
2164
.pdfособенно важна установка опор качения в узлах машин, работающих с частыми пусками и остановками.
2.Малый момент трения в шарикоподшипниковых узлах позволяет сужать зону нечувствительности приборов.
3.Экономия большого количества цветных металлов – меди, олова, свинца, расходуемых на изготовление вкладышей подшипников скольжения.
4.Малый расход смазочных материалов.
5.Отсутствие необходимости в принудительном охлаждении.
6.Упрощение обслуживания.
7.Исключение изнашивания шеек валов при правильно назначенных посадках.
8.Высокая степень стандартизации и комплектная поставка шарико- и роликоподшипников упрощает конструирование подшипниковых узлов и монтаж машины.
9.Снижение стоимости машин.
10.Возможность восприятия осевых нагрузок, действующих на шпиндель металлорежущего станка, преимущественно при использовании упорных подшипников качения.
Недостатки подшипников качения следующие:
1.Пониженная долговечность при высоких окружных скоростях и динамических нагрузках. Подшипники выходят из строя главным образом вследствие выкрашивания тел качения и поверхностей качения колец. Между тем подшипники скольжения при жидкостной смазке в соответствующих условиях могут работать неограниченно долго. Поэтому в машинах, предназначенных для длительной работы в режиме высоких скоростей, используют гидродинамические подшипники скольжения.
2.Большие диаметральные размеры при меньшей длине, чем у подшипников скольжения. Иногда это является существенным недостатком. Так, при заданном расстоянии между валками прокатных станов применение шарикоподшипников требует уменьшения диаметра шеек валков, а это ограничивает допустимые усилия при прокатке. Установка шарико- и роликоподшипников в нижней шатунной головке двигателей внутреннего cгoрания значительно увеличивает ее габариты и массу, что приводит к росту не только инерционных нагрузок, но и габаритов картера.
В связи с рассматриваемым здесь вопросом особо остановимся на игольчатых подшипниках. Они имеют меньшие наружные диаметры, чем любые другие подшипники качения равного внутреннего диаметра. Игольчатые подшипники не могут воспринимать осевую нагрузку, при
230
низких окружных скоростях они выдерживают высокие радиальные нагрузки. При малых нагрузках и отсутствии толчков они могут удовлетворительно работать при частоте вращения до 60 000 об/мин. Однако следует учитывать, что во время работы иглы не только катятся, но и скользят, отчего игольчатые подшипники нагреваются сильнее шариковых. Предпочтительно устанавливать их на медленно вращающихся и тяжело нагруженных осях. Область их применения: поршневые пальцы и опоры распределительных валов двигателей внутреннего сгорания, пальцы прицепных шатунов, оси коромысел, поворотные цапфы автомобильных колес, оси холостых колес шкивов, натяжных и направляющих роликов и звездочек, промежуточных зубчатых колес, сателлитов, крестовины карданов, втулки рессор и т. п.
3.Неудовлетворительная работа в условиях вибрационной нагрузки,
атакже при движении с малыми углами поворота. В этих случаях на дорожках качения образуются углубления, напоминающие отпечатки шарика при испытании на твердость по Бринеллю. Данное явление названо бринеллированием или ложным бринеллированием. Впервые оно было обнаружено в подшипниках автомобилей после длительной их перевозки по железной дороге.
Случаи бринеллирования опор качения отмечаются при вибрациях корпуса судна или фундаментов механизмов, расположенных вблизи опор.
В карданных передачах с карданными шарнирами, работающими при углах взаимного смещения вилок менее 10, карданный шарнир быстро выходит из строя вследствие бринеллирования. В этих случаях следует увеличивать угол смещения.
В некоторых случаях бринеллирование вызывает необходимость замены подшипников качения на подшипники скольжения.
4.Большой шум при работе.
5.Большая чувствительность к запыленности абразивом и к загрязнению смазочного масла, чем у подшипников скольжения. Разрушение тел качения подшипника связано с возникновением подповерхностных трещин в местах максимальных касательных напряжений, что характерно для усталостного изнашивания. Другими причинами разрушения тел качения являются относительно высокая шероховатость их поверхности и воздействие частиц загрязнений в масле. В последнем случае большое значение имеет размер этих частиц. Так, при уменьшении их размера от 40 до 3 мкм долговечность подшипника может снизиться в 7 раз. Более крупные частицы загрязнений не входят в контакт,
аболее мелкие не вызывают повреждений поверхности тела качения.
