
Сборник 70 студ конференции БГТУ
.pdf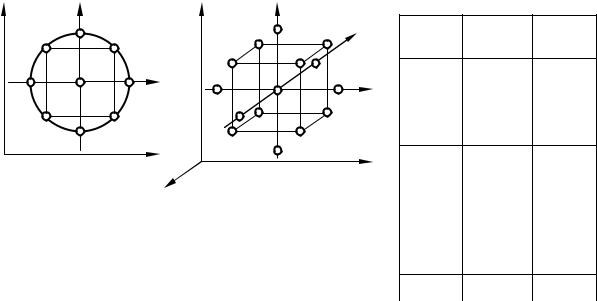
51
yˆ b0 |
k |
|
k |
, |
(1) |
bixi |
bijxixj |
||||
|
i 1 |
|
i, j 1 |
|
|
где yˆ – расчетные значения критерия оптимизации; bi – линейные коэффициенты; bij – коэффициенты двойного взаимодействия факторов; k – число факторов. Далее проводят расчет коэффициентов b и анализ уравнения методами статистики.
Если линейного приближения недостаточно для математического описания объекта исследований с нужной точностью, то возникает необходимость в построении моделей в виде полиномов второй степени. Для этого используют планы Хартли, а также ортогональные и ротатабельные планы.
При ротатабельном планировании эксперимента второго порядка достраивают план ПФЭ до плана второго порядка добавлением к «ядру» определенного количества «звездных» и нулевых точек (табл. 2). В качестве «ядра» используют матрицу ПФЭ (табл. 1). «Звездные» точки строят на осях координат на расстоянии «звездного» плеча от нулевой точки. Такое планирование является центральным, т. к. все экспериментальные точки располагаются симметрично относительно центра эксперимента (рис. 3).
В общем случае уравнение регрессии, полученное в результате ротатабельного планирования эксперимента, имеет вид
k |
k |
yˆ b0 bixi |
bij xixj |
i 1 |
i, j 1 |
|
k |
x |
2 |
... |
(2) |
b |
|||||
|
ii |
|
i |
|
|
i 1
|
|
|
|
|
|
|
|
|
Таблица 2 |
|
|
|
|
|
|
|
Матрица ротатабельного |
||
c2 |
+x2 |
|
c3 |
+x3 |
|
|
планирования при k = 2 |
||
2 |
8 |
1 |
8 |
6 |
14 |
5 |
№ |
x1 |
x2 |
+ |
|
7 |
+x2 |
опыта |
|||||
5 |
6 |
|
|
|
12 10 |
1 |
+ |
+ |
|
+1 |
9 |
|
|
||||||
|
- |
+x1 |
|
11 |
|
1 +x1 |
2 |
– |
+ |
4 |
- |
3 |
|
2 |
|
3 |
+ |
– |
|
7 |
4 |
|
3 |
4 |
– |
– |
|||
|
c1 |
13 |
|
5 |
– |
0 |
|||
|
k = 2 |
|
|
|
c1 |
||||
|
|
k = 3 |
6 |
1,414 |
0 |
||||
|
|
c2 |
|||||||
|
|
|
|
|
|
7 |
+ |
– |
|
|
|
|
|
|
|
|
|||
|
Рис. 3. Расположение точек |
|
8 |
1,414 |
1,414 |
||||
|
|
|
0 |
+ |
|||||
ротатабельного плана второго порядка |
|
||||||||
|
0 |
1,414 |
|||||||
|
|
|
|
|
|
|
|
||
|
|
|
|
|
|
|
9 |
0 |
0 |
Ротатабельное планирование было применено при исследовании влияния электрического тока на коэффициент сцепления локомотива. Объектом исследования являлся натурный стенд, разработанный и изготовленный в лаборатории кафедры «Подвижной состав железных дорог».
52
Основу стенда составляет трибологическая пара «колесо локомотива – рельс».
На основании закона локомотивной тяги (Fкл = ψηG) в качестве основных (управляющих) факторов были приняты сила вертикального нагружения колеса Fв, и сила электрического тока I, подаваемого в зону контакта колеса и рельса. Для обеспечения необходимой достоверности результатов испытаний уровни варьирования факторов были выбраны в соответствии с техническими возможностями и рабочими характеристиками локомотивов.
