
- •ВВЕДЕНИЕ
- •ГЛАВА 1. ТЕХНОЛОГИЧЕСКАЯ СИСТЕМА ПРЕДПРИЯТИЯ
- •1.1. Производственная система предприятия: общее понятие, структура и классификация
- •1.1.1. Производство. Общая структура и тенденции развития.
- •1.1.2. Классификация производств
- •1.2. Технология и технологическая система предприятия
- •1.2.1. Технология.
- •1.2.2. Технологическая система предприятия
- •1.3. Основные закономерности развития технологических систем. Технологическое развитие фирмы
- •1.3.2. Технологические пределы и преемственность технологий.
- •1.3.3. Продуктовые и технологические нововведения, их взаимосвязь и влияние на развитие технологического процесса.
- •1.3.4. Технология и факторы производства.
- •1.3.5. Технология и производственная мощность предприятия.
- •1.6. Технологические уклады в системе мирового технико-экономического развития
- •1.7. Макротехнологии – общее понятие и развитие
- •ГЛАВА 2. СЫРЬЕВОЙ КОМПЛЕКС РОССИИ
- •2.1. Сырье: общее понятие, классификация и применение
- •2.2. Обогащение сырья
- •2.3. Комплексное использование сырья
- •2.4. Общая характеристика сырьевой базы России
- •ГЛАВА 3. МЕТАЛЛУРГИЧЕСКИЙ КОМПЛЕКС
- •3.1.Общая характеристика комплекса
- •3.2. Черная металлургия
- •3.2.1. Общая характеристика отрасли, ее состояние и роль в народном хозяйстве. Экспортные особенности.
- •3.2.4. Классификация сталей. Их свойства и примене-
- •3.3. Цветная металлургия
- •3.3.4. Титан: свойства и применение.
- •3.3.5. Никель: свойства и применение.
- •3.3.7. Порошковая металлургия. Общие сведения.
- •4.1. Общая характеристика и состояние комплекса
- •4.3. Литейное производство
- •4.3.1. Общие сведения.
- •4.3.2. Литье в песчано-глинистые формы.
- •4.3.3. Литье в оболочковые формы.
- •4.3.5. Изготовление отливок центробежным литьем.
- •4.3.7. Литье под давлением.
- •4.4. Обработка металла давлением
- •4.4.1. Прокатное производство.
- •4.4.3. Прессование.
- •4.5. Кузнечно-штамповочное производство
- •4.5.1. Ковка.
- •4.5.4. Особые способы листовой штамповки.
- •4.6. Обработка конструкционных материалов резанием
- •4.6.1. Общие сведения.
- •4.6.3. Основные механизмы и узлы станков.
- •4.6.4. Токарные станки.
- •4.6.5. Сверлильные и расточные станки.
- •4.6.6. Фрезерные станки.
- •4.6.8. Обработка заготовок на шлифовальных стан-
- •4.6.9. Отделочные методы обработки.
- •ГЛАВА 5. ПЛАСТМАССЫ
- •5.1. Основные виды, свойства и применение
- •5.2. Основные виды термопластичных пластмасс, их свойства и применение
- •5.3. Основные виды термореактивных пластмасс, их свойства и применение
- •5.4. Производство изделий из пластмасс
- •ГЛАВА 6. СТРОИТЕЛЬНЫЙ КОМПЛЕКС
- •6.1. Общая структура комплекса, его развитие и состояние
- •6.2. Строительные материалы
- •6.2.1. Классификация строительных материалов.
- •6.2.2. Основные свойства строительных материалов
- •6.2.3. Природные каменные материалы.
- •6.2.4. Искусственные керамические и каменные материалы.
- •6.2.5. Древесные материалы.
- •6.2.7. Асбестоцементные изделия.
- •6.2.8. Органические вяжущие материалы и изделия на их основе.
- •6.2.9. Стекло и изделия из стекла.
- •6.3. Строительство
- •6.3.1. Принципы классификации зданий. Основные части зданий и их конструкционное выполнение.
- •6.3.2. Проектирование строительства. СНиП и другие нормативные документы.
- •6.3.3. Организация и порядок проведения строительных работ.
- •6.4. Инженерное обеспечение зданий и сооружений
- •6.4.1. Система водоснабжения.
- •6.4.2. Система канализации.
