
новая папка / БЕЗОПАСНОСТЬ ТРАНСПОРТНЫХ СРЕДСТВ В ЭКСПЛУАТАЦИИ
.pdf
Рис. 2. Исходная модель двухэтажного пассажирского вагона с вырезом четверти
Система включает в себя дополнительные эвакуационные выходы в полу коридора первого этажа (рис.3 а), на боковой стене (рис.3 б) и крыше коридора второго этажа (рис.3 в).
Эвакуационные выходы на крыше (рис.3 а) и в полу (рис.3 в) предназначены для обеспечения эвакуации пассажиров при опрокидывании вагона на боковую стену и имеют размеры 600 730 мм. Выходы выполнены в виде люков с крышками, оборудованными специальным запорным устройством, обеспечивающими беспрепятственное их сбрасывание в аварийной ситуации.
а
Рис. 3. Усовершенствованная модель двухэтажного пассажирского вагона с вырезом четверти. Эвакуационные выходы: а – в крыше, б – в боковой стене, в – в полу
Для эвакуации пассажиров второго этажа из вагона в вертикальном положении предусмотрены два эвакуационных выхода в зоне коридора на боковой стене (рис. 3 б), оборудованных приспособлениями для быстрого и безопасного спуска пассажиров и обслуживающего персонала на земляное полотно. Выходы на боковой стене образуются при
70

удалении подоконной зоны и стеклопакета специальным механизмом, приводимым в действие изнутри вагона.
На основе исходной конечно-элементной модели кузова вагона выполнена усовершенствования модель (рис. 3). Соответствующая конечно-элементная модель кузова (рис. 3) имеет близкое к исходной (рис. 2) число степеней свободы. Расположение люков и их размеры приняты исходя из обеспечения минимального времени эвакуации пассажиров, в том числе и травмированных с использованием специальных средств спасения (рис. 4).
Рис. 4. схема расположения аварийных выходов на первом и втором этажах: 1 – окно, 2 – купе, 3 – простенок, 4 – аварийный выход, 5 – коридор,
6– рециркуляционный воздуховод
Оценка адекватности предложенной модели была подтверждена данными натурных испытаний. Анализ напряженно деформированного состояния несущей конструкции кузова от действия нормативных нагрузок показал, что наличие в конструкции кузова дополнительных вырезов в виде люков не значительно влияют на ее несущую способность, что подтверждает возможность реализации предложенной системы эвакуации пассажиров.
Применение предлагаемой системы позволит сократить время самостоятельной эвакуации пассажиров в 1,6 раза, эвакуации травмированных пассажиров силами поездной бригады в 2,7 раза и силами страдников спасательных служб 1,9 раза.
Библиографический список
1.Технический регламент «О безопасности железнодорожного подвижного состава» Утвержден Правительством РФ 15.07.2010.
2.Bukowski, R.W., et al. Development of a Hazard Assessment-Based Method for Evaluating the Fire Safety of Passenger Trains. Paper presented a the 7th International Conference on Fire and Materials. January 22-24, 2001. San Francisco, CA.
3.Train Evacuation Risk Model: A report for Railway Safety Ltd, Rail Safety and Standards Board Evergreen House 160 Euston Road London. June 2002
71
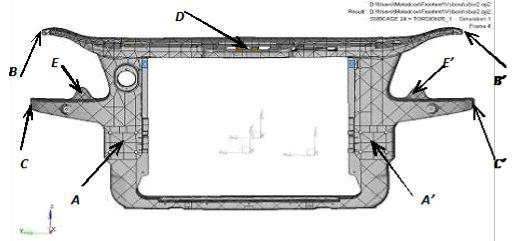
УДК 629.113
ИСПОЛЬЗОВАНИЕ РАСЧЕТНЫХ МЕТОДОВ ПРИ ПРОЕКТИРОВАНИИ И ОПТИМИЗАЦИИ КОНСТРУКЦИИ ФРОНТ-ЭНДА
Карев Р.В., Молодцов А.С.
