
Сборник 70 студ конференции БГТУ
.pdf181
Работа по типизации ТП деталей «Вал» является базой построения алгоритмов. В качестве основы используем типовые решения в сочетании с индивидуальными, учитывающими особенности предприятий и отдельных отраслей в машиностроении. Для данного класса (группы, подгруппы или вида деталей) устанавливаем так называемый обобщенный маршрут обработки, характерный для определенного класса, подкласса или группы деталей. Этот перечень является упорядоченным и представляет собой множество существующих единичных маршрутов, которые имеют типовые последовательность и содержание.
Необходимое условие включения единичных маршрутов в обобщенный
— наличие области пересечения операций, например маршрутов Mi и Mj как непустого множества.
Каждой операции обобщенного маршрута соответствует логическая функция. Она зависит от условий, учитывающих геометрические особенности поверхностей, вид заготовки, требуемую точность обработки, качество поверхностного слоя детали, размер партии, габариты деталей.
В общем случае логическая функция выбора k-й операции имеет вид
n |
|
|
n |
|
|
|
|
|
2 |
|
1 |
|
|
fk |
|
|
Ai |
|||
|
|
|
|
|
|
|
j 1 i 1 |
j k |
где Ai — условие назначения операций;
j=1,2, ..., n1 — число условий, связанных конъюнкцией; j =1,2,..., n2 — число условий, связанных дизъюнкцией;
к = 1, 2,..., n3 — количество операций в обобщенном маршруте.
Тогда логическую функцию, определяющую обобщенный маршрут, можно представить в следующем виде:
3n2 n1
Фn
k 1 j 1 i 1
Ai
j k
где k=1, 2,..., n3 — число операций в обобщенном маршруте. Синтез индивидуальных технологических маршрутов осуществляется путем их выделения из обобщенного маршрута. Обобщенный маршрут содержит логические функции, соответствующие каждой операции:
n |
|
|
n |
|
|
|
|
|
2 |
|
1 |
|
|
f |
|
|
|
Ai |
|
|
|
|
|
|
|
|
|
j 1 i 1 |
j |
Схема алгоритма решения данной задачи представляет собой: Блок 1, который вызывает обобщенный маршрут обработки деталей с кодами операций и логическими функциями fk; Блок 2, осуществляющий вызов условий, характерных для данной детали Лд (например, особенности геометрии, точность, качество поверхностного слоя, требования к контролю и др.); Блок 3 для вызова k-й операции обобщенного маршрута My с
182
логической функцией fk. Если логическая функция fk равна 1, то операция включается в результирующий маршрут.
Если fk = 0, то из расчетного блока автоматизированной подсистемы дается команда на вызов следующей операции обобщенного маршрута до тех пор, пока не будут просмотрены все его операции.
В данной статье по типизации ТП деталей типа «Вал» рассматриваем реализацию описанного метода в САПР ТП «ТехноПро». Одним из основных режимов работы «ТехноПро» является автоматическое проектирование ТП на базе обобщенных ТП (ОТП). При этом предполагаются два этапа, выполняемых в различных модулях системы отдельными пользователями: 1. Проектирование ОТП. 2. Автоматизированное проектирование конкретного (индивидуального ТП) на базе созданного ОТП.
Создание ОТП производится в следующей последовательности: один из технологических процессов группы принимается за базовый и вводится в
виде ОТП в диалоговом режиме (можно скопировать один из КТП), затем в него добавляются недостающие операции и переходы из других ТП (КТП).
Автоматическое проектирование технологических процессов основано на информации внесенной в базу ОТП. База ОТП создается пользователями на основе технологических процессов, уже апробированных в производстве или новых, - внедряемых в производство. ОТП охватывают технологию изготовления определенных групп изделий, классифицируемых по конструктивно-технологическим признакам, содержат операции и переходы с перечнями применяемой в них оснастки и инструмента.
Таким образом, ТехноПро обеспечивает автоматическое формирование текстов переходов, содержащих значения любых параметров детали, элементов, режимов, оснастки и других параметров технологического процесса.
Работа выполнена под руководством доц. каф. «Технология машиностроения» Е.А. Польского
А.И. Сидоренкова ТЕХНОЛОГИЧЕСКОЕ ОБЕСПЕЧЕНИЕ ЭКСПЛУАТАЦИОННЫХ СВОЙСТВ ДЕТАЛЕЙ ОПОРНО-УПОРНЫХ ПОДШИПНИКОВ
ТУРБИН
Объект исследования: детали узлов опорно-упорных подшипников свободных турбин, подлежащие изготовлению на ремонтных предприятиях ОАО «Газэнергосервис».
