
новая папка / БЕЗОПАСНОСТЬ ТРАНСПОРТНЫХ СРЕДСТВ В ЭКСПЛУАТАЦИИ
.pdf
Рис. 2. Стенд лаборатории тормозов НАМИ с установленным дисковым тормозом
а) |
б) |
Рис. 3. Процессы торможения для различных типов накладок: а) – АСК; б) – МК 1 – приводное давление; 2 – тормозной момент;
3 – скорость вращения; 4 - мощность трения
Рис. 4. Скоростные характеристики |
Рис. 5. Температурные характеристики |
коэффициента трения |
коэффициента трения |
1 – – – АСК; 2 ––– МК |
– – – АСК; ––– МК |
30
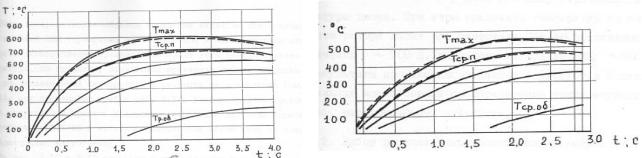
Дальнейшие экспериментальные и аналитические исследования показали, что в случае нестабильного коэффициента трения происходит увеличение рабочих температур пар трения. В результате проведенных расчетов с использованием системы уравнений динамики трения, в которых используются экспериментальные зависимости, полученные для данной конструкции, были определены температурные характеристики различных вариантов торможений. На рисунках 6 и 7 представлены температурные графики процессов торможения при начальной скорости 60 км/ч и конечной 30 км/ч. Как видно из представленных зависимостей, кроме ухудшения динамики торможения, нестабильность коэффициента трения АСК накладок приводит к значительному росту температур на поверхности трения диска и среднеобъемных. Применение материала МК позволяет значительно снизить рабочие температуры тормоза и обеспечить их значения в пределах допустимых по условиям требований стандартов.
Рис. 6. Расчетные температуры диска при |
Рис. 7. Расчетные температуры диска при j=0,3g |
j=0,3g материал накладок АСК |
материал накладок МК |
Металлокерамические образцы тормозных накладок обеспечивают по сравнению с асбестосмоляной композицией более высокую динамику торможения при скоростной и температурной стабильности коэффициента трения, позволяют значительно снизить рабочие температуры диска. При этом градиенты температур по нормали к поверхности трения диска составляют при использовании материала АСК значения ̴ 700 К, тогда как для материала МК ̴ 500 К.
На практике нестабильность коэффициента трения рассмотренного варианта АСК тормозных накладок может приводить к блокировке тормоза в конце торможения, что ухудшает безопасность. С точки зрения долговечности нестабильность коэффициента трения приводит к появлению микротрещин на поверхности трения диска, в то время как при использовании накладок из МК трещинообразования на поверхности диска по результатам испытаний не отмечено.
Библиографический список
1.Браун, Э.Д. Моделирование трения и изнашивания в машинах / Ю.А. Евдокимова, А.В. Чичинадзе - М., Машиностроение, 1982, -190 с.
2.Чичинадзе, А.В. Расчет, испытание и подбор фрикционных пар. / А.В. Чичинадзе - М.: Наука,
1979, -267 с.