Для Fв уровни варьирования выбраны на основании анализа нагрузок на ось отечественных тепловозов, которые изменяются от 170 кН (17 тс) для тепловоза ТГМ6 до 230 кН (23 тс) для 2ТЭ10М, 2ТЭ116 и 2ТЭ25К. Таким образом, для одного колеса диапазон значений силы Fв составил (кН)
85 ≤ Fв ≤ 115. (3) Границы диапазона значений I (А) назначены на основании анализа рабочих характеристик современных тяговых генераторов тепловозов, используемых на железнодорожном транспорте России, и на основании
предварительныхопытов:
600 ≤ I ≤ 3000. (4) Предварительные опыты выявили значительное влияние силы тока I на коэффициент сцепления ψ, которое имеет нелинейный характер. Поэтому для получения математических моделей рассматриваемых процессов был
использован ротатабельный план второго порядка.
Для выделенной области факторного пространства кодированные и натуральные значения основных факторов, принятых для исследования коэффициента сцепления, приведены в табл 3.
Кодированные и натуральные значения факторов |
Таблица 3 |
|||||||||||
|
|
|||||||||||
Факторы |
|
Интервалы |
|
Уровни варьирования |
||||||||
|
варьирования (ε) |
–1,414 |
|
–1 |
|
0 |
+1 |
|
+1,414 |
|||
|
|
|
|
|
||||||||
Fв, кН (х1) |
|
15 |
|
79 |
85 |
|
100 |
115 |
|
121 |
||
I, А (х2) |
|
1200 |
100 |
600 |
|
1800 |
3000 |
|
3500 |
|||
Проведение |
экспериментов |
осуществлялось на основании матрицы |
||||||||||
ротатабельного планирования (табл. 4). |
|
|
|
|
|
|
|
Таблица 4 |
||||
|
Матрицы ротатабельного планирования |
|
|
|||||||||
|
|
|
|
|
||||||||
№ опыта |
Матрица планирования |
|
|
Рабочая матрица |
||||||||
|
х1 |
|
х2 |
|
Fв, кН |
|
|
|
I, А |
|||
|
|
|
|
|
|
|
||||||
1 |
+ |
|
+ |
|
|
115 |
|
|
3000 |
|||
2 |
|
– |
|
+ |
|
|
85 |
|
|
3000 |
||
3 |
+ |
|
– |
|
|
115 |
|
|
600 |
|||
4 |
|
– |
|
– |
|
|
85 |
|
|
600 |
||
5 |
|
–1,414 |
|
0 |
|
|
79 |
|
|
1800 |
||
6 |
+1,414 |
|
0 |
|
|
121 |
|
|
1800 |
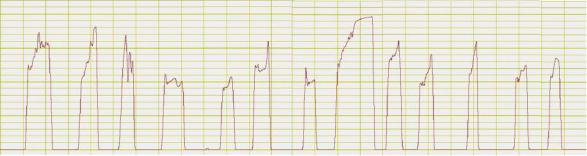
53
7 |
0 |
–1,414 |
100 |
100 |
8 |
0 |
+1,414 |
100 |
3500 |
9 |
0 |
0 |
100 |
1800 |
10 |
0 |
0 |
100 |
1800 |
11 |
0 |
0 |
100 |
1800 |
12 |
0 |
0 |
100 |
1800 |
13 |
0 |
0 |
100 |
1800 |
В качестве контролируемого фактора была принята степень загрязнения контакта колеса и рельса, т. е. наличие в контакте машинного
Fк |
Опыт № |
№ |
|
№ |
№ |
№ |
|
№ |
|
№ 9 |
№ |
||||
, |
|
№ 4 |
№ |
№ |
№ |
№ |
|
|
|
|
|
||||
10 |
|
|
|
|
|
||
|
|
|
|
|
|
|
|
5 |
|
|
|
|
|
|
|
0 |
10 |
2 3 40 |
50 6 70 |
80 90 10 |
11 t, |
||
|
|
Рис. 4. Осциллограмма цикла экспериментов |
|
|
масла.
Осциллограмма цикла экспериментов при воздействии на зону контакта колеса и рельса постоянным током и при наличии в контакте машинного масла приведена на рис. 4. На основании осциллограммы рассчитаны экспериментальные значения коэффициента сцепления (табл . 5).
