
ТРАНСВУЗ-2015.Часть 2
.pdf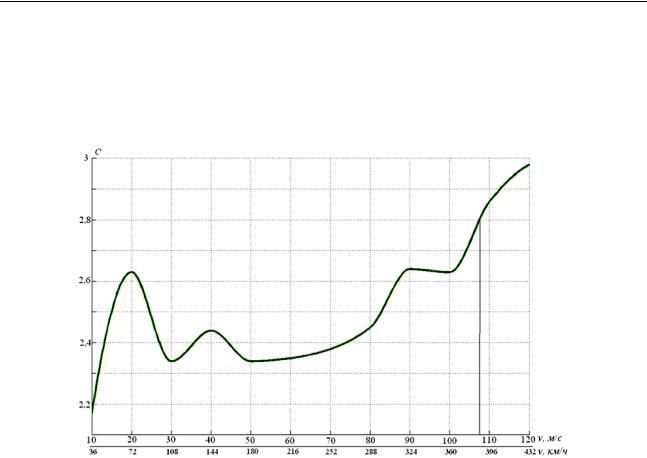
Ремонт и динамика подвижного состава
Из зависимости коэффициента горизонтальной плавности хода С от скорости (рис. 5) видно, что коэффициент плавности хода С не превышает своего допустимого значения. До скорости 108 м/с у экипажа отличное качество плавности хода, а при скорости свыше 108 м/с – хорошее.
Рис. 5. График зависимости коэффициента плавности хода С от скорости движения v
По приведенным выше зависимостям ПДК можно сделать вывод, что спроектированный рельсовый экипаж может эксплуатироваться при скоростях до 120 м/с или 432 км/ч.
Список литературы
1.ГОСТ Р 55513-2013 Локомотивы. Требования к прочности и динамическим качествам. – М: Стандартинформ, 2014. – С. 77.
2.Савоськин, А. Н. Случайные колебания рельсовых экипажей с нелинейными характеристиками рессорного подвешивания / А. Н. Савоськин, Г. П. Бурчак, Р. К. Насыров, А. А. Акишин // Вестник Научноисследовательского института железнодорожного транспорта. – 2015. – №3. – С. 10 – 21.
3.Савоськин, А. Н. Выбор параметров горизонтальных связей рессорного
подвешивания моторного вагона на четырех одноосных тележках в
20

ТРАНСВУЗ – 2015
высокоскоростном электропоезде/ А. Н. Савоськин, А. А. Акишин / Транспорт
Российской Федерации. – 2015. – №3. – С. 10 – 13. |
|
||
4. Савоськин, А. Н. |
Моделирование |
многомерного |
случайного |
возмущения в задачах |
динамики рельсовых |
экипажей/ А. Н. Савоськин, |
Ю. С. Ромен, А. А. Акишин / Транспорт Российской Федерации. – 2015. – №3. – С. 31 – 37.
УДК 629.42:629.4.054
О. С. Аблялимов
К РАЗРАБОТКЕ ТЕХНОЛОГИИ ИЗГОТОВЛЕНИЯ ПРУЖИН РЕССОРНОГО ПОДВЕШИВАНИЯ ЭЛЕКТРОВОЗА «УЗБЕКИСТАН»
Представлены результаты исследований по разработке технологического процесса изготовления цилиндрических винтовых пружин для двух ступеней рессорного подвешивания электровозов «Узбекистан» в условиях ремонтного производства АО «Ўзбекистон темир йўллари».
Одним из путей успешного решения задачи, связанной с повышением эффективности эксплуатационной деятельности железных дорог АО «Ўзбекистон темир йўллари» является модернизация существующих локомотивов эксплуатируемого парка тягового подвижного состава железнодорожной отрасли и пополнение (обновление) упомянутого парка высокопроизводительными локомотивами дизельной и электрической тяги «нового» поколения.
Так, в настоящее время, грузовые, пассажирские и грузопассажирские электровозы «Узбекистан» (Китайская Народная Республика – Узбекистан) уже составляют более двадцати одного процента от всех локомотивов электровозного парка, где тринадцать единиц приходится на последние.
Данные исследования посвящены одному из вопросов локализации деталей, узлов, систем и агрегатов, касающихся, именно, новых типов локомотивов электрической тяги.
21

Ремонт и динамика подвижного состава
Объект исследования – грузопассажирский электровоз «Узбекистан» (в дальнейшем электровоз «Узбекистан») и организация обслуживания его рессорного подвешивания в условиях ремонтного производства.