31
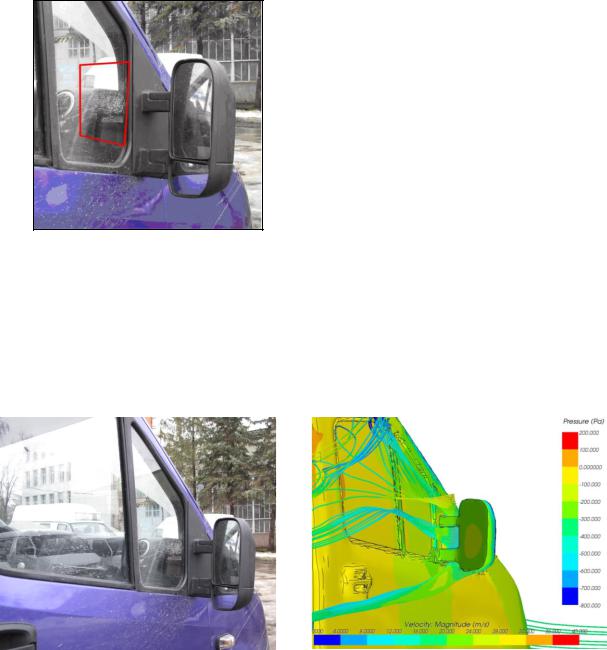
УДК 629.113
УСТРАНЕНИЕ ЗАГРЯЗНЕНИЯ БОКОВЫХ СТЕКОЛ ДВЕРЕЙ ПУТЕМ УЛУЧШЕНИЯ АЭРОДИНАМИЧЕСКИХ СВОЙСТВ ФОРМЫ ЗЕРКАЛ ЗАДНЕГО ВИДА
Миронов С.В., Капитанова Ю.А.
ООО «ОИЦ»
Постановка задачи.
В процессе испытания нового автомобиля, при движении в плохую погоду, отмечено загрязнение средней части неподвижных стекол левой и правой дверей на уровне боковых верхних стоек зеркал, что существенно ухудшает видимость с места водителя через зеркала заднего вида.
Определение причины загрязнения. В процессе работы была выявлена причина загрязнения - результат неоптимального движения токов воздуха в области зеркал заднего вида.
Выбор варианта решения задачи. В ходе решения задачи рассмотрено несколько вариантов конструктивных решений: изменение формы зеркала, изменение стойки зеркала, изменение сечения стойки «А», изменение формы сопряжения капот – крыло.
Ввиду разного рода условий, с точки зрения технологичности, качества, потребительских свойств, принято решение использовать вариант по изменению формы зеркала заднего вида. Данный путь был наименее ресурсозатратный и отвечал всем выше перечисленным требованиям.
Испытание и доводка поверхности зеркала заднего вида.
Для определения оптимальной формы зеркала заднего вида проведен расчет вариантов зеркал в расчетном пакете STAR CCM+, что позволило уменьшить сроки доводки конструкции и снизить ресурса затраты.
Рис. 2. Результат испытаний, результат расчетов в Star CCM+
Для проведения расчета использовалась точная модель всего автомобиля. В расчете моделировалось движение автомобиля со скоростью 80 км/ч.
32
Врезультате расчета исходного варианта поверхности зеркала была отмечена сходимость результатов расчета с реальными результатами испытаний (рис.2), что позволило сделать вывод о возможности применения данной расчетной схемы для определения оптимальной формы зеркала используя STAR CCM+.
Для наработки расчетных вариантов был выполнен анализ конструкции и формы зеркал заднего вида автомобилей-аналогов и разработано несколько вариантов поверхностей формы зеркала, которые были введены в конструкцию автомобиля, и рассчитаны используя STAR CCM+. В результате была выявлена оптимальной формы зеркала, удовлетворяющая выше перечисленным требованиям.
Для подтверждения результатов расчета окончательного варианта формы зеркала выполнено макетирование на реальном образце и прохождение дорожных испытаний. С помощью пластилина, была воспроизведена новая, доведенная поверхность формы зеркала заднего вида. Дорожные испытания образца дали положительные результаты.
Окончательное решение.
Врезультате проделанной работы устранен дефект «загрязнения боковых стекол дверей», тем самым улучшена обзорность, которая влияет на безопасное движение автомобиля. В короткие сроки с привлечением малых ресурсов получены положительные результаты испытаний поверхностей зеркала заднего вида, выполнена доводка поверхности с точки зрения общего стиля автомобиля, изготовлена опытная партия зеркал заднего вида.
Развитие проекта.
Приобретены опыт и знания, позволяющие производить доводку конструкции в кратчайший срок с минимальными затратами. Полученный положительный результат позволяет говорить о возможности получать решение таких задач, как снижение аэродинамических потерь и шума автомобиля, повышение эффективности работы стеклоочистителя, вентиляции салона автомобиля, охлаждения агрегатов автомобиля с использованием пакета Star CCM+.
