
новая папка / БЕЗОПАСНОСТЬ ТРАНСПОРТНЫХ СРЕДСТВ В ЭКСПЛУАТАЦИИ
.pdf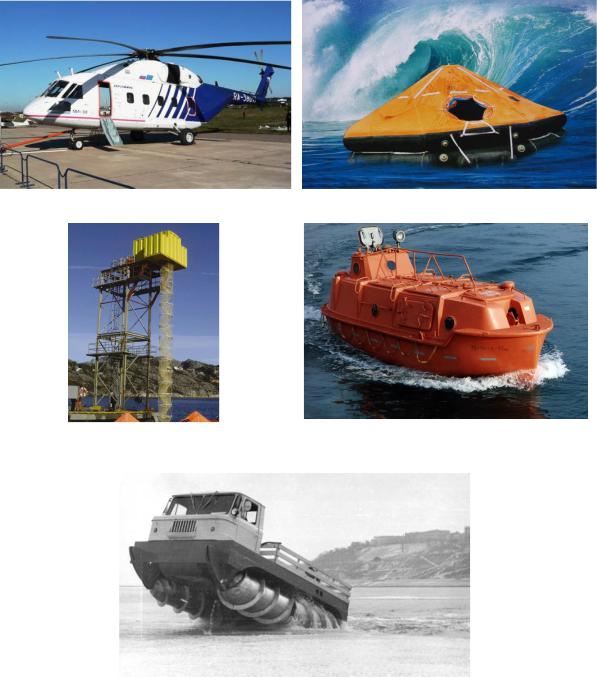
распложенные на воде или на льду; 5. Поддерживать режим автономной работы до нескольких суток.
В данной ситуации необходимо рассмотреть возможность применения транспортных средств, движители которых обладают отличительным характером взаимодействия с опорным основанием. Среди плавающих машин особое место занимают машины с роторновинтовым движителем (РВД). Особенности этого движителя позволяют применять транспортно-технологические средства, оснащенные им, в разных условиях эксплуатации, где применение других типов движителей невозможно или нерационально. РВД позволит обеспечить движение по замерзающим водоемам круглый год и проводить эвакуацию людей в случае аварий в арктических зонах (рис. 7).
Рис. 3. Воздушные средства эвакуации |
Рис. 4. Пример надувного спасательного |
|
плота для эвакуации людей |
Рис. 5. Средство транспортировки людей с |
Рис. 6. Спасательная шлюпка |
платформы на спасательные плоты |
|
Рис. 7. Демонстрация выход на лед роторно-винтовой машины ГПИ-72
Отличительная особенность РВД состоит в том, что, сочетая в себе качества гидравлического и сухопутного движителей, он может с достаточной эффективностью работать на сильно переувлажненных грунтах, снегу, льду, воде и среде, являющейся
150

комбинацией перечисленных сред. Используют РВД на машинах различного назначения – дорожно-строительных, сельскохозяйственных, военных и т.д. Так, например, в России РВД применяется на тяжелых и мощных ледорезных машинах и на легких снегоболотоходах. В США – на военных бронетранспортерах для передвижения по болотам и залитым водой полям. В Польше поставили РВД на специальный тягач, передвигающийся по толстому слою ила и предназначенный для обслуживания рыбных хозяйств после спуска из них воды. В Японии изготавливают спасательные и прогулочные транспортные средства с РВД.
В частности японской компанией Mitsui построены несколько роторно-винтовых машин (РВМ), одна из которых предназначена специально для движения в арктических льдах у побережья Аляски. Согласно данным этой компании при испытаниях модели РВМ на льду толщиной 30...50 см без снега наивысшее максимальное тяговое отношение (отношение силы тяги к весу) было равно 45 % при угле наклона винтовой лопасти 30 градусов и при отношении высоты лопасти к диаметру базового цилиндра 0,15. Построив и испытав в реальных условиях эксплуатации РВМ массой 10,8 т и длиной 7 м, инженеры компании Mitsui приводят следующие результаты: машина может буксировать грузы порядка 200 т по воде со скоростью 3 узла, на льду - со скоростью 25...40 узлов; может двигаться в условиях льда покрытого водой на 50 см, где любые другие машины и суда двигаться не могут; РВМ ломает лед толщиной до 43 см.
