
Калин Физическое материаловедение Том 5 2008
.pdf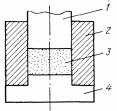
способом можно получать также порошки сплавов, используя смеси жидких карбонилов.
18.6.3. Формование порошков
Формование – это придание порошковому материалу формы, размеров, плотности и прочности, необходимых для выполнения последующих операций изготовления изделия. Существует много методов формования порошков. Наиболее распространенный из них – прессование в стальной пресс-форме. Схема простой прессформы приведена на рис. 18.13.
Пресс-форма состоит из матрицы и двух пуансонов, сжимающих слой порошка. Прессование может быть односторонним, когда только один пуансон перемещается относительно матрицы, и двухсторонним, когда подвижны оба пуансона.
Давление прессования находится обычно в пределах от 300 до 1000 МПа; твердые сплавы прессуют под
меньшим давлением – до 150 МПа, так как частицы карбидов хрупкие и при чрезмерном давлении дробятся.
Перемещение частиц при прессовании приводит к возникновению «бокового давления», т. е. давления порошка на боковые стенки, а также «внешнего трения», т. е. трения порошка о стенки. Смещение частиц порошка перпендикулярно линии приложения давления затруднено из-за трения и сцепления между частицами. Поэтому боковое давление меньше давления прессования и составляет менее 40 % от него. Потери энергии на внешнее трение тем больше, чем больше высота прессуемого изделия. Внешнее трение «съедает» до 60–90 % давления прессования и приводит к неравномерности уплотнения по высоте. Двухстороннее прессование позволяет уменьшить неравномерность уплотнения.
Один из наиболее радикальных способов уменьшить трение и улучшить процесс уплотнения (повысить плотность и уменьшить разброс ее по объему прессовки) – это применение смазок. Смазку можно вводить в прессуемый порошок и смазывать ею стенки
251
прессформы. В качестве смазок используют стеариновую кислоту и ее соли, парафин, глицерин, дисульфид молибдена и другие вещества. Количество смазки колеблется в пределах 0,1–0,15 %; оно уменьшается с повышением размеров зерен порошка и увеличением активности смазки.
После прессования к прессовке необходимо приложить усилие, чтобы извлечь ее из формы. Это усилие называют давлением выталкивания. Оно составляет 25–40 % от давления прессования, и тем больше, чем выше прессуемое изделие и меньше его поперечное сечение.
После снятия нагрузки и освобождения из пресс-формы, прессовка расширяется, причем не минуты и часы, а дни и недели. Расширение прессовки вызывается действием внутренних напряжений. Это явление называется упругим последействием. Размер упругого последействия составляет 3–5 % в направлении прессования и 1–5 % в перпендикулярном направлении. Время между прессованием и спеканием не должно превышать нескольких часов.
Современным методом формования является изостатическое прессование. Порошок в пластичной, резиновой оболочке уплотняют вибрированием и вакуумируют, затем переносят в рабочую камеру. Порошок в оболочке равномерно обжимается со всех сторон, при этом внешнее трение порошка отсутствует, так как оболочка перемещается вместе с порошком. Плотность прессовки получается практически одинаковой, а давление прессования для достижения заданной плотности гораздо меньше, чем при прессовании в стальных пресс-формах.
Изостатическое прессование с обжатием жидкостью (масло, вода, глицерин) называется гидростатическим, а с обжатием газом – газостатическим. Гидростатически прессуют цилиндры, трубы, шары, тигли и изделия сложной формы. Масса прессовки может достигать 500 кг. Упрощенным вариантом всестороннего обжатия является прессование в стальных пресс-формах, покрытых утолщенной эластичной оболочкой. Оболочки изготавливают из различных органических веществ и используют многократно. Оболочка из массы на основе натурального каучука выдерживает до 1000 циклов прессования.