Предмет исследования – цилиндрические винтовые пружины (в дальнейшем пружины) двух ступеней рессорного подвешивания электровоза «Узбекистан» и технологический процесс их изготовления на локомотиворемонтных предприятиях АО «Ўзбекистон темир йўллари».
Электровоз «Узбекистан» [1] предназначен для вождения грузовых и пассажирских поездов на железнодорожных магистралях АО «Ўзбекистон темир йўллари» и относится к локомотивам нового поколения, отличительной особенностью которых является электрическая передача переменно-постоянно- переменного тока с бесконтактным регулированием оборотов тяговых электродвигателей и мощности.
Рассмотрим конструктивные особенности некоторых узлов экипажной части электровоза «Узбекистан».
Электровоз имеет две торцевых и одну промежуточную тележки, посредством которых не только передается «тяговая нагрузка» на раму электровоза, но и обеспечивается образование касательной силы тяги. Обе торцевых тележки одинаковые по конструкции и могут быть взаимозаменяемыми между собой. Причём рама торцевой тележки выполнена в виде «П» – образной фигуры.
Каждая из тележек имеет по два колесно-моторных блока и содержит раму, тяговое устройство, две ступени рессорного подвешивания, основное и вспомогательное тормозные устройства. А для уменьшения износа колёсных пар на торцевой тележке установлено «смазочное устройство».
Первая ступень рессорного подвешивания (буксовое подвешивание)
состоит из вертикальных поводков, цилиндрических пружин и гидравлического демпфера (гаситель колебаний). Упругие боковые опоры второй ступени рессорного подвешивания, через которые кузов опирается на каждую тележку, состоят из цилиндрической пружины, горизонтального и вертикального гасителей колебаний (торцевая тележка), а у промежуточной тележки – цилиндрические пружины, вертикальный гаситель колебаний, роликовое устройство и горизонтальные кронштейны.
22

ТРАНСВУЗ – 2015
Приведём основные характеристики и параметры на цилиндрические пружины первой ступени рессорного подвешивания электровоза «Узбекистан» (чертёж № 323003000060 [1]): рабочее число витков – 5; общее число витков – 5,5; максимальное напряжение – 696,9 Н/мм2; развернутая длина – 3488 мм; вертикальное усилие – 44,049 кН; статический прогиб – 51,99 мм; вертикальная жесткость – 848,8 Н/мм; горизонтальная жесткость – 550,5 Н/мм и направление вращения – правое. Диаметр пружины – 38±0,15 мм.
Основные характеристики и параметры на цилиндрические пружины второй ступени рессорного подвешивания электровоза «Узбекистан» (чертёж № 323024000020 [1]) следующие: рабочее число витков – 9; общее число витков – 10,5; максимальное напряжение – 614,1 Н/ мм2; развернутая длина – 6855 мм; вертикальное усилие – 44,962 кН, статический прогиб – 105 мм; вертикальная жесткость – 428,3 Н/мм; горизонтальная жесткость – 111,6 Н/мм и направление вращения – правое. Диаметр пружины – 43±0,5 мм.
Технические условия и требования для цилиндрических пружин обеих ступеней рессорного подвешивания электровозов «Узбекистан».
Химический состав материала должен соответствовать требованиям GB/T1222 «Пружинная сталь», а предел прочности материала – (1470…1570) Н/мм2. Для пружинной стальной проволоки сдирать и шлифовать до размера 38±0,15 мм и 43±0,5 мм с шероховатостью поверхности 1,6 и до навивки пружины проводить магнитную дефектацию, при этом не допускается любой дефект. Закалка – 45HRC…52HRC. Декарбонизация поверхности должна отвечать требованиям GB/1224 «Метод измерения глубины слоя декарбонизации стали», а наибольший слой декарбонизации не более 0,2 мм. Проверить визуально каждую пружину, на поверхности которой вмятины, трещины, острые кромки и угарная «рябь», окалины не допускаются. Проводить дробеструйную обработку по ТВ/Т1Т58 «Технические условия по дробеструйной обработке пружин электровоза».
Для изготовленной пружины проводить испытание на сжатие давлением и нагрузкой три раза. Покрыть поверхность пружины противокоррозийным слоем. Маркировать высоту и номер изготовленной пружины в паспорте пружины под нагрузкой Р=44,05 кН.
Обозначим общие положения, предложенного нами технологического процесса на изготовление пружин обеих ступеней рессорного подвешивания
23

Ремонт и динамика подвижного состава
электровоза «Узбекистан», опираясь на специальные технические требования и указания [3], который состоит из следующих операций: резка заготовок; обдирка, шлифовка заготовок и накатка их роликами; оттяжка концов заготовок и накатка их роликами; навивка и правка пружин; закалка, отпуск с последующей проверкой геометрических параметров и качества изготовления; испытание и приёмка пружин; окраска.
