
s90mec7
.pdf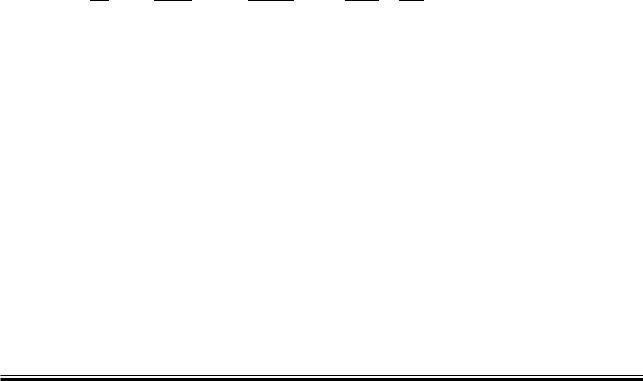
MAN B&W |
6.04 |
|
|
|
Page of 12 |
Exhaust Gas Amount and Temperature
Influencing factors
The exhaust gas data to be expected in practice depends, primarily, on the following three factors:
a) The specified MCR point of the engine (point M):
PM |
: power in kW at SMCR point |
nM |
: speed in r/min at SMCR point |
and to a certain degree on the matching point O with the percentage power PO% = % of SMCR power:
PO% = (PO/PM) x 100%
b)The ambient conditions, and exhaust gas back pressure:
Tair |
: actual ambient air temperature, in °C |
pbar |
: actual barometric pressure, in mbar |
TCW |
: actual scavenge air coolant temperature, |
|
in °C |
∆pM |
: exhaust gas back pressure in mm WC at |
|
specified MCR |
c)The continuous service rating of the engine (point S), valid for fixed pitch propeller or controllable pitch propeller (constant engine speed):
PS : continuous service rating of engine, in kW