252
Ленты из порошков и их смесей формуют прокаткой между двумя гладкими валками. Прочность прессовки достаточна для последующего спекания. Одновременная прокатка порошков двух разных металлов или металлического листа со слоем порошка позволяет получать многослойный прокат. В настоящее время широкое применение получает прокатка в вакууме или инертной среде порошков из химически активных металлов – титана, тантала, циркония.
Длинномерные заготовки типа прутков, труб, уголков получают мундштучным прессованием (экструзией). Для этого порошок с пластификатором помещают в контейнер и выдавливают из него пуансоном через отверстие в мундштуке. В качестве пластификаторов используют парафин, поливиниловый спирт и др. Алюминий и его сплавы прессуют при 400–600 °С, медь при 800–900 °С, никель и стали при 1050–1250 °С. Химически активные металлы (титан, цирконий, бериллий) прессуют в защитных средах или в защитных оболочках из стекла, графита или металлической фольги.
Изделия сложной формы, которые трудно изготавливать обычными способами прессования, получают шликерным формованием. Этот процесс заключается в заливке в пористую форму шликера – однородной концентрированной суспензии порошка в жидкости. Количество порошка составляет 40–70 %. Жидкость впитывается в поры формы, а частицы порошка оседают на ее стенках, создавая твердый слой. Формирование слоя занимает 1–60 мин в зависимости от толщины стенки изделия, затем изделие вынимают и сушат при 100–150 °С. Относительная плотность полученных изделий может достигать 60 %.
В последние годы при прессовании активно применяют импульсные нагрузки и вибрации. Приложение нагрузки с высокими скоростями и вибрация позволяют получать более плотные и однородные прессовки.
18.6.4. Спекание и последующая обработка
Спекание – важная операция в формировании свойств изделия. Оно всегда должно обеспечивать увеличение прочности изделия и во многих случаях – увеличение плотности. Главным, что обусловливает процессы при спекании, является большая поверхностная
253
энергия порошков: площадь поверхности порошков составляет несколько квадратных метров на один грамм массы. Спекание многокомпонентных смесей может осуществляться как в твердой фазе (твердофазное спекание), так и в присутствии жидкой фазы (жидкофазное спекание). Твердофазное спекание проводят при температурах 0,7–0,9 абсолютной температуры плавления наиболее легкоплавкого компонента смеси. На начальной стадии спекания благодаря поверхностной диффузии происходит расширение участков контакта частиц порошка и увеличивается сцепление частиц. При этом пустоты между частицами постепенно сфероидизируются, приобретают округлую форму, но объем пустот не изменяется. На последующих стадиях спекания активируется объемная диффузия, уменьшается объем пор и прессовки в целом (идет усадка прессовки). Выдержка прессовки при постоянной температуре сопровождается сначала быстрой усадкой, потом усадка замедляется и размеры изделия стабилизируются. Плотность и прочность спекаемых изделий существенно зависят от атмосферы, в которой проводят спекание.
Восстановительные среды предпочтительнее нейтральных газов, так как восстановление оксидных пленок на частицах порошка ускоряет спекание. Полно и быстро проходит спекание в вакууме. Длительность выдержки при спекании – от получаса до нескольких часов. Получить беспористый материал при твердофазном спекании практически не удается.
Жидкофазное спекание позволяет получать существенно более плотные изделия, чем твердофазное. Они могут быть практически беспористыми (пористость менее 1–2 %). Жидкая фаза облегчает спекание только тогда, когда она хорошо смачивает твердую фазу. В противном случае она тормозит спекание. Расплавы металлов хорошо смачивают чистые металлические поверхности, а также поверхности тех неметаллических веществ (карбидов, нитридов, боридов, оксидов и др.), с которыми они взаимодействуют. Различают спекание с жидкой фазой, остающейся до конца процесса, и спекание с исчезающей жидкой фазой. С оставшейся жидкой фазой спекают материалы на основе железа, содержащие медь, фосфор, серу. Характерным примером спекания с исчезающей жидкой фазой является производство бронзографитных материалов. В этом
254
случае при спекании сплавов системы медь – олово – графит олово плавится сначала, потом оно постепенно растворяет медь и жидкая фаза исчезает.
