
2164
.pdfВеличины γ и γs обычно определяют опытным путем по средним значениям р и Vcк, а затем по формуле (9.2) подсчитывают коэффициент износа k. Так, например, испытание образцов при средних режимах эксплуатации (рср= 16 · 105 Па, (Vск)ср = 2 м/с) показало, что за время tр = 100 ч работы средний износ составил δ = 2 мкм, следовательно, из формулы (9.1)
k/(pVск ) 2 10 2 /(16 105 2) 6,25 10 9 мкм/(ч Па м с 1).
Всправочниках приведены опытные данные по γ и γs.
Интенсивность изнашивания γs может меняться в весьма широких пределах, примерно от γs =10-12 (износ 0,001 мкм на 1 км пути трения, т.е.
очень малая величина) до γs = 10-3 (износ 1 мм на 1 м пути трения, т. е. очень большая величина).
Свойство материала оказывать сопротивление изнашиванию в определенных условиях трения, оцениваемое величиной, обратной скорости или интенсивности изнашивания, называют износостойкостью. На износостойкость влияют твердость материалов, их упругие свойства, режим работы (нагрузка, скорость, температура), внешние условия (смазка, окружающая среда), конструктивные особенности узла трения.
По величине γs различают 10 классов износостойкости материалов, которые можно разделить на 3 основные группы в зависимости от вида контактного взаимодействия поверхностей трения: 0 – V классы (γs=10- 12..10-7) – высокая износостойкость вследствие упругого деформирования); VI – VII классы (γs = 10-6...10-5) – средняя износостойкость при упругопластическом деформировании); VIII – IX классы (γs=10-4...10-3) – весьма низкая износостойкость при микрорезании).
Так, например, по опытным данным для шатунных шеек стальных коленчатых валов двигателей автомобилей γs = 5 · 10-12...4 · 10-11 (весьма высокая износостойкость при упругом контакте), а для зуба ковша экскаватора (сталь 45) γs = 10-4 ...10-3 (весьма низкая износостойкость при микрорезании).
В последнее время большое внимание уделяют материалам деталей машин, механизмов и приборов, предназначенных для работы в узлах трения без специальной смазочной среды: материалы на основе полимеров (подшипники, зубчатые колеса, кулачки и др.), углеграфитные материалы (уплотнительные элементы, вкладыши гидронасосов, детали узлов трения в авиационной и химической промышленности), металлокерамические материалы (детали узлов трения, работающие при высоких температурах) и др.
Для повышения износостойкости трущихся поверхностей новых деталей наряду с гальваническими покрытиями широко применяют их
220
термическую обработку: поверхностную закалку с нагревом газовым пламенем (для поверхностного упрочнения стальных зубчатых колес, червяков, шеек коленчатых валов и пр.), высокочастотную закалку (кулачковые валы, шестерни, шейки валов, гильзы цилиндров, станины станков и др.). С этой же целью применяют обработку поверхностным пластическим деформированием, в процессе которого повышается твердость поверхностных слоев и достигается нужный класс шероховатости поверхности (обкатывание и раскатывание цилиндрических и плоских поверхностей, прошивание, калибрование и др.).
Принимаются во внимание и соображения замены деталей при ремонте машины: ремонт упрощается и удешевляется, если изношенная деталь простая и легко заменимая (например, втулка или вкладыш).
Иногда оказывается более выгодным не замена, а восстановление и увеличение срока службы деталей путем наращивания изношенных поверхностей трения газовой или электродуговой наплавкой, газовой или электрической металлизацией, плазменным напылением (для нанесения тугоплавких соединений) и другими способами.
Износ в общем случае определяют по формуле
tp
k pVск dt . |
(9.5) |
0 |
|
Для удобства расчета в механизмах с одной степенью свободы формулу (9.5) целесообразно преобразовать, введя обобщенную координату φ и обобщенную скорость ω = φ. Тогда износ за один цикл работы, для которого φ= φц,
ц
ц |
k p(Vск |
/ )d , |
(9.6) |
|
0 |
|
|
где Vск/ω=Vск(φ)/ω – аналог скорости скольжения (или передаточная функция ds/dφ) в рассматриваемой точке элемента кинематической пары.
Если число циклов работы nц, то износ
цnц . |
(9.7) |
По формуле (9.7) можно найти число циклов работы по заданной величине предельного износа, что необходимо при определении ресурса работы машины.
Анализ формул (9.5), (9.6) показывает, что величина износа кроме коэффициента износа, который во многом определяется материалом трущихся поверхностей, качеством их обработки, смазкой и т.д., зависит от удельного давления и передаточной функции механизма (Vск/ ).
