
- •ВВЕДЕНИЕ
- •ГЛАВА 1. ТЕХНОЛОГИЧЕСКАЯ СИСТЕМА ПРЕДПРИЯТИЯ
- •1.1. Производственная система предприятия: общее понятие, структура и классификация
- •1.1.1. Производство. Общая структура и тенденции развития.
- •1.1.2. Классификация производств
- •1.2. Технология и технологическая система предприятия
- •1.2.1. Технология.
- •1.2.2. Технологическая система предприятия
- •1.3. Основные закономерности развития технологических систем. Технологическое развитие фирмы
- •1.3.2. Технологические пределы и преемственность технологий.
- •1.3.3. Продуктовые и технологические нововведения, их взаимосвязь и влияние на развитие технологического процесса.
- •1.3.4. Технология и факторы производства.
- •1.3.5. Технология и производственная мощность предприятия.
- •1.6. Технологические уклады в системе мирового технико-экономического развития
- •1.7. Макротехнологии – общее понятие и развитие
- •ГЛАВА 2. СЫРЬЕВОЙ КОМПЛЕКС РОССИИ
- •2.1. Сырье: общее понятие, классификация и применение
- •2.2. Обогащение сырья
- •2.3. Комплексное использование сырья
- •2.4. Общая характеристика сырьевой базы России
- •ГЛАВА 3. МЕТАЛЛУРГИЧЕСКИЙ КОМПЛЕКС
- •3.1.Общая характеристика комплекса
- •3.2. Черная металлургия
- •3.2.1. Общая характеристика отрасли, ее состояние и роль в народном хозяйстве. Экспортные особенности.
- •3.2.4. Классификация сталей. Их свойства и примене-
- •3.3. Цветная металлургия
- •3.3.4. Титан: свойства и применение.
- •3.3.5. Никель: свойства и применение.
- •3.3.7. Порошковая металлургия. Общие сведения.
- •4.1. Общая характеристика и состояние комплекса
- •4.3. Литейное производство
- •4.3.1. Общие сведения.
- •4.3.2. Литье в песчано-глинистые формы.
- •4.3.3. Литье в оболочковые формы.
- •4.3.5. Изготовление отливок центробежным литьем.
- •4.3.7. Литье под давлением.
- •4.4. Обработка металла давлением
- •4.4.1. Прокатное производство.
- •4.4.3. Прессование.
- •4.5. Кузнечно-штамповочное производство
- •4.5.1. Ковка.
- •4.5.4. Особые способы листовой штамповки.
- •4.6. Обработка конструкционных материалов резанием
- •4.6.1. Общие сведения.
- •4.6.3. Основные механизмы и узлы станков.
- •4.6.4. Токарные станки.
- •4.6.5. Сверлильные и расточные станки.
- •4.6.6. Фрезерные станки.
- •4.6.8. Обработка заготовок на шлифовальных стан-
- •4.6.9. Отделочные методы обработки.
- •ГЛАВА 5. ПЛАСТМАССЫ
- •5.1. Основные виды, свойства и применение
- •5.2. Основные виды термопластичных пластмасс, их свойства и применение
- •5.3. Основные виды термореактивных пластмасс, их свойства и применение
- •5.4. Производство изделий из пластмасс
- •ГЛАВА 6. СТРОИТЕЛЬНЫЙ КОМПЛЕКС
- •6.1. Общая структура комплекса, его развитие и состояние
- •6.2. Строительные материалы
- •6.2.1. Классификация строительных материалов.
- •6.2.2. Основные свойства строительных материалов
- •6.2.3. Природные каменные материалы.
- •6.2.4. Искусственные керамические и каменные материалы.
- •6.2.5. Древесные материалы.
- •6.2.7. Асбестоцементные изделия.
- •6.2.8. Органические вяжущие материалы и изделия на их основе.
- •6.2.9. Стекло и изделия из стекла.
- •6.3. Строительство
- •6.3.1. Принципы классификации зданий. Основные части зданий и их конструкционное выполнение.
- •6.3.2. Проектирование строительства. СНиП и другие нормативные документы.
- •6.3.3. Организация и порядок проведения строительных работ.
- •6.4. Инженерное обеспечение зданий и сооружений
- •6.4.1. Система водоснабжения.
- •6.4.2. Система канализации.
- •6.4.3. Системы теплоснабжения.
