
новая папка / БЕЗОПАСНОСТЬ ТРАНСПОРТНЫХ СРЕДСТВ В ЭКСПЛУАТАЦИИ
.pdf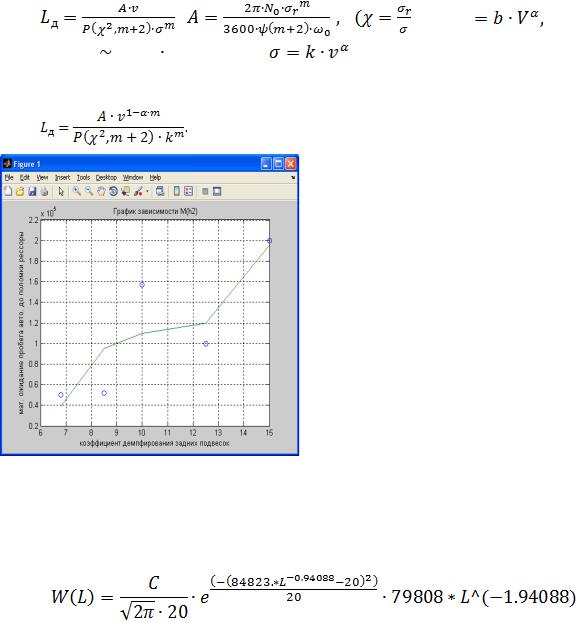
, |
|
), |
S |
|
|
|
|
σ(Н/м2 ) 0,0026 S (м); То есть |
, где k=0.0026*b, m=3.3 |
|
|
||||
(3.3 2) 3.1383 2.65 4.6604 |
|
|
|
|
|
|
|
При подстановке (2) в (1) получаем: |
|
|
|
|
|
|
|
|
В настоящее время при эксплуатации |
||||||
|
в хороших дорожных условиях (асфальтовое |
||||||
|
покрытие) |
долговечность |
|
рессор |
|||
|
магистральных грузовиков составляет 100- |
||||||
|
150 тыс. км пробега, но в плохих условиях |
||||||
|
(грунтовые дороги, работа на стройках) она |
||||||
|
падает вдвое и доходит до 10-15 тыс. км в |
||||||
|
случае применения рессор, изготовленных |
||||||
|
ремонтными предприятиями [4]. Это даѐт |
||||||
|
оценочную |
информацию |
для подстановки |
||||
|
требуемых |
коэффициентов |
в |
наши |
|||
|
расчѐтные формулы. |
|
|
|
|||
|
Предполагаем, |
что |
плотность |
||||
|
распределения |
вероятностей |
|
скорости |
|||
|
автомобиля «Газель» на его типичном |
||||||
|
маршруте |
может |
быть |
аппроксимирована |
|||
Рис. 4. График зависимости математического |
нормальным распределением. |
|
|
||||
Плотности |
вероятностей |
случайных |
|||||
ожидания пробега до поломки задней рессоры |
|||||||
|
|
|
|
|
|
Откуда находим, что m=3.3. |
величин, связанных нелинейной |
|
Сведѐм расчѐтные формулы к следующей последовательности вычислений. |
||
от коэффициента демпфирования задних |
зависимостью, определяются формулой: |
|
подвесок. |
||
W(L)= W(V)* | 1/ dL/dV| . |
||
|
||
Откуда получим искомую функцию плотности вероятности пробега до поломки |
||
W(L) (на примере для коэффициента демпфирования задней подвески h2=8.5 kN sec/m): |
Математическое ожидание пробега автомобиля до поломки рессоры можем найти по формуле: .
Библиографический список
1.Пархиловский, И.Г. Автомобильные листовые рессоры: Теория, расчет и испытания. – 2-е изд., перераб. и доп. – М. Машиностроение, 1968. – 232 с.
2.Мусарский, Р.А. Математические модели колѐсных экипажей. Учебное пособие. – Изд-во Нижегородского государственного университета им. Н.И. Лобачевского, 2008. – 164 с.
3.Пархиловский, И.Г. Исследование нагрузочного режима и методика расчѐта долговечности рессор автомобильных подвесок./ Ф.А Цхай. – В кн.: "Исследования в области конструирования автомобилей". М. Машиностроение,1970. – с.165-205.
