
- •ВВЕДЕНИЕ
- •ГЛАВА 1. ТЕХНОЛОГИЧЕСКАЯ СИСТЕМА ПРЕДПРИЯТИЯ
- •1.1. Производственная система предприятия: общее понятие, структура и классификация
- •1.1.1. Производство. Общая структура и тенденции развития.
- •1.1.2. Классификация производств
- •1.2. Технология и технологическая система предприятия
- •1.2.1. Технология.
- •1.2.2. Технологическая система предприятия
- •1.3. Основные закономерности развития технологических систем. Технологическое развитие фирмы
- •1.3.2. Технологические пределы и преемственность технологий.
- •1.3.3. Продуктовые и технологические нововведения, их взаимосвязь и влияние на развитие технологического процесса.
- •1.3.4. Технология и факторы производства.
- •1.3.5. Технология и производственная мощность предприятия.
- •1.6. Технологические уклады в системе мирового технико-экономического развития
- •1.7. Макротехнологии – общее понятие и развитие
- •ГЛАВА 2. СЫРЬЕВОЙ КОМПЛЕКС РОССИИ
- •2.1. Сырье: общее понятие, классификация и применение
- •2.2. Обогащение сырья
- •2.3. Комплексное использование сырья
- •2.4. Общая характеристика сырьевой базы России
- •ГЛАВА 3. МЕТАЛЛУРГИЧЕСКИЙ КОМПЛЕКС
- •3.1.Общая характеристика комплекса
- •3.2. Черная металлургия
- •3.2.1. Общая характеристика отрасли, ее состояние и роль в народном хозяйстве. Экспортные особенности.
- •3.2.4. Классификация сталей. Их свойства и примене-
- •3.3. Цветная металлургия
- •3.3.4. Титан: свойства и применение.
- •3.3.5. Никель: свойства и применение.
- •3.3.7. Порошковая металлургия. Общие сведения.
- •4.1. Общая характеристика и состояние комплекса
- •4.3. Литейное производство
- •4.3.1. Общие сведения.
- •4.3.2. Литье в песчано-глинистые формы.
- •4.3.3. Литье в оболочковые формы.
- •4.3.5. Изготовление отливок центробежным литьем.
- •4.3.7. Литье под давлением.
- •4.4. Обработка металла давлением
- •4.4.1. Прокатное производство.
- •4.4.3. Прессование.
- •4.5. Кузнечно-штамповочное производство
- •4.5.1. Ковка.
- •4.5.4. Особые способы листовой штамповки.
- •4.6. Обработка конструкционных материалов резанием
- •4.6.1. Общие сведения.
- •4.6.3. Основные механизмы и узлы станков.
- •4.6.4. Токарные станки.
- •4.6.5. Сверлильные и расточные станки.
- •4.6.6. Фрезерные станки.
- •4.6.8. Обработка заготовок на шлифовальных стан-
- •4.6.9. Отделочные методы обработки.
- •ГЛАВА 5. ПЛАСТМАССЫ
- •5.1. Основные виды, свойства и применение
- •5.2. Основные виды термопластичных пластмасс, их свойства и применение
- •5.3. Основные виды термореактивных пластмасс, их свойства и применение
- •5.4. Производство изделий из пластмасс
- •ГЛАВА 6. СТРОИТЕЛЬНЫЙ КОМПЛЕКС
- •6.1. Общая структура комплекса, его развитие и состояние
- •6.2. Строительные материалы
- •6.2.1. Классификация строительных материалов.
- •6.2.2. Основные свойства строительных материалов
- •6.2.3. Природные каменные материалы.
- •6.2.4. Искусственные керамические и каменные материалы.
- •6.2.5. Древесные материалы.
- •6.2.7. Асбестоцементные изделия.
- •6.2.8. Органические вяжущие материалы и изделия на их основе.
- •6.2.9. Стекло и изделия из стекла.
- •6.3. Строительство
- •6.3.1. Принципы классификации зданий. Основные части зданий и их конструкционное выполнение.
- •6.3.2. Проектирование строительства. СНиП и другие нормативные документы.
- •6.3.3. Организация и порядок проведения строительных работ.
- •6.4. Инженерное обеспечение зданий и сооружений
- •6.4.1. Система водоснабжения.
- •6.4.2. Система канализации.
- •6.4.3. Системы теплоснабжения.
- •6.4.4. Системы вентиляции и кондиционирования.