УДК 629.113
ВЛИЯНИЕ МИКРОКЛИМАТА САЛОНА АВТОМОБИЛЯ НА БЕЗОПАСНОСТЬ ЭКСПЛУАТАЦИИ
Макарова И.В., Уразаев А.Х.
ФГБОУ ВПО «Камская государственная инженерно-экономическая академия»
В связи с динамичным ростом автомобилизации и, в особенности с ее негативными последствиями, во всем мире возрастают требования к безопасности в процессе эксплуатации автомобильной техники. Возникшие проблемы обеспечения безопасности дорожного движения ставят новые задачи перед автомобильной промышленностью – это разработка и создание безопасных, экономичных, экологичных и эргономичных автомобилей, удовлетворяющих запросам потребителя.
По-прежнему, одной из острейших социальных проблем, особенно для России, является проблема снижения уровня аварийности на автомобильных дорогах, вследствие которой растет число погибших и пострадавших в дорожно-транспортных происшествиях [1]. По статистике, большинство дорожно-транспортных происшествий происходит по вине водителя, поэтому для безопасности движения, повышения производительности труда и сохранения здоровья водителя большое значение имеет рациональная организация рабочего места, которая заключается в оснащении, оборудовании и планировке рабочего места в соответствии с психофизиологическими и антропометрическими характеристиками человека [2].
33
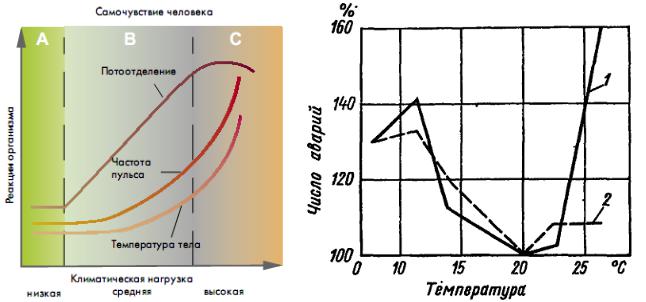
Исходя из вышеизложенного, можно сказать, что вопросы безопасности движения автомобиля являются основополагающими при разработке конструкций узлов и систем, в том числе систем микроклимата, обеспечивающих требуемые параметры воздушной среды.
Системы обеспечения микроклимата (СОМ) в салоне выполняют важную функцию повышения активной безопасности автомобиля. Во-первых, в комфортных условиях при надежных, правильно скомпонованных и хорошо работающих системах кондиционирования, вентиляции и отопления салона повышается работоспособность водителя и концентрация внимания на быстро изменяющихся условиях движения. Во-вторых, безопасность движения автомобиля в значительной степени зависит от надежной и эффективной защиты стекол от запотевания и обмерзания, что достигается их равномерным обдувом теплым воздухом, и тем самым, обеспечивается хорошая видимость [3].
Как доказано исследованиями, микроклимат оказывает существенное влияние на организм человека [4]. Помимо этого, научные исследования, проведенные Всемирной организацией здравоохранения (ВОЗ), показали, что степень концентрированности и быстрота реакций человека при неблагоприятных нагрузках на его организм существенно снижаются [5].
Одной из таких неблагоприятных нагрузок является высокая температура воздуха. Наиболее благоприятная для водителя температура лежит в диапазоне от 20 до 220C (рисунок 1). Это соответствует зоне А климатической нагрузки на человека.
Интенсивное солнечное облучение автомобиля может повысить температуру в салоне на 150C по сравнению с температурой наружного воздуха – особенно на уровне головы, где такое повышение является наиболее опасным.
При повышении температуры воздуха повышается температура тела, растет пульс, увеличивается потоотделение. Мозг получает слишком мало кислорода. Все это можно видеть в зоне B климатической нагрузки на человека.
Зона C является зоной перегрузок для человека. Медики, работающие в области дорожной медицины, называют такое состояние «климатическим стрессом».