Calculation Method
To enable the project engineer to estimate the actual exhaust gas data at an arbitrary service rating, the following method of calculation may be used.
The partial calculations based on the above influencing factors have been summarised in equations [4] and [5].
Mexh |
: exhaust gas amount in kg/h, to be found |
|
|
|
|
|
|
|
|||||||||
Texh |
: exhaust gas temperature in °C, to be found |
|
|
|
|
|
|
|
|||||||||
|
|
P |
|
∆m |
|
|
|
∆M |
|
|
∆m |
|
P |
|
|
||
Mexh |
= ML1 x |
M |
x 1 + |
|
M% x 1 + |
|
amb% x 1 + |
|
s% x |
S% |
kg/h |
+/ 5% [4] |
|||||
|
|
PL1 |
|
100 |
|
|
|
100 |
|
|
100 |
100 |
|
|
|||
Texh = TL1 + ∆TM + ∆TO + ∆Tamb + ∆TS |
°C /+15 °C |
|
|
|
|
|
[5] |
||||||||||
where, according to ‘List of capacities’, i.e. referring to ISO ambient conditions and 300 mm WC |
|||||||||||||||||
back pressure and specified/matched in L1: |
|
|
|
|
|
|
|
|
|||||||||
ML1: exhaust gas amount in kg/h at nominal MCR (L1) |