В производстве некоторых видов изделий применяют пропитку спрессованного и спеченного каркаса из тугоплавкого вещества легкоплавким сплавом. Так, пропитывают медь свинцом, карбид титана сталью, вольфрамовое волокно медью и медноникелевыми сплавами. Основное условие пропитки – смачивание тугоплавкого вещества расплавом. Пропитку выполняют погружением пористого каркаса в расплав или кладут на пористый каркас кусочек легкоплавкого сплава и расплавляют его в защитной среде; под действием капиллярных сил происходит пропитка каркаса.
Спеченные изделия в ряде случаев подвергают дополнительной обработке. Основные ее виды – это формирование оптимальной структуры и размерная обработка изделий. Регулирование структуры осуществляется термообработкой, доводка изделий по размеру
– калибровкой или механической обработкой. Калибровку осуществляют в специальных калибровочных пресс-формах. Усилие калибровки составляет 10–25 % от усилия прессования. Калибровка – почти всегда отделочная операция. Она позволяет достичь 1–2 класса точности при 7–9 классах чистоты поверхности. Механическая обработка спеченных изделий трудоемка и сопряжена с затруднениями из-за пористости; при этом трудно получить требуемую чистоту поверхности. Выполняют механическую обработку на больших скоростях твердосплавным режущим инструментом.
Экономическая эффективность изготовления деталей из порошков тем больше, чем больше серийность, так как стоимость прессформ и оборудования (прессов, печей) достаточно велика.
Практика показала, что детали из литья и проката черных металлов целесообразно переводить на изготовление из порошков при серийности 10000 штук, а детали из цветных металлов – при серийности 2000–3000 штук.
18.6.5. Современные направления порошковой металлургии
Прогресс в области порошковых материалов связан с разработкой новых методов оптимизации фракционного состава порошков
255
исовершенствованием технологии получения и компактирования ультрадисперсных и наноразмерных порошков.
Порошковая металлургия с использованием быстрозакаленных порошков позволяет получать однородный и изотропный материал вследствие реализации эффекта высокоскоростного затвердевания
иприменения последующего горячего изостатического прессова-
ния. Металлургия гранул (ПМ ГИП-технология, PM HIP – Powder Metallurgy Hot Isostatic Pressing) представляет перспективное на-
правление в получении изделий сложной формы, например, из высоколегированных жаропрочных сталей и сплавов.
Быстрозакаленные сплавы характеризуются высокодисперсной дендритной, микрокристаллической, нанокристаллической или аморфной структурой, высокой однородностью химического состава, формированием аномально-пересыщенных твердых растворов, образованием метастабильных фаз, структурных и фазовых составляющих, что обеспечивает высокий уровень технологических и служебных свойств.
Рассматривается как перспективное применение метода механоактивации (mechanical alloying) для получения заготовок сталей
типа MA957 (Fe–14 Cr–0,9 Ti–0,3 Mo–0,1 Al и 0,25 Y2O3, % мас.),
упрочненных высокодисперсными частицами оксидов (дисперсно-
упрочненные (ДУ), Oxide Dispersion Strengthened (ODS) материа-
лы) с использованием быстрозакаленных порошков.
MIM-технология (Metal Injection Moulding) представляет собой современный метод изготовления изделий точной геометрии, сложной формы, переменного состава из быстрозакаленных порошков легированных сталей, сочетающий высокие качество и свойства изделий с высокой производительностью и низкой стоимостью. Эта технология дополняет существующие методы традиционной порошковой металлургии с использованием прессования, спекания, механической обработки и метод литья по выплавляемым моделям. MIM-технология, как и другие методы порошковой металлургии позволяет конструировать изделия переменного состава, например для роторов измерителей скорости вращения, из аустенитной стали 316L с элементами из магнитно-мягкой стали 17-4PH. Быстроразвивающийся рынок ее применения охватывает такие направления как автомобильная, часовая, ювелирная про-
256
мышленность, медицина и др. Сущность метода состоит в использовании быстрозакаленных сферических порошков диаметром менее 20 мкм, получаемых распылением расплава, что, в частности, позволяет обеспечить высокую точность заполнения сложных форм при прессовании и соответственно точность изготовления изделий.