Результаты, полученные лично автором: разработан научный подход к нормированию параметров качества и точности рабочих поверхностей деталей типа сухарь для обеспечения требуемых показателей надежности сборочных узлов для заданных условий эксплуатации.
Важнейшим этапом жизненного цикла рабочих поверхностей деталей является проектирование, когда закладываются требования к их качеству или
183
непосредственно к эксплуатационным свойствам (а именно контактной жесткости). Эти требования должны формироваться исходя из физической картины контактного взаимодействия деталей и обеспечения оптимальной надежности изделий машиностроения.
В формализованном виде процесс обеспечения технологичности изделия можно представить как воздействие на множество параметров точности размеров изделия X={x1,...,xn}, которое приводит к достижению экстремальной цели при соблюдении сформулированных ограничений вида
gi(X) 0 |
и hj (X) 0 [2]. |
|
|
|
|
|
Q(X) extr |
|
|
|
|
|
|
X S |
|
|
|
|
|
|
|
|
|
|
|
i 1,I; |
|||
|
gi(X) 0, |
||||
|
S : |
|
|
|
|
|
(X) 0, |
j 1,J, |
|||
|
h |
||||
|
j |
|
|
|
|
где Q, g, h - функции, которые определяются исходя из требований точности размеров изделия и разнообразных производственных, эксплуатационных и ремонтных факторов, влияющих на технологичность изделий.
В рассмотренной методике размерного анализа и расчёта размерных цепей размерная структура техпроцесса представляется в двух основных видах: в виде размерной схемы и в виде размерного графа, объединяющего размеры детали, заготовки и техпроцесса
G Gдет,Gзаг,Gтех ,
где Gдет - граф конструкторских размеров детали, Gзаг - граф конструкторских размеров исходной заготовки, Gтех - граф технологических размеров и припусков ТП механической обработки.
Часть ограничений учитывается при построении матрицы типовой размерной структуры ТП, для учета остальных на основе МСЭД создаем матрицу точности и свойств поверхностей (ТСП), записывая в матрице экономических допусков нули вместо допуска для тех случаев, когда простановка размера между поверхностями не возможна
Размерно-точностной анализ технологического процесса оптимизируется по критериям минимизации припуска и (или) миниммуму рабочих ходов при различных схемах простановки операционных размеров.
В рамках выпускной квалификационной работы мной рассмотрены технологические методы формирования рабочих поверхностей деталей упорного подшипника – Сухаря верхнего и Сухаря нижнего. Для данных деталей характерно упругое контактное взаимодействие. Детали входят в состав самоустанавливающегося упорного подшипника, расположенного внутри статора, и компенсируют отклонения от форм поверхностей и осевое смещение ротора. Основным эксплуатационным свойством для данных деталей является контактная жесткость. Необходимо было провести анализ контактного взаимодействия деталей в сборке, задачей проведения которого являлось подтверждение правильности назначения параметров качества на
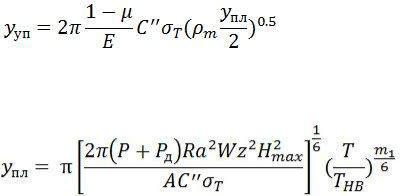
184
контактирующие поверхности и механические свойства материала для обеспечения заданной долговечности.
Контактная жесткость определяет способность поверхностных слоев деталей, находящихся в контакте, сопротивляться действию сил, стремящихся их деформировать. Вершины выступов поверхностей деталей, вступивших в контакт, имеют переходный характер деформаций от упругих к пластическим. Этот переход обусловлен величиной критического сближения. Если контактное перемещение вершин выступов меньше критического, то они будут иметь упругий характер деформаций, а если больше, то вершины будут находиться в режиме пластических деформаций.