ООО «ОИЦ»
Рамка радиатора (фронт-энд) – элемент кабины автомобиля, выполняющий ряд функций: несущую, жесткостную, эстетическую.
Несущая функция рамки радиатора заключается в установке на неѐ элементов различных систем автомобиля. При этом должно быть обеспечено выполнение требований к жесткости конструкции, надежности установки узлов в различных условиях эксплуатации автомобиля. В этом заключается ее жесткостная функция. Кроме этого, рамка радиатора должна полностью вписываться в общую структуру дизайна автомобиля и обеспечивать его эстетическое восприятие.
По конструкционному исполнению рамки радиатора можно разделить на три типа: металлические, состоящие из отдельных частей (сварные или сборные), цельные пластиковые и пластиковые с местными металлическими вставками, обеспечивающими требуемые показатели прочности.
В данной работе рассматривается рамка радиатора нового проектируемого автомобиля. Планируемый материал детали – композитный материал на основе полипропилена, обеспечивающий высокую жесткость конструкции и малые деформации при тепловых нагрузках. Фронт-энд (рис.1) выполнен как единая деталь. На восьми болтах (точки А, А’) рамка радиатора крепится к нижним лонжеронам кабины, а в точках В и В’ – к верхним усилителям кабины.
С, С’ – места крепления передних крыльев кузова и боковин бампера на фронт-энд. Кроме того, на нем устанавливаются фары (точки Е и Е’) и радиатор, а также осуществляется крепление всех элементов переднего пластикового бампера. Таким образом, фронт-энд выполняет несущую функцию для элементов кузова.
Рис. 1. Общий вид фронт-энда
В работе описываются методика расчета прочности и жесткости конструкции в различных эксплуатационных условиях, а так же разрабатывается методика оптимизации конструкции.
Определение конструктивных требований и постановка задачи.
Разработка пластикового фронт-энда – это эффективное решение как в плане улучшения потребительских свойств автомобиля, так и в плане конструкторского опыта. Это передовая технология в мировом и инновация в отечественном автопроме.
72
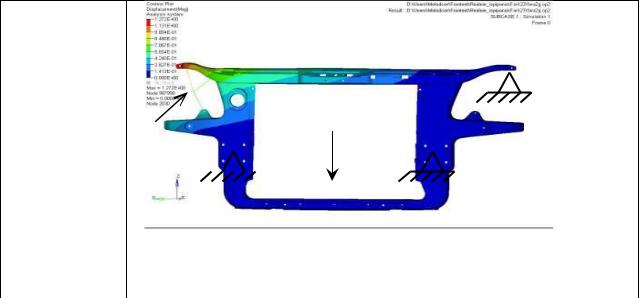
Отсутствие опыта проектирования подобных деталей заставляет разрабатывать новые методики расчета, в том числе и при сотрудничестве с другими компаниями. На основе анализа существующих аналогов и данных, предоставленных партнерами.
Исходя из конструктивных особенностей рамки радиатора и автомобиля в целом, были определены основные требования по жесткости (таблица 1) и прочности.
Таблица 1
Требования к конструкции фронт-энда по жесткости
Конструктивные показатели |
Ориентировочные значения |
Перемещения точек крепления фары |
<0,25 мм |
Перемещение точек крепления радиатора |
<0,25 мм |
Изменение ориентирных диагоналей |
<0,75 мм |
Прочность конструкции определяется механическими свойствами материала. Ориентировочный материал фронт-энда – полипропилен, армированный стекловолокном. Однако, моделирование армированного материала применительно в рамке радиатора достаточно условно, т.к. свойства материала зависят от конечной ориентации волокон в детали. Поэтому, для материала задаются изотропные свойства.
Свойства материала:
–плотность 1120 кг/м3
–коэффициент Пуассона 0.3
|
-40°С |
23°С |
80°С |
120°С |
модуль упругости |
7800 МПа |
4900 МПа |
3400 МПа |
2700 МПа |
предел прочности |
101 МПа |
78 МПа |
54 МПа |
39 МПа |
Анализ фронт-энда при локальных нагрузках.
