
Калин Физическое материаловедение Том 5 2008
.pdfмежду припоем и соединяемыми металлами проходит твердофазное взаимодействие с образованием в контакте между ними нового сплава, более легкоплавкого, чем паяемые материалы; при его затвердевании образуется паяный шов. При реактивно-флюсовой пайке припой образуется в результате взаимодействия основного металла с флюсом. Диффузионная пайка – это процесс, при котором паяный шов затвердевает при температуре, превышающей температуру солидуса припоя.
Пайка имеет ряд значительных преимуществ перед сваркой благодаря возможности: соединять детали без расплавления основного металла, без нарушения геометрических размеров изделия, без зон гетерогенных структурно-фазовых состояний, соединять всевозможные сплавы, в том числе плохо сваривающиеся, одинаковые и разнородные, а также соединять металл со стеклом, керамикой графитом, полупроводниками; формировать соединения практически одновременно по всем поверхностям контакта, а не последовательно, как при сварке, изготавливать такие сложные по конструкции узлы, какие невозможно сделать другими способами; получать (формировать) качественные физические швы при соединении деталей в различных пространственных положениях; совмещать операции пайки и термической обработки при использовании одного и того же нагревательного оборудования.
Кромки деталей не оплавляются, поэтому при пайке можно сохранить размеры и форму деталей и паяного узла в целом.
Многие паяные соединения можно распаивать, что важно при монтаже и ремонте в приборостроении. Процесс пайки легко поддается механизации и автоматизации, особенно при массовом производстве. Все это обеспечило широкое применение пайки в разных областях машиностроения.
18.8.2. Технологические и вспомогательные материалы при пайке
Припои. Припои относят к технологическим материалам и подразделяют по температуре плавления на низкотемпературные (до 450 °С) и высокотемпературные (свыше 450 °С). Применяют припои в виде проволоки, ленты, фольги, штампованных колец, порошков или паст, смешанных с флюсами.
271
Низкотемпературные припои. Наиболее распространенными низкотемпературными припоями являются оловянно-свинцовые (ПОС). Они обладают высокими технологическими свойствами, весьма пластичны. Пайку этими припоями проводят обычно при нагреве паяльником. Для повышения прочности в ПОС вводят сурьму. Припои на основе олова, содержащие серебро, сурьму, медь, обладают высокой коррозионной стойкостью и применяются для пайки проводов, работающих во всех климатических условиях, без защиты соединений лакокрасочными покрытиями. Временное сопротивление большинства припоев этой группы 32–45 МПа, относительное удлинение 35–50 %, предел прочности паяных соединений на срез 22–32 МПа.
Для пайки паяльником латуни и меди используют припои на основе свинца с 1,5–3 % Ag. Они имеют большую термостойкость, чем оловянно-свинцовые, но уступают им по технологическим свойствам.
Для низкотемпературной пайки изделий из алюминиевых и цинковых сплавов используют припои на основе цинка с оловом.
Широкое применение при пайке полупроводниковых материалов, стеклянных и кварцевых изделий, вакуумных соединений, узлов криогенной техники получили индиевые припои, содержащие от 42 до 97 % In. Они легкоплавкие (температуры плавления в пределах 72–156 °С), хорошо смачивают металлы и неметаллические материалы, обладают высокой коррозионной стойкостью и пластичностью. Последнее позволяет паять ими материалы с разными температурными коэффициентами линейного расширения.
Высокотемпературные припои. Широкое применение для пай-
ки углеродистых и многих легированных сталей, никеля и никелевых сплавов получили медь, латунь и ряд других медных сплавов. Медь – самый распространенный припой для пайки в вакууме. Она обладает хорошей жидкотекучестью и легко затекает в капиллярные зазоры. Этим пользуются, когда необходимы соединения протяженностью более 15–20 мм. При пайке протяженных соединений в вакууме и в защитных средах медь на стальные детали наносят электролитически слоем 5–15 мкм. Существенный недостаток меди как припоя – высокая температура плавления.
272
Латунями паяют углеродистые стали, медь и чугун при быстром нагреве токами высокой частоты, в печах, пламенем газовой горелки или в соляных ваннах; в качестве флюсов используют буру и различные смеси. В газовых защитных средах и в вакууме латунями не паяют из-за испарения цинка. В качестве припоев можно использовать простые латуни (сплавы медь–цинк), но лучше пользоваться латунями с небольшим количеством кремния и олова. Кремний является активным раскислителем, поэтому цинк испаряется меньше и швы получаются более плотными. Температуры полного расплавления медно-цинковых припоев 825–980 °С, временное сопротивление 210–340 МПа, относительное удлинение –
1–48 %.