- •6.4.3. Системы теплоснабжения.
- •6.4.4. Системы вентиляции и кондиционирования.
- •ГЛАВА 7. МЕЖОТРАСЛЕВЫЕ ТЕХНОЛОГИЧЕСКИЕ СИСТЕМЫ. СВАРКА И ПАЙКА МЕТАЛЛОВ
- •7.1. Сварка
- •7.1.1. Общие сведения.
- •7.1.2. Электродуговая сварка.
- •7.1.3. Электрическая контактная сварка.
- •7.1.4. Газовая сварка (рис. 7.4).
- •7.1.5. Сварка лазерным лучом
- •7.1.7. Прочие виды сварки.
- •7.2. Пайка
- •ГЛАВА 8. ТОПЛИВНО-ЭНЕРГЕТИЧЕСКИЙ КОМПЛЕКС
- •8.1. Общие тенденции развития
- •8.2. Добыча и фракционная перегонка нефти
- •8.3. Нефтепродукты
- •ТЕРМИНОЛОГИЧЕСКИЙ СЛОВАРЬ
- •БИБЛИОГРАФИЧЕСКИЙ СПИСОК
- •ОГЛАВЛЕНИЕ
51
была практически перестроена на энергосырьевое обеспечение промышленно-развитых стран.
В 2007 г. в России было произведено 5% мирового выпуска стали, при этом около половины пошло на экспорт (10% мировой торговли). Доля России в мировом производстве основных видов цветных металлов (алюминий, никель, медь, цинк, свинец, олово) составляет около 8,5%. На экспорт отправляется около 80% их производства и 70% редких металлов. В экспорте черных металлов 60% занимают полуфабрикаты (слябы, чугун, лом, руда и т.д.), в экспорте цветных металлов 80% приходится на первичные, т.е. не прошедшие обработку, металлы и лишь 10% – на прокат и металлоизделия. Следствием перестройки металлургии на выпуск первичных металлов стало резкое сокращение производства металлопродукции, т.е. металлоизделий и различного вида проката.
Таким образом, в результате спада производства в металлопотребляющих отраслях, нарушения и разрыва производст- венно-хозяйственных связей в стране, а также удорожания топлива, перевозок и электроэнергии произошла коренная перестройка металлургического комплекса на выпуск первичных металлов и поставку их на экспорт. Основными металлами, поставляемыми на экспорт, являются черные металлы (10% от общего экспорта), алюминий, медь, никель, металлы платиновой группы.
Значительную долю в составе экспорта занимает также металлолом (6-14 млн т в 2000–2007 гг.), вывоз которого в последние годы вызывает острый дефицит в отечественной металлургии.
3.2.Черная металлургия
3.2.1.Общая характеристика отрасли, ее состояние и роль в народном хозяйстве. Экспортные особенности. Чер-
ные металлы – сталь, чугуны и др. сплавы железа с углеродом являются основным конструкционным материалом, что обусловлено широким спектром их физико-механических свойств и невысокой, относительно других материалов с аналогичными свойствами, стоимостью.
Производство черных металлов в СССР выросло за 70 лет более чем в 30 раз. Основными производителями были РСФСР – 57% и УССР – 35%. После распада СССР началось падение производства черных металлов.
Динамика производства черных металлов (рис. 3.1) показывает, что их наибольший выпуск в России был достигнут в 1988 г., затем началось падение производства. В 1992–94 гг. его темпы
52
достигли 16–17%, однако с 1995 г. предприятия переориентировались на экспорт и темпы падения снизились: в 1998 г. был достигнут минимум – 52% от 1990 г., с 1999 г. начался восстановительный рост и в 2007 г. индекс металлургического производства и производства готовых металлических изделий составил 98,2% к 1992 г.
С 1990 по 2007 год экспорт черных металлов вырос в несколько раз, отходов и металлолома – с 433 до 9315 тыс. т, чугуна – с 1931 до 5805 тыс. т, ферросплавов – с 203 до 791 тыс. т, отходов и металлолома – с 433 до 9315, полуфабрикатов
– с 3675 до 144492 тыс. т и т.д., на экспорт идет более 60% выпуска черных металлов.
По общему объему выплавки стали Россия занимает четвертое место в мире (табл. 3.1), однако по технологическим параметрам производства металлов и их качеству она уступает промышленно развитым странам.
