
Сборник 70 студ конференции БГТУ
.pdf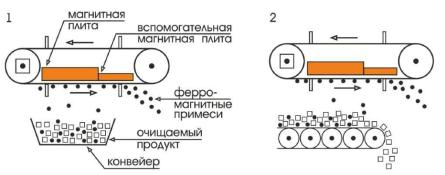
61
установить только в зоне разгрузки конвейера. На рисунке 1 представлены оба варианта размещения отделителя.
Рис. 1. Схема размещения металлоотделителя:
1 – перпендикулярно движению ленты; 2 – последовательно
Пластинчатый конвейер, применяемый в данной схеме механизации, является наклонным. Его производительность составляет 500 т/ч, длина горизонтальной проекции – 75000 мм, угол наклона – 18 градусов.
Конструкция конвейера типовая и включает в себя набор стандартных элементов: приводную станцию, натяжную станцию, волнистый коробчатый настил, две тяговые цепи и металлоконструкцию.
В состав привода конвейера входит электродвигатель АИР315М8, червячно-глобоидный редуктор Чг-50, колодочный тормоз нормальнозамкнутого типа ТКГ-600 и приводной вал с установленными на нём приводными звездочками. Соединение вала электродвигателя и входного вала редуктора осуществляется упругой втулочно-пальцевой муфтой с установленным на ней тормозным шкивом, выходной вал редуктора и приводной вал конвейера соединены посредством зубчатой муфты.
Натяжное устройство, примененное на данном конвейере – пружинновинтовое. Выбор осуществлен согласно рекомендации, в которой указано, что при длине конвейера более 20000 мм осуществляется установка пружинно-винтового натяжного устройства. В его состав входят: натяжной винт, пружина, натяжная ось и установленные на ней звездочки натяжного устройства.
Отдельно стоит обратить внимание на то, что установка отделителя непосредственно на пластинчатом конвейере невозможна, так как будет сложно обеспечить невозможность отрыва настила самого конвейера, а также снизить износ катков тяговой цепи при применении различных удерживающих устройств в зоне установке отделителя.
Работа выполнена под руководством к.т.н., доцента Е.П. Зуевой
А.В. Гришин ТРАВОЛАТОРС ЛИНЕЙНЫМАСИНХРОННЫМДВИГАТЕЛЕМ
Объект исследования: траволатор производительностью 3000 чел/ч. Результаты, полученные лично автором: разработана методика
ориентировочного расчёта траволатора с линейным приводом.
62
Развитие техники в современном мире невозможно без инновационных решений. Одним из таких решений является применение линейных асинхронных двигателей для машин непрерывного транспорта.
Траволатордвижущаяся бесступенчатая дорожка, которая позволяет ускорить или облегчить передвижение пешеходов.
Основание траволатора представляет собой сварную металлоконструкцию из профильного металлопроката с несущими балками. Между балками закреплены ролики на которые опирается лента.
Линейный асинхронный двигатель состоит из двух элементов: первичного элемента – статора и вторичного элемента – якоря. Статор представляет собой магнитопровод с обмоткой, получает энергию из сети.Основное назначениеобмотки статора – создание магнитного поля. Якорь выполняется в виде листов (полос), чаще всего это сталь, алюминий, медь. Якорь получает энергию от магнитного поля статора.
Принцип действия траволатора с линейным асинхронным двигателем заключается в следующем: первичные элементы крепятся к металлоконструкции, количество которых выбирается в зависимости от тягового усилия. Вторичным элементом является стальная обрезиненная лента с одной стороны . Между первичными и вторичными элементами должен быть минимальный воздушный зазор. Для каждого линейного двигателя в справочнике изготовителя выбирается свой размер воздушного зазора. Первичные элементы подключают к сети трехфазного переменного тока, образуется переменное магнитное поле, ось которого будет перемещаться с определённой скоростью вдоль воздушного зазора. Это перемещающееся вдоль зазора магнитное поле пересекает вторичные элементы и индуцирует в них ЭДС, под действием которой во вторичных элементах начнёт протекать ток. Взаимодействие тока с магнитным полем приведет к появлению силы, стремящейся вытолкнуть вторичные элементы из поля статора.Траволаторпод действием этой силы начинает двигаться. Привод поручня осуществляется от головного неприводного барабана посредствам цепной передачи.