В общем виде эти упругие контактные деформации могут быть рассчитаны по следующей формуле:
Данные детали работают при динамическом воздействии нагрузок, вызывающих увеличение пластических контактных деформаций, которые рассчитываются из уравнения:
Учитывая высокие требования по прочности, а так же требования по обеспечению заданной контактной жесткости, был выполнен контроль отсутствия внутренних дефектов и наружных трещин. Из расчета величин упругих и пластических контактных деформаций рассматриваемых деталей, можно сделать вывод, что для уменьшения величины пластического выдавливания необходимо скорректировать параметр шероховатости, заданный конструктором, с Ra6,3 мкм до Ra3,2 мкм.
Работа выполнена под руководством зав. каф. "Технология машиностроения", к.т.н., доц. Е.А. Польского
К.А. Смолякова РАЗРАБОТКА АВТОМАТИЗИРОВАННОЙ СИСТЕМЫ
ОПРЕДЕЛЕНИЯ ТИПА ПРОИЗВОДСТВА
Объект исследования: этап технологической подготовки производства по определению типа производства.
Результаты, полученные лично автором: разработан программный модуль автоматизированной подсистемы расчета показателей участка механического цеха для определения типа производства.
Одной из основных задач технологической подготовки производства является проектирование технологических процессов изготовления деталей нового изделия. Только после её решения можно приступать к проектированию и изготовлению специальной оснастки и инструмента,
185
оформлению заявок на поставку стандартного и нормализованного инструмента, проката. Поэтому автоматизация технологической подготовки производства предусматривает в первую очередь применение ЭВМ в процессе технологического проектирования.
Расчётные технологические задачи являются первыми, для которых были созданы методы решения на ЭВМ и реализованы на промышленном уровне. Проектирование техпроцесса предусматривает обязательное решение целого ряда задач. Актуальность темы состоит в разработке автоматизированной системы определения типа производства, который необходим для автоматизации управления на предприятии. Правильное определение типа производства позволяет выбрать эффективный метод его организации, то есть ответить на вопрос, как эффективнее осуществить производственный процесс.
Создание автоматизированной системы определения типа производства актуально, поскольку это позволяет сократить время на проектирование, пользователь имеет возможность внести свои данные и тут же получить результат.
Тип производства в соответствии с ГОСТ 3.1108-74 характеризуется коэффициентом закрепления операций Кз.о.
Для расчета Кз.о. используются следующие параметры:
наименование операции;
модель оборудования;
штучное tшт или штучно-калькуляционное tшт-к время, мин;
годовая программа выпуска деталей.
Система проектирования состоит из нескольких форм. В первой форме пользователь может произвести предварительное определение типа производства, а также уточнение типа производства. Предварительно тип производства может быть определен по годовому объему выпуска и массе деталей или по количеству деталей в партии и массе деталей. Для уточнения типа производства пользователь вводит исходные данные, необходимые для расчета. Ввод операций техпроцесса производится путем нажатия кнопки «Добавить операцию», «Новая операция», в которой вводится необходимая информация.
После ввода всех операций техпроцесса пользователю необходимо нажать на кнопку «Оптимизация», в которой происходит расчет необходимых параметров и найденное значение Кз.о. и типа производства деталей выдается на экран в соответствующих полях (рис. 1).
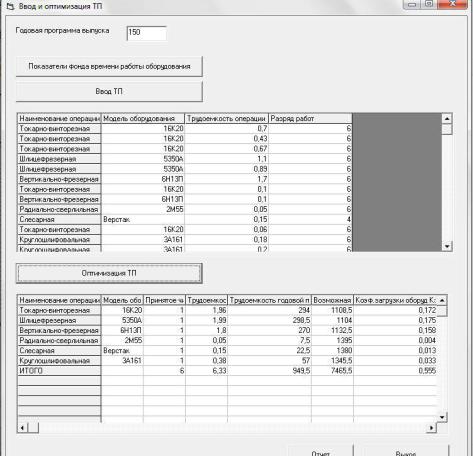
186
Рис. 1. Главная форма автоматизированной системы.
Если производство – серийное, система позволяет определить размер партии выпуска деталей. Для этого необходимо нажать на соответствующую кнопку. В форме для расчета размера партии деталей после ввода необходимых данных, происходит расчет, и искомая величина размера партии выдается в одноименном поле. Если производство деталей – крупносерийное или массовое, то необходимо определить такт выпуска деталей. Для этого пользователю необходимо нажать на кнопку «Определение такта выпуска деталей», после чего произойдет расчет и в соответствующем поле появится значение такта выпуска деталей.
