
новая папка / БЕЗОПАСНОСТЬ ТРАНСПОРТНЫХ СРЕДСТВ В ЭКСПЛУАТАЦИИ
.pdf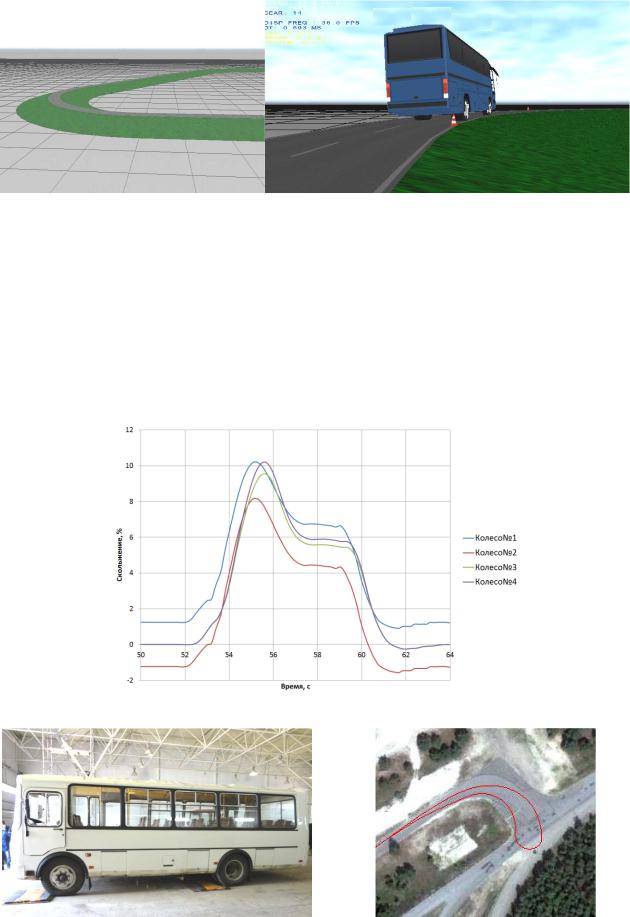
Рис. 2. Моделируемая траектория движения и модель автобуса
Создана виртуальная модель автобуса ПАЗ (рис. 2). Заданы соответствующие параметры водителя и программа управляющего воздействия. Для оценки скольжения в критических режимах движения на рисунке 3 представлены результаты компьютерного моделирования.
Для проверки адекватности и работоспособности разработанных компьютерных моделей был проведен ряд натурных исследований. В качестве базового было выбрано испытание «поворот» согласно ГОСТ 52302-2004.
Исследования выполнены сотрудниками Автомобильного института НГТУ при поддержке Испытательной лаборатории НГТУ и Группы ГАЗ. Объектом исследования являлся автобус ПАЗ-4234-05 (рис. 4а). Дорожные испытания проводились на автополигоне ГАЗ (рис. 4б).
Рис. 3. Скольжение колес при входе в поворот
а) |
б) |
Рис. 4. Дорожные испытания а – автобус ПАЗ-4234-05б –траектория движения на полигоне
20
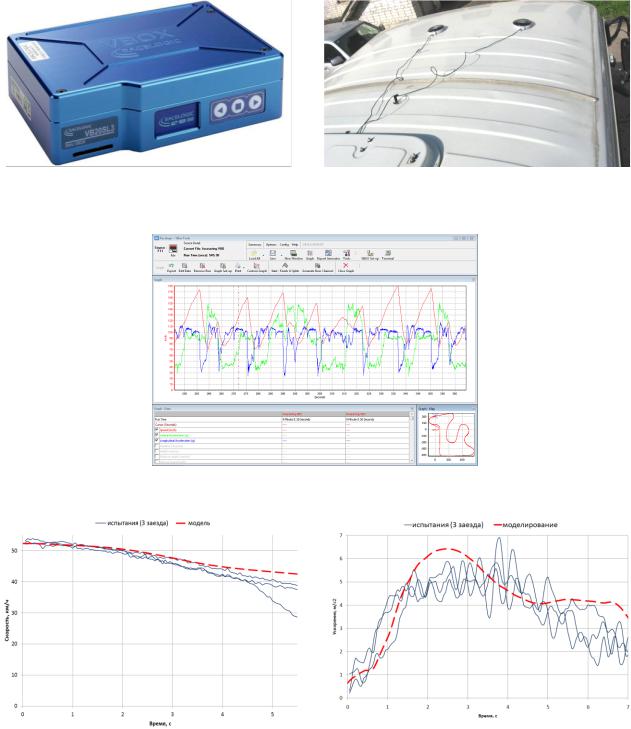
Для определения параметров движения автобуса использовалась современная измерительная система RaceLogicVB20SL3 20HzGPSDataLoggerWithSlip, PitchandRollAngle.