С целью реализации изложенного выше и организации производства по изготовлению пружин обеих ступеней рессорного подвешивания электровоза «Узбекистан» разработан кузнечный цех, где предусмотрены отделения: штамповочно-молотовое, рессорное и болтовое со спецификацией и расстановкой основного оборудования, которое используется для изготовления всех элементов рессорного подвешивания локомотивов и в частности, упомянутых выше пружин, а также бытовое помещение и контора в примыкающем к цеху здании.
Кроме этого, осуществлена модернизация типового станка для навивки пружин в части возможности его использования при изготовлении пружин первой и второй ступеней рессорного подвешивания электровоза «Узбекистан» путём применения спроектированных для реализации этих целей специальных «навивочных» оправок.
Далее приводим основные технологические операции при организации производственного процесса изготовления пружин обеих ступеней рессорного подвешивания электровоза «Узбекистан».
Резку прутка стали на заготовки производить на пресс - ножницах в нагретом состоянии по месту реза при температуре 750° – 900°С, а оттяжку концов заготовок производить в нагретом состоянии (при температуре 950°…1000°С) на молоте в специальных штампах, бойках или вальцах.
Концы заготовки пружины должны быть оттянуты на длине 2/3 длины витка и иметь постепенный переход от круглого к прямоугольному сечению, а поверхности оттянутых концов должны быть ровными (без уступов). Высота оттянутого конца пружины не должна быть более 1/3 диаметра прутка, а ширина – не менее 0,7 диаметра. Измерение производить на расстоянии от конца заготовки, равном диаметру прутка.
После оттяжки концов охладить их в воде до температуры 650°…500°С с последующим охлаждением на воздухе.
24

ТРАНСВУЗ – 2015
Нагрев заготовок под навивку производить в нагревательных электропечах или электрическим контактным способом до температуры не выше 1000°С.
Нагрев электрическим контактным способом производить в две стадии, то есть непрерывный нагрев до нужной температуры с последующей кратковременной выдержкой при этой температуре.
Продолжительность нагрева в нагревательных печах обусловливается конструкцией печи и площадью сечения заготовок и должна быть в пределах 10...30 мин. Нагрев контролировать термопарой, находящейся на высоте не более 150 мм от пола печи в высоте нагрева заготовок. Допускается (возможно) определение температуры нагрева оптическим или радиационным пирометрами. При этом нагрев прутков должен быть равномерным по всей их длине.
Навивку, правку и закалку пружин производить с одного нагрева заготовки.
Навивку пружин производить на навивочных станках, обеспечивающих получение пружин заданного внутреннего диаметра и шага, а ритм навивки пружин (время от выемки заготовки из печи до момента погружения в закалочную среду) должен быть таким (приблизительно 25...40 с), чтобы пружина перед закалкой не была охлаждена ниже температуры в 850°С.
Правку производить на специальных приспособлениях, а закалку пружин производить в закалочных ваннах, отвечающих правилам пожарном безопасности и охране труда, а в качестве закалочной среды применять воду, температуру которой поддерживать в пределах 30°…45°С.
После закалки пружину подвергнуть отпуску в печах электрических или плазменных при температуре 440°…480°С с минимальным разрывом во времени после закалки во избежание образования в ней закалочных трещин.
При отпуске пружин соблюдать следующие условия: печь для отпуска по всей рабочей площади должна иметь температуру 440°…480°С; выдержка пружин при температуре отпуска должна быть не менее 60 мин; пружины после отпуска охлаждать на воздухе. Причём нагрев пружин под закалку и отпуск, одновременно в одной камере печи запрещается.
25

Ремонт и динамика подвижного состава
Твердость пружины после отпуска должна быть НВ 370…440, которую следует замерять на боковой поверхности опорного витка на расстоянии 30 мм от начала рабочего витка.
Изготовленные пружины испытать на прессе с манометром, позволяющим определить нагрузку на отсутствие остаточной деформация под пробной нагрузкой и на определение величины действительной стрелы прогиба под рабочей статистической нагрузкой.
Испытаниям подвергать не менее трёх процентов от партии пружин. Величины пробной и рабочей нагрузок, расчётного прогиба необходимо (следует) указывать на чертеже.