В ходе работы были определены наиболее характерные расчетные схемы для фронтэнда. Схемы и результаты их анализа приведены в таблице 2.
Анализ фронт-энда в составе автомобиля.
Следующим этапом работы были расчеты фронт-энда в составе автомобиля. Фронтэнд был включен в состав конечно-элементной модели автомобиля. Были проведены расчеты стандартных схем нагружения: свес переднего колеса, двойная гравитационная перегрузка, экстренное торможение. Расчеты проводились при характеристиках материала, соответствующих температуре 80°С. Были установлены «датчики» для измерения изменения расстояния между характерными точками. Результаты приведены в таблице 3.
Таблица 2
Результаты анализа фронт-энда
1. Воздействие |
|
|
|
фары при |
|
|
|
двойной |
А |
||
вертикальной |
|
|
2g |
перегрузке |
|
|
|
|
|
|
|
|
|
|
|
Температура |
Максимальная |
Максимальное |
Допустимая |
Допустимые |
|
деформация, |
напряжение, σmax |
напряжения, σf |
|||
расчета |
деформация (мм) |
||||
max (мм) |
(МПа) |
(МПа) |
|||
|
|
||||
23°C |
0.38 |
2.07 |
0.25 |
78 |
73
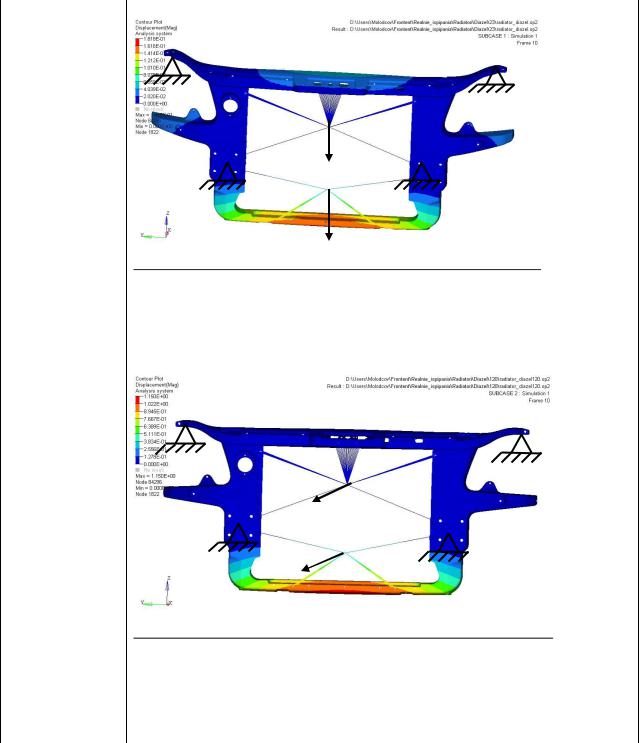
80°С |
0.55 |
2.07 |
0.25 |
54 |
2. Воздействие |
|
|
|
радиаторов при |
|
|
|
двойной |
|
|
|
вертикальной |
А |
|
|
перегрузке |
2g |
||
|
|||
(дизельный |
В |
|
|
двигатель) |
|
||
|
2g |
||
|
|
Температура |
Перемещение |
Максимальное |
Допустимая |
Допустимые |
|
ц.м. радиатора, |
напряжение, σmax |
напряжения, σf |
|||
расчета |
деформация (мм) |
||||
max (мм) |
(МПа) |
(МПа) |
|||
|
|
||||
23°C |
0.06 |
2.96 |
0.25 |
78 |
|
80°C |
0.09 |
2.96 |
0.25 |
54 |
|
120°C |
0.1 |
2.96 |
0.25 |
39 |
3. Воздействие |
|
|
|
радиаторов при |
0.8 |
А |
|
экстренном |
|||
|
|
||
торможении |
|
|
|
(дизельный |
|
|
|
двигатель) |
0.8 |
В |
|
|
|
Температура |
Максимальная |
Максимальное |
Допустимая |
Допустимые |
|
деформация, |
напряжение, σmax |
напряжения, σf |
|||
расчета |
деформация (мм) |
||||
max (мм) |
(МПа) |
(МПа) |
|||
|
|
||||
23°C |
0.22 |
5.68 |
|
78 |
|
80°C |
0.32 |
5.68 |
|
54 |
|
120°C |
0.36 |
5.68 |
|
39 |
Разработка методики оптимизации конструкции фронт-энда.