Принцип работы системы основан на использовании GPSтехнологий. На крышу автомобиля устанавливаются магнитные антенны (рис. 5), которые обеспечивают связь со спутником и позволяют зафиксировать скорость транспортного средства, ускорение (по 2-м осям), траекторию движения, угол крена и угловую скорость поворота (рис. 6).
а) |
б) |
Рис. 5. Автобус ПАЗ-4234-05
а – блок сбора данных системы RaceLogic; б – схема установки антенн на крыше автобуса
Рис. 6. Интерфейс программного обеспечения RaceLogic
Приведем сравнение результатов компьютерного моделирования и натурных испытаний.
а) б) Рис.7.Сравнение результатов моделирования и натурных испытаний а - сравнение скорости движения; б-сравнение поперечных ускорений
На рисунке7 дано сравнение результатов моделирования и натурных испытаний. Сплошными линиями показаны данные, зафиксированные в ходе натурных испытаний, пунктирными – данные компьютерного моделирования. Видно, что отличие не превосходит
21
10 % при сравнении скорости движенияи 15% при сравнении поперечных ускорений.Сравнение результатов компьютерного моделирования и дорожных испытаний показало хорошую сходимость.
По результатам исследования можно сделать следующие выводы:
1.Натурными испытаниями автобуса выявляется предельная скорость, позволяющая осуществлять поворот с радиусом 35 метров. Дальнейшее увеличение скорости не позволяет осуществлять заданную траекторию из-за скольжения колѐс.
2.Натурные испытания не позволяют выявить, как и в каком порядке колѐса
начинают скользить. Полную картину скольжения колѐс при подходе к критической скорости позволяет осуществить моделирование входа в поворот на пространственной математической модели.
3.С помощью программного пакета SDK-Simulation проведена имитация испытания «поворот» в соответствии с требованиями нормативного документов и был разработан виртуальный участок дорожного полотна. Создана виртуальная модель автобуса ПАЗ 4234-05 и заданы параметры водителя и программа управляющего воздействия.
4.Разработанная имитационная модель автобуса и результаты исследований могут быть использованы при разработке методики оценки свойств активной безопасности транспортных средств по результатам имитационного моделирования, которая имеет важное практическое значение на этапах проектирования и доводки автомобилей.
Библиографический список
1. Журавлев, В.Ф. Механика систем с неудерживающими связями / Н.А.Фуфаев. - М.: Наука, 1993. 240 с.
2. Мусарский, Р.А. Математические модели колѐсных экипажей. - Учебное пособие. ННГУ им. Н.И. Лобачевского, 2008. 163 с.
3.Костин, С.Ю.Исследование свойств активной безопасности транспортных средств методом имитационного моделирования / А.М. Грошев, А.В.Тумасов и др. // Журнал ААИ – 2011 - №2 - С.34-37.
УДК 623.19.47
ОПРЕДЕЛЕНИЕ ПАРАМЕТРОВ АВТОМОБИЛЯ, ВХОДЯЩИХ В МАТЕМАТИЧЕСКУЮ МОДЕЛЬ
Никольский В.А.