6.Недостаточная коррозионная и тепловая стойкость.
7.Значительно меньшая грузоподъемность и долговечность упорных подшипников качения по сравнению с подшипниками скольжения.
231
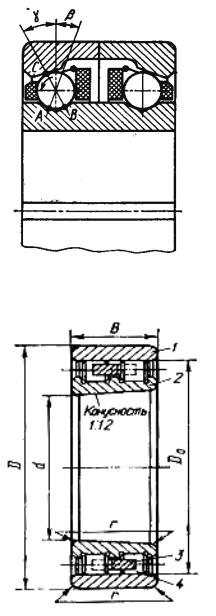
8. Трудности в изготовлении подшипников в случаях, когда для удобства монтажа либо ввиду особенностей конструкции вала требуются разъемные опоры. Например, при ремонте тракторных двигателей устанавливали на шатунные шейки роликовые, преимущественно игольчатые подшипники с кольцами, имевшими шевронные разъемы.
Положительные качества подшип- |
|
|||
ников качения |
позволяют |
расширить |
|
|
область их применения путем даль- |
|
|||
нейшего совершенствования |
конструк- |
|
||
ции подшипников и узлов машин и |
|
|||
технологии сборки. Рассмотрим три |
|
|||
конструкции подшипников качения, из |
|
|||
которых первые две выполнены с учетом |
|
|||
специфических |
требований |
к |
опорам |
|
шпинделей металлорежущих станков. |
|
|||
Подшипники шпинделей |
должны |
|
||
удовлетворять |
требованиям |
|
высокой |
|
точности вращения в течение дли- |
|
|||
тельного времени в условиях частых |
|
|||
остановок и пусков станка, жесткости в |
Рис.9.8. Подшипник шпинделя |
|||
радиальном и осевом направлениях и |
|
|||
простоты регулирования зазоров. Этим |
|
|||
требованиям |
отвечают специальные |
|
||
шарикоподшипники. На рис.9.8 показана |
|
|||
конструкция такого подшипника. Его |
|
|||
внутреннее кольцо имеет две дорожки |
|
|||
качения, профиль каждой из которых |
|
|||
описан двумя радиусами. Наружное |
|
|||
кольцо состоит из двух половин с |
|
|||
коническими дорожками качения конус- |
|
|||
ностью около 220. Шарики каждого ряда |
|
|||
контактируют с дорожками качения в |
|
|||
трех точках: А и В на внутреннем кольце |
|
|||
и С – на наружном. Прямые, прове- |
|
|||
денные через точки А и В и центр |
Рис.9.9. Роликовый подшипник |
|||
шарика, образуют с вертикалью, прохо- |
||||
дящей через шарик, углы β и γ около 11 и |
|
310. При работе шарики получают дополнительное вращение, показанное стрелкой, что обеспечивает их равномерное изнашивание. Сепараторы из текстолита центрируются по шарикам. Высокую точность вращения подшипников обеспечивают специальной обкаткой с эталонными шариками.
232

Роликовый подшипник (рис.9.9) для шпинделей металлорежущих станков применяют и в других машинах. Подшипник – двухрядный с роликами одного ряда, смещенными на полшага относительно роликов другого ряда. Благодаря значительному числу роликов и расположению их в шахматном порядке увеличивается число контактов роликов с дорожками качения и улучшаются условия работы подшипника. Наличие конического отверстия у внутреннего кольца подшипника позволяет при его монтаже на коническую шейку шпинделя снизить зазор до минимума.
Для ликвидации причин бринеллирования в упорном роликовом подшипнике винта вертолета Н.И. Камовым и его сотрудниками было внесено изменение в конструкцию сепаратора, позволившее в несколько раз повысить ресурс этого винта. В сепараторе два или три гнезда под ролики (рис.9.10) расположены под углом к радиальному направлению. Момент сил трения оказывается при
этом неодинаковым по величине при движении роликов в разные стороны, в результате чего при колебательном движении кольцо с большим моментом трения смещает комплект роликов с сепаратором в одном направлении.
В некоторых подшипниках качения применяют полые ролики для повышения демпфирующей способности, компенсации неточностей изготовления и монтажа деталей подшипникового узла, уменьшения массы, центробежных и инерционных нагрузок. Предельная грузоподъемность подшипника с полыми роликами составляет не более 50 % грузоподъемности аналогичных стандартных подшипников. Наилучшим методом смазывания для них является циркуляционный, особенно при невысоких частотах вращения. Наименьший диаметр применяемых роликов 8 мм. Верхнего предела диаметров полых роликов, по-видимому, не существует.
