
- •ПРОИЗВОДСТВО КАБЕЛЕЙ И ПРОВОДОВ
- •ПРЕДИСЛОВИЕ
- •ОБЩИЕ СВЕДЕНИЯ О КАБЕЛЬНОМ ПРОИЗВОДСТВЕ
- •1.1. ОСНОВНЫЕ ТЕХНОЛОГИЧЕСКИЕ ПРОЦЕССЫ
- •1.2. КЛАССИФИКАЦИЯ КАБЕЛЬНОГО ОБОРУДОВАНИЯ
- •1.3. ОСНОВНЫЕ МЕХАНИЗМЫ КАБЕЛЬНЫХ МАШИН
- •1.4. ОТДАЮЩИЕ УСТРОЙСТВА
- •1.5. НАКОПИТЕЛИ
- •1.6. ТЯГОВЫЕ УСТРОЙСТВА
- •1.7. ИЗМЕРИТЕЛИ ДЛИНЫ
- •1.9. МЕХАНИЗМЫ РАСКЛАДКИ
- •1.10. МЕХАНИЗМЫ РЕГУЛИРОВАНИЯ СКОРОСТИ ПРИЕМНОГО УСТРОЙСТВА
- •1.11. ТЕХНОЛОГИЧЕСКАЯ ДОКУМЕНТАЦИЯ
- •КРУТИЛЬНЫЕ МАШИНЫ
- •2.1. ПРИНЦИП ДЕЙСТВИЯ КРУТИЛЬНЫХ МАШИН;
- •2.2. ТЕХНОЛОГИЧЕСКИЕ ПАРАМЕТРЫ ПРОЦЕССА СКРУТКИ
- •2.4. ОТКРУТКА ПРИ СКРУТКЕ
- •2.5. МАШИНЫ РАЗНОНАПРАВЛЕННОЙ СКРУТКИ
- •И НЕИЗОЛИРОВАННЫХ ПРОВОДОВ
- •3.1. СКРУТКА НЕИЗОЛИРОВАННЫХ ПРОВОДОВ ДЛЯ ЛИНИЙ ЭЛЕКТРОПЕРЕДАЧИ
- •3.4. СКРУТКА ГЕРМЕТИЗИРОВАННЫХ
- •тппгк
- •4.2. ЛЕНТО- и НИТЕОБМОТОЧНЫЕ МАШИНЫ
- •4.3.0БМ0ТКА БУМАЖНЫМИ ЛЕНТАМИ ЖИЛ СИЛОВЫХ КАБЕЛЕЙ НА НАПРЯЖЕНИЕ 1—35 кВ
- •4.4. ОСОБЕННОСТИ НАЛОЖЕНИЯ ИЗОЛЯЦИИ НА ЖИЛЫ МАСЛОНАПОЛНЕННЫХ КАБЕЛЕЙ
- •4.5. НАЛОЖЕНИЕ БУМАЖНОЙ ЛЕНТОЧНОЙ ИЗОЛЯЦИИ НА ЖИЛЫ КАБЕЛЕЙ СВЯЗИ
- •ИЗОЛЯЦИИ НА ЖИЛЫ КАБЕЛЕЙ СВЯЗИ
- •4.9. НАЛОЖЕНИЕ ВОЛОКНИСТОЙ ИЗОЛЯЦИИ НА ОБМОТОЧНЫЕ ПРОВОДА
- •5.1.3. Течение расплава полимера в дозирующей зоне экструдера
- •5.2. РАСЧЕТ ПРОЦЕССА ЭКСТРУЗИИ
- •5.2.1. Расчет количества полимера, поступающего в головку
- •5.2.2. Упрощенный расчет общей объемной производительности экструдера
- •5.3. УТОЧНЕННЫЕ МЕТОДЫ РАСЧЕТА ЭКСТРУЗИИ
- •5.4. ОСОБЕННОСТИ РАСЧЕТА ЭКСТРУДЕРОВ ДЛЯ ПЕРЕРАБОТКИ РЕЗИНОВЫХ СМЕСЕЙ
- •5.5. КЛАССИФИКАЦИЯ ЭКСТРУДЕРОВ
- •5.7. ФОРМУЮЩИЙ ИНСТРУМЕНТ И ТЕХНОЛОГИЧЕСКИЕ ПАРАМЕТРЫ ЭКСТРУЗИИ
- •НАЛОЖЕНИЕ ПЛАСТМАССОВОЙ И РЕЗИНОВОЙ ИЗОЛЯЦИИ МЕТОДОМ ЭКСТРУЗИИ
- •6.4. ОСОБЕННОСТИ НАЛОЖЕНИЯ СШИТОЙ ПОЛИЭТИЛЕНОВОЙ ИЗОЛЯЦИИ
- •>6.6. НАЛОЖЕНИЕ ПОРИСТОЙ ПОЛИЭТИЛЕНОВОЙ ИЗОЛЯЦИИ НА ЖИЛЫ КАБЕЛЕЙ СВЯЗИ
- •6.8. НАЛОЖЕНИЕ СПЛОШНОЙ ИЗОЛЯЦИИ ИЗ ФТОРОПЛАСТОВ
- •ЭМАЛИРОВАНИЕ
- •7.1. АГРЕГАТЫ ДЛЯ ПРОИЗВОДСТВА ЭМАЛИРОВАННЫХ ПРОВОДОВ
- •7.1.1. Агрегаты для производства проводов диаметром 0,015—0,09 мм
- •7.2. СПОСОБЫ И ТЕХНОЛОГИЯ ЭМАЛИРОВАНИЯ
- •ки толщиной
- •7.3. ЭМАЛИРОВАНИЕ ИЗ РАСПЛАВА СМОЛЫ
- •НЕТИПОВЫЕ СПОСОБЫ НАЛОЖЕНИЯ ИЗОЛЯЦИИ
- •8.1. ИЗОЛИРОВАНИЕ ЖИЛ КАБЕЛЕЙ СВЯЗИ ПОРИСТОЙ БУМАЖНОЙ МАССОЙ
- •8.2. ИЗГОТОВЛЕНИЕ КОАКСИАЛЬНЫХ ПАР С ШАЙБОВОЙ ИЗОЛЯЦИЕЙ
- •КАБЕЛЕЙ
- •9.3. СКРУТКА ГЕРМЕТИЗИРОВАННЫХ КАБЕЛЕЙ
- •9.4. СКРУТКА ЖИЛ КАБЕЛЕЙ СВЯЗИ В ПАРЫ И ЧЕТВЕРКИ
- •9.4.2. Скрутка жил кабелей дальней связи в четвёркй
- •9.5. ПОВЙВНАЯ СКРУТКА КАБЕЛЕЙ СВЯЗИ
- •9.6. ПУЧКОВАЯ СКРУТКА КАБЕЛЕЙ СВЯЗИ
- •ПРОЦЕССЫ СУШКИ И ПРОПИТКИ КАБЕЛЕЙ
- •10.1. СУШКА И ПРОПИТКА БУМАЖНОЙ ИЗОЛЯЦИИ СИЛОВЫХ КАБЕЛЕЙ
- •10.3. ПРИГОТОВЛЕНИЕ ПРОПИТОЧНЫХ СОСТАВОВ
- •НАЛОЖЕНИЕ МЕТАЛЛИЧЕСКИХ ОБОЛОЧЕК
- •11.1. СПОСОБЫ НАЛОЖЕНИЯ МЕТАЛЛИЧЕСКИХ ОБОЛОЧЕК
- •11.3. ТЕХНОЛОГИЧЕСКИЙ ПРОЦЕСС НАЛОЖЕНИЯ СВИНЦОВЫХ ОБОЛОЧЕК
- •11.7. ТЕХНОЛОГИЯ ПРЕССОВАНИЯ АЛЮМИНИЕВЫХ ОБОЛОЧЕК
- •11.8.2. Высокочастотная сварка оболочек
- •11.9. ГОФРИРОВАНИЕ ОБОЛОЧЕК
- •НАЛОЖЕНИЕ ОБОЛОЧЕК И ШЛАНГОВ ИЗ ПЛАСТМАСС И РЕЗИНЫ
- •12.1. НАЛОЖЕНИЕ ПОЛИЭТИЛЕНОВЫХ ОБОЛОЧЕК И ШЛАНГОВ НА ЭКСТРУЗИОННЫХ АГРЕГАТАХ
- •12.3. ОСОБЕННОСТИ НАЛОЖЕНИЯ АЛЮМОПОЛИЭТИЛЕНОВЫХ ОБОЛОЧЕК
- •НАЛОЖЕНИЕ ЭКРАНИРУЮЩИХ И ЗАЩИТНЫХ ОПЛЕТОК
- •13.1. ТЕХНОЛОГИЧЕСКИЕ ПАРАМЕТРЫ ОПЛЕТКИ
