
Калин Физическое материаловедение Том 5 2008
.pdfстекает вниз, выжимая шлак, и затвердевает. Так постепенно формируется весь шов.
Сварку больших толщин осуществляют электродной проволокой, металлическими пластинами или лентой.
Флюсы для электрошлаковой сварки должны обладать высокой электропроводностью в жидком состоянии и оптимальной вязкостью, что обеспечивают повышенным количеством плавикового шпата CaF2, причем флюсы для сварки высоколегированных сталей на 70–100 % состоят из CaF2. Для начала электрошлакового процесса без возбуждения дуги используют электропроводный флюс в твердом состоянии.
При сварке конструкций с толщиной стенки более 40–60 мм производительность электрошлаковой сварки в 6–10 раз больше, чем автоматической сварки под флюсом. При этом существенно уменьшается расход электроэнергии и сварочных материалов (флюса и проволоки).
Существенный недостаток электрошлаковой сварки, ограничивающий ее применение, – это сильный разогрев околошовной зоны и, следовательно, возможность изменения СФС свариваемых сплавов. Это приводит к изменению свойств сплава, главным образом к повышению критической температуры хрупкости. Радикальный путь восстановления исходного уровня свойств сплава – это термическая обработка сварного изделия. Для повышения вязкости металла в околошовной зоне применяют электрошлаковую сварку с пониженной энергией, способы ускорения охлаждения шва во время сварки и местную термическую обработку сварных соединений
Электронно-лучевая сварка. Свариваемые детали, собранные без зазора или с маленьким зазором, помещают в вакуумную камеру и оплавляют зону сварки электронным пучком. При поглощении электронов с энергией порядка несколько десятков кэВ происходит разогрев и оплавление металла. Перемещая электронный луч вдоль стыка, получают сварной шов. Установка для электронно-лучевой сварки состоит из электронной пушки, вакуумных камер, устройств для перемещения луча вдоль стыка, блоков питания и управления. Электронная пушка предназначена для создания и фокусирования пучка электронов. Для фокусировки пучка электронов на деталь применяют магнитные линзы-катушки. Они позволяют фокусиро-
261
вать электронный луч в пятно диаметром 0,1–0,5 мм. Мощность нагрева электронным лучом (при токе в сотни миллиампер) может достигать 1,5–100 кВт и больше. Рабочий вакуум в камерах элек- тронно-лучевых установок составляет 10–2–10–3 Па. Перемещение луча вдоль линии соединения достигается либо чисто механическим перемещением деталей при неподвижном луче, либо отклонением луча электрическим или магнитным полем, что удобно для автоматизации процесса.
Режим и интенсивность нагрева можно точно и просто регулировать изменением тока луча, напряжения, фокусировки и времени. Интенсивность нагрева можно регулировать в очень широких пределах от 102 до 5 108 Вт/см2. Первая цифра соответствует интенсивности нагрева газовой горелкой, вторая – сфокусированному лазерному излучению. Это делает электронно-лучевой нагрев универсальным, применимым для самых разнообразных процессов термической обработки, пайки, сварки, резки. Сварку выполняют на режимах, обеспечивающих интенсивность нагрева порядка 106 Вт/см2, так как при чрезмерной интенсивности нагрева металл мгновенно испаряется и вместо сварки происходит резка.
Процессу электронно-лучевой сварки присущи две характерные особенности: первая – сварка протекает в вакууме, вторая – интенсивность нагрева очень велика.
Вакуум является идеальной защитной средой для сварки химически активных металлов. Парциальное давление кислорода и азота уже при вакууме 1,3 Па меньше, чем в особо чистом аргоне при атмосферном давлении. В камерах электронно-лучевых установок давление еще на 2–3 порядка ниже, поэтому при электроннолучевой сварке происходит не поглощение газов из окружающей среды, а дегазация расплавленного металла, соответственно, изменяются и свойства. Так, при сварке циркония в камере с аргоном твердость шва почти вдвое больше твердости основного металла, а при электронно-лучевой сварке шов даже несколько мягче основного металла. Поэтому электронно-лучевой сваркой сваривают конструкции из циркония, молибдена, хрома, ванадия и других химически активных металлов.