4.http://www.parts777.ru/library/trucks-articles/trucks-interesting-facts/trucks-suspenders/
100
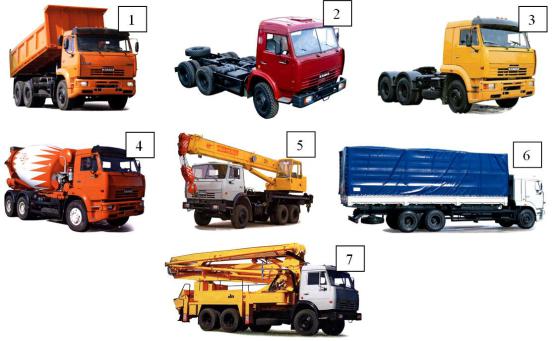
УДК 629.113; 656.135; 303.732
ИСПОЛЬЗОВАНИЕ СТАТИСТИЧЕСКИХ ДАННЫХ ПО РЕКЛАМАЦИЯМ ДЛЯ ПОВЫШЕНИЯ НАДЕЖНОСТИ НЕСУЩЕЙ СИСТЕМЫ ГРУЗОВЫХ АВТОМОБИЛЕЙ
Исхаков А.С., Макарова И.В., Хабибуллин Р.Г.
ГОУ ВПО «Камская государственная инженерно-экономическая академия»
Современные тенденции рынка диктуют свои условия эксплуатации грузовой автомобильной техники, и не редкость, когда учет пожеланий потребителя в процессе проектирования или модернизации модельного ряда ставит перед конструкторами задачи совмещения противоречивых решений (например, снижение массы автомобиля с одновременным увеличением его грузоподъемности и т.д.). На деле готовый продукт представляется в виде определенной гаммы автомобилей, в которой каждая отдельная модель спроектирована для решения своего круга задач (Рисунок 1).
Рис. 1. Грузовые автомобили, шасси и спецтехника КАМАЗ: 1-автосамосвал; 2-шасси для надстроек; 3-седельный тягач; 4-автобетоносмеситель; 5-автокран; 6-бортовой автомобиль; 7- автобетононасос
При определении областей рационального использования грузовых автомобилей, в том числе и спецтехники, практически не учитывается фактический уровень надежности машин, его влияние на эффективность работы на маршруте в целом. Вместе с тем, при эксплуатации грузовых автомобилей имеют место многочисленные случаи отказов, повреждений и разрушений деталей, узлов, элементов конструкций, что резко снижает эффективность использования машин.
Для повышения качества продукции, еѐ конкурентоспособности важно еще на стадии проектирования из множества вариантов обоснованно и в сжатые сроки выбрать наилучший, который отвечал бы всем требованиям. Поэтому инженеры-конструкторы все шире используют возможности различных САПР (CAD/CAM/CAE/PDM-систем), которые позволяют сократить время выпуска нового модельного ряда, улучшить характеристики автомобиля, а также снизить затраты на доработку.
Структура отказов по грузовым автомобилям КАМАЗ за 2010 год (см. рис.2) такова, что доля отказов по несущей системе среди прочих на первый взгляд мала. Но, с учетом того, что рама грузового автомобиля является основным несущим элементом конструкции,
101
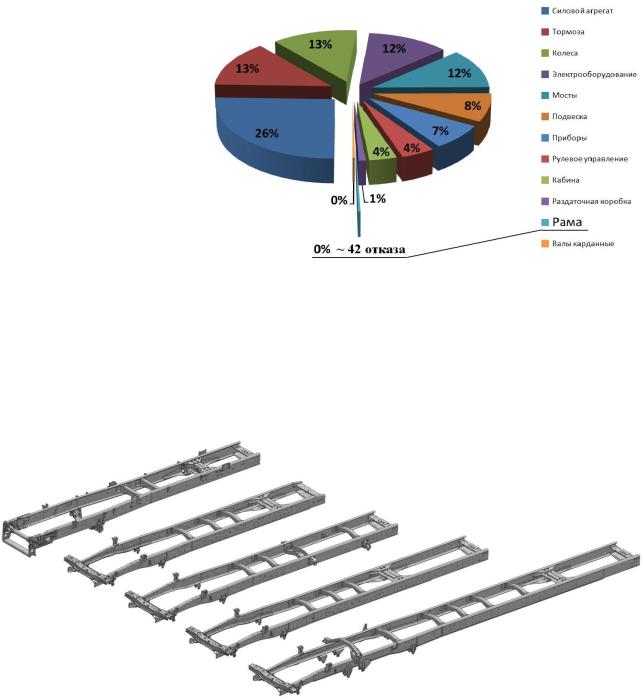
который воспринимает все нагрузки, возникающие при движении автомобиля по дорогам и местности, является основанием для крепления узлов и агрегатов машины, а также рассчитывается на полный срок службы всего автомобиля до его списания, следует отметить недостаточный уровень надежности и прочности при разнообразных режимах нагружения. Это обусловлено тем, что выход из строя несущей системы вследствие поломки или необратимой деформации отдельных еѐ частей связан с трудоемкими и дорогостоящими видами работ по еѐ ремонту или замене, а также внеплановым простоем всего автомобиля.
