
новая папка / БЕЗОПАСНОСТЬ ТРАНСПОРТНЫХ СРЕДСТВ В ЭКСПЛУАТАЦИИ
.pdf
РКЦМП. Первое это – расчетное исследование силовых систем и элементов конструкций машин на соответствие требованиям пассивной безопасности и второе – расчетное определение параметров нагруженности несущих конструкций машин с последующей оценкой их долговечности.
Рис. 1. Наукоемкие компьютерные технологии проектирования машин
Расчетная оценка показателей прочности и жесткости конструкций.
В рамках работ по оценке пассивной безопасности транспортных средств в РКЦМП разработаны методики проведения виртуальных испытаний согласно следующим нормативным документам:
Правила ЕЭК ООН №: 29 (Пересмотр 1); 52; 58 (Пересмотр 2); 66; 73; 93.
СТБ ИСО 3471-2001 «Машины землеройные. Устройства защиты при опрокидывании. Технические требования и лабораторные испытания» (ISO 3471).
ГОСТ 12.2.002.2-91 «Тракторы сельскохозяйственные и лесные колесные. Метод статических испытаний защитных конструкций».
50

Необходимо отметить, что приведенные выше Правила ЕЭК ООН уже сегодня допускают замену натурных испытаний транспортных средств расчетными при условии их адекватности. Последнее достигается тщательной отработкой методик моделирования на основе анализа результатов натурных испытаний, в итоге которого выделяются наиболее значимые параметры компьютерных моделей, способы описания и задания граничных условий и свойств материалов.
Рассмотрим в качестве примера виртуальные испытания передних противоподкатных защитных устройств (ППЗУ) грузовых автомобилей (Правила № 93 ЕЭК ООН). Основные этапы методики расчета ППЗУ включают:
создание компьютерной геометрической модели ППЗУ с фрагментом рамы автомобиля;
создание конечно-элементной модели исследуемой конструкции;
наложение граничных условий, соответствующих экспериментальному закреплению конструкций и способу приложения нагрузок;
выполнение расчета (виртуальных испытаний);
анализ результатов расчета.
Базовым конструктивным элементом ППЗУ является противоподкатный брус,
который располагается в передней части транспортного средства симметрично относительно его продольной оси и крепится к лонжеронам рамы автопоезда при помощи системы кронштейнов сложной формы. Для иллюстрации сказанного на рис. 2 приведена установка конструкции ППЗУ автомобиля во время натурных испытаний и конечно-элементная модель, разработанная в программном комплексе конечно-элементного анализа ANSYS.
а) |
б) |
Рис. 2. |
Испытания ППЗУ грузового автомобиля |
а – экспериментальная установка (конструкция перевернута); б – конечно-элементная модель
Приведенная конечно-элементная модель включает |
|
|||
в общей сложности 42585 конечных элемента трех |
|
|||
различных типов, в том числе: 10-узловые квадратичные |
|
|||
конечные элементы четырѐхгранной формы и 20-узловые |
|
|||
конечные элементы шестигранной формы, а также |
|
|||
контактные элементы (3128 шт.). Суммарное число |
|
|||
узлов – 77253. |
|
|
|
|
Как видно из рис. 2 данная конструкция обладает |
|
|||
достаточно большим числом деталей соединенных с |
|
|||
использованием болтовых и заклепочных соединений. |
|
|||
Поэтому существенными особенностями такой модели |
|
|||
является необходимость определения способов описания |
Рис. 3. Нагрузки, |
|||
и параметров, во-первых – болтовых |
и заклепочных |
|||
прикладываемые к модели |
||||
соединений |
и, во-вторых – |
взаимодействия |
||
ППЗУ грузового автомобиля |
||||
контактирующих поверхностей. На рисунке 3 приведен |
||||
|
||||
|
|
51 |
|
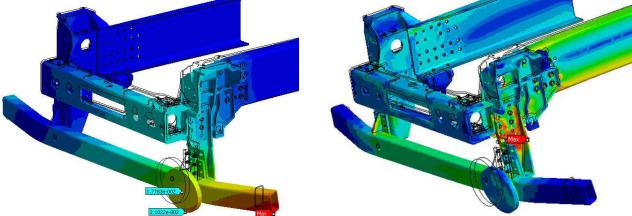
фрагмент модели с заданными и графически обозначенными силовыми воздействиями, моделирующими прикладываемую нагрузку и силы от затяжки болтовых соединений.
