
2164
.pdf
О
Основная окружность
ra2
r2
|
|
rb2 |
|
|
|
n |
5 A |
4 |
|
|
|
5′ |
4′ |
|
3 |
|
|
|
|
|
2 |
||
|
|
|
3 |
|
|
|
|
|
|
a |
|
t |
|
|
|
|
|
|
|
|
|
1′ |
ra1
r1
rf2
101˚
2˚
W 3˚ |
|
t |
|||
4˚ |
|
|
|||
5˚ |
|
b |
|
|
|
|
|
|
|
αW |
|
|
|
|
|
B |
|
|
|
|
|
|
|
|
|
|
|
|
n |
|
Производящая |
|
|
||
|
прямая rb1 |
|
W |
||
|
|
α |
|||
|
|
|
|
|
|
|
|
|
|
|
|
O1
Рис. 4.15. Построение эвольвентного профиля зуба
К основным окружностям проводим касательную n – n, которая на межосевой линии О1О2 определит положение полюса зацепления W. Эта точка определит также и радиусы начальных окружностей rw1 и rw2, которые в данном случае равны r1 и r2 соответственно, как отрезки О1W и О2W.
Участок данной касательной АВ, т.е. расстояние между точками касания касательной с основными окружностями носит название теоретического участка линии зацепления.
Участок этой же касательной, ограниченный точками ав, которые получаются как пересечение касательной с окружностями выступов колес, называется рабочим участком линии зацепления. Этот
110

участок есть геометрическое место точек касания профилей зубьев зубчатых колес в процессе их движения в проекции на неподвижную плоскость.
Далее строятся профили зубьев зубчатых колес (рис. 4.15). С этой целью на основной окружности выделяется дуга, например 05, которая делится на ряд малых интервалов 01, 12, 23, 34, 45. Через точки 0, 1, 2, 3, 4, 5 проводим касательные к основной окружности. На этих касательных откладываем отрезки, равные по величине rb·∆αi, где ∆αi – угол, определяющий положение точек 1, 2, 3, 4, 5 на основной окружности относительно межосевой линии О1О2 между этой линией и линиями 021, 022, 023, 024, 025. В результате на касательных находятся точки 1˚,2˚,3˚,4˚,5˚, соединяя которые плавной кривой, строим эвольвенту.
4.4.Косозубые зубчатые колёса
Впрямозубых передачах зубья вступают в зацепление и выходят из него, соприкасаясь по образующим цилиндра, параллельным оси колеса. Для улучшения плавности передачи, связанной с увеличением коэффициента перекрытия, или уменьшения числа зубьев колес, изготовляемых методом обкатки нормальным инструментом, все чаще применяют другие формы зуба, например винтовую.
Зубчатые колеса с параллельными осями и винтовой формой зуба известны под названием колес с косым зубом. Данные колеса обеспечивают плавность и бесшумность хода при умень-
шенном числе зубьев и увеличивают передаточное число.
Образование косых зубьев можно легко представить себе, если рассечь прямозубое колесо на равные части плоскостями, перпендикулярными к его оси. В результате получится ряд зубчатых дисков равной толщины. Если теперь все эти диски повернуть относительно друг друга на один и тот же угол, то получим форму зуба, изображенную на рис. 4.16. Будучи скрепленными между собой, такие диски составляют уже не исходное колесо, а ступенчатое, которое будет входить в зацепление с парным ему колесом не сразу всеми ступенями, а в заданной последовательности. Это приведет к увеличению дуги зацепления на величину смещения зубьев по начальной окружности, что, в свою очередь, вызывает повышение плавности работы передачи.
111

Однако если представить себе, что число мысленно выделенных дисков неограниченно увеличится, то в пределе мы получим уже не ступенчатый, а косой зуб, совпадающий с винтовой линией на прямом цилиндре, благодаря чему косозубое колесо можно уподобить многозаходному винту с резьбой, имеющей эвольвентный профиль зуба в торцевом сечении (рис.4.17).
В отличие от прямозубой передачи в косозубой различают параметры в торцевом и нормальном сечениях (рис. 4.18). Косозубые колёса нарезают теми же инструментами, что и прямозубые. Наклон получают поворотом инструмента на угол
.