Достоинства:
–применение линейных электродвигателей позволяет упростить или полностью исключить механическую передачу;
–повышение экономичности и надежности работы траволатора;
–простота конструкции;
–возможность плавногорегулирования скорости траволатора в широких пределах.
Работа выполнена под руководством к.т.н.,доц . Гончарова К. А.
Егоров А.В. Панчишин Е.А.
ПЕРЕВОД ГРУЗОПОДЪЕМНЫХ КРАНОВ НА ДИСТАНЦИОННОЕ РАДИОУПРАВЛЕНИЕ НА ПРЕДПРИЯТИЯХ ПО "БЕЖИЦКАЯ СТАЛЬ" И ЗАО УК "БМЗ"
Объект исследования: перевод грузоподъёмных кранов промышленных предприятий на дистанционное управление.
63
Результаты, полученные лично авторами: проведен анализ информации о ходе перевода грузоподъемных кранов на радиоуправление, установлено, что в целом интенсивность оснащения кранов этими системами не снижается, это будет способствовать техническому прогрессу на предприятиях.
ОАО ПО «Бежицкая сталь», также как и другие промышленные предприятия г. Брянска, активно начало внедрять дистанционное управление своими грузоподъемными кранами, начиная с 2012 года. За основу переоборудования кранов на радиоуправление предприятие выбрало зарубежные системы «Telecrane»LEEHI-TECHENTERPRISECO., LTD.
Услуги по оснащению кранов этими системами предложило предприятие
ООО «Мобильный крановый сервис». За 2012-2014 годы было модернизировано 17 мостовых кранов грузоподъемностью 5-10 тонн.Кран, установленный в литейном цехе 2 на четвертом участке, в четвертом пролете, оборудован системой с широким спектром регулирования скоростей основных механизмов, так как условия его работы предполагают особые требования к плавности срабатывания и точности установки грузозахватного органа. Все остальные краны по условиям эксплуатации оборудовались системами без широкого спектра регулирования скоростей с кнопочным пультом управления. В течение последнего года предприятие испытывало значительные сложности с реализацией продукции и реорганизацией производства. Это привело не только к замедлению оснащения кранов системами радиоуправления, но и к полной остановке этого процесса. Так, за прошедший год не было модернизировано дистанционным управлением ни одного крана. Предполагаемые перспективы вхождения этого предприятия в состав ЗАО УК «БМЗ» возможно возродит былые темпы перехода на дистанционное управление этими кранами, что будет служить общей модернизации литейного производства.
Внедрение систем дистанционного управления на предприятии г. Брянска в массовом порядке началось в 2010 году. Наиболее быстрыми темпами переоборудуются краны на ЗАО УК "БМЗ". К апрелю 2014 года на этом предприятии оборудовали радиоуправлением уже 21 работающий кран. В том числе один кран в цехе магистральных тепловозов был оснащен кнопочным пультом управления, система которого не предусматривает возможности регулирования скоростей механизма подъема в широком диапазоне. Остальные системы радиоуправления внедрялись с пультом управления, имеющим джойстик, с возможностью широкого регулирования скоростей механизмов подъема. В течение следующего времени на предприятии продолжалось интенсивное оборудование грузоподъемных кранов системами дистанционного управления. К марту 2015 года число таких кранов увеличилось до 35 и до конца года планируется перевести на радиоуправление еще 13 мостовых кранов. Оборудование поставляет фирма "Радук". Основные элементы системы управления выполнены на этом предприятии, которое с 1995 года активно разрабатывает и поставляет системы радиоуправления на предприятия страны для модернизации кранов различных типов. Фирма "Радук" создала солидную сервисную сеть по
64
установке систем радиоуправления и ее обслуживанию, разработала и внедрила согласованную с надзорными организациями программу обучения и аттестации крановщиковоператоров.Мостовые краны установлены в основных цехах магистрального и маневрового тепловозостроения. Это производство в 2014-2015 годах намного более продуктивно и держит "наплаву" предприятие. Переоборудование системами радиоуправления производится подрядными организациями "ДиР", "Альманах", "Траксервис", "Энергосервис". Большое распространение на ЗАО УК "БМЗ" получили системы радиоуправления с широким спектром регулирования скоростей механизмов подъема и передвижения с помощью пульта управления, имеющего джойстик. В настоящее время предприятие находится в сложных экономических условиях, что сдерживает темпы модернизации технологических кранов системами дистанционного радиоуправления, но в перспективе предприятие будет переводить большинство кранов на системы радиоуправления.
