
ЛЕНТОЧНО-ЦЕПНОГО ТИПА
Объект исследования: конвейер ленточно-цепного типа грузоподъемностью 40 т.
Результаты, полученные лично автором: построена динамическая модель опоры конвейера в программной среде Femap NX Nastran, получены формы и частоты собственных колебаний конвейера, зависимости перемещений и напряжений от времени для анализа реакции объекта на внезапное приложение нагрузки.
В современной промышленности конвейеры занимают значительное место. В связи с последними разработками широкое применение получили
20
конвейеры ленточно-цепного типа, имеющие ряд преимуществ перед обычными ленточными конвейерами (большая прочность, меньшее натяжение ленты).
Для статического и динамического анализа была создана стрежневая модель конвейера в среде Femup NX Nastran. Нагрузку на конвейер рассчитывали исходя из приблизительного веса песка равномерно распределенного вдоль всей поверхности ленты. В работе рассматривается два случая: 1) конвейер нагружен только собственным весом; 2) конвейер нагружен силами тяжести груза.
При статическом анализе были получены максимальные напряжения: 1) 40 МПа; 2) 75 МПа. Далее проводились исследования реакции системы на внезапное приложение нагрузки (падение груза) с использованием и без использования вязкого демпфирования, целью которого являлось получение коэффициента динамики Кд.: 1) конвейер нагружен только собственным весом без трения - Кд = 1,5; 2) конвейер нагружен только собственным весом с трением - Кд = 1,3; 3) конвейер нагружен силами тяжести груза без трения - Кд = 2; 3) конвейер нагружен силами тяжести груза при наличии трения- Кд = 1,2. Также был проведен анализ собственных частот и форм колебаний, в ходе которого было получено 10 различных частот в диапазоне от 4 Гц до 16 Гц. Можно сделать вывод о том, что этот диапазон частот следует избегать при эксплуатации конвейера.
Работа выполнена под руководством доц. каф «Механика и динамика и прочность машин» В.А. Алдюхова
Косова В. Е. , Кожухов И.А.
ПРИМЕНЕНИЕ МЕТОДА КОНЕЧНЫХ ЭЛЕМЕНТОВ ДЛЯ РАСЧЕТА НАПРЯЖЕННО-ДЕФОРМИРОВАННОГО СОСТОЯНИЯ ДЕТАЛИ КРЕПЛЕНИЯ ТЕЛЕЖКИ И ТЭД ЛОКОМОТИВА 2ТЭ25А «СТРАХОВКА»
Объект исследования: деталь крепления тележки и ТЭД локомотива 2ТЭ25А «страховка».
Результаты, полученные лично авторами: выполнен расчет
напряженно-деформированного состояния |
методами сопротивления |
материалов и МКЭ. |
|
Метод конечных элементов - один из наиболее эффективных численных методов решения задач, описывающих состояние физических систем сложной структуры. Возникновение этого метода связано с решением задач космических исследований (1850 г.). Впервые он был опубликован в работе Тернера, Клужа, Мартина и Топп . Эта работа способствовала появлению других работ; был опубликован ряд статей с применениями метода конечных элементов к задачам (строительной механики и механики сплошных сред. Важный вклад в теоретическую разработку метода сделал в