Интенсивный точечный нагрев при электронно-лучевой сварке приводит к очень быстрому плавлению и затвердеванию металла. В
262
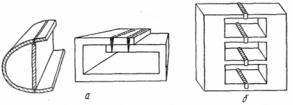
результате шов получается мелкозернистым с высокими механическими свойствами, а ширина зоны термического влияния сводится до минимума, в ряде случаев практически до нуля. Это позволяет сваривать сплавы, чувствительные к нагреву, а также предварительно закаленные изделия без ухудшения свойств околошовной зоны.
Благодаря интенсивному нагреву, шов имеет вид длинного узкого клина, соотношение глубины проплава и ширины шва 10–12 («кинжальный проплав»). Площадь зоны проплавления при элек- тронно-лучевой сварке примерно в 25 раз меньше, чем при дуговой. В результате сводятся до минимума сварочные деформации и резко сокращается затрата энергии на единицу длины шва. При дуговой сварке она в 10–15 раз больше.
Малый диаметр электронного пучка и его независимость от свариваемого изделия позволяют выполнять сварные соединения в узких разделах и труднодоступных местах, что невозможно другими способами сварки. Когда нет доступа к одному из элементов конструкции, выполняют прорезные швы: сварное соединение получают, проплавляя насквозь один из элементов. Удается также получать сварные соединения проплавлением трех–четырех стыков одновременно (рис. 18.14).
Рис. 18.14. Проплавные (а) и трехстыковое (б) соединения при электроннолучевой сварке
Регулирование мощности нагрева электронным лучом позволяет осуществлять сварку почти любых сплавов, в том числе тугоплавких и редких металлов, сталей и цветных сплавов.
Отсутствие деформаций при электронно-лучевой сварке способствует широкому применению ее в машиностроении, так как сварные детали можно использовать без последующей механической обработки.
263
Основные препятствия на пути к более широкому применению электронно-лучевой сварки – это сложность и дороговизна установок, особенно с большими вакуумными камерами, и необходимость защиты персонала от мощного потока рентгеновского излучения, возникающего при работе установки.
Газовая сварка. Интенсивность нагрева металла газокислородным пламенем невелика (102–103 Вт/см2), гораздо меньше, чем при дуговой сварке (103–105 Вт/см2). Поэтому газовым пламенем металл нагревается медленнее, чем дугой, и ширина зоны термического влияния значительно больше.
Управлять процессом нагрева и расплавления металла при газовой сварке легче, чем при дуговой: процесс не такой быстрый, визуально контролируется, можно в широких пределах изменять интенсивность нагрева, приближая – отдаляя или наклоняя горелку. Это очень существенно при сварке малых толщин.
Газовую сварку широко применяют во многих отраслях для изготовления изделий из тонкого листа, трубопроводов небольшого диаметра, сварки чугуна, бронзы и цветных сплавов, а также для выполнения наплавочных работ. Очень часто газовую сварку используют для выполнения работ в полевых условиях, где нет электроэнергии, и для выполнения различных ремонтных работ (сварка труб в зданиях, кабин автомобилей и дорожных машин и др.). Основные недостатки газовой сварки по сравнению с ручной дуговой: меньшая производительность и экономичность при толщинах более 5 мм, большие деформации основного металла, перегрев и рост зерна в сварном соединении.
Наиболее универсальным и эффективным горючим газом для газовой сварки является ацетилен. Температура ацетиленокислородного пламени достигает 3150 °С. Она выше, чем при сжигании любого другого газа. Но ацетилен дорог и взрывоопасен, поэтому в ряде случаев вместо ацетилена используют другие горючие газы – природный газ, пропан-бутановые смеси, а также керосин и бензин. Такая замена возможна при сварке всех металлов, кроме легированной стали, меди, никеля и его сплавов, серебра.