Изделия из коррозионностойких сталей паяют в вакууме или в инертных газах припоями на основе медь–никель и медь–никель– марганец. Они позволяют получать соединения с пределом выносливости 200–240 МПа. Температуры полного расплавления этих припоев 900–1280 °С. При пайке в вакууме марганец из припоя частично испаряется, и температура плавления припоя растет. Поэтому температура распайки соединения выше температуры пайки,
исоединение является жаропрочным до 500°С и выше.
Вэлектротехнической промышленности для пайки меди и ее сплавов широко применяют сплавы меди с фосфором (4–9) % Р и добавками других элементов. Медь и ряд медных сплавов можно паять этими припоями без флюсов, так как они самофлюсующиеся. Температура полного расплавления медно-фосфорных припоев – 850°С. Медно-фосфорные припои, содержащие серебро, более пластичны и легкоплавки, чем простые медно-фосфорные.
Изделия из меди и стали, испытывающие повышенные статические и вибрационные нагрузки, предпочтительно паять серебряными припоями (15–71 % Ag, остальное – медь и добавки). Они отличаются высокой пластичностью и технологичны. Особенно широко применяют припой, содержащий 72% Ag, эвтектический сплав с очень хорошими технологическими свойствами; температура плавления его 779 °С. При пайке этими припоями применимы все виды нагрева (кроме паяльников), флюсы, газовые среды и вакуум. Предел прочности на срез при пайке низкоуглеродистых сталей серебряными припоями больше их предела текучести. Введение лития,
273
цинка и других элементов позволяет снижать температуру плавления серебряных припоев и регулировать их свойства. Применение серебряных припоев лимитируется лишь дефицитностью серебра.
Для пайки коррозионностойких, жаропрочных и жаростойких сталей и сплавов широко применяют никелевые припои. Большинство из них содержит хром, повышающий жаропрочность и жаростойкость, а также элементы, снижающие температуру плавления (Si, P, В, Мn и др.). Температуры плавления этих припоев находятся в интервале 900–1280 °С. Легирование никелевых припоев бором и щелочными металлами обеспечивает им самофлюсуемость и позволяет паять коррозионностойкие и конструкционные стали в среде аргона без флюсов.
Алюминиевые сплавы паяют преимущественно припоями на основе сплавов системы алюминий–кремний. Обычно используют эвтектический сплав, содержащий 12% Si и плавящийся при 577 °С. Снизить температуру плавления припоя можно, вводя в него медь. Наиболее легкоплавок припой, содержащий 6% Si и 28 % Сu (tпл = = 525 °С). Все припои системы Al–Si–Сu пригодны для пайки сплавов, не упрочняемых термической обработкой. Введение цинка и германия в припой позволяет снизить температуру полного расплавления до 460–500°С и паять термически упрочненные сплавы (например, дуралюмины).
Припои на основе магния применяют преимущественно для пайки магния и его сплавов. Легирующие элементы в этих припоях
– алюминий, цинк и другие; температура их полного расплавления не превышает 600 °С. При пайке этими припоями в печах или газовой горелкой необходимы флюсы, предохраняющие припой от воспламенения.
Флюсы при пайке относят к вспомогательным материалам.
Для низкотемпературной пайки используют канифольные и галогенидные флюсы. Канифоль удаляет оксиды таких металлов, как медь, серебро, олово, и широко используется для пайки соединений, когда после пайки нельзя промыть изделие: остатки канифоли не вызывают коррозии. Применяют чистую канифоль и раствор канифоли в спирте. В последние годы получили применение канифольные флюсы с добавками хлоридов, анилина и других органи-
274
ческих веществ. С их помощью можно паять не только медные сплавы, но также стали, оцинкованное и никелированное железо.
Галогенидные флюсы можно использовать для низкотемпературной пайки почти всех черных и цветных металлов. Шире всего применяют хлористый аммоний и хлористый цинк, а также смеси, содержащие эти и другие хлориды. В последние годы все большее применение получают флюсы на основе солянокислого гидразина, анилина и других органических веществ. Соли гидразина при нагреве разлагаются с выделением водорода и хлористого водорода. Анилин имеет высокую флюсующую активность, причем анилиновые флюсы при пайке дают остаток, защищающий шов от коррозии.