Угол , образованный осью колеса и винтовой линией, постоянный, он носит название угла наклона зубьев. Два сопряженных колеса должны иметь равные
углы наклона зубьев. В плоскостях, перпендикулярных к оси колеса, зацепление происходит так же, как и в обыкновенных зубчатых колесах, но в каждый рассматриваемый момент в зацеплении участвуют различные точки профилей. Поэтому влияние погрешностей при изготовлении этих колес оказывается гораздо меньше, чем у колес с прямыми зубьями.
В колесах с косыми зубьями следует различать три шага зацепления, измеряемых по делительному цилиндру: торцевой шаг рt, получаемый в пересечении колеса плоскостью Т – Т, перпендикулярной к оси делительного цилиндра в торцевом сечении, и нормальный шаг р, получаемый пересечением колеса плоскостью N – N, нормальной к винтовой линии на делительном цилиндре ( см. рис. 4.18).
Связь между этими шагами имеет следующий вид:
|
|
Т |
|
N |
N - N |
|
|
|
|
|
Р |
|
d |
β |
|
|
|
a |
|
f |
|
d |
|
d |
|
|
|
|
β – угол наклона |
|
|
зубьев |
|
|
Т |
|
|
N |
|
Рис. 4.18. Геометрия косозубого колеса |
рt = р / cos .
112
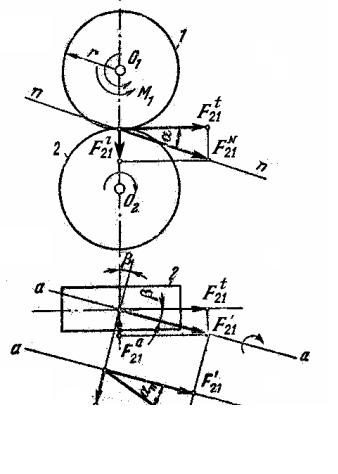
Соответственно может быть установлена и связь между модулем в торцевом mt сечении, равным mt = рt / π, и модулем в нормальном сечении, равным m = р/ π. Из этого следует
mt = m/cos .
Профиль колеса с косым зубом в нормальном сечении совпадает с профилем прямого зуба. Таким образом, в передаче с косозубыми колесами одновременно в зацеплении может находиться уже не одна или две пары зубьев. В некоторых случаях число пар зубьев, находящихся одновременно в зацеплении, может достигнуть десяти. При вращении колес линии контакта перемещаются в поле зацепления. В отличие от прямозубого косозубое зацепление не имеет зоны однопарного зацепления. В прямозубом зацеплении нагрузка с двух зубьев на один или с одного на два передается мгновенно. Это явление сопровождается ударом и шумом. В косозубых передачах зубья нагружаются постепенно по мере захода их в поле зацепления, а в зацеплении всегда находится минимум две пары. Плавность косозубого зацепления значительно понижает шум и дополнительные динамические нагрузки.
Отмеченное преимущество косозубого зацепления становится особенно значительным в быстроходных передачах, так как динамические нагрузки возрастают пропорционально квадрату скорости. Одной из причин повышения прочности косозубых передач является увеличение эквивалентного параметра(zv) с увеличением угла наклона . Поэтому косозубые колеса широко применяются не только для передач с большими скоростями, но и с большими мощностями, где zv – приведённое число зубьев.
а)
б)
в)
Рис. 4.19. Передача усилий в косозубом зацеплении
Рис. 8.9
F21r
F21a
F21t
Диаметр d делительной окружности, измеренный в торцевом сечении, равен
d = mz/cos .
Прочность зуба определяется его размерами и формой в нормальном сечении, а форму косого зуба в сечении N–N принято определять через параметры приведённого прямозубого колеса. Тогда
z = d / mcos3 = mt / mcos3 = = z / cos3 .
Рассмотрим вопрос о действии сил в зубчатой передаче. На зуб колеса 2 действует сила F21, расположенная в нормальной к зубу плоскости, содержащей прямую О1О2 (рис. 4.19) и отклоненная на угол от торцевого сечения. В этой плоскости сила F21 направлена под углом зацепления α к нормальной плоскости. Сила F21 может быть представлена как сумма трех составляющих, лежащих в трех перпендикулярных
плоскостях: силы F21t , направленной по касательной к начальным цилиндрам, силы
F21r , направленной по радиусу колеса 2, и
силы F21a , направленной параллельно оси колеса 2:
F21 F21t F21r F21a .