- •13.3. НАЛОЖЕНИЕ ПРОВОЛОЧНЫХ ЭКРАНОВ И ЗАЩИТНЫХ ОПЛЕТОК
- •13.4. НАЛОЖЕНИЕ ВОЛОКНИСТЫХ ЗАЩИТНЫХ ОПЛЕТОК
- •13.5. ПРОПИТКА ПРОВОДОВ
- •13.6. ЛАКИРОВКА ПРОВОДОВ
- •НАЛОЖЕНИЕ БРОНЕПОКРОВОВ
- •14.1. БРОНИРОВОЧНЫЕ МАШИНЫ
- •14.3. ТЕХНОЛОГИЯ НАЛОЖЕНИЯ ЗАЩИТНЫХ ПОКРОВОВ
- •14.4. НАЛОЖЕНИЕ ПРОФИЛЬНОЙ [ГИБКОЙ] БРОНИ
- •ВСПОМОГАТЕЛЬНЫЕ ПРОЦЕССЫ КАБЕЛЬНОГО ПРОИЗВОДСТВА
- •15.1. ПЕРЕМОТКА ПОЛУФАБРИКАТА, ЗАГОТОВКИ И ГОТОВЫХ КАБЕЛЕЙ И ПРОВОДОВ
- •15.2. РЕЗКА БУМАГИ И ПЛЕНОК НА ЛЕНТЫ
- •15.4. ИЗГОТОВЛЕНИЕ РЕЗИНОВЫХ СМЕСЕЙ
- •15.5. ПРЕДВАРИТЕЛЬНАЯ ПРОПИТКА МАТЕРИАЛОВ ЗАЩИТНЫХ ПОКРОВОВ
- •ОПЕРАЦИОННЫЙ КОНТРОЛЬ В ПРОИЗВОДСТВЕ КАБЕЛЕЙ И ПРОВОДОВ
- •16.2. ОПЕРАЦИОННЫЙ КОНТРОЛЬ
- •36.3. УПРАВЛЕНИЕ КАЧЕСТВОМ
- •17.1. ОСНОВЫ ТЕХНИКИ БЕЗОПАСНОСТИ И ПРОИЗВОДСТВЕННОЙ САНИТАРИИ
- •17.2. ОСНОВЫ ПРОТИВОПОЖАРНОЙ ТЕХНИКИ
- •ОСНОВЫ ПРОЕКТИРОВАНИЯ КАБЕЛЬНОГО ПРОИЗВОДСТВА
- •18.1. ОРГАНИЗАЦИЯ КАБЕЛЬНОГО ПРОИЗВОДСТВА — СТРУКТУРА ЗАВОДА И ЦЕХА
- •18.3. ПЛАНИРОВКА ЦЕХОВ И ОТДЕЛЕНИИ
- •18.4. ОПРЕДЕЛЕНИЕ СЕБЕСТОИМОСТИ ПРОДУКЦИИ И ТЕХНИКО-ЭКОНОМИЧЕСКИХ
- •СПИСОК ЛИТЕРАТУРЫ
мя зонами — 1-я зона не менее 50°С, 2-я зона не менее 40°С, 3-я зона — водопроводная вода.
Обдув полиэтиленовых корделя и трубки для удале ния с поверхности влаги производится сжатым возду хом давлением не менее 0,2—0,3 МПа.
Рис. 6.7. Ф ормующ ий инструмент для изготовления трубки из поли этилена для изоляции радиочастотны х кабелей.
а — матрица с цилиндрической частью; б — дорн.
Скорость изготовления корделя 40—110 м/мин, вре мя его охлаждения 3—9 с, длина охлаждающей ванны 6—12 м и время, необходимое для охлаждения трубки из полиэтилена, 4,5—20 с.
После наложения полиэтиленовой трубки ее прива ривают к корделю хотя бы в одной точке по длине вит ка спирали.
6.8. НАЛОЖЕНИЕ СПЛОШНОЙ ИЗОЛЯЦИИ ИЗ ФТОРОПЛАСТОВ
Оплошная .изоляция для различных видов нагревостойких ка
белей и проводов выполняется обычно из |
фторополимеров, |
назы |
|||||
ваемых |
фторопластами. Ф торопласт-4, обладаю щ ий |
наиболее |
вы |
||||
сокими электроизоляционны ми характеристиками, не |
м ож ет |
|
пере |
||||
рабатываться м етодом экструзии расплава, |
так как д а ж е |
при |
тем |
||||
пературе, превышающей 370°С, его вязкость |
очень велика. П оэтом у |
||||||
этот материал применяется для изоляции в |
виде пленок, |
суспензий, |
|||||
а такж е |
с |
помощ ью специальных способов переработки. |
Ф торо- |
||||
пласт-4М Б, |
фторопласт-40111, ф торопласт-2М |
относят |
к |
так |
назы |
ваемым плавким фторполимерам . Они .при определенны х тем перату рах переходят в состояние расплава, причем несмотря на то, что вязкости их расплавов довольно высокие, эти материалы мож но перерабаты вать на экструзионны х линиях.
Вкабельной промышленности применяются следую щ ие отече
ственные плавкие фториолимеры . |
Ф торолласт-4М Б, представляю |
|||
щий собой сополимер этилена и |
гексафторлропилена, |
имеет |
при |
|
300°С вязкость |
расплава 103— 105 |
П а -с. Температура |
его перера |
|
ботки составляет |
370— 390°С. |
|
|
|
ф торопласт-4М Б -2 отличается |
от фторопласта-4М Б |
более |
ста- |
т
бильными электроизоляционны ми характеристиками в области вы соких частот и температур.