- •ГЛАВА 7. МЕЖОТРАСЛЕВЫЕ ТЕХНОЛОГИЧЕСКИЕ СИСТЕМЫ. СВАРКА И ПАЙКА МЕТАЛЛОВ
- •7.1. Сварка
- •7.1.1. Общие сведения.
- •7.1.2. Электродуговая сварка.
- •7.1.3. Электрическая контактная сварка.
- •7.1.4. Газовая сварка (рис. 7.4).
- •7.1.5. Сварка лазерным лучом
- •7.1.7. Прочие виды сварки.
- •7.2. Пайка
- •ГЛАВА 8. ТОПЛИВНО-ЭНЕРГЕТИЧЕСКИЙ КОМПЛЕКС
- •8.1. Общие тенденции развития
- •8.2. Добыча и фракционная перегонка нефти
- •8.3. Нефтепродукты
- •ТЕРМИНОЛОГИЧЕСКИЙ СЛОВАРЬ
- •БИБЛИОГРАФИЧЕСКИЙ СПИСОК
- •ОГЛАВЛЕНИЕ

139
Рис. 4.33. Токарный станок-автомат:
1 – механизм подачи прутка, 2 – механизм зажима прутка, 3 – зажимная цанга, 4 – поперечный суппорт, 5 – расточной резец, 6 – револьверный суппорт, 7 – распределительный вал
Управление станком осуществляется автоматически рас-
пределительным валом 7 с помощью системы кулачков. За один оборот распределительного вала происходит полная обработка заготовки.
Заготовка (пруток) через отверстие в шпинделе подается кулачковым механизмом 1 на длину детали, затем, по мере поворота распределительного вала, кулачковый механизм 2 прижимает цангу к поверхности заготовки, кулачок 6 перемещает суппорт с резцом 5 и производит обработку заготовки.
По окончании обработки кулачок сдвигает суппорт в исходное положение, следующий кулачковый механизм – с поперечным суппортом 4 – отрезает деталь, кулачковый механизм 2 разжимает цангу и освобождает пруток, кулачковый механизм 1 производит его подачу для изготовления следующей детали. После этого весь цикл обработки повторяется, пока не будет переработан весь пруток.
4.6.5. Сверлильные и расточные станки. Цилиндриче-
ские отверстия получают и обрабатывают с помощью различных режущих инструментов на сверлильных, токарных, револьверных, расточных и некоторых других металлорежущих станках. На сверлильных станках выполняют следующие виды работ:
1 – сверление (рис. 4.34, а) – один из самых распространенных способов образования круглых отверстий с помощью различного диаметра и вида сверл;
2 – рассверливание (рис. 4.34, б) – процесс увеличения имеющихся отверстий сверлом большего диаметра;
3 – зенкерование (рис. 4.34, в) – обработка цилиндрических литых, штампованных или предварительно просверленных

140
отверстий зенкером для придания им правильной геометрической формы, требуемой точности размеров и шероховатости поверхности;
4 – растачивание отверстий резцами (рис. 4.34, г, д) осуществляют тогда, когда координаты осей отверстий должны быть точно расположены, а их диаметр превышает размеры выпускаемых сверл;
5 – развертывание (рис. 4.34, е) – обработка отверстий для получения точных размеров и малой шероховатости поверхности;
6 – зенкование (рис. 4.34, ж) – образование цилиндрических или конических углублений в предварительно просверленных отверстиях под головки болтов, винтов или других деталей с помощью цилиндрических и конических зенковок или сверл большего диаметра;
Рис. 4.34. Схемы обработки отверстий
7 – цекование (рис. 4.34, з, и) – обработка торцовых поверхностей под гайки, шайбы и кольца ножами (пластинами) или торцовыми зенкерами;
8 – нарезание резьбы метчиками (рис. 4.34, к).
При работе на сверлильных станках режущий инструмент, вращаясь вокруг своей оси, совершает главное движение, а перемещение его вдоль оси является движением подачи. Сверлиль-
ные станки подразделяются на вертикально-сверлильные, ради- ально-сверлильные, многошпиндельные и горизонтальносверлильные.
Вертикально-сверлильные станки (рис. 4.35) выпус-
кают различных типоразмеров (по диаметру сверла) и применяют в цехах единичного и серийного производства. На фундаментной плите 1 крепится станина 9. Главное (вращательное) движение

141
сверлу 3, закрепленному в нижней части шпинделя 4, передается через коробку скоростей 5 от электродвигателя 6. Движение подачи (вдоль оси) передается сверлу от коробки подач, укрепленной в подвижном кронштейне 7; подача сверла вручную осуществляется при помощи штурвала 8. Заготовка (деталь) крепится на столе 2, который рукояткой 10 можно перемещать вертикально на нужную высоту.