- •6.4.4. Системы вентиляции и кондиционирования.
- •ГЛАВА 7. МЕЖОТРАСЛЕВЫЕ ТЕХНОЛОГИЧЕСКИЕ СИСТЕМЫ. СВАРКА И ПАЙКА МЕТАЛЛОВ
- •7.1. Сварка
- •7.1.1. Общие сведения.
- •7.1.2. Электродуговая сварка.
- •7.1.3. Электрическая контактная сварка.
- •7.1.4. Газовая сварка (рис. 7.4).
- •7.1.5. Сварка лазерным лучом
- •7.1.7. Прочие виды сварки.
- •7.2. Пайка
- •ГЛАВА 8. ТОПЛИВНО-ЭНЕРГЕТИЧЕСКИЙ КОМПЛЕКС
- •8.1. Общие тенденции развития
- •8.2. Добыча и фракционная перегонка нефти
- •8.3. Нефтепродукты
- •ТЕРМИНОЛОГИЧЕСКИЙ СЛОВАРЬ
- •БИБЛИОГРАФИЧЕСКИЙ СПИСОК
- •ОГЛАВЛЕНИЕ

149
На рис. 4.43 приведен горизонтально-протяжный станок для внутреннего протягивания. По направляющим станины 5 с помощью гидравлического привода перемещается ползун 2, на конце которого установлено приспособление 1 для закрепления протяжки. При работе длинными протяжками второй конец их поддерживается подвижным люнетом1 4. Обрабатываемая заготовка устанавливается в приспособлении 3.
Станки отличаются высокой производительностью, но применяются только в серийном и массовом производстве в связи с высокой стоимостью инструмента.
Аналогично работает прошивочный станок, только режущий инструмент (прошивка) здесь проталкивается через отверстие (рис. 4.43, б).
4.6.8. Обработка заготовок на шлифовальных стан-
ках.
Шлифованием называется процесс обработки заготовок абразивными2 материалами. К абразивным материалам относятся твердые горные породы – алмаз, корунд, гранат, кварц и др. и искусственные горные породы – карборунд, карбид бора и др., применяемые для обработки материалов в виде абразивных (наждачных) кругов, паст или бумаги (ткани) с нанесенным слоем абразива. Шлифование применяют для чистовой и отделочной обработки с высокой (до 0,002 мм) точностью. Применяется шлифование в большинстве случаев для окончательной, чистовой обработки и является основным методом получения высокой точности и требуемой шероховатости.
Шероховатость поверхности – совокупность микронеровностей обработанной поверхности, образующих ее рельеф и рассматриваемых на определенном участке. Она характеризуется среднеарифметическим отклонением профиля (5 наибольших выступов и 5 впадин) от среднего значения и максимальной высотой неровностей на установленной (базовой) длине сечения поверхности (ГОСТ 2789–73).
Шлифование производится на шлифовальных станках.
Классификация шлифовальных станков. По виду выполняемых работ шлифовальные станки подразделяются на следующие типы (рис. 4.44):
круглошлифовальные – для обработки наружных поверхностей вращения (рис. 4.44, а, б);
1Люнет (франц. lunette) – приспособление к металлорежущему станку, служащее добавочной опорой для вращающихся обрабатываемых длинных нежёстких заготовок.
2От лат. аbrasio – соскабливаю.
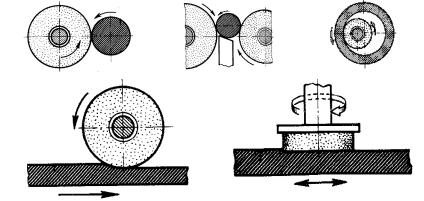
150
внутришлифовальные – для обработки внутренних поверхностей вращения (рис. 4.44, в);
плоскошлифовальные – для обработки плоскостей
(рис. 4.44, г, д);
специальные (шлицешлифовальные, зубошлифовальные, резьбошлифовальные и т.д.);
б в
а
г |
д |
Рис. 4.44. Основные виды шлифовальных работ
заточные – для заточки режущего инструмента. Наиболее распространенными являются круглошлифо-
вальные и плоскошлифовальные станки.
Круглошлифовальный станок (рис. 4.45, а) предназна-
чен для шлифования наружных цилиндрических и конических поверхностей. На станине 4 станка размещены все основные узлы и детали. Внутри станины находится привод, сообщающий возврат- но-поступательное движение продольной подачи столу. На столе размещены передняя бабка 1 и задняя бабка 3.