Работа выполнена под руководством доц. И.Е. Ильина
М.С. Разенков ПРОЧНОСТИ СВАРНЫХ БАЛОК ПРИ ИЗГИБЕ
Объект исследования: сварная двутавровая балка.
Результаты, полученные лично автором:повышение надежности сварных швов и балки в целом, особенно для коротких балок, когда длина балки превышает 4-5 высот ее сечения.
Сварные балки широко применяются в строительстве, мостостроении, дорожном машиностроении и многих других отраслях промышленности. Повышение их надежности и прочности имеет исключительно большое значение для обеспечения долговечности конструкций и требований техники безопасности. При изгибе в балках возникают нормальные и касательные напряжения, причем для балок, длина которых намного больше размеров поперечного сечения, касательными напряжениями, как правило, можно пренебречь. Для сварных балок именно касательные напряжения часто приводят к появлению трещин в сварных швах и выходу из строя всей конструкции.Формулы неточно характеризуют распределение напряжений в зоне, близкой к внутренней поверхности наплавленного металла. Фактически имеет место концентрация напряжений, и зону контакта стенки и полкибалки можно рассматривать, как трещину определенной длины. Вблизи точекнаплавленного металла,концентрация напряжений может увеличиваться в 4 - 5 раз, и если в этих зонах имеются дефекты: поры, микротрещины, непроплавленные участки, то возможно развитие трещины, увеличение ее длины. Во многом отрицательное влияние оказывают непровары в сварных швах. Эта зона может быть концентратором напряжений, а иногда в ней расположены небольшие трещины, длина которых может увеличиваться. Это приводит к разрушению конструкции.
Существенно повысить прочность и надежность балки можно, изменив ее конструкцию:выполнить стенки балки с выступами. После плотного
65
соединения элементов балки осуществляется их сварка; в такой конструкции сварные швы в значительной степени разгружены. Углубления в полках можно выполнить механической обработкой (фрезерованием), но предпочтительнее получать их обработкой давлением: выдавливание штампом напрессе или прокатка в валках с выступом, формирующим периодические впадины. В этой конструкции не только сварные швы, но и выступы обеспечивают прочное соединение ее составных частей. Выступы существенно повышают передачу тангенциальных усилий между отдельными элементами балки. Это позволяет в 1,3 - 2 раза повысить надежность сварных швов и балки в целом, особенно для коротких балок, когда длина балки превышает 4-5 высот ее сечения.
Повышение прочности и надежности сварных конструкций имеет большое значение для обеспечения их долговечности и безопасности. Для этого используют различные конструктивные и технологические приемы. В ряде случаев добиться повышения надежности можно изменением положения сварного соединения — переносом его в зону действия меньших напряжений. Все это относится и к балкам, сварку которых приходится осуществлять не в цехах, а при воздействии ветра, влаги, низких температур и т. д., когда хорошая подготовка поверхностей и обеспечение необходимых режимов сварки затруднены. В этих случаях следует проработать разные варианты конструкции балок с целью обеспечения надежного соединения их элементов и уменьшения напряжений в сварных швах.
Появление трещин в зонах сварки и их распространение могут привести к тому, что элементы сечения (полки, стенки) не будут деформироваться как единое целое. Следовательно, это приводит к уменьшению (иногда в несколько раз) момента инерции сечения балки, поломкам и деформациям балок, нагруженных поперечным изгибающим моментом.