53
Рис. 3.1 см. Аосновы отр техн сбор 2010а граф

54
Мартеновское производство стали в его общем объёме составляет в России 17%, в то время как в США – 2,5%, в Японии – его нет, в Германии сходит на нет. Около 60% стали в России разливается в слитки, в то время как в США, Японии и Германии уже более 90% перерабатывается на машинах непрерывного литья.
Таблица 3.1
Динамика производства стали в мире
|
2000 |
2001 |
2002 |
2003 |
2004 |
2005 |
2006 |
2007 |
|
|
|
|
|
|
|
|
|
ВСЕГО |
847,7 |
850 |
904 |
969 |
1067 |
1146 |
1250 |
1344 |
Китай |
127 |
151 |
182 |
222 |
280 |
355 |
423 |
489 |
Япония |
106 |
102 |
107 |
110 |
113 |
112 |
116 |
120 |
США |
102 |
90 |
92 |
94 |
100 |
95 |
99 |
98 |
Россия |
59 |
59 |
60 |
61 |
66 |
66 |
71 |
72 |
Германия |
46 |
45 |
46 |
45 |
46 |
45 |
47 |
48 |
Ю.Корея |
43 |
44 |
45 |
46 |
47 |
48 |
48 |
51 |
Украина |
31 |
33 |
34 |
37 |
39 |
39 |
40 |
42 |
Бразилия |
28 |
27 |
30 |
31 |
32 |
31 |
31 |
34 |
Индия |
27 |
27 |
29 |
32 |
33 |
46 |
49 |
53 |
Италия |
27 |
26 |
26 |
27 |
29 |
29 |
32 |
32 |
Франция |
21 |
20 |
20 |
20 |
21 |
19 |
20 |
29 |
Тайвань |
17 |
17 |
18 |
19 |
19 |
19 |
20 |
20 |
Канада |
17 |
16 |
15 |
16 |
16 |
15 |
15 |
16 |
Испания |
16 |
16 |
16 |
16 |
18 |
18 |
18 |
19 |
Мексика |
16 |
13 |
14 |
15 |
17 |
16 |
16 |
18 |
Великобритания |
15 |
13 |
12 |
13 |
14 |
13 |
14 |
14 |
Турция |
14 |
15 |
16 |
18 |
20 |
21 |
23 |
26 |
Др. страны |
135 |
135 |
140 |
146 |
158 |
157 |
165 |
171 |
Ист.: http//www.promwest.info/3543464
Доля сортовой металлопродукции в прокате составляет около 60%, листового проката с покрытиями – 4% (в названных странах, соответственно, 39,7, 39,6, 31,2 и 31,3, 16, 15,2%). Тру-
дозатраты изготовления 1 т проката составляют 8–16 чел./час, а в США на интегрированных предприятиях – 6–12, на минизаводах – 1–2 чел./часа1. Удельный вес электростали в мире составляет 33,9% (1998), ее среднегодовой рост составляет 3%, в то время как в России, занимающей 4 место по производ-
1 Молотилов Б., Бродов А., Маторин В. Тенденции развития черной металлургии // Экономист.– 1997.– № 3.

55
ству электроэнергии в мире после США, Китая и Японии, электросталь занимает лишь 26%1.
В последние годы технологическая система черной металлургии несколько улучшилась – доля кислородно-конвертер- ного производства увеличилась до 57%, непрерывное литье в общем объеме выплавки стали увеличилось до 68%. Переключение предприятий черной металлургии и металлообработки на экспорт помогло сохранить отрасль, хотя и с упрощением технологии, на уровне, обеспечивающем России четвертое место по производству стали в мире.
Крупнейшим потребителем железной руды является Азия: три основные страны-импортеры железной руды – Китай, Япония и Республика Корея. Крупнейшим поставщиком железной руды является Бразилия2. Россия импортирует концентраты и руду преимущественно из стран СНГ (11 млн т в 2006 г.), экспорт железных руд и концентратов в дальнее зарубежье составляет более 10 млн т.
