
Калин Физическое материаловедение Том 5 2008
.pdfется с газами в виде SO2, H2S и др. Остальная часть в виде сульфидов FeS, CaS и др. соединений переходит в чугун и в шлак. Наиболее опасен сульфид железа FeS, хорошо растворяющийся в расплавленном чугуне. Основным способом десульфурации является образование сульфида кальция CaS по реакции: FeS + СаО = = CaS + FeO + Q. Сульфид CaS нерастворим в чугуне, но хорошо растворяется в шлаке. Наиболее интенсивно сера удаляется при прохождении капель чугуна через слой шлака; коэффициент перехода серы в шлак составляет 0,9–0,99.
Шлакообразование. Значение шлака очень велико: его состав и свойства определяют конечный состав чугуна. Примерно в средней по высоте печи области образуется первичный шлак. Происходит плавление относительно легкоплавких соединений Тпл = 1150– 1250 °С, входящих в состав агломерата и окатышей, а также образующихся при сплавлении флюсов и окислов пустой породы руды. При стекании вниз и накоплении в горне шлак существенно изменяет свой состав. В результате взаимодействия с остатками несгоревшего кокса и расплавленным чугуном в шлаке растворяются SiO2, A12O3, из золы кокса сульфиды FeS и MnS, частично восстанавливаются оксиды железа и т. д. В сложных физико-химических процессах взаимодействия системы «чугун – кокс – шлак» большое значение имеет не только состав шлака, но и его количество, вязкость и др. свойства, температура горна и т. п.
Продукты доменной плавки. Основным продуктом доменного производства является чугун, а шлак и доменный газ – побочными продуктами.
В доменных печах выплавляют передельные и литейные чугуны, а также некоторые ферросплавы.
Передельный чугун предназначается для дальнейшего передела в сталь. На его долю приходится около 90 % общего производства чугуна. Обычно такой чугун содержит 3,8–4,4 % С, 0,3–1,2 % Si, 0,2–1 % Мn, 0,15–2 °/о Р и 0,02–0,07 % S.
Литейный чугун применяется после переплава в плавильных цехах для отливки чугунных изделий. Чугуны с низким содержанием фосфора (0,1–0,3 %) используют для изготовления высокопрочных литых изделий.
161
В зависимости от размеров доменной печи выпуск чугуна проводят по 10–18 раз в сутки. При выпуске плавки расплавленный чугун в ковшах-чугуновозах вместимостью 80–100 т по железнодорожным путям подают в сталеплавильный цех завода для передела
всталь или на разливочную машину. В первом случае чугун сливают в миксеры (копильники) вместимостью до 2000 т, отапливаемые газом. При выдержке в миксере выравниваются химический состав и температура чугуна, происходит дополнительное удаление серы. Разливочная машина представляет собой конвейер с укрепленными на нем формами (мульдами); в них получают небольшие слитки – чугунные чушки массой до 55 кг, которые направляют на другие заводы.
Доменные ферросплавы. Эти сплавы используют при выплавке сталей для раскисления и легирования. Ферромарганец содержит 70–75 % Мn, доменный ферросилиций 9–13 % Si (иногда больше) и до 3 % Мn. В доменных печах из руд некоторых месторождений выплавляют также природнолегированные чугуны, содержащие хром, ванадий, никель и т. п.
Доменный шлак по мере его накопления выпускают в расплавленном состоянии через шлаковые летки в ковши-шлаковозы вместимостью около 30 т, транспортируемые по железнодорожным путям. В настоящее время почти весь шлак используют для получения строительных материалов.
Доменный или колошниковый газ выделяется в больших количе-
ствах и непрерывно удаляется из доменной печи через газоотводы
вколошнике. При сгорании 1 т кокса образуется около 5000 м3 газа. Таким образом, в крупных печах (объемом 3000–3200 м3) в сутки выделяется примерно 15–17 млн. м3 газа. Он содержит зна-
чительное количество горючих составляющих (26–32 % СО, до 4 % Н2), его теплота сгорания около 3,6–4,0 кДж/м3. После очистки от пыли (частиц руды, топлива, флюсов) доменный газ используют как топливо для нагрева воздухонагревателей доменных печей, водяных и паровых котлов, а в смеси с более высококалорийными коксовым или природным газами – для отопления мартеновских и нагревательных печей. Колошниковая пыль содержит 45–50 % Fe .