Таблица 5
Экспериментальные значения коэффициента сцепления
№ опыта |
1 |
2 |
3 |
4 |
5 |
6 |
7 |
|
|||||||
|
|
|
|
|
|
|
|
yи = ψ |
0,261 |
0,282 |
0,1 |
0,124 |
0,177 |
0,149 |
0,12 |
|
|||||||
|
|
|
|
|
|
|
|
№ опыта |
8 |
9 |
10 |
11 |
12 |
13 |
Σ |
|
|||||||
|
|
|
|
|
|
|
|
yи = ψ |
0,27 |
0,17 |
0,173 |
0,168 |
0,172 |
0,165 |
2,323 |
|
|||||||
|
|
|
|
|
|
|
|
После расчета коэффициентов регрессии и выполненного статистического анализа была получена регрессионная математическая модель процесса:
0,177 7,13 10 4 Fв 1,62 10 5I 1,09 10 8I2.
(5)
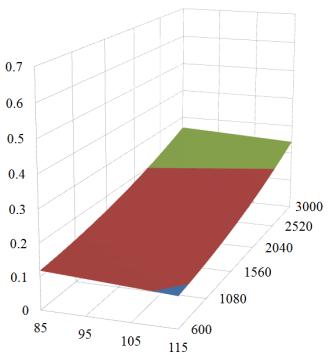
54
На основании уравнения (5) построена графическая зависимость предельного коэффициента сцепления от силы постоянного тока I и силы вертикального нагружения Fв при наличии в контакте колеса и рельса машинного масла
(рис. 5).
ψ
I, А
Fв, кН
Полученную регрессионную модель процесса можно использовать для прогнозирования тяговых качеств локомотивов в рассмотренных выше условиях.
Доклад подготовлен под руководством доц. Ивахина А.И.
Н.И.Товпеко, О.Б. Никитенко ИСПОЛЬЗОВАНИЕ НЕПАРАМЕТРИЧЕСКОГО ПРОГНОЗИРОВАНИЯ ДЛЯ ПОИСКА НОВЫХ ТЕХНИЧЕСКИХ КОНЦЕПЦИЙ. УСТАНОВКА ДЛЯ ОПРЕДЕЛЕНИЯ КОЭФФИЦИЕНТА ТРЕНИЯ
Объект исследования: непараметрическое прогнозирование. Результаты, полученные лично автором: было использовано
непараметрическое прогнозирование для поиска новых технических концепций на примере установки для определения коэффициента трения.
К непараметрическому прогнозированию относят прогнозирование появления новых технических идей, сущность которого заключается в генерации изобретательских решений для прогнозируемого развития потребностей, с последующим их исследованием и отбором тех, которые с наибольшей вероятностью могут быть реализованы в рассматриваемое время.
55
При использовании непараметрического прогнозирования для поиска новых технических концепций целью прогноза становится выявление ситуации, когда прогнозный рост потребностей лимитирован ограниченными возможностями. В качестве основного метода анализа авторами предложено использовать матрицу развития потребностей и возможностей их удовлетворения.
Метод матрицы развития потребностей был использовандля прогнозирования развития противобоксовочных систем локомотива, в результате чего был получен прогноз о том, что в будущем функции противобоксовочной системы радикально изменятся, и основной функцией станет управление сцепными свойствами в системе «колесо-рельс», основанное на прогнозировании изменение сцепных свойств под действием внешних факторов.
На каждом из рассматриваемых этапов развития концепции машины или узла, соответствующую этому этапу (современную ему) можно рассматривать, как общий способ решения проблемы надсистемы, в которую входит данная машина или узел. Это решение формируется, с одной стороны, задачей, постановка которой предопределена потребностями, порожденными общей проблемой надсистемы, а с другой, ресурсами, которыми производитель может располагать на данном этапе. Рассмотренную матрицу развития потребностей и технических возможностей их удовлетворения можно рассматривать как реинвентирование процесса выработки общих концепций этапа развития.