Испытание на остаточную деформацию производить следующим образом: загрузить пружину пробной нагрузкой два раза и после снятия нагрузки замерить высоту ее в свободном состоянии; далее вторично нагрузить пружину пробной нагрузкой, разгрузить её и замерить высоту. Высота пружины в свободном состоянии, замеренная ранее, должна оставаться неизменной.
Пружины, выдержавшие испытания на остаточную деформацию, испытать на прессе для определения величины действительной стрелы прогиба под рабочей статистической нагрузкой.
В случае неудовлетворительных результатов какого-либо вида испытаний произвести повторное испытание по этому виду удвоенного количества пружин. При неудовлетворительных результатах повторных испытаний хотя бы одной пружины, все пружины партии проверить поштучно по данному виду испытаний.
Результаты испытания пружин занести в журнал и следует считать их удовлетворительными, если пружины выдержали установленное (регламентированное) контрольное число циклов. Ежемесячно готовые пружины должны подвергаться металлографическому анализу для проверки стабильности технологического процесса термической обработки. Исследованию подлежит одна пружина из прутка одного диаметра и одной марки стали.
Для оценки микроструктуры и определения обезуглероженности слоя, образцы вырезают из любого рабочего и однородного опорного витка пружины. Микроструктура должна соответствовать эталонам, а глубина
26

ТРАНСВУЗ – 2015
обезуглероженного слоя не должна превышать 2,5 процента от диаметра прутка пружины.
Каждая, качественно изготовленная пружина после приёмки должна быть окрашена битумным лаком. Перед окраской пружины необходимо очистить от окалины, масла, грязи и подогреть их до температуры 30°...40°С. При хранении и транспортировке изготовленные пружины укладывать рядами, чтобы полностью исключить возможность механического повреждения от коррозии.
Для внедрения практической составляющей предложенного технологического процесса изготовления цилиндрических винтовых пружин первой и второй ступеней рессорного подвешивания электровозов «Узбекистан» на локомотиворемонтных предприятиях АО «Ўзбекистон темир йўллари» необходимо провести цикл экспериментальных исследований, связанных с обоснованием параметров некоторых отдельных положений (технических и технологических операций) упомянутого процесса, а именно:
установить электрические и временные нормативы нагрева в зависимости от марки стали и геометрических параметров заготовки;
определить (подобрать) ритм навивки пружины, то есть продолжительность времени от выемки заготовки из печи до момента погружения её в закалочную среду, в течение которого пружина перед закалкой не должна быть охлаждена ниже температуры 850°С;
обосновать продолжительность (время) минимальной "паузы" после закалки перед отпуском с целью исключения возможности образования в пружине всякого рода (вида) закалочных трещин;
определить (обосновать) величину расчётного параметра стрелы прогиба пружины, то есть разность между высотой пружины в свободном состоянии и высотой пружины, сжатой нагрузкой.
Список литературы
1. Электровоз с приводом переменного тока O’ZBEKISTON. Описание об использовании и содержании электровоза с приводом переменного тока для Узбекистана [Текст] / Технический центр при Чжучжоуском электровозостроительном заводе. – СSR: ЧЭВЗ, 2003. – 714 с.
27

Ремонт и динамика подвижного состава
УДК 629.423
В. А. Нехаев, В. А. Николаев, В. А. Ушак, М. Х. Минжасаров
СРАВНИТЕЛЬНЫЙ АНАЛИЗ ДИНАМИКИ ЛОКОМОТИВОВ МЕТОДАМИ ФИЗИЧЕСКОГО МОДЕЛИРОВАНИЯ
Физическое моделирование локомотивов, основанное на теории подобия, является одним из наиболее широко распространенных методов исследования динамики подвижного состава. В данной статье приведены результаты физического моделирования электровоза нового поколения 2ЭС10 «Гранит» с типовым и квазиинвариантным рессорными подвешиваниями.
Сложность процессов происходящих в вертикальной динамике электровозов полезно изучить в лабораторных условиях на основе математического и физического моделирования. Математическое моделирование основано на изучении уравнений описывающих протекающие процессы. Главный недостаток математического моделирования заключается в том, что исследуемый процесс воспроизводится лишь в рамках заданных уравнений, отражающих не реальную механическую систему, а ее расчетную схему [1]. При составлении расчетной схемы выполняются допущения, которые понижают точность моделирования.
В свою очередь физическое моделирование позволяет изучить особенности непосредственно самих механических процессов происходящих в системе и при обнаружении недостатков проектируемого локомотива внести изменения в конструкцию. Основные преимущество физического моделирования заключаются в том, что оно позволяет избежать решения системы нелинейных дифференциальных уравнений, которые решаются лишь приближенно.
