
- •ПРОИЗВОДСТВО КАБЕЛЕЙ И ПРОВОДОВ
- •ПРЕДИСЛОВИЕ
- •ОБЩИЕ СВЕДЕНИЯ О КАБЕЛЬНОМ ПРОИЗВОДСТВЕ
- •1.1. ОСНОВНЫЕ ТЕХНОЛОГИЧЕСКИЕ ПРОЦЕССЫ
- •1.2. КЛАССИФИКАЦИЯ КАБЕЛЬНОГО ОБОРУДОВАНИЯ
- •1.3. ОСНОВНЫЕ МЕХАНИЗМЫ КАБЕЛЬНЫХ МАШИН
- •1.4. ОТДАЮЩИЕ УСТРОЙСТВА
- •1.5. НАКОПИТЕЛИ
- •1.6. ТЯГОВЫЕ УСТРОЙСТВА
- •1.7. ИЗМЕРИТЕЛИ ДЛИНЫ
- •1.9. МЕХАНИЗМЫ РАСКЛАДКИ
- •1.10. МЕХАНИЗМЫ РЕГУЛИРОВАНИЯ СКОРОСТИ ПРИЕМНОГО УСТРОЙСТВА
- •1.11. ТЕХНОЛОГИЧЕСКАЯ ДОКУМЕНТАЦИЯ
- •КРУТИЛЬНЫЕ МАШИНЫ
- •2.1. ПРИНЦИП ДЕЙСТВИЯ КРУТИЛЬНЫХ МАШИН;
- •2.2. ТЕХНОЛОГИЧЕСКИЕ ПАРАМЕТРЫ ПРОЦЕССА СКРУТКИ
- •2.4. ОТКРУТКА ПРИ СКРУТКЕ
- •2.5. МАШИНЫ РАЗНОНАПРАВЛЕННОЙ СКРУТКИ
- •И НЕИЗОЛИРОВАННЫХ ПРОВОДОВ
- •3.1. СКРУТКА НЕИЗОЛИРОВАННЫХ ПРОВОДОВ ДЛЯ ЛИНИЙ ЭЛЕКТРОПЕРЕДАЧИ
- •3.4. СКРУТКА ГЕРМЕТИЗИРОВАННЫХ
- •тппгк
- •4.2. ЛЕНТО- и НИТЕОБМОТОЧНЫЕ МАШИНЫ
- •4.3.0БМ0ТКА БУМАЖНЫМИ ЛЕНТАМИ ЖИЛ СИЛОВЫХ КАБЕЛЕЙ НА НАПРЯЖЕНИЕ 1—35 кВ
- •4.4. ОСОБЕННОСТИ НАЛОЖЕНИЯ ИЗОЛЯЦИИ НА ЖИЛЫ МАСЛОНАПОЛНЕННЫХ КАБЕЛЕЙ
- •4.5. НАЛОЖЕНИЕ БУМАЖНОЙ ЛЕНТОЧНОЙ ИЗОЛЯЦИИ НА ЖИЛЫ КАБЕЛЕЙ СВЯЗИ
- •ИЗОЛЯЦИИ НА ЖИЛЫ КАБЕЛЕЙ СВЯЗИ
- •4.9. НАЛОЖЕНИЕ ВОЛОКНИСТОЙ ИЗОЛЯЦИИ НА ОБМОТОЧНЫЕ ПРОВОДА
- •5.1.3. Течение расплава полимера в дозирующей зоне экструдера
- •5.2. РАСЧЕТ ПРОЦЕССА ЭКСТРУЗИИ
- •5.2.1. Расчет количества полимера, поступающего в головку
- •5.2.2. Упрощенный расчет общей объемной производительности экструдера
- •5.3. УТОЧНЕННЫЕ МЕТОДЫ РАСЧЕТА ЭКСТРУЗИИ
- •5.4. ОСОБЕННОСТИ РАСЧЕТА ЭКСТРУДЕРОВ ДЛЯ ПЕРЕРАБОТКИ РЕЗИНОВЫХ СМЕСЕЙ
- •5.5. КЛАССИФИКАЦИЯ ЭКСТРУДЕРОВ
- •5.7. ФОРМУЮЩИЙ ИНСТРУМЕНТ И ТЕХНОЛОГИЧЕСКИЕ ПАРАМЕТРЫ ЭКСТРУЗИИ
- •НАЛОЖЕНИЕ ПЛАСТМАССОВОЙ И РЕЗИНОВОЙ ИЗОЛЯЦИИ МЕТОДОМ ЭКСТРУЗИИ
- •6.4. ОСОБЕННОСТИ НАЛОЖЕНИЯ СШИТОЙ ПОЛИЭТИЛЕНОВОЙ ИЗОЛЯЦИИ
- •>6.6. НАЛОЖЕНИЕ ПОРИСТОЙ ПОЛИЭТИЛЕНОВОЙ ИЗОЛЯЦИИ НА ЖИЛЫ КАБЕЛЕЙ СВЯЗИ
- •6.8. НАЛОЖЕНИЕ СПЛОШНОЙ ИЗОЛЯЦИИ ИЗ ФТОРОПЛАСТОВ
- •ЭМАЛИРОВАНИЕ
- •7.1. АГРЕГАТЫ ДЛЯ ПРОИЗВОДСТВА ЭМАЛИРОВАННЫХ ПРОВОДОВ
- •7.1.1. Агрегаты для производства проводов диаметром 0,015—0,09 мм
- •7.2. СПОСОБЫ И ТЕХНОЛОГИЯ ЭМАЛИРОВАНИЯ
- •ки толщиной
- •7.3. ЭМАЛИРОВАНИЕ ИЗ РАСПЛАВА СМОЛЫ
- •НЕТИПОВЫЕ СПОСОБЫ НАЛОЖЕНИЯ ИЗОЛЯЦИИ