Заготовка укрепляется или одним концом в патроне шпинделя, вторым – в центре задней бабки, или между центрами передней и задней бабки (в этом случае вращение заготовки обеспечивается вращением поводка планшайбы, закрепленной на шпинделе). В шлифовальной бабке 2 установлен на шпинделе шлифовальный круг, который приводится во вращение от отдельного электродвигателя. При вращении заготовки вращающийся шлифовальный круг снимает с нее стружку, а заготовка совершает возвратно-поступательные движения вдоль станка.

151
Рис. 4.45, а. Круглошлифовальный станок
Плоскошлифовальные станки. Станки для плоского шлифования подразделяются на шлифующие круглой боковой и плоской торцевой поверхностями шлифовального круга (см. рис. 4.44, г и др.) Наибольшее распространение получили плоскошлифовальные станки с прямоугольным столом и горизонтальным шпинделем для шлифования заготовок боковой поверхностью круга (рис. 4.45, б).
Рис. 4.45, б. Плоскошлифовальный станок На столе станка укреплена электромагнитная плита 4,
служащая для установки и закрепления заготовки. Стол совершает возвратно-поступательное движение по направляющим станины 3. По вертикальным направляющим стойки 1 перемещается шлифовальная бабка 2 для установки шлифующего круга на глубину шлифования. Поперечное перемещение шлифовального круга может осуществляется вручную – маховиком 5 или автоматически, вертикальное перемещение – маховиком 6.
4.6.9. Отделочные методы обработки. Отделочными и доводочными методами обработки достигается получение глад-

152
ких зеркальных поверхностей с высокой точностью размеров. Основными видами отделочных работ являются хонингование,
суперфиниш, притирка и полировка.
Хонингование (англ. Honing от hone, буквально – то-
чить) – метод отделки поверхности сквозных отверстий вращающимися мелкозернистыми абразивными брусками 2 (рис. 4.46, а), которые вставлены в специальное приспособление – хонинговальную головку 1, и совершают вместе с ней вращательное и поступательное перемещение вдоль заготовки 3.
аб
Рис. 4.46. Схемы тонкой обработки поверхностей
Применяется при обработке точных отверстий, например, в блоках цилиндров внутреннего сгорания.
Суперфиниш (рис. 4.46, б) – применяют, в основном, для наружной обработки поверхностей. Бруски, закрепленные в головке над заготовкой, совершают продольное поступательновозвратное движение ∆Sпр, а заготовка вращается со скоростью V3 и движется возвратно-поступательно (Snр).
Притирка – метод чистовой обработки, обеспечивающий получение точных размеров (до 1 мкм) и малой шероховатости поверхности. Притирка производится абразивными пастами или порошками, смешанными со смазкой и нанесенными на поверхность притира. Наиболее часто для этой цели используется так называемая паста ГОИ (разработана Государственным оптическим институтом). В процессе притирки совершается перемещение притира и детали.
Притирка выполняется на универсальных и специальных притирочных станках, а также вручную. В качестве притиров используют вращающиеся диски, плиты, бруски и т.д.
Полировальные работы. Окончательная обработка поверхности достигается полированием ее быстро вращающимся эластичным кругом, покрытым войлоком, тканью и т.д., с нанесени-
153
ем на него полировальной пасты – абразивного порошка, смешанного с воском, салом, парафином и др. материалами. Наибольшее распространение получила указанная выше паста ГОИ. Полирование поверхности в обязательном порядке производится при ее последующей гальванической обработке – при покрытии никелем или хромом.
4.6.10. Механизация и автоматизация производственных процессов. Станки с числовым программным управлением (станки с ЧПУ). В зависимости от масштаба производства (единичного, серийного, массового) предприятия оборудуются станками различной степени автоматизации.
При единичном производстве используется универсальное оборудование, позволяющее производить его быструю переналадку и изготовление различных видов деталей. Однако производительность такого оборудования низкая, и для ее повышения осуществляются механизация и автоматизация наиболее трудоемких процессов при его обслуживании. Под механизацией понимается применение устройств, заменяющих ручной труд по обслуживанию станка – ускоренные перемещения суппортов, установка и закрепление деталей и т.д. При автоматизации ручное управление процессом работы станка заменяется автоматическими устройствами. При этом следует от-
личать два понятия – автоматизированное производство и автоматическое. Первое предполагает участие в управлении станком человека по отдельным функциям управления и контроля, второе – работа ведется полностью без какого-либо участия человека.