221
Удельное давление в отдельных кинематических парах также связано с установлением нагружения механизма, его динамикой и распределением усилий по кинематическим парам, которое опять же связано со структурой и геометрией этого механизма. Решению вопросов расчета и уменьшения износа в кинематических соединениях посвящена большая техническая литература, выходящая за рамки данного учебника. Поэтому далее коснемся только отдельных общих вопросов, связанных с данной областью знаний.
9.2. Некоторые сведения о выборе материалов для трущихся элементов кинематических соединений
Трущиеся детали, в зависимости от их назначения, изготавливают из конструкционных, фрикционных, износостойких и антифрикционных материалов широкой номенклатуры. Во многих случаях материалы наносят в виде покрытия, пленок или накладок на основной композиционный материал. В ряде случаев трущиеся детали изготавливают из сталей и других сплавов специального назначения, окислов металлов, металлокерамических и неметаллических материалов.
Из конструкционных сталей выпускают детали, которые должны удовлетворять условиям высокой прочности, жесткости или податливости и иметь на тех или иных участках поверхности трения. Это детали типа валов, пальцев, зубчатых колес, роликов кулачковых механизмов и т.д. Из стали, а также чугуна изготавливают силовые цилиндры, плунжеры, ползуны и поршневые кольца, направляющие станков и ползуны.
Фрикционные материалы – это такие, которые в контакте с металлической поверхностью имеют высокий коэффициент трения. Применяются в тормозах и фрикционных муфтах, разделяются на органические, металлические, асбестокаучуковые, пластмассовые, металлокерамические на различных основах.
Износостойкими называют материалы, которые при трении даже в тяжелых условиях нагружения сравнительно мало изнашиваются. В качестве износостойких материалов используют конструкционные стали, упроченные по всему объему или рабочим поверхностям деталей, специальные стали, чугуны, порошковые материалы, резину, пластмассу и др.
Из всех пар трения подшипники скольжения вызывали в свое время наибольшую трудность в обеспечении их длительной нормальной работы в силу высоких удельных давлений при сравнительно больших скоростях скольжения. Для таких подшипников были разработаны сплавы с малым коэффициентом трения, получившие название антифрикционных (разумеется, при работе со стальным валом).
222
В дальнейшем любой подшипниковый материал с твердостью, меньшей твердости сопряженной детали, стали называть антифрикционным.
Понятие «антифрикционность» включает в себя комплекс свойств, которым должен удовлетворять подшипниковый материал: достаточную статическую и динамическую прочность при повышенных температурах; способность образовывать прочный граничный слой смазочного материала и быстро восстанавливать его в местах, где он разрушен; низкий коэффициент трения при несовершенной смазке; отсутствие заедания на валу в случае перерыва подачи смазочного материала; высокие теплопроводимость, теплоемкость, прирабатываемость; хорошую износостойкость сопряжения; недефицитность и высокую технологичность и др.
Все пары трения, как правило, должны обладать антифрикционностью, под которой следует понимать комплекс свойств, которым должно удовлетворять сочетание трех тел: материалов пары трения и применяемого смазочного материала. Последний является таким же конструктивным фактором, как и материал детали. Заметим, что износостойкость является требованием, общим для всех материалов, в том числе и фрикционных, за исключением приработочных покрытий.
Подходя к антифрикционности с общих позиций, в парах трения трудно отделить антифрикционный материал от износостойкости. Например, пара «поршневое кольцо–цилиндр» должна быть износостойкой, иметь малый коэффициент трения и хорошо прирабатываться, а кольцо должно иметь еще и высокую упругость. При подборе материала кольца по показателю высокой износостойкости пары всегда неявно имеют в виду и антифрикционность.
При подборе материалов для многих пар трения в точке зрения их антифрикционных свойств имеется возможность большого сочетания материалов в отличие от пары трения «вал–подшипник», где возможность варьирования материала вала ограничена.
В этой связи выбор материалов представляет собой трудную задачу, так как зависит от конструкции и назначения пар трения, технологии производства, условий эксплуатации, от требований к общей прочности деталей, сроку их службы и надежности при учете стоимости материала и эксплуатационных расходов.
На выбор материалов могут оказать влияние физико-химические явления на поверхности трения, зависящие от условий работы. Специальные материалы применяются при работе соединений в условиях ударной нагрузки, возникающей при перекладке зазоров в кинематических парах механизмов.
223
Фрикционные материалы должны противостоять термической усталости: на поверхности трения не должно возникать трещин в результате многократного совместного нагружения.