- •8.1. ИЗОЛИРОВАНИЕ ЖИЛ КАБЕЛЕЙ СВЯЗИ ПОРИСТОЙ БУМАЖНОЙ МАССОЙ
- •8.2. ИЗГОТОВЛЕНИЕ КОАКСИАЛЬНЫХ ПАР С ШАЙБОВОЙ ИЗОЛЯЦИЕЙ
- •КАБЕЛЕЙ
- •9.3. СКРУТКА ГЕРМЕТИЗИРОВАННЫХ КАБЕЛЕЙ
- •9.4. СКРУТКА ЖИЛ КАБЕЛЕЙ СВЯЗИ В ПАРЫ И ЧЕТВЕРКИ
- •9.4.2. Скрутка жил кабелей дальней связи в четвёркй
- •9.5. ПОВЙВНАЯ СКРУТКА КАБЕЛЕЙ СВЯЗИ
- •9.6. ПУЧКОВАЯ СКРУТКА КАБЕЛЕЙ СВЯЗИ
- •ПРОЦЕССЫ СУШКИ И ПРОПИТКИ КАБЕЛЕЙ
- •10.1. СУШКА И ПРОПИТКА БУМАЖНОЙ ИЗОЛЯЦИИ СИЛОВЫХ КАБЕЛЕЙ
- •10.3. ПРИГОТОВЛЕНИЕ ПРОПИТОЧНЫХ СОСТАВОВ
- •НАЛОЖЕНИЕ МЕТАЛЛИЧЕСКИХ ОБОЛОЧЕК
- •11.1. СПОСОБЫ НАЛОЖЕНИЯ МЕТАЛЛИЧЕСКИХ ОБОЛОЧЕК
- •11.3. ТЕХНОЛОГИЧЕСКИЙ ПРОЦЕСС НАЛОЖЕНИЯ СВИНЦОВЫХ ОБОЛОЧЕК
- •11.7. ТЕХНОЛОГИЯ ПРЕССОВАНИЯ АЛЮМИНИЕВЫХ ОБОЛОЧЕК
- •11.8.2. Высокочастотная сварка оболочек
- •11.9. ГОФРИРОВАНИЕ ОБОЛОЧЕК
- •НАЛОЖЕНИЕ ОБОЛОЧЕК И ШЛАНГОВ ИЗ ПЛАСТМАСС И РЕЗИНЫ
- •12.1. НАЛОЖЕНИЕ ПОЛИЭТИЛЕНОВЫХ ОБОЛОЧЕК И ШЛАНГОВ НА ЭКСТРУЗИОННЫХ АГРЕГАТАХ
- •12.3. ОСОБЕННОСТИ НАЛОЖЕНИЯ АЛЮМОПОЛИЭТИЛЕНОВЫХ ОБОЛОЧЕК
- •НАЛОЖЕНИЕ ЭКРАНИРУЮЩИХ И ЗАЩИТНЫХ ОПЛЕТОК
- •13.1. ТЕХНОЛОГИЧЕСКИЕ ПАРАМЕТРЫ ОПЛЕТКИ
- •13.3. НАЛОЖЕНИЕ ПРОВОЛОЧНЫХ ЭКРАНОВ И ЗАЩИТНЫХ ОПЛЕТОК
- •13.4. НАЛОЖЕНИЕ ВОЛОКНИСТЫХ ЗАЩИТНЫХ ОПЛЕТОК
- •13.5. ПРОПИТКА ПРОВОДОВ
- •13.6. ЛАКИРОВКА ПРОВОДОВ
- •НАЛОЖЕНИЕ БРОНЕПОКРОВОВ
- •14.1. БРОНИРОВОЧНЫЕ МАШИНЫ
- •14.3. ТЕХНОЛОГИЯ НАЛОЖЕНИЯ ЗАЩИТНЫХ ПОКРОВОВ
- •14.4. НАЛОЖЕНИЕ ПРОФИЛЬНОЙ [ГИБКОЙ] БРОНИ
- •ВСПОМОГАТЕЛЬНЫЕ ПРОЦЕССЫ КАБЕЛЬНОГО ПРОИЗВОДСТВА
- •15.1. ПЕРЕМОТКА ПОЛУФАБРИКАТА, ЗАГОТОВКИ И ГОТОВЫХ КАБЕЛЕЙ И ПРОВОДОВ
- •15.2. РЕЗКА БУМАГИ И ПЛЕНОК НА ЛЕНТЫ
- •15.4. ИЗГОТОВЛЕНИЕ РЕЗИНОВЫХ СМЕСЕЙ
- •15.5. ПРЕДВАРИТЕЛЬНАЯ ПРОПИТКА МАТЕРИАЛОВ ЗАЩИТНЫХ ПОКРОВОВ
- •ОПЕРАЦИОННЫЙ КОНТРОЛЬ В ПРОИЗВОДСТВЕ КАБЕЛЕЙ И ПРОВОДОВ
- •16.2. ОПЕРАЦИОННЫЙ КОНТРОЛЬ
- •36.3. УПРАВЛЕНИЕ КАЧЕСТВОМ
- •17.1. ОСНОВЫ ТЕХНИКИ БЕЗОПАСНОСТИ И ПРОИЗВОДСТВЕННОЙ САНИТАРИИ
- •17.2. ОСНОВЫ ПРОТИВОПОЖАРНОЙ ТЕХНИКИ
- •ОСНОВЫ ПРОЕКТИРОВАНИЯ КАБЕЛЬНОГО ПРОИЗВОДСТВА
- •18.1. ОРГАНИЗАЦИЯ КАБЕЛЬНОГО ПРОИЗВОДСТВА — СТРУКТУРА ЗАВОДА И ЦЕХА
- •18.3. ПЛАНИРОВКА ЦЕХОВ И ОТДЕЛЕНИИ
- •18.4. ОПРЕДЕЛЕНИЕ СЕБЕСТОИМОСТИ ПРОДУКЦИИ И ТЕХНИКО-ЭКОНОМИЧЕСКИХ