По сравнению с другими видами наземных движителей роторно-винтовой имеет ряд преимуществ [4]: 1. Обеспечивает особо высокую проходимость транспортного средства; 2. Создает очень малые давления на грунт; 3. Позволяет развить большую силу тяги; 4. Обеспечивает выход на лед и на необорудованный берег, 5. Обеспечивает амфибийные качества.
Опыт использования РВД на амфибийных транспортно-технологических и ледовофрезерных машинах указывает на перспективность разработки автономного универсального, по способности двигаться в перечисленных средах, спасательного средства для оказания помощи терпящим бедствие экипажам судов и персоналу ледостойких стационарных платформ.
На рис. 8 и 9 показан разработанный в НГТУ проект универсального спасательного средства с роторно-винтовым движителем и условия эксплуатации.
Рис. 8. Модель универсального спасательного |
Рис. 9. Иллюстрация условий эксплуатации |
средства с роторно-винтовым движителем |
универсального спасательного средства с |
|
роторно-винтовым движителем |
После предварительной проработки вопросов условий эксплуатации и конструктивных особенностей существующих спасательных средств для эвакуации персонала нефтегазодобывающих платформ на шельфе Арктических морей сформулирована основная концепция универсального спасательного средства.
Разработанное спасательное средство представляет собой роторно-винтовую плавающую машину со следующими параметрами: Габаритные размеры: длина 12 м, ширина 6 м, высота 4,5 м. Осадка полностью укомплектованного спасательного средства с экипажем
151
и эвакуируемым персоналом 1,0 м. Полная масса 10 т. Вместимость 42 человека (два человека экипаж). Скорость на льду – до 35 км/ч, снегу — до 40 км/ч и на воде — до 7 км/ч. Диаметр базового цилиндра движителя 1,2 м. Длина роторно-винтового движителя 9,0 м. Высота винтовой лопасти 0,2 м. Клиренс 0,5 м.
Способность двигаться по пятну горящей нефти обеспечивается наружной изоляцией корпуса жаропрочными плитками, применяемыми на корпусах космических кораблей многоразового использования. Определение окружающей обстановки обеспечивается применением систем технического зрения. Автономность работы в течение нескольких суток достигается за счет применения систем жизнеобеспечения.
Библиографический список
1.Осадчий, А. Нефть и газ российского шельфа: оценки и прогнозы // Журнал «Наука и жизнь». –
2006. – №7.
2.Мокроусов, С.Н. Проблемы обеспечения безопасности при освоении нефтегазовых ресурсов на континентальном шельфе и на суше Российской Федерации // Журнал-каталог «Транспортная безопасность и технологии». – 2006. – №1.
3.Богатырева, Е.В. Методы обеспечения безопасности персонала нефтегазовых платформ арктического шельфа: Автореферат дисс. …канд. техн. наук. – М, 2004.
4.Куляшов, А.П. Роторно-винтовые машины. Основы теории движения / В.А. Шапкин, И.О. Донато и др. – Нижний Новгород: НГТУ, 2000. - 451 с.
152
Секция 4 |
СОВРЕМЕННЫЕ ПРОБЛЕМЫ |
|
АВТОМОБИЛЬНОГО ТРАНСПОРТА |
|
|
|
|
УДК 67.02
ИМИТАЦИОННОЕ МОДЕЛИРОВАНИЕ, КАК СПОСОБ РЕШЕНИЯ СОВРЕМЕННЫХ ПРОБЛЕМ АВТОМОБИЛЬНОГО ТРАНСПОРТА
Веркин Е.Н.