Результаты виртуальных испытаний в виде картины деформаций и распределения эквивалентных напряжений исследуемой конструкции приведены на рис. 4.
Максимальное перемещение ППЗУ в направлении продольной оси автомобиля имеет крайняя точка противоподкатного бруса. На конечной стадии моделирования, при действии усилия 160 кН, перемещение этой точки составило 23,2 мм. Максимальное перемещение по вертикали – 12,3 мм. Сравнение результатов моделирования с требованиями Привил №93 ЕЭК ООН показывает, что перемещения контрольных точек ППЗУ, полученные при моделировании, существенно меньше допускаемых пределов (анализ компоновочной схемы ППЗУ дает допустимые пределы перемещений в продольном направлении – 108 мм и в вертикальном направлении – 67 мм). Следовательно, конструкция ППЗУ удовлетворяет требованиям безопасности Правил № 93 в отношении проведенных виртуальных (расчетных) испытаний.
а) |
б) |
Рис. 4. Результаты виртуальных испытаний ППЗУ грузового автомобиля |
|
(величина нагрузки – |
160 кН): а – картина распределения перемещений; б – картина |
распределения эквивалентных напряжений
Необходимо отметить, что отработка методики виртуальных испытаний ППЗУ на соответствие требованиям Правилам №93 ЕЭК ООН выполнялась сразу в нескольких программных пакетах (LS-DYNA, MSC Nastran и ANSYS) для возможности выработки единых рекомендаций. Сопоставление результатов моделирования с данными натурных испытаний показали, что их отличие находится в пределах 10%. При этом виртуальная модель ведет себя несколько более податливой, чем натурный образец ППЗУ, что исключает риск завышения жесткости конструкции.
Расчетная оценка усталостной долговечности конструкций.
Продолжением вопроса расчетного прочностного анализа автотранспортных конструкций является оценка их долговечности, так как каждого производителя непосредственно интересует вопрос – обеспечит ли разрабатываемая конструкция предъявляемые к ней требования по ресурсу и на какой пробег можно гарантировать отсутствие ее отказов. Учитывая, что одной из основных причин выхода из строя несущих конструкций является накопление и развитие усталостных повреждений, то ниже приводится пример применения компьютерных трехногий при анализе причин разрушения конструкции оси прицепа со штампосварными опорами (далее – оси в сборе).
Конечно-элементная модель исследуемой конструкции была разработана в препроцессоре программного пакета конечно-элементного анализа ANSYS с применением оболочных элементов (штампосварная опора, рис. 6) и объемных элементов (труба оси, полуось и опорный диск, рис. 6). В связи с тем, что конструкция и все граничные условия имеют плоскость симметрии, создавалась только половина модели. К модели
52
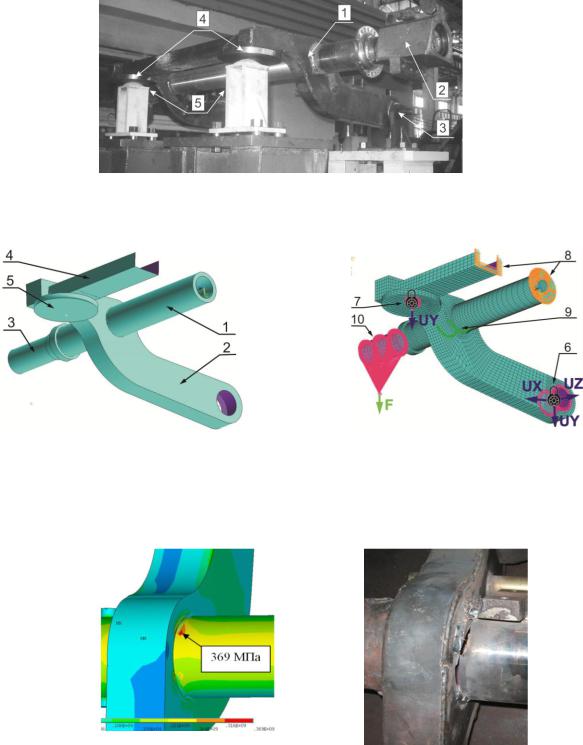
прикладывались граничные условия, соответствующие условиям проведения натурных испытаний. Моделирование сварного соединения стенки штампосварной опоры с трубой оси выполнялось с применением балочных элементов по методу, описанному в работе [1], а также с описанием сварного шва с использованием объемных конечных элементов.