Основные цели оптимизации конструкции:
–обеспечение требуемой жесткости. Проведенные расчеты показали, что первая генерация конструкции фронт-энда на некоторых режимах имеет отклонение требований по жесткости.
–оптимизацию конструкции возможно провести с уменьшением массы фронтэнда со снижением его стоимости.
–выполнение требований по прочности. Изменение конструкции не должно привести к ухудшению ее прочностных характеристик.
74

Таблица 3
|
E |
D |
E |
|
|
|
|
B |
F |
|
F |
|
|
B |
|
|
|
|
C C
A A
A (A’) – крепление на лонжероне,
B (B’) – крепление «на руке»,
C (C’) – крепление крыла,
D – крепление замка капота,
E (E’) – верхнее наружное крепление фары,
F (F’) – нижнее крепление фары
|
|
|
σmax |
|
|
|
|
σf |
|
|
|
||
1. Свес левого |
|
|
15.63 |
|
|
|
|
50 |
|
|
|
||
|
|
Относительные деформации фронтенда*, (мм) |
|
|
|||||||||
колеса |
|
|
|
|
|||||||||
EF |
E’F’ |
AB’ |
A’B |
AD |
A’D |
BD |
B’D |
AC’ |
|
A’C |
BC’ |
B’C |
|
|
|
||||||||||||
|
0.66 |
-0.64 |
0.62 |
-0.6 |
0.24 |
-0.26 |
-0.84 |
0.8 |
0.05 |
|
-0.06 |
-0.49 |
0.44 |
|
|
|
σmax |
|
|
|
|
σf |
|
|
|
||
2. Свес правого |
|
|
15.54 |
|
|
|
|
50 |
|
|
|
||
|
|
Относительные деформации фронтенда*, (мм) |
|
|
|||||||||
колеса |
|
|
|
|
|||||||||
EF |
E’F’ |
AB’ |
A’B |
AD |
A’D |
BD |
B’D |
AC’ |
|
A’C |
BC’ |
B’C |
|
|
|
||||||||||||
|
|
|
|
|
|
|
|
|
|
|
|
|
|
|
-0.69 |
0.72 |
-0.65 |
0.65 |
-0.25 |
0.26 |
0.89 |
-0.86 |
-0.06 |
|
0.07 |
0.53 |
-0.48 |
|
|
|
|
|
|
|
|
|
|
|
|
|
|
|
|
|
σmax |
|
|
|
|
σf |
|
|
|
||
3. Двойная |
|
|
11.40 |
|
|
|
|
50 |
|
|
|
||
вертикальная |
|
|
Относительные деформации фронтенда*, (мм) |
|
|
||||||||
перегрузка |
EF |
E’F’ |
AB’ |
A’B |
AD |
A’D |
BD |
B’D |
AC’ |
|
A’C |
BC’ |
B’C |
|
0.09 |
0.09 |
-0.02 |
-0.1 |
-0.12 |
-0.16 |
-0.07 |
0.04 |
-0.12 |
|
-0.12 |
-0.05 |
0.01 |
|
|
|
|
|
|
|
|
|
|
|
|
|
|
|
|
|
σmax |
|
|
|
|
σf |
|
|
|
||
4. Экстренное |
|
|
18.52 |
|
|
|
|
50 |
|
|
|
||
|
|
Относительные деформации фронтенда*, (мм) |
|
|
|||||||||
торможение |
|
|
|
|
|||||||||
EF |
E’F’ |
AB’ |
A’B |
AD |
A’D |
BD |
B’D |
AC’ |
|
A’C |
BC’ |
B’C |
|
|
|
||||||||||||
|
|
|
|
|
|
|
|
|
|
|
|
|
|
|
-0.42 |
-0.56 |
-0.45 |
-0.52 |
-0.02 |
-0.19 |
0.09 |
0.13 |
-0.28 |
|
-0.21 |
-0.23 |
-0.07 |
|
|
|
|
|
|
|
|
|
|
|
|
|
|
Возможные направления оптимизации конструкции:
–изменение толщин корки или/и ребер;
–изменение конструкции (формы корки, расположения ребер, введение дополнительных ребер);
–интегрированный метод, включающий в себя изменение целого набора параметров.