- •СПИСОК ЛИТЕРАТУРЫ
ных кабелей в первом технологическом варианте совме щаются вторая и третья, а во втором — первая и вторая операции.
Внедрение принципиально новых ,машин разнона правленной скрутки открыло широкие возможности совмещения как однородных, так и разнородных техно логических операций. Так, при построении технологи ческого потока по второму варианту можно объединить третью операцию — циклической разнонаправленной скрутки малопарных сердечников из элементарных пуч ков с операциями продольного наложения экрана и на ложения пластмассовой оболочки. В то же время сов мещение таких двух операций, как разнонаправленная скрутка главных пучков и однонаправленная скрутка многопарных сердечников, представляется нецелесооб разным из-за громоздкости комбинированной машины, которая бы понадобилась для этой цели, и из-за много образия вариантов конструкций кабелей, содержащих от трех-четырех пучков до полутора-двух десятков пуч
ков. |
скрутки |
элементарных пучков |
т = |
Кратности шага |
|||
= 40ч-'50, а главных |
пучков |
т = 304-40. Кратность |
ша |
га скрутки внешнего повива сердечников т = 20-4-25.
Глава десятая
ПРОЦЕССЫ СУШКИ И ПРОПИТКИ КАБЕЛЕЙ
10.1. СУШКА И ПРОПИТКА БУМАЖНОЙ ИЗОЛЯЦИИ СИЛОВЫХ КАБЕЛЕЙ
Для получения высоких электрических характеристик бумажная изоляция силовых кабелей подвергается суш ке и пропитке маслами или специальными пропиточны ми составами. Электрические свойства изоляции тем лучше, чем меньшее количество влаги остается в изоля ции после сушки.
В исходном состоянии бумажная изоляция кабеля при относительной влажности окружающего воздуха 70—80% содержит 6—8% влаги. При этом, если клас сифицировать влагу по характеру связи с бумажной изо ляцией, можно выделить следующие виды влаги: хи мически связанная влага, т. е. влага, входящая в состав
молекулы целлюлозы в виде гидроксильных групп; ад сорбционная влага — влага, находящаяся на поверхнос ти бумажных лент, а также на стенках капиллярных со судов в виде мономолекулярного слоя; капиллярная вла га — влага, заполняющая микро- и макрокапилляры по ристой бумажной изоляции и механически связанная влага.