Из рис 4.19 следует, что сила Fr21 равна
=F21t tgα .
=F21t tgβ ,
=2М1/d1
113

где F21t – окружная сила в зацеплении; F21r – радиальная сила;
F21a – осевая сила. Аналогично определяются и силы, действующие на колесо 1. Ввиду наклонного расположения зубьев появляется осевая сила Fa , действующая на опоры и направленная вдоль оси вала, которая дополнительно нагружает опоры валов, что является недостатком косозубых колес. Этот недостаток устраняется, если применять сдвоенные косозубые колёса с симметричным, относительно середины,
правым и левым наклонами зубьев. Колёса называются (рис. 4.20) шевронными. В данном случае осевые силы уравновешиваются на самом колесе. И следовательно, отпадает необходимость в установке опорных подшипников. Для большего удобства изготовления шевронное колесо делают иногда с промежуточным желобом посередине.
4.5. Методы нарезания зубчатых колёс
Чтобы удовлетворить требованиям компактности и экономии металла, направленным на снижение стоимости производства, необходимо при проектировании зубчатых колёс стремиться к уменьшению их размеров, зависящих в значительной мере от принятого числа зубьев.
4.5.1. Основные способы изготовления эвольвентных
зубчатых колес
Прежде всего, ознакомимся в общих чертах со способами нарезания зубьев на специальных зуборезных станках. Существует два способа – метод копирования и метод обкатки.
Метод копирования предусматривает нарезание зубьев инструментом, режущая кромка которого имеет очертание, в точности совпадающее с формой очертания впадины между смежными зубьями фреза
Рис. 4.21. Нарезание зубьев дисковой фрезой |
Рис. 4.22. Пальцевая фреза |
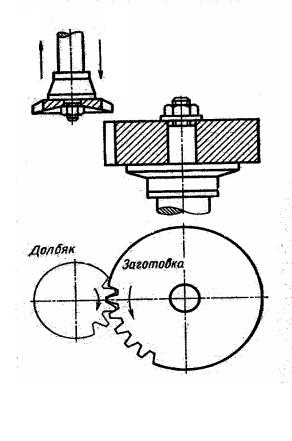
Вращаясь вокруг своей оси, фреза перемещается вдоль образующей цилиндра заготовки и вырезает впадину между зубьями, т.е. обрабатывает эвольвентные поверхности двух смежных зубьев – правую для одного и левую для другого зуба.
Завершив прорезь одной впадины, фреза возвращается в исходное положение, а нарезаемое колесо поворачивается делительной головкой станка на угол = 2 /z, после чего начинается прорезь следующей впадины. Так продолжается до завершения процесса нарезания всех зубьев на поверхности заготовки. Чтобы осуществить правильное зацепление эвольвентных профилей, необходимо изготовить отдельный инструмент для каждой партии колёс с данным модулем m и числом зубьев z, так как с изменением данных параметров меняются радиус основной окружности и кривизна эвольвенты. В этом заключается один из недостатков метода копирования. Однако, принимая во внимание, что в ряде случаев небольшие погрешности в эволь-вентном зацеплении не играют существенной роли, на практике пользуются набором из 8…15 дисковых фрез для нарезания колёс данного модуля и угла зацепления с разным числом зубьев. При этом мирятся с тем, что каждая фреза набора нарезает лишь только те колёса, у которых эвольвента такая же, как у фрезы. Все остальные зубчатые колёса в рассмотренных случаях нарезаются с некоторой погрешностью.
При больших модулях и индивидуальном производстве колёс применяются пальцевые фрезы (рис.