Несущие системы колесных машин в эксплуатации подвержены случайному нагружению вследствие воздействия неровностей дороги, переменных сил сопротивления движению, колебательных процессов, возникающих в системах подрессоривания кузова, узлов трансмиссии и ряда других факторов. В связи
сэтим, напряженное
состояние элементов конструкции характеризуется
случайным изменением напряжений во времени.
Отмечается, что поломки элементов несущей системы в процессе эксплуатации, возникают как вследствие действия предельных статических нагрузок, так и носят усталостный характер. В результате многолетнего опыта проектирования и эксплуатации, несущая система грузовых автомобилей КАМАЗ принимает определенные компоновочные формы, которые варьируются в незначительных пределах в зависимости от назначения той или иной машины.
Рис. 3. Некоторые модели рам а/м КАМАЗ
Для всестороннего анализа конструкции несущей системы целесообразно оценивать напряженно-деформированное состояния при всех нагрузочных режимах, встречающихся в эксплуатации, а не только предельных. Они могут иметь иной характер воздействия (длительный) и меньшие амплитудные величины. Такие нагрузки учитываются при определении усталостной прочности конструкции, поэтому их анализ также очень важен.
102
В современных условиях роль расчетных методов при обеспечении прочности конструкций неуклонно повышается как в связи с необходимостью сокращения сроков проектирования машин и ускорения организации серийного производства, так и ввиду высокой стоимости и трудоемкости экспериментальных исследований.
Традиционно, для получения информации о характеристиках и свойствах машины, широко применяют экспериментальные исследования, которые на этапе проектирования не всегда доступны. В этом случае решения принимают на основе опыта создания аналогичных конструкций, теоретического анализа и расчетных методов. Опыт внедрения новой техники показал, что дорогостоящие, трудоемкие, длительные испытания в ряде случаев при обоснованном теоретическом подходе могут быть заменены моделированием процессов нагружения.
Среди многочисленных методов моделирования напряженно-деформированного состояния деталей, в первую очередь, следует отметить метод конечных элементов. Он обладает значительным потенциалом и широкими возможностями оценки напряжений в конструкции сложной формы. Однако, результаты, с приемлемой точностью, могут быть получены только при достаточно обоснованном использовании. На точность метода влияет множество факторов:
–полнота и достоверность исходных данных;
–упрощения в принятых допущениях;
–степень совершенства расчетных схем (включая способы учета нагрузок, граничных условий, формы объекта и свойств материалов);
–выбор типов конечных (граничных) элементов;
–качество разбивок на элементы;
–характеристики и проработка численных алгоритмов;
–надежность программного обеспечения;
–возможности вычислительной техники.
Система фирменного сервиса, которая присуща мировым брендам автомобилестроения, позволяет создать единую информационную среду, благодаря которой можно отследить весь жизненный цикл автомобиля от момента его разработки до утилизации. Создание подобной системы дает возможность организации сбора и анализа причин отказов и дефектов, которые возникают в процессе эксплуатации автомобиля, т.е. определения конструктивных недоработок и нарушений технологии производства автомобилей, которые не были выявлены во время проектирования и испытания опытных образцов.
Анализ статистической информации об отказах позволяет выявить «слабые» места конструкции. Учет такой информации позволяет в дальнейшем провести проверочные расчеты, изменив схемы нагружения. Такие расчеты позволят выявить причины возникновения отказов, установив, при каком нагружении возможен такой отказ. Это позволит вносить коррективы в уже существующую конструкцию, вырабатывать рекомендации по эксплуатации, а также учитывать возможность возникновения установленных ситуаций при разработке новых моделей автомобильной техники.