С целью исследования описанной системы, с участием автора, была разработана установка для определения коэффициента трения, на которую был получен патент на полезную модель №14958.Предлагаемое техническое решение, разработанное с использованием метода непараметрического прогнозирования, предназначено для определения коэффициента трения в трущихся парах деталей машин. Использование предлагаемого технического решения способствует приближению условий проведения испытаний для измерения силы трения к эксплуатационным условиям.
Работа выполнена под руководством доцента, к.т.н. В.И. Воробьева
Е.М.Чепурная РАЗРАБОТКАНОВОЙКОНСТРУКЦИИРАМЫПЛАТФОРМЫ
ДЛЯКОНТЕЙНЕРНО-КОНТРЕЙЛЕРНЫХПЕРЕВОЗОКИВЫБОР РАЦИОНАЛЬНЫХСЕЧЕНИЙЭЛЕМЕНТОВКОНСТРУКЦИИ
Объект исследования: вагон-платформа для контрейлерноконтейнерных перевозок.
Результаты, полученные лично автором: разработана детализированная пластинчато-стержневая конечно-элементная модель вагона-платформы для контрейлерно-контейнерных перевозок, выполнен анализ нагруженности несущей конструкции вагона-платформы.
56
Комбинированные автомобильно-железнодорожные перевозки являются на сегодняшний день одним из перспективных способов сухопутной транспортировки широкого спектра грузов, так как позволяет совместить доставку "от двери до двери" автомобильным транспортом с такими преимуществами железнодорожного транспорта, как низкая себестоимость перевозки на большие расстояния и меньший вред для окружающей среды.
Контрейлерные перевозки относятся к интермодальным. Этот термин означает перевозку груза в одной таре или транспортном средстве на нескольких видах транспорта без перегрузки самого груза (транспортной единицей может быть контейнер, автопоезд и/или полуприцеп).
К месту погрузки на железнодорожный состав автопоезда подъезжают своим ходом и ожидают отправки на специальной площадке. Состав подается к рампе, с которой автопоезда заезжают на платформы. Время погрузки автопоезда - 8 минут. После «раскрепления» автопоезда лобовые и боковые стекла кабин закрываются листами фанеры или картона.
Прицепы закрываются и опечатываются согласно обычному таможенному порядку. Оформление документов при пересечении границы производит дирекция поезда, а водители и сопровождающие груз лица, находящиеся во время движения в пассажирских вагонах состава, проходят пограничное оформление как обычные пассажиры.
Основной задачей при проектировании платформы для автопоездов и крупнотоннажных контейнеров являлось снижение массы тары, а соответственно и увеличение ее грузоподъемности. С этой целью в конструкции рамы предусмотрены боковые обвязки, выполненные в виде объемно-пространственных ферм. Это связано с тем, что ферма имеет большую жесткость при меньшей металлоемкости
В работе предложена детализированная пластинчато-стержневая конечно-элементная расчетная схема, разработанная на основе пространственной трехмерной модели конструкции вагона-платформыдля контрейлерно-контейнерных перевозок в среде программного комплекса
Femap 10.3.
При оценкенагруженности вагона-платформы рассматривалисьтри варианта загрузки вагона-платформы: двумя 40-футовыми контейнерами; тремя 20-футовыми контейнерами и автопоездом с трехосным полуприцепом.
Расчет проводился в статической постановке от нагрузок соответствующих расчетным режимам «Норм…».
Расчеты показали,что наибольшие напряжения возникают при загрузке вагона двумя 40-футовыми контейнерами под действием сжимающих нагрузок первого расчетного режима.
Наиболее нагруженными узлами оказались узлы соединения балки шкворневой с раскосами и балки шкворневой с боковой обвязкой рамы. В них напряжения достигли 291.7 МПа. Также вторым по-нагруженности
57
оказался узел соединения шкворневой балки с хребтовой. В нем напряжения достигли 230 МПа.
В результате расчетов была выбрана сталь для изготовления данного вагона, а именно сталь 10 ХНДП с пределом текучести 350 МПа.
Произведен выбор рационального сечения верхней обвязки фермы. Производилось исследование напряженно-деформированного состояния платформы при изготовлении верхней обвязки их двух швеллеров №33, №30, №27, а также из профиля 300х200х6.5, при неизменных вертикальных стойках фермы рамы вагона-платформы, выполненных из швеллера №22.
