
Сборник 70 студ конференции БГТУ
.pdf71
УЧЕБНО-НАУЧНЫЙ ТЕХНИЧЕСКИЙ ИНСТИТУТ
АВТОМАТИЗИРОВАННЫЕ ТЕХНОЛОГИЧЕСКИЕ СИСТЕМЫ МЕТАЛЛОРЕЖУЩИЕ СТАНКИ И ИНСТРУМЕНТЫ
П. А. Акулов АВТОМАТИЗИРОВАННОЕ УСТРОЙСТВО ПРОТЯЖКИ И НАМОТКИ ЛЕНТОНОСИТЕЛЯ С КОНТАКТАМИ
ДЛЯ ГАЛЬВАНИЧЕСКОЙ ЛИНИИ НАНЕСЕНИЯ ПОКРЫТИЙ В УСЛОВИЯХ «КАРАЧЕВСКИЙ ЗАВОД „ЭЛЕКТРОДЕТАЛЬ“»
Объект исследования: гальваническая линия нанесения полного и локального покрытия.
Полученные результаты: разработано устройство протяжки ленты, рассчитаны внутренние напряжения и прогиб, разработана управляющая программа для поворота шагового двигателя.
Линия предназначена для гальванического нанесения полного и локального покрытия на штыри электрических соединителей методом контролируемого погружения в электролит в ленте-заготовке. Линия может применяться автономно.
Принцип действия: лента, сматываясь с бобины передающего механизма, в процессе покрытия деталей последовательно проходит через ванны с рабочими растворами. Лента-заготовка с покрытыми деталями наматывается на бобину приемного механизма.
На предприятии «Электродеталь» протяжка ленты с контактами на гальванической установке осуществляется с помощью вертикально расположенных валков. На валках радиально расположены штыри, которые в процессе протяжки входят в зацепление с лентой (благодаря специальным отверстиям в самой ленте).Особенностью такой передачи движения является деформация ленты, возникающаяиз-за погрешностей расположения отверстий в ленте и штырей валков.Вследствие этого лента сжимается и растягивается. Для решения данной проблемы необходима модернизация системы протяжки.
Был предложен один из вариантов модернизации системы протяжки
ленты,особенность которого заключается |
в замене |
вертикальных валков |
с радиальными штырями на гладкие. |
Благодаря |
этому практически |
исключается проблема сжатия и растяжения ленты.
Суть процесса протяжки: лента входит в зацепление между двумя валками (является промежуточным звеном в, так называемой, фрикционной передаче). Как и вначальном варианте, ведущий барабан, стоящий в конце линии, тянет и наматывает всю ленту. Необходимо учесть возможность провисания ленты под действием силы тяжести. Для решения этой проблемы была предложена возможность регулирования угла наклона валков. Т.е., при падении (провисании) ленты, валки должны повернуться на положительный угол (относительно нормали) для того, чтобы лента пошла вверх,
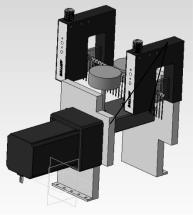
72
и, наоборот, придвижении вверх, выше допустимого значения, валки должны повернуться на отрицательный угол для того, чтобы лента пошла вниз.
Поворот валков на определенный угол будет осуществляться с помощью шагового мотор-редуктора.Оптические датчики контроля положения края ленты определят текущее положение и передадут полученные данные в микроконтроллер, который определит требуемый угол поворота валков, а также необходимое число импульсов, которые необходимо подать на вход драйвера управления шаговым двигателем. Эти данные будут отображаться на LCD-дисплее и подаваться после обработки ШИМ на драйвер. Выходные данные с драйвера поступят на вход шагового мотор-редуктора.
Таким образом, структурная схема разработанной системы состоит из следующих элементов: оптический датчик с аналоговым выходом, аналогово-цифровой преобразователь, микроконтроллер, индикатор, драйвер управления шаговым двигателем, шаговый мотор-редуктор. На рис 1. представлена спроектированная установка.
