
Калин Физическое материаловедение Том 5 2008
.pdfих диссоциацию) металлов в плазме H2+CH4, H2+He, H2+Ar и др. газовых смесей; получение ультрадисперсных порошков оксидов и карбидов металлов; плазменная плавка металлов и сплавов.
Специфика плазменного синтеза материалов состоит в том, что требуется предварительное измельчение сырья, непрерывная его подача в плазму и обеспечение равномерности распределения в плазме, а в ряде случаев перевода в газовую фазу, и резкое охлаждение получаемого продукта. Во всех случаях в плазме велика доля капельной фазы. К сожалению, серьезные проблемы необходимо решать по повышению чистоты получаемых веществ и материалов.
2. Модифицирование материалов: формирование заданного рельефа поверхности, например травление и очистка поверхности, для улучшения смачиваем ости и адгезии; нанесение покрытий (слоев) на изделия; синтез химических соединений заданного состава на поверхности; плазмохимическое насыщение поверхностного слоя азотом (азотирование), углеродом (цементация) или одновременно азотом и углеродом (нитроцементация).
Ионно-плазменные технологии. Использование ионно-
плазменных технологий расширяет возможности обработки по сравнению с ионно-пучковыми, так как дает возможность чередовать операции распыления, нанесения покрытий и имплантации ионов. Ионно-плазменная обработка как процесс одновременной или последовательной обработки поверхности ионами и плазмой весьма эффективна при создании функциональных покрытий и пленок на материалах. В этом случае осуществляется ряд операций, необходимых для получения прочного сцепления покрытий с подложкой в следующей комбинации или последовательности: предварительная очистка поверхности, напыление атомов, ионное перемешивание в процессе напыления покрытий (ионноассистированные покрытия).
В результате улучшается адгезия атомов пленки, повышается плотность пленок, снижается температура их получения, сохраняется их стехиометрия, возможно создание многослойных пленок и др. достоинства. Однако еще недостаточно изучены физикохимия процессов формирования таких пленок, зависимость качества пленок от параметров плазмы и пучка ионов, сложно выбирать необходимые режимы осаждения и бомбардировки, необходимо тонко
301
регулировать и температуру подложки, и скорости осаждения, а также решать другие проблемы.
Концентрированные потоки энергии. Для различных видов КПЭ общим являются: высокие плотности мощности (~1012 Вт/см2) и энергии (~100 Дж/см2), высокие градиенты температуры, создаваемые в поверхностном слое (106 –108 К/см) и высокие скорости нагрева и закалки (109–1011 К/с), достижимые при определенных условиях. Каждая КПЭ-технология имеет свои особенности воздействия на твердое тело. Это касается передачи энергии в твердом теле: электронам при лазерном излучении, электронам и ядрам при электронном облучении, атомам, электронам и ядрам при ионной и плазменной обработке. Вследствие этого наблюдаются отличия в характере энерговыделения по глубине мишени и, следовательно, в распределении температуры и термонапряжений в твердом теле. Наибольшее проникновение в глубину мишени можно достичь при электронной обработке. Воздействие КПЭ на металлы с плотностью энергии до 106 Дж/кг вызывает испарение атомов, а при воздействии более 106 Дж/кг наблюдается гидродинамический выброс (взрыв) расплавленного вещества и образование плазменной «подушки». Плазменная «подушка» экранирует воздействие на поверхность «хвоста» импульса КПЭ и, следовательно, уменьшает жесткость воздействия потока энергии. При короткоимпульсном ( десятки наносекунд) воздействии КПЭ возможны следующие процессы: возбуждение и эволюция интенсивных механических возмущений в мишени; гидродинамическое движение расплава и образующегося пара; плазмообразование; интенсивное испарение вещества; дефектообразование, например, кратерообразование и формирование шероховатой поверхности.
КПЭ находят применение как для получения новых материалов, так и для модифицирования.