Широкое распространение получили канифольные флюсы, содержащие в различных сочетаниях неорганические вещества (галогениды, бориды и др.) и органические (гидразин, глицерин и др.). Такие флюсы успешно применяют для пайки меди, различных конструкционных и коррозионностойких сплавов.
Для пайки алюминиевых и магниевых сплавов используют высокоактивные флюсы на основе хлоридов, фторборатов и органических веществ.
Флюсы для высокотемпературной пайки. При пайке углероди-
стых сталей, чугуна и медных сплавов медно-цинковыми и серебряными припоями в качестве флюса используют борную кислоту и буру в различных сочетаниях. При пайке легированных сталей и жаропрочных сплавов флюсующего действия буры и борной кислоты недостаточно, и в состав флюса вводят галогениды. Чаще всего вводят фториды натрия, калия, лития и кальция, а также фторбораты натрия и калия.
Флюсы для высокотемпературной пайки алюминиевых, магниевых и титановых сплавов состоят из различных хлоридов и фторидов.
18.8.3.Быстрозакаленные припои
Кнедостаткам пайки можно отнести загрязнение паяных швов
вслучае использования флюсов, развитие ликвационных процессов
ипористости при использовании припоев с широким интервалом кристаллизации, образование и рост хрупких интерметаллидных
275
фаз при пайке разнородных материалов, рост зерна в основном металле вследствие длительности процесса пайки, ограниченность выбора сплавов-припоев, совместимых с паяемыми материалами и отвечающих требованиям последующей эксплуатации паяного соединения. В целом используемые сегодня припои обладают рядом недостатков, связанных как с их химическим составом, так и с формой применения. В связи с этим весьма перспективными представляются новые высокотемпературные ленточные и порошковые припои, полученные в аморфном или микрокристаллическом состоянии методом быстрого затвердевания расплава и обладающие рядом уникальных свойств, – быстрозакаленные припои (БЗП).
Положительными характеристиками БЗП являются высокая химическая и фазовая однородность, достигаемые за счет фиксации в твердом состоянии жидкоподобной аморфной структуры или формирования микрокристаллической (нанокристаллической) структуры. При закалке металлических расплавов со скоростями 104– 106 К/с фиксируют: состояние пересыщенного твердого раствора (αт ≈ αж > αравн), гомогенное по объему распределение легирующих компонентов, подобное распределению в расплаве, созданном индукционной плавкой. Кластерное строение (распределение по размером и объемная доля) в аморфных БЗП регулируется перегревом расплава. При производстве БЗП получают калиброванную гибкую ленту толщиной 20–100 мкм и шириной 2–50 мм. После размола предварительно термообработанной ленты можно получать микропорошки.
Физико-химические качества БЗП обусловливают значительно более высокую диффузионную и капиллярную активность по сравнению с кристаллическими аналогами, а также превосходную гибкость. Быстрое затвердевание сужает интервалы плавления и кристаллизации, что в сочетании с малой толщиной (20–50 мкм) обеспечивает “мгновенное” равномерное плавление припоя по всему объему. Аморфность структуры означает также идентичность физико-химических свойств произвольно взятого участка ленты из любой партии сплава-припоя (при условии, конечно, одинаковости химического состава исходного сплава), что, в свою очередь, означает непрерывность и однородность сколь угодно большого по площади паяного соединения.
276
К числу положительных эффектов применения БЗП можно отнести и тот факт, что при оптимальном термическом цикле пайки ( 30 мин при Т > 700°) вследствие высокой химической однородности припоя, узкого температурного интервала плавления, равномерного плавления припоя по объему, хорошей смачиваемости поверхности, высокой капиллярной и диффузионной активности компонентов расплавленного припоя в паяном шве отсутствуют интерметаллиды даже при пайке таких металлов, как Be–Cu. Важно, что применение БЗП часто не требует дополнительной обработки паяемых поверхностей металлов. Для полной реализации свойств, заложенных в структурном состоянии БЗП, можно широко варьировать скоростями нагрева и охлаждения паяемой сборки.