Блок-схема процесса оптимизации конструкции фронт-энда показана на рис.2
75
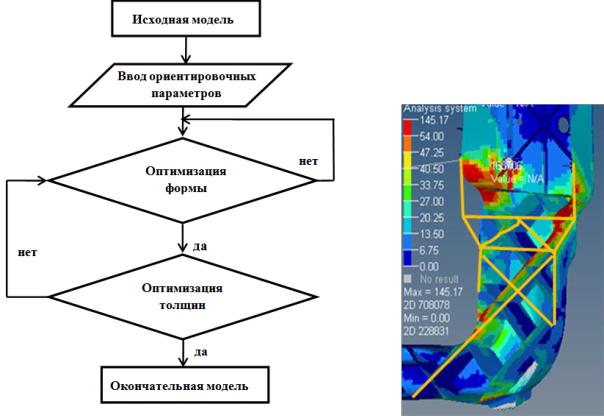
Рис. 2. Блок-схема процесса оптимизации конструкции |
Рис. 3. Пример оптимизация |
фронт-энда |
конструкции фронт-энда |
Геометрические параметры модели были выбраны переменными. Основной параметр
– масса модели. Ограничивающие параметры – напряжения в элементах и перемещение основных точек конструкции.
Таким образом, целью оптимизации является уменьшение массы модели за счет изменения ее геометрии при соблюдении прочностных и жесткостных требований.
На рис.3 показан пример изменения формы корки фронт-энда и положения его ребер. Как уже отмечалось выше, рассмотренный нами модуль является принципиально
новым для нашего предприятия.
–В ходе проектирования фронт-энда были определены и использовались расчетные схемы, определяющие характеристики модели и позволяющие уже на стадии проектирования разработать наиболее оптимальную конструкцию.
–Были проведены расчеты фронт-энда как при локальных нагрузках, так и в составе автомобиля. Анализ полученных результатов определил главные направления оптимизации конструкции.
–Была разработана принципиальная схема оптимизации конструкции. Были определены основные параметры оптимизации.
–Были определены направления дальнейших исследований в области проектирования пластикового фронт-энда:
испытания и расчеты существующей модели фронт-энда,
более полное определение режимов нагружения,
разработка методики оптимизации конструкции фронт-энда.
76
УДК 629.113
ОЦЕНКА УСТАЛОСТНОЙ ДОЛГОВЕЧНОСТИ КУЗОВА АВТОБУСОВ НЕФАЗ-5299
Хабибуллин Р.Г., Галимянов И.Д., Салахов И.И. Камская государственная инженерно - экономическая академия
Анализ статистической информации об эксплуатационных повреждениях кабин грузовых автомобилей и автобусов городских и междугородних сообщений показывает, что усталостные трещины несущих элементов, являются основным видом повреждения их конструкции. Из-за сложности конструкции автобусов и неопределенности, действующих на них нагрузок, наиболее эффективным методом оценки усталостной долговечности и ее повышения, является расчетно-экспериментальный метод. При этом существует два подхода:
а) испытание натурной конструкции кузова в составе автобуса; б) испытание и доводка отдельных несущих узлов кузова.
Исследование натурных узлов кузова в условиях эксплуатации или при имитации нагрузок в лаборатории дает возможность оценить напряженно-деформированное состояние кузова, выявить потенциально опасные с точки зрения сопротивления усталости, места конструкции и получить для них нагрузочные режимы, необходимые для проведения расчетов и разработки режимов испытаний кузова на усталостную долговечность. Но эти исследования не позволяют проводить детальный анализ предельных состояний различных вариантов конструктивно-технологического исполнения узлов кузова и находить оптимальный.