Рис. 1. Влияние температуры на |
Рис. 2. Зависимость между температурой |
самочувствие человека |
воздуха в салоне и числом аварий |
|
1 – мужчины, 2 – женщины |
Как показывают исследования, повышение температуры с 25 до 350C на 20% уменьшает способность адекватно оценивать ситуацию и принимать правильные решения. Это эквивалентно содержанию алкоголя в крови 0,5 промилле.
При высокой влажности воздуха степень некомфортности в салоне многократно увеличивается.
34
Температура воздуха в салоне автомобиля влияет на число дорожно-транспортных происшествий (рисунок 2). Как следует из графика, эксплуатация автомобилей в условиях повышенной или пониженной температур в салоне напрямую влияет на рост числа аварий.
Вышеприведенные факты свидетельствуют о том, что независимо от времени года вопросы создания микроклимата в салоне автомобиля остаются актуальными, Это относится как к решению вопросов климатический комфорта путем совершенствования систем кондиционирования, отопления и вентиляции салона автомобилей, так и к обеспечению свободного обзора через стекла, что является важным элементом повышения активной безопасности при движении.
Библиографический список
1.Ротенберг Р.В. Вероятностная оценка времени реакции водителя / Р.В. Ротенберг, Ш.И. Хубелашвили //Динамические процессы в транспортных системах. – М.: МАДИ, 1982. – 172 с.
2.Афанасьев Л.Л. Конструктивная безопасность автомобиля / Л.Л. Афанасьев, А.Б. Дьяков, В.А. Иларионов. — М.: Машиностроение, 1983. — 212 с. ил.
3.Ветохин А.С. Автотранспортная эргономика: учебное пособие / А.С. Ветохин, В.В. Ляндербургский. – Пенза: ПГАСА, 2003 – 126 с.,
4.Носаков И.В. Анализ технического уровня и потребительских свойств АТС. Предпроектные исследования / И.В. Носаков, С.М. Кудрявцев - Автомобильная промышленность. -2001. -№2. – с.13-16.
5.Зезюля О. Журнал «Охрана труда и техника безопасности» №7, 2009г.
6.Программа самообучения Audi 208 «Автомобильные климатические установки. Устройство и принцип действия».
7.Афанасьев Л.Л. Конструктивная безопасность автомобиля / Л.Л. Афанасьев, А.Б. Дьяков, В.А. Иларионов. — М.: Машиностроение, 1983. — 212 с. ил.
УДК 629.021
К ВОПРОСУ О РАСЧЕТЕ ПРОИЗВОДИТЕЛЬНОСТИ НАСОСА ГИДРОУСИЛИТЕЛЯ РУЛЯ
Салахова Р.Р., Цыбунов Э.Н., Шайхразиев Ф.М. Камская государственная инженерно-экономическая академия
Характеристики и свойства системы рулевого управления с гидроусилителем определяются соответствующими характеристиками элементов системы: рулевого механизма, распределителя, гидроусилителя, насоса гидроусилителя. Применение имитационного моделирования позволит конструктору на ранней стадии проектирования оценить и проанализировать функциональные свойства рулевого управления автомобиля. Определение требуемой производительности насоса гидроусилителя является одной из важных задач проектирования рулевого управления с гидроусилителем.
В литературе, посвященной расчету гидроусилителя рулевого управления, даются рекомендации по выбору производительности насоса. В книге И. П. Чайковского, П. А. Саломатина [1] производительность насоса гидроусилителя руля выбирается из условия превышения скорости поворота колес гидроцилиндром над максимально возможной скоростью поворота колес водителем. Указано, что, если подача насоса не удовлетворяет вышеуказанному условию, то возникает вероятность возникновения во время быстрых поворотов рулевого колеса водителем повышенного сопротивления повороту. Данное явление приводит к ухудшению управляемости, а следовательно, к снижению безопасности движения, средней скорости и производительности транспортного средства.
Л. Л. Гинцбург отмечает, что номинальная (расчетная) производительность должна быть достигнута гидронасосом при числе оборотов двигателя, превышающих холостые, не более чем на 25% и давлении 0,5pmax, где pmax – максимальное давление, развиваемое насосом
35

гидроусилителя [2]. Производительность насоса при дальнейшем увеличении числа оборотов ограничивается клапаном расхода.