4.22). Они устанавливаются на станке таким образом, чтобы их ось вращения
совпадала с радиусом нарезаемого колеса. Иногда зубья выполняются строганием фасонными резцами. Второй, более совершенный способ предусматривает
нарезание зубьев методом обкатки. Режущим инструментом в этом случае является зубчатое колесо (долбяк), называемое инструментальным (рис. 4.23), зубчатая рейка или червячная фреза. Обрабатываемой заготовке и режущему инструменту любой формы в процессе нарезания на специальном зуборезном станке сообщается такое относительное движение, которое имели бы два колеса, находящиеся в правильном зацеплении. Очевидно, в случае применения инструментального колеса начальные окружности его и нарезаемой заготовки катятся одна по другой без скольжения. Если в качестве режущего инструмента используется зубчатая рейка, делительная окружность заготовки колеса в
115

относительном движении катится без скольжения по начальной прямой этой рейки.
Долбяк и заготовка при обработке зубьев непрерывно вращаются с постоянным отношением угловых скоростей, как будто находятся в зацеплении. Ввиду этого профиль зуба получается как огибающая различных относительных положений режущей кромки инструмента, который как бы обкатывает нарезаемое колесо.
Особенность этого способа заключается в том, что он позволяет нарезать по методу обкатки и колеса с внутренним зацеплением.
На рис. 4.24 изображена инструментальная рейка, при помощи которой производится нарезание зубчатых колес. Толщина зуба рейки по средней прямой С – С равна ширине впадины. Угол стандартных реек a=200. Часть зуба рейки, расположенная вне средней прямой С – С, называется его головкой, остальная ножкой. Высота головки и ножки зуба у инструментальной рейки одинакова. Причем коэффициент высоты ha* принимается равным единице для нормального зуба и 0,8 для укороченного. Помимо профилирующей части зуба, очерченной прямой линией, головка и ножка зуба имеют закругленные части, служащие для образования радиального зазора между
головкой и ножкой зуба введенных в зацепление нарезаемых зубчатых колес.
Шаг по делительной окружности нарезаемого колеса равен шагу рейки, толщина зуба – ширине впадины рейки по делительной прямой, а ширина впадины колеса – толщине зуба рейки.
Инструментальная рейка имеет 5…10 зубьев и поэтому за полное перемещение от одного до другого края может нарезать также только 5…10 зубьев. При нарезании большего числа зубьев инструментальную рейку приходится переставлять обратно, что связано с потерей времени. Поэтому производительность зуборезных станков, работающих инструментальной рейкой, ниже, чем производительность станков, работающих зубчатым долбяком.
Еще более производительным при нарезании колес с внешним зубчатым венцом считается зубофрезерование с помощью червячных фрез. Однако и в этом случае нормальное сечение червячной фрезы повторяет геометрию инструментальной рейки.
4.5.2. Нарезание зубчатых колес со смещением инструментальной рейки
Реечное станочное зацепление инструментальной рейки и заготовки изготовляемого колеса, как и всякое зацепление, имеет начальные линии. Напомним, что начальные линии катятся друг по другу без скольжения. В реечном станочном зацеплении изготавливаемого колеса равен радиусу его инструментальной рейки может не совпадать с ее средней говорят о том, что станочное зацепление настроено относительно делительной окружности изготавливаемого
Такое смещение может быть:
–нулевое, когда средняя линия С – С касается
–положительное, когда средняя линия отодвинута
–отрицательное, когда средняя линия пересекается
116

Смещение инструмента выражают в виде произведения модуля m на коэффициент смещения х и ему присваивают знак.
При нулевой установке смещения m x = 0, x = 0; при положительной m x 0, x 0; при отрицательной m x 0, x 0.
Смещение инструмента в станочном зацеплении применяется с различными целями. В частности, при нарезании зубьев методом обкатки в некоторых случаях обнаруживается следующее: головки зубьев режущего инструмента удаляют материал с ножек зубьев колеса в большем количестве, чем нужно, искажая тем самым профиль зубьев. В результате происходит подрезание ножек, снижающее объёмную прочность зубьев. Такое положение наблюдается в тех случаях, когда рабочий участок линии зацепления выходит за пределы теоретической линии
зацепления АВ |
(см. рис. 4.15). В результате не |
Рис. 4.25. К расчету коэффициента |
|
удовлетворяется |
требование основной теоремы |
смещения |
|
зацепления, вследствие чего профили, выходящие за |
|||
|
пределы теоретической линии зацепления, не будут рабочими. Значительное подрезание ослабляет ножку зуба и потому является недопустимым, небольшое
подрезание полезно для улучшения условий контакта зубьев в начале (или в конце) зацепления. Определим минимальное количество зубьев из условия неподрезания ножки.