Результаты исследования показали, что наиболее рациональной является конструкция , в которой верхняя обвязка фермы рамы вагона-платформы выполнена из двух швеллеров № 30. Максимальные напряжения,возникающие в раме достигают 296,5 МПа, что меньше допустимых напряжений по первому расчетному режиму.
Выполнен анализ напряженно-деформированного состояния конструкции при изготовлении вертикальных стоек фермы из швеллеров №18а, №20, №22, №24, при верхней обвязке из двух швеллеров №30.
На основании расчета сделан вывод о том, что наиболее рациональной является конструкция, в которой верхняя обвязка выполнена из двух швеллеров №30, а стойки остаются неизменными и выполняются из швеллера №22
Предлагаемая конструкция верхней обвязки фермы, выполненной из 2-х швеллеров №30, имеет меньший вес по сравнению с конструкцией верхней обвязки фермы, выполненной из 2-х швеллеров №33, на 120 кг. Это обеспечивает общее снижение металлоемкости конструкции рамы на 240 кг.
Оценка прочности предлагаемой конструкции рамы платформы при действии нагрузок по I и III режимам подтвердила её работоспособность.
Работа выполнена под руководством проф. В.В. Кобищанова
П.И. Шалупина ИННОВАЦИОННЫЕ РЕШЕНИЯ В ОБЛАСТИ
ТЯГОВОГОПОДВИЖНОГО СОСТАВА ЖЕЛЕЗНЫХ ДОРОГ
Объект исследования: инновационные решения в области тягового подвижного состава.
Результаты, полученные лично автором: детальнорассмотрены современные решения в области тягового подвижного состава.
Ведущим звеном российской транспортной системы являются железные дороги, они исполняют роль основного элемента в производственной инфраструктуре. Тем не менее, заметно снизился приток инвестиций в железнодорожный транспорт. В связи с этим большая часть проблем, существующих на данный момент, в железнодорожной отрасли остается без должного внимания.
58
В данной работе подробно изучена проблема использования топливно-энергетических ресурсов и ее решение в свете внедрения инновационных решений в области подвижного состава железных дорог.
Вобласти производства железнодорожной техники ведется постоянная борьба между крупными компаниями-производителями, заключающаяся в разработке новейших технологий, которые смогли бы обеспечить снижение потребления энергетических ресурсов, а также значительное сокращение выбросов вредных веществ в окружающую среду. Такое стремление западных компаний связано с ужесточением норм загрязнения окружающей среды в Евросоюзе, а также неуклонным ростом цен на топливно-энергетические ресурсы в последние годы.
Внастоящее время выделяют три основных направления инновационной работы в области производства тяговой железнодорожной техники:
использование двух энергетических установок (дизелей) в одной секции тепловоза;
развитие гибридной тяги;
использование в качестве накопителей энергии высокопроизводительных и надежных суперконденсаторов;
активное внедрение газотурбовозов.
Наиболее компромиссным и сбалансированным решением в данных обстоятельствах, по мнению ряда экспертов, является широкое применение локомотивов с гибридным тяговым приводом.
Основные конструктивные элементы гибридной установки (рис. 1):
двигатель внутреннего сгорания;
редукторы, оси;
гидравлическая система.
На борту локомотива также необходимо наличие двигателягенератора, силовой электроники и накопителя энергии (аккумуляторные батареи или суперконденсаторы).Тяговая силовая установка гибридного локомотива может представлять собой водородный двигатель, работающий за счет протекающей химической реакции между водородом и кислородом. В данном исполнении накопители энергии заряжаются во время торможения.
В настоящее время производство гибридных локомотивов освоено ЗАО «УК «БМЗ». Гибридным является локомотив ТЭМ35 – маневровый тепловоз, предназначенный для среднетяжелых маневровых работ. Номинальная энергоемкость накопителей энергии (суперконденсаторов) данного локомотива составляет 22,7, МДж.