Рис. 1 – Спроектированная установка. (1-Стойки, 2-Шаговый мотор-редуктор, 3-Корпус, 4-Ролики, 5-Оптический датчик).
Регулирование скорости подачи ленты будет осуществляться с помощью регулирования скорости вращения вала двигателя постоянного тока, который будет приводить в движение ведущий барабан, наматывающий ленту с контактами.
Вся необходимая информация задается с пульта оператора, расположенного отдельно от гальванической линии.
Преимущества разработанной системы:
1)обеспечение требуемой точности;
2)гибкость;
3)возможность управления. Недостатки:
1)более сложная реализация по сравнению с существующей;
2)увеличение затрат на реализацию.
Работа выполнена под руководством проф. каф.«Автоматизированныетехнологические системы» О.Н. Федонина
73
А.В. Алексеев РАЗРАБОТКА ПРИСПОСОБЛЕНИЯ ДЛЯ АВТОМАТИЧЕСКОЙ
РЕЗЬБЫ В ШТАМПОВАННЫХ ДЕТАЛЯХ
Объект исследования: сверлильно-резьбонарезной станок FLOTT. Полученные результаты: разработано автоматическое зажимное
приспособление, разработан лоток для перемещения деталей, составлен алгоритм работы, расчет силы трения между деталью и упором .
Станокмашина используемая для обработки различных материалов, либо приспособление для выполнения чего-либо. Станки характеризуются наличием станины, иногда ее саму называют станком.
Современные станки имеют, как правило, оригинальную компоновку, позволяющую повысить их жесткость, улучшить защиту направляющих и винтовых передач, обеспечить свободный отвод стружки и удаление её из рабочей зоны, применять загрузочное устройство любых типов, обеспечить свободный допуск к инструменту и приспособлениям, повысить безопасность работы.
Сверлильный станок FLOTT.
Мощный и высокотехнологичные станки FLOTT отличаются надежностью и высокой производительностью. Станки сделаны с немецкой точностью и выдержанным современным дизайном.
FLOTTизвестный мировой производитель оборудования, который отвечает за качество своей продукции. Данное оборудование имеет широкий модельный ряд и большое количество опций.
Станком FLOTT доступны следующие задачи:
1.Сверление;
2.Нарезание резьбы;
3.Фрезерование; Стандартная комплектация:
1.Аварийный выключатель
2.Предохранитель
3.Защита сверла
4.Быстро регулируемый ограничитель глубины сверления
5.Силовой кабель (1.5м) со штекером CEE
6.Защита от перегрева
Сверлильный станок FLOTTнемецкое качество, высокая точность, современный дизайн.
Предприятие ОАО «Карачевский завод «Электродеталь»» недавно купила станок фирмы FLOTT TB 13 plus, станок очень маленький, закреплен на столе большими анкерами, станок в основном на предприятии используют для нарезания резьбы в штампованных деталях. И через некоторое время возникли неудобства эксплуатации этого станка. Причина была в том что, постоянная перестановка деталей занимала очень много времени, постоянно приходилось поддерживать детали, значительно невысокая производительность, неудобства вертикального перемещения шпинделя. И
74
было принято автоматизировать и разработать приспособление для автоматической нарезки резьбы.
Предложения по разработке: Шпиндель в данном станке опускается с помощью боковой рукоятки и ей же создается усилие нарезания резьбы в детали. Для решения это проблемы было предложено поставить мотор редуктор.
Для подачи детали на стол поштучно и автоматически, мной было рассмотрено 2 варианта решения этой задачи:
1.Поставить рядом со столом магазинный накопитель деталей.
2.Поставить лоток для накопления заготовок.
С первым вариантом была проблема с подачей деталей на стол, для этого надо было поставить робота, который бы осуществлял дополнительные перемещения. Во втором варианте вместо заводского стола поставить лоток для накопления заготовок. Я считаю что это позволит сократить время на переустановку детали и увеличится производимость.
