
Калин Физическое материаловедение Том 5 2008
.pdf
Таблица 16.1
Возможные виды деформирования конструкционных элементов ЯЭУ
Вид |
Зависимости деформации, |
Измеряемая |
|
||||
деформиро- |
напряжения и температуры |
характеристика |
Примечание |
||||
вания |
от времени |
|
|
|
|
|
|
Растяжение |
|
Tπ Tp |
|
р – нагрузка |
|||
(сжатие) |
|
в |
|
0,2 |
|
|
|
|
р = const, Т = const |
Tp |
Tp |
|
|
||
|
|
|
|
|
|
|
|
Ползучесть |
|
Tp |
|
Tp |
|
– постоянное |
|
|
|
, |
|
напряжение |
|||
|
const, T const |
%,ч |
|
|
ч |
|
|
|
|
|
|
|
|
|
|
Ползучесть |
|
|
|
|
|
|
|
неизотерми- |
|
T%,p ч , |
Tчp |
|
|||
ческая |
const |
|
|
|
|
|
|
|
|
|
|
|
|
|
|
Ползучесть |
|
|
|
|
|
|
m – среднее |
при цикличе- |
|
Tp |
|
|
Tр |
|
напряжение |
ских напря- |
T const |
%,ч , |
σч |
|
|
||
жениях |
|
|
|
|
|
|
|
|
|
|
|
|
|
|
|
Ползучесть |
|
|
|
|
|
|
|
динамическая |
|
T%,πч , |
Tчp |
|
|
||
|
T const |
|
|
|
|
|
|
Усталость |
|
|
|
|
|
|
|
(высокотем- |
|
Tπ |
|
|
|
|
|
пературная) |
|
1,N |
|
|
|
||
T const |
|
|
|
|
|
|
|
|
|
|
|
|
|
|
|
Термоуста- |
|
|
|
|
|
|
|
лость |
|
1,T |
|
|
|||
|
0 |
|
|
|
|
|
|
Усталость |
|
1,T |
|
Nц 104 |
|||
малоцикло- |
|
|
|
||||
вая |
|
|
|
|
|
|
|
В случае растягивающих (сжимающих) нагрузок работоспособность материала в части зависимости от его свойств будет определяться пределом прочности на разрыв и запасом пластичности. При длительной эксплуатации при достаточно высоких температурах например, выше 200 °С для сплавов циркония, 360 °С для углеродистой стали и 450 °С для коррозионно-стойкой стали материал
51
будет деформироваться при напряжениях, меньших предела текучести (вследствие ползучести). В данном случае важными ограничивающими характеристиками материала являются предел ползучести и предел длительной прочности.
Однако часто явление ползучести материалов протекает в условиях циклирования температуры, напряжений и при наличии вибрации и поэтому интерес представляют данные о характеристиках неизотермической, нестационарной и динамической ползучести.
При режимах эксплуатации материала, связанных с цикличностью механических нагрузок, работоспособность будет зависеть от циклической прочности, важной характеристикой которой является предел выносливости материала.
Напомним, что в зависимости от числа циклов нагружения, необходимого для достижения предела выносливости материала, различают явление усталости (число циклов N > 105, суммарная деформация незначительная), малоцикловой усталости (N 104) и повторно-статического разрушения (N < 102, значительные деформации).
Основной характеристикой материала, описывающей его сопротивление усталости, является предел выносливости –1,N, представ-
ляющий собой наибольшее циклическое напряжение, выдерживаемое материалом неограниченное число раз (обычно более 107 раз).
Предел выносливости при симметричном цикле нагружения обозначают –1, при несимметричном – R. Для материалов, при испытании которых кривая усталости непрерывно понижается с увеличением числа циклов, устанавливают предел ограниченной выносливости. В этом случае обязательно указывают число циклов N (базу испытаний) – –1,N или R,N. При циклическом изменении тепловых потоков, вызывающих соответствующее изменение температуры, необходимо знать величины предела выносливости материала в условиях термической усталости ( –1,Т).
Таким образом, работоспособность материала и, следовательно, КЭ будет определяться рядом его механических характеристик, полученных при испытании в условиях, максимально приближенных к эксплуатационным.