Нижегородский государственный технический университет им. Р.Е. Алексеева
Исследование свойств активной безопасности является важной задачей на этапах проектирования, доводки и сертификации транспортных средств (ТС). Все большее значение при выполнении работ, направленных на повышение активной безопасности автотранспортных средств, приобретает имитационное моделирование, представляющее процесс конструирования на ЭВМ модели сложной реальной системы, функционирующей во времени, и постановки экспериментов на этой модели с целью либо понять поведение системы, либо оценить различные стратегии, обеспечивающие функционирование данной системы [1]. Имитационные модели транспортных средств и систем могут быть использованы для оценки их эксплуатационных свойств, определения возможных способов совершенствования их конструкций, оценки влияния определенных конструктивных изменений на тормозные свойства, управляемость и устойчивость.
Важной задачей на первых этапах исследования свойств активной безопасности является определение параметров ТС, входящего в математическую модель, одни из которых определяются на основании имеющейся технической и конструкторской документации,
22
другие – на основании эксперимента или расчета. Для адекватного отражения реальных процессов, протекающих к примеру при торможении, параметры автомобиля в целом, его узлов и систем должны быть определены экспериментальным, а при невозможности, расчетно-экспериментальным путем. Введение в математическую модель параметров, определенных экспериментальным путем, приближает результаты моделирования к реальным и при доводке автомобиля исследования на натурном образце могут быть заменены исследованиями на математической модели.
Особое внимание необходимо уделить определению параметров тормозных механизмов, элементов АБС, подвески, регуляторов тормозных сил и привода. Немаловажно проводить углубленный анализ параметров тормозной системы и в частности характеристик рабочих тормозных механизмов, так как они работают при резко переменных режимах как с точки зрения регулируемого тормозного момента, так и изменения значений объемных и поверхностных температур. Одним из таких параметров является коэффициент пропорциональности между тормозным моментом, создаваемым на колесе, и давлением в приводе:
КТ |
|
М |
, |
(1) |
|
р0 |
|||||
|
|
|
|
||
где М , Нм – тормозной момент, реализуемый |
данным |
тормозным механизмом; |
р0 , бар – давление в приводе.
Вследствие воздействия температуры, скоростного и температурного режимов в широких пределах изменяется и коэффициент пропорциональности передних и задних тормозных механизмов и, как следствие, соотношение тормозных сил по осям. Высокая стабильность тормозных механизмов является одним из главных условий реализации преимущества регулирования тормозных сил. Поэтому при моделировании процесса торможения необходимо располагать как экспериментальными данными характеристик передних и задних тормозных механизмов, так и теоретическими зависимостями.
Для определения коэффициента пропорциональности тормозных механизмов различных типов существуют расчетные формулы, приведенные в учебниках по Конструированию и расчету автомобиля таких авторов, как Гришкевич А.И., Лукин П.П., Осепчугов В.В., Вахламов В.К.
Помимо расчетных существуют экспериментальные методы определения характеристик тормозных механизмов как на стенде, так и в дорожных условиях. Широкое распространение получили стенды с инерционными массами (см. рис. 1). Во время испытания на инерционном стенде тормозной механизм поглощает кинетическую энергию маховика, предварительно разгоняемого до определенной скорости. Таким образом торможение происходит при изменяющейся скорости скольжения. Рассматриваемые стенды наиболее полно и точно воспроизводят действительные условия работы тормозного механизма в автомобиле. Для разгона маховика можно использовать электродвигатели сравнительно небольшой мощности. Принципиальных отличий в конструкции и методиках проведения исследований на таких стендах нет.
Принцип работы стенда следующий: осуществляется разгон инерционной массы до заданной скорости, выключается электродвигатель и включается регистрирующая аппаратура, далее происходит включение привода тормозного механизма и торможение инерционных масс до полной остановки. Управление стендом осуществляется вручную или автоматически с заданными интервалом между торможениями. Ручное управление применяют при снятии характеристик тормозного механизма, а автоматическое – при испытаниях на долговечность. На стенде регистрируются следующие параметры: момент инерции маховиков, скорость вращения инерционных масс, давление в приводе, температура тормозных накладок, время торможения, тормозной путь и тормозной момент.