Детали под наклоном лотка будут скатываться вниз и с помощью серво-привода будет подаваться на стол по штучно. После того как деталь попала на стол ее необходимо зафиксировать, зажимается деталь в магнитных блоках с упором. Дальше осуществляется зажим детали и нарезается резьба. Как только резьба нарезалась происходит разжим и деталь проталкивается так же с помощью серво-привода вниз по лотку и попадает в железную емкость для дальнейшего использования .
Лотки предназначены для накопления и самотёчного, полу самотёчного или принудительного перемещения заготовок в загрузочных устройствах и в устройствах меж станочного транспортирования. Расчет силы трения между деталью и упором проводится для выбора сервопривода по известной нормальной нагрузке и коэффициенту трения скольжения между деталью и направляющей лотка.
Проектирование любого приспособления характеризуется большим объемом работы, значительную часть которой занимают проектноконструкторские расчеты, важнейшим среди которых является расчет точности приспособлений. Данный вопрос достаточно полно освещен в справочной литературе, но сведения носят разрозненный характер и зачастую расчет приспособления на точность требует работы с большим количеством источников. Я считаю,что разработанная мной конструкция в решении данной проблемы поможет предприятию ОАО «Карачевский завод «Электродеталь»» увеличить производительность станка, улучшить качество выпускаемой продукции и обеспечить безопасность работы.
Работа выполнена под руководством доц. каф. «Автоматизированные технологические системы» В.П. Матлахова
75
З.А. Астапова, А.М. Ушаков РАЗРАБОТКА И ИЗГОТОВЛЕНИЕ СИСТЕМЫ УПРАВЛЕНИЯ
ПОДАЧЕЙ РАБОЧЕГО ГАЗА И МАГНЕТРОНА В УСТАНОВКЕ ДЛЯ НАНЕСЕНИЯ ИЗНОСОСТОЙКИХ ПОКРЫТИЙ
Известно, что работоспособность изделия определяется, прежде всего, свойствами его поверхностных слоев. Поэтому на практике получило широкое распространение нанесение покрытий в вакууме. В частности эти покрытия используются и на режущем инструменте, улучшая его эксплуатационные свойства, увеличивая ресурс инструмента.
Сейчас существует множество методов упрочняющей обработки режущего инструмента. В машиностроении наиболее широко применяются магнетронный и вакуумно-дуговой методы нанесения покрытий.
На кафедре «Металлорежущие станки и инструменты» производится модернизация вакуумной установки для нанесения покрытий на инструмент методом магнетронного распыления. Модернизация предусматривает совершенствование вакуумной и газовой системы, а также источника распыления материала мишени.
Вакуумная система включает: собственно вакуумную камеру, насосы, магистрали, датчики вакуума, запорную арматуру. Система подачи газа в установке также содержит: источник газа (баллон с редуктором), магистрали (трубопроводы, смесители), устройство напуска газов, а также устройство управления.
В общем случае вакуумные процессы осуществляются в следующей последовательности: откачка и напуск газов, и собственно сами процессы.
Процесс откачки рабочей камеры до предельного вакуума можно разделить на две стадии. На первой осуществляется удаление основного количества газа с помощью насоса предварительного разрежения (форвакуумного насоса) до давления порядка 10 Па. На второй стадии посредством высоковакуумных насосов удаляется не только оставшийся газ, но и газ, адсорбированный деталями установки.
Напуск газов осуществляется с помощью специальных устройств и приборов. Возникают два противоположных процесса – напуск рабочего газа в камеру и откачка газа (воздуха) из камеры. Эти процессы должны оставаться равновесными, т.к. от них зависит предельное остаточное давление в камере.
Для откачки газов в вакуумных системах существуют насосы. На экспериментальной установке используются два вида вакуумных насосов: форвакуумный – механический и высоковакуумный – паромасляный.
Для напуска газов в зависимости от требуемого его количества (расхода газа) используются либо натекатели, либо регуляторы расхода газа – РРГ. На основе РРГ также возможно получение смесей газов. Рассматриваемая вакуумная система содержит натекатель игольчатого типа.