162

18.1.2. Производство стали
Стали – железоуглеродистые сплавы, содержащие практически до 1,5 % углерода (теоретически до 2,14 % углерода)1. Кроме углерода, сталь всегда содержит в небольших количествах постоянные химические элементы-раскислители: марганец (до 0,8 %) и кремний (до 0,4 %), а также примеси: фосфор (до 0,07 %), серу (до 0,06 %) и др., что связано с особенностями технологии ее выплавки. Кроме углеродистых сталей, в технике широко применяют легированные стали, в состав которых входят хром, никель и другие элементы. Существуют свыше 1500 марок углеродистых и легированных сталей – конструкционных, инструментальных, коррозионностойких и др.
Современные способы производства стали. Для массового производства стали в современной металлургии основными исходными материалами являются передельный чугун и стальной скрап (см. п.18.1.1). Выплавка стали сводится к проведению окислительной плавки для удаления избытка углерода и других элементов. Для выплавки легированных сталей в их состав вводят соответствующие элементы. Для обеспечения качества стали при плавке необходимо как можно полнее удалять из металла вредные примеси – серу и фосфор, кислород, азот, неметаллические включения.
Первыми массовыми способами получения стали явились бессемеровский (1855–1856 гг., Франция) и томасовский (1878 г., Англия) процессы. Подробную информацию о технологических процессах и металлургическом оборудовании (конверторах) при реализации этих процессов можно найти в специальной металлургичесой литературе.
Недостатками указанных процессов являются невысокое качество стали и ограниченность сырьевой базы из-за ограничений по составу чугунов.
В 1864–1865 гг. во Франции был разработан мартеновский процесс, менее производительный, но позволяющий выплавлять более качественную сталь, названную мартеновской сталью. Для выплавки мартеновской стали используется наиболее распространенный
1 Физическое материаловедение. М.: МИФИ, 2007. Т. 2. П. 5.3.
163
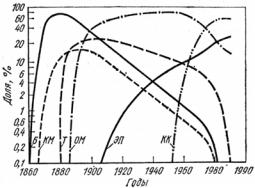
чугун (непригодный для бессемеровского и томасовского передела) и огромное количество вторичного металла – стального скрапа. В период 1910–1970 гг. мартеновский процесс был главным при выплавки стали.
Новый современный этап в металлургии стали связан с широким использованием кислорода. Были разработаны новые кислородные процессы: кислородно-конвертерный, плавка в двухванных печах. Кислородно-конвертерный процесс – главный способ массового производства стали. Выплавляемая сталь по качеству практически равноценна мартеновской стали.
Следует отметить, что кислород широко применяют также для интенсификации мартеновского и электросталеплавильного процессов.
Легированную сталь выплавляют в основном в электрических дуговых и индукционных печах. Сталь особо высокого качества выплавляют в вакуумных электрических печах, путем электрошлакового, плазменного переплава и другими новейшими способами
(рис. 18.2).
Внедоменные способы производства железа (стали) – одно из перспективных направлений в металлургии, например, по двухстадийной технологии: руда → чугун → сталь.
Рис. 18.2. Диаграмма, показывающая изменение доли отдельных процессов
вмировом производстве литой стали:
Б– бессемеровский процесс; КМ – кислый мартеновский; Т – томасовский; ОМ – основной мартеновский; ЭП – электросталеплавильный;
КК– кислородно-конвертерный
164
Кислородно-конвертерный процесс. Сущность процесса со-
стоит в том, что в плавильный агрегат – конвертер – загружают стальной скрап, заливают расплавленный чугун (более 70% по массе плавки) и продувают струей кислорода сверху. В металлической шихте С, Si, Mn и другие примеси энергично окисляются, и оксиды выводятся из объема расплава – продукта плавки, т.е. стали заданного состава.