Для определения расчетной производительности насоса гидроусилителя составлено уравнение расхода гидроцилиндра усилителя (1), которое учитывает сжимаемость и утечки жидкости между рабочими полостями гидроцилиндра:
Q А |
dz |
|
V dp |
k |
|
p , |
(1) |
||
|
|
|
|
|
|||||
п dt |
|
2E dt |
|
ут |
|
|
где Ап – площадь поршня гидроусилителя; z – перемещение поршня гидроцилиндра; V – сжимаемый объем рабочей жидкости; E –модуль объемной упругости рабочей жидкости; p – перепад давления в рабочих полостях гидроцилиндра; kут – коэффициент утечек жидкости между рабочими полостями гидроусилителя.
Для имитации различных режимов работы составлена математическая модель рулевого управления. При построении математической модели приняты следующие допущения:
–давление источника мощности – величина постоянная;
–не учитывается гидравлическое сопротивление магистралей;
–не учитываются утечки жидкости в гидравлических магистралях;
–жесткость правой и левой частей рулевого привода одинакова, на основании чего рассматривается одно управляемое колесо, имеющее удвоенную величину момента инерции относительно шкворня;
–не учитывается влияние подвески.
Математическая модель рулевого управления с гидроусилителем и роторным распределителем имеет следующий вид (2):
х |
з рк kос ср , |
|
|
|
|
|
|
|
|
|
|
|
|
|
|
|
|
|
|
|
|
|
|||||||||||||||||||
|
|
|
|
|
d 2 z |
|
|
|
|
|
|
|
dz |
|
|
|
|
|
|
|
|
|
|
|
|
|
|
|
|
dz |
|
|
|
|
|
||||||
m |
|
|
|
k |
|
|
|
c |
|
|
|
z P |
|
|
sgn |
( p |
p |
|
) А |
, |
|||||||||||||||||||||
|
|
|
|
|
|
|
|
|
|
|
|
|
|
|
|
|
|
|
|
||||||||||||||||||||||
|
|
п |
dt 2 |
|
|
|
|
|
в |
dt |
|
|
|
|
пр |
|
|
|
|
|
тр |
|
|
dt |
1 |
|
2 |
п |
|
||||||||||||
|
|
|
|
|
|
|
|
dz |
|
|
|
V dp |
|
|
|
|
|
|
|
|
|
|
|
|
|
|
|
|
|
|
|
|
|||||||||
Q |
|
|
А |
|
k |
|
|
|
p, |
|
|
|
|
|
|
|
|
|
|
|
|||||||||||||||||||||
|
|
|
|
|
|
|
|
|
|
|
|
|
|
|
|
|
|
|
|
|
|
|
|
|
|||||||||||||||||
|
|
|
|
|
|
|
п dt |
|
|
2E dt |
|
|
|
|
|
ут |
|
|
|
|
|
|
|
|
|
|
|
|
|
||||||||||||
|
|
|
|
|
|
|
|
|
|
|
|
|
|
|
|
|
|
|
|
|
|
|
|
|
|
|
|
|
|
|
|
|
|
|
|
|
|
|
|
|
|
|
|
|
|
|
|
|
|
|
|
|
|
|
|
|
|
d р |
|
|
|
p |
|
|
p sgn x |
|
|
|
|
|
|
|
|
||||||||||
|
|
|
3 b |
|
|
|
|
|
|
|
|
|
|
п |
з |
|
|
|
|
|
|
|
|||||||||||||||||||
Q |
|
|
|
|
|
|
|
x |
|
|
|
|
|
|
|
|
|
|
|
|
|
|
|
|
, |
|
|
|
|