Направляющие качения применяют для облегчения прямолинейного движения суппортов, кареток, столов и тому подобных деталей, а также для обеспечения кругового движения некоторых из этих деталей.
233

Направляющие качения имеют следующие преимущества перед направляющими скольжения.
1.Снижение сопротивления движению, что особенно важно при ручном приводе (например, у заточных станков) и имеет решающее значение для уменьшения мощности приводов подачи в станках с программным управлением. В металлорежущих станках, где подача осуществляется ходовыми винтами, уменьшается их износ. Меньшее сопротивление движению позволяет при наличии гидропривода снизить рабочее давление в системе, уменьшить диаметр гидроцилиндра и вместимость масляного бака; снизить нагрев масла при прохождении его через дроссели и уменьшить тепловые деформации прецизионных станков.
2.Ликвидация эффекта взаимного прилипания поверхностей при трении скольжения, наблюдающегося при весьма малых подачах и приводящего к прерывистому движению и уменьшению точности.
3.Исключение влияния разности толщин масляного слоя на биение кареток и суппортов при высоких скоростях перемещения.
4.Упрощение технического обслуживания.
5.Облегчение замены изношенных деталей при одновременном повышении их долговечности.
В направляющих качения применяют такие же шарики, ролики или иглы, что и в подшипниках качения. Преимуществом шариковых направляющих является их меньшая чувствительность к погрешностям изготовления. Однако вследствие меньшей грузоподъемности шариков по сравнению с роликами того же диаметра применение чугунных направляющих ограничивается областью весьма малых нагрузок – для легких станков и приборов. Грузоподъемность закаленных стальных направляющих планок примерно в 30 раз выше, чем шариковых
направляющих. Допускаемую нагрузку р на тело качения можно определить по формулам:
–для шариковых направляющих р=kd;
–для роликовых направляющих p=kbd,
где k – условное напряжение, зависящее от материала направляющих и точности изготовления их и тел качения; d – диаметр шарика или ролика; b – длина ролика.
Винтовые пары качения. Для облегчения точных рабочих и установочных перемещений передачей «винт–гайка», а также
234

для уменьшения сил трения в механизмах с ручным приводом применяют передачи с трением качения (вместо трения скольжения). Одна из таких конструкций показана на рис.9.11. Она имеет гайку, состоящую из трех закаленных роликов, расположенных в общем корпусе симметрично относительно оси винта. Каждый ролик является цилиндрической рейкой, сопрягающейся с винтом. Осевые усилия, передаваемые на ролики, воспринимаются упорными шарикоподшипниками, а радиальные – игольчатыми подшипниками.
Более технологична винтовая пара с шариками (рис.9.12). Винтовые канавки на теле винта и гайки служат дорожками качения. Непрерывность движения шариков при вращении винта достигается тем, что начало и конец резьбы гайки соединены обводным каналом, образованным телом гайки и
скрепленным с ним отражателем. Рабочие поверхности деталей закалены. Смазывание производят при сборке.
Высокоскоростные совмещенные опоры. Совмещенными называются опоры, у которых рабочие элементы подшипников находятся непосредственно на валу или на оси опоры. Отсутствие внутренних колец исключает отрицательное действие их разностенности, кроме того, создается возможность увеличить предельную частоту вращения, уменьшить габариты узла и нагрузки от центробежных сил за счет уменьшения диаметра по центрам тел качения.
Имеются опоры качения, у которых элементы совмещены как с валом, так и с корпусом или деталями изделия, заменяющими внутренние и наружные кольца. Разборные совмещенные опоры получили широкое распространение в технике.
Совмещенные опоры имеют такие недостатки, как неточности изготовления подшипников, посадочных мест, фланцев, крышек и других деталей опоры, что вызывает взаимный неконтролируемый перекос дорожек качения. С целью уменьшения воздействия этого фактора разработаны неразборные совмещенные опоры.