Наибольшей энергией связи обладает химическая влага, удаление ее связано с процессом деструкции мо лекул целлюлозы, и поэтому режимы сушки должны быть выбраны так, чтобы не допустить удаления хими-
Рис. 10.1. Распределение температу ры и влажности по толщине изоляции кабеля при сушке.
Ти Т2— температурные кривые в начале и конце первой стадии сушки; w x, w2 — рас пределение влажности в изоляции в начале и конце первой стадии сушки.
чески связанной влаги. Все остальные виды влаги в про цессе сушки желательно удалить. Чем выше напряже ние, на которое рассчитан кабель, тем меньше должно быть остаточное содержание влаги в изоляции. В изоля ции кабелей высокого напряжения после сушки жела тельно иметь не более 0,05—0,07% влаги.
Сушка изоляции кабеля производится при темпера туре 100—135 °С в вакууме с остаточным давлением 6,5—400 Па. В начальной стадии сушки, когда содержа ние влаги изоляции велико, удаление влаги из кабеля происходит за счет явления диффузии влаги, термодиф фузии и термовлагопроводности. Диффузия влаги — движение влаги под действием градиента влажности, ко торый создается в изоляции на первой стадии сушки. Действительно, под действием высокой температуры и при наличии вакуума вокруг изоляции происходит интен сивное испарение влаги с поверхности кабеля, поэтому влажность наружных слоев становится значительно меньше, чем влажность слоев изоляции, расположенных у жилы (рис. 10.1).
Термодиффузия характеризуется молекулярным пе реносом влаги в изоляции под действием потока тепла в более холодную часть изоляции. Для интенсификации этого процесса необходимо создать з изоляции градиент температуры. Этот градиент получается при нагревании кабеля постоянным током в жиле. Одновременно обогре ваются и наружные слои изоляции, однако их нагрев от стает от нагрева жилы, что и позволяет получить гради ент температуры по толщине изоляции кабеля (рис. 10.1). Перенос влаги при термовлагопроводности обусловлен движением жидкости, заполняющей капилляры, в сторо ну менее нагретых слоев за счет разности поверхностных натяжений менисков водяных включений.
В процессе сушки происходит постепенный нагрев ка беля, а также уменьшение и перераспределение влаги в изоляции. При этом скорость сушки замедляется. Это объясняется тем, что постепенно изменяется градиент влажности (рис. 10.1), что связано с уменьшением ис парения влаги с поверхности (с уменьшением влажнос ти уменьшается парциальное давление воды на поверхности изоляции, следовательно, уменьшается ко личество испаряемой жидкости). Кроме того, при уве личении температуры и уменьшении влажности изоляции замедляется и практически прекращается явление тер мовлагопроводности. После проведения этого этапа суш ки влагосодержание изоляции снижается до 1%, т. е. удаляется основное количество влаги из изоляции (меха нически связанная влага и влага макрокапилляров).
Более низкое содержание влаги, необходимое для изоляции кабелей высокого напряжения, можно полу чить, применив глубокую степень разряженности окру жающей среды (высоковакуумная сушка). Остаточное давление среды вокруг кабеля должно составлять 0,1— 0,01 Па. Эта фааа сушки может продолжаться значи тельное время. Здесь происходит удаление влаги из мик рокапилляров и адсорбционно связанной влаги. В конце высоковакуумной сушки возможно даже некоторое газоотделение за счет частичного разложения целлюлозы.
Определенный эффект может дать высокочастотная сушка, которая применяется для кабелей высокого на пряжения и проводится перед высоковакуумной сушкой. При подключении кабеля к генератору напряжения час тотой 600—800 кГц происходит интенсивный нагрев изо ляции за счет диэлектрических потерь, причем так как
влажность менее нагретых наружных слоев к моменту высокочастотного нагрева выше, чем влажность слоев, расположенных у жилы, то снаружи выделяется боль- ~ шее количество энергии. При этом изоляция кабеля рав номерно прогревается до 115—120 °С.
Перенос влаги, несмотря на изотермическое поле внутри изоляции, происходит в этот момент очень интен сивно, так как он обусловлен разностью избыточных дав лений водяного пара внутри изоляции. Однако при вве дении высокочастотного нагрева появляется возмож ность возникновения тлеющих разрядов в изоляции ка беля, что может ухудшить качество изоляции.
Пропитка силовых кабелей напряжением до 35 кВ включительно производится вязкими маслоканифольны ми составами. Изоляция кабелей напряжением 110 кВ и выше пропитывается минеральными маслами малой ли бо средней вязкости. При температуре пропитки 105— 120°С, однако, все эти составы обладают малой вяз костью, что делает возможным полную пропитку бу мажной изоляции.