После определения всех необходимых параметров, если пользователю необходимо создать отчет, он нажимает на кнопку «Отчет» и происходит формирование отчета в текстовом редакторе.
Данная система разработана с целью сокращения времени определения типа производства, снижения себестоимости проектирования, и максимального упрощения расчетов, что приведет к снижению рисков возникновения ошибок при проектировании.
Работа выполнена под руководством доц. каф. «Технология машиностроения» Е.А. Польского, С.В. Сорокина
Р
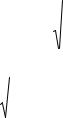
187
.П. Соломян, М.И. Чумичев ТЕХНОЛОГИЧЕСКОЕ ОБЕСПЕЧЕНИЕ ПАРАМЕТРОВ ИНЖЕНЕРИИ ПОВЕРХНОСТИ ДЛЯ ДОСТИЖЕНИЯ УСТАНОВЛЕННОЙ НАДЕЖНОСТИ УЗЛОВ МАШИН
Объект исследования: детали узлов трения машин, работающих в условиях контактного деформирования и граничного трения.
Результаты, полученные лично автором: разработан научный подход к нормированию параметров инженерии поверхности для достижения установленных показателей надежности, в частности, долговечности работы пар трения.
Качество машин и его главный показатель – надежность – определяются надежностью соединения деталей. Технологический аспект рассмотрения надежности соединений становиться одним из важнейших и исследуется наряду с конструкционными аспектами.
Качество машин определяется непосредственно качеством соединений. В свою очередь, показатели качества имеют широкие границы рассеивания.
|
|
|
|
|
|
|
|
|
|
|
|
|
|
|
|
|
H7 |
|||||
Оно может существенно изменяться даже от колебаний |
фактических |
|||||||||||||||||||||
размеров в пределах допусков. Так, |
например, в пределах посадки |
s6 |
|
|
натяг, |
|||||||||||||||||
|
|
|
|
|
|
|
|
|
|
|
|
|
|
|
|
|
|
|
|
H7 |
||
а, следовательно, и прочность посадок, как один из показателей качества в |
||||||||||||||||||||||
диапазоне диаметров 80…120 мм меняется в 3,5 раза, а для посадки |
|
|
p6 в 7 |
|||||||||||||||||||
раз. |
|
|
|
|
|
|
|
|
|
|
|
|
|
|
|
|
|
|
|
|
|
|
Основные положения и методика расчета поверхностей на трение и |
||||||||||||||||||||||
износ при скольжении изложены в работах Суслова А.Г.: |
|
|
|
|
|
|||||||||||||||||
Приработка: |
|
|
|
|
7/6 |
|
|
|
|
|
|
|
|
|
|
|
|
|||||
|
|
|
|
1.2 Ra |
2/3 |
|
|
p |
|
|
|
|
2 H 0 1 |
2 |
|
|
||||||
|
|
|
|
|
|
|
|
|
|
1/3 |
|
|
|
|
||||||||
Ih |
|
|
|
|
|
|
15 |
2 Wz Hmax |
1 |
|
|
|
|
|||||||||
n Sm tm3/2 |
H |
E |
|
|
||||||||||||||||||
|
|
|
|
|
|
|
0 |
|
|
|
|
|
|
|
|
|
|
|||||
Нормальное изнашивание: |
|
|
|
|
|
|
|
|
|
|
||||||||||||
|
|
|
|
|
|
|
|
|
|
|
|
|
|
|
|
|
||||||
I |
h |
|
|
1.2 p7/6 |
|
|
|
30 (1 2) (2 Ra Wz Hmax)1/3 |
|
|
|
|
|
|
|
|
||||||
|
n tm3/2 H 03/2 |
|
|
|
E Sm |
|
|
|
|
|
|
|
|
|
||||||||
|
|
|
|
|
|
|
|
|
|
|
|
|
|
|
Учитывая довольно тесную корреляционную связь упругих и пластических деформаций, зависимости определения контактной жесткости примут вид:
|
|
|
2 P |
|
2 |
2 |
H max |
2 |
|
1/3 |
|
||||
упл1 |
|
|
Ra1 |
Wz1 |
1 |
|
|
|
|||||||
|
|
|
|
|
|
|
|
|
|||||||
|
|
|
A Uн1 Т1 |
|
|
|
|
|
|
||||||
|
|
|
|
|
|
|
|
|
|
|
|||||
|
|
|
|
|
2 |
|
|
|
|
|
|
|
|
|
0.5 |
|
|
|
|
|
|
|
|
|
|
|
|
упл1 |
|
||
|
|
|
|
1 1 |
|
|
|
|
|
|
|||||
ууп1 |
|
Uн1 |
|
Sm1 |
|
|
|
||||||||
E |
|
|
|
Ra |
|||||||||||
1 |
Т1 |
|
|
|
|||||||||||
|
|
|
|
|
|
|
|
|
|
|
1 |
|
Рассмотрение действий контактных деформаций поверхности и изнашивания раздельно, вводит некоторую неточность в расчет, но позволяет получить уравнения, которые в большей степени удобны для технологического управления этими эксплуатационными свойствами. В результате их можно более гибко использовать для проведения размерного
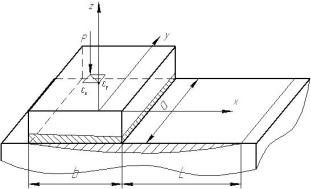
188
анализа сборок и позволит получить выходы на технологию изготовления отдельных деталей (рис. 1).