Недостаток инвестиций ограничивает возможности отрасли перейти на более современные технологии, которые обеспечили бы расширение сегмента рынка, рост дополнительных доходов и конкурентоспособность на мировом рынке. Устаревшие технологии делают продукцию неконкурентоспособной не только на внешнем, но и, в присутствие импорта, на внутреннем рынке. Поэтому важнейшей задачей комплекса является повышение уровня технологического обеспечения отрасли.
3.2.2. Чугун. Производство, классификация и приме-
нение. Железоуглеродистые сплавы делятся на стали – с содержанием углерода менее 2,14% и чугуны – с содержанием углерода более 2,14%. Чугуны отличаются большей твердостью, хрупкостью, хорошо льются, плохо обрабатываются резанием, не обрабатываются давлением.
Основным способом производства чугуна является доменный процесс, суть которого состоит в восстановлении железа из оксидов, в превращении в шлак и сливе пустой породы. При этом углерод кокса растворяется в железе и его науглероживает. Исходными материалами для производства чугуна яв-
ляются железные руды, топливо и флюсы. Смесь, составлен-
ная из перечисленных материалов, называется шихтой. Наиболее применимы руды с содержанием железа не
менее 40% – бурый, шпатовый, красный и магнитный железняки, представляющие собой различные виды соединения железа с
1БИКИ. – 1999. – 9 дек.; Россия в цифрах... 2008.– 224 с.
2БИКИ.–1999.– 18 мая.– С.14–15.

56
кислородом, поэтому сущность доменного процесса состоит в восстановлении железа углеродом.
Топливом служит кокс и природный газ. Кокс пред-
ставляет собой продукт высокотемпературной перегонки каменного угля без доступа воздуха, при которой выплавляются смолы и содержание углерода повышается до 95–99%.
Флюсы. В железных рудах и в золе, получающейся при сгорании кокса, содержится глинозем, кремнезем и другие элементы, которые могут создать в чугуне вредные примеси. Для их удаления в шихту добавляется флюс – материал, реагирующий с примесями и превращающий их в шлак. Как правило, для этой цели используется известняк.
Для повышения эффективности доменного процесса проводят подготовку руды к плавке – дробление крупных кусков, промывку – при содержании песчаноглинистых пород, агломерацию (спекание мелкой руды, смешанной с топливом), окатывание (обработку рудного концентрата известью и связующим материалом с последующей сушкой и обжигом получившихся комков – окатышей), магнитное и другие виды обогащения. Для магнитного обогащения используют магнитные сепараторы (рис. 3.2) – оборудование, в котором измельченная руда перемещается в электромагнитном поле. Железосодержащие мелкие куски притягиваются электромагнитом, пустая порода по инерции отсеивается. Производство чугуна осуществляется в доменной печи – непрерывно действующем агрегате шахтного типа (рис. 3.3). Шихта подается в доменную печь сверху с помощью наклонного подъемника.
Пустая
порода
Руда
Рис. 3.2. Электромагнитный сепаратор Воздух поступает в печь через фурмы (устройства для
дутья) 8, расположенные в фурменной части горна 5. Шахта печи 2 имеет вид усеченного конуса, поэтому шихта свободно опускается от колошника 1 в более горячие зоны 2, 3, 4, где последовательно идут процессы удаления влаги, подсушки, разложение гидратов, карбонатов и т.д.
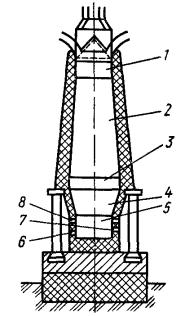
57
Расплавленная пустая порода вместе с флюсами образует шлак. Так как его плотность меньше чугуна, то он располагается выше чугуна и сливается через верхнюю летку (отверстие) 7, а более тяжелый расплавленный чугун сливается через нижнюю летку 6.
Чугуны подразделяются на передельные (около 80% выпуска) – идут на переплавку в сталь, литейные (около 20%) – используются для производства отливок и специальные – с высоким содержанием кремния и марганца, иначе называемые
ферросплавами. По назначению чугуны подразделяются:
1) на серые – с высокими
Рис. 3.3. Доменная печь механическими свойствами, широко применяются для производ-
ства станин, зубчатых колес, корпусов и т.д. Маркируются буквами СЧ, затем следует число, показывающее предел прочности на разрыв, например, СЧ15 – имеет предел прочности 15 кгс/мм2;
2)на ковкие – с лучшими механическими свойствами, применяют для изготовления деталей автомобилей, тракторов
ит.д. Маркируются буквами КЧ, затем следует число, показывающее предел прочности на разрыв, второе число показывает
относительное удлинение образца в % к первоначальной длине, например, КЧ 30–6 – выдерживает нагрузку 30 кгс/мм2 и может увеличиваться по длине на 6%.;
3)на высокопрочные – получаются с добавлением модификаторов или присадок, например, магния, что повышает их прочность. Маркируются словом ВЧ, далее так же, как в предыдущем случае. Пример: ВЧ–60–2;.