Получение (синтез) материалов: путем испарения мишени и конденсации атомов на заданной подложке (получение пленок, наноразмерных порошков, например, тугоплавких соединений); в результате инициирования химических реакций на поверхности и в объеме (твердофазные реакции создания новых фаз).
Модифицирование материалов (поверхностного слоя): в резуль-
тате сверхбыстрой закалки сплавов, в том числе из жидкого со-
302
стояния, формируется дисперсная и термоупрочненная структура (аморфизация, измельчение зерна, квазипериодические или многозонные структуры); осуществляется изменение элементного состава и фазового состояния путем имплантации элементов из плазмы и жидкофазного перемешивания (легирования) атомов мишени и пленки, предварительно нанесенной на мишень; формируется заданный рельеф поверхности путем ее оплавления, при этом возможно заглаживание дефектов или их устранение, создание дефектов для увеличения адгезионной способности поверхности; объемное ударное упрочнение путем формирования волн напряжений в мишени вследствие сверхбыстрого испарения поверхностного слоя материала; удаление ранее нанесенных пленок и покрытий путем испарения атомов или, наоборот, наплавка покрытий или слоев при соответствующей подаче вещества в зону воздействия КПЭ.
Проблемы внедрения РПТ. В настоящее время для модифицирования материалов широкое применение нашли лазерная обработка, ионная имплантация и использование плазменных (плазмохимических) процессов, в том числе для обработки материалов, полуфабрикатов и изделий. В стадии технологического освоения находятся ионно-плазменные процессы, мощные импульсные пучки ионов, электронов и потоки высокотемпературной плазмы.
Контрольные вопросы
1.Приведите примеры современных методов получения и обработки металлов и сплавов.
2.Перечислите основные этапы металлургического процесса получения сталей.
3.Рассмотрите на примерах основные этапы металлургических процессов получения цветных металлов.
4.Дайте определение основных технологических свойств металлов и сплавов, приведите примеры.
5.Рассмотрите основные технологические свойства металлов и сплавов и влияние на них состава и СФС.
6.Назовите основные процессы доменной плавки. Дайте характеристику и приведите реакции, протекающие при выплавке чугуна.
303
7.Рассмотрите основные способы производства стали, укажите их преимущества и недостатки.
8.Методы раскисления и их влияние на качество получаемых сталей.
9.Способы снижения содержания в стали и чугуне вредных примесей (серы, фосфора и др.).
10.Особенности современных технологий получения сталей особо высокого качества.
11.Роль шлака и его состав, свойства и формирование при выплавке чугуна и стали.
12.Влияние огнеупорных материалов, применяемых при выплавке чугуна и стали на качество металла.
13.Преимущества применения кислородного дутья при выплавке ста-
ли.
14.Определение пирометаллургии и гидрометаллургии на примере производства цветных металлов.
15.Конвертирование штейна и рафинирование черновой меди.
16.Плавка на шлак при производстве титана и особенности магниетермического восстановления титана.
17.Методы обогащения при производстве меди и титана.
18.Рассмотрите литейные свойства сплавов на примере получения отливок из чугунов и сталей.
19.Типы литейных форм, основные составляющие литейной оснастки
иих роль в получении качественных отливок.
20.Непрерывная разливка стали, ее преимущества.
21.Определение основных видов термической обработки и привести примеры их применение в качестве технологических операций и при формировании оптимального СФС.
22.Технология проведения основных видов отжига сталей.
23.Основные виды закалки сталей, критическая скорость охлаждения при закалке.
24.Влияние легирования на критическую скорость охлаждения и прокаливаемость сталей.
25.Применение отпуска и старения для достижения высокой прочности сталей и сплавов.
26.Основные способы цементации и азотирования сталей, их оптимальные режимы.
27.Классификация методов, обеспечивающих повышение уровня свойств поверхностного слоя изделий.
28.Рассмотрите преимущества и недостатки статических и динамических методов обработки металлов давлением.
304
29.Современные способы горячей и холодной обработки давлением, примеры их применения.
30.Влияние схемы и скорости нагружения на выбор оптимального способа обработки давлением.