Библиографический список
1.Проскуряков, В.Б. Динамика и прочность рам и корпусов транспортных машин – Л.: Машиностроение, 1972. – 232 с.
2.Бочаров, Н.Ф. Конструирование и расчет колесных машин высокой проходимости: Общие вопросы конструирования / Л.Ф. Жеглов, В.Н. Зузов – М.: Машиностроение, 1992. – 352с.
3.Когаев, В.П. Расчеты на прочность при напряжениях, переменных во времени – М.: Машиностроение, 1977. – 232с.
4.Волохов, Г.М. Эффективный метод повышения прочности и снижения металлоемкости несущих систем автомобилей/, П.Д. Павленко, Ю.Н. Петер // Автомобильная промышленность. – 1985. - №2. – С. 12-13.
103
УДК 629.113
К ВОПРОСУ ПОВЫШЕНИЯ БЕЗОПАСНОСТИ ДВИЖЕНИЯ АВТОМОБИЛЯ ЗА СЧЁТ ОПТИМАЛЬНОГО РАСПРЕДЕЛЕНИЯ КРУТЯЩИХ МОМЕНТОВ
Барыкин А.Ю.
Камская государственная инженерно-экономическая академия
Сложность оптимального распределение крутящих моментов в межосевом и межколѐсном приводе определяется большим числом внешних и внутренних факторов воздействия и ограниченностью выбора рациональных характеристик распределяющего механизма или системы. Следует выполнить, во-первых, ранжирование внешних факторов по степени их влияния на эксплуатационные свойства автомобиля (проходимость, устойчивость, маневренность) и безопасность движения; во-вторых, произвести выбор критериев оптимальности и диапазоны их изменения, определяющие поведение автомобиля в различных условиях эксплуатации.
Данная задача является основной при проектировании механизмов и систем распределения мощности полноприводных легковых автомобилей. Известны различные конструктивные варианты, чаще всего представляющие собой фрикционные многодисковые муфты с автоматическим управлением. В большинстве случаев такие устройства используют компоненты имеющейся на автомобиле антиблокировочной системы, от контрольных датчиков до блока управления.
Анализ существующих систем распределения мощности показывает, что основные контролируемые параметры режима движения автомобиля принимаются, исходя из следующих групп показателей:
–частоты вращения колѐс, частоты вращения приводов мостов, проскальзывание колес;
–моменты инерции колѐс;
–угол поворота автомобиля;
–включение тормозной системы, давление в тормозном приводе, тормозное усилие;
–скорость и ускорение автомобиля;
–сила тяги, силы сцепления колѐс с опорной поверхностью, суммарные силы, действующие на ведущие колѐса;
–положение дроссельной заслонки, давление наддува двигателя, температура
масла, режим гидротрансформатора.
Существующие системы регулирования тяговых усилий не всегда позволяют добиться повышения безопасности движения автомобиля, так как выбор моментов трения в дифференциалах или управляемых многодисковых муфтах должен соответствовать оптимальному для объективно существующих внешних условий.
Объективный анализ существующих факторов информационного пространства важен и при выборе блокирующих свойств обычных, не автоматических дифференциалов (повышенного трения, самоблокируемых). Основные системные критерии информационного пространства названной задачи оптимизации предложены автором в работах [3, 4]. Информационное пространство системы управления распределением мощности определяется внешними (окружающая среда, дорога) и внутренними (двигатель, привод) объектами воздействия, каждый из которых можно характеризовать сводимым к минимуму конечным числом факторов. Рассматриваются оценочные показатели механизмов и систем автомобиля, условий дороги и окружающей среды, продолжительность, характер и амплитуда воздействия учитываемых факторов. На основе выбранных критериев и задаваемых конечных оценочных показателей системы следует разрабатывать математическую модель и программный алгоритм управления.
104
Факторы воздействия внешней среды и режима эксплуатации механизмов являются весомыми в различной степени, так как не только оказывают многообразное влияние на степень блокировки колѐс (мостов), но и воздействуют друг на друга. В научной литературе известны и исследованы некоторые из таких воздействий, значительная же часть остаѐтся неизученной.