9.3.5. Разгрузка рабочих поверхностей
Поверхности трения в некоторых случаях можно разгрузить, внеся в конструкцию машины изменения, направленные на снижение
235

действующих усилий, или уменьшив нагрузку, воспринимаемую непосредственно контактирующими деталями. Простейшим примером такой разгрузки может служить шевронная передача, в которой осевые усилия с полушевронов не передаются на валы и их опоры. Другим примером является двухколодочный тормоз, разгружающий валы и подшипники от радиальных сил.
В центробежных насосах при одностороннем подводе жидкости к рабочему колесу возникает осевое усилие, вызываемое различием статических давлений по обе стороны колеса. Такова же природа осевого усилия на колесах центробежных вентиляторов и нагнетателей (рис.9.13).
Рис.9.13. Колесо центробежного вентилятора
Для разгрузки рабочих колес применяют:
разгрузочные отверстия в диске, иногда – специальный обводной трубопровод, которые выравнивают давление по обе стороны колеса. Этот способ связан с необходимостью дополнительного уплотнения между нагнетательной и разгрузочной камерами и с увеличением гидравлических потерь, поэтому его используют только в одноступенчатых насосах.
двусторонний подвод жидкости к колесу;
симметричное расположение колес в многоступенчатых насосах;
гидравлические пяты, автоматически обеспечивающие уравновешивание осевых усилий на ротор при всех нагрузках; давление в разгрузочной камере определяется сопротивлениями на пути от камеры нагнетания до всасывающего патрубка и повышается с увеличением расхода жидкости через осевой зазор между разгрузочным диском и уплотнительным кольцом. При увеличении осевого усилия ротор насоса
236

может переместиться в сторону всасывания, что уменьшает осевой зазор и количество перетекающей жидкости. Давление в разгрузочной камере вследствие этого падает, и осевое усилие на разгрузочном диске как результирующая двух осевых сил увеличивается. Каждой осевой нагрузке соответствует определенное положение ротора. Установочный осевой зазор назначают в пределах 0,10 – 0,12 мм для среднего диаметра разгрузочного кольца до 150 мм, 0,15 – 0,20 мм при среднем диаметре от 150 до 250 мм и 0,25 мм при диаметре свыше 250 мм.
Уравновешивание динамических усилий в звеньях машин уменьшает нагрузку на сочленения. В частности, в многоцилиндровых двигателях, в которых силы инерции первых порядков уравновешены в пределах блока цилиндров, применяют иногда противовесы для разгрузки опорных подшипников.
Работе шестеренного насоса свойственна следующая особенность. Степень перекрытия шестерен у него больше единицы, т.е. пара зубьев вступает в зацепление, когда предыдущая пара еще из него не вышла. В начале зацепления пары между точ-
ками А и В (рис.9.14) образуется замкнутая полость с жидкостью в ней. При дальнейшем повороте шестерни объем этой полости становится минимальным, когда точки зацепления новой пары зубьев и предыдущей расположены симметрично относительно полюса зацепления Р. Указанная полость сохраняет свой объем до момента выхода из зацепления предыдущей пары зубьев в точке С на линии зацепления. Вследствие малой сжимаемости жидкости и большого сопротивления протеканию ее через торцовые зазоры между шестернями и корпусом насоса уменьшение объема полости сопровождается резким повышением давления в ней. В итоге на зубья шестерен, на валики и подшипники передается значительная пульсирующая нагрузка; известны случаи, когда по этой
причине насосы приходили в негодность за 8–10 часов эксплуатации из-за сильного износа подшипниковых втулок.
Для устранения вредного влияния давления жидкости делают разгрузочные канавки с торцов зубьев. Назначение канавок – сообщить замкнутую полость с камерой наг-
Рис.9.15. Схема разгрузки |
237 |
|
|
подшипников насоса |
|

нетания. Конфигурацию и глубину канавок рассчитывают. Второй способ нейтрализации давления заключается в скосе зуба ведомой шестерни таким образом, чтобы замкнутый объем все время возрастал. Это более дорогостоящий способ и рекомендуется для сильно нагруженных насосов и гидравлических двигателей.
Целесообразна разгрузка подшипников с помощью гидравлического противодавления, которое создается путем соединения полостей нагнетания и всасывания с разгрузочными камерами. Схема разгрузки опор изображена на рис.9.15. Чтобы свести к минимуму утечки через радиальные зазоры, разгрузочные камеры (дуги b и b1) отделяют от ближайшей полости двумя зубьями.