Указанны е материалы применяются для изоляции и оболочки различных нагревостойких кабелей и проводов, причем ф торопласт-
4М Б -2 используется |
главным образом длярадиочастотны х и |
вы со |
ковольтных кабелей и проводов. |
|
|
П орообразую щ ий |
ф торопласт-4М Б -2, представляю щ ий |
собой |
композицию сополим ера этилена и гексафторпропилена с неболь
шими |
количествами |
нитрида |
бора |
и |
ф реона, |
при |
|
переработке |
об р а |
|||||||||||||||
зует |
пористую |
изоляцию, |
использую щ ую ся |
для |
изоляции |
нагрево |
||||||||||||||||||
стойких радиочастотны х кабелей. |
|
|
|
|
|
|
|
|
|
|
|
|
|
|
|
|||||||||
Фторопласт-40111 представляет собой сополимер этилена |
и |
|||||||||||||||||||||||
тетраф торэтилеяа. |
Вязкость |
расплава |
|
этого |
материала |
при |
295°С |
|||||||||||||||||
составляет |
|
104— 106 |
П а -с, |
а |
ф торопласта-40Ш Б — 104— 105 |
П а -с . |
||||||||||||||||||
Тем пература |
певеработки |
этих |
м атериалов 300— 340°С. Они |
приме |
||||||||||||||||||||
|
|
|
|
|
|
|
|
|
|
няются |
в |
трех кабелях и проводах, |
||||||||||||
|
|
|
|
|
|
|
|
|
|
где требуется повы ш енная стой |
||||||||||||||
|
|
|
|
|
|
|
|
|
|
кость |
|
изоляции |
к |
механическим |
||||||||||
|
|
|
|
|
|
|
|
|
|
воздействиям |
в |
сочетании |
с вы со |
|||||||||||
|
|
|
|
|
|
|
|
|
|
кой |
радиационной |
стойкостью |
и |
|||||||||||
|
|
|
|
|
|
|
|
|
|
повышенной |
|
нагревостойкосты о. |
||||||||||||
|
|
|
|
|
|
|
|
|
|
|
|
Ф торопласт-2 |
представляет |
|||||||||||
|
|
|
|
|
|
|
|
|
|
собой |
|
полимер |
|
винилиденфтори- |
||||||||||
Рис. 6.8. С хема |
налож ения |
и зо |
|
да, |
а |
ф торопласт-2М — м одиф ици |
||||||||||||||||||
|
рованный |
ф торопласт-2, |
|
об л а д а ю |
||||||||||||||||||||
ляции с вы тяжкой (м етодом |
|
щий |
|
меньшими |
|
ж есткостью , |
твер |
|||||||||||||||||
осаж ден и я ). |
|
|
|
|
|
|
|
достью |
и |
тем пературой |
|
плавле |
||||||||||||
|
|
|
|
|
|
|
|
|
|
ния. |
|
Соответственно у |
этого |
м а |
||||||||||
териала лучш ие технологичность и холодостойкость, |
больш ее |
удл и |
||||||||||||||||||||||
нение |
при |
разрыве. Ф торопласт-2М |
используется |
для |
изоляции |
м он |
||||||||||||||||||
таж ны х проводов |
и |
изготовления |
механически |
прочных |
|
оболочек. |
||||||||||||||||||
Температура |
его переработки |
составляет |
210 — 250°С. |
|
|
|
|
|
|
|||||||||||||||
П о сравнению |
с |
такими |
ш ироко распространенны ми терм опла |
|||||||||||||||||||||
стами, как полиэтилен и поливинилхлоридны й |
пластикат, |
п ерера |
||||||||||||||||||||||
ботка |
плавких |
фторопластов |
связана |
с |
|
рядом |
особенностей. П р еж |
|||||||||||||||||
д е всего |
следует |
отметить, |
что |
тем пература |
переработки |
|
плавких |
фторопластов выше, чем тем пература других термопластов, и она
близка |
к |
тем пературе разлож ения, что |
требует |
тщ ательной |
регу |
||||||||
лировки температуры |
по зонам |
экструдера. Д ля разны х |
материалов |
||||||||||
колебания |
этой температуры |
|
не |
долж ны |
превышать |
2— 10°С. |
|||||||
С ледует |
отметить |
такж е |
высокую |
вязкость |
раоплавов |
ук азан |
|||||||
ных плавких |
фторопластов. |
В |
то |
ж е |
время критические |
скорости |
|||||||
сдвига |
для |
расплавов |
этих полимеров невысоки. Отмеченные |
ф ак |
|||||||||
торы |
обусловливаю т |
необходим ость |
применения |
деталей |
головки |
экструдера с плавными внутренними переходам и, сглаженны ми
углами, |
что |
облегчает |
пр охож дени е |
расплава |
через эти |
каналы и |
||||||||||
уменьш ает возм ож ность |
заторм аж ивания его |
слоев |
и |
разлож ения. |
||||||||||||
Д ля |
предотвращ ения |
возм ож ности |
разры ва |
расплава |
(см. |
|||||||||||
§ 5 .1 ), |
наблю даю щ егося |
при |
достиж ении |
критических |
скоростей |
|||||||||||
сдвига, |
применяют экструдеры с небольш им |
диам етром |
червяка |
|||||||||||||
(25— 45 |
мм) |
и небольш ой |
частотой |
вращ ения |
(до |
10— 30 |
о б /м и н ). |
|||||||||
Кроме |
того, |
использую т |
способ |
налож ения изоляции |
с |
вы тяжкой |
||||||||||
(рис. |
6 .8). Вы тяжка |
по |
сечению, |
например, |
для ф торопласта-4М Б |
|||||||||||
м ож ет |
|
достигать |
до |
2 0 0 :1 . |
При |
таком |
способе |
обеспечивается |
||||||||
высокая |
линейная |
скорость |
изолирования |
при сравнительно |
мальде |
Скоростях |
бдвигй в расплаве полимера, вы ходящ его |
йз |
головкй |
|
в виде трубки со значительно больш ей толщиной, |
чем |
требуем ая |
||
толщ ина |
изоляции. |
|
|
|
Трудности переработки плавких ф торопластов |
связаны |
такж е |
с вы делением ими при высоких тем пературах переработки агрес
сивных |
летучих |
продуктов, оказы вающ их |
вредное |
воздействие на |
|||||
оборудование, а |
такж е и |
на |
обслуж иваю щ ий персонал. Вы деляю |
||||||
щ иеся |
продукты |
разлож ения |
разруш аю т |
обычные |
стали, |
причем |
|||
ж елезо |
является, |
в |
свою |
очередь, |
катализатором разлож ения этих |
||||
фторполимеров. П о |
этой |
причине |
для изготовления |
деталей |
экстру |
||||
дера, |
соприкасаю щ ихся |
с |
расплавом, |
применяют специальные |
коррозионно-стойкие хромоникелевы е и никель-молибденовы е спла вы с небольшим содерж анием ж елеза.
П ри температуре фторполимеров свыше |
200— 250°С наблю дает |
ся вы деление в незначительных количествах |
фтористого водорода |
ифторированны х углеводородов. При тем пературах выше 300—
350°С вы деляю тся |
такие |
токсичные |
вещ ества, как перф торизобути- |
||||||||||||
лен, |
фтористый карбонил. Указанны е |
газообразны е |
продукты |
бес |
|||||||||||
цветны и не имею т ощ утимого |
зап аха. При |
наруш ении |
правил |
тех |
|||||||||||
ники |
безопасности |
они |
могут вызывать |
у |
обслуж иваю щ его персо |
||||||||||
нала |
признаки отравления |
(сухость |
в |
горле, |
недом огание, |
сла |
|||||||||
бость). В се кабельное |
оборудование для |
переработки фторполимеров |
|||||||||||||
при |
повышенных |
тем пературах |
снабж ается |
системами |
вентиляции |
||||||||||
для |
удаления газообразны х |
продуктов |
разлож ения. |
|
|
|
|||||||||
|
(Выбор |
разм еров |
и |
формы |
червяка, |
формую щ его |
инструмента |
||||||||
для |
экструдеров обусловлен требованиями к расплаву, отмеченны |
||||||||||||||
ми |
выше. |
М атрица |
применяется |
обычно двухконусная, углы |
по |
||||||||||
ворота каналов вы бираю тся равными 45°. П ри больш их углах |
уве |
||||||||||||||
личивается |
давление |
и |
создаю тся |
дополнительны е |
неж елательны е |
||||||||||
нагрузки в |
экструдере, |
при |
меньш их |
углах |
за |
счет |
увеличения по |
верхностей трения могут увеличиться скорости сдвига и возникнет
опасность |
разры ва |
расплава. |
Д лина |
матрицы |
составляет |
||||
(12— 2 0 ) £ Иэ. Если |
изоляция или |
оболочка |
наклады вается |
без |
вы |
||||
тяж ки, |
то |
диам етр |
матрицы немного превы шает требуемы й |
д и а |
|||||
метр по |
изоляции |
или оболочке. Зазор м еж ду дорном |
и |
матрицей |
устанавливается |
1,5— 2,5 мм. |
|
|
|
|
|
|
|
||||
В экструдерах для переработки плавких ф торопластов приме |
||||||||||||
няются |
червяки |
с отнош ением длины к |
диам етру |