Результаты расчета показателей прочности исследуемой конструкции позволили установить, что одной из наиболее нагруженных зон оси является окончание сварки на переходе стенка опоры – труба оси снизу (ближе к кронштейну крепления опоры), как показано на рис. 7. Этот результат полностью соответствует данный экспериментальных исследований.
Рис. 5. Установка экспериментальной конструкции на испытательном стенде 1 – ось в сборе со штампосварными опорами, 2 – захват для крепления гидроцилиндра,
3 – резинометаллический шарнир, 4 – опорные диски, 5 – сферические опоры
а) б) Рис. 6. Модель оси прицепа со штампосварными опорами
а– геометрическая; б – конечно-элементная
1– труба оси, 2– штампосварная опора, 3 – полуось, 4 – поперечина, 5 – опорный диск, 6, 7, 8 – граничные условия, 9 – узлы со связанными степенями свободы,
10 – наборы узлов, объединенные уравнениями связей
а) |
б) |
Рис. 7. Опасная зона оси в сборе (вид снизу) |
|
а – картина растягивающих напряжений расчет; б – разрушение в эксперименте
53
Входе экспериментальных исследований с целью оценки адекватности разрабатываемой модели реальной конструкции проводилось тензометрирование контрольных зон на трубе оси. Результаты сопоставления расчетных и экспериментальных данных растягивающих напряжений на трубе оси показали, что их отличие находится в пределах 5%. При расчете были получены более высокие значения напряжений.
Растягивающие напряжения в зоне, показанной на рис. 7, достигают 369 МПа. Однако, при анализе напряженно-деформированного состояния конструкций, содержащих модели сварных швов, для дальнейшей оценки усталостной долговечности в соответствии с работами [2,3] за основу должен быть принят характер распределения напряжений на некотором удалении от границы шва. Расчетными являются точки, расположенные на расстоянии 0,5 и 1,5 толщины металла свариваемых элементов от основания сварного шва. Для модели с «балочным» описанием сварного шва значения растягивающих напряжений в этих точках составляют 246 и 225 МПа, а в модели с объемным описанием – 237 МПа и 221 МПа. Учитывая, что значение коэффициент асимметрии для режима нагружения при стендовых испытаниях R=0,5, расчетные величины размаха напряжений для модели с описанием сварного шва на основе балочных и объемных элементов составляют 243,7 МПа и 232,7 МПа соответственно. Следуя рекомендациям по расчетной оценке усталостной долговечности [2] получены следующие значения числа циклов до наступления предельного состояния оси – 100 и 116 тыс. циклов для модели с описанием сварного шва на основе балочных и объемных элементов. Результаты стендовых испытаний трех конструкций показали среднюю наработку в 255 тыс. циклов. Учитывая, что полученные расчетные значения соответствуют достаточно высокой вероятности неразрушения – 97,6% [2], то полученный результат можно считать вполне удовлетворительным.