ФГБОУ ВПО «Камская государственная инженерно-экономическая академия»
Автомобильный транспорт – это становой хребет сильной экономики и динамичного общества. Поэтому вполне правомерно и необходимо сохранить эту отрасль, жизненно важную для экономического роста, социального развития, процветания и, в конечном счете, мира и играющую ключевую роль в жизни каждого из нас как в промышленно развитых, так и развивающихся странах. Вследствие этого автомобильный транспорт представляет собой наиболее эффективное средство, которое позволяет обеспечить доступ всех предприятий ко всем крупнейшим мировым рынкам, продвигать торговлю, создавать рабочие места, обеспечивать лучшее распределение материальных благ и сплачивать всех людей.
Важной частью всей истории развития отрасли автомобильного транспорта является устойчивый прогресс. Мировые производители грузовых автомобилей, городских и междугородных автобусов и такси стремятся к созданию более безопасных, эффективных, чистых и малошумных автомобилей. Они воплощают в себе самую современную технологию в лучшем смысле этого слова и обеспечивают более высокое качество жизни, чем то, которое мы имеем сегодня [1].
Российская автомобильная промышленность не обеспечивает потребности транспортного рынка в конкурентоспособном подвижном составе высокого уровня безопасности, качества, ресурса и других технико-экономических показателей. Это одна из основных причин ухудшения работы автотранспорта.
По своим техническим характеристикам, безопасности, комфортности, надежности и другим важнейшим показателям продукция российской автомобильной промышленности существенно отстает от мировых аналогов.
Кпримеру, по результатам последних аналитических исследований «ПСМА Рус» (совместное предприятие PSA Peugeot-Citroen и Mitsubishi), конкурентное преимущество России в виде дешевых энергоносителей и рабочей силы не оправдано. Стоимость производства автомобилей на калужском заводе Peugeot-Citroen и Mitsubishi на 5% выше, чем стоимость производства тех же машин в Европе и Бразилии, и на 15-20% выше – чем в Китае или Корее. Поэтому единственный способ снизить себестоимость производства – наращивать его объемы, что позволит «размыть» постоянные издержки на большее число автомобилей [2].
Кпроблемам отечественных автопроизводителей можно отнести не только вышеуказанные, но и более низкую производительность труда, а также высокие издержки производства.
Характер видов деятельности и условия, в которых они осуществляются в промышленном мире, в значительной степени эволюционировали за последние годы. Факторы, которые явились причиной этих изменений, очень многочисленны, но среди них можно выделить два критических. С одной стороны, технологический прогресс и переворот, вызванный информационными технологиями, привели к революционным изменениям с точки зрения занятости, с другой – неопределенность экономического рынка потребовала большей гибкости в управлении персоналом и организации работы. Тем не менее, одной идеей, которая получила положительный отклик в ходе экспериментов в разных странах,
153
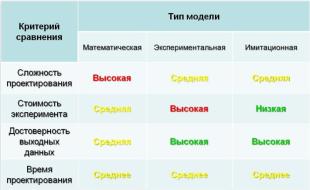
компании воспользовались: должна быть возможность направлять изменения и смягчать их негативное воздействие, используя соответствующие виды анализа и все ресурсы для взаимодействия между разными участниками производственного процесса [3].
Именно в этом контексте мы должны сегодня рассматривать анализ деятельности человека, считая его инструментом, позволяющим нам лучше описывать задачи и виды деятельности, чтобы формировать различные способы воздействия для повышения производительности труда и снижения издержек производства, например, обучение, разработку новых организационных режимов или проектирование инструментов и рабочих систем.
В данной статье описывается опыт участия в проекте «Модернизация технологической деятельности», полученный на предприятии ОАО «КАМАЗ», где активно внедряется имитационное моделирование, являющееся на сегодняшний день наиболее эффективным инструментом для решения множества производственных задач (см. табл.1).
Грамотная эргономика начинается с поиска «узких» мест на исследуемом сборочном производстве предприятия, которые можно выявить на основе анализа статистической информации за прошлые периоды времени.