Для формирования рабочей газовой среды в камеру планируется напускать несколько газов: аргон, азот, а также их смесь. Для этого
76
необходимы два регулятора. Режимы работы: расход аргона 4,08 л/ч, расход азота до 1,02 л/ч, суммарное рабочее давление в камере 0,15 Па. Размер рабочей камеры составляет 700х600х500 куб.мм. Регулирование расходом и смесью газов будет осуществляться механически.
При дуговом методе между катодом и анодом инициируется вакуумная дуга, которая испаряет материал катода. Осаждение частиц осуществляется из плазмы испаряемого материала покрытия. Этот метод позволяет наносить покрытия с высокой скоростью, однако их качество является не достаточно высоким. Поэтому было решено наносить покрытия с помощью магнетронного распылителя, который лишен этого недостатка.
В ходе выполнения работы были изучены возможные варианты конструкции кольцевого планарного магнетрона: с собственным анодом и без анода, когда его роль выполняет сама камера. Основными конструктивными элементами магнетрона являются: обойма из магнитомягкого материала с находящимися в ней магнитами и магнитопровод, которые расположены в водоохлаждаемом корпусе и при установке магнетрона он должен быть электрически изолирован от камеры.
Магнитная система предлагаемого магнетрона состоит из постоянных цилиндрических магнитов, собранных в два кольца разных диаметров. Мишень, диаметр распыляемой части которой равен 64 мм, расположена непосредственно над магнитной системой.
Постоянные магниты, образующие магнитную систему, могут быть изготовлены из различных магнитных материалов. Были применены магниты из NdFeB с никелевым покрытием и SmCo. Самарий-кобальтовые магниты имеют высокую температурную стойкость (до 350°С) по сравнению с неодимовыми (в нашем случае до 120°С), которые, в свою очередь, обладают большей магнитной силой и меньшей стоимостью, а покрытие из никеля обеспечивает коррозионную стойкость.
Рассмотренные магнетроны устанавливаются внутри вакуумной камеры, что предполагает ввод охлаждения непосредственно в камеру. Это является их существенным недостатком, поскольку сложно обеспечить герметичность такого вакуумного ввода. В связи с этим рассматривается третий вариант конструкции магнетрона, при которой он расположен снаружи вакуумной камеры и крепится к ней с помощью фланца. Кроме того при таком варианте отсутствует необходимость в применении вакуумного токоввода для подключения источника питания, расположенного сзади вакуумной камеры для обеспечения соблюдения правил электробезопасности.
Основным достоинством магнетронных систем является высокая чистота наносимых пленок, а недостатком низкая скорость напыления и малый коэффициент использования материала мишени.
Работа выполнена под руководством проф. каф. «Металлорежущие станки и инструменты» А.В. Хандожко
77
Блохин К.О.
РАЗРАБОТКА КОНТРОЛЬНО-СОРТИРОВОЧНОГО УСТРОЙСТВА ДЛЯ АВТОМАТИЧЕСКОЙ ЛИНИИ ПРОИЗВОДСТВА КЕРАМИЧЕСКОЙ ПЛИТКИ
Объект исследования: параметры качества керамической плитки Результаты полученные лично автором: структурная схема
управления контрольно-сортировочным устройством
Потребность в повышении качества готовой продукции, а также в повышении конкурентоспособности данного товара на рынке привела к тому, что предприятием было решено установить для данной линии устройство контроля готовой продукции с целью контроля параметров ее качества, а также разработать сортировочный механизм для сортировки продукции по типу годности. Так как раньше контроль осуществлялся визуально и не все параметры могли быть проконтролированы, то данное устройство должно внести большой вклад в качество выпускаемой предприятием продукции.