Врезультате дальнейших расчетных исследований был проанализирован ряд конструктивных решений штампосварной оси и определен вариант, позволяющие существенно повысить долговечность конструкции.
Заключение.
Подводя итоги приведенных выше примеров практической реализации виртуальных испытаний необходимо так же отметить, что на основе накопленных в РКЦМП данных по моделированию ППЗУ грузовых автомобилей была разработана Методическая инструкция по расчетным испытаниям, которая была согласована Государственным комитетом по стандартизации Республики Беларусь.
Приведенные результаты представляют собой только часть проделанных работ и являются красноречивым примером того, как компьютерные технологии моделирования и виртуальных испытаний автотракторной техники успешно занимают свою нишу в процессе разработки новых машин.
Библиографический список
1.Biaxial/Multiaxial fatigue and fracture. Editors: A. Carpitneri, M. Freitas, A. Spangnoli. Based on the papers presented at the 6th International Conference on Biaxial/Multiaxial Fatigue and Fracture / ESIS publication 31. ELSEVIER/ 2003. 516 p.
2.Design of steel structures. NORSOK standard N-004. Annex C. Fatigue strength analysis. December 1998, p. 213-488.
3.European standard. Eurocode 3: Design of steel structures. Part 1.9: Fatigue. – June 2004. – pp. 4-30.
54
УДК 629.113
ПРИМЕНЕНИЕ ВИРТУАЛЬНО – ФИЗИЧЕСКОЙ ТЕХНОЛОГИИ МОДЕЛИРОВАНИЯ ДЛЯ ПРОЕКТИРОВАНИЯ СИСТЕМ АКТИВНОЙ
БЕЗОПАСНОСТИ
В.Г. Дыгало, А.А. Ревин Волгоградский государственный технический университет
В настоящее время все производители стараются ускорить цикл проектирования колѐсных машин, одновременно совершенствуя модельный ряд, предлагая все более новые системы, упрощающие процесс управления колѐсной машиной в сложных режимах движения. В области проектирования и производства колѐсных машин за последние годы произошли очень серьезные изменения. Можно даже заключить, что цифровые технологии набрали в середине 90-х годов некую критическую массу, которая позволила почти всем крупным производителям разом совершить качественный скачок.
Конкурентная борьба вынуждает производителей все больше и больше сокращать сроки разработки и организации производства новых моделей. Кроме того, производимую продукцию необходимо сертифицировать согласно международным нормативам и требованиям.
Данное стремление приводит производителей к все большему усложнению систем, что влечет за собой вопрос о выявлении ошибок на ранних стадиях проектирования автомобиля.
Известно много случаев, когда новая модель, запущенная в серийное производство, отзывалась на завод или в сервисные центры для устранения недостатков допущенных при проектировании изделия. Данное явление особенно опасно в случае ошибок в системах активной безопасности, таких как тормозные.
Отечественные производители автотранспортных средств в последнее время активизировали работы по установке антиблокировочных систем (АБС) на свою продукцию. Известно, что основные требования к тормозным системам автомобилей с АБС определяют правила № 13 ЕЭК ООН (ГОСТ Р 41.13, ГОСТ Р 41.13Н). Внедрение АБС на конкретных типах автомобилей связано с определенными трудностями и материальными затратами, особенно остро проявляющимися на этапе доводки. Строительство собственных специальных полигонов для испытания тормозных автоматизированных систем чрезвычайно дорого из-за специальных требований к поверхности дороги. Следует признать, что полигонные испытания не являются идеальным средством для проведения доводочных работ и используются фирмами на этапе заключительной оценки, поскольку они не позволяют обеспечить высокую воспроизводимость условий испытаний автомобиля при оценке его свойств наиболее эффективным методом сравнения состояний. Это приводит к невозможности отслеживания влияния какой-либо отдельно взятой настройки блока управления АБС, структурной схемы или выбранного технического решения исполнительной части на процесс торможения в целом. Кроме того, новыми регламентами допускается проведение альтернативных испытаний при сертификации новых систем (приложение 21 к правилам 13 ЕЭК ООН).