По мнению автора, основными оценочными показателями ограничения блокирующего воздействия для достижения оптимальных критериев эксплуатационных свойств (устойчивости, управляемости, тяговой динамики) являются следующие группы:
–разность оборотов колес одного моста, угол поворота рулевого колеса и динамический ход подвески (ограничение для режимов поворота, скольжения колес, отделения колес от опорной поверхности);
–скорость автомобиля, углы бокового увода шин, угол поворота рулевого колеса и состояние дорожного покрытия (ограничение по условию безопасного прохождения поворота на высокой скорости);
–скорость и амплитуда изменения распределения крутящих моментов, поворот рулевого колеса и состояние дорожного покрытия (ограничение по условию безопасного прохождения поворота на скользком покрытии);
–скорость и амплитуда изменения распределения крутящих моментов, воздействие окружающей среды и состояние дорожного покрытия (ограничение возможности аварийной ситуации);
–значения отрицательных крутящих моментов на ведущих колесах (ограничение для случаев торможения и циркуляции паразитной мощности);
–величины крутящих моментов на колесах, суммарные силы сопротивления и свойства опорной поверхности (ограничение по условию проходимости);
–величины и продолжительность действия моментов трения в механизмах распределения мощности, условия работы механизмов, воздействие окружающей среды (ограничение по условию обеспечения эффективной
работы механизма распределения).
Проблема оптимального перераспределения нагрузки по критериям безопасности прохождения поворота заключается в следующем противоречии:
1)быстрое изменение крутящих моментов только по критериям разности угловых скоростей может привести к существенному изменению склонности к повороту;
2)медленное (плавное) изменение моментов может оказаться неэффективным и привести к скольжению колес.
3)интенсивность перераспределения должна увязываться с конкретным режимом движения, свойствами дорожного покрытия, которые могут испытывать дополнительное влияние со стороны других факторов (воздействия внешней
среды и др.).
Другой проблемой оптимизации является нестабильность момента трения дифференциала (фрикционной муфты), определяемого в существенной степени значением коэффициента трения в контакте вращающихся деталей. В данном случае следует
принимать во внимание давление на поверхности трения, температуры трансмиссионного масла и деталей, степень износа фрикционных элементов [3]. Влияние указанной нестабильности на распределение крутящих моментов и на безопасность движения определяется выбранным типом дифференциального механизма. Следует оценивать стабильность коэффициента блокировки kб с помощью зависимостей вида
которые автором в работе [2] предложено называть статическими характеристиками дифференциалов. Исследования различных типов дифференциалов позволяют сделать вывод, что стабильность блокирующих свойств зависит от ряда конструктивных и нагрузочных параметров, при этом определяющим фактором стабильности следует считать коэффициент трения рабочих поверхностей дифференциала. Корректирование режима
105

работы системы распределения мощности по известной статической характеристике механизма трения позволит произвести рациональное изменение блокирующих свойств для сложных условий эксплуатации.
Критерий оптимальности при выборе типа механизма распределения мощности следует определять в виде:
g |
|
Д эфДj j RДрj , |
(1) |
р 1 |
|
где j - коэффициенты весомости различных факторов рациональности |
блокирующих |
свойств RДрj для j -го типа механизм. |
|
Такими факторами следует считать:
1)фактор рациональности блокирующих свойств дифференциала по условиям реализации тяговых сил на ведущих колѐсах;
2)фактор рациональности блокирующих свойств по влиянию на управляемость;
3)фактор рациональности блокирующих свойств по влиянию на устойчивость;
4)фактор рациональности блокирующих свойств по влиянию на динамику и приемистость автомобиля;
5)фактор рациональности блокирующих свойств по плавности включения и безударной работе механизма распределения мощности;
6)фактор надѐжности конструкции дифференциала для расчѐтных конструктивных параметров.
Для обеспечения активной безопасности автомобиля наиболее важными из перечисленных выше являются факторы рациональности блокирующих свойств по условиям реализации тяговых сил на ведущих колѐсах, по влиянию на управляемость, устойчивость, динамику и приемистость автомобиля.