18.7.Методы сварки
18.7.1.Классификация способов сварки плавлением
идавлением
Сваркой называют процесс получения неразъемного соединения в результате возникновения атомно-молекулярных связей между соединяемыми деталями. Сварные соединения можно получать двумя принципиально разными путями – сваркой плавлением и сваркой давлением. При сварке плавлением атомно-молекулярные связи между деталями создают, оплавляя их примыкающие кромки так, чтобы получилась смачивающая их общая ванна. При сварке давлением обязательным является совместная пластическая деформация деталей сжатием зоны соединения. Этим обеспечивается очистка свариваемых поверхностей от пленок загрязнений, изменение их рельефа и образование атомно-молекулярных связей. Существуют и комбинированные процессы, когда металл доводят до расплавления и обжимают зону сварки (например, при точечной контактной сварке).
Нагрев свариваемых деталей осуществляют разными способами: электрической дугой, газокислородным пламенем, прямым пропусканием тока, лазером и т. д. По-разному обеспечиваются защита зоны сварки от воздействия воздуха и ее принудительная деформация. Отсюда – многообразие технологических процессов сварки. Сейчас их известно более семидесяти. Одни процессы применяются широко, другие – ограниченно, но сварка в целом является наиболее важным способом получения неразъемных соединений.
В судостроении, например, использование сварки вместо клепки позволило сократить цикл строительства судов в 5–10 раз и на 20– 25 % снизить их металлоемкость. В строительстве предварительная
257
подготовка крупных сварных блоков и их последующая сборка и сварка на монтаже в 2–3 раза и более ускоряет сооружение мостов, крупных резервуаров, цементных печей, нефтеперерабатывающих установок, доменных печей. Сейчас практически все строительные металлоконструкции – сварные. На изготовление сварных конструкций расходуется около половины выплавляемой стали.
Доминирующее положение в производстве уже около полувека занимает дуговая сварка. На нее приходится более 60% всего объема сварочных работ.
Cвариваемость сплава зависит от комплекса свойств, определяющих возможность получить сварное соединение с требуемой прочностью при принятом технологическом процессе сварки. Одни сплавы можно сваривать по простейшей технологии, получая соединения высокого качества, при сварке других необходимы строгое соблюдение режимов, специальный выбор материалов, а в некоторых случаях – подогрев, проковка швов. Третьи сплавы можно сваривать только с предварительным и сопутствующим подогревом, последующей термической обработкой и т.д. Наконец, четвертые сплавы, склонные к образованию трещин, во время сварки необходимо подогревать, а после нее проводить термическую обработку. Перечисленные группы сплавов называют соответственно хорошо, удовлетворительно, ограниченно и плохо сваривающимися.
Свариваемость главным образом зависит от химического состава сплавов, поэтому для сварных конструкций используют стали и сплавы только определенных составов. Свариваемость некоторых сталей и цветных сплавов зависит от их структурного состояния, поэтому перед сваркой таких материалов может быть необходима термическая обработка.
В структуре сварного соединения можно выделить три участка: литую зону, зону частичного расплавления или переходную зону и зону термического влияния. Зона термического влияния – это участки основного металла, в которых под влиянием термического цикла сварки происходит изменение структурно-фазового состояния. Как правило, это приводит к ухудшению прочностных свойств основного металла. Могут быть участки с закалочными структурами (зона нормализации) и, наконец, участки, в которых проходят отпуск или старение. В некоторых сплавах идут и другие процессы.
258
Ширина зоны термического влияния и отдельных ее зон зависит от свойств материала и режима сварки.