Быстрозакаленные аморфные и микрокристаллические сплавы, получаемые в виде порошков при распылении расплава или лент (фольг) методом спиннингования, быстрой закалки плоской струи расплава, применяют в качестве припоев для высокотемпературной пайки соединений из циркония, титана, никеля, меди, стали и ряда других материалов. Некоторые составы БЗП и режимы их использования для пайки различных материалов приведены в табл. 18.1.
Пайка циркониевых изделий в атомной технике проводилась с испытанием припоев на основе Au, Ag, Pd с добавками Cu, Ni, Mn, Co, Be. Большинство этих припоев продемонстрировало значительное взаимодействие с цирконием с образованием соответствующих фаз. Для снижения физико-химического взаимодействия были использованы добавки в припой Zr или применены припои на основе циркония: Zr–Ni–Mn–Ag–B, Zr–Be–Sn. По комплексу механических свойств и коррозионной стойкости лучшими бинарными припоями являются сплавы Zr–50% Ag, Zr–29% Mn и Zr–24% Sn.
Применительно к пайке дистанционирующих решеток в тепловыделяющих сборках ядерных реакторов лучшим припоем по результатам длительных коррозионных (гидродинамических) испытаний и механическим свойствам является пятикомпонентный сплав на основе циркония: (80–91)Zr–(5,5–15)Fe–1,5Ge–(1–3)Cr–2,5Be.
Температура плавления этих припоев находится в интервале 930–1020 °С, а температура пайки составляет 960–1030 °С. Это весьма высокая температура для сплавов циркония и, поэтому, в процессе пайки наблюдается рост зерна основного металла с 7–8
277
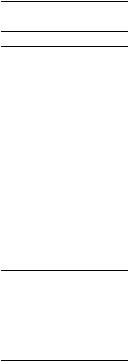
баллов до 5–6. Путем изменения состава и быстрой закалки удалось создать припои на основе циркония с температурами пайки ниже 900 °С.
|
|
|
|
Таблица 18.1 |
|
|
Характеристики быстрозакаленных припоев |
||||
|
|
|
|
|
|
Марка |
Состав, масс.% |
Начало/конец |
Тпайки, °С |
Паяемые материалы |
|
|
|
плавления,°С |
|
Медь и ее сплавы |
|
С1101 |
Cu–8,8Ni–7,0P–3,5 Sn |
615/660 |
650–750 |
||
|
|
|
|
Медь, медные сплавы |
|
С1108 |
Cu–12Sn–5In–2Ni |
750/870 |
870–950 |
и стали в любом соче- |
|
тании. Бериллий, |
|||||
|
|||||
|
|
|
|
вольфрам – медные |
|
|
|
|
|
сплавы |
|
С1201 |
Ti–12,0Ni–12,0Zr– |
830/900 |
900–1000 |
Титан и его сплавы |
|
24,0Cu |
|||||
|
|
|
|
||
С1202 |
Ti–12,0Ni–12,0Zr– |
750/850 |
850–950 |
Титан и его сплавы |
|
22,0Cu–1,5Be–0,8V |
|||||
|
|
|
Оксидная и нитридная |
||
|
|
|
|
||
C1203 |
50Ti–50Cu |
950/1000 |
1000–1050 |
керамика, керамика – |
|
|
|
|
|
металл |
|
|
|
|
|
Коррозионно-стойкие |
|
C1301 |
Ni–7,0Cr–4,6Si–3,1B– |
980/1010 |
1010–1180 |
стали, дисперсно- |
|
|
3,0Fe |
|
|
упрочненные стали, |
|
|
|
|
|
никелевые сплавы |
|
С1311 |
Ni–16,0Co–5,0Fe– |
980/1015 |
1020–1050 |
Стали – твердые спла- |
|
|
|
|
|
||
|
4,0Si–4,0B–0,4Cr |
|
|
вы типа ВК; Т5К10 |
|
|
Zr–14,0Ni–11,0Ti– |
|
|
Титан и его сплавы, |
|
С1409 |
690/750 |
750–850 |
цирконий и его спла- |
||
12,0Cu–2,0Nb–1,5Be |
|||||
|
|
|
|
вы, сплавы циркония |
|
|
|
|
|
со сталью |
Например, БЗП состава Zr–8Fe–8Nb–2,2Be имеет интервал плавления 815–865 °С и температуру пайки 890 °С и позволяет создавать паяные соединения сплавов циркония с температурой распайки выше 1500 °С. Важно подчеркнуть, что легирующие компоненты припоя должны иметь минимальные сечения захвата тепловых нейтронов, понижать температуру плавления сплава, обеспечивать его аморфизацию и жидкотекучесть. Припой в итоге должен обеспечивать температуру пайки ниже температуры α β
278
превращения сплава (циркония, титана) и ниже температуры образования эвтектик с компонентами паяемых материалов, иметь температуру распайки не ниже 1200 °С (условие стабильности при полной потере теплоносителя – аварии типа LOCA – Loss of Coolant Accident), обеспечивать коррозионную стойкость спая, не ухудшать коррозионные и прочностные свойства основного материала и обеспечивать механическую надежность изделия.