д о 20 — 25. Чащ е |
||||||||
использую тся червяки |
с |
короткой |
зоной |
сж атия (длина |
ее |
состав |
||||||
ляет |
половину |
ш ага |
нарезки). Д озирую щ ая зона |
по |
длине |
равна |
||||||
4— 5 |
диам етрам |
червяка. |
Степень |
сж атия |
составляет |
3— 4. |
П овы |
|||||
ш енная |
вязкость расплава ф торопластов |
требует |
более |
мощ ного |
||||||||
(в |
1,5— 2 раза) |
привода |
экструдера. В |
|
современны х |
экструдерах |
применяется привод постоянного тока с тиристорным управлением,
обеспечиваю |
щ им возм ож ность |
плавного |
изменения частоты вращ е |
|
ния червяка |
в |
ш ироком диапазоне. |
|
|
В виду вы |
соких вязкостей |
расплавов |
и вероятности разлож ения |
при высоких тем пературах переработки к экструдерам для пере
работки |
плавких |
|
фторопластов |
предъявляю тся ж есткие |
требования |
||||||||
к стабильности |
температурны х |
реж имов. |
Ц илиндр экструдера, |
пе |
|||||||||
реходны й |
участок |
от |
цилиндра |
к |
головке |
и сама |
головка имеют |
||||||
индивидуальные |
зоны |
обогрева |
с |
автоматическим |
поддерж анием |
||||||||
заданны х |
температур. |
В |
зоне загрузки |
охлаж дение |
цилиндра |
во |
|||||||
дяное, |
а |
в остальных |
зон ах — воздуш ное |
при помощ и |
вентилято |
||||||||
ров. О хлаж дение |
червяка, |
как |
правило, |
не |
применяется. |
|
Я р и |
переработке плавких фторопластов недопустим о |
д а ж е м е |
||||||||||
стное |
охлаж ден ие |
расплава. |
Это |
м ож ет |
привести к резком у |
ув е |
||||||
личению |
вязкости |
и торм ож ению |
массы |
с последую щ им |
ее |
р азл о |
||||||
ж ением |
или ж е к |
образованию в |
толщ е |
изоляции |
участков |
с |
внут |
|||||
ренними |
напряжениями, |
которые |
сущ ественно |
повы ш ают |
склон |
|||||||
ность |
изоляции |
кабелей |
и проводов к растрескиванию . |
|
|
|
||||||
По |
этой |
ж е |
причине |
необходим |
подогрев |
заготовки |
|
перед |
входом в головку экструдера. В зависим ости от вида фторопласта
температура заготовки |
вы бирается |
в |
пределах |
от 120 |
д о |
280°С |
и |
||
долж на |
ж естко |
контролироваться |
и |
поддерж иваться |
постоянной, |
||||
так как перегрев |
сверх |
нормы приводит к разлож ению |
материала, |
||||||
а недостаточный |
нагрев — сниж ает стойкость |
к растрескива-нию. |
|||||||
В |
зависимости от |
скорости |
охлаж ден ия |
вы ходящ его |
из |
го |
ловки слоя полимера получается та или иная степень его кристал
личности. |
|
При |
медленном |
|
охлаж дении |
|
степень |
кристалличности |
|||||||||||||||||||||||
выше, |
причем |
больш ое |
значение |
имеет |
вид |
материала. П оэтом у |
для |
||||||||||||||||||||||||
охлаж дения |
проводов |
с |
изоляцией |
из |
плавких |
ф торопластов |
|
приме |
|||||||||||||||||||||||
няют |
разны е |
способы |
охлаж дения: |
холодную |
|
и |
горячую |
воду, |
|||||||||||||||||||||||
а |
такж е |
воздуш ное |
|
охлаж ден ие |
как |
наиболее |
м едленное. |
|
|
|
|||||||||||||||||||||
|
Как |
указы валось |
выше, |
|
при |
налож ении |
изоляции |
с |
|
вы тяжкой |
|||||||||||||||||||||
м ож но |
|
получить |
больш ие |
скорости |
изолирования |
при |
небольш их |
||||||||||||||||||||||||
частотах |
вращ ения |
червяка |
|
(10— 20 |
о б /м и н ). |
Н апример, |
|
при |
нал о |
||||||||||||||||||||||
жении |
|
изоляции |
из |
|
ф торопласта-4М Б |
с |
вы тяжкой |
на |
экструдере |
||||||||||||||||||||||
с |
червяком |
32 |
мм |
при |
|
частоте |
вращ ения |
червяка |
10— 15 |
об/м и н |
|||||||||||||||||||||
м ож но |
|
наклады вать |
тонкостенную |
изоляцию |
с |
линейной |
|
скоростью |
|||||||||||||||||||||||
до 200 м /м ин . Величина вытяжки В связана |
с |
разм ерам и |
ф орм ую |
||||||||||||||||||||||||||||
щего инструмента и изготавливаем ого |
провода |
следую щ им |
соотн о |
||||||||||||||||||||||||||||
шением |
(см. рис. |
6.8): |
|
|
|
|
|
|
Д2М- |
D \ |
|
|
|
|
|
|
|
|
|
|
|
|
|||||||||
|
|
|
|
|
|
|
|
|
|
|
|
|
JTP |
|
|
|
|
|
|
|
|
|
|
|
(6 .3) |
||||||
|
|
|
|
|
|
|
|
|
|
В = 7 T - D * - d \ |
|
|
|
|
|
|
|
|
|
|
|
||||||||||
|
|
|
|
|
|
|
|
|
|
|
|
|
|
|
|
|
|
|
|
|
|
||||||||||
где Dм — диаметр матрицы; |
|
/ ) д — наруж ны й |
диам етр дорна; |
|
£>из — |
||||||||||||||||||||||||||
диаметр |
|
по |
изоляции; |
dm — диам етр |
токопроводящ ей |
жилы; |
5 Тр, |
||||||||||||||||||||||||
5 из — поперечны е |
сечения |
вы прессовы ваемой |
трубки |
и |
слоя |
|
изоля |
||||||||||||||||||||||||
ции после |
осаж дения. |
|
|
|
|
|
|
|
|
|
|
|
|
|
|
|
|
В, м ож но |
|
||||||||||||
|
И з |
|
(6.3) видно, |
что, |
изменяя |
величину |
вы тяжки |
при |
|||||||||||||||||||||||
том ж е |
ф ормую щ ем |
|
инструменте |
получать |
провода |
с |
разной |
тол |
|||||||||||||||||||||||
щиной |
|
изоляции. |
О днако |
установлено, что |
сущ ествую т |
|
оптималь |
||||||||||||||||||||||||
ные величины вытяжки, |
обеспечиваю щ ие |
наилучш ие |
характеристики |
||||||||||||||||||||||||||||
изолированного |
провода |
|
(стабильность |
диам етра |
по |
изоляции, элек |
|||||||||||||||||||||||||
трической |
прочности, |
механических |
характеристик |
и |
д р .). |
|
Так, |
для |
|||||||||||||||||||||||
ф торопласта-4М Б |
оптимальное |
значение |
вытяжки |
В составляет |
50. |
||||||||||||||||||||||||||
Расплав |
долж ен |
быть вытянут |
до |
нуж н ого |
диам етра |
по |
|
изоляции |
|||||||||||||||||||||||
на |
расстоянии |
10— 30 |
мм |
от |
конца |
матрицы |
(см. рис. |
6 .8). |
|
|
|
||||||||||||||||||||
|
С |
учетом температурной |
|
усадки |
при |
охлаж дении |
налож енного |
||||||||||||||||||||||||
с |
вы тяжкой |
слоя |
изоляции |
из |
ф торопласта-4М Б |
|
диаметр |
матрицы |
|||||||||||||||||||||||
определяю т |
с помощ ью следую щ его |
соотнош ения: |
|
|
|
|
|
|
|
|
|
||||||||||||||||||||
|
|
|
|
|
|
|
|
|
|
D M= |
U |
|
5 |
^ |
p |
4 |
|
|
|
|
|
|
|
|
|
|
|
(6 .4) |
|||
|
|
|
|
|
|
|
|
|
|
|
|
|
|
|
|
|
иж |
|
|
|
|
|
|
|
|
|
|
|
|
|
|
|
Д лина |
цилиндрической |
|
части |
|
матрицы |
принимается |
равной |
|||||||||||||||||||||||
20Da3. Угол нарезки червяка равен |
20°. |
Температурны е |
режимы |
||||||||||||||||||||||||||||
переработки |
плавких |
|
фторопластов |
|
приведены |
в |
табл. |
6.11. |
|
|
|
Т а б л и ц а 6.11
Температурные режимы в экструдере при переработке плавких фторопластов
|
|
|
Температура, °< |
|
|
Материал |
Цилиндр по зонам |
Головка |
Матрица |
||
|
1-я |
2-я |
3-я |
||
|
|
|
|||
Ф торопласт-4М Б |
260— 310 |
280— 320 |
320— 340 |
340— 380 |
330— 370 |
Фторопласт-40111 |
260— 280 |
280— 310 |
330— 340 |
340— 350 |
310— 330 |
Ф торопласт-2М |
180— 210 |
220— 240 |
250— 270 |
270— 290 |
260— 270 |
6.9. НАЛОЖЕНИЕ И ВУЛКАНИЗАЦИЯ РЕЗИНОВОЙ ИЗОЛЯЦИИ
Производство изолированных резиной токопроводя щих жил кабелей, проводов и шнуров является в техно логическом отношении более сложным процессом, чем производство жил с изоляцией из полиэтилена или по ливинилхлоридного пластиката. Это объясняется тем, что полученный после наложения в экструдере слой ре зины необходимо подвергнуть в у л к а н и з а ц и и , в ре зультате которой невулканизованная пластичная рези новая смесь за счет образования сшитой структуры при обретет эластические свойства.