Данное устройство способно контролировать такие поверхностные и геометрические параметры как:
1.Геометрия плитки. Измеряются размеры по продольному и поперечному направлениям плитки, проходя под датчиками и затемняя их, а так как известна скорость конвейера можно подсчитать длины сторон, а затем сравниваем изделие с эталонным образцом, изготавливаемым, как правило, из матового стекла.
2.Качество поверхности изделия, которые в свою очередь делятся
на:
- измерение кривизны краев. Для данного дефекта используются значения полученные на краях диагоналей и медианах. Высчитывается разница между средней величиной, считаных на углах значений, и величиной, полученной в центре проверяемой стороны.
- Измерение вогнутости и выпуклости. Этот дефект выявляется при подсчете разницы между значением полученным в центре плитки и средним значением по краям.
- Измерение углов. С помощью данного измерения контролируются четыре угла плитки независимо друг от друга. Для каждого угла есть три результата. Самое большое значение определяет направление изгиба: плюс – изгиб кверху, минус – изгиб книзу.
- Измерение перекоса. Под перекосом понимается отклонение четвертого угла плитки относительно поверхности трех остальных. Высчитывается нахождением разницы между суммой значений, полученных по краям одной диагонали и суммой значений, полученных по краям другой диагонали.
- Измерение локализованных дефектов. Плитка разбивается на множество квадратов в каждом из которых выявляются локализованные дефекты.

78
Устройство контроля «Newcheck» Итальянской фирмы «Nuovafima» представлено двумя основными модулями контроля: «модуль планара» и «модуль калибро», а также панелью оператора, узлом ременной передачи и центратором для выравнивания изделий проходящих под устройством. Теперь подробнее о каждом из них, «модуль планара» представляет из себя устройство для контроля поверхностных параметров качества плитки. Данный контроль осуществляется с помощью оптических датчиков закрепленных непосредственно над изделием, их количество может быть от трех до одиннадцати, отколичество датчиков зависит качество контроля изделия. Вторым основным устройством контроля является «модуль калибро» он служит для контроля геометрических параметров изделий. В его состав входит 7 фотоэлементов, состоящих из передатчика и приемника, для контроля продольной геометрии изделия и две камеры высокого разрешения для измерения поперечных размеров. Собранные параметры анализируются и сравниваются с эталонным образцом, присваивая изделию статус брак или не брак.
Также для данного устройства разработан сортировочный механизм для отсеивания бракованных изделий с конвейера. В качестве составных частей данного механизма используется программируемый логический контроллер, принимающий выходной сигнал от устройства контроля, анализирует его и в зависимости от годности изделия посылает управляющих сигнал на пневматический привод. Данный пневматический привод располагается непосредственно над конвейером и получая сигнал о годности изделия через определенно заданный временной интервал, либо сбивает его с конвейера, либо пропускает далее. Структурная схема контрольно-сортировочного устройства представлена на рис.1.
Рис. 1.
Внедрение данного контрольно-сортировочного устройства в значительной степени увеличит качество выпускаемой продукции, поможет сократить численность обслуживающего персонала, а также повысить надежность линии в целом.
Работа выполнена под руководством доц. кафедры «АТС» Агеенко А.В.
79
С.Ю. Голяков СОВЕРШЕНСТВОВАНИЕ ТЕХНОЛОГИЧЕСКОГО ПРОЦЕССА ОБРАБОТКИ ДЕТАЛИ «ПОДКЛАДКА» С ЦЕЛЬЮ ПОВЫШЕНИЯ
ПРОИЗВОДИТЕЛЬНОСТИ ДЛЯ УСЛОВИЙ ОАО ПРИБОРНЫЙ ЗАВОД «СИГНАЛ»
Объект исследования: технологический процесс изготовления детали «Подкладка» и предлагаемая инструментальная оснастка.
Результаты, полученные лично автором: разработан новый вариант технологического процесса изготовления детали и спроектирован штамп совмещенного действия.
На ОАО Приборном заводе "Сигнал" изготавливают детали «Подкладка». Первоначально была произведена партия в количестве 10 штук. В базовом технологическом процессе обработки детали широко использованы универсальные станки с ручным управлением и с ЧПУ. Общее время обработки составляло около 35 минут.