К расчетной оценке усталостной долговечности можно приступить тогда, когда имеются следующие данные:
а) спектр напряжений в виде гистограммы гармонических колебаний i |
ni , |
получаем схематизацией (лучше всего методом «стекающего дождя») записей процессов изменения напряжений в критическом месте конструкции при эксплуатационных режимах
работы автобуса; где i - амплитуда или размах напряжений, а ni - |
их количество в i -ых |
интервалах гистограммы, i 1,2...k. |
|
б) кривая усталости критического места конструкции |
i Ni , полученная |
экспериментально (или хотя бы расчетом), где Ni количество циклов нагружения до разрушения конструкции при уровне напряжения i .
Если был получен спектр напряжений i ni при движении автобуса по дорогам (y=1,2…) определенной протяженности Li км, тогда накопленное усталостное повреждение
от этих спектров напряжений по отдельности в соответствии с линейной гипотезой суммирования Пальмгрена-Майнера будет равно:
k |
ni |
|
|
|
Di |
. |
(1) |
||
|
||||
i 1 |
Ni |
|
Накопленное усталостное повреждение конструкции при движении автобуса по блоку типичных дорог эксплуатации принятой протяженности Ltip может быть подсчитано
включением в сумму повреждений, полученных при движении по отдельным видам дорог в соответствии с вероятностью Pi работы автобуса на этих дорогах (y=1,2…) в течении всего
срока эксплуатации Lt :
k |
Ltip |
|
|
|
Dtip Pi Di |
. |
(2) |
||
|
||||
i 1 |
L |
|
||
t |
|
|||
Количество повторений блока типичных дорог |
q в течении срока службы автобуса |
определяется из следующего отношения:
77
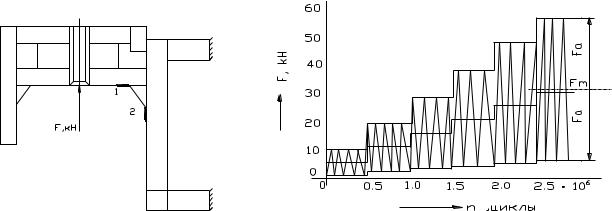
q |
D |
, |
(3) |
|
|||
|
Dtip |
|
|
а средняя долговечность конструкции в км. пробега |
|
||
L Ltip q . |
(4) |
Здесь D - предельная величина накопленного усталостного повреждения (в соответствии с линейной гипотезой суммирования D 1).
Пример использования изложенного подхода для оценки усталостной долговечности. В качестве объекта испытаний была взята часть кузова автобуса НЕФАЗ-5299 в месте крепления подвески заднего моста (рис.1).
Рис. 1. Конструкция узла крепления |
Рис. 2. Нагрузочный блок испытываемого |
пневмобаллона |
узла кузова |
подвески заднего моста автобуса |
|
Определяющими нагрузками, действующими на эту часть кузова в эксплуатации, являются вертикальные нагрузки F от пневмобаллона подвески моста.
Статические испытания показали, что наибольшие напряжения действуют в местах наклейки тензодатчиков 1 и 2 (в месте приварки усилительной косынки несущей фермы основания кузова). При испытаниях на усталость по блок - программе нагружения (рис.2.).
На четвертом уровне нагрузки в вертикальной стойке основания кузова (датчик 2) появилась усталостная трещина. При дальнейшем циклическом нагружении трещина быстро развивалась вдоль сварного шва соединения стойки с усилительной косынкой. Возникновение трещины однозначно подтвердило результаты статических испытаний о наличии высокой концентрации напряжений в этом месте, и неблагоприятном влиянии термического воздействия сварки.