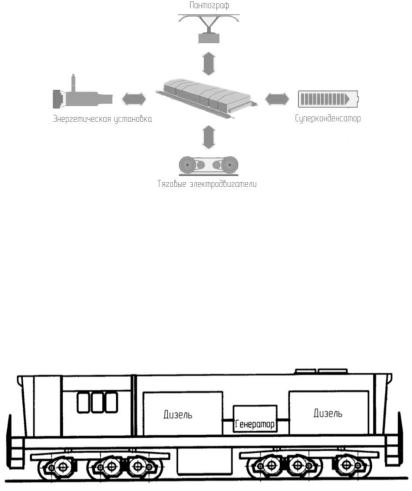
59
Рис. 1. Конструктивные элементы гибридной установки Также целесообразно развитие производства двухдизельных
тепловозов (рис. 2). Использование двух дизелей в конструкции тепловоза позволяет получить большие значения мощности тяговых единиц, что является необходимым при грузоперевозках. Особенностью данного типа тепловозов является то, что один из дизелей может не работать в случае необходимости.
Рис. 2. Пример схемы реализации двухдизельной конструкции В заключение, стоит отметить, что одним из главных направлений
развития железных дорог мира является энергосбережение. Возрастающие экологические требования и повышение цен на топливо привлекают внимание общественности к вопросу эффективности использования энергоресурсов. Более того, компании-производители крайне положительно реагируют на малейшую возможность создания инновационного продукта с низким потреблением топлива.
Работа выполнена под руководством проф.кафедры «Подвижной состав железных дорог» Г.С. Михальченко
ПОДЪЕМНО-ТРАНСПОРТНЫЕ МАШИНЫ И ОБОРУДОВАНИЕ
А.А. Боборыкин ПЛАСТИНЧАТЫЙ КОНВЕЙЕР И МЕТАЛЛООТДЕЛИТЕЛЬ
Объект исследования: пластинчатый конвейер и металлоотделитель Результаты, полученные лично автором: рассмотрены конструкции и принцип действия типового пластинчатого конвейера и
металлоотделителя
60
Пластинчатый конвейер и металлоотделитель входят в состав схемы механизации по транспортировке горелой земли. Горелая земля поступает из литейного цеха предприятия и в своем составе имеет ферромагнитные включения, от которых нужно избавиться и отправить их, включения, на переплавку, а очищенную землю – для повторного создания литейных форм. В связи с этим и возникает необходимость включения в транспортную линию металлоотделителя.
В производстве используются металлоотделители различных видов: магнитные барабаны, магнитные решетки, магнитные сепараторы и магнитные плиты с механической или автоматической очисткой. В данном случае для исследования была выбрана магнитная плита с автоматической очисткой. Установка других типов отделителей в данном случае неудобна по конструктивным или технологическим причинам.
Упомянутый ранее металлоотделитель представляет собой небольшой ленточный конвейер длиной 2450 мм. Его основными элементами являются: металлоконструкция, приводной барабан с приводом от моторредуктораMMRV050, натяжной барабан с винтовым натяжным устройством, специальная конвейерная лента и магнитные плиты (основная и дополнительная).
Выбор мотор-редуктора в качестве привода осуществляется из необходимости соблюдения небольших габаритов конструкции. Использование винтового натяжного устройства связанно с компактными размерами конструкции относительно типовых ленточных конвейеров, небольшим ходом натяжки, меньшей стоимостью по сравнению с другими натяжными устройствами и собственной компактностью относительно других натяжных устройств, применяемых в конструкциях ленточных конвейеров. Установка тормозного устройства в данной конструкции не предусмотрена за отсутствием необходимости – во время работы отделителя не возникает огромных динамических нагрузок, которые необходимо гасить.
Установка металлоотделителя должна производиться на определенной высоте – не более 350 мм. Это связанно с потерей эффективности используемых электромагнитов при увеличении расстояния между отделителем и поверхностью, с которой производится отбор ферромагнитных включений. Отделитель может размещаться как с закреплением на металлоконструкции основного конвейера, в этом случае должны применяться дополнительно устанавливаемые стойки, так и путем подвешивания на стропах. Во втором случае отделитель можно использовать сразу для нескольких конвейеров путем подвешивания его на грузовой тали или ином устройстве, способном перемещать отделитель.
Для рассматриваемого типа металлоотделителя существует две принципиальные схемы размещения: перпендикулярно движению ленты основного конвейера и параллельно с ним. В первом случае установка отделителя может производиться как вблизи зоны разгрузки, так и по остальной длине конвейера. В последнем случае отделитель можно