По конструкции системы управления различают станки с
цикловым программным управлением (ЦПУ) и с числовым программным управлением (ЧПУ).
В условиях массового производства наиболее рентабельны станки с ЦПУ – станки-автоматы, в которых автоматизирован как процесс установки и съема заготовки, так и весь цикл ее обработки. В этих станках управление осуществляется распределительным валом и системой соединенных с ним различных кулачков. При полном повороте распределительного вала осуществляется полный цикл обработки заготовки (например, рассмотренный выше токарный станок-автомат). Достоинствами таких станков являются высокая производительность и автоматический цикл обработки, но такие станки предназначены чаще всего для изготовления деталей определенного типоразмера и требуют чрезвычайно длительной переналадки для изготовления другой, даже подобной детали. Поэтому их применение ог-
154
раничено продукцией массового производства и необходимостью достаточно длительного применения.
С начала 80-х годов широкое распространение получили станки с числовым программным управлением, сокращенно – станки с ЧПУ.
Сущность станков с ЧПУ состоит в том, что программа выполнения всех необходимых для изготовления детали перемещений исполнительных органов (изменения режимов резания, переключения частот вращения шпинделя, скорости, направления, величины подачи резца или заготовки и др.) записывается с помощью числового кода на программоносителе. В качестве программоносителя могут быть использованы перфокарты, перфоленты, магнитные диски и ленты, лазерные компакт-диски и др. носители информации. Записанная программа вводится в считывающее устройство станка, в котором она преобразуется в командные импульсы, передающиеся исполнительным органам станка, обеспечивающие их необходимые перемещения. В функциональную систему ЧПУ входят три основных компонента: управляющая про-
грамма, блок управления и объект управления – станок.
Эффективность систем с ЧПУ объясняется тем, что изменение программы не требует существенной перестройки станка. Станки с ЧПУ позволяют в 3–6 раз повысить производительность труда в мелкосерийном и единичном производстве, одновременно повышая качество обработки и стабильность размеров.
Практически все основные виды металлорежущих станков могут выпускаться и выпускаются с ЧПУ.
Обработка крупных корпусных деталей может состоять из ряда различных операций – сверления, растачивания, фрезерования и т. д. Переход к каждой операции требует смены инструмента и заготовки, транспортировки заготовки от станка к станку, т.е. требует значительных дополнительных затрат времени. Поэтому в последнее время широкое распространение получили многоцелевые станки с ЧПУ – обрабатывающие центры. Они позволяют обрабатывать деталь с применением многих, до 150 шт., инструментов без снятия детали.
Пример обработки заготовки на обрабатывающем центре, созданном на базе горизонтально-расточного станка, показан на рис. 4.47. На станке имеются два приспособления – спутники 2 и 10, предназначенные для последовательного перемещения и смены заготовок на столе 8 по мере их обработки. Технологический процесс обработки состоит из следующих операций. Первая операция – заготовка 3 устанавливается на спутник 2 и подается с него на поворотный стол 8 под шпиндельную бабку
155
9. Затем, по заданной программе, установленным в шпинделе 7 инструментом, начинается обработка заготовки. Пока идет обработка первой заготовки, на второе приспособление – спутник 10 устанавливается следующая заготовка. После окончания первой операции обработки заготовки двухзахватный оператор 5 вынимает одним захватом (5а) из шпинделя отработавший инструмент, другим (5б) вынимает из магазина 4 инструмент для следующей операции обработки, затем поворачивается на 180º, вставляет отработавший инструмент в магазин, новый инструмент – в шпиндель, и производится следующая операция обработки заготовки. По окончании обработки готовая деталь переносится на спутник 2 и удаляется, новая заготовка со спутника 10 устанавливается на поворотный стол и начинается ее обработка. Все действующие операции перемещения и обработки производятся автоматически по программе.
На обрабатывающих центрах можно обрабатывать все поверхности детали, кроме базовой, без перестановки заготовки.
Обрабатывающие центры отличаются высокой производительностью и находят широкое применение в промышленности.
156
Рис. 4.47. Многоцелевой станок мод. 2623ПМФ3 и схема его двухзахватного оператора см. Аосновы отр техн сбор 2010а граф