
- •ВВЕДЕНИЕ
- •ГЛАВА 1. ТЕХНОЛОГИЧЕСКАЯ СИСТЕМА ПРЕДПРИЯТИЯ
- •1.1. Производственная система предприятия: общее понятие, структура и классификация
- •1.1.1. Производство. Общая структура и тенденции развития.
- •1.1.2. Классификация производств
- •1.2. Технология и технологическая система предприятия
- •1.2.1. Технология.
- •1.2.2. Технологическая система предприятия
- •1.3. Основные закономерности развития технологических систем. Технологическое развитие фирмы
- •1.3.2. Технологические пределы и преемственность технологий.
- •1.3.3. Продуктовые и технологические нововведения, их взаимосвязь и влияние на развитие технологического процесса.
- •1.3.4. Технология и факторы производства.
- •1.3.5. Технология и производственная мощность предприятия.
- •1.6. Технологические уклады в системе мирового технико-экономического развития
- •1.7. Макротехнологии – общее понятие и развитие
- •ГЛАВА 2. СЫРЬЕВОЙ КОМПЛЕКС РОССИИ
- •2.1. Сырье: общее понятие, классификация и применение
- •2.2. Обогащение сырья
- •2.3. Комплексное использование сырья
- •2.4. Общая характеристика сырьевой базы России
- •ГЛАВА 3. МЕТАЛЛУРГИЧЕСКИЙ КОМПЛЕКС
- •3.1.Общая характеристика комплекса
- •3.2. Черная металлургия
- •3.2.1. Общая характеристика отрасли, ее состояние и роль в народном хозяйстве. Экспортные особенности.
- •3.2.4. Классификация сталей. Их свойства и примене-
- •3.3. Цветная металлургия
- •3.3.4. Титан: свойства и применение.
- •3.3.5. Никель: свойства и применение.
- •3.3.7. Порошковая металлургия. Общие сведения.
- •4.1. Общая характеристика и состояние комплекса
- •4.3. Литейное производство
- •4.3.1. Общие сведения.
- •4.3.2. Литье в песчано-глинистые формы.
- •4.3.3. Литье в оболочковые формы.
- •4.3.5. Изготовление отливок центробежным литьем.
- •4.3.7. Литье под давлением.
- •4.4. Обработка металла давлением
- •4.4.1. Прокатное производство.
- •4.4.3. Прессование.
- •4.5. Кузнечно-штамповочное производство
- •4.5.1. Ковка.
- •4.5.4. Особые способы листовой штамповки.
- •4.6. Обработка конструкционных материалов резанием
- •4.6.1. Общие сведения.
- •4.6.3. Основные механизмы и узлы станков.
- •4.6.4. Токарные станки.
- •4.6.5. Сверлильные и расточные станки.
- •4.6.6. Фрезерные станки.
- •4.6.8. Обработка заготовок на шлифовальных стан-
- •4.6.9. Отделочные методы обработки.
- •ГЛАВА 5. ПЛАСТМАССЫ
- •5.1. Основные виды, свойства и применение
- •5.2. Основные виды термопластичных пластмасс, их свойства и применение
- •5.3. Основные виды термореактивных пластмасс, их свойства и применение
- •5.4. Производство изделий из пластмасс
- •ГЛАВА 6. СТРОИТЕЛЬНЫЙ КОМПЛЕКС
- •6.1. Общая структура комплекса, его развитие и состояние
- •6.2. Строительные материалы
- •6.2.1. Классификация строительных материалов.
- •6.2.2. Основные свойства строительных материалов
- •6.2.3. Природные каменные материалы.
- •6.2.4. Искусственные керамические и каменные материалы.
- •6.2.5. Древесные материалы.
- •6.2.7. Асбестоцементные изделия.
- •6.2.8. Органические вяжущие материалы и изделия на их основе.
- •6.2.9. Стекло и изделия из стекла.
- •6.3. Строительство
- •6.3.1. Принципы классификации зданий. Основные части зданий и их конструкционное выполнение.
- •6.3.2. Проектирование строительства. СНиП и другие нормативные документы.
- •6.3.3. Организация и порядок проведения строительных работ.
- •6.4. Инженерное обеспечение зданий и сооружений
- •6.4.1. Система водоснабжения.
- •6.4.2. Система канализации.
- •6.4.3. Системы теплоснабжения.
- •6.4.4. Системы вентиляции и кондиционирования.
- •ГЛАВА 7. МЕЖОТРАСЛЕВЫЕ ТЕХНОЛОГИЧЕСКИЕ СИСТЕМЫ. СВАРКА И ПАЙКА МЕТАЛЛОВ
- •7.1. Сварка
- •7.1.1. Общие сведения.