31.Сущность порошковой металлургии, ее преимущества по сравнению с традиционной технологией выплавки слитков.
32.Современные технологии получения порошков и последующего компактирования на основе учета СФС порошков.
33.Основные эффекты влияния высокоскоростного охлаждения расплава на СФС быстрозакаленных сплавов.
34.Преимущества и недостатки основных методов сварки и пайки; привести примеры оптимального их применения.
35.Рассмотрите механизмы и основные параметры электрохимических, электроэрозионных и радиационно-пучковых способов обработки.
Список использованной литературы
1.Материаловедение и технология металлов: Учебник для вузов / Фетисов Г.П., Карпман М.Г., Матюнин В.М. и др. – М.: Высш. шк., 2005. – 862 с.
2.Конструкционные материалы ядерных реакторов: Учебник для вузов / Бескоровайный Н.М., Калин Б.А., Платонов П.А., Чернов И.И. –М.: Энергоатомиздат, 1995. – 704 с.
3.Материаловедение. Технология конструкционных материалов: Учебное пособие для студентов вузов. – М.: Высш. шк., 2005. – 752 с.
4.Б.А. Калин, М.И. Солонин Перспективные технологии получения и обработки материалов. Учебное пособие. – М.: МИФИ, 1999. – 52с.
5.Г.А. Ягодин, О.А. Синегрибова, А.М. Чекмарев Технология редких металлов в атомной технике – М.: Атомиздат, 1974. – 344 с.
6.Шульга А.В. Металловедение быстрозакаленных сплавов. Учебное пособие. – М.: МИФИ, 2000. – 68 с.
7.Металловедение и технология быстрозакаленных сплавов: Учебник для вузов: в 2 кн./О.Х. Фаткуллин, Г.Б. Строганов, А.А. Ильин, А.В. Шульга, В.Н. Мартынов. – Кн. 1. – М.: Изд-во МАИ, 2007. – 364 с.; Кн. 2.
–М.: Изд-во МАИ, 2007. – 416 с.
8.Шульга А.В. Основы металловедения быстрозакаленных сплавов: Уч. пособие. – М.: МИФИ, 2005. – 68с .
9.Структура и свойства быстрозакаленных сплавов/ А.А. Ильин, О.Х. Фаткуллин, Г.Б. Строганов, А.В. Шульга, В.Н. Марнынов/ Под общ. ред. чл.-корр. РАН А.А. Ильина. – М.: Альтекс, 2008. – 588 с.
305
10.Шульга А.В. Методы и техника получения быстрозакаленных сплавов. Учебное пособие. – М.: МИФИ, 2001. – 84 с.
11.Порошковая металлургия и напыленные покрытия. Учебник для вузов / В.Н. Анциферов, Г.В. Бобров, Л.К. Дружинин и др. – М.: Металлургия, 1987. – 791 с.
12.Стали и сплавы для высоких температур: Справ. Изд. В 2-х кн./ Масленков С.Б., Масленкова Е.А. – М.: Металлургия, 1991. – 832 с.
13.Новиков И.И. Теория термической обработки металлов. Учебник для вузов. – М.: Металлургия, 1986. – 392 с.
14.Гуляев А.П. Металловедение. – М.: Металлургия, 1986. – 647 с.
15.Перспективные радиационно-пучковые технологии обработки материалов: Учебник для вузов/ В.А Грибков, Ф.И. Григорьев, Б.А. Калин, В.Л. Якушин / Под ред. Б.А. Калина. – М.: Круглый год, 2001 – 528 с.
16.Григорьянц А.Г. Основы лазерной обработки материалов. – М.: Машиностроение, 1989. – 304 с.
17.Сварка и свариваемые материалы: В 3-х т. Т. II. Технология и оборудование. Справ. изд. / Под ред. В.М. Ямпольского. – М.: Изд-во МГТУ им. Н.Э. Баумана, 1998. – 574 с.
18.Лашко С.В., Лашко Н.Е. Пайка металлов. – М.: Машиностроение,
1988. – 376 с.