Ацетилен и кислород смешивают в нужной пропорции в сварочной горелке. Горючая смесь, выходящая из мундштука горелки, сгорает, создавая устойчивое и концентрированное высокотемпе-
264
ратурное сварочное пламя. В пламени сварочной горелки выделяют три зоны: ярко светящийся внутренний конус (ядро), основанием которого является отверстие мундштука, довольно четко очерченную внутреннюю зону и наружную зону – факел пламени. Для полного сгорания одного объема ацетилена нужно 2,5 объема кислорода. В горелку же подают один – полтора объема кислорода, а остальной кислород поступает из окружающего воздуха. В ядре пламени много непрореагировавшего кислорода, во внутренней зоне в основном происходит окисление ацетилена подаваемым кислородом, в факеле – догорание ацетилена за счет кислорода воздуха. В ацетилено-кислородного пламени эти три зоны легко различимы визуально.
Взависимости от отношения объемов кислород–ацетилен различают три основных вида пламени: нормальное – не вызывающее окисления металла или насыщения его углеродом, окислительное – вызывающее окисление металла, и науглероживающее – вызывающее переход углерода из продуктов горения в металл.
Вбольшинстве случаев сварку выполняют нормальным пламенем. Иногда используют слегка науглероживающее или слегка окислительное пламя.
18.7.3. Специальные виды сварки
Плазменная сварка, или сварка сжатой дугой – это особый вид сварки дугой прямого действия в среде защитного газа. При этом металл нагревается потоком плазмы с температурой до 20 000– 30 000 °С, истекающим со сверхзвуковой скоростью. В камере плазмотрона помещается вольфрамовый электрод и между ним и деталью горит дуга. Через камеру под давлением подается плазмообразующий газ (аргон, гелий и др.). Ось потока газа совпадает с осью дуги. Газ проходит через сопло на выходе плазмотрона, обжимается и приобретает высокие температуру, степень ионизации и скорость. По кольцевому каналу вокруг плазменного сопла дополнительно подают инертный газ для защиты зоны сварки. Защита необходима, потому что плазменная струя вытекает с большой скоростью и увлекает за собой в зону сварки окружающий воздух. В качестве защитного газа используют аргон, азот, смесь аргона с
265
водородом, гелием или азотом – в зависимости от свойств свариваемого материала.
Интенсивность нагрева металла плазменной струей больше, чем при дуговой сварке, поэтому ее можно использовать для высокопроизводительной сварки, а также для резки металла. Этим способом сваривают медь и ее сплавы, алюминиевые сплавы, высоколегированные стали. Толщина свариваемого металла от 0,5 до 12 мм, а скорость сварки 4–30 м/ч и больше.
Широкое применение получила микроплазменная сварка для сварки высоколегированной стали и различных цветных металлов толщиной до 0,5 мм со скоростями до 25 м/ч. Стабильное горение дуги и устойчивость микроплазмы на малых токах (0,1 А и выше) достигается благодаря непрерывному горению вспомогательной «дежурной» дуги между электродом и соплом плазмотрона, а также благодаря сильному сжатию столба дуги из-за малого диаметра сопла (диаметр канала в нем меньше 1 мм). При микроплазменной сварке часто необходимо дополнительно подавать инертный газ для защиты остывающих участков и обратной стороны сварного шва.
Микроплазменную сварку выполняют вручную и автоматически и используют для сварки таких изделий, как сильфоны, мембраны, миниатюрные трубопроводы, полупроводниковые приборы.
Лазерная сварка – это способ сварки плавлением, при котором металл нагревают излучением лазера. Интенсивность нагрева металла (плотность потока мощности) сфокусированным лазерным излучением может достигать 5 108 Вт/см2, что достаточно для мгновенного испарения металла. Сварку осуществляют при меньших интенсивностях нагрева.