- •7.1.2. Электродуговая сварка.
- •7.1.3. Электрическая контактная сварка.
- •7.1.4. Газовая сварка (рис. 7.4).
- •7.1.5. Сварка лазерным лучом
- •7.1.7. Прочие виды сварки.
- •7.2. Пайка
- •ГЛАВА 8. ТОПЛИВНО-ЭНЕРГЕТИЧЕСКИЙ КОМПЛЕКС
- •8.1. Общие тенденции развития
- •8.2. Добыча и фракционная перегонка нефти
- •8.3. Нефтепродукты
- •ТЕРМИНОЛОГИЧЕСКИЙ СЛОВАРЬ
- •БИБЛИОГРАФИЧЕСКИЙ СПИСОК
- •ОГЛАВЛЕНИЕ
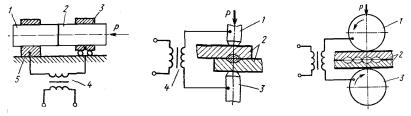
231
Аргонодуговую сварку применяют при сварке нержавеющих и жаропрочных сталей, никеля, титана, алюминия, магния и др. цветных металлов и сплавов.
7.1.3. Электрическая контактная сварка. Электрическая контактная сварка находит широкое применение в машиностроении и в приборостроении. Она основана на том, что при прохождении тока через соединяемые поверхности он встречает максимальное сопротивление в месте их соединения. Здесь происходит разогрев металла до пластического состояния и оплавление. Поверхности металлов в точке разогрева сжимаются и происходит диффузия металлов. Основными способами контактной сварки являются стыковая, шовная и точечная (рис. 7.3).
При стыковой сварке (рис. 7.3, а) свариваемые детали 1–2 (стержни, полосы, рельсы, трубы) закрепляют в медных зажимах машины. Зажим 3 установлен на подвижной плите, перемещающейся по направляющим станины, а зажим 5 укреплен на неподвижной плите. Вторичная понижающая обмотка трансформатора 4 соединена с плитами медными гибкими шинами.
а |
б |
в |
Рис. 7.3. Основные схемы контактной сварки:
а – стыковая; б – точечная; в – шовная
Стыковую сварку разделяют на сварку сопротивлением и сварку оплавлением.
232
При сварке сопротивлением заготовки соединяются и включается электрический ток. В зоне контакта электрический ток встречает наибольшее сопротивление и выделяется наибольшее количество теплоты, торцы заготовок нагреваются, и в зоне нагрева металл переходит в пластическое состояние. После этого ток отключают, заготовки сжимают, происходит диффузия металлов и в результате получается сварное соединение. Сварку сопротивлением применяют для неответственных конструкций небольшого сечения (диаметром до 20–25 мм), изготовляемых из низкоуглеродистых сталей.
При сварке оплавлением заготовки сближают при включенном трансформаторе. По мере их сближения обеспечивается контакт по всему поперечному сечению, и поверхности стыка, за счет выделения теплоты при прохождении тока, равномерно оплавляются. После этого заготовки сжимаются и образуется сварной шов по всей плоскости. Стыковую сварку оплавлением применяют при соединении железнодорожных рельсов, газо- и нефтепроводов.
Точечную сварку применяют для соединения заготовок, свариваемых внахлестку в отдельных точках (рис. 7.3, б). Свариваемые заготовки 2 для обеспечения их контакта зажимаются силой между двумя стержневыми медными электродами 1 и 3, к которым подводится электрический ток от вторичной обмотки трансформатора 4. Между электродами, в месте контакта заготовок, имеющем наиболее высокое сопротивление, поднимается температура, металл переходит в пластичное или расплавленное состояние, и образуется сварная точка. Массивные медные электроды практически не нагреваются, так как сопротивление меди невысокое.
В качестве источника электрической энергии обычно используется однофазный трансформатор переменного тока. Синхронизация работы механизмов сжатия и источника электрического тока обеспечивается электронными программными устройствами, задающими цикл работы машины. Точечную сварку применяют для соединения заготовок из углеродистых и легированных конструкционных сталей, алюминиевых, медных, титановых сплавов.