52
Основными методами оценки работоспособности конструкций или КЭ являются стендовые, натурные и эксплуатационные испытания. Однако в ряде случаев, например из-за высокой трудоемкости или больших материальных затрат, эти испытания нельзя осуществлять полностью или частично. В таком случае, а также при разработке или проектировании, например, оптимальной заданной конструкции, проводят расчетное обоснование прочности элементов установок. При этом по соответствующим нормам с учетом эксплуатационных условий проводят оценки прочности по таким предельным состояниям, как вязкое и хрупкое разрушение, пластическая деформация, потеря устойчивости, изменение формы и размеров, появление макротрещины, например, при циклическом нагружении.
Обоснование прочности конструкции проводят в два этапа. Сначала выбирают основные размеры конструкции, а затем осуществляют поверочный расчет. При выборе размеров изделия в качестве основных используют такие механические характеристики, как пределы прочности и текучести, ползучести и длительной прочности с учетом соответствующих запасов.
При поверочном расчете, служащем обоснованием прочности проектируемого элемента конструкции, учитывают все нагрузки и эксплуатационные условия и, по существу, проверяют допустимость возникающих напряжений и деформаций. В процессе расчета необходимо учесть изменение механических характеристик вследствие взаимодействия (совместимости) материалов, их корро- зионно-эрозионного поведения, неоднородности полей излучения и температур, возможных структурных превращений в процессе эксплуатации. Поверочный расчет должен четко коррелировать с функциональным назначением конструктивного элемента, его формой (размерами), характером и величиной прикладываемых нагрузок и температурных воздействий, определяющих предельное состояние элемента. Исходя из этого расчет может быть проведен на статическую прочность (например, корпуса ВВЭР), устойчивость (например, корпуса ТЯР, оболочки твэла), циклическую прочность (например, корпуса ИТЯР), длительную прочность (например, канальных труб, оболочек твэла) и др. Во всех случаях
53
удовлетворение условий прочности проверяется для наиболее напряженных участков элементов конструкции путем вычисления приведенных напряжений и их сравнения с допускаемыми. Например, критерий прочности при расчете конструкции в условиях статического нагружения можно представить в виде пр < [ ], где пр – приведенное напряжение; [ ] – допускаемое напряжение. Допускаемое (номинальное) напряжение, например, для корпуса реактора, работающего под давлением (ВВЭР), принимают наименьшим из следующих значений:
[ ] = min в/nв; 0,2/n0,2; п/nп; дл/nдл Tp, (16.9)
где Тр – рабочая температура; nв, – запас прочности (nв, = 2,5); n0,2 – запас по пределу текучести (n0,2 = 1,5); nп – запас по пределу ползучести (nп = 1,2); nдп – запас по пределу длительной прочности
(nдп = 2,0).
При расчете на статическую прочность при высокой рабочей температуре важно определить факторы, лимитирующие работоспособность материала: или деформация, или разрушение. Если ограничение накладывается на величину допускаемой деформации, то в формуле (16.9) определяющей характеристикой будет предел ползучести с указанием допустимой деформации.
Если ограничивающим фактором является разрушение, то определяющей характеристикой будет предел длительной прочности. Расчет изделий на устойчивость требует знания модуля нормальной упругости материала (Е). При расчетах на прочность при длительной эксплуатации в условиях высоких температур необходимо знать пределы ползучести и длительной прочности материала в условиях, близких к эксплуатационным.
В общем случае для характеристики или расчета сопротивления материалов пластическим деформациям и разрушению с позиций статической прочности требуется знание минимум четырех механических характеристик материала: пределов прочности, текучести, ползучести и длительной прочности. В этом случае определяют эквивалентное (максимально допустимое) напряжение как минималь-
ную величину указанных выше пределов, т.е. σэmax min σi , а также определяют возможные механизмы деформации.