Особые требования предъявляются к материалам, работающим при высоких температурах, или в условиях высокого вакуума, или в среде инертного газа. Материалы пар трения, работающих при высоких температурах, должны иметь хорошие показатели жаропрочности, теплопроводности, коррозийной стойкости и сопротивления термической усталости. В условиях высокого вакуума или среде инертного газа образование защитных пленок на поверхностях трения исключено или затруднено. В этом случае говорят о «чистом» трении.
Таким образом, подбор подходящих материалов для пар трения можно в каждом отдельном случае сделать только на основании тщательного сопоставления условий работы трущихся деталей, исходных свойств материалов и тех изменений, какие они претерпевают на поверхности трения, а также других обстоятельств. Вместе с тем существуют некоторые общие правила подбора материалов.
Сочетать твердый материал с мягким, имеющим температуру рекристаллизации ниже средней температуры поверхности трения при работе. При таком сочетании металлы хорошо противостоят заеданию и характеризуются высокой надежностью. Хорошие результаты дают пары «хром–резина» при смазывании минеральным маслом и водой и «хром– бронза» при использовании пластичных смазочных материалов.
Сочетать твердый металл с твердым (сочетание пар из азотированной, хромированной и закаленных сталей). Такие пары трения обладают высокой износостойкостью вследствие малого взаимного внедрения их поверхностей. Налипание приработочных покрытий повышает надежность пар в наиболее опасный период работы – во время приработки. Применение этих пар ограничивается скоростями скольжения. Высокая точность изготовления и сборки, значительная жесткость конструкции, тщательная приработка, улучшение условий смазывания значительно расширяют область применения пар трения из твердых материалов.
Избегать сочетания мягкого материала с мягким, а также пар из одноименных материалов (незакаленная сталь к незакаленной стали, алюминиевый сплав по алюминиевому, медный сплав по алюминиевому, хром по хрому, никель по никелю, пластмасса по пластмассе), за исключением пар из политетрафторэтилена и полиэтилена. Подобранные пары имеют низкую износостойкость и ненадежны в работе. При незначительных нагрузках в парах образуются очаги схватывания и происходит глубинное вырывание материалов с взаимным их налипанием на поверхности трения.
224
Использовать в качестве труднодоступных для смазывания конструкциях пористые, порошковые и антифрикционные сплавы.
Применять в качестве фрикционных и антифрикционных материалов пластические массы. В ряде случаев они повышают надежность и срок службы узла трения, снижают массу конструкции и расход дефицитных цветных металлов, уменьшают вибрации и улучшают акустические свойства машин.
Стремиться путем выбора материалов пары трения, смазочных материалов и присадок к ним создавать при работе пары условия режима избирательного переноса (металлическую защитную пленку на поверхности трения толщиной порядка 1–2 мкм, например, из меди).
Учитывать возможность при эксплуатации наводороживания поверхностей трения, что резко снижает износостойкость и надежность работы узла трения, т.е. так называемого водородного изнашивания – явления, открытого в начале 70-х годов прошлого века. Применять материалы, трудно поддающиеся наводороживанию.
Стальные детали узлов трения при окончательной доводке их поверхностей подвергать финишной антифрикционной безабразивной обработке.
9.3. Основные конструктивные способы повышения износостойкости элементов подвижных соединений
9.3.1. Подбор жесткости, податливости и специальной конфигурации элементов кинематических пар
Увеличение податливости одной из деталей сопряженного узла или, наоборот, повышения жесткости детали либо узла в целом может благоприятно влиять на его долговечность.
Податливость детали, общая или местная, оказывает ее рабочей поверхности следовать за деформацией сопряженной детали. Самоустанавливающийся опорный подшипник является примером конструкции, имеющей деталь свободной податливости в виде вкладыша, обладающего угловой подвижностью. Полнее роль податливости проявляется в резинометаллических вкладышах, во вкладышах из пластмасс и мягких покрытиях рабочих поверхностей.
Так, сухая резина имеет коэффициент трения выше, чем у других материалов, и в то же время в паре со сталью, бронзой и латунью при смазывании маловязкой жидкостью, как вода, имеет высокие антифрикционные свойства. Объясняется тем, что гибкая и легко деформируемая резина хорошо приспосабливается к неровностям поверхности вала без нарушения в зоне нагружения непрерывности
225
смазочного слоя. Последний благодаря этому может быть меньше толщины, чем при металлической поверхности вкладыша. Высокая способность деформации резины обусловливает более равномерное распределение давления по длине вкладыша.