Устройство конвертера. Конвертор представляет агрегат, корпус (кожух) которого сварен из листовой стали толщиной до 100 мм. Внутренняя футеровка корпуса – двух или трехслойная, общей толщиной 700–1000 мм, – изготовлена из основных огнеупорных материалов, преимущественно из магнезита и доломита. Внутренний – рабочий – слой обычно делают из высокоогнеупорного доломитового кирпича; его стойкость до ремонта 400–800 плавок.
Благодаря наличию основной футеровки в конвертер при плавке загружается известь и образуется основной шлак, который обеспечивает достаточно полное удаление из металла вредных примесей – серы и фосфора. Вместимость современных конвертеров 70–350 т.
Кислородное дутье. Кислород под давлением подается по водоохлаждаемой трубе (фурме), которую вводят по оси конвертера через горловину. Режим кислородного дутья (давление, расход и т.п.) оказывает очень большое влияние на производительность конвертера и качество стали. Давление кислорода примерно 1–1,5 МПа на выходе из фурмы должно обеспечивать достаточную кинетическую энергию струи и требуемое ее углубление в металл для «усвоения» кислорода и перемешивания ванны – циркуляции металла и шлака.
Чистота технического кислорода должна быть 99,5–99,7%, что обеспечивает в готовой стали низкое содержание вредной примеси
– азота 0,002–0,004%. Значительно более дешевый технологический кислород 98–99% можно применять при выплавке стали, в которой содержание азота жестко не регламентируется.
Шихтовые материалы. Основная масса металлической шихты – передельный расплавленный чугун – более 70%; стальной лом добавляют до 25–30%. В кислородных конвертерах можно пререработать чугун различного химического состава: с пониженным и повышенным содержанием Mn, Si, высокофосфористые и т. д. Наиболее выгоден для передела чугун с оптимальным составом:
165
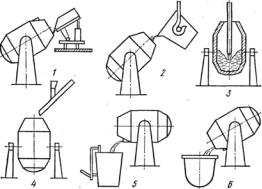
3,8–4 % С; 0,5–1,5 % Si, 0,5–1,5 % Mn, 0,15–0,3 % Р, 0,02–0,06 % S.
При его переделе проводят наиболее простой технологический вариант – обыкновенный кислородно-конвертерный процесс. Плавку ведут с одним шлаком, обеспечивая нужную степень удаления фосфора и серы. При содержании в чугуне Р > 0,3 % плавку необходимо проводить с остановкой продувки для слива промежуточного высокофосфористого шлака и его обновления для завершающей части плавки.
Технология плавки. Последовательность основных операций и рабочие положения конвертера приведены на рис. 18.3.
Рис. 18.3. Технологические операции кислородно-конвертерной плавки: 1 – загрузка стального скрапа; 2 – заливка расплавленного чугуна;
3 – продувка кислородом; 4 – загрузка извести и железной руды с началом продувки и по ходу плавки; 5 – выпуск металла; 6 – выпуск шлака
В конвертер загружают стальной лом и заливают расплавленный чугун. С началом продувки загружают примерно 2/3 по массе шлакообразующих: извести, боксита (плавикового шпата), железной руды; остальную их часть вводят отдельными порциями по ходу продувки. Конец продувки определяют по времени, количеству израсходованного кислорода, виду пламени из горловины. Затем отбирают контрольные пробы металла и шлака для экспрессанализа, измеряют температуру.
При выпуске стали проводят ее раскисление и легирование. Готовую сталь направляют на разливку. Шлак сливают в шлаковый ковш через горловину.
166
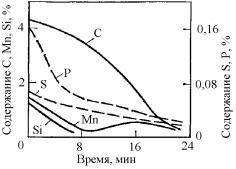
Окисление при продувке. Окисление железа, углерода и других примесей при продувке происходит за счет: газообразного кислорода {О}; кислорода, растворенного в металле [О]; закиси железа (FeO). Здесь приняты стандартные обозначения: [С], [Si] и т. д. – компонент растворен в металле: (FeO), (CaO) и т. д. – в шлаке; {О}, {СО} и т. д. – находится в газовой фазе.