При шовной или роликовой сварке (рис. 7.3, в) свариваемые заготовки 2, соединяемые внахлестку, зажимают постоянной силой между двумя медными электродами 1, 3, выполненными в виде вращающихся роликов. Роликовая сварка аналогична точечной, но она предназначена для получения не-
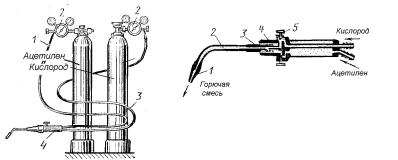
233
прерывного сварного шва. Шовную сварку применяют для получения герметичных соединений емкостей, баков, сосудов высокого давления и т.д. Толщина свариваемых заготовок может быть от 0,001 до 3 мм.
7.1.4. Газовая сварка (рис. 7.4). При газовой сварке в качестве источника теплоты используют газовое пламя, образующееся при сгорании горючего газа в атмосфере кислорода.
а |
б |
Рис. 7.4. Оборудование газосварочного рабочего места:
а – схема питания от баллонов: 1 – шланг подачи ацетилена; 2 – регулятор давления газа; 3 – шланг подачи кислорода; 4 – сварочная горелка;
б – схема инжекторной горелки: 1 – мундштук; 2 – ствол горелки; 3 – смесительная камера; 4 – инжектор; 5 – вентиль
Применяют различные горючие газы – ацетилен, водород, природные газы, пропан, бутан, пары бензина. Самую высокую температуру пламени (3200 °С) обеспечивает ацетилен, поэтому аце- тилено-кислородное пламя нашло наибольшее применение.
234
Питание газовой горелки ацетиленом и кислородом осуществляется преимущественно от баллонов – ацетиленового (белого цвета) и кислородного (голубого цвета), поставляемых на место сварки.
Для получения пламени ацетилен и кислород подают из баллонов, снабженных газовыми регуляторами давления, в горелку. Применяют, главным образом, горелки инжекторного типа (рис. 7.4, б). Суть его заключается в следующем.
Кислород, подаваемый под давлением 0,1–0,4 МПа, выходит из инжектора 4 с большой скоростью и создает разрежение в смесительной камере 3. За счет этого в нее подсасывается ацетилен. Здесь он смешивается с кислородом, и образующаяся горючая смесь поступает по трубке наконечника к выходному отверстию мундштука. Сгорание смеси происходит в сварочном пламени на выходе из мундштука. Тепловую мощность пламени регулируют сменными наконечниками горелки с разным расходом газа.
7.1.5. Сварка лазерным лучом (рис. 7.5). При сварке лазерным лучом источником тепловой энергии служит сконцентрированный световой луч, получаемый в специальных установках, называемых лазерами. В настоящее время основное применение имеют рубиновые лазеры с искусственным рубином.
Такой лазер состоит из цилиндрического рубинового стержня 1, ксеноновой лампы 2, охлаждающей системы 3 и линзы 4. Торцы стержня отполированы и посеребрены. Торец, служащий для выхода наружу светового луча, частично прозрачен. При вспышке ксеноновой лампы, питаемой разрядным током конденсаторов, атомы хрома рубинового кристалла переходят из нормального состояния в возбужденное. Однако через несколько миллисекунд они снова возвращаются в исходное состояние, излучая фотоны монохроматического красного света. Их поток вдоль оси стержня вызывает излучение новых фотонов, которые попеременно отражаются от зеркальных торцовых граней, увеличивая этим интенсивность общего излучения. При накоплении определенного уровня фотонов они, в виде потока красного света, прорываются через полупрозрачный торец стержня наружу. Пройдя через линзу 4, сфокусированный пучок 5 попадает на заготовку 6. Продолжительность импульса излучения лазерного луча равна тысячным и миллионным долям секунды.
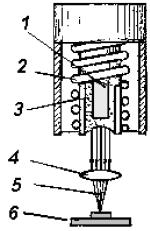
235
Рис. 7.5. Схема сварки световым лазерным лучом:
1 – рубиновый стержень, 2 – ксеноновая лампа, 3 – охлаждающая система, 4 – линза, 5 – луч, 6 – заготовка
Точечной сваркой лазерного луча можно сваривать различные металлы толщиной до 0,5 мм. Его применяют также для получения отверстий в твердых сплавах, тугоплавких металлах, алмазах, рубинах и др. материалах.
7.1.6. Плазменно-дуговая сварка. Электронной плазмой называют ионизированный газ, состоящий из нейтральных атомов и молекул, ионов и электронов. Для получения плазменного пламени через электрическую дугу (рис. 7.6), горящую между анодом (+) и катодом (-), пропускают поток газа. Сжатый в сопле 3 газ, под воздействием электрической дуги, ионизируется и превращается в плазму с температурой 20 000–30 000º С. Различают плазменную дугу прямого и косвенного действия.