Этим требованиям удовлетворяет припой Zr–5,5 Fe–2,5Be–1Nb с добавками Ge–Cu–Sn–Cr и температурой пайки 780°С. Лучшие результаты по коррозионной стойкости паяных соединений сплавов циркония получены в режиме «быстрой» вакуумной пайки (нагрев до 780°С, выдержка – пайка 60–80 с, последующие охлаждение до 580 °С и выдержка 6 ч при этой температуре).
БЗП успешно используются для пайки разнородных металлов, например, трубчатых переходников цирконий–коррозионно- стойкая сталь и титан–коррозионно-стойкая сталь, которые являются важными узлами конструктивных элементов активных зон ЯЭУ и другой энергонапряженной техники. Для пайки переходников сталь–цирконий выбран БЗП в аморфном состоянии состава: Zr–Fe–Nb–Cu–Be–Sn–Cr. Для пайки переходников сталь–титан выбран БЗП в аморфном состоянии состава: Ti–25Cu–12Zr–12Ni– 1,5Be–0,8V.
Пайка с использованием быстрозакаленных высокотемпера-
турных припоев (MBF – Metal Brazing Foil) применяется в авиаци-
онно-космической промышленности при изготовлении лопаток газотурбинных двигателей, сопловых аппаратов из жаропрочных сплавов на основе титана, никеля, а также сотовых конструкций для обшивки двигателей, стенки камеры сгорания, стабилизаторов ракет, гондолы двигателя, панелей шумоглушения, диффузоров, теплообменников, повышения жесткости конструкций и т.д.
Быстрозакаленные низкотемпературные припои (MSF – Metal Solder Foil) обеспечивают высокие эксплуатационные характеристики металлических соединений в высокотехнологических областях электронной промышленности, в частности, при производстве силовых полупроводниковых устройств. Исключительная однородность и чистота быстрозакаленных припоев позволяет получать
279
прочные соединения, которые имеют дисперсную кристаллическую структуру (размер зерен не превышает 1 мкм), высокую долговечность по сравнению с пайкой традиционными припоями.
БЗП на основе титана и на основе никеля для пайки деталей и узлов газо-турбинных двигателей выпускают в виде сферических порошков (гранул) или лент. Порошковые припои изготавливают или методом газоструйного распыления расплава аргоном, или путем размола быстрозакаленной ленты. Плавку шихты осуществляют в вакууме. Очистка аргона перед распылением обеспечивает высокую чистоту быстрозакаленных порошковых припоев.
Методологические особенности создания БЗП для атомной техники. Проблема соединения разнородных материалов является одной из наиболее серьезных в атомной технике, надежность и безопасность которой является определяющей. Соединения деталей, работающих в активной зоне или на ее стыке с подводящими системами, должны обладать необходимыми механическими характеристиками, высокой коррозионной и радиационной стойкостью, обеспечивать проектную работоспособность конструктивных узлов.
В настоящее время проблема соединения конструктивных элементов решается многими способами. В реакторном машиностроении освоены все виды сварки, включая контактно-стыковую и диффузионную. Для соединения элемента корпуса разрядной камеры ИТЭРа планируют использовать горячее изостатическое прессование, диффузионную сварку и пайку различными припоями.
Разработка каждого припоя проводится на основе анализа условий работы соединения, формулирования требований к свойствам припоя, физико-химического анализа по выбору состава, экспериментального исследования физико-химических особенностей данного сплава, оценки критериев аморфизации (нанокристаллизации), отработки технологии быстрого затвердевания, оценки свойств паяльных композиций.
Основными требованиями к высокотемпературным припоям для создания прочных неразъемных соединений являются: температура плавления ниже, чем у соединяемых материалов и хорошая смачивать паяемых материалов. Применительно к атомной технике состав припоя должен обеспечить, наряду с механической прочно-
280