По условиям реализации тяговых сил на ведущих колѐсах рациональность оценивается обратным критерием рациональности блокирующих свойств j -го типа
дифференциала для заданного числа расчѐтных режимов п :
|
|
m |
n |
|
|
|
|
|
П pxij i |
|
|||
F 1 |
= |
j 1 i 1 |
|
, |
(2) |
|
|
|
|
||||
дj |
|
|
n |
|
|
|
|
|
m П pxij i |
|
|||
|
|
|
i 1 |
|
|
|
где i - вероятность работы дифференциала |
в i -м |
режиме; П pxi |
- показатель частной |
рациональности характеристик дифференциала по условию реализации тяговых сил на ведущих колѐсах в условиях i -го расчѐтного режима:
П |
pxi |
|
( k |
брацi |
k p |
) k |
брацi |
100% , |
(3) |
|
|
|
бi |
|
|
|
|||
kбрацi - коэффициент блокировки дифференциала |
в i -м режиме, |
определяемый для |
отношений средних значений коэффициентов опорной поверхности kопот kопзаб отстающего и забегающего колеса (моста) по справочным данным; kбрi - расчѐтное значение коэффициента
блокировки исследуемого типа дифференциала. Коэффициент опорной поверхности предложен автором и представляет собой сумму значений коэффициента сцепления колеса с дорогой и коэффициента сопротивления качению для заданных условий.
Рациональность блокирующих свойств по влиянию на управляемость определяется критерием лѐгкости управления по блокирующим свойствам дифференциала k упр , что
позволяет ограничить негативное влияние дифференциала на сопротивление повороту в рулевом приводе:
k |
|
|
M сопр.пов |
|
M сопр.пов |
k упр , |
(4) |
упр |
|
|
|||||
|
|
М трmax |
M шестmax |
бI |
|
||
|
|
|
|
|
|||
|
|
106 |
|
|
|
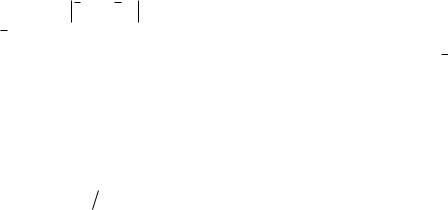
где M сопр.пов - момент сопротивления повороту; M трmax - максимальный момент трения исследуемого дифференциала; Mшестmax - максимальный момент трения обычного шестерѐнного дифференциала с малым трением; kбупрI - коэффициент блокировки,
рациональный по критериям управляемости.
Рациональность блокирующих свойств по влиянию на устойчивость задаѐтся критерием устойчивости по блокирующим свойствам, определяемым по формуле:
kуст 1 kбуст2 kб 2 j ,
где kбуст2 - среднее значение коэффициента блокировки второго рода, являющееся рациональным по условию обеспечения устойчивости автомобиля; kб 2 j - среднее значение
расчѐтного коэффициента блокировки второго рода j-го типа дифференциала для рассматриваемых вероятных режимов движения.
Рациональность блокирующих свойств по влиянию на динамику |
и |
приемистость |
автомобиля оценивается критерием тяговой динамики автомобиля |
с |
j-м типом |
дифференциала. Данный критерий |
находится по |
формулам, основанным |
на методике |
|||||||
А.С. Нарбута, описанной в [1]: |
|
|
|
|
|
|
|
|||
kтд kопрасчj |
kопрац , |
|
|
|
|
|
|
|
||
kопрац kоп1 |
kоп2 ( 1 f1 ) ( 2 f2 ) ( f ) , |
|
|
|||||||
kопрасчj |
( min fmin ) ( 1 kб1 |
) |
|
2 ( min fmin ) |
, |
|
|
|||
|
|
|
|
|||||||
|
|
|
|
|
|
1 kб 2 |
|
|
|
|
где k рац , |
k |
расч - |
рациональный |
и |
|
расчѐтный |
коэффициенты |
опорной |
поверхности |
|
оп |
опj |
|
|
|
|
|
|
|
|
|
соответственно; 1 |
, 2 - коэффициенты сцепления колѐс с дорогой; |
f1 , f2 - коэффициенты |
сопротивления качению колес; min , fmin - минимальные значения коэффициентов сцепления и сопротивления качению для выбранных условий; kб1 , kб 2 - коэффициенты блокировки первого и второго рода.