23
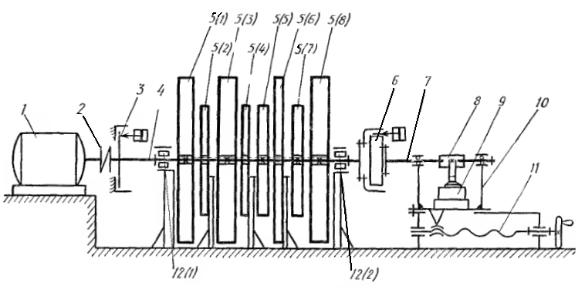
Рис. 1. Принципиальная кинематическая схема инерционного стенда 1 – электродвигатель; 2 – соединительная муфта; 3 – аварийный тормоз; 4 – вал;
5(1)-5(8) – набор инерционных масс; 6 – испытываемый тормоз; 7 – вал подвижного суппорта стенда; 8 – динамометрический рычаг; 9 – датчик силы; 10 – корпус суппорта; 11 – винтовой механизм для перемещения суппорта; 12 – опоры вала.
Момент инерции вращающихся масс выбирают исходя из обеспечения равенства кинетических энергий инерционных масс стенда и части общей инерционной массы ТС, приходящейся на тормозящее колесо.
Преимуществами инерционных стендов являются: близость режимов испытаний к реальным условиям работы тормозного механизма, независимость проведения испытаний от погодных условий, возможность комплексного исследования тормозного механизма. К недостаткам стоит отнести их дороговизну, ограниченность использования и большие временные затраты при подготовке и проведении испытаний.
Процедура определения коэффициента пропорциональности тормозных механизмов в дорожных условиях заключается в следующем: отключают один из контуров тормозной системы (передний или задний); на горизонтальном участке дороги проводят серию торможений, увеличивая давление от заезда к заезду. При этом регистрируются давление рабочего тела в переднем и заднем контурах, замедление при торможении. Необходимое количество заездов определяют по методике минимально-необходимой статистической обработки результатов односерийных и сравнительных экспериментов. Далее проводят обработку полученных результатов и вычисляют значения коэффициентов пропорциональности колес передней и задней осей.
Определение характеристик тормозных механизмов методом дорожных испытаний связано с большой трудоемкостью при подготовке автомобиля к испытаниям, а жесткая зависимость от погодных условий ограничивается возможный период проведения испытаний, что в итоге увеличивает сроки внедрения новых систем активной безопасности на автомобиль.
Специалистами Научно-исследовательской лаборатории транспортных интеллектуальных систем АМИ НГТУ им. Р.Е. Алексеева предложен расчетноэкспериментальный метод определения коэффициента пропорциональности, в основу которого заложены аналитический метод расчета и экспериментальный метод с использованием роликового тормозного стенда. Данный метод позволяет достаточно быстро оценивать характеристики тормозных механизмов в составе автомобиля.
Исходя из известных конструктивных параметров тормозной системы коэффициент пропорциональности определяется в соответствии с формулами, приведенными в [2],
24

которые учитывают закон распределения давлений по длине тормозной накладки, обусловленный жесткостью и температурой деталей тормоза, режимом торможения.
С помощью роликового тормозного стенда, принципиальная схема которого изображена на рис. 2, измеряют тормозные силы ( F ) колес каждой оси и усилие на
тормозной педали ( FП ), если автомобиль имеет гидравлический привод тормозной системы,
или давление воздуха ( PВ ), если автомобиль оснащен пневматическим тормозным приводом.
Рис. 2. Схема стенда 1 – колеса ТС; 2 – ролики; 3 – электродвигатель; 4 - динамометр
Тормозной момент определяется из известной тормозной силы по следующей формуле:
M |
τ |
F |
rД , |
(2) |
|
τ |
|
|
где rД, м – динамический радиус колеса.