Вулканизацию проводят или раздельно с наложе нием изоляции, или одновременно. В первом случае пос ле наложения слоя резиновой изоляции его охлаждают в ванне с холодной водой и кабельное изделие или по луфабрикат принимают на барабаны или специальные тарелки с тальком с соблюдением мер, исключающих взаимную деформацию витков с мягкой невулканизованной изоляцией. Принципиальная схема экструзион ной линии, использующейся при раздельном наложении и вулканизации резиновой изоляции или оболочки, при ведена на рис. 6.9.
После наложения изоляции или оболочки осуществ ляется процесс вулканизации в специальных вулкани зационных котлах, горизонтального или вертикального типа. В первых проводится процесс вулканизации кабе лей или проводов, намотанных на барабаны, во вто рых— кабелей или проводов, уложенных на специаль ные тарелки. Последний способ применяется для изго товления крупногабаритных кабелей или проводов, имеющих значительную массу на единицу длины.

| |
Следует отметить, что если |
I |
раньше раздельные изолирова- |
| |
ние и вулканизация широко при- |
§менялись на кабельных заводах,
*то в настоящее время наиболее
ч> широко используется совмещен-
уный способ наложения и вулка-
§низации резиновой изоляции или
§ |
оболочки на к а б е л ь н ы х |
ли- |
S |
ния х н е п р е р ы в н о й |
в у л- |
uк а н и з а ц и и (ЛКНВ). Схема
§ЛКНВ представлена на рис. 6.10.
|
в |
Для |
вулканизации |
слоя |
резины, |
||||||
|
l" |
наложенной |
в |
экструдере |
этой |
||||||
-• « |
линии, |
используется |
теплоноси- |
||||||||
тель |
— |
насыщенный |
водяной |
||||||||
§ S |
пар, |
находящийся |
при |
высоком |
|||||||
§ “ |
(1,3—2,0 МПа) давлении в длин- |
||||||||||
S | |
ной |
вулканизационной |
камере, |
||||||||
•g | |
Повышенная |
температура |
пара |
||||||||
g | |
(190—210°С) |
и |
большая |
длина |
|||||||
| |
| |
вулканизационной |
и |
охлаждаю- |
|||||||
§, ° |
щих |
камер позволяют допускать |
|||||||||
к ■* |
большие |
скорости |
прохождения |
||||||||
| |
а |
изолированной |
токопроводящей |
||||||||
g | |
жилы через узлы линии. Приме- |
||||||||||
3 | |
нение ЛКНВ, |
кроме |
повышения |
||||||||
* * |
производительности, |
обеспечива- |
|||||||||
4 о, |
ет значительную |
экономию |
за |
||||||||
х з |
счет |
сокращения |
производствен- |
||||||||
* | |
ных площадей, количества при- |
||||||||||
* 4 |
меняемого оборудования, количе- |
||||||||||
'§ Is |
ства операций и межоперацион- |
||||||||||
я |
gig, |
ных |
транспортировок, численно- |
||||||||
| |
У® |
сти рабочего персонала и др. |
|
||||||||
а 1*.! |
Одной из |
основных |
техноло |
||||||||
г и § |
гических характеристик резин яв- |
||||||||||
* £ | |
ляется так называемое плато вул- |
||||||||||
5 ®| |
канизации. Если |
построить зави |
|||||||||
сь I'X |
симость какой-либо механической |
||||||||||
а> |
|
характеристики |
резины, |
|
напри- |
||||||
ю' Цё |
мер прочности при разрыве сгр, от |
||||||||||
а “ ? |
времени выдержки т при темпе- |
||||||||||
а |
|
ратуре вулканизации, то получим |
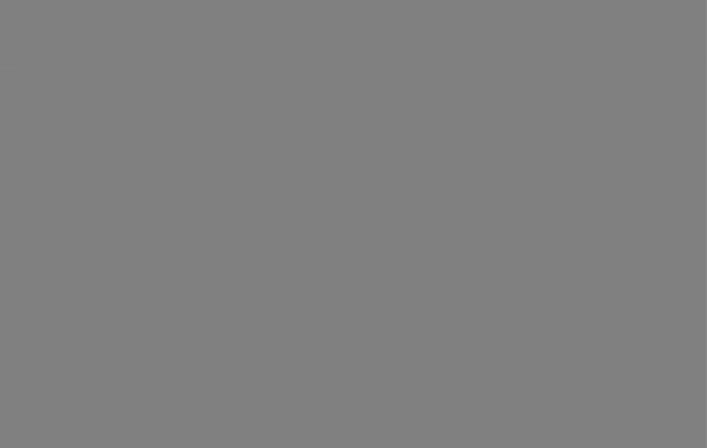
характерный |
ход этой зависимости (рис. 6.11). По мере |
||||
протекания |
процесса вулканизации |
(участок |
до точки |
||
А) |
наблюдается увеличение |
механической |
прочности, |
||
что |
связано |
с образованием |
сшитой |
структуры. Затем |
в течение некоторого времени свойства резины сущест венно не меняются, что указывает на то, что процесс вулканизации в основном завершен. При дальнейшей выдержке при температуре вулканизации наблюдается ухудшение механических показателей (участок после
л6? А |
В |
|
л |
Рис. 6.11. Характерная зависи мость прочности при растяжении резиновых смесей от времени вы держки при температуре вулкани зации.
точки ь). Это происходит из-за явления перевулканизации, выражающейся в деструкции материала под дейст вием высоких температур. Участок АБ называют п л а т о в у л к а н и з а ц и и . У разных видов резин приведенная выше зависимость имеет различный вид; различно так же плато вулканизации. Чем меньше время, соответст вующее точке А, тем быстрее наступает вулканизация, тем производительнее технологический процесс. Чем ши ре участок АБ, тем менее вероятно, что резина будет перевулканизована. Опасность перевулканизации связа на с тем, что при нагревании слоя изоляции в вулкани зационной камере наружные слои практически мгновен но приобретают температуру пара (около 200°С), а внут ренние слои прогреваются значительно дольше. Указан ное различие в нагреве особенно проявляется при вул канизации изоляции или оболочки большой радиальной толщины. Поэтому плато вулканизации должно быть та ким, чтобы за время, необходимое для полной вулкани зации внутренних слоев, наружные слои не успели перевулканизоваться.
В табл. 6.12 приведены некоторые марки резин, при меняемых для переработки на ЛКНВ, а также данные, характеризующие процесс их вулканизации.
На ЛКНВ практически могут перерабатываться ре зины, которые вулканизуются при 143°С за время, не превышающее 10—30 мин (или за 20—40 с при 200°С). При раздельной технологии наложения слоя резины и вулканизации могут использоваться резины со време-
270
|
|
|
|
Т а б л и ц а 6.12 |
|
Параметры, характеризующие плато |
вулканизации |
|
|||
некоторых типов резины |
|
|
|
|
|
|
|
Темпера |
Оптималь |
Макси |
Темпера |
|
Марка рези |
мально |
турный |
||
Тип резины |
тура вулка |
ное время |
допусти |
коэффицр- |
|
новой смеси |
низации, |
вулканиза |
мое время |
ииент ско |
|
|
|
°С |
ции, с |
вулканиза |
рости вулка |
|
|
|
|
ции, мин |
низации |
Изоляционные: |
ТСШ-35А |
|
|
50 |
2 |
РТИ-1 |
173 |
60 |
|||
VPTH-2 |
ТСШ-30А |
173 |
90 |
50 |
2 |
Шланговые: |
|
|
90 |
120 |
2 |
РШ-1 |
ШВП-50 |
173 |
|||
РШ-2 |
ШБМ-40А |
173 |
1 0 |
120 |
2 |
РШН-1 |
ШН-50 |
173 |
90 |
200 |
2 |
РШН-2 |
ШН-40 |
173 |
90 |
200 |
2 |
нем вулканизации при 143°С (обычная температура в вулканизационном котле при давлении пара 0,3 МПа) до 2 ч.
Использование ЛКНВ основывается на свойстве ре зиновых смесей существенно быстрее вулканизоваться при увеличении температуры вулканизации. Установле но, что скорость протекания процесса вулканизации ра стет значительно быстрее, чем происходит рост темпе ратуры. Если для вулканизации резины определенной марки при температуре t\ требуется время ть то для по лучения той же степени вулканизации этой резины при температуре /2 необходимо время т2, которое определя ется из следующего соотношения:
(6.5)
где К — температурный коэффициент скорости вулкани зации, для разных резин лежащий в пределах 1,5—2.