Степень получения травм, включая совокупные расстройства вследствие их получения, в настоящее время характеризуется наивысшей степенью при осуществлении сборочных работ во всех процессах автомобильного сектора из-за повышенного коэффициента мускульноскелетных расстройств, вследствие монотонной работы и перенапряжения.
Статистика на исследуемом предприятии ОАО «КАМАЗ» за прошедший год показывает, что на сборочном производстве 53% травм, связанных с потерей трудоспособности, являются следствием мускульно-скелетных расстройств, которые обусловлены чрезмерными нагрузками, растяжениями и монотонными действиями.
Решение этой проблемы может быть обеспечено внедрением эргономических программ, составленных на основе анализа факторов риска и структурного снижения силовых, частотных и позиционных стрессов при выполнении работ, связанных с повышенной опасностью получения травмы.
После получения исходных данных для моделирования, необходимо разработать схему взаимодействия программных модулей. Для этого используются корпоративноинформационная система, модуль Teamcenter Engineering, представляющий собой систему инженерных данных, САПР UnigraphicsNX, программа имитационного моделирования Tecnomatix Jack и программа для создания электронных документов AdobeAcrobat 3D.
Данные из программных модулей поступают в среду имитационного моделирования Tecnomatix Jack, где происходит экспериментальное исследование.
Исследования деятельности человека в поточной системе сборки грузовых автомобилей подтверждают тот факт, что хорошо спроектированная рабочая зона способствует не только хорошему здоровью и состоянию работников, но также и повышению производительности и качества изделий. И наоборот, плохо спроектированная рабочая зона, вероятно, вызовет или будет способствовать развитию хронических производственных заболеваний, появлению жалоб на ухудшение здоровья, а также на проблемы, связанные с поддержанием качества и производительности на установленном уровне.
154
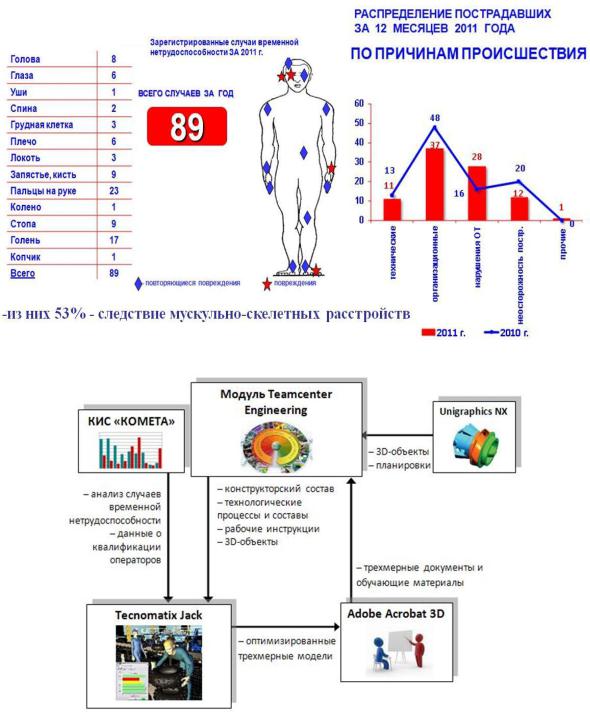
Для любого специалиста по эргономике выше сделанное заявление может показаться тривиальным. Каждый специалист по эргономике также признает, что во всем мире в условиях, в которых выполняется работа, можно найти не только недостатки, но грубые нарушения ее базовых принципов. Совершенно очевидно, что ответственные лица, например, производственные инженеры и менеджеры, часто не осведомлены о важности анализа рабочих зон.
Рис.1. Статистическая информация по травмам на сборочном производстве
Рис. 2. Концепция взаимодействия программных модулей
Нужно отметить, что во всем мире в отношении работы на производстве наблюдается тенденция, которая, как кажется, подчеркивает важность эргономических факторов: растущее требование улучшения качества продукции, гибкость и точность в поставках изделий. Эти требования несовместимы с консервативной точкой зрения относительно проектирования работы и рабочих мест. Качество конечного результата процесса опирается
155
на три составляющих: эргономические знания, интеграция с производительностью и требования по качеству, и участие [4].