Проведение испытаний на стендовом оборудовании в лабораторных условиях дает несомненные преимущества перед полигонными. Возможно обеспечение отличной воспроизводимости условий испытаний, а также обеспечение секретности разработок от посторонних глаз. Проведение испытаний в лаборатории не зависят от погодных условий и времени суток, что позволяет значительно сократить сроки разработки и адаптации новых систем. Однако современные стенды классического типа (роликовые, барабанные и ленточные) обеспечивающие скорость движения колѐсной машины свыше 100 км/ч довольно дорогостоящи и громоздки. Например, стенды, разрабатываемые для крупнейших автомобилестроительных концернов фирмой MTS, обходятся заказчику в сумму ~ 10 млн. $.
55
При разработке новых систем перед конструкторами встает вопрос апробирования принятых при проектировании решений.
Если рассмотреть цикл проектирования тормозных систем, то можно отметить, что несомненную помощь на определенных этапах оказывают комплексы CAD/CAE/CAM, но в случае проведения испытаний тормозных и других систем возможностей данных комплексов оказывается недостаточно.
Выходом из создавшейся ситуации является дальнейшее совершенствование стендового оборудования и методов испытаний, которые в рамках доводочных испытаний позволяют получить необходимую информацию о разработанной системе, оценить эксплуатационные свойства колѐсной машины с АБС в режиме торможения, выбрать оптимальную структуру управления тормозными механизмами.
Для подготовки к сертификации и проверки работоспособности систем колѐсной машины экономически целесообразно после этапа проектирования осуществлять проверку принципиальной правильности принятия решений на основе проведения комплексного моделирования систем и агрегатов колѐсной машины.
Проведенные с 70-х годов исследования в области комплексной технологии моделирования позволяют сделать вывод о возможности проведения виртуальных лабораторных испытаний новых образцов тормозных систем и проверки правильности принятых решений.
Например, несмотря на применение комплексов CAD/CAE/CAM на этапе функциональных испытаний, возможностей последних зачастую оказывается недостаточно при проектировании и отработки перспективных систем.
В настоящее время такой системой стала Электрогидравлическая тормозная система
(Electro-hydraulics breaking (EHB) system).
Для проведения поэлементных и комплексных испытаний Электрогидравлических тормозных систем (Electro-hydraulics breaking (EHB) system) в лаборатории и отработки принципов торможения по проводам (Break by Wire Technology), а также поиска путей снижения стоимости системы был создан испытательный стенд (рисунок 2) при построении которого были использованы принципы Комплексной технологии моделирования. Стенд разработан в результате сотрудничества кафедры Технической эксплуатации и ремонта автомобилей Волгоградского государственного технического университета (Россия), и кафедры Механики Туринского политехнического института (Италия)
Для обеспечения моделирования рабочих процессов EHB на стенд был установлен гидравлический блок Bosch ESP 5.7, блок электроклапанов от гидравлического блока Bosch ABS 5.3, передний тормозной механизм от автомобиля Alfa Romeo 166, гидроаккумулятор для поддержания высокого давления в системе, гидравлический цилиндр двустороннего действия подключенный к насосной станции для имитации нажатия на тормозную педаль с разными скоростями.
Вычислительная часть стенда построена на базе двух персональных компьютеров использующих MathLab/Simulink для построения модели на головном компьютере – сервере. Для обеспечения управления стендом и обработки сигналов в реальном масштабе времени использовалась операционная система реального времени MathWorks XPCtarget загружаемая на второй «целевой» компьютер оснащенный устройствами сопряжения объектов.
Перед проведением испытаний модель компилируется и загружается на «целевой» компьютер, который после запуска процесса моделирования выполняет управление стендом и осуществляет сбор и обработку данных автономно.