Для балок, подвергающихся продольному изгибу (колонн, стоек), последствия могут быть более тяжелыми: возможны потеря устойчивости и разрушение здания.В некоторых случаях улучшить условия работы сварных балок можно, изменив их конструкцию, т. е. используя на участках контакта выступы и впадины для передачи тангенциальных усилий от одних элементов конструкции к другим.
Работа выполнена под руководством доц.Е.П. Зуевой
А.О. Селифонтов ТРАНСБОРДЕРНАЯ ТЕЛЕЖКА С ЛИНЕЙНЫМ АСИНХРОННЫМ
ДВИГАТЕЛЕМ
Объект исследования: трансбордерная тележка грузоподъемностью48т. Результаты, полученные лично автором: предложена оригинальная конструкция трансбордерной тележки с линейным двигателем, подана заявка
на патент.
Развитие техники в современном мире невозможно без инновационных решений. Одним из инновационных решений является применение линейных асинхронных двигателей для грузоподъемных машин.
66
Трансбордер применяется в ремонтных цехах для передачи грузового вагона с одной ремонтной операции на другую.
Основание трансбордера представляет собой сварную металлоконструкцию из листового и профильного металлопроката с несущими балками. Между балками рамы закреплены рельсы для перемещения изделий.
Линейный асинхронный двигатель состоит из двух элементов:первичного элемента – статора и вторичного элемента – якоря. Статор представляет собой магнитопровод с обмоткой, получает энергию из сети.Основное назначениеобмотки статора – создание магнитного поля. Якорь выполняется в виде листов (полос), чаще всего это сталь, алюминий, медь. Якорь получает энергию от магнитного поля статора.
Принцип действия трансбордерной тележки с линейным асинхронным двигателем заключается в следующем: первичные элементы крепятся к самой тележке, количество которых выбирается в зависимости от тягового усилия. Вторичные элементы крепятся к фундаменту вдоль всего пути. Между первичными и вторичными элементами должен быть минимальный воздушный зазор. Для каждого линейного двигателя в справочнике изготовителя выбирается свой размер воздушного зазора. Первичные элементы подключают к сети трехфазного переменного тока, образуется переменное магнитное поле, ось которого будет перемещаться с определённой скоростью вдоль воздушного зазора. Это перемещающееся вдоль зазора магнитное поле пересекает вторичные элементы и индуцирует в них ЭДС, под действием которой во вторичных элементах начнёт протекать ток. Взаимодействие тока с магнитным полем приведет к появлению силы, стремящейся вытолкнуть вторичные элементы из поля статора.Тележкапод действием этой силы начинает двигаться.
Достоинства:
–применение линейных электродвигателей позволяет упростить или полностью исключить механическую передачу;
–повышение экономичности и надежности работы трансбордера;
–простота конструкции;
–возможность остановки трансбордера без применения дополнительных тормозных устройств.
Работа выполнена под руководством проф. В.П. Дунаева
В.М. Трушаков СПЕЦИАЛЬНЫЙ ПЛАСТИНЧАТЫЙ КОНВЕЙЕР С ЛИНЕЙНЫМ
АСИНХРОННЫМ ДВИГАТЕЛЕМ
Объект исследования: специальный пластинчатый конвейер. Результаты, полученные лично автором: предложена оригинальная
конструкция пластинчатого конвейера с линейным двигателем, подана заявка на патент.
67
Современное развитие конвейерного транспорта невозможно без инновационных конструктивных решений. Одним из инновационных решений является применение линейных асинхронных двигателей для машин непрерывного транспорта, в частности пластинчатого конвейера.
Линейный асинхронный двигатель состоит из двух элементов: первичного элемента – статора и вторичного элемента – якоря. Статор
представляет собой магнитопровод с обмоткой, получает энергию из сети. Основное назначение обмотки статора – создание магнитного поля. Якорь выполняется в виде листов (полос), чаще всего это сталь, алюминий, медь. Якорь получает энергию от магнитного поля статора.