В настоящее время правительство России обращает большое внимание на необходимость модернизации производства. В последнее время мы наблюдаем, как ряд российских предприятий начинает следовать стратегии модернизации. Это верный путь для увеличения конкурентоспособности. Однако требуется время, чтобы этот, пока еще вялотекущий, процесс превратился в общероссийский тренд. Очевидно, что сложности, вызванные кризисом, помогли многим руководителям понять необходимость модернизации [5].
Библиографический список:
1. Автомобильный транспорт России 2002-2003. Краткий обзор. Ежегодный доклад (Синяя книга IRU).
2.Сайт аналитического агентства «Автостат». URL: http://www.autostat.ru/news/view/9048/. Дата обращения: 13.09.2012
3.Вероника Де Кейзер. Анализ видов деятельности, задач и производственных систем. URL: http://base.safework.ru/iloenc?doc&nd=857400288&nh=0&ssect=0. Дата обращения: 14.09.2012
4.Роланд Кадефорс. Рабочие станции.
5.―Наш бизнес в России – это яркая история успеха Siemens PLM Software‖ Интервью Eric Sterling
и Steffen Buchwald, топ-менеджеров Siemens PLM Software. Издание CAD/CAM/CAE Observer #1 (61) / 2011.
УДК 629.3.083 (075.8)
ПРОДЛЕНИЕ ЭФФЕКТИВНОГО РЕСУРСА АВТОМОБИЛЕЙ ЗА СЧЕТ УСИЛЕННОГО КОНТРОЛЯ СОСТОЯНИЯ
Обшивалкин М.Ю.1, Паули Н.В.2 1 Ульяновский государственный технический университет
2 Пензенский государственный университет архитектуры и строительства
При эксплуатации подвижного состава в настоящее время актуальным вопросом является определение конкретных рамок эффективного использования. Однако данный период сильно варьируется и зависит от большого перечня условий. Это связано в первую очередь с качеством самого автомобиля, технического обслуживания, текущего ремонта, применяемых запасных частей, с номенклатурой используемого оборудования. Немалое значение имеет ряд организационных причин, в том числе условия процесса перевозок и многие другие факторы, планирование которых с необходимой точностью либо крайне затруднительно, либо вообще невозможно. Большую роль играет также квалификация персонала, выполняющего технические воздействия, а также способы стимулирования качества работ по обслуживанию и ремонту автомобилей. Немаловажно также учитывать сложность и ремонтопригодность подвижного состава.
Однако в некоторых случаях нормативно – техническая документация может иметь приблизительные значения эффективных ресурсов [1]. Также такого рода информация часто указывается в различных источниках, где проводились конкретные оценки эффективности эксплуатации подвижного состава [3, 4, 5]. По причинам широкого расхождения условий, указанных выше, в которых эксплуатируются автомобили, необходимо учитывать, что для конкретного автотранспортного предприятия принимать данные значения для планирования будет категорически нецелесообразно. Так, очень многое зависит от качества слежения за технически исправным состоянием подвижного состава. Большую роль играет мера, по которой выполняется дефектация частей автомобиля.
Целью любого автотранспортного предприятия является получение прибыли от выполнения деятельности, связанной с автомобилями. Соответственно, организация
156
всесторонне стремится повысить данный показатель. Одним из путей повышения является экономия на запасных частях, которая происходит повсеместно. В итоге очень часто элементы устройства автомобилей после демонтажа устанавливаются в заведомо неисправном состоянии. Однако это состояние является работоспособным, что дает возможность выполнения последующего производственного процесса. Выполнение данного действия хотя и рискованно, но оправдывает себя при ощутимой экономии на запасных частях (показателе удельных затрат на поддержание работоспособного состояния) и по причине крайне слабого воздействия на техническую эксплуатацию подвижного состава, на наработку на отказ.