18.7.2. Некоторые основные виды сварки
Дуговая сварка. Ручная дуговая сварка плавящимися электродами – самый распространенный способ дуговой сварки. Электрическая дуга между изделием и электродом, закрепленном в электрододержателе, оплавляет металл в зоне сварки. Все операции по зажиганию дуги, перемещению ее относительно изделия и подаче электрода выполняются вручную сварщиком. Стали, чугуны и многие цветные металлы можно сваривать этим способом, изменяя марку электрода и режим сварки.
При ручной дуговой сварке плавящимся электродом металл шва состоит главным образом из материала электрода. Поэтому характеристики электрода оказывают решающее влияние на качество шва. Электрод должен обеспечивать получение наплавленного металла с требуемыми прочностными и другими эксплуатационными характеристиками (например, коррозионной стойкостью). Кроме того, он должен иметь приемлемые сварочно-технологические свойства. К ним относятся устойчивость горения дуги, возможность сварки в различных пространственных положениях, отсутствие трещин и пор в шве, легкость очистки шва от шлака, производительность. Основные характеристики электрода определяются составом покрытия стержня и толщиной покрытия.
Впроцессе сварки по мере плавления стержня электрода покрытие расплавляется и создает шлак или газ, защищающий сварочную ванну от контакта с воздухом. Кроме того, в покрытие входят компоненты, стабилизирующие горение дуги, раскисляющие и легирующие металл швы.
Вкачестве шлако- и газообразующих компонентов используют мрамор, мел, плавиковый шпат, рутил, целлюлозу и др. Связующим в большинстве электродов является жидкое стекло (силикат натрия или калия). Стабилизаторами дуги служат вещества, содержащие щелочные и щелочноземельные металлы, понижающие потенциал ионизации дугового газа. В качестве раскислителей и легирующих добавок используют порошки соответствующих
259
ферросплавов, лигатур и чистых металлов. Многие составляющие покрытий выполняют сразу несколько функций. Например, мрамор
– это шлако- и газообразующее вещество и стабилизатор дуги, жидкое стекло – связка, шлакообразующее вещество и стабилизатор, а алюминобариевая лигатура – раскислитель и стабилизатор.
Аргоно-дуговая сварка (АДС) вольфрамовым электродом – один из самых универсальных и распространенных процессов дуговой сварки. В этом случае дуга горит между нерасходуемым вольфрамовым электродом и деталью. Через кольцевое сопло горелки, по оси которого расположен электрод, непрерывно подают инертный газ (аргон или гелий), защищающий сварочную ванну. Присадочный материал в виде прутков или проволоки подают в дугу сбоку вручную. Инертный газ обеспечивает более эффективную защиту сварочной ванны, чем при других способах дуговой сварки. Поэтому дуговую сварку вольфрамовым электродом в инертных газах широко применяют для химически активных материалов, которые необходимо особо тщательно изолировать от воздуха, например: алюминиевых, магниевых и жаропрочных сплавов, высоколегированных сталей, титана и др. Для алюминиевых сплавов это основной способ сварки плавлением. Лимитируют область применения АДС дороговизна и дефицитность аргона и гелия. В качестве электродов используют прутки и проволоку из чистого вольфрама, вольфрама с примерно 1,5 % оксида лантана, иттрия или тория. Введение оксидов приводит к снижению работы выхода электронов и позволяет повысить сварочный ток.
Электрошлаковая сварка. Электрошлаковая сварка, разрабо-
танная в институте электросварки им. Е. О. Патона, заключается в следующем. В замкнутое пространство между водоохлаждаемыми медными пластинами и вертикально установленными кромками свариваемых деталей засыпают флюс и подают электродную проволоку. Источник питания подсоединяют к электродной проволоке и свариваемым деталям. В начале процесса возбуждают дугу, флюс плавится и образуется электропроводный шлак. Шлак шунтирует дугу, она гаснет, и выходная цепь источника питания замыкается через шлак – начинается собственно электрошлаковый процесс. Ток, проходя через шлак, разогревает его до высокой температуры, в результате чего плавятся основной металл и электрод. Расплав
260