Основные реакции непосредственного окисления кислородом: [С] + 1/2{O2} = {СО} + Q; [Si] + {O2} = (SiO2) + Q; кислородом,
растворенным в металле: [Mn] + [О] = MnO + Q; [С] + [О] = {СО}. При продувке кислородом в большом количестве образуется огксид железа, который хорошо растворяется и в металле [FeO], и в шлаке (FeO). При растворении в металле [FeO] → [Fe] + [О] металл обогащается растворенным кислородом. В шлаке (FeO) окисляет примеси: [Si] + 2 (FeO) = (SiO2) + 2Fe и т. д.
Изменение химического состава металла по ходу плавки показано на рис. 18.4. Окисление углерода имеет наиболее важное значение для регулирования его концентрации в стали и достижения его заданного содержания и определяет продолжительность продувки. Так как окисление углерода можно проводить с большой скоростью, то конверторная плавка стали является высоко производительной.
Рис. 18.4. Изменение химического состава металла по ходу плавки
В начальный период кислород расходуется преимущественно на окисление Si, Mn и др. и скорость окисления углерода невелика – 0,1–0,15 %/мин. Затем скорость обезуглероживания достигает 0,5 % С/мин, что примерно на два порядка выше, чем в мартеновском процессе. Замедление окисления углерода к концу продувки
167
облегчает выплавку стали заданного состава. Выделяющиеся при окислении углерода пузырьки СО удаляют из металла азот; интенсивно перемешивая металл и шлак, они способствуют также удалению фосфора и серы.
Кремний окисляется практически полностью, марганец примерно на 70 % уже в начале продувки. Это объясняется их высоким сродством к кислороду при невысокой температуре (реакции – экзотермические).
Фосфор удаляется путем ошлакования (перехода в шлак) по ре-
акции: 2 [Р] +5 (FeO) + 3 (CaO) = (P2O5 3CaO) +5[Fe] + Q (эта реак-
ция суммарная и протекает в несколько стадий). Интенсивное удаление фосфора происходит с началом продувки, чему способствует раннее образование шлака с достаточным содержанием СаО и FeO и относительно невысокая температура (реакция – экзотермическая). За всю плавку в шлак переходит до 95–98 % фосфора шихты; готовая сталь содержит < 0,04 % Р.
До 90 % всей удаляемой серы ошлаковывается известью по ре-
акции: [FeS] + (СаО) = (CaS) + (FeO); до 10 % удаляется при пря-
мом окислении дутьем в виде {SO2}. Основная причина невысокой степени удаления серы – значительное содержание FeO в шлаке, что препятствует ошлакованию серы. Основная часть серы поступает с чугуном. Для выплавки стали с 0,04 % S в чугуне должно быть не более 0,06–0,07 % S.
Окисление и испарение железа. При продувке металла кислоро-
дом неизбежно происходит окисление железа с образованием FeO: потери составляют до 2% Fe. Характерной особенностью является испарение железа – до 1,5 % при контакте струи кислорода с металлом, где развивается температура 2000–2500 °С.
Шлаковый режим является существенным параметром плавки. Наиболее важная характеристика состава шлака – его основность: Qшл = % СаО/% SiO2. В начале продувки Qшл 1 (около 30 % СаО, 30 % SiO2); по ходу плавки она непрерывно повышается до Qшл2–2,5 (40–50 % СаО, до 20 % SiO2) перед выпуском стали. При такой основности обеспечивается дефосфорация и десульфурация металла. Состав шлака – его основность, содержание FeO, температура и другие особенности шлакового режима существенно влияют на ход плавки и качество стали.
168
При обычном одношлаковом процессе масса шлака составляет 12–16 % от массы металла. При переработке фосфористых чугунов с промежуточным удалением шлака его масса составляет 20–30 %.