Расчет модели и работа стенда проводились с временным интервалом 0,001 с в реальном масштабе времени за счет применения операционной системы реального времени. Для коммутации, обеспечения работы клапанов гидравлического блока и возможности изменения алгоритма работы разработана и изготовлена оригинальная коммутационная аппаратура. В качестве электрических переключателей клапанов гидравлического блока применялись реле фирмы CRYDOM с временным интервалом работы 0,001 с.
56
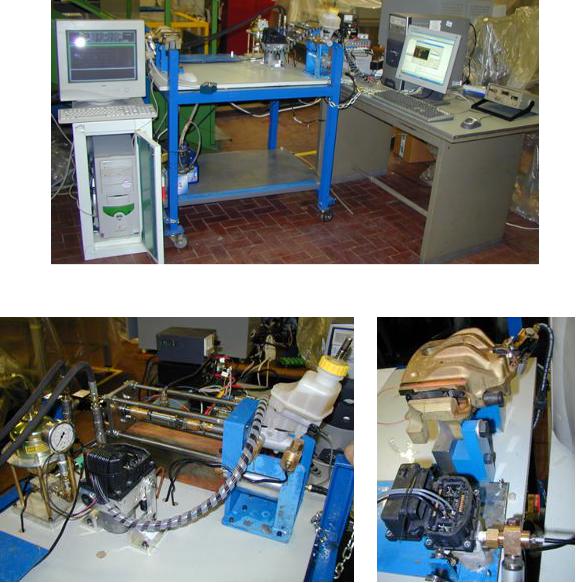
Рис. 1. Внешний вид стенда для испытаний Электрогидравлических тормозных систем
(Electro-hydraulics breaking (EHB) system)
Рис. 2. Вид монтажа гидравлического блока Bosch ESP |
Рис. 3. Вид монтажа тормозного |
5.7, гидроаккумулятора высокого давления, |
механизма и клапанов |
гидроцилиндра, главного тормозного цилиндра и |
гидравлического блока |
эмулятора усилия педали |
Bosch ABS 5.3 |
Система датчиков подключена к двум платам производства National Instruments, для аналого/цифрового преобразования сигналов датчиков стенда и передачи управляющих сигналов на стенд.
Необходимо отметить, что данные результаты были достигнуты с использованием элементов стандартных, серийно выпускаемых и широко используемых систем Bosch ESP 5.7
иBosch ABS 5.3. Это позволяет предположить, что в недалеком будущем возможно широкое применение Электрогидравлических тормозных систем на более доступных для потребителя автомобилях.
Таким образом, данный стенд позволяет проводить полный цикл испытаний Электрогидравлических тормозных систем (ЕНВ) и отработки логики работы блока управления в лабораторных условиях, позволяя находить пути снижения стоимости системы
исокращать затраты на проведение функциональных испытаний.