4)на различные специальные чугуны, легированные другими металлами и используемые для легирования и раскисления стали.
Чугуны широко поставляются на экспорт: в среднем 300 – 400 тыс. т в месяц по цене 120 долл. за тонну. В 1994 г. на российский чугун была введена антидемпинговая пошлина в виде разницы цены товара и минимальной цены 149 экю за тонну.
58
3.2.3. Сталь, ее свойства, производство и примене-
ние. Сталь по сравнению с чугуном имеет более высокие механические и технологические свойства – обрабатывается давлением, резанием, хорошо льется. Она является основным видом конструкционных материалов в промышленности и строительстве. На рис. 3.4 представлена схема сталеплавильного производства.
Максимум производства стали – 89,7 млн т был достигнут в 1990 г., затем началось падение производства – до 43,7 млн т в 1998 г., с 1999 г. начался подъем и в 2007 г. ее производство составило 62,8 млн т или 70% от 1990 г., в том числе производство кислородно-конвертерной стали –165%, электростали – 75%. Выпуск готового проката составил 70%, стальных труб – 51%.
Исходными материалами для производства стали служат: передельный чугун, металлолом (скрап), отходы металлургического производства, при этом в промышленно развитых странах Запада использование металлолома носит более приоритетный характер, чем чугуна, так как это приносит меньше экологических убытков, дает более дешевую продукцию и возможность получения сразу легированных сталей.
Задача плавки состоит в удалении углерода и примесей
– фосфора, серы, кремния и др. Процесс плавки состоит из трех этапов:
1.В расплавленной шихте под воздействием вдуваемого кислорода или кислорода добавляемой руды окисляются и всплывают в виде шлака примеси.
2.Углерод окисляется кислородом и удаляется с поверхности, при этом сталь как бы кипит.
Рис. 3.4 . Передел чугуна в сталь. Новолипецкий металлургический зав
см. Аосновы отр техн сбор 2010а граф
59
3. Так как при продувании часть кислорода соединилась с железом, производится ее раскисление путем ввода ферромарганца, ферросилиция и ферроалюминия. Раскисленная сталь при разливке не кипит и обозначается при маркировке как сп, нераскисленная сталь после застывания содержит пузырьки газа и называется кипящей (кп), промежуточная – полуспокойная (пс). Основными способами получения стали являются мартеновский, кислородно-конвертерный и электротермический с постепенным уменьшением доли мартена. На Ново-Оскольском комбинате применена схема прямого восстановления железа из руд, при которой сталь производится из руды, минуя стадию получения чугуна.
Производство стали в кислородных конвертерах.
В кислородных конвертерах выплавляется большая часть стали. Сущность кислородно-конвертерного способа плавки стали состоит в том, что через расплавленный и залитый в конвертер чугун продувается технически чистый кислород, который вступает в реакцию с углеродом чугуна и примесями, переводит их в шлак и отходящие газы.
Конвертер (рис. 3.5) представляет собой стальной сосуд грушевидной формы. Наружная часть – кожух изготавливается из толстолистовой стали. Внутренняя часть футерована (выложена) огнеупорным материалом. Конвертер опирается на стойки и может поворачиваться при сливке стали и шлака.
Подвод кислорода под давлением осуществляется с помощью фурмы. Сначала в конвертер загружают холодные материалы: стальной скрап (металлолом), известь, железную руду, затем заливают расплавленный чугун. После заливки, через охлаждаемую медную трубку (фурму) подается под давлением кислород. Необходимая температура плавки при этом достигается за счет сгорания углерода чугуна и примесей.
Завершающей стадией является раскисление стали, которое производится для удаления из расплава кислорода, присутствующего в нем в виде оксидов железа. Для раскисления стали в ее расплав загружают ферромарганец, ферросилиций или алюминий.