В данном случае параметр ДэфДj является целевой функцией, образованной по
аддитивному принципу и представляющей сумму произведений нормированных частных критериев на их весовые коэффициенты. Автором разработана математическая модель, позволяющая производить сравнение эффективности применения и оптимальный выбор автомобильных дифференциалов различного типа по критериям эксплуатационных свойств. Перечисленные факторы используются при вычислении показателя эффективности (критерия оптимальности) трансмиссии.
Библиографический список
1.Вишняков, Н.Н. Автомобиль. Основы конструкции. // Вишняков Н.Н., Вахламов В.К., Нарбут А.Н. – М.: Машиностроение, 1986. – 303 с.
2.Барыкин, А.Ю. К вопросу стабильности блокирующих свойств дифференциалов различного типа. // “Образование и наука - производству”. Сборник трудов Международной научнотехнической и образовательной конференции. В 2-х ч. Ч. 1, кн. 2. – Наб. Челны: ИНЭКА, 2010. С. 102…105.
3.Барыкин, А.Ю. Основы теории современных дифференциалов. - Наб. Челны: КамПИ, 2001. – 277 с: ил.
4.Barykin A.Yu. Automatic differential: Synthesis of structure of bloking properties. // Int. Conf. MSTU MAMI, 27-28 Sept. 2000. - M.: MAMI, 2000. P. 35...36.
107
УДК 629.113:011.5
ФОРМИРОВАНИЕ СТРУКТУРЫ И МЕХАНИЧЕСКИХ СВОЙСТВ СТАЛИ 38ХА ДЛЯ ПОЛУЧЕНИЯ ВЫСОКОПРОЧНЫХ БОЛТОВ
Пачурин В.Г., Пачурин Г.В., Филиппов А.А.
Нижегородский государственный технический университет им. Р.Е. Алексеева
Безопасность конструкции автомобиля во многом определяется эксплуатационной надежностью элементов ее составляющих. К числу ответственных и широко распространенных в машиностроении деталей относится автомобильный крепеж, изготавливаемый из углеродистой, высокоуглеродистой и легированной проволоки.
В настоящее время в метизном производстве довольно широко распространены стали 35Х, 38ХА и 40Х. Так более 60% крепежа классом прочности 10.9 и выше изготавливают из этих стали с последующим термоулучшением высаженных болтов. Свойства метизов и их эксплуатационные показатели формируются на всех стадиях металлургического передела, начиная с выбора шихтовых материалов для выплавки металла и заканчивая обработкой готовой проволокой [1].
Наряду с применением высокопрочных металлоизделий традиционной формы, внедрением новых прогрессивных конструкций актуальной задачей остается производство крепежных изделий без внутренних дефектов и дефектов поверхности. Для обеспечения изготовления методом холодной объемной штамповки массовых деталей требуется качественный горячекатаный прокат с осадкой до 1/3 первоначальной высоты образца, а калиброванный прокат должен выдерживать осадку до 1/4 первоначальной высоты образца.
Известно [3], что выпуск высококачественной продукции зависит: от качества исходного проката, технологии изготовления изделий, характера нагрузки, степени деформации, от состояния оборудования и квалификации обслуживающего персонала. Материал, применяемый для объемной холодной штамповки метизов, должен обладать достаточной пластичностью, равномерными механическими свойствами и химическим составом, а также не должен иметь поверхностных и внутренних дефектов [4]. Если эти условия выполняются, то применение холодной высадки при производстве крепежных изделий позволяет достичь коэффициента использования металла 95-98%.
При уменьшении расхода металла основной фактор – качество исходного проката. Причиной повышенного расхода металла является отбраковка по дефектам «трещины» и «надрывы» горячекатаного проката, поставляемого с металлургических заводов. К поверхностным дефектам относятся такие дефекты, как раскатные газовые пузыри, волосовины, рванины, закаты и др. Также дефектом поверхности металлопроката является образование обезуглероженного слоя, существенно ухудшающего механические свойства в поверхностных слоях проката. Поверхность становится восприимчивой к образованию рисок, задиров, царапин при прокатке, калибровке и холодной высадке [1,5]. По своему характеру дефекты на поверхности горячекатаного проката, поступающего с металлургических предприятий, могут быть металлургического (при выплавке и разливке стали, охлаждении слитков), прокатного (при деформации и охлаждении проката) и волочильного (при калибровании проката или волочении проволоки) производства [1].