Основное достоинство лазерной сварки – быстрый точечный нагрев металла до плавления. Это позволяет свести к минимуму ширину околошовной зоны, сварочные напряжения и деформации. Механизм процессов при лазерной сварке во многом схож с элек- тронно-лучевой сваркой, но для выполнения лазерной сварки не обязательно вакуумировать изделие и не требуется защита персонала от рентгеновского излучения. Мощность лазерных сварочных установок ограничена несколькими киловаттами, тогда как мощность электронно-лучевых установок может быть любой. Кроме того, КПД преобразования энергии в лазерное излучение очень ни-
266
зок – не превышает нескольких процентов. Поэтому лазером сваривают преимущественно толщины до 1 мм.
«Холодная» сварка – это сварка давлением при комнатной температуре. Наиболее распространены точечная и стыковая холодная сварка. Точечной сваркой сваривают внахлестку листы толщиной до 0,2–15 мм, сжимая их круглыми или прямоугольными пуансонами. Для получения сварной точки пуансон вдавливают на глубину 0,7–0,9 толщины свариваемых деталей. Таким способом можно сваривать только пластичные металлы – алюминий, никель, медь, технически чистое железо, свинец и некоторые другие. Давление, необходимое для сварки, составляет для меди 2000 МПа, а для отожженного алюминия 600 МПа.
Диффузионная сварка – это способ сварки давлением в вакууме. Свариваемые детали сжимают, нагревают в вакууме до температуры, не превышающей 0,8 температуры плавления, и длительно выдерживают. Длительная выдержка при нагреве и сжатии способствует протеканию процессов диффузии в металле и позволяет получать соединения при небольшой пластической деформации. В большинстве случаев деформируются только микровыступы на соединяемых поверхностях, и изменение размеров узла в целом ничтожно мало. Диффузионную сварку можно осуществлять не только в вакууме, но и в защитных газах – гелии, аргоне, водороде.
Этим способом можно соединять практически любые металлы, а также металлы с полупроводниками и другими неметаллическими материалами (например, медь с сапфиром). Основные достоинства метода, определяющие область его применения, – это ничтожно малая деформация, возможность получения сварного соединения при относительно низких температурах и сварка разнородных материалов. Диффузионную сварку широко применяют в электронной промышленности (сварка металлических выводов с полупроводниками, сварка магнитов и др.). Имеется опыт применения ее для изготовления деталей сложной формы в машиностроении.
Сварка трением – это способ сварки давлением с нагревом, при котором свариваемые поверхности нагревают трением одну о другую. В простейшем случае сварку трением встык осуществляют, вращая одну деталь, когда другая неподвижна, и сжимая их осевым усилием. Трущиеся поверхности разогреваются, трение способст-
267
вует разрушению оксидных пленок на них. Затем вращение прекращают, продолжая сжатие, и совместная пластическая деформация приводит к образованию соединения, как при стыковой контактной сварке. Осевое усилие в процессе сварки может оставаться неизменным, а может и меняться. Часто в конце процесса прикладывают увеличенное «ковочное» усилие.
Основные достоинства сварки трением – простота, малая энергоемкость, стабильность качества соединений, высокая производительность, возможность сварки разнородных металлов, а также металлов с керамикой. Диапазон свариваемых сечений 30–8000 мм2. Наиболее широко сварку трением используют в крупносерийном и массовом производстве (например, при изготовлении сверл, калибров, клапанов двигателей и т. п.), когда одна часть детали делается из дорогой легированной стали, другая – из дешевой углеродистой.
Сварка взрывом – это особый вид сварки давлением. Соединение образуется при соударении двух свариваемых деталей (пластин) под действием ударной волны. Одну из пластин (неподвижную) укладывают на твердое массивное основание, вторую (метаемую) располагают под углом 3–10° к поверхности первой при расстоянии 2–3 мм в вершине угла. На метаемую пластину накладывают равномерным слоем взрывчатое вещество и около вершины угла устанавливают электродетонатор. При взрыве детонатора развивается давление до 20 ГПа, сообщающее метаемой пластине скорость более 1000 м/с. Соударение метаемой пластины с неподвижной сопровождается местной пластической деформацией и нагревом металла. При этом пластины очищаются и свариваются, обычно с образованием волнистой границы между свариваемыми деталями.