|
|||||||||||
|
|
|
|
|
|
|
|
|
|
|
|
|
|
|
|
|
|
|
|
|
|
|
|
|
|
|
|
|
|
||||||||||||
|
|
|
|
|
|
|
|
|
180 |
|
|
з |
2 |
|
|
|
|
|
|
|
|
|
|
|
|
|
|
|
|
|
|
(2) |
|||||||||
|
|
|
|
|
|
|
|
|
|
|
|
|
|
|
|
|
|
|
|
|
|
|
|
|
|
|
|
|
|
|
|
|
|
|
|
|
|
|
|
|
|
r |
|
|
|
z, |
|
|
|
|
|
|
|
|
|
|
|
|
|
|
|
|
|
|
|
|
|
|
|
|
|
|
|
|
|
||||||||
с |
|
|
|
|
с |
|
|
|
|
|
|
|
|
|
|
|
|
|
|
|
|
|
|
|
|
|
|
|
|
|
|
|
|
|
|
|
|
|
|
|
|
Tc cпр ( с hc срhk ), |
|
|
|
|
|
|
|
|
|
|
|
|
|
|
|
||||||||||||||||||||||||||
|
|
|
|
d 2 ср |
|
|
|
|
|
|
|
d ср |
|
|
|
|
|
|
|
|
|
|
|
|
|
|
|
|
|
|
|||||||||||
J |
|
|
|
k |
|
|
|
с |
|
|
|
T h , |
|
|
|
|
|||||||||||||||||||||||||
|
|
|
|
|
|
|
|
|
|
|
|
|
|
|
|
|
|
|
|||||||||||||||||||||||
|
к |
|
|
|
dt 2 |
|
|
|
|
|
|
|
тр |
|
|
|
dt |
|
|
|
|
|
к |
|
|
ср |
|
c к |
|
|
|
|
|
||||||||
|
|
|
|
|
|
|
|
|
|
|
|
|
|
|
|
|
|
|
|
|
|
|
|
|
|
|
|
|
|
|
|
|
|
|
|
|
|
|
|
|
|
|
|
|
|
|
|
|
|
|
|
|
|
|
|
|
|
|
|
|
|
|
|
|
|
|
|
|
|
|
|
|
|
|
|
|
|
|
|
|
|
|
|
где xз – угловое смещение роторного распределителя; αрк – угол поворота рулевого колеса; kос – коэффициент обратной связи по углу поворота управляемых колес; θcp – средний угол поворота управляемых колес; mп – масса поршня усилителя; kв – коэффициент вязкого трения о стенки цилиндра; спр – приведенная к поршню гидроусилителя жесткость элементов привода управляемых колес; Ртр – сила сухого трения, приложенная к поршню; р1 и р2 – давление рабочей жидкости в правой и левой полостях гидроцилиндра; р – перепад давления в гидроцилиндре; μ – коэффициент расхода; b – длина окна щели ротора распределителя; dр – диаметр ротора; рп – давление питания насоса гидроусилителя; ρ – плотность рабочей жидкости; rс – радиус начальной окружности сектора рейки-поршня; Ωс – угол поворота сошки; Тс –усилие в продольной тяге; hс – длина сошки; hк – длина поворотного рычага; Jк – момент инерции управляемых колес и жестко соединенных с ними деталей, приведенной к оси шкворня; kтр – коэффициент скоростного сопротивления в рулевом приводе, гидросистеме и шинах; cк – приведенная жесткость управляемых колес, включающая
36
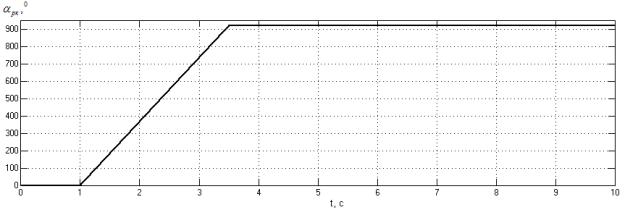
коэффициент стабилизирующего момента, возникающего вследствие наклонов шкворней, коэффициент момента сопротивления поворота управляемых колес при движении.