Рис. 1. Расчетная схема сопряжения
При статическом описании выходного параметра объекта необходимо учитывать:
а) его зависимость от условий нагруженности и эксплуатации (скорости движения, потребляемой мощности, температуры и т.д.), которые в эксплуатации не постоянны и могут рассматриваться как случайные процессы;
б) различия исходного качества изготовления отдельных поверхностей
объекта, вызванные различиями размеров, твердости и т.д.; |
|
|
|||||||||
в) |
зависимость |
параметров от |
медленно |
протекающих |
процессов |
||||||
(приработка, изнашивание, коррозия). |
|
|
|
|
|
|
|||||
В ряде случаев выходной параметр удается представить в виде трех |
|||||||||||
независимых составляющих: |
|
|
|
|
|
|
|||||
zj |
(t) 0 f1 |
g1(t),g2(t),...,gi (t) h t (t) |
|
|
|
|
|
|
|||
где: |
0 |
- |
случайная величина, оценивающая начальное качество; |
f |
|||||||
|
1 - |
||||||||||
неслучайная |
|
функция |
возмущений; |
h t |
и |
(t) |
- случайные |
функции, |
оценивающие соответственно влияние медленно протекающих процессов и внезапных случайных флуктуаций параметра.
В общем случае работоспособность объекта, качество его функционирования определяется не одним, а совокупностью s выходных параметров состояния z1, z2, … zi, которые можно считать компонентами некоторого вектора Z. Тогда пространство состояний некоторой граничной поверхностью можно разделить на две области: область Ω работоспособных состояний и область отказов. Безотказность в этом случае определяется как вероятность того, что за время функционирования системы T параметры состояния zi не выходят за соответствующие границы Ri1 и Ri2.
Неоднородность качества может быть вызвана рассеянием начальных размеров, а так же различием физических свойств у контактирующих поверхностей, приводящих к варьированию средней скорости процесса каждой реализации.
Работа выполнена под руководством зав. каф. "Технология машиностроения", к.т.н., доц. Е.А. Польского
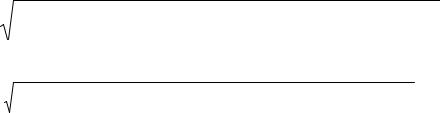
189
К.О. Урвачев РАЗРАБОТКА АВТОМАТИЗИРОВАННОЙ ПОДСИСТЕМЫ
РАСЧЕТА ПОГРЕШНОСТИ ОБРАБОТКИ, ВЫЗВАННОЙ УПРУГИМИ ДЕФОРМАЦИЯМИ ТЕХНОЛОГИЧЕСКОЙ СИСТЕМЫ ПОД ВЛИЯНИЕМ СИЛЫ РЕЗАНИЯ
ПРИ ФРЕЗЕРНОЙ И РАСТОЧНОЙ ОБРАБОТКЕ
Объект исследования: этап технологической подготовки производства по расчету элементарных составляющих суммарной погрешности обработки деталей машин.
Результаты, полученные лично автором: разработан программный модуль автоматизированной подсистемы расчета погрешности обработки, вызванной упругими деформациями технологической системы под влиянием силы резания для чистовых операций, выполняемых на станках сверлильно- фрезерно-расточной группы.