Принцип действия специального пластинчатого конвейера с линейным асинхронным двигателем заключается в следующем: первичные элементы располагаются между ходовыми путями. Их количество зависит от потребного тягового усилия всего пластинчатого конвейера. Вторичным элементом является ходовая часть (настил). Настил состоит из швеллеров с приваренными к ним проушинами и соединенными между собой осями с колесами. Между первичными и вторичными элементами должен быть минимальный воздушный зазор. Для каждого линейного двигателя в справочнике изготовителя выбирается свой размер воздушного зазора. Первичные элементы подключают к сети трехфазного переменного тока, образуется переменное магнитное поле, ось которого будет перемещаться с определённой скоростью вдоль воздушного зазора. Это перемещающееся вдоль зазора магнитное поле пересекает вторичные элементы и индуцирует в них ЭДС, под действием которой во вторичных элементах начнёт протекать ток. Взаимодействие тока с магнитным полем приведет к появлению силы, стремящейся вытолкнуть вторичные элементы из поля статора. Настил под действием этой силы начнет двигаться.
Достоинства:
1.Применение линейных электродвигателей позволяет упростить или полностью исключить механическую передачу, повысить экономичность и надежность работы конвейера;
2.Возможность плавного регулирования скорости конвейера в широких пределах;
3.Возможность остановки конвейера без применения дополнительных тормозныхустройств;
4.Возможность задавать пошаговоеперемещение;
5.Значительное снижение металлоемкости за счет исключения приводной инатяжнойстанции, а также тормозногоустройства.
Работа выполнена под руководством проф. В.П. Дунаева
В.И.Шуваева ВЫБОР ТЕХНОЛОГИЧЕСКИХ РЕШЕНИЙ ПРИ ИЗГОТОВЛЕНИИ
ДЕТАЛЕЙ
Объект исследования: схема формирования технологического решения при изготовлении детали.
68
Результаты, полученные лично автором: метод поиска рационального варианта изготовления детали, рассмотренный на примере цилиндрического отверстия.
Основой технологической операции являются переходы, во многом определяющие эффективность изготовления детали. Операционная технология разрабатывается технологом вручную или с помощью системы автоматизированного проектирования технологических процессов(САПР ТП). В любом случае качество операции определяется элементной базой средств технологического обеспечения и методикой поиска технологического решения (ТР) изготовления детали, т. е. выбором способа получения и обработки ее поверхностей.
На предприятиях, где разработка операций ведется вручную, данные по элементной базе, как правило, отличаются недостаточной полнотой, кроме того, они могут находиться в разных источниках (справочники, рабочие материалы) и в различном виде (альбомы, ведомости и т. п.). При использовании САПР ТП элементная база средств технологического обеспечения не только более упорядочена, но и отличается более организованным поиском технических решений. Однако в любом случае поиск ТР осуществляется технологом и зависит от его опыта и квалификации, при этом, как правило, принимаются два-три варианта, не подкрепляемые расчетом. В результате разработанные технологические операции далеки от оптимальных, а на их разработку требуется значительное время.
Очевидно, что для нахождения оптимальной технологической операции необходимы элементная базаи методика поиска наилучшего технологического решения, которое должно обеспечивать заданные параметры (форма, размеры, качество) поверхности. Методика поиска ТР должна включать в себя выбор в определенной последовательности составных элементов ТР, а именно: метода обработки, инструмента, материала рабочей части инструмента, схему базирования.
Для этих целей была разработана методика поиска ТР. Рассмотрим ее на примере выполнения цилиндрического отверстия по таким параметрам, как диаметр, длина, точность и шероховатость поверхности, которые в той или иной степени определяют выбор обработки, инструмента, его материала, схему базирования.
Одну и ту же поверхность можно изготовить различными способами. Так, например, отверстие можно выполнять резанием, абразивной обработкой, пластическим деформированием или используя электрофизикохимические методы. Известны такие способы резания, как сверление, рассверливание, высверливание, зенкерование и развертывание.
69
В основе поиска ТР лежит схема ее формирования. Для выбора элементов ТР для выполнения отверстия с заданными параметрами необходимо знать факторы, ограничивающие область применения каждого элемента, например, такие показатели, как форма, размеры, материал и качество поверхности заготовки, в некоторых случаях расположение изготовляемой поверхности. Например, при определении области.