Рис. 4.35. Общий вид |
Рис. 4.36. Общий вид |
вертикально-сверлильного станка |
радиально-сверлильного станка |
Радиально-сверлильный станок (рис. 4.36) предназна-
чен для сверления отверстий в крупногабаритных заготовках, которые трудно перемещать по плоскости вертикально-сверлильно- го станка. Станок состоит из фундаментальной плиты 1, на которой закреплена тумба 2. Вокруг нее поворачивается гильза 3, вдоль нее по вертикали перемещается с помощью винта 9 траверса 6. На траверсе установлен двигатель 5 и имеются горизонтальные направляющие, по которым перемещается сверлильная головка 7.
Механизм головки состоит из коробки скоростей, коробки подач и шпинделя 8. Обрабатываемые детали устанавливают на съемном столе 10, фундаментной плите 1 или возле станка. Шпиндель 8 со сверлильной головкой может перемещаться горизонтально вдоль направляющих траверсы, а вместе с траверсой 6 и гильзой 3 вокруг оси неподвижной колонны. Эти перемещения шпинделя обеспечивают установку инструмента в любых координатах с радиусом не более хода сверлильной головки по траверсе.
142
По числу шпинделей станки подразделяются на одношпиндельные и многошпиндельные.
В горизонтально-сверлильных станках шпиндель расположен горизонтально.
Расточные станки применяют для обработки крупных корпусных деталей. На них можно сверлить отверстия, растачивать и обтачивать цилиндрические поверхности, зенкеровать, фрезеровать и т.д., т.е. производить полную обработку заготовки без ее перестановки, что предохраняет от смещения обрабатываемых поверхностей и центров. Применяются при изготовлении матриц и др. заготовок, требующих точного расположения отверстий относительно базовой поверхности. Станки дорогие и малопроизводительные. Особой точностью отличаются координатно-расточные и алмазно-расточные станки.
Горизонтально-расточные станки. На рис. 4.37 пред-
ставлен общий вид горизонтально-расточного станка и примеры выполняемых на нем работ.
Заготовку устанавливают на поворотном столе 9, который может перемещаться по салазкам 10 в продольном и поперечном направлениях относительно оси шпинделя и совершать круговое движение. На основании станка 11 установлены две стойки – передняя стойка 3, по направляющим которой перемещается вверхвниз шпиндельная бабка 7 с расточным шпинделем 6 и планшайбой 5, и задняя 1 с люнетом 2, предназначенным для опоры второго конца оправки (бортштанги) с резцом (фрезой) при обработке верхней поверхности заготовки. На планшайбе смонтирован суппорт 4, обеспечивающий обработку резцом плоских поверхностей. Управление станком осуществляется с пульта 8.
На рис. 4.38 отображен набор операций, которые можно выполнять на горизонтально-расточном станке. При обработке заготовки резцом, установленном в шпинделе, можно сверлить, зенкеровать и развертывать отверстия (рис. 4.38, а); резцом, установленном в суппорте 5 на планшайбе 4, можно растачивать отверстия большого диаметра (рис. 4.38, б, в); обтачивать, подрезать пластинчатым резцом и фрезеровать торцовые поверхности (рис. 4.38, г, д, е); резцом, закрепленным на оправке, можно растачивать одно или несколько отверстий, а также набором фрез обрабатывать плоскости и фасонные поверхности (рис. 4.38, ж) и др.
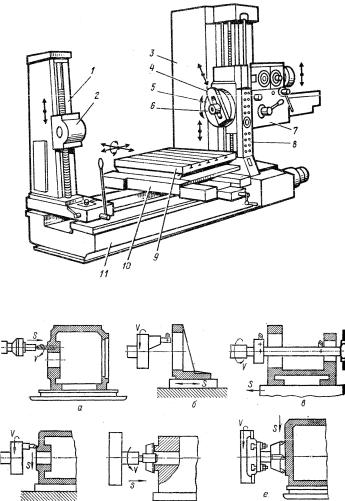
143
Рис. 4.37. Горизонтально-расточной станок
Рис. 4.38. Примеры работ, выполняемых на горизонтально-расточном станке
Подача инструмента может осуществляться перемещением шпинделя 6 вдоль оси, шпиндельной бабки по вертикальным направляющим и суппорта с резцом по радиальным направлениям.
Таким образом, на станке можно производить все виды обработки заготовки без ее перестановки, что позволяет сохранить координаты обрабатываемых поверхностей относительно базовой поверхности.