Задача автоматизированного проектирования для современного машиностроения является чрезвычайно сложной и актуальной. Ее решение обеспечит резкое сокращение сроков внедрения в производство новых проектно-конструкторских разработок и повышение его эффективности.
Существенным преимуществом автоматизированных систем технологической подготовки производства (ТПП) является выполнение рутинных процессов и подготовка информации с помощью средств электронной обработки данных. Специалист, работающий с автоматизированными системами ТПП, избавляется от монотонного, нетворческого труда. Кроме того, благодаря большому быстродействию средств электронной обработки данных появляется возможность использования различных альтернативных решений.
В данном исследовании рассмотрена задача автоматизации расчета составляющей суммарной погрешности обработки для двух вариантов получения элементарной поверхности – фрезерование плоских поверхностей и уступов и растачивание отверстий. Данные переходы могут быть реализованы применением станков сверлильно-фрезерно-расточной группы с консольным закреплением металлорежущего инструмента.
Математическое обеспечение любых систем автоматизации проектирования (САПР) по назначению и способам реализации делится на две части. Первую составляют математические методы и построенные на их основе математические модели, описывающие объекты проектирования или их части и параметры объектов.
Суммарную погрешность обработки деталей на настроенных станках для диаметральных размеров (чистовое растачивание отверстий) определяют
по уравнению: |
2 |
|
2 |
|
2 |
|
|
2 |
|
|
2 |
|
|
|
2 |
у |
н |
1,73 и |
ст |
т |
, |
||||||
|
|
|
|
1,73 |
|
1,73 |
для линейных размеров (чистовое фрезерование плоских поверхностей и уступов):
|
|
|
у2 |
|
|
н2 |
2 |
|
|
2 |
1,73 |
т |
2 |
ε2у , |
|
|
|
1,73 и |
|
1,73 ст |
|
|
|
|
190
где У – погрешность обработки, вызванная упругими деформациями технологической системы под влиянием силы резания; Н – погрешность настройки станка; И – погрешность, вызванная размерным износом инструмента; СТ – погрешность, вызванная геометрическими неточностями станка; Т – погрешность обработки, вызванная температурными деформациями технологической системы; εУ – погрешность установки заготовки.
Таким образом, необходимо определить значения всех элементарных погрешностей. Основной сложностью при проведении расчетов является необходимость постоянного анализа эмпирических данных по точности и жесткости оборудования и выбору справочных материалов из большого числа таблиц и графиков. В ходе проведенной работы для возможности применения подсистемы для всех видов оборудования и инструментальных материалов была решена задача преобразования эмпирических справочных таблиц в математические зависимости, обеспечивающие получения адекватных и значимых результатов для различных вариантов исходных данных.
При использовании автоматизированной подсистемы расчета погрешности обработки необходимо выполнять определенный набор действий. При открытии программы в главном меню выбрать тип обработки нажав на кнопку «Растачивание» или «Фрезерование». В открывшемся меню программы заполнить исходные данные. Все поля обязательны для заполнения, кроме «значение допуска». Так же можно оставить пустым поле, либо n – частота вращения фрезы, либо V – скорость резания. При наличии одного из полей программа самостоятельно рассчитает второе. Выбрать из выпадающих списков необходимые тип станка, модель станка, материал заготовки, тип фрезы, тип фрезерования и главный угол в плане у инструмента.
После того, как все поля заполнены и выбраны, следует нажать на кнопку «ОК», которая откроет новое окно с таблицами. В таблицах указаны расчетные параметры, коэффициенты, используемые при расчетах и режимы резания. Для формирования отчета необходимо нажать кнопку «Отчет».
При проектировании маршрута обработки элементарной поверхности необходимо дать заключение, для каждого варианта последовательности технологических переходов, о возможности обеспечения требуемой точности. Единственным критерием позволяющим выбрать тот или иной маршрут обработки является сравнение суммарной погрешности обработки с допуском на выполняемый размер. Разработанная программа доступна широкому кругу пользователей, но создавалась в первую очередь для технологов, чтобы помочь им при оценке возможности осуществления обработки детали на станке с заданной точностью. Предполагается, что данная автоматизированная система в дальнейшем будет являться частью более крупной САПР, являющейся комплексным решением для большинства технологических задач.
Работа выполнена под руководством доц. каф. «Технология машиностроения» Е.А. Польского, С.В. Сорокина