Исходные данные для поиска ТР: параметры отверстия, условия его обработки средства, технологического оснащения на данном предприятии.Поиск ТР ведется следующим образом. Из всех способов обработки выбирают те, с помощью которых можно получить заданную форму поверхности детали. Из них отбирают способы, обеспечивающие заданный размер. Затем каждый из оставшихся способов исследуют на область применения для достижения заданной точности и шероховатости поверхности. Если такие способы отсутствуют, то переходят к поиску способов обработки заготовки за два рабочих хода.
Если есть возможность достижения требуемых параметров: диаметра, точности и шероховатости поверхности, то сопоставляют заданный припуск с рекомендуемым припуском для получения заданной точности и шероховатости с учетом материала заготовки. Если заданный припуск окажется больше, то этот способ обработки не подходит. Из оставшихся способов обработки следует выбрать лучший, т. е. с максимальной производительностью или минимальной себестоимостью.Аналогично выбирается инструмент с учетом доступа к месту изготовления отверстия, заданного диаметра, длины, точности и шероховатости поверхности. Если выбранным инструментом нельзя обработать отверстие с заданной точностью или шероховатостью, то надо вернуться к забракованным способам обработки, выбрать другой и в соответствии с этим выбирать инструмент. Из нескольких вариантов конструкций сверла выбираются лучший по максимальной производительности или минимальной себестоимости. Таким же образом выбирается материал рабочей части инструмента и схема его базирования.
Работа выполнена под руководством к.т.н.доцента Е.П. Зуевой
Н.С. Яковлева ИССЛЕДОВАНИЕ МЕХАНИЗМА И ТЕХНИЧЕСКОЙ
ВОЗМОЖНОСТИ ПРЕДОТВРАЩЕНИЯ НАЕЗДА НА ПЕШЕХОДА
Объект исследования: наезд на пешехода.
Результаты, полученные лично автором: выявлены основные направления исследований в области установления механизма и технической возможности предотвращения наезда на пешехода.
Непрерывное увеличение автомобильного транспорта страны, повышение интенсивности использования подвижного состава и загрузки автомобильных дорог делают все более актуальной задачу снижения темпов роста аварийности связанной с таким видом ДТП, как наезд на пешехода.
70
Исследование вопроса о предотвращения наезда на пешехода состоит в установлении для водителя транспортного средства технической возможности:
-предвидеть наступление аварийных последствий в процессе возникшей опасности;
-предотвратить ДТП путём принятия мер с момента возникновения опасности;
-не допустить перерастания опасной обстановки в аварийную.
Для решения вопросов по установлению механизма и технической возможности предотвращения ДТП данного вида требуются специальные исследования.
Если в ходе исследований будет установлено, что к моменту достижения автомобилем линии движения пешехода последний успевал выйти за пределы опасной зоны (даже когда водитель не принимал мер к снижению скорости) и, следовательно, не создавал помехи для движения автомобиля, следует сделать вывод об отсутствии причинной связи между действиями пешехода и возникновением происшествия. Причиной происшествия, с технической точки зрения, в данном случае явились действия водителя, который неоправданным манёвром создал аварийную обстановку.
Если в ходе исследований будет установлено, что пешеход успевал выйти за пределы опасной зоны лишь при своевременном торможении автомобиля, значит, он создавал опасность для движения автомобиля и, следовательно, его действия находились в причинной связи с происшествием (являлись необходимым условием возникновения данного происшествия). Однако причиной происшествия явились действия водителя, который, имея возможность предотвратить происшествие путём торможения, применил неоправданный манёвр. В случае же, когда к моменту достижения автомобилем линии движения пешехода последний при первоначально избранной скорости не успевал выйти за пределы опасной зоны даже при своевременном принятии водителем мер к остановке автомобиля, предпринятый водителем манёвр являлся вынужденным и, следовательно, причиной происшествия являлись только действия пешехода.
Работа выполнена под руководством проф. С.П. Шеца