Высокотемпературный нагрев металла в металлургических печах перед его нагревом при прокатке вызывает интенсивное развитие газовой коррозии на его поверхности, следствием которой является окалинообразование, обеднение поверхностных слоев углеродом, перераспределение легирующих элементов в этих слоях (угар легкоокисляемых элементов и повышение концентрации относительно инертных к кислороду элементов).
Если на слитке пороки полностью не удалены, то при прокатке они переходят на блюмы (слябы), заготовки, на горячекатаный прокат, на готовый калиброванный прокат и далее на крепежные изделия в процессе холодной объемной штамповки.
108
Основной технический дефект при производстве крепежа связан с высокой степенью деформации (до 88%) в процессе холодной объемной штамповки, т.к. трещины исходного горячекатаного и калиброванного проката, не лежащие на поверхности, распространяются на штампуемом изделии в результате максимальных полных касательных напряжений. Чаще всего трещины, возникающие при холодной штамповке, параллельны оси подката, а трещины, возникающие при отделочных операциях, перпендикулярны его оси.
Однако даже соблюдение всех технологических требований и рекомендаций по структуре и механическим свойствам исходного горячекатаного и калиброванного проката еще не гарантирует отсутствие брака металлоизделий при обработке давлением.
Наиболее распространенным видом дефектов металлургического происхождения являются неметаллические включения – частицы шлака и огнеупоров. При выпуске расплавленного металла из печи в ковш и из ковша в изложницу шлак механически извлекается струей металла из футеровки печи или изложницы. Таким образом, частицы огнеупорного материала попадают в сталь. При дальнейшей обработке круглого проката холодным пластическим деформированием трещины образуются в местах наибольших скоплений неметаллических включений даже при самых благоприятных для холодной объемной штамповки механических свойствах и микроструктуре.
Поэтому одной из проблем изготовления качественного материала для холодной высадки является обеспечение минимального содержания неметаллических включений. При этом осуществляя входной контроль металлопроката для холодной высадки важно проводить исследование на их наличие.
Причиной образования трещин при штамповке со степенью деформации от 40% и более могут также являться дефекты сталеплавильного (при разливке и охлаждении слитков) и прокатного (при деформации и охлаждении проката) происхождения.
Важным условием повышения технологичности производства калиброванного проката и дальнейшей холодной высадки крепежа является наличие однородной структуры и уровня механических свойств по сечению мотков металла.
Структура – основное звено, связывающее технологию материала и его поведение в эксплуатации. Для успешного осуществления технологических операций холодной объемной штамповки калиброванный прокат должна иметь оптимальную макро- и микроструктуру. Макроструктура стали должна быть однородной без усадочных рыхлостей, расслоений, неметаллических включений, не иметь пор, пузырей, трещин, ликвационной зоны, флокенов и других дефектов, видимых невооруженным глазом на поперечных темплетах после травления [6]. Площадь ликвационной зоны не должна превышать 40% поперечного сечения заготовки, в противном случае на головках изделий образуются трещины, а при накатывании резьбы – расслоения.
Макроструктура легированной стали должна соответствовать ГОСТ 4543-71. Величина аустенитного зерна в легированной стали должна быть не крупнее номера 5 [7]. Характер микроструктуры, применяющейся для ХОШ, влияет на протекание технологического процесса и качество изделий. Для обеспечения стойкости рабочих деталей штампов, исключения появления трещин, разрывов сталь в состоянии поставки должна иметь однородную микроструктуру, в которой не допускается полосчатость [19], структурно-свободный цементит, расположенный по границам зерен в виде скоплений или сетки. Микроструктура калиброванной стали марки 38ХА не должна иметь грубоплатинчатого перлита, игольчатости и видманштеттовой структуры, поскольку они резко снижают пластичность и ударную вязкость стали [8]. К стали для холодной высадки могут быть предъявлены следующие дополнительные требования: повышенные нормы по поперечному сужению, нормированная макро и микроструктура, размер зерна, глубина обезуглероженного слоя, ограничение содержания кремния.
На штампуемость легированной стали 38ХА большое влияние оказывает размер и ориентировка зерен и структура стали. При значительном размере зерен и резко выраженной их пластичности при холодном выдавливании возможны скалывание и расслоение головки
109