Для критического места стойки у тензодатчика 2 расчетным путем были определены пределы выносливости на базах 5 106 и 1 107 циклов нагружения. При этом показатели угла наклона кривой усталости m были приняты равными, соответственно 4 и 5. Пределы выносливости 1 составили, соответственно 40 и 50 МПа. При движении испытуемого
автобуса по модельной дороге (с переездом через стандартное препятствие, см. рис.2) в критическом месте узла кузова были замерены амплитуды пиковых (резонансных) напряжений, которые оказались несколько выше пределов усталости. Для более глубокого анализа эксплуатационных напряжений было произведено их измерения на четырѐх характерных видах покрытия дорог городского маршрута с различным покрытием:
I.гладкая асфальтированная дорога;
II.щебеночная дорога с покрытием хорошего качества;
III. щебеночная дорога с покрытием удовлетворительного качества; IV. разбитая щебеночная дорога;
78
Через участок каждой дороги, длиной 500 м исследуемый автобус проезжал несколько раз в обоих направлениях (туда и обратно). Полученные записи процессов изменения напряжений в критическом месте конструкции кузова были схематизированы методом «стекающего дождя» (приведены к эквивалентному блоку гармонического нагружения). Количество циклов нагружения пересчитано на пробег автобуса Ltip равный 1000 км. В
таблице 1 приведены накопленные усталостные повреждения конструкцией узла Di при
движении автобуса по каждой из четырѐх типов дорог. Из таблицы 1 видно сильное влияние качества покрытия дороги на усталостное повреждение. При эксплуатации автобуса на дорогах с щебеночным покрытием низкого качества ресурс узла оказался ниже требуемого (500 тыс. км пробега). В связи с этим конструкция узла кузова была усилена. Применена стойка кузова с большей толщиной и снижена концентрация напряжений за счет недоведения сварных швов до кромок усилительной косынки на 5 мм. Это позволило добиться требуемого ресурса исследуемого узла кузова.
Таблица 1
Накопленные усталостные повреждения в критическом месте узла кузова при движении автобуса по дорогам с различным покрытием, протяженностью 1000 км
|
Накопленное усталостное повреждение |
|||
Тип |
|
|
|
|
Нижнее |
Верхнее |
|||
дорожного |
||||
( m=4,N0=107, -1=40МПа) |
(m=5,N0=5 106, -1=50МПа) |
|||
покрытия |
||||
|
|
|
||
I |
9,4562 10-7 |
2,0734 10-8 |
||
II |
7,4503 |
10-4 |
1,5201 10-4 |
|
III |
1,4102 |
10-3 |
3,2823 10-4 |
|
IV |
1,4605 |
10-2 |
9,7295 10-3 |
Библиографический список
1.Павленко А.П. Подход к решению задачи обеспечения требуемой долговечности кузова автобуса / И.Д. Галимянов, Л.И. Кухаренко // Проблемы исследования и проектирования машин. II Международная научно-техническая конференция. Пенза, 2007. - С. 87-95.
2.Хачатуров, А.А. Динамика системы дорога - шина - автомобиль - водитель / Под ред. А.А. Хачатурова. - М.: Машиностроение, 1976. - 535 с.
УДК 629.113
ОСОБЕННОСТИ МОДЕЛИРОВАНИЯ НАГРУЖЕНИЯ КУЗОВА В УСЛОВИЯХ ОПРОКИДЫВАНИЯ АВТОБУСА
Рогов П.С., Орлов Л.Н., Тумасов А.В.
Нижегородский государственный технический университет им. Р.Е. Алексеева
Показаны результаты расчѐтной оценки пассивной безопасности автобусов. Выполнены расчетные исследования деформируемости секций кузова в условиях опрокидывания автобуса. Рассмотрены варианты моделирования условий нагружения. Показаны их преимущества и недостатки.
Проблема снижения тяжести последствий дорожно-транспортных происшествий (ДТП) является весьма актуальной для мирового сообщества. Известно, что опрокидывание является одним из наиболее опасных видов ДТП, хотя происходит оно не так часто в сравнении с лобовым или боковым столкновениями. Повышение пассивной безопасности автобусов в большей мере зависит от создания прочных и безопасных кузовов. Кузов автобуса должен поглощать энергию удара и сохранять необходимое жизненное пространство для пассажиров. Эти требования регламентированы Правилами ЕЭК ООН
79