Давление в приводе тормозных механизмов определяется исходя их конструктивных особенностей тормозного привода и измеренного значения усилия на тормозной педали (для автомобиля с гидравлическим тормозным приводом):
p0 FП UУ UП UР / SГТЦ , |
(3) |
где UУ – передаточное отношение усилителя; U П – передаточное число |
педального |
привода; U Р – передаточное отношение регулятора тормозных сил (если установлен),
SГТЦ , м2 – площадь поршня главного тормозного цилиндра.
При испытаниях ТС по определению коэффициентов пропорциональности тормозных механизмов на роликовом тормозном стенде не принимается во внимание динамика торможения, так как имитируется движение на небольших скоростях (3-5 км/ч), то есть испытания проходят в режиме, близком к статическому.
С целью оценки адекватности предложенного метода были проведены испытания автомобиля ГАЗ-2705 по определению коэффициентов пропорциональности тормозных механизмов колес передней и задней осей. Результаты данных испытаний сравнивались с результатами испытаний тормозных механизмов полностью аналогичной конструкции, проведенных в лабораторных условиях на инерционном стенде на территории Управления конструкторских и экспериментальных разработок ГАЗ.
Тормозная система автомобиля ГАЗ-2705 имеет гидравлический привод с разделением по двум контурам на передние и задние колеса. Передние тормозные механизмы колодочные, дискового типа с одним рабочим цилиндром и автоматической регулировкой
25
зазора. Задние тормозные механизмы колодочные, барабанного типа с одним рабочим цилиндром, автоматической регулировкой зазора между накладками и барабаном.
Оборудование на котором проводились замеры - Стенд роликовый IW2 Euro-Prof Minc 1 Euro 3т фирмы «МАНА», оснащенный датчиком для определения усилия на тормозной педали. Давление воздуха в шине контролировалось с помощью манометра МТИ, зав. №1109, диапазон измерений 0 – 4 кгс/см2, цена деления 0,02 кгс/см2.
На основании испытаний автомобиля ГАЗ-2705, проведенных расчетноэкспериментальным методом, получены следующие значения коэффициентов пропорциональности тормозных механизмов (см. табл. 1).
|
|
Таблица 1 |
|
Коэффициенты пропорциональности тормозных механизмов |
|||
|
|
|
|
Номер испытания |
Передний дисковый |
Задний барабанный |
|
|
тормозной механизм, КТ |
тормозной механизм, КТ |
|
1 |
2,299 |
2,199 |
|
2 |
2,144 |
1,982 |
|
3 |
2,048 |
1,790 |
|
4 |
1,971 |
1,689 |
|
5 |
1,872 |
1,683 |
|
6 |
1,766 |
1,656 |
|
Значения коэффициентов пропорциональности тормозных механизмов, полученные при испытаниях в лабораторных условиях на инерционном стенде, составляют: 2,346 – для колес передней оси; 2,1 – для колес задней оси.
Полученные данные показывают, что расхождение результатов расчетноэкспериментального и экспериментального методов составляет от 2 до 25% для дисковых тормозных механизмов и от 5 до 21% для барабанных.
Библиографический список
1.Вахламов, В.К. Автомобили: Конструкция и элементы расчета: учебник для студентов высших учебных заведений – М.: Издательский центр «Академия», 2006. – 480 с.
2.Гришкевич, А.И. Автомобили: Конструкция, конструирование и расчет. Системы управления и ходовая часть: Учеб. пособие для вузов/ Д.М. Ломако, В.П. Автушко и др.; Под ред. А.И. Гришкевича. – Мн.: Выш. Шк., 1987. – 200 с.: ил.
3.Балабин, И.В Испытания автомобилей: Учебник для машиностроительных техникумов по специальности «Автомобилестроение»/ Б.А. Куров, С.А. Лаптев. –М.: Машиностроение, 1988. – 192 с., ил.
4.Цимбалин, В.Б. Испытания автомобилей: Учебное пособие/В.Н. Кравец, С.М. Кудрявцев, И.Н. Успенский, В.И. Песков. –М.: Машиностроение, 1978. – 199 с., ил.