С получением заказа на 10000 штук, было принято решение о переработки технологического процесса и использование более производительного оборудования.
На основе полученного задания, был критически проанализирован базовый процесс обработки и намечены основные пути его совершенствования. Для повышения производительности процесса вместо нескольких наиболее трудоемких операций механической обработки предлагается использовать прессовую операцию для получения детали требуемого контура. Для этого необходимо спроектировать инструментальную оснастку в виде штампа совмещенного действия. Штамп должен позволять одновременно выполнять вырубку детали и пробивку отверстия заданного размера.
На основе выполненных расчетов и принятых элементов конструкции была разработана 3D модель проектируемого штампа (рис. 1).
Основные элементы и узлы штампа совмещенного действия:1-плита блока нижняя; 2-плита подкладная (нижняя); 3-держатель пуансон-матрицы; 4-резиновый буфер; 5-съемник; 6-матрица; 7-пуансонодержатель; 8-плита подкладная (верхняя); 9-плита блока верхняя; 10-хвостовик; 11-толкатель; 12-плита подкладная (верхняя); 13-пуансон; 14-выталкиватель; 15-пуансон- матрица; 16-направляющая; 17-втулка.
Принцип работы штампа: через хвостовик 10 штамп соединяется с ползуном пресса. К столу пресса штамп крепится прихватами к полкам нижней плиты 1. Полоса металла кладется на съемник 5 и прижимается боковой стороной к упорам и торцом к утопающему упору. После этого приводится в движение ползун пресса через хвостовик 10. Движение ползуна передается верхней плите 9 и матрица 6 прижимает полосу к съемнику 5. Далее под действием усилия пресса происходит сжатие резинового буфера 4, и вырубание контура детали пуансон-матрицей 15, одновременно с этим происходит вырубание отверстий пуансоном 13. После завершения рабочего
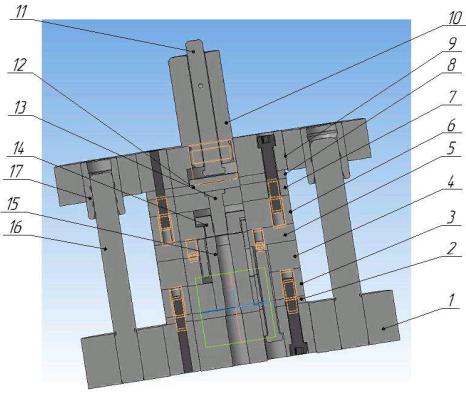
80
хода ползун пресса перемещается вверх, коромысло, установленное в прессе бьет по шпильке толкателя 11, через траверсу и штифты движение передается выталкивателю 14 и готовая деталь выбивается из полости матрицы 6.
Рис. 1. 3D модель штампа
В настоящее время разработаны сборочные чертежи штампа и выполняется детальная проработка рабочих чертежей деталей штампа.
Спроектированный штамп позволит повысить производительность ориентировочно до 20 раз, а также снизить себестоимость изготовления детали «Подкладка» до 3 раз.
Работа выполнена под руководством доц. каф «Металлорежущие станки и инструменты» Л.А. Захарова
М. В. Гребень
АВТОМАТИЗИРОВАННАЯ СИСТЕМА УПРАВЛЕНИЯ ВЕЛИЧИНОЙ ПОГРУЖЕНИЯ ЛЕНТЫ-ЗАГОТОВКИ В ЭЛЕКТРОЛИТ НА ГАЛЬВАНИЧЕСКОЙ ЛИНИИ ЛОКАЛЬНОГО ПОКРЫТИЯ ОАО «КАРАЧЕВСКИЙ ЗАВОД «ЭЛЕКТРОДЕТАЛЬ»
Объект исследования: гальваническая линия локального покрытия ОАО «Карачевский завод «Электродеталь».
Результаты, полученные лично автором: структурная схема автоматизированной системы.