Аналогично резине ведут себя мягкие покрытия вкладышей, податливость которых обусловлена малым сопротивлением пластической деформации. У пластмасс, подобно резине, в соответствии с их модулями упругости нагрузка по длине вкладыша также распределяется равномернее, чем у металлов.
Детали и узлы технологических машин должны обладать такой жесткостью, чтобы неточность размеров и формы изделия, связанная с относительными перемещениями инструмента и деталей машины под действием рабочих усилий, не выходила за пределы допуска. Повышение износостойкости требует учитывать не только общую, но и местную жесткость конструкции.
Нагрузочная способность цилиндрических и конических зубчатых передач тем выше, чем равномернее распределена нагрузка по длине зуба. Неравномерному распределению нагрузки, помимо неточности изготовления деталей передачи и их сборки, способствуют изгиб и кручение валов, деформация опор и корпусов. На рис.9.2, а и б приведена схема перекоса зубьев шестерни и колеса, возникающего вследствие упругой податливости детали передачи под нагрузкой. Если бы зубья были абсолютно жесткими, то перекос повлек бы за собой точечное касание зубьев у одного из торцов (рис.9.2, в). На самом деле зубья податливы, и если перекос невелик, то он полностью компенсируется деформацией зубьев. Суммарная деформация (рис.9.2, г) зубьев будет неодинакова по их длине, и произойдет концентрация нагрузки по ширине зубчатого колеса (рис.9.2, д). В данном случае увеличение жесткости валов, опор и корпусов является фактором благоприятным.
Опыты с гипоидными передачами, применяемыми в автомобилях, показали, что при переходе от консольной схемы к неконсольной (рис.9.3, а и б) с добавлением подшипника 3 со стороны малого основания конуса шестерни (введения местной избыточной связи) нагрузочная способность передачи возрастает в среднем на 30 % . Опоры 2 и 3 по обе стороны шестерни желательно иметь с цилиндрическими роликами: они менее податливы, чем шариковые, и позволяют уменьшить зазор.
Однако не только увеличением жесткости элементов передачи можно добиться большой равномерности распределения нагрузки вдоль зубьев. Деформация зубьев под нагрузкой способствует выравниванию давления, поэтому большая податливость зуба является положительным качеством. Повысить податливость зуба можно, увеличив его высоту, или применяя разрезные зубья.
226
Зацепление повышенной жесткости показано на рис.9.4, где 1 – колесо; 2 – шестерня; 3 – зуб колеса с пазом 4; 5 – зуб шестерни с перемычкой 6, увеличивающей жесткость. Данная конструкция имеет свою геометрию зацепления (японский патент).
Изменением обычной конфигурации зубчатых поверхностей элементов кинематических пар удается в ряде случаев улучшить работу пар трения. Например, для предупреждения концентрации нагрузки у концов прямых зубьев цилиндрических и конических колес зубьям придают (путем дополнительной обработки их боковой поверхности на специальных станках) бочкообразную форму, при которой толщина зуба уменьшается от середины шестерни к торцам. Наибольшая разница толщины составляет 0,02 – 0,04 мм. Бочкообразная форма зуба не только способствует увеличению долговечности передачи, но и уменьшает также шум во время работы.
9.3.2. Плавающие элементы кинематических соединений (введение «лишних» степеней свободы в механизм)
Вузлах трения эти детали встречаются в виде плавающих пальцев, плавающих втулок и шайб. Поясним на примере.
Сочленение поршневого пальца с шатуном производят закреплением пальца в бобышках поршня или в шатунной головке; установкой пальца с возможным поворотом как в бобышках поршня, так и в шатунной головке. Палец такой конструкции называется плавающим.
При работе механизма плавающий палец под действием сил трения со стороны шатуна проворачивается. Угловое перемещение шатуна складывается из углового перемещения относительно пальца и поворота пальца в бобышках, поэтому скорость пальца в каждом из этих перемещений примерно вдвое меньше, чем при закрепленном пальце.
Врезультате снижается скорость изнашивания пальца и вкладышей,
аизнос поверхности пальца распределяется равномерно. Кроме того, повышается надежность соединения: палец, заевший в шатуне, может качаться вместе с ним в бобышках поршня и наоборот.
Плавающие элементы в узлах машин предусматриваются для компенсации тепловых деформаций. Если подшипники закрепить жестко на валу и в корпусе, то удлинение вала при повышении температуры узла в процессе работы вызовет уменьшение осевого зазора в подшипниках и последующее защемление тел качения между кольцами, что снизит долговечность подшипников. Такая угроза устраняется применением плавающих опор.