Однако, после проведения функциональных испытаний, для запуска новой модели системы автомобиля в серийное производство, необходимо проведение большого количества доводочных испытаний, в ходе которых ведется проверка на соответствие нормативным требованиям, как автомобиля в целом, так его отдельных узлов и агрегатов. Дорожные
57
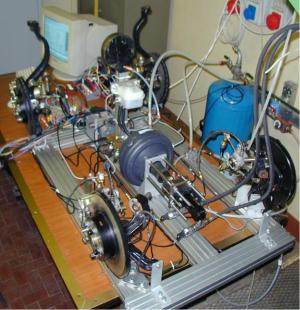
|
испытания |
являются |
|
наиболее |
|
||||
|
|
|
|||||||
ресурсоемкими |
и |
дорогими. |
Причем |
|
|||||
проведение |
данного |
вида |
|
испытаний |
|
||||
возможно |
|
лишь |
|
на |
специально |
|
|||
оборудованных для этого полигонах (На |
|
||||||||
территории РФ – НИЦИАМТ г. Дмитров, 21 |
|
||||||||
НИИ МО г. Бронницы). К тому же дорожные |
|
||||||||
испытания являются и самыми опасными как |
|
||||||||
для водителя оператора – испытателя, так и |
|
||||||||
для дорогостоящей измерительной техники, |
|
||||||||
не говоря уже о самой исследуемой колѐсной |
|
||||||||
машине. Являясь основным критерием |
|
||||||||
правильности |
принятых |
технических |
|
||||||
решений, вместе с тем, дорожные испытания |
|
||||||||
не |
позволяют |
добиться |
|
идеальной |
|
||||
воспроизводимости |
условий |
проведения |
|
||||||
эксперимента, т.к. параметры дорожного |
|
||||||||
полотна и |
окружающие |
условия |
в разные |
|
|||||
Рис. 4. Внешний вид стенда для испытаний |
|||||||||
|
|
|
|
|
|
|
|
||
временные отрезки не совпадают. Вследствие |
систем активной безопасности |
этого довольно трудно, а порой и невозможно, например, отследить влияние какого либо из параметров настройки блока управления
системой. При проведении дорожных испытаний в условиях жесткой конкуренции появляется новая проблема – защита новых моделей и разработок от посторонних «глаз» конкурентов.
Ниже кратко приведены примеры систем для исследования полнокомплектных систем активной безопасности в лаборатории. Стенд (рис. 4) реализованный в лаборатории Туринского политехнического института (Politecnico di Torino, Torino, Italy) стал результатом очередного научного сотрудничества исследовательских групп ВолгГТУ и ТПИ. Данный стенд базируется на агрегатах Alfa-Romeo 157 mod. и позволяет проводить испытания полнокомплектных систем активной безопасности, как ABS, так и ESP.
Программное обеспечение стенда реализовано с помощью MathLab/Simulink. Технической особенностью стенда стало применение специализированной платы УСО dSPACE DS1103.
Ниже приведены результаты испытаний систем Bosch ABS 5.3 и Bosch ESP 5.7 а также оптимизации разработанных алгоритмов работы систем ABS и ESP.
При проведении испытаний использовались различные технические решения подключения блоков. Так, для верификации работы стенда использовалась электронная начинка блоков Bosch ABS 5.3 и Bosch ESP 5.7, а для отработки собственных алгоритмов использовалось непосредственное подключение к клапанам гидроблока.
Проведение испытаний в лаборатории позволяет добиться прекрасной воспроизводимости испытаний и защитить новые разработки.
Выполнение данных исследований возможно на специальном стенде, позволяющем имитировать управляющие воздействия водителя и реакцию на них автомобиля, а также обратное действие – исследование физиологической реакции на человека посредством механизмов управления поскольку согласно требований правил № 13 ЕЭК ООН водитель может корректировать траекторию движения автомобиля в процессе торможения.
Для реализации выдвигаемых выше положений в ВолгГТУ (в соответствии с Научнотехнической программой – «Научные направления высшей школы по приоритетным направлениям науки и техники», подпрограмма 205 Транспорт, раздел научно-технической программы 205.03 Наземные транспортные средства, тема 205.03.01.14 «Разработка стендатренажера для испытания автомобилей с АБС в режиме торможения») разработан имитационный стенд-тренажер, который показан на рисунке 8. Стенд включает следующие
58

основные узлы и блоки: соединенных в сеть три персональных компьютера; стенд с физической моделью тормозной системы легкового автомобиля, выполненной на основе реальных агрегатов тормозного привода и элементов АБС; устройство для моделирования тактильных воздействий на рулевое колесо; устройство сопряжения объектов; энергетическую и измерительную систему стенда.
а |
б |
в |
г |
д |
е |
Рис. 5. Вид элементов стенда для испытаний систем активной безопасности:
а– управляющий ПК с платой dSPACE DS1103; б – привод ГТЦ (имитатор ноги водителя);
в– плата сопряжения; г – насосная станция; д – гидроблок системы активной безопасности;
е– тормозной механизм
59