Физическое моделирование не всегда позволяет получить модель натурного объекта по абсолютному подобию [2], которое представляет собой абстрактное понятие, реализуемое только умозрительно (в геометрических построениях и отдельных видах математического подобия). И как следствие, при решений практических технических задач, которым и является физическое
28
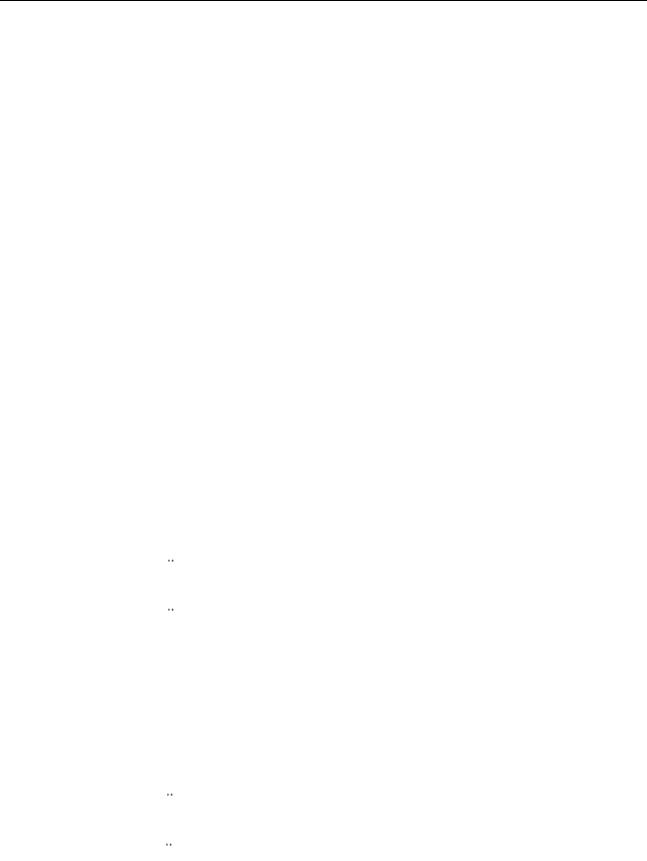
ТРАНСВУЗ – 2015
моделирование вертикальной динамики электровозов, используют методы приближенного или практического моделирования.
Для получения модели колебания локомотива и пути будем руководствоваться следующими правилами [1, 3]:
–исследуемые процессы локомотива и его модели должны описываться одинаковыми дифференциальными уравнениями или иметь одинаковые функциональные зависимости;
–начальные и граничные условия локомотива и модели должны быть тождественны;
–модель должна быть геометрически подобна объекту;
–одноименные критерии подобия, входящие в систему дифференциальных уравнений, описывающих моделируемые явления, в модели
иобъекте должны быть соответственно равны.
В общем случае при формировании системы дифференциальных уравнений вертикальной динамики локомотива возможно использование различных расчетных схем. Наиболее простой, но в тоже время содержательной моделью является так называемый «условный одноосный локомотив», который представляет собой два тела, соединенных упруго-диссипативными связями. Система дифференциальных уравнений, описывающая его движение с учетом выбранного возмущающего фактора (стыковой неровности пути) имеет вид [4]:
m z |
|
с (z |
|
z |
) 0; |
|
|
|
|
|
|
|
|
|
к |
к |
к |
к |
т |
|
|
|
|
|
V |
|
(1) |
|
|
|
ск (zт |
zк ) сб zт |
сб |
h |
cos |
||||||
mт zт |
|
1 |
|
t . |
|
||||||||
2 |
1.8 l |
|
|||||||||||
|
|
|
|
|
|
|
|
|
|
|
|
Для выполнения одного из условий подобия натурного локомотива и модели необходимо, чтобы они описывались одинаковой системой дифференциальных уравнений. Поэтому физическую модель локомотива следует представить в виде двух массовой модели, колебания которой описывались бы уравнениями:
m z |
|
с (z |
|
z ) 0; |
|
|
|
|
|
|
|
|
|
2 |
2 |
2 |
2 |
1 |
|
|
|
V |
|
|
(2) |
|
|
|
с2 (z1 |
z2 ) с1 z1 с1 |
h |
cos |
|
|||||
m1 z1 |
1 |
1 |
1 |
t1 |
. |
|
||||||
2 |
1.8 l1 |
|
||||||||||
|
|
|
|
|
|
|
|
|
|
|
где m2 – масса груза, моделирующего кузов;
29