5.Лукин, П.П. конструирование и расчет автомобиля: Учебник для студентов втузов, обучающихся по специальности «Автомобили и тракторы»/Г.А. Гаспарянц, В.Ф. Родионов. – М.: Машиностроение, 1984. – 376 с., ил.
6.Осепчугов В.В. Автомобиль. Анализ конструкций, элементы расчета/А.К. Фрумкин. – М.: Машиностроение, 1989. – 304 с.
7.Правила ЕЭК ООН №13-10 «Единообразные предписания, касающиеся официального утверждения транспортных средств категорий М, N и О в отношении торможения».
8.Теория автомобиля: Учебное пособие/В.Н. Кравец; НГТУ. – Нижний Новгород, 2007. – 368 с.
9.Соцков, Д.А. Повышение активной безопасности автотранспортных средств при торможении: дис. доктора техн. наук / Д.А. Соцков. Владимир, 1988. – 547 с.
10.Шеннон, Р. Имитационное моделирование систем – искусство и наука / Р. Шеннон. М.: Мир, 1978. – 415с.
11.Грошев, А.М. Применение программно-аппаратных комплексов для оценки тормозных свойств транспортных средств по результатам имитационного моделирования/ В.В. Михайлов, В.А. Никольский, А.В. Тумасов // Труды Нижегородского государственного технического университета им. Р.Е. Алексеева № 2 (87) – Нижний Новгород, 2011, – С. 127-132.
26
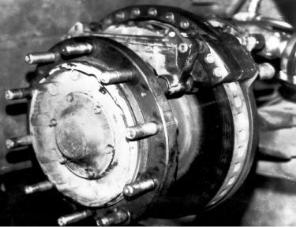
УДК 629.113
ВЛИЯНИЕ КОЭФФИЦИЕНТА ТРЕНИЯ НА ТРИБОТЕХНИЧЕСКИЕ ХАРАКТЕРИСТИКИ ПАР ТРЕНИЯ ДИСКОВОГО ТОРМОЗА
Турбин И.В., Соломатин Н.С., Сабитов М.С.
ГОУ ВПО «Тольяттинский государственный университет» Кафедра «Проектирование и эксплуатация автомобилей»
Современные требования к тормозным системам автомобилей предусматривают обеспечение максимально возможной эффективности торможения, управляемости и устойчивости движения автомобиля, высокой надежности и безотказности.
Выполнение данных требований возможно при решении задач расчетноэкспериментального подбора геометрических, физико-механических и фрикционноизносных характеристик пар трения тормозов. Как известно, дисковые тормоза обладают рядом преимуществ по сравнению с барабанными. Основные преимущества – стабильный тормозной момент, пропорциональный приводному усилию на скобе, меньшая масса. Дисковые тормоза применяются гораздо шире на легковых автомобилях, что связано с переходом на низкопрофильные шины и увеличением диаметра обода колеса.
В настоящее время разработаны работоспособные схемы конструкций, успешно применяемых на ряде грузовых автомобилей. Однако, тяжелые условия работы и необходимость обеспечения запаса прочности деталей дисковых тормозов большегрузных автомобилей не позволяют достичь максимального снижения их массы. Это связано с внутренним кольцевым пространством между ступицей и ободом колеса, ограничивающим размер диска. В тяжелых автомобилях размеры такого пространства не позволяют увеличить поверхность трения диска, по сравнению с барабанами, для которых возможно увеличение ширины.
Тем не менее, поиск решений продолжается, так например, проводилась разработка конструкции дискового тормоза для автобусов большого класса, с выполнением необходимых расчетов, изготовлением опытных образцов тормоза и проведением стендовых и дорожных испытаний. В ходе испытаний определены основные параметры и характеристики тормоза, внешний вид которого показан на рисунке 1.