Процесс пропитки кабеля можно условно разделить на два этапа: первый этап — пропитка бумажной изоля ции, второй этап — заполнение пустот в жиле, причем второй этап не менее важен, чем первый, так как нали чие воздушных включений в жиле так же нежелательно, как и в изоляции. В процессе эксплуатации кабеля под воздействием циклических токовых нагрузок воздушные включения, находящиеся в жиле, могут перемещаться внутрь изоляции, при этом электрическая прочность кабеля уменьшается.
На первом этапе пропитки проникновение массы в
изоляцию происходит за счет давления р\ |
|
||
|
Р= р1—р2 +р3, |
(Ю .1) |
|
где р\ — давление над |
зеркалом |
пропиточного |
состава; |
р2— противодавление, |
оказываемое воздушными вклю |
||
чениями, находящимися внутри |
кабеля; р3 — давление, |
эквивалентное силам адсорбции.
Если пропитка происходит под действием атмосфер ного давления или при некотором избыточном давле нии пропиточного состава, то давление рз намного меньше р\. Давление р2 увеличивается в процессе заполнения пор бумажной изоляции. Если в начале про цесса р2 определяется степенью разреженности прост-
27 — 1201 |
417 |
ранства при вакуумной сушке, то в конце первого эта па эту величину можно рассчитывать, пользуясь зако ном Бойля — Мариотта, так как процесс пропитии про исходит при постоянной температуре:
( 10.2)
Р г к Он ’
где Р2п и р2К— давление воздушных включений кабель ной изоляции в начале и конце первого этапа пропитки‘> он и Ок — объем воздушных включений в кабеле 0 нача ле и конце первого этапа пропитки.
Если положить, что
° н = |
(1 ~ т1)т.г\-\-тк(Я2 — г\); |
(10.3) |
ик = |
(1 — т?) w*0, |
|
где г] — коэффициент заполнения жилы; т — пористость бумажной изоляции (для изоляции силовых кабелей 0,5), т. е. отношение объема воздуха к объему Цел люлозы; /о и Я — радиусы кабеля по жиле и по изоля
ции, то |
|
А* = Л н{1+ T Z ^ [ ( - £ ) — ! ]}- |
(10-4) |
Выражение в фигурных скобках в формуле (10.4) зависит только от конструкции и геометрических разме ров кабеля, поэтому порядок этой величины может быть оценен для каждой конкретной конструкции. Для кабе лей 35 кВ значение этого выражения колеблется от 10 до 30. Однако если учесть, что р2п составляет около 130—260 Па, то р2к « 1300-^-4200 Па, что составляет 2—4% атмосферного и, следовательно, на первом этапе пропитки изменением этой величины можно пренебречь.
Таким образом, на первом этапе скорость пропитки определяется практически только давлением над зерка лом пропиточного состава при прочих равных условиях. Из уравнения Дарси для определения скорости пропитки
S= —k grad р, |
(10.5) |
где S — скорость проникновения пропиточного состава в изоляцию на единице длины кабеля; k — коэффициент фильтрации; р — давление пропиточного состава, мож но получить выражение для времени, необходимого для
418
полного заполнения пустот |
в изоляции, т. |
е. времени |
первого этапа пропитки: |
|
|
t = ■ |
2kpt |
( 10.6) |
На втором этапе пропитки заполнение пустот в жи ле происходит под действием давления
P = P i — p2. |
(Ю.7) |
В этом случае изменение рч в процессе пропитки су щественно и его нельзя не учитывать. Время заполнения пустот в жиле можно определить также, воспользовав шись уравнением (10.5), однако при этом необходимо учесть изменение р2, используя зависимость (10.2), при чем в выражение (10.2) следует ввести поправку, учи тывающую частичное растворение воздуха в пропиточ ном составе при пропитке, что несколько снижает р2. Тогда время окончания пропитки на втором этапе мож но рассчитать по более сложной формуле:
t = |
Ук |
Вр2Н |
Pi П —а) |
Pi |
(I — «) Pi |
Pi ВРгн ) ) . 00.8) |
|
где а — коэффициент |
растворимости |
воздуха в пропи- |
|
точном составе; |
|
|
? = i
Анализируя (10.6) и (10.8), можно сделать следую щие выводы.
Время пропитки существенно уменьшается, если уве личивать давление Р\.