По сравнению с мартеновским конвертерный способ производства стали отличается высокой производительностью (процесс длится 50–60 мин., в то время как мартеновский – до 12 час.), лучшими экологическими свойствами, так как не используется топливо, и требует меньше капвложений. Сталь получается несколько хуже мартеновской.

60
Рис. 3.5. Кислородный конвертер
Мартеновский способ получения стали. Мартенов-
ская печь представляет собой пламенную печь (рис. 3.6), в которой над плавильным пространством достигается необходимая температура за счет сгорания газа, предварительно нагретого в регенераторах-теплообменниках
Газ и обогащенный кислородом воздух проходят через регенераторы – массивные конструкции из огнеупорного кирпича (на рис. 3.6 – справа) и по каналам 2 поступают в плавильное пространство печи. Здесь газ и воздух смешиваются и сгорают, образуя пламя высокой температуры. Продукты сгорания по каналам 1 поступают во вторую пару регенераторов (на рис. 3.6 – слева), нагревают их и выходят в дымовую трубу. Затем клапаны переключаются, кислород и газ направляются через нагретые регенераторы, нагреваются и поступают в плавильное пространство. По мере охлаждения регенераторов направление газа и воздуха снова меняют на обратное, и процесс повторяется. Таким образом, газ и воздух при работе печи попеременно переходят через нагреваемые то левые, то правые регенераторы, что дает возможность достичь необходимой температуры плавки за счет предварительного нагрева вдуваемых газа и воздуха за счет отходящих газов.

61
Рис. 3.6. Схема мартеновской печи
Недостаток мартена состоит в том, что, во-первых, он требует затрат на энергоресурсы, во-вторых, их сжигание загрязняет атмосферу, в-третьих, производительность его ниже, чем в конвертерах. Поэтому в Японии, Англии, Германии мартены заменены конвертерами, в России проведены работы по их модернизации, однако проблема их замены еще остается
Плавка стали в электропечах. Плавка стали происхо-
дит в печах, нагреваемых под воздействием электрического тока. Печи подразделяются на электродуговые, где плавка происходит за счет электрической дуги, возникающей между шихтой и графитовыми электродами, и индукционные, где плавка осуществляется нагревом шихты за счет индукции вихревых токов.
Преимущество: быстрая нагреваемость, контролируемость процесса, возможность создания вакуума или установленной определенной газовой среды. Получают сталь высокого качества и заданного состава, так как исключаются примеси. В настоящее время этот способ широко применяют для выплавки
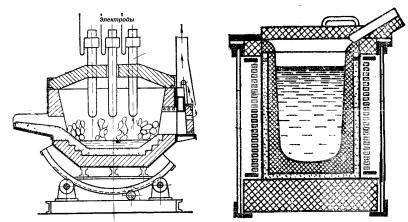
62
высококачественных углеродистых и легированных сталей, а также ферросплавов. В 2007 г. электротехническая сталь составила 26% общего выпуска стали.
Электродуговая сталеплавильная печь (рис. 3.7,а)
представляет собой стальной цилиндр, выложенный огнеупорным кирпичом. Сверху вставлены три графитовых электрода. При пропускании электрического тока между ними и шихтой возникает вольтова дуга и происходит нагрев металла.
|
|
|
Электроды |
а |
б |
|
|
|
|
|
|
|
|
|
|
|
|
Рис. 3.7. Схема устройства электродуговой (а) и индукционной (б) печей
Индукционная сталеплавильная печь (рис. 3.7,б) со-
стоит из тигля (сосуда, выложенного огнеупорным кирпичом) и водоохлаждаемого индуктора. При прохождении по индуктору тока высокой частоты (500–2000 кГц) образуется электромагнитный поток, который индуцирует в металлической шихте мощные вихревые токи, нагревающие ее до расплавления (устройство напоминает домашнюю микроволновую печь). По окончании плавки сливается сначала шлак (верхний слой), затем сталь.
Индукционные печи по сравнению с дуговыми обладают рядом преимуществ:
а) отсутствие дуги позволяет выплавлять металлы с малым содержанием углерода и газов;
б) возникающие электродинамические силы перемешивают жидкий металл, способствуя выравниванию химического состава и всплыванию неметаллических включений;