Управляющее воздействие в системе рулевого управления – угол поворота рулевого колеса представлено на рисунке 1. Управляющий сигнал действует на систему в течение 10 секунд, в начальный момент времени он равен 0. С момента времени, равному 1 секунде, угол поворота начинает возрастать, в момент времени 3,5 секунды, устанавливается на максимальном значении и становится постоянной величиной. Имитируется крутой поворот, водитель доводит рулевое колесо до упора и удерживает его в неподвижном положении.
На рисунке 2 представлен график расхода, поступающего в напорную полость гидроусилителя. В момент начала действия управляющего воздействия расход увеличивается до максимального значения. Когда угол поворота рулевого колеса перестает возрастать, расход плавно уменьшается до 0. В это время рулевое колесо неподвижно, необходимость поступления энергии гидравлической жидкости в гидроусилитель отсутствует, поршень усилителя останавливается. При крутом повороте автомобиля, когда водитель доводит рулевое колесо до упора и удерживает его, расход в гидроусилитель не поступает, так как наступает установившееся движение, рассогласование в системе, то есть угловое смещение роторного распределителя равно 0. Полученная характеристика позволяет определить расход насоса, требуемый для гидравлической системы.
По данному графику получено, что требуемая производительность насоса гидроусилителя руля должна составлять 16,8 л/мин. Следует отметить, что расчеты проводились на примере рулевого управления КАМАЗ-5308, производительность насоса гидроусилителя КАМАЗ-5308 составляет 16 л/мин. Применение в системе рулевого управления насоса гидроусилителя с меньшей производительностью нецелесообразно, так как в данном случае повышается вероятность возникновения значительного запаздывания поворота управляемых колес относительно поворота рулевого колеса. Это объясняется недостаточным количеством жидкости, поступающей в силовой цилиндр. Применение насоса гидроусилителя руля с большей производительностью приведет к излишне резкому включению гидроусилителя, а также к увеличению гидравлических потерь в гидросистеме и к перегреву масла.
На рисунке 3 представлена характеристика перемещения поршня гидроусилителя системы рулевого управления. При повороте автомобиля поршень начинает перемещаться и достигает своего максимального значения в момент установления максимального среднего угла поворота управляемых колес. Изменение среднего угла поворота управляемых колес представлено на рисунке 4. В момент времени 3,5 секунды при установившемся повороте поршень усилителя останавливается в крайнем положении. Данный график позволяет оценить ход поршня усилителя с нейтрального положения до крайнего при повороте рулевого колеса до упора.
Рис. 1. Угол поворота рулевого колеса
37
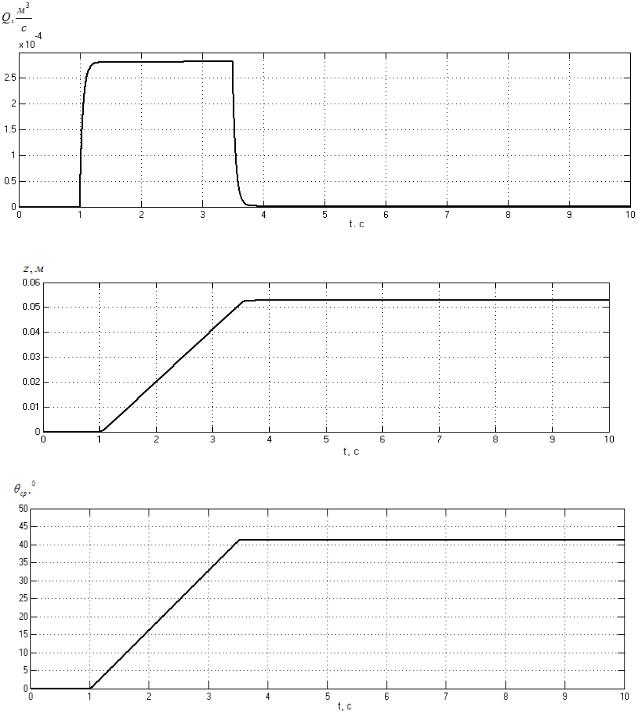
Рис. 2. Расход, поступающий в напорную полость гидроусилителя
Рис. 3. Перемещение поршня усилителя
Рис. 4. Средний угол поворота управляемых колес
Представленные виды характеристик, полученные при имитационном моделировании системы рулевого управления, позволяют на ранней стадии проектирования получить полную картину о работе системы и проанализировать функциональные свойства и поведение системы.