Из анализа (10.8) видно, что время t может сущест венно возрастать при больших отрицательных значениях выражения
|
In ( |
Pi (1 — « л |
|
Pl — iPlш ) ’ |
|
Последнее возможно, |
если |
|
Л |
— ■р,(| |
|
\ |
Pi |
PP211 J |
Отсюда можно получить начальное давление воздуш ных включений или, что то же самое, максимальное ос-
27* |
419 |
таточное давление окружающей кабель среды при его
сушке. |
|
Действительно, из условия |
* вытекает, что |
полная пропитка возможна лишь при |
|
<109»
Таким образом, если p2n>api/p, то t-+oо, а это озна чает, что при выбранных режимах полной пропитки ка беля не произойдет. Соотношение (10.9) позволяет выбрать давление в кабеле при сушке, которое обес печивает полную пропитку кабеля. Для кабеля 35 кВ Р2и<0,01рь что при /?1= 0,1 МПа составляет 0,001 МПа.
10.2. СУШИЛЬНО-ПРОПИТОЧНОЕ ОБОРУДОВАНИЕ. ПРИНЦИП ДЕЙСТВИЯ, КЛАССИФИКАЦИЯ, УСТРОЙСТВО
Принципиальные схемы сушки и пропитки изоляции силовых кабелей представлены на рис. 10.2—10.4. Все применяемое оборудование в этих схемах можно разде лить на следующие основные группы: сушильно-пропи точные котлы; вакуумные системы, обеспечивающие нужное разрежение среды в сушильно-пропиточных котлах, емкостях для хранения пропиточного состава, а также в дегазационных устройствах; оборудование для подготовки пропиточного состава (дегазационные ко лонки, фильтры); теплообменники для пропиточного со става; насосы для перекачки пропиточного состава; си стема дистанционного управления и автоматического контроля за режимами сушки и пропитки.
Если пропитка кабеля производится маслоканифоль ными составами, то кроме перечисленного оборудования необходимо также оборудование для варки пропиточ ных составов (варочный котел, котел-дегазатор и т. д.).
Сушильно-пропиточные котлы вертикального типа для кабелей на напряжение до 35 кВ (рис. 10.5) имеют диаметр 3—4 м, высота котлов около 2,5 м, что позволя ет размещать внутри две-три корзины с кабелем. Котлы имеют паровой обогрев.
Давление пара в паровой рубашке котла составляет 0,3—0,4 МПа. В верхней части котел имеет ввод ваку ум-провода, в нижней — патрубок для ввода пропиточ-
420
Рис. 10.2. Схема установки для сушки и пропитки кабелей на напря жение до 35 кВ.
/ — котел для псдготопки массы; 2 — насос |
для |
перекачки массы; |
3 — резер |
||||||||
вуар для хранения необработанной массы; |
4 — дозирующий |
насос; |
5 — тепло |
||||||||
обменник, 6 — фильтр; |
7, 8 — дегазатор |
(I |
и II |
ступеней); |
9 — маслоотдели |
||||||
тель; Ю — глубоковакуумная |
установка; |
11— вакуумная |
установка; |
12 — ре |
|||||||
зервуар |
для хранения |
готовой массы; |
13 — насос |
для подачи |
массы |
под |
дав |
||||
лением; |
/-/ — насос для |
перекачки отработанной |
массы; |
15 — котел для сушки |
|||||||
и пропитки кабелей; |
/6 — устройство |
для |
охлаждения |
откачиваемого |
газа |
||||||
(конденсационная колонка); |
/7 —г подача |
холодной воды |
в |
конденсационную |
|||||||
колонку; |
18 — вакуумная насосная установка; 19 — электрический обогрев. |
|
ного состава. Кроме того, в стенке котла имеется элек трический ввод для подключения к жилам кабеля постоянного напряжения, а также несколько измеритель ных вводов для проводов термопар или терморезисто ров. В паровой рубашке котла предусматриваются пат рубки для ввода пара под давлением (сверху) и для вы вода конденсата (снизу). Сверху котел закрывается крышкой со смотровым окном. Конструкция уплотняю-
Рис. 10.3. Схема установки для сушки и пропитки высоковольтных кабелей (110—500 кВ).