19. Понимаш И.Д., Орлов А.В., Рыбкин Б.В. Вакуумная пайка реакторных материалов. – М.: Энергоатомиздат, 1995. – 192 с.
306

ГЛАВА 19. СТАБИЛИЗАЦИЯ СТРУКТУРНО-ФАЗОВОГО СОСТОЯНИЯ МАТЕРИАЛОВ
Равновесное состояние сплавов, как следует из теории и простейших диаграмм состояний систем (ДСС), является частным случаем реального термодинамически нестабильного состояния, в котором эксплуатируется большинство материалов. Более того, сложнолегированные материалы с заданным уровнем свойств почти во всех случаях термодинамически нестабильны, а равновесное состояние не всегда является оптимальным с точки зрения свойств материала. Учитывая, что свойства в значительной степени опре-
деляются структурно-фазовым состоянием (СФС) материалов,
целесообразно рассматривать относительную стабильность материала, т.е. сохранение СФС и, следовательно, свойств в реальных условиях в течение всего времени работы материала.
Заданную структуру обычно получают, комбинируя определенным образом операции деформации, термообработки и диффузионного отжига, причем происходящие превращения искусственно затормаживаются, как правило, охлаждением до комнатной температуры в выбранный момент времени. Успешное проведение этих операций является существенной частью современных технологий получения материалов с требуемыми свойствами.
Например, материалы, полученные посредством плавления и литья, обладают далеко не оптимальной (литой) структурой, для разрушения которой и гомогенизации состава традиционно приме-
няют термомеханическую (ТМО) или многократную термомеха-
ническую (МТМО) обработки. Сама по себе механическая обработ-
ка может быть холодной (Тобр < Трекр) или горячей (Тобр > Трекр). По-
следующий нагрев стимулирует рекристаллизацию, т.е. получение заданного размера зерна.
307

19.1. Проблема стабильности структурно-фазового состояния материалов
СФС материалов включает в себя особенности строения материала, в том числе состав, кристаллическую структуру, микроструктуру, размер и распределение фаз (фазовое состояние), изменяемые легированием, технологиями изготовления и обработки. Как отмечалось ранее1, реальные материалы, обладающие избытком свободной энергии, нестабильны или относительно стабильны. Всегда могут протекать процессы, связанные с увеличением энтропии ( S max) и уменьшением свободной энергии ( G min) материала. Если исходное СФС было оптимальным, то эти изменения будут приводить к ухудшению состояния и свойств материала.
Представление о присущей металлическим материалам нестабильности показано на рис. 19.1,а на примере изменения свободной энергии атомов при переходе из руды в металл или сплав ( G возрастает), а затем – при коррозии ( G уменьшается). С этой точки зрения состояние атомов в руде является наиболее стабильным, и металл неизменно стремится вновь перейти в более стабильное химическое состояние, отличающееся от металлического.
Изменение уровня свободной энергии атомов при переходе в более стабильное состояние показано на рис. 19.1,б. Меньшему уровню G соответствует более стабильное состояние атома. Однако для перехода в более стабильное состояние (меньшее по G) требуется активировать процесс и преодолеть тот или иной потен-
циальный барьер ( GA 1, 2, 3 ).
Дополнительную свободную энергию, необходимую для перехода из одного положения в другое, атом получает за счет тепловых флуктуаций.
Таким образом, не трудно видеть, что величина Gi (как и Si) указывает общее направление процесса взаимодействия атомов: чем меньше уровень свободной энергии, тем стабильнее положение атомов и СФС. Но кинетика процесса перестроения атомов (и СФС) будет определяться энергией активации (GAi) этого процесса.
1 Физическое материаловедение. Т. 2. – М.: МИФИ, 2007. С. 337.
308
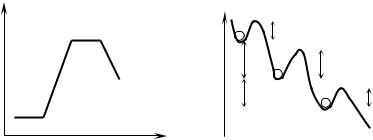
В большинстве практических случаев GA > kТ, так что скорость преодоления энергетического барьера очень мала.