|
|
|
|
|
||||||||||||
TL1: exhaust gas temperature after turbocharger in °C at nominal MCR (L1) |
|
|
|||||||||||||||
|
|
|
|||||||||||||||
Fig. 6.04.06: Summarising equations for exhaust gas amounts and temperatures |
|
|
The partial calculations based on the influencing factors are described in the following:
a)Correction for choice of specified MCR point
When choosing a specified MCR point ‘M’ other than the nominal MCR point ‘L1’, the resulting
changes in specific exhaust gas amount and temperature are found by using as input in diagrams the corresponding percentage values (of L1) for specified MCR power PM% and speed nM%:
PM% = PM/PL1 x 100% nM% = nM/nL1 x 100%
MAN B&W ME-B, ME/ME C, ME GI engines
MAN Diesel |
198 43 18 1.2 |
|
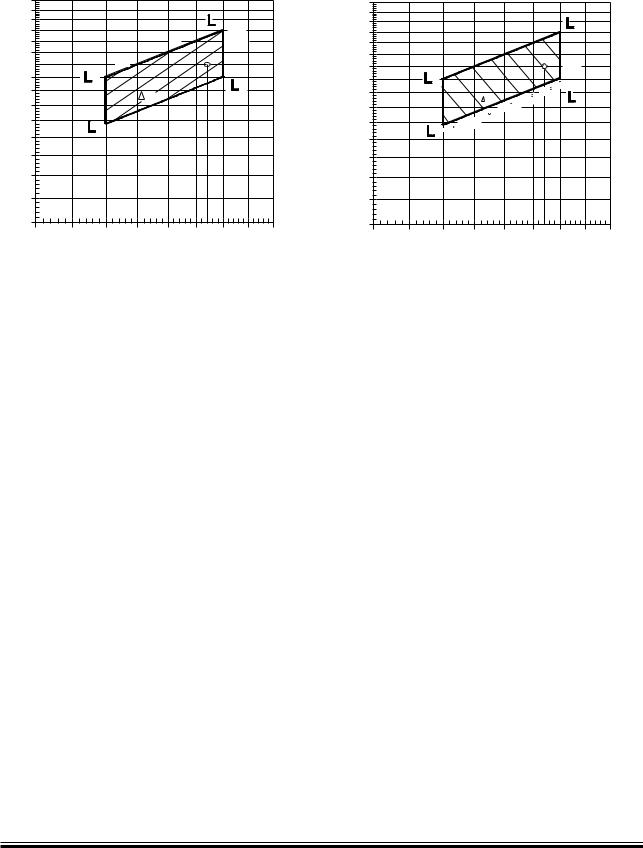
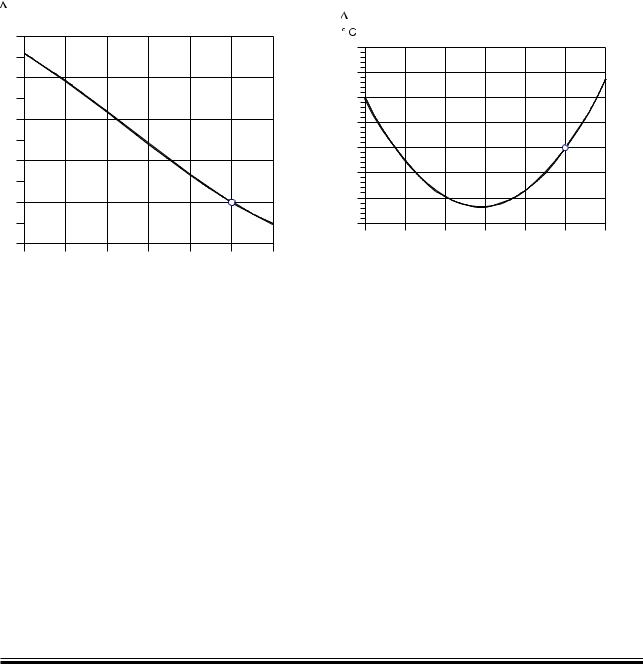

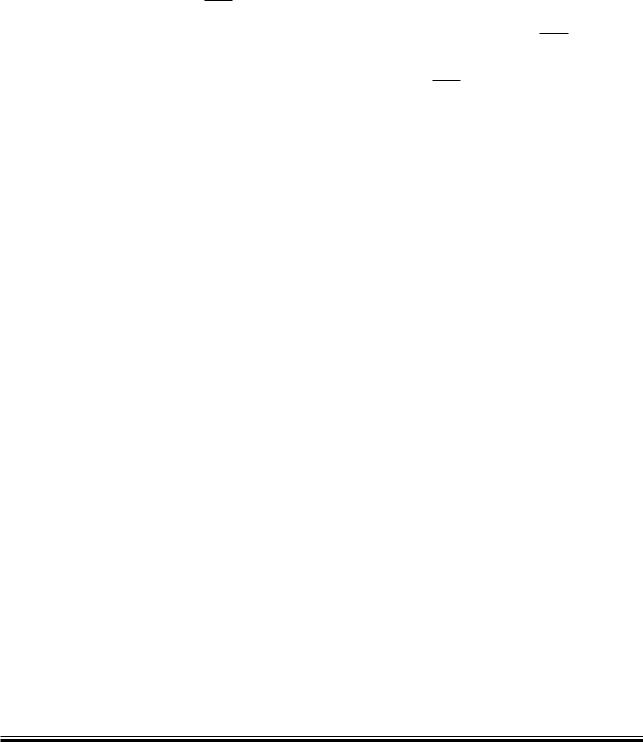
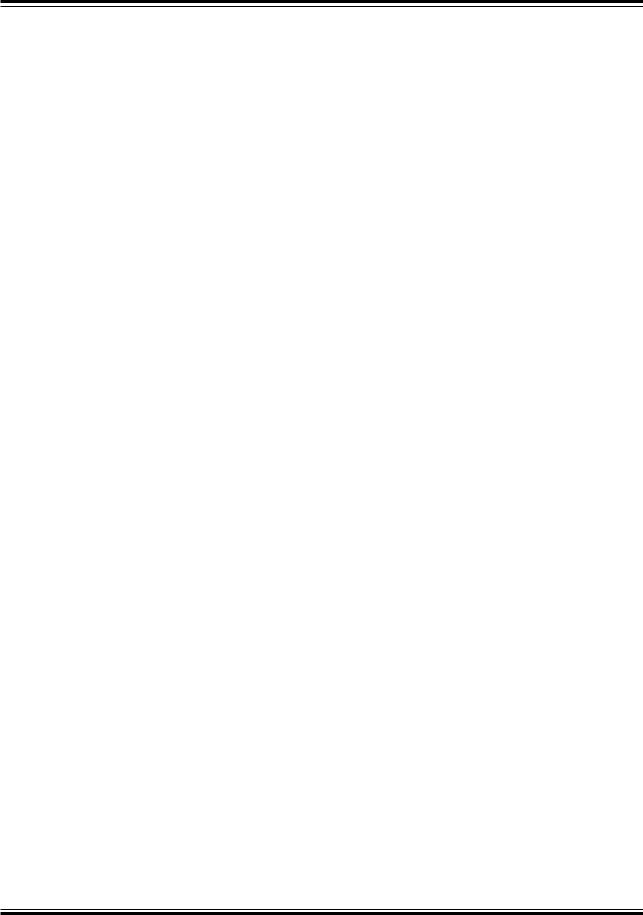

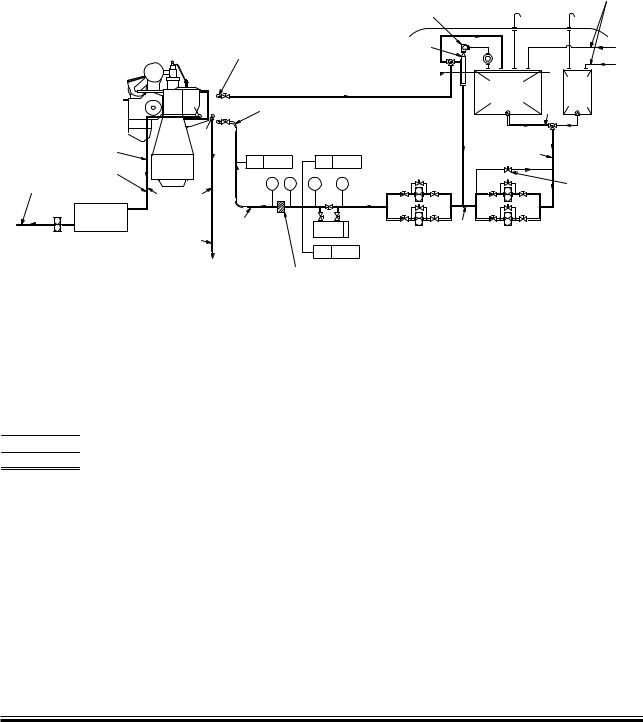