/ — дозирующий насос; 2 — теплообменник; 3, 4 — дегазатор (I и II ступеней); 5 — маслоотделитель; 6 — диффузионный насос; 7 — высоковакуумная насосная установка; 8 — вакуумная насосная установка; 9 — насос для перекачки масла;
10 '—фильтр; |
// — конденсатор; |
12 — дегазатор |
(3-я ступень); |
13 — резервуар |
|
для готового масла; 14 — насос |
для |
перекачки |
отработанного |
масла; /5 —про |
|
межуточный |
резервуар; 16 — кстел |
для сушки |
и пропитки; |
/7 —шлюз; 18 — |
|
пресс для наложения металлической |
оболочки; |
19 — электрический обогрев. |
щего устройства должна обеспечивать создание остаточ ного давления в котле 260—1300 Па, а также пропитку под избыточным давлением 0,15 МПа. В современных котлах уплотнение крышки производится с помощью прокладки из кремнийорганической резины и байонет ного затвора. Байонетный затвор позволяет создать не обходимое давление на прокладку за счет поворота
крышки |
на |
некоторый угол |
вокруг вертикальной оси |
|
котла. |
|
|
|
напря |
Для проведения сушки и пропитки кабелей |
||||
жением |
до |
35 кВ включительно кабели укладываются |
||
в корзины, |
которые затем |
устанавливаются в |
котлах. |
После пропитки и охлаждения корзины с пропитанным
кабелем вместе с пропиточным |
составом извлекаются |
из котлов и устанавливаются на |
отдающее устройство |
422
для наложения металлической оболочки. При такой ор ганизации технологического процесса есть возможность попадания воздушных включений в изоляцию кабеля при наложении оболочки. Поэтому современные сушильно пропиточные установки, предназначенные для изготовле
ния кабелей на 110 кВ и выше, исключают возможность непосредственного воздействия на изоляцию кабеля ок ружающей среды.
Для сушки и пропитки таких кабелей применяются котлы прямоугольной формы значительно больших раз меров (рис. 10.6), которые позволяют размещать внут ри на барабане одну или две строительные длины кабе ля. Котел также имеет паровой обогрев, электрические выводы для подключения кабеля к источнику постоян ного напряжения 50—500 В при токе 500 А (а при необ ходимости также к высокочастотному генератору) и для проводов термопар или терморезисторов, патрубки для подключения к вакуум-проводу и к системе подачи пропиточного масла. Система герметизации котла по зволяет поддерживать внутри остаточное давление по рядка 1,0—0,1 Па, а также производить пропитку кабе лей под давлением 0,15 МПа. Охлаждение кабеля после
Рис. 10.4. Схема установки для сушки и пропитки кабелей высокого напряжения после наложения металлической оболочки.
/ — дозирующий насос; 2 — теплообменник; 3 — фильтр; 4 и 5 — дегазатор (I и
II |
ступеней); 6 — маслоотделитель; |
7 — диффузионный |
насос; 8 — вакуумная |
||
насосная установка; 9 — резервуар |
для хранения |
готового масла; 10 — насос |
|||
для |
нагнетания масла; // — концевые |
соединения; |
12 — предварительно высу |
||
шенный в сушильной камере кабель |
в металлической |
оболочке. |
пропитки должно производиться в котле, и для ускоре ния этого процесса в конструкции котла предусматрива ется возможность принудительной замкнутой циркуля ции пропиточного масла под давлением с его охлаж дением в теплообменнике. После охлаждения кабель подается на пресс для наложения металлической оболоч ки непосредственно из котла через специальное шлюзо вое устройство. Это устройство имеет герметичное сое динение с котлом и с головкой пресса. Перед началом опрессования устройство вакуумируется и может за полняться пропиточным маслом, что обеспечивает сохра нение высоких свойств изоляции.
Свойства пропитанной изоляции во многом опреде ляются, как уже отмечалось, степенью разрежения при сушке. Поэтому очень важен выбор соответствующих
424
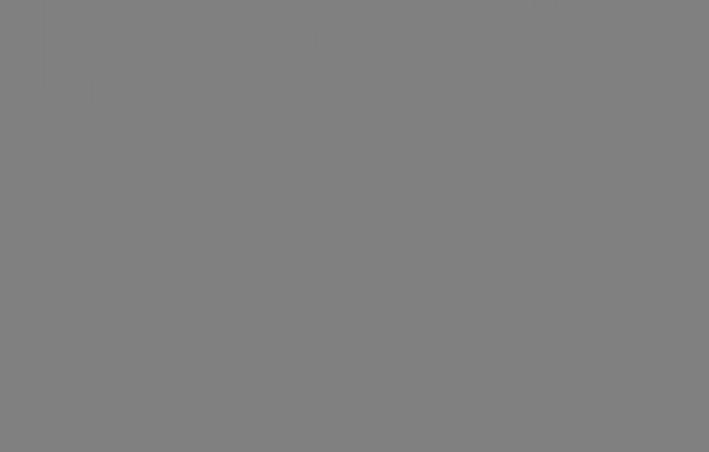
вакуумных установок. Особенностью работы вакуум ных установок является требование откачки больших объемов воздуха, содержащих пары воды или масла. Поэтому в системы вакуумных установок, как правило, включаются вакуумные насосы, конденсационные колон ки и маслоотделители.