По вышеперечисленным причинам проверка технического состояния выполняется визуально, либо, как максимум, с применением более простого оборудования, результатом которого не может быть полноценное исправное состояние, которого добиваются при производстве. С течением наработки это ведет к накоплению неисправностей, называемых скрытыми – такими, которые не могут быть обнаружены в условиях транспортного предприятия по тем или иным причинам [6]. Итогом продолжительной эксплуатации подвижного состава с работоспособными, но неисправными элементами обычно рано или поздно приводит к повышению количества поломок в определенный период наработки [2]. Следствием является снижение значения основного показателя безотказности – наработки на отказ. Результатом длительной эксплуатации будет критическое значение коэффициента технической готовности (КТГ), а это непосредственно оценивает крайне низкую эффективность применения автомобилей [7].
Конечно, далеко не все элементы конструкции применяются в заведомо неисправном состоянии. Многие из них заменяются на новые, т.к. невыполнение этого действия однозначно крайне негативно скажется на работоспособности техники. Однако в основном это особенно касается так называемых расходных элементов – различных резинотехнических изделий, фильтров, фрикционных частей и некоторых других деталей.
Но не следует забывать, что любая деталь имеет конечное значение эффективного ресурса, по истечению которого потребуется ее замена.
Для комплексного анализа представленной модели указана вероятность отказа, а также прирост затрат на ее эксплуатацию. Очевидно, что при условии замены элементов в момент ресурсных наработок, вероятность отказа будет иметь некоторое фиксированное значение во времени, а прирост затрат не будет изменять свою интенсивность. Ситуация не изменяется с большой наработкой, при которой уже выполнено 4 и более замены элемента с минимальным ресурсом – происходит только лишь колебание значения относительно некоторого среднего уровня, названного на рис. 1 аппроксимирующей прямой [8].
Проблемой же привязки указанной модели к реальным системам является большой перечень параметров, по которым оценивается исправность конкретного элемента. А исправность всех элементов определяет исправность системы, в которую они входят. Данная модель имеет место для узлов и агрегатов (их частей) автомобиля, которые отличаются от других доминантным показателем, имеющим максимальную интенсивность изменения технического состояния. Примером тому является пара элементов тормозной системы «тормозная колодка» - «тормозной барабан».
Степень износа фрикционного элемента колодки характеризует остаток ресурса данной детали. Аналогично толщина барабана, или уровень его выработки, определяет ресурс этой детали. Причиной тому является тот факт, что в течение продолжительной эксплуатации вероятнее всего система несколько раз откажет в момент предельного износа фрикционов (который легко планируется), а потом – в момент предельного износа барабана (тоже легко подвергается планированию между заменами спаренного элемента).
Однако автомобиль в своем устройстве имеет большое количество (90 % и более) деталей, которые не имеют доминантного показателя технического состояния. Они имеют большой перечень сложно планируемых в течение эксплуатации показателей, имеющих важное значение в оценке остаточного ресурса. Более того, при дефектовке в условиях
157

автотранспортных предприятий учет всех параметров не производится по перечисленным выше причинам. Обычно проверка выполняется только лишь на работоспособность – годен / не годен, не определяя конкретного состояния, уровня неисправности детали.
Рис. 1. Зависимость вероятности отказа узла и составляющих его элементов от общей наработки [8]
Для элементов, которые имеют сложно планируемое изменение характеризующих их параметров, основным способом планирования является статистически определенная средняя наработка на отказ. Большинство таких деталей будет иметь зависимость изменения своего состояния по закону нормального распределения [2] (Гаусса) (рис. 2).
Соответственно при превышении средней наработки на отказ для конкретного элемента будет значительно падать надежность как его эксплуатации, так и системы «автомобиль» в целом. Это крайне негативно скажется на уровне удельных затрат, а значит и на эффективности эксплуатации автомобиля. Также это отразится и на периоде экономически целесообразного применения подвижного состава, т.к. отказ, который последует вследствие критического состояния элемента, может привести также к поломке и значительному негативному изменению параметров других деталей.