Из треугольника АТО (рис. 4.25) имеем
0,5 mz + xm - ha*m = 0,5 zcos2α.
Отсюда коэффициент смещения инструментальной рейки x = ha*- 0,5z (1 - cos2α).
При α = 20˚и ha* = 1 x = (17 - z ) / 17.
При этом min число зубьев меньшего колеса, при котором отсутствует явление подрезания
ножек,
Zmin = 2hа* / sin2 = 2hа* / sin220˚ = 17.
Следовательно, если число зубьев обрабатываемого колеса меньше 17 (на практике допускается Zmin = 14), то при нарезании зубьев реечным инструментом с углом = 20˚ и hа* = 1 надо применять положительное смещение, определяя его значение по приведенным выше формулам.
Помимо избежания подреза зубьев за счет смещения исходного контура инструментальной рейки при проектировании зубчатых колес достигается увеличение прочности зубьев и уменьшение их износа путем соответствующего подбора очертания профилей, а также увеличение плавности работы передачи. Подробно эти вопросы рассмотрены в специальной литературе.
На практике чаще всего можно встретиться со следующими комбинациями колес, находящихся в зацеплении и образующих следующие передачи:
1)нулевая передача, когда оба колеса нарезаны без смещения или когда одно колесо положительное, а второе отрицательное при равном для обоих колес смещении, т.е. одно колесо с положительным, а второе – с равным ему по абсолютной величине отрицательным смещением (высотная коррекция);
2)положительная передача:
–нулевое колесо с положительным колесом;
–положительное колесо с отрицательным колесом (при неравных коэффициентах смещения, но при положительной сумме смещений).
Вэтих передачах делительные диаметры зубчатых колес остаются без изменения:
di = mzi.
Диаметры окружностей вершин da и впадин df зубьев будут равны
da = d + 2m (ha*+х), df = d - 2m (ha*+ c*- х).
В общем случае угол зацепления определится в соответствии с формулой
invaw inva 2(х1 х2 ) tqa, z1 z2
где aw – угол зацепления передачи в сборке; х1 и х2 – коэффициенты смещения колеса и шестерни; z1 и z2
– числа зубьев колеса и шестерни.
117
Межосевое расстояние будет равно
a |
w |
|
m |
(z |
1 |
z |
2 |
) |
cos a |
. |
|
|
|||||||||
|
2 |
|
|
|
сos a w |
На основе последней формулы можно сделать вывод о том, что за счет изменения угла aw путем смещения инструмента достигается изменение межосевого расстояния.
118

5. ПРОСТРАНСТВЕННЫЕ ЗУБЧАТЫЕ МЕХАНИЗМЫ
5.1. Основные виды пространственных зубчатых передач
Пространственные передачи передают вращение между валами с пересекающимися осями. Наиболее общим видом пространственной передачи является гиперболоидная. По способу образования сопряженных поверхностей зубьев различают гиперболоидные передачи первого рода, в которых обе сопряженные поверхности могут быть образованы одной производящей поверхностью, и гиперболоидные передачи второго рода, в которых производящая поверхность совпадает с одной из сопряженных поверхностей.
В качестве начальных поверхностей
Рис. 5.1. Гиперболоидная передача
Рис. 5.3. Гипоидная передача |
|
колеса (рис.5.3), в которых вместо |
|
произвольно вырезанных частей гипер- |
|
болоидов применены усеченные конусы. |
|
Вследствие замены гиперболической |
|
поверхности на цилиндрическую сопря- |
|
женные профили винтовых колес |
|
касаются не по линии, а в точке. Кроме |
Рис.5.2. Винтовые зубчатые |
того, относительная скорость сколь- |
колеса |
жения профилей в винтовой паре |
|
существенно выше, чем в |
|
цилиндрической передаче. Это приводит к тому, что винтовая передача имеет низкую нагрузочную способность и применяется при малых мощностях (в танковых двигателях для привода насосов, центрифуг и сепараторов). Частным случаем винтовой передачи, когда угол между
119