227

9.3.3. Замена внешнего трения внутренним трением упругого элемента
Кинематические пары с жесткими звеньями для относительно небольших линейных, угловых или совместных перемещений в ряде случаев могут быть заменены неподвижными соединениями с промежуточным элементом высокой упругости, что имеет ряд преимуществ. Взаимное смещение звеньев в процессе их работы достигается за счет деформации специальной эластичной детали; при этом внешнее трение скольжения или качения заменяется внутренним трением упругого элемента из резины. Это соединение выполняется в виде резинометаллического шарнира.
Крепление резины к металлам осуществляется вулканизацией соприкасающейся с металлом резиновой смеси, склеиванием или сцеплением путем
предварительного сжатия резины при монтаже металлических поверхностей шарнира. Резина легко вулканизуется к стали, чугуну, латуни и алюминиевым сплавам. Наиболее прочно резина скрепляется с латунями определенного состава. Некоторые ингредиенты резины или клея для ее крепления могут вызвать корродирование стали и чугуна, поэтому одним из наиболее распространенных способов крепления резины является вулканизация смеси в контакте с латунированной поверхностью металлической арматуры.
По способу изготовления различают шарниры, вулканизованные в сборе, закатанные и сборные. Закатанные шарниры встречаются только в виде резинометаллических.
На рис.9.6 изображен шарнир, применяемый в подвеске автомобиля. Резиновое кольцо 3, надетое на внутреннюю втулку 1, вводится в
тонкостенную стальную трубу, которую затем раскатывают, в результате чего уменьшается диаметр трубы при некотором увеличении ее длины и создается необходимое сцепление между резиной и металлической арматурой. Края трубы после раскатки завальцовывают. Наружную втулку 2 запрессовывают в проушину листовой рессоры, внутреннюю втулку закрепляют при сборке неподвижно между стенками кронштейна рамы.
Конструкция шарнира в виде резинового башмака (рис.9.7) встречается в креплениях рессор автомобилей. Концы рессоры зажаты в таких вкладышах. Удлинение рессоры при ее прогибе компенсируется деформацией резины.
228
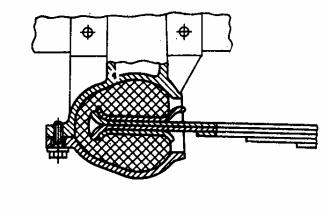
Резинометаллические втулки обладают не только радиальной, но в малых пределах также осевой и даже угловой подвижностью. Все шесть степеней подвижности имеют универсальные шарниры со сферической резиновой прокладкой.
Резинометаллические шарниры нашли применение в узлах подвески автомобилей и тракторов, в мягких карданах, в гусеницах тягачей, сочленениях вагонных и локомотивных рам с их поворотными тележками и т. п. По сравнению с обычными резинометаллические шарниры имеют следующие преимущества: отсутствует изнашивание от внешнего трения, что исключает абразивное изнашивание деталей; отпадает необходимость в смазывании и установке уплотняющих устройств; упрощается обслуживание; уменьшается масса; в узлах подвески амортизируются удары, что способствует бесшумности хода; в упругих карданах помимо смягчения ударов при резком увеличении крутящего момента происходит гашение вибраций и демпфирование крутильных колебаний. Отсутствие смазочного материала в шарнирах имеет особое значение для машин пищевой и текстильной промышленности.
9.3.4. Замена трения скольжения трением качения
Такая замена во многих случаях целесообразна для повышения долговечности деталей, надежности их работы и экономичности машин.
Подшипниковые узлы. Каждому виду опор скольжения или качения свойственны как положительные, так и отрицательные стороны.
Подшипники качения имеют следующие преимущества:
|
1. |
Малые потери на трение |
||
|
по сравнению с потерями у |
|||
|
подшипников скольжения, рабо- |
|||
|
тающих при граничной смазке или |
|||
|
даже при жидкостной смазке. |
|||
|
Применение |
подшипников каче- |
||
|
ния, как правило, повышает КПД |
|||
|
машины и силовой установки. |
|||
|
Коэффициент трения подшипника |
|||
Рис.9.7. Конструкция шарнира |
качения сравнительно мало изме- |
|||
в рессорах автомобиля |
няется |
в |
большом |
диапазоне |
|
нагрузок |
и |
окружных |
скоростей. |
Статический момент подшипника лишь на 30 – 50 % превышает момент трения при установившемся движении, в то время как в подшипниках скольжения это превышение достигает 15 раз и более. В связи с этим
229