Однако, такого рода ситуация просматривается далеко не на каждом предприятии. При хорошем функционировании отдела контроля ремонтных работ и технического состояния автомобилей можно получить совсем иные результаты анализа хозяйственной деятельности организации. Следствием скрупулезного отношения к технической эксплуатации подвижного состава является получение высокого уровня безотказности и в общем надежности.
Для определения ресурса конкретных деталей, которые имеют множество важных в эксплуатации параметров, необходимо определить среднюю наработку на отказ для них. Получив это значение в условиях конкретного предприятия, можно в дальнейшем управлять периодичностью принудительной замены таковых элементов. В итоге для систем автомобиля с определенными средними ресурсными наработками элементов можно построить зависимость, аналогичную изображенной на рис. 1. Отличительной особенностью будет
158
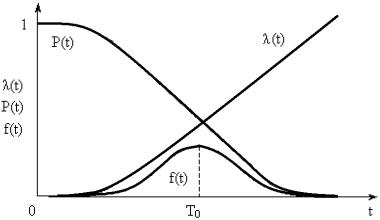
являться неопределенность основных параметров детали, которые имеют непосредственное влияние на поток отказов. Однако по среднему значению наработки на отказ можно судить о том, что в этот момент выполнить замену будет эффективно. Это не только положительно скажется на значении затрат на эксплуатацию, но и продлит ресурс использования автомобиля в целом.
Рис. 2. Графики изменения показателей безотказности при нормальном распределении: Р(t) - вероятность нахождения в работоспособном состоянии; λ(t) – вероятность отказа; f(t) - плотность распределения наработки до отказа; T0 - центр симметрии распределения; t – наработка [2].
Для подтверждения возможности продления периода эффективного ресурса собраны и обработаны данные с одного из крупных автотранспортных предприятий г. Ульяновска. Проанализировано изменение среднего значения наработки на отказ в течение продолжительной эксплуатации (рис. 3). Основной идеей стратегии, которой стало придерживаться предприятие, является комплексное восстановление технического состояния автомобилей. В табл. 1 представлена общая характеристика исследуемого подвижного состава: указаны дорожные условия, пробег автомобилей на момент начала и в течение исследования, а также средние удельные затраты на эксплуатацию. Подвижной состав разделен на группы автомобилей одной модели. Всего представлено 5 групп: Вольво F12, Мерседес Актрос, КАМАЗ 43101, КАМАЗ 44108 и КАМАЗ 53215.
|
|
|
|
Таблица 1 |
|
Характеристика анализируемого подвижного состава |
|
||
|
|
|
|
|
Группа |
Дорожные |
Пробег на |
Анализируем |
Удельные |
автомобилей |
условия |
начало |
ый пробег |
затраты |
|
|
исследования |
|
|
Вольво F12 |
Асфальт, за пределами города |
600000 км |
400000 км |
0,637 руб/км |
Мерседес |
Асфальт, за пределами города |
200000 км |
400000 км |
1,104 руб/км |
Актрос |
|
|
|
|
КАМАЗ 43101 |
Грунт, за пределами города |
75000 км |
200000 км |
1,623 руб/км |
КАМАЗ 44108 |
Грунт, за пределами города |
50000 км |
200000 км |
1,169 руб/км |
|
|
|
|
|
КАМАЗ 53215 |
Асфальт, за пределами города |
150000 км |
300000 км |
1,017 руб/км |
Рассмотренные группы автомобилей имеют низкие показатели удельных затрат на эксплуатацию, что характеризует их эффективность эксплуатации. На них влияет приспособленность транспорта к условиям эксплуатации и качество процесса поддержания работоспособного состояния, т.к. с течением наработки показатель безотказности не падает, а значит и надежность системы «автомобиль» имеет фиксированную величину.
Первая подгруппа, которая включает автомобили марок Вольво F12, Мерседес Актрос и КАМАЗ 53215, дает возможность непосредственного сравнения уровня безотказности произведенного в России подвижного состава с иностранным. Вторая подгруппа,
159