Из выражения (6.5) видно, что при /С=2 повышение температуры на 10°С ведет к уменьшению времени, не обходимого для вулканизации, в 2 раза. Процесс вулка низации начинает происходить в резиновой смеси при температуре, превышающей 120—130°С. Для более бы строй вулканизации в соответствии с (6.5) требуется повышать температуру среды, в которой происходит вулканизация.
В качестве теплонйсящей среды для проведения вул канизации резин при производстве кабелей и проводов применяется насыщенный водяной пар. Применение его имеет ряд преимуществ по сравнению с другими тепло носителями: простота получения и удобство транспор тировки, большое теплосодержание, технологическая чи
стота, |
наличие |
однозначной связи |
между |
значениями |
|||||||||
давления и температуры |
(рис. 6.12), что .позволяет срав |
||||||||||||
|
|
|
|
|
|
|
нительно |
легкими |
способами |
||||
|
|
Давление пара, МПа |
|
контролировать |
и |
поддержи |
|||||||
|
|
0,3 |
0,4 |
О,В0,в1,01,21,41,8 |
вать |
(измеряя и изменяя |
дав |
||||||
|
во |
~г~т т “ |
Г " Т " ~т ~ I |
1 |
|||||||||
|
|
|
|
|
Щ |
ление) заданную |
температуру |
||||||
|
1 |
|
|
|
|
||||||||
% 1 |
|
|
|
|
вулканизации. |
Повышенное |
|||||||
|
|
|
|
|
|||||||||
i |
20 |
|
|
|
|
|
давление |
пара в вулканизаци |
|||||
|
|
|
|
|
онной камере способствует по |
||||||||
§ |
Ю |
|
|
|
|
|
вышению |
качества |
изоляции, |
||||
§ |
|
|
|
|
|
препятствуя |
образованию |
||||||
i |
|
|
|
|
|
||||||||
I |
* |
|
|
|
|
|
вздутий и пористости, которые |
||||||
1 |
4 |
|
|
|
|
|
могут |
произойти |
в |
процессе |
|||
I |
2 |
|
|
|
|
|
вулканизации и последующего |
||||||
|
|
|
|
|
охлаждения. Давление пара в |
||||||||
I |
'-5 |
|
|
|
|
|
|||||||
t |
>0 |
Г |
|
|
|
|
вулканизационной |
|
камере |
||||
^0,75 |
|
|
|
|
|
ЛКНВ различно |
для |
разных |
|||||
|
0,S\/ |
|
|
|
|
|
|||||||
|
|
|
|
|
|
резиновых |
смесей |
и |
зависит |
||||
|
130 |
150 |
ПО |
130 |
°с |
||||||||
Рис. 6.12. Зависимость ско |
главным образом от вида кау |
||||||||||||
чука, |
входящего |
в состав |
сме |
||||||||||
рости вулканизации |
резино |
си. Для резиновых смесей, со |
|||||||||||
вых изоляций и оболочки от |
|||||||||||||
температуры |
|
насыщенного |
держащих |
натуральный, |
изо- |
||||||||
пара. |
|
|
|
|
|
преновый |
или бутиловый |
кау |
|||||
|
|
|
|
|
|
|
чук, давление пара |
составляет |
1,5—1,6 МПа, что соответствует 200—203°С, для резино вых смесей на основе бутадиеновых, бутадиен-стироль- ных И бутадиен-нитрильных каучуков — 1,9—2,0 МПа (211—213°С), для резин на основе полихлоропренового каучука (наирита) давление в зависимости от марки резины равно: 1,7—1,8 МПа (206—209°С) для ШН-40, 1,2—1,3 МПа (191—194°С) для ШН-50.
Длина вулканизационных камер ЛКНВ достигает 100 м. На таком большом участке за счет естественно го прогиба изолируемой жилы на поверхности изоляции (или оболочки) могут возникать поверхностные повреж дения за счет трения о стенки камеры. Чем больше мас са единицы длины кабеля или провода, тем вероятнее образование таких дефектов. Поэтому на ЛКНВ, имею-
272
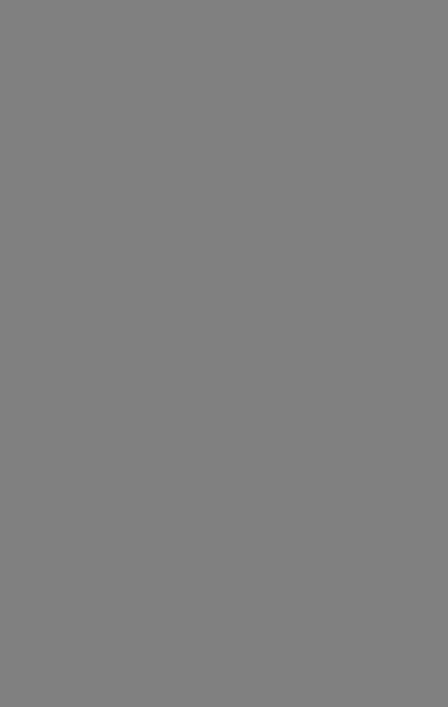
кать за время, соотЁётствуюЩёе плам вулканизации. Чем длиннее вулканизационная камера, тем большую скорость прохождения жилы через нее можно допустить при обеспечении нужной степени вулканизации.
В состав ЛКНВ обычно входят: отдающее устройст во; горизонтальный накопитель для непрерывной рабо ты линии при переходе с одной заготовки на другую; тормозное устройство; устройства для подогрева, полуотжига и отжига токопроводящей жилы сечением до 50 мм2; экструдер; заправочная камера; вулканизацион ная камера с концевым затвором и камера концевого затвора, обеспечивающая давление пара, равное давле нию воды, или вулканизационная камера с паровым затвором; охлаждающая камера с концевым затвором; насосная станция; ванна открытого охлаждения; обду вочное устройство; тяговое устройство; талькирующее устройство; компенсатор приемного устройства; прием ное устройство.
Основными элементами ЛКНВ, определяющими ее производительность, являются экструдер и вулканиза ционная камера. От параметров экструдера зависит скорость наложения изоляции или оболочки, а от дли ны вулканизационной камеры и температуры в ней за висит скорость процесса вулканизации, что в конечном
итоге определяет |
производительность процесса. |
|||||
Э к с т р у д е р ы |
для наложения резиновой |
изоляции |
||||
или |
оболочки по |
конструкции |
похожи на |
экструдеры |
||
для |
переработки |
пластмасс. |
О |
некоторых |
отличиях в |
|
их параметрах говорилось выше |
(см. § 5.4). |
Отметим |
также, что наиболее распространены в экструдерах для переработки резин двухзаходные червяки (для больших экструдеров могут применяться четырехзаходные). Чер вяки выполняют полыми, в них вставляются со сторо ны хвостовой части трубки, по которым подается вода для охлаждения.
Наиболее часто применяются в экструдерах ЛКНВ прямоугольные головки (см. рис. 5.20,а). Внутренние полости в головке имеют возможно меньший объем и плавные переходы. Это необходимо для предотвраще ния задержки потока резиновой смеси и ее перегрева и преждевременной вулканизации. Перед матрицей в го ловке помещают специальное кольцо, имеющее разные отверстия для прохода резиновой смеси. Так как поток в прямоугольной головке, переходя из цилиндра в мат
рицу, испытывает поворот на 90°, то необходимо выров нять давление в матрице, которое может быть неравно мерным из-за прохождения разными частями потока разных по длине путей при повороте. Выравнивание давления достигается тем, что меньшие отверстия в кольце (т. е. большее сопротивление потоку) распола гаются на пути тех участков потока смеси, которые про ходят меньший путь. Этим обеспечивается лучшая кон центричность накладываемого слоя резины. Устройство головки в экструдерах ЛКНВ таково, что имеется воз-
Рис. 6.14. Входной затвор АНВ (заправочная камера).
/ — подвижная телескопическая труба; 2 — цилиндр заправочной камеры; 3 — штурвал запирающего механизма; 4 — маховичок с шестеренкой; 5 —зубчатая рейка; б — вулканизационная камера; 7 — паровая рубашка.