Раскисление стали. Все способы выплавки стали из чугуна и скрапа – окислительные процессы. В конце плавки сталь всегда содержит кислород: [О], [FeO] и т. п.; в затвердевшей стали присутствует твердый раствор кислорода в железе, FeO и другие оксиды. Кислород снижает прочность, и в особенности пластичность и вязкость стали. Поэтому обязательной завершающей операцией при выплавке является раскисление стали, т. е. уменьшение содержания кислорода до допустимых норм.
Существует несколько способов раскисления стали: глубинное, диффузионное и др. Для кислородно-конвертерной стали применяют глубинное раскисление – наиболее распространенный и дешевый способ. Глубинное раскисление состоит в том, что в глубину металлической ванны вводят раскислители – элементы, имеющие большое сродство к кислороду. Вещества, образующиеся при их окислении, имеют меньшую плотность, чем сталь; они всплывают «осаждаясь» в слой шлака.
Наиболее часто сталь раскисляют марганцем (ферромарганцем), кремнием (ферросилицием) и алюминием по реакциям:
[Мn] + [О] = (MnO) + Q; [Si] + 2 [О] = (SiO2) + Q;
2 [Al] + 3 [О] = (Al2O3) + Q.
Кипящая сталь – наименее раскисленная – может быть получена при раскислении только одним ферромарганцем. В такой стали реакция [С] + [O] = СО не прекращается, и металл продолжает «кипеть» из-за выделяющихся пузырей СО. Эти газовые пузыри остаются в большом количестве в теле слитка и устраняются при последующей горячей прокатке. Такая сталь наиболее дешевая. При ее производстве получается наибольший выход годного металла.
Спокойная сталь – наиболее раскисленная – получается при последовательном раскислении металла ферромарганцем, ферросилицием и алюминием. После введения раскислителей выделение пузырей СО прекращается, и металл «успокаивается». Эта сталь наиболее качественная, но и наиболее дорогая. В верхней части слитка образуется усадочная раковина, что значительно уменьшает выход годного металла.
169
Полуспокойная сталь получается при раскислении ферромарганцем и уменьшенным количеством ферросилиция (иногда и алюминия). По качеству и по стоимости она является промежуточной между спокойной и кипящей сталью.
Кислородно-конвертерным способом выплавляют спокойную, полуспокойную и кипящую стали. Выплавка легированных сталей в конвертерах затруднена; в них выплавляют в основном низколегированные стали. Неокисляющиеся элементы, например никель, можно вводить во время плавки. Большинство легирующих элементов (хром, марганец и др.) легко окисляются. При их введении во время продувки происходит большой угар. Один из способов легирования – при выпуске плавки в ковше, куда загружают или заливают в расплавленном состоянии соответствующие ферросплавы.
Производство стали в мартеновских печах. Мартеновская печь по устройству и принципу работы является пламенной регенеративной печью. В ее плавильном пространстве сжигается газообразное топливо или мазут. Высокая температура для получения стали в расплавленном состоянии обеспечивается регенерацией тепла печных газов.
Рабочее плавильное пространство печи ограничено снизу ванной, образованной подом и откосами; сверху – сводом; с боков – передней и задней стенками; с торцов – головками. В передней стенке расположены окна, через которые в печь загружают исходную шихту и дополнительные материалы (по ходу плавки), а также берут пробы металла и шлака, удаляют шлак при дефосфорации. Окна закрыты заслонками со смотровыми отверстиями. Готовую плавку выпускают через отверстие, расположенное в задней стенке на нижнем уровне пода. Отверстие плотно забивают малоспекающимися огнеупорными материалами, которые для выпуска плавки выбивают. В качестве топлива для мартеновских печей на отечественных заводах используют смесь доменного, коксового и природного газов, мазут или природный газ.
Масса плавки мартеновских печей колеблется в очень широких пределах. Для выплавки небольших количеств стали применяют (30–80)-тонные печи. На больших металлургических заводах наи-
более распространены (250–500)-тонные печи с площадью пода до
115 м2.
170