G |
|
|
G |
|
|
|
|
|
|
|
|||
|
|
Сплав |
|
GA1 |
|||||||||
|
|
|
|
|
|
||||||||
Металл |
|
Коррозия |
|
|
G1 |
|
|
|
|
|
|
||
|
|
|
|
|
GA2 |
||||||||
|
|
|
|
|
|
|
|
||||||
|
|
|
|
|
|
G2 |
|
|
|
|
|
|
|
Руда |
|
|
|
|
|
|
|
|
GA3 |
||||
|
|
|
|
|
|
|
|
|
|
||||
|
Время |
|
|
|
|
|
|
|
|
|
|
||
|
|
|
|
|
|
|
|
|
|
|
|
|
|
|
|
|
|
|
|
|
|
|
|
|
Время |
||
|
|
а |
|
|
|
|
|
б |
Рис. 19.1. Изменение свободной энергии атомов в материале:
а– при получении металла из руды и при последующем окислении (коррозии);
б– при переходе атома (СФС) в более стабильное состояние. Здесь GAi – энергия
активации процесса, Gi – изменение свободной энергии атома при переходе из одного в другое состояние
Хорошо известно, что скорость того или иного термически активируемого процесса перехода атомов из одного состояния в другое определяется энтальпией активации ( HAi = GAi + Т SAi) и температурой:
|
|
|
|
Н |
|
|
|
v |
перех |
Ае |
kT . |
(19.1) |
|||
|
|||||||
|
|
|
|
|
|
Скорость перехода весьма чувствительна к температуре. Например, рассмотрим процесс перехода атомов из одного состояния в другое с энергией активации, равной 2 эВ/ат. При температуре T = 300 K скорость перехода атома будет пропорциональна
|
H A |
10–33. При температуре T = 1000 K скорость перехода уве- |
||
e kT |
||||
личится на 23 порядка и будет пропорциональна e |
H A |
10–10. Для |
||
kT |
сравнения по времени – это 1 с и 3 1014 лет. Весьма заметная скорость перехода при увеличении температуры всего на 700 К.
Существуют два различных типа возможной нестабильности СФС: истинная нестабильность и так называемая метастабиль-
309
ность. В последнем случае СФС перед достижением более стабильного состояния (с меньшим уровнем свободной энергии) должно пройти, как показано на рис. 19.1,б, через промежуточные менее стабильные состояния с повышенной энергией, отделенные одно от другого потенциальным барьером.
Наличие барьера может быть связано, например, с необходимостью зарождения и роста зародыша новой фазы (зерна) до критического размера, прежде чем метастабильная структура (СФС) приобретет возможность превратиться в более стабильную. При истинной нестабильности таких барьеров нет. Исходное СФС нестабильно и может переходить в другое состояние без предварительного увеличения энергии. В реальности перестроение СФС обусловлено движением атомов в решетке твердого тела, а для этого необходима активация этого движения. Разница между двумя типами стабилизации СФС состоит в том, что при метастабильных превращениях в стадии активации участвует множество атомов, тогда как для превращения второго типа достаточна последовательная активация лишь одного атома. Необходимость термической активации возникает потому, что при температуре, низкой по сравнению с абсолютной температурой плавления (Тпл), скорости диффузионных процессов, как показано на вышеприведенном примере оценке скорости перехода атомов, пренебрежимо малы. Существенные скорости изменения СФС наблюдаются, как правило, лишь при температуре, превышающей примерно 0,3Тпл.
19.2. Движущие силы изменения структурно-фазового состояния
Как видно на рис. 19.1,б, величины G1 и G2 характеризуют избыток свободной энергии атомов по сравнению с более стабильным состоянием. Поэтому абсолютные значения этих величин можно рассматривать как относительные движущие силы процесса перехода атомов в более стабильное состояние. Чем больше по абсолютной величине G, тем больше стимул к переходу системы в новое состояние. Причиной изменения СФС материала могут быть внутренние и внешние факторы.
310