Вакуумные насосы, применяемые для сушки и про питки кабелей до 35 кВ, в основном являются насосами механическими, т. е. действие их основано на механи ческом сжатии и выталкивании откачиваемого газа. В
указанных схемах применяются |
насосы двух типов — |
||
поршневые (типа ДВНП-6) |
и |
плунжерные |
(типа |
ВН-6Г). Поршневые насосы типа |
ДВНП-6— это |
двух |
ступенчатые насосы, причем одна ступень используется для создания разрежения в зоне выброса газа основной ступенью. Это позволяет получить в откачиваемом объ еме более высокий вакуум. Наибольшей скоростью откач ки обладают плунжерные насосы (около 120 л/с). С по мощью этих насосов можно получить, кроме того, более низкое остаточное давление в откачиваемом объеме — 130,0—200 Па. Плунжерные насосы относятся к враща
тельным насосам с масляным |
уплотнением |
(рис. 10.7). |
В процессе работы эксцентричный ротор со специаль |
||
ным плунжерным устройством |
увеличивает или умень |
|
шает объем рабочей камеры. |
В момент |
наименьшего |
объема рабочая камера соединяется с впускным патруб ком насоса. При последующем увеличении объема ра бочей камеры в нее засасывается откачиваемый газ до тех пор, пока объем ее достигнет максимума. В этот момент камера отсоединяется от впускного патрубка. За тем объем рабочей камеры начинает уменьшаться. При этом происходит сжатие газа до атмосферного давления и выталкивание его через выпускной клапан. При низ ком остаточном давлении в откачиваемом объеме необ ходима дополнительная герметизация деталей насоса, чтобы препятствовать перетеканию газа со стороны вы сокого давления на сторону впуска. Это достигается на личием масляной пленки. Для этого в насос заливается определенное количество вакуумного масла марок ВМ-4, ВМ-6.
Следует иметь в виду, что обычно вращающиеся на сосы с масляным уплотнением не пригодны для откач ки парогазовых смесей, так как при сжатии (коэффици ент сжатия в таких насосах достигает 700) происходит
конденсация пара внутри рабочей камеры, образуется водно-масляная эмульсия, которая стекает в сторону впускного клапана и, испаряясь, вновь попадает в отка чиваемый объем.
Для откачки парогазовых смесей более пригодны насосы, снабженные специальным газобалластным уст ройством. Это устройство впускает в рабочую камеру в момент сжатия сухой воздух. Количество воздуха под бирается таким образом, чтобы давление в рабочей ка
Рис. |
10.7. Схема |
плунжер |
Рис. |
10.8. Схема |
двухротор |
ного |
вакуумного |
насоса. |
ного |
вакуумного |
насоса. |
мере было достаточным для открывания выпускного клапана, но при этом оно меньше, чем давление насы щения паров. Насос типа ВН-6Г является плунжерным насосом с газобалластным устройством.
Для сушки и пропитки кабелей сверхвысокого на пряжения для обеспечения остаточного давления поряд ка 0,1—0,01 Па необходимо применять специальные ва куумные агрегаты, состоящие из двухроторных насосов типа 2ДВН-1500 и последовательно соединенных с ними насосов плунжерного типа ВН-6Г. Двухроторные насо сы (рис. 10.8) применяются в основном для откачки больших объемов до давлений 0,1—0,01 Па. Основной частью этих насосов являются роторы специальной кон фигурации, вращающиеся в противоположные стороны с большими скоростями. Этим достигается необходимое быстродействие насосов (1500 л/с). Однако сравнитель
но большие зазоры между роторами и небольшой коэф фициент компрессии позволяют применять эти насосы только при последовательном соединении с механичес кими масляными насосами.
Для устойчивой работы вакуумных насосов при от качке паров, содержащих большое количество влаги (особенно в первые часы сушки кабелей), между насо сом и сушильно-пропиточным котлом устанавливается конденсационная колонка, где происходят охлаждение воздуха и частичная конденсация водяных паров за счет соприкосновения с поверхностью вертикальных тру бок, внутри которых протекает холодная вода. При ва куумировании пространства над поверхностью масла
Рис. 10.9. Способы дегазации масла.
а —дегазация |
а каплях; б — дегазация в пленках; / — форсунка; 2 — змеевик |
для обогрева |
колонки паром; 3 — алюминиевые кольца. |
или пропиточного состава необходимо между откачива емым объемом и вакуумным насосом размещать масло отделитель для уменьшения количества масляных паров, попадающих в насос. Конденсация масляных паров в маслоотделителе осуществляется за счет соприкосно вения с холодными поверхностями.
Наиболее простыми дегазационными устройствами являются котлы-дегазаторы, в которых поддерживается температура 125°С и остаточное давление 1,5—2,5 кПа. Эти котлы предназначены для дегазации маслокани фольных составов методом замкнутой циркуляции в те чение 8—12 ч. Объем дегазационного состава примерно 2/з объема котла-дегазатора.