Библиографический список
1.Чайковский, И.П., Рулевые управления автомобилей / Саломатин П.А. – М.: Машиностроение,
1987. – 176 с.
2.Гинцбург, Л.Л. Гидравлические усилители рулевого управления автомобилей. – М.: Машиностроение, 1972. – 120 с.
3.Метлюк, Н.Ф. Динамика пневматических и гидравлических приводов автомобилей / Автушко В.П. – М.: Машиностроение, 1980. – 231 с.
38
УДК 629.113
РАЗРАБОТКА ТИПОРАЗМЕРНОГО РЯДА ПЕРСПЕКТИВНЫХ УНИФИЦИРОВАННЫХ СИНХРОНИЗИРОВАННЫХ МНОГОСТУПЕНЧАТЫХ КОРОБОК ПЕРЕДАЧ С АВТОМАТИЗИРОВАННЫМ УПРАВЛЕНИЕМ
Недялков1 А.Н., Блохин2 А.Н., Тумреев3 В.Ю., Фадеев3 А.С.
1- ГНЦ РФ ФГУП «НАМИ», 2 – НГТУ им. Р.Е. Алексеева, 3 – ООО «Ком-Проект»
В трансмиссиях автомобилей во всем мире наиболее массовое распространение получили механические ступенчатые синхронизированные коробки передач с фрикционным сцеплением, обладающие такими положительными качествами, как малый вес и габариты, высокая надежность и ресурс, низкая стоимость, высокие энергетические показатели, простота обслуживания и ремонта.
Для большинства грузовых автомобилей и тягачей автопоездов широко применяются многоступенчатые коробки передач, использование которых позволяет обеспечить высокие тягово-скоростные качества, снижение расхода топлива и улучшение экологических свойств. Такие коробки передач рационально использовать с автоматизированным управлением, которое в полной мере позволяет реализовать преимущества широкого диапазона передаточных чисел, создает более комфортные условия для водителя, повышает безопасность движения.
Основными тенденции развития современных механических коробок передач являются следующие [1, 2]:
1.Увеличение плотности ряда передаточных чисел на всем диапазоне коробки передач, что, прежде всего, имеет место в коробках передач автомобилей большой и особо большой грузоподъемности.
2.Увеличение диапазона передаточных чисел, определяющего предельные тяговые и скоростные показатели автомобиля. Это позволяет повышать тяговые качества автомобиля или автопоезда и одновременно уменьшать работу буксования сцепления, тем самым увеличивать надежность и долговечность его работы.
3.Применение новых конструктивных схем коробок передач, позволяющих обеспечить требуемое число передач. Это достигается использованием многоступенчатых коробок передач, имеющих сравнительно малое число шестерен и дополнительные приводные пары перед основным редуктором (делитель) или планетарный синхронизированный демультипликатор, устанавливаемый за основным редуктором, либо за счет применения так называемых комбинированных схем, включающих в себя как передний делитель, так и задний планетарный демультипликатор.
4.Применение новых конструкций малогабаритных энергоемких синхронизаторов с использованием молибденированных конусов трения, в том числе двухконусных.
5.Тенденция установки шестерен на валах на игольчатых подшипниках в сепараторах, что позволяет существенно повысить скоростной режим работы коробки передач, а также улучшить центрирование шестерен на валах. Данное конструктивное решение в сочетании со смазкой под давлением, что особенно необходимо для высоконагруженных коробок передач, обеспечивает гарантированно надежную работу этого узла.
6.Все возрастающее применение автоматизированного управления сцеплением и переключением передач. Практически все известные фирмы, как, например, ZF, Volvo, Mercedes-Benz, Scania, Renault, Eaton и др. устанавливают в виде штатного или по требованию заказчика автоматизированное электропневматическое управление коробками передач.
39