Основные особенности и принцип действия разработанной конструкции: Однодисковый тормозной механизм с плавающей скобой, с клиновыми разжимными механизмами, с пневматическим приводом. Тормозной диск, закрепленный на ступице колеса, при торможении зажимается колодками. Тормозной момент передается от торцов колодок суппорту. Скоба тормоза плавающего типа, с односторонним приводом от двух клиновых разжимных механизмов, полностью разгружена от воздействия тормозного момента.
Скоба тормоза представляет собой замкнутую раму и состоит из активной и реактивной частей, расположенных хордально относительно тормозного диска и связанных
между собой тяговыми винтами, проходящими над окружностью диска. Перпендикулярное поверхностям трения диска перемещение скобы обеспечивается направляющими винтами, которые снабжены резиновыми кольцами. Винты с кольцами входят в направляющие отверстия балок и вворачиваются с обеих сторон охватывающего диск суппорта.
27
При подаче воздуха в тормозные камеры, давление на диафрагмы заставляет перемещаться клиновые механизмы, при этом создается приводное усилие на толкателях активной балки скобы. Одновременно с прижатием активной колодки, происходит перемещение реактивной балки и прижатие к диску реактивной колодки.
Механизмы привода снабжены автоматическими регуляторами зазора, которые срабатывают при определенной величине хода плунжера. Поворачиваясь за счет имеющейся на боковой поверхности винтовой канавки относительно направляющего штифта, плунжер совершает регулировочный ход, при этом зубья втулок смещаются относительно друг друга на один шаг. При обратном ходе плунжера под воздействием возвратной пружины, втулки поворачиваются на угол, соответствующий величине угла винтовой нарезки, за счет чего толкатель выдвигается на величину хода, соответствующую шагу резьбы его винтовой части. В таблице 1 приведены данные, необходимые для определения силовой характеристики тормоза.
|
|
|
|
Таблица 1 |
Технические характеристики автобуса большого класса |
|
|||
|
|
|
||
|
Наименование характеристик |
Значение |
||
Масса автобуса снаряженная, |
кг |
|
9600 |
|
Масса автобуса полная G а , |
кг |
|
17420 |
|
Нагрузка на переднюю ось, кг, при G a = 17420 кг |
6204 |
|||
|
||||
Нагрузка на заднюю ось, |
кг, |
при G a = 17420 кг |
11216 |
|
|
||||
Предельная вместимость, |
пасс. |
|
120 |
|
Максимальная скорость, |
км/час |
|
70 |
|
База L, м |
|
|
|
5,84 |
Высота центра тяжести h, м, |
при G a = 9600 кг/ при G a = 17420 кг |
0,9/1,2 |
||
|
||||
Координаты центра тяжести, |
м, |
до передней оси L 1 /задней оси L 2 |
3,76/2,08 |
|
Динамический радиус колеса |
r д , |
м |
0,445 |
По данным техническим характеристикам определяются расчетные геометрические и силовые параметры тормозного механизма. Тормозной механизм должен обеспечить необходимые значения замедления и тормозного пути транспортного средства в экстренной ситуации. Поэтому предварительный силовой расчет проводится для максимальной массы автобуса, при условии максимальных значений коэффициента сцепления шин с дорожным покрытием. В данном случае предварительный подбор силовой характеристики привода осуществляется для условий достижения максимальных величин касательных реакций при вращении заторможенного колеса на грани юза. Расчетные характеристики тормозного механизма приведены в таблице 2.