В тяжелых станках – карусельных и других – разгрузка круговых направляющих столов и планшайб целесообразна для повышения долговечности опорных поверхностей и для уменьшения момента от сил трения в периоды неустановившегося движения, что благоприятно отражается на равномерности вращения стола и весьма важно, например, при нарезании колес на зубофрезерных станках.
Одним из методов разгрузки пар трения является перенос усилий с ответственных поверхностей трения на менее ответственные. Так, нагрузку на направляющие можно уменьшить с помощью роликовых опор на подпружиненном основании.
9.4. Методы расчета износа элементов кинематических пар
Можно указать следующие основные виды расчета на износ:
по давлению (среднему или максимальному), действующему на поверхности трения; полученные значения сравнивают с
допускаемыми, взятыми, как правило, из практики.
Давление – один из главных, но не единственный фактор, определяющий скорость изнашивания. Поэтому расчеты по ним дают лишь сугубо ориентировочные. Сравнительные данные о размерах сопряжений в ряде случаев могут привести к неправильным выводам о способах повышения износостойкости конструкции;
по величине износа и форме изношенной поверхности – этот вид расчета позволяет указать основные пути повышения долговечности сопряжения при конструировании и эксплуатации.
Рис.9.16. Расчет износа конических
поверхностей
238

При расчете формы изношенной поверхности определяют величину износа поверхности сопряженных деталей в каждой точке, эпюру давлений р на поверхности трения и изменение взаимного положения в результате износа, т.е. износ сопряжения. Эти расчеты базируются на закономерностях изнашивания материалов и учитывают конфигурацию сопряжения.
Для пояснения методики рассмотрим расчет на износ сопряжения в виде конических поверхностей (рис.9.16) при линейных законах изнашивания.
Определим характер эпюры давлений на поверхности трения при принятых закономерностях изнашивания. Начало координат поместим в вершину конуса, а ось у направим по образующей. Скорость относительного скольжения в данной точке поверхности трения будет V = 2 πρn =2 πncos α, а закономерности kpV примут вид
|
|
1 |
k1 p2 ncos y; |
|
|||||||||||||||
|
Применяя формулу |
2 |
k2 p2 ncos y. |
(9.8) |
|||||||||||||||
|
|
|
|
|
|
|
|
|
|
|
|
|
|
|
|
|
|
|
|
|
|
1 2 |
|
1 2 |
, |
|
|||||||||||||
|
|
|
|
|
|
|
|||||||||||||
|
|
|
|
|
|
|
|
|
|
cos |
|
|
|
|
|
||||
|
получим |
|
|
|
|
|
|
|
|
|
|
|
|
|
|
|
|
|
|
|
1 2 |
1 |
|
2 |
|
k1 |
k2 2 npy, |
(9.9) |
|||||||||||
|
|
|
|
|
|||||||||||||||
|
|
|
|
|
cos |
|
|
|
|
|
|
|
|
|
|
|
|||
|
откуда |
|
|
|
|
|
|
|
|
|
|
|
|
|
|
|
|
|
|
|
|
р |
|
|
1 2 |
|
|
|
|
1 |
. |
(9.10) |
|||||||
|
|
2 n k |
|
k |
2 |
|
|
у |
|||||||||||
|
|
|
|
|
|
|
1 |
|
|
|
|
|
|
|
|
|
|||
|
Из этого равенства видно, что эпюра давлений имеет |
||||||||||||||||||
гиперболический характер, |
так |
|
|
как |
|
для |
|
|
заданных режимов |
работы |
|||||||||
1 2 |
const . |
|
|
|
|
|
|
|
|
|
|
|
|
|
|
|
|
|
|
|
Для определения значений найдем зависимость между силой Р и |
||||||||||||||||||
давлением р, распределенным по поверхности трения: |
|
||||||||||||||||||
|
|
|
|
|
|
|
y2 |
|
|
|
|
|
|
|
|
|
у2 |
|
|
|
Р рcos dS 2 рcos p dy 2 cos2 ру dy , |
|
|||||||||||||||||
|
S |
|
|
|
|
|
у1 |
|
|
|
|
|
|
|
|
|
у1 |
|
|
где |
1 |
r |
|
|
|
; 2 |
|
R |
|
|
|
и у cos . |
|
||||||
cos |
cos |
|
|||||||||||||||||
|
|
|
|
|
|
|
|
|
Подставляя в эту формулу значения р из формулы (9.10), интегрируя и решая уравнение относительно g1-2, получим
239