можность смещать относительно друг друга дорн и матрицу в ллоскости, перпендикулярной их осям. Для этого служат специальные регулировочные болты. Это дает возможность регулировать концентричность накла дываемого слоя резиновой смеси.
З а п р а в о ч н а я к а м е р а (рис. 6.14) служит для герметичного соединения головки экструдера с вулка низационной камерой. Она представляет собой цилиндр, внутри которого расположена выдвижная телескопиче ская труба. С одной стороны труба может плотно соеди няться с головкой экструдера, а с другой — в месте вхо
да в цилиндр — имеется |
специальное уплотнение. На |
||
личие такой |
подвижной |
трубы позволяет |
с помощью |
специального |
устройства |
(зубчатая рейка |
со штурва |
лом) открывать заправочную камеру при неработающем экструдере и осуществлять заправку ЛКНВ.
В у л к а н и з а ц и о н н а я к а м е р а представляет со бой длинную трубу, состоящую из нескольких звеньев— высокопрочных стальных труб диаметром 75—250 мм. Одним концом вулканизационная камера соединяется с заправочной камерой, другим через паровой (промежу точный) затвор — с охлаждающей камерой. К входу
вулканизационной камеры подводится труба с подавае мым насыщенным паром для нагрева слоя резины и его вулканизации, на выходе камеры имеется отводная труба для удаления воды (конденсата), образовавшейся при отдаче тепла паром изоляции или оболочке. Коэф фициент теплоотдачи от насыщенного пара к изоляции примерно в 1,5 раза выше, чем от горячей воды. Поэто му необходимо удалять из камеры образующийся кон денсат. Для этой цели камера имеет уклон (0,3—0,5 см на 1 м длины) для стока конденсата.
Для лучшей теплоизоляции вулканизационной каме ры, предотвращающей увеличение расхода пара и сни жение скорости вулканизации из-за уменьшения тем пературы, используются паровые рубашки или индук ционный обогрев трубы. Паровая рубашка образуется за счёт размещения поверх вулканизационной камеры теплоизолированных труб большего диаметра. В про межуток между этими трубами подается -пар обычно того же давления, что и в вулканизационную камеру. При индукционном нагреве на вулканизационную тру бу накладывается теплоизоляция и обмотка из провода с нагревостойкой изоляцией. Обмотка разбита по дли не трубы на несколько секций, подключенных к сети са мостоятельно. По обмотке пропускается переменный ток, создающий в толще трубы переменное магнитное поле. За счет потерь на вихревые токи и перемагничивание стальная труба нагревается. Температура нагрева контролируется и регулируется автоматически путем отключения или подключения данной секции к сети при отклонении температуры от заданного значения.
Так как при нагреве вулканизационная камера зна чительно удлиняется, то она неподвижно прикреплена
лишь с одной |
стороны — к станине заправочной каме |
|||
ры. На остальных опорах камера |
лежит свободно |
на |
||
катках. |
з а т в о р |
(рис. 6.15) |
обеспечивает, с |
од |
П а р о в о й |
||||
ной стороны, |
свободное |
прохождение изолированного |
провода или жилы кабеля из вулканизационной каме ры в охлаждающую, с другой — предотвращает выход из вулканизационной камеры пара, находящегося под высоким давлением. Это осуществляется путем примене ния ряда резиновых и стальных эластичных прокладок, имеющих отверстия для прохождения кабеля или прово да. При закрывании затвора нажимным устройством
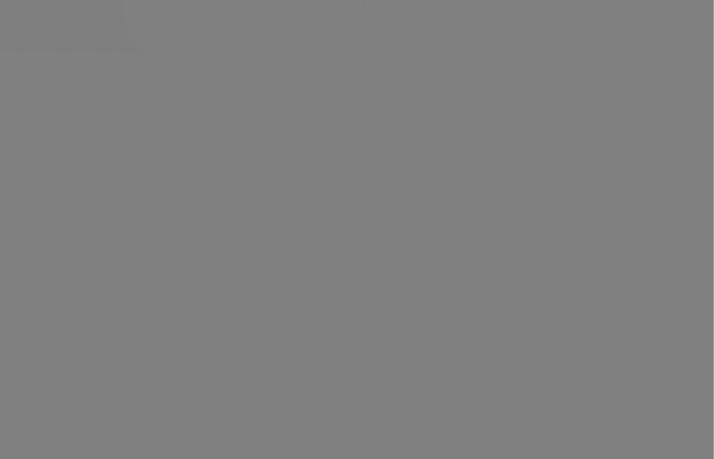
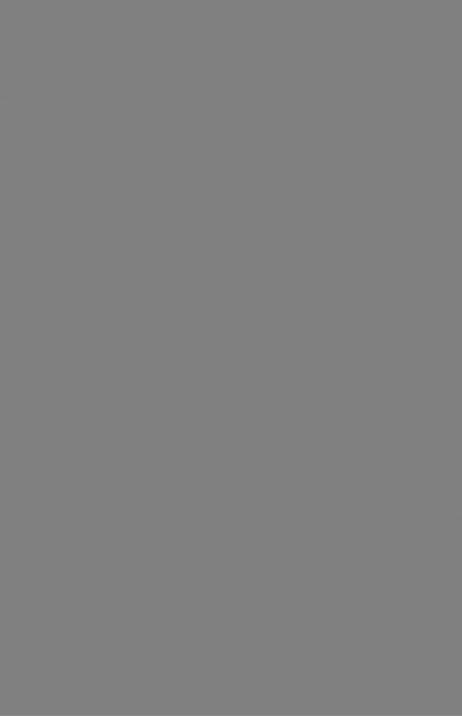
В некоторых случаях в ЛКНВ применяются охлаж дающие устройства с холодной водой, находящейся под тем же давлением, что и пар в вулканизационной ка мере. В конце охлаждающей камеры размещен конце вой водяной затвор, устройство которого сходно с паро вым затвором.
В ряде ЛКНВ для дополнительного охлаждения име ется открытый желоб с проточной водой. При наложе нии резиновой изоляции для удаления остатков воды с поверхности применяют обдувочное устройство. В нем
струя воздуха давлением до |
0,4 МПа направлена на |
встречу изолированной жиле. |
ЛКНВ должно обеспечи |
Т я г о в о е у с т р о й с т в о |
вать большие усилия для протягивания кабеля или про вода через все узлы линии. Тяговые устройства бывают колесного и гусеничного типов. Для увеличения силы трения между поверхностями тягового колеса и изоли рованной жилы или оболочки и для уменьшения возмож ности проскальзывания применяют не одно, а два коле са, причем изолированная жила огибает их несколько раз. Применяются также колеса с трапециевидным же лобом, в который уложен провод или кабель для увели чения поверхности трения, и с клиновидным по форме желоба ремнем, прижимающим их к желобу. Для ка белей большого диаметра применяются тяговые меха
низмы гусеничного типа |
(см. § 1.6). |
||
Н а т я ж н о й |
м е х а н и з м |
устанавливается перед |
|
экструдером и |
служит |
для |
поддержания постоянного |
натяжения кабеля или провода в вулканизационной ка мере. Это натяжение должно поддерживаться постоян ным и согласованным с натяжением тягового механиз ма. Натяжные механизмы также бывают колесного и гусеничного типов.
О т д а ю щ е е и п р и е м н о е у с т р о й с т в а должны обеспечивать непрерывную работу ЛКНВ без остановок на заправку и съем продукции, а также равномерность схода заготовки с отдающего устройства и приема ка беля или провода на приемное устройство. Токопрово дящие жилы поступают на ЛКНВ в бухтах, контейне рах или на барабанах. Заготовки для наложения оболо чек поступают на барабанах. Бухты или контейнеры устанавливаются вблизи экструдера, конец жилы одно го контейнера или бухты заранее сваривается с началом жилы другого контейнера. Жилы, поступающие на ме-
•’галлййескйх барабанах, устанавливаются в сдвйённоё безынерционное отдающее устройство. Применяются также сдвоенные отдающие устройства с устройством для торможения барабанов. Приемные'устройства вы полняются сдвоенными, причем процесс намотки, пере вода изолированной жилы с заполненного на свободный барабан и разрезка жилы осуществляются обычно ав томатически.
В зависимости от типа ЛКНВ те или иные перечис ленные элементы могут не входить в состав линии. На пример, тормозное устройство применяется на таких ли ниях с экструдерами большого диаметра червяка, как ЛКНВ-160, ЛКНВ-200 и ЛКНВ-250.