Соединение при сварке взрывом, в отличие от всех других способов сварки, образуется практически мгновенно – за микросекунды. Благодаря этому взрывом можно сваривать разнородные металлы, которые не свариваются другими способами из-за образования хрупких интерметаллических соединений. Взрывом можно сваривать и небольшие, и крупногабаритные изделия.
Способ применяют для получения биметаллических заготовок и деталей (например, плакирование коррозионностойкой сталью лопастей гидротурбин), а также для сварки различных деталей.
268
18.7.4. Проблемы создания сварных соединений атомной техники
Эксплуатационная надежность твэлов и других внутриреакторных устройств во многом определяется качеством соединения конструктивных элементов, обеспечивающим герметизацию твэлов, точное их дистанционирование внутри тепловыделяющих сборок (ТВС), а также ТВС в активной зоне. Наиболее распространенной технологией для соединения элементов различных конструкций является сварка: газо-дуговая, лазерная, электронно-лучевая, кон- тактно-точечная, контактно-шовная, контактно-стыковая, магнит- но-импульсная и диффузионная. Использование сварки обусловлено такими достоинствами, как высокая скорость процесса и его автоматизация, обеспечение сплошности, размера и формы изделий, норм герметичности, высокой коррозионной стойкости и прочностных характеристик соединений.
Однако качество сварки в значительной степени зависит от элементного и фазового составов соединяемых материалов, однородности их структуры и качества технологии получения. При отклонении от технологических требований при сварке могут наблюдаться непровары и трещины в зоне шва и в зоне термического влияния, поры, газовые каналы (свищи, вздутия) и другие дефекты.
Особенно сложным обеспечение качества соединений становится при сварке дисперсно-упрочненных материалов, имеющих сложную температурную зависимость пластических характеристик, а также при сварке разнородных материалов, переходников разнородных металлов. Лидирующей технологией при производстве переходников, например, сталь–титан и сталь–цирконий является метод сварки в твёрдой фазе (ударом, взрывом, совместным прессованием, экструзией и т. д.). К существенным недостаткам сварки в твёрдой фазе переходников, включая диффузионную сварку, можно отнести достаточно сложную технологию, требующую специального производственного оборудования. Для получения надёжного соединения необходимо иметь большие развитые площади контакта сопрягаемых деталей и т.д.
При контактно-стыковой сварке изделий требуется определенная ширина контактной зоны, равная не менее диаметра электрода.
269
Это накладывает определенные ограничения на конструкцию изделий. Наличие зазоров, зоны термического влияния, остаточных напряжений – это все особенности технологии сварки.
18.8. Методы пайки
Пайка – это процесс соединения частей изделия с помощью введенного между ними промежуточного материала – припоя, температура плавления которого ниже, чем у паяемых металлов. Процесс пайки схож со сваркой плавлением, но при сварке плавятся и присадочный, и основной металл, при пайке же плавится только припой, а основной материал изделия не доводится до расплавления. Паяное соединение образуется при затвердевании припоя благодаря физико-химическому взаимодействию между припоем и основным металлом.
18.8.1. Технологическая классификация способов пайки
Современные процессы пайки подразделяют по температуре плавления припоя на две группы: пайка низкотемпературными припоями (tпл до 450 °С) и пайка высокотемпературными припоями (tпл выше 450 °С). Низкотемпературные припои используют в промышленности и в быту для пайки изделий, которые не подвергаются воздействию высоких температур и значительных механических нагрузок. Высокотемпературные припои применяют тогда, когда требуются высокая прочность и (или) работоспособность при повышенных температурах.
Нагрев при пайке осуществляют разными способами. Основные из них – пайка в печах, индукционная, сопротивлением, погружением в расплавы солей или припоев, паяльниками, нагреванием электронным пучком или лезерным излучением.
По условиям заполнения зазора и механизму образования паяного соединения способы пайки подразделяют на капиллярный, некапиллярный, контактно-реактивный, реактивно-флюсовый и диффузионный. При капиллярной пайке припой затекает в зазор и удерживается в нем под действием капиллярных сил. При кон- тактно-реактивной пайке между соединяемыми металлами или
270