Необходимый тормозной момент с учетом перераспределения масс при торможении:
|
|
|
j |
h |
|
|
|||
|
rд G |
L2 |
|
|
|
|
|
||
|
g |
|
|
||||||
Μ max |
|
|
|
|
, |
(1) |
|||
|
|
|
|||||||
Т |
2 |
а |
L |
|
|
|
|
|
|
|
|
|
|
|
|
|
|
|
|
|
|
|
|
|
|
|
|
|
где: φ = 0,8 - коэффициент сцепления шин с дорогой; j = 6,0 м/c² - нормативное замедление. Тогда необходимое усилие привода скобы:
|
|
|
|
|
max |
|
МТmax |
|
|
|
|
|
|
|
Nпр |
|
, |
(2) |
|
|
|
|
|
|
|
||||
|
|
|
|
|
|
|
rэф 2 ср |
|
|
2 |
|
r3 |
r3 |
|
|
|
|
|
|
где: rэф |
|
|
н |
в |
- эффективный радиус трения диска. |
|
|||
3 |
r2 |
r2 |
|
||||||
|
|
|
н |
в |
|
|
|
|
|
28
Требуемое усилие на штоке пневмокамеры для клинового разжимного механизма:
р |
|
|
Nпр |
tg |
|
, |
(4) |
шт |
|
к |
|||||
|
|
nк |
|
|
|||
|
|
|
|
|
|
где: α к - угол клина, град.; n к - число приводных механизмов (пневмокамер).
|
|
|
Таблица 2 |
|
Технические характеристики тормозного механизма |
|
|
||
|
|
|
||
Параметр |
Ед. измерения |
Значение |
||
Наружный диаметр диска, |
|
мм |
420 |
|
Внутренний диаметр диска, |
|
мм |
240 |
|
Толщина диска |
|
мм |
40 |
|
Число вентиляционных каналов |
|
кол. |
40 |
|
Материал диска |
|
- |
СЧ мод. |
|
Площадь тормозной накладки |
|
м² |
210∙10 |
4 |
|
|
|
|
|
Расчетный коэффициент трения, |
μ ср |
- |
0,35 |
|
Число пневматических камер «тип»-12, n к |
кол. |
2 |
|
|
Угол клина |
|
град. |
6 |
|
Усилие привода на скобе, Nпр , |
при р=0,6 МПа/р=0,8 МПа |
кН |
80/100 |
|
|
|
|
|
|
Тормозной момент, Μ Т , при р=0,6 МПа/р=0,8 МПа |
кН∙м |
9,5/12,2 |
||
|
|
|
Таким образом, после определения основных силовых параметров тормозного механизма, разработана конструкция, выполнены рабочие чертежи деталей, изготовлены опытные образцы для стендовых и дорожных испытаний.
В ходе испытаний определены основные характеристики дискового тормоза, взаимосвязь параметров торможения в функции изменения коэффициента трения для различных материалов тормозных накладок. Для исследований изготовлены экспериментальные тормозные колодки из двух вариантов материалов: асбестосмоляной композии и металлокерамической на основе железа (в дальнейшем соответственно АСК и МК). Интерес для анализа представляют результаты, полученные в ходе проведения стендовых испытаний при одинаковых начальных условиях работы тормоза, таких как нагрузка, скорость вращения, геометрия и разных материалов накладок. Внешний вид тормоза, установленного для испытаний на стенде показан на рисунке 2. В общем случае при торможении происходит непрерывное изменение коэффициента трения во взаимосвязи с такими параметрами, как скорость, нагрузка, температура, которые в свою очередь также непрерывно меняются во времени.
На рисунке 3 представлены экспериментальные зависимости процессов торможения для различных типов материалов фрикционных накладок. Из графиков видно, что при одинаковых начальных условиях: начальной скорости вращения маховых масс стенда, давления воздуха в приводе, результаты значительно отличаются.
При этом видно, что время от начала торможения до полной остановки для графиков а) составляет 3,6 с, графиков б) 2,9 с. Характерно изменение тормозного момента, в первом случае происходит его непрерывное изменение – увеличение с уменьшением скорости вращения диска, во втором момент практически постоянен по скорости вращения.
С целью дальнейшего анализа были определены изменения коэффициента трения данных пар в зависимости от скорости и температуры, графические зависимости которых представлены на рисунках 4 и 5.
Как видно из представленных зависимостей, коэффициент трения для материала АСК изменяется весьма в широких пределах как в зависимости от скорости, так и от температуры. В этой связи задача точного определения коэффициента трения при составлении расчетной модели торможения является весьма сложной, при ее решении на каждом шаге расчета необходимо уточнение текущего значения коэффициента трения.
29