Перечень и основные характеристики ЛКНВ даны в табл. 6.13. Формующий инструмент (дорн, матрица) для экструдеров ЛКНВ изготавливается из материалов с
Рис. 6.17. Формующий ин струмент для наложения ре зиновой изоляции и оболоч ки на ЛКНВ.
а —дорн; б — матрица.
термообработанной поверхностью при нормированных твердости и параметре шероховатости. Дорны для изо лирования токопроводящих жил сечением до 2,5 мм2 изготавливаются с твердосплавными вставками. Выбор формующего инструмента для экструдеров ЛКНВ про изводится в соответствии с рис. 6.17 и табл. 6.14 и 6.15.
Температурные режимы работы экструдеров при на ложении изоляции или оболочки из резин разных типов приведены в табл. 6.16. Рабочие давления, а следова тельно, и температуры насыщенного пара, в среде кото рого производится в вулканизационной камере вулкани зация резиновой изоляции или оболочек, приведены в табл. 6.17.
Режимы технологического процесса наложения рези новой изоляции на жилы приведены в табл. 6,18, а ре зиновой оболочки— в табл. 6.19.
Во время работы ЛКНВ осуществляется контроль температуры цилиндра и головки экструдера, давления
280
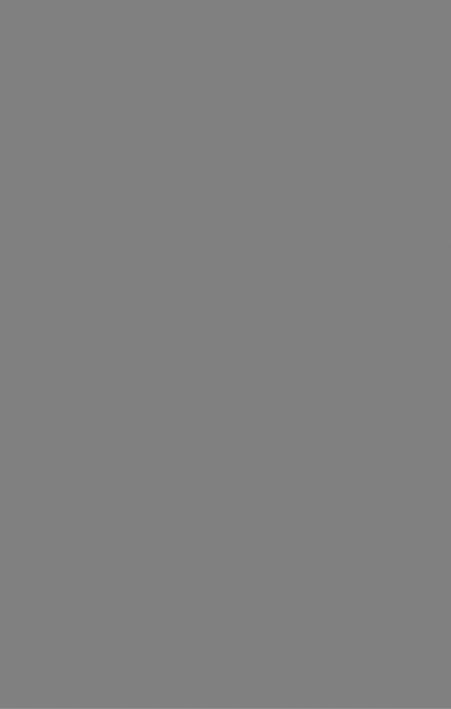
Характеристика дорна для наложения резиновой изоляции и оболочки (рис. 6.17, а )
Диаметр жилы |
|
Диаметр отвер |
Длина цилинд |
Наружный диа |
|
Угол конуса |
метр торцевой |
||||
или заготовки d, |
дорна а |
стия дорна d , |
рической части |
части дорна |
|
мм |
|
|
мм |
дорна /, мм |
£>д, мм |
|
|
Н алож ение изоляции |
|
||
До |
2 |
55—60° |
1,09с? |
4—6 |
1.3ЙД |
2—4 |
55—60 |
1,08с? |
4—6 |
|
|
4—6 |
50—60 |
1,0 8 d |
4—6 |
1,25d & |
|
6— 10 |
50—60 |
1,07d |
5—8 |
1,2 0da |
|
10— 14 |
45—55 |
1,05d |
6—9 |
1.14d A |
|
14—20 |
45—55 |
1,05с/ |
7— 10 |
1 , КИд |
|
20 и выше |
35—50 |
\ %Ш |
9— 12 |
1,06с?д |
|
|
|
Н алож ение ~оболочки |
|
||
До |
8 |
5 0 -6 0 |
l,06d |
4— 6 |
1, 13 d a |
8— 10 |
50—60 |
l,05d |
5—8 |
1 ,12 d R |
|
10— 15 |
45—55 |
1,04с? |
6—9 |
1 , Ш д |
|
15—20 |
40—55 |
1,035с? |
7— 10 |
1 ,10da |
|
20—30 |
35—50 |
1,03с? |
7— 10 |
1,0 7 d a |
|
30 и выше |
30—40 |
1,025с? |
9— 12 |
1,05йд |
Т а б л и ц а 6.15
Характеристика матрицы для наложения резиновой изоляции и оболочки (рис. 6.17, б )
Диаметр изделия |
Угол конуса |
Диаметр отвер |
Длина формую |
Глубина |
|
по изоляции или |
стия матрицы |
щей части |
|||
матрицы 0 |
матрицы /, |
фаски 5, мм |
|||
оболочке ^из, мм |
D , мм |
||||
|
|
|
мм, не менее |
|
|
|
Н алож ение изоляции |
|
|||
До 7 |
65—75° |
0 ,99с?из |
3—4 |
0,25DM |
|
8— 19 |
70—85 |
0 ,99^/дз |
5—6 |
0,12DM |
|
20 и выше |
75—90 |
0,99с?яз |
6—7 |
0,07 Z?M |
|
|
IIалож ение оболочки |
|
|||
До 15 |
70—85 |
0,99d0c |
3—4 |
0 . 127?м |
|
16—29 |
70—90 |
0,99rfo6 |
5—6 |
0,07Z)M |
|
30 и выше |
75—90 |
P,99rfp6 |
6 - 7 |
0,04DM |
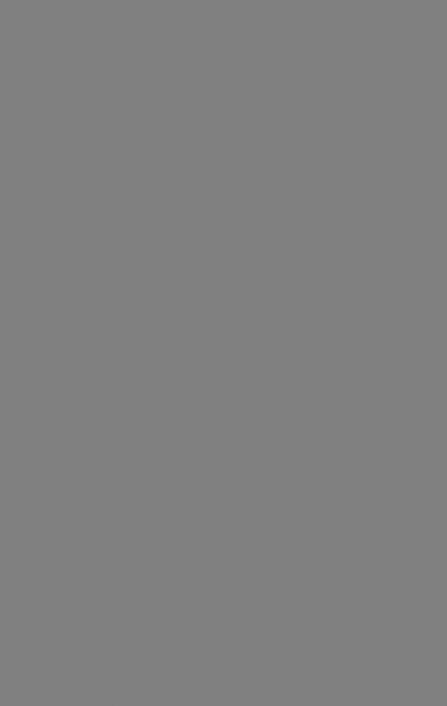
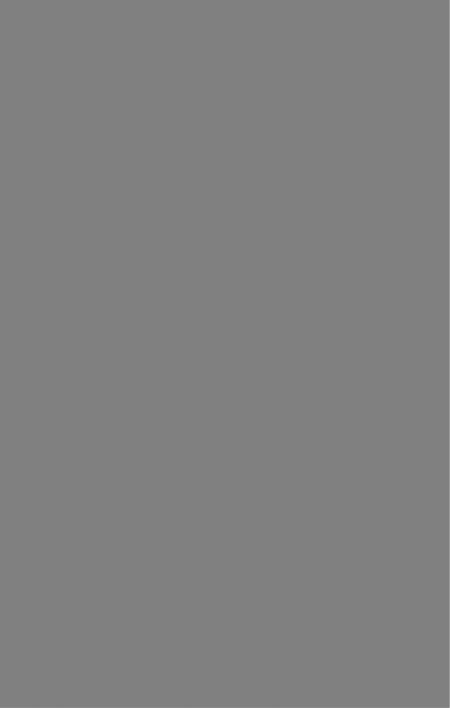
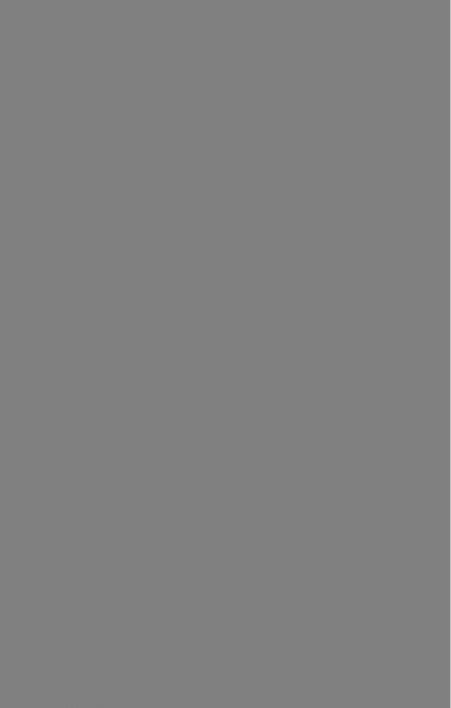