54
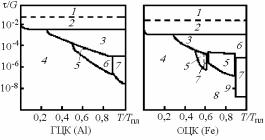
При определении механизмов деформации материала в процессе эксплуатации важными являются величины максимально допустимого приведенного напряжения (определяемого отношениями /Е или /G, где – нормальное, а – сдвиговое напряжения, Е – модуль Юнга, G – модуль сдвига) и приведенной рабочей температуры (определяемой отношением рабочей температуры к температуре плавления материала – Тр/Тпл). Зная приведенные напряжения и температуры, по известным в литературе картам деформации, которые строятся для материалов в координатах: приведенные напряжения – приведенные температуры, т.е. /Е = f(Тр/Тпл) или /G = = f(Тр/Тпл), определяют основной механизм деформации материала
(рис 16.4).
Рис. 16.4. Типичные карты деформации для ОЦК и ГЦК металлов: 1 – теоретическая прочность при сдвиге ( /G): (ГЦК – 0,033–0,045;
ОЦК – 0,100–0,125); 2 – дислокационное скольжение; 3 – дислокационная ползучесть; 4 – область упругости; 5 – зернограничная ползучесть (Кобла); 6 – диффузионная ползучесть (переползание дислокаций, миграция атомов); 7 – диффузионная ползучесть (образование и миграция вакансий);
8 – превращение ОЦКα–Fe – ГЦКγ–Fe; 9 – превращение ГЦКγ–Fe – ОЦКδ–Fe
Если рабочая температура относительно низкая (Тр < 0,3·Тпл), то выбираемый материал должен отвечать критериям прочности. Если же Тр > 0,3–0,4, то выбираемый материал должен отвечать критериям длительной прочности, т.е. быть жаропрочным. Если возможны циклические изменения температуры, то материал должен быть термостойким и так далее.
Механические свойства позволяют определить долговечность конструктивных элементов в условиях циклирования механической
55
нагрузки, при этом используют значения предела выносливости материала. Для конструктивных элементов, работающих под действием больших давлений, необходимо проводить оценку надежности материалов, их сопротивления хрупкому разрушению. Это важно в том случае, если материал склонен к охрупчиванию в процессе эксплуатации вследствие старения, накопления радиационных дефектов, коррозионного взаимодействия со средой (водородное охрупчивание, межкристаллитная коррозия), действия остаточных напряжений, статических и динамических перегрузок и других причин. В качестве критериев определения надежности материала, т.е. его сопротивления внезапному хрупкому разрушению, могут быть использованы температурный запас вязкости Т, критическая длина трещины lкр или удельная работа зарождения и роста трещины аk, коэффициент интенсивности напряжений K1С.
Температурный запас вязкости определяется по формулеТ = Тр–Тхр, где Тр – рабочая температура, Тхр – критическая температура хрупкости, соответствующая переходу металла из пластичного в хрупкое состояние. Поэтому для применяемых материалов важно знать Тхр, значение которой в общем случае может быть найдено по следующей формуле:
Тхр = Тхр0 + ТN + Тст + Трад + Ткор, |
(16.10) |
где Тхр0 – критическая температура хрупкости материала в исход-
ном состоянии; ТN – сдвиг критической температуры вследствие накопления усталостных повреждений; Тст – сдвиг вследствие старения материала в процессе эксплуатации; Трад – сдвиг вследствие накопления радиационных повреждений; Ткор – сдвиг вследствие коррозионного взаимодействия со средой. Удельная работа зарождения и роста трещины
аk = аз + ар, |
(16.11) |
где аз – работа зарождения трещины; ар – работа роста трещины. Представление удельной работы зарождения и роста трещины в виде двух слагаемых позволяет лучше оценить сопротивление материала хрупкому разрушению. Высокопрочные материалы имеют высокие значения аз и низкие ар, а пластичные материалы – низкие
56
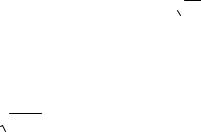
значения аз и высокие ар. Высокой конструктивной прочностью обладают материалы, имеющие наибольшие значения аk, аз и ар.
Коэффициент интенсивности напряжений K1 характеризует локальное повышение уровня растягивающих напряжений у вер-
шины трещины. При длине трещины, равной 2l, K1 = πl . Коэффициент K1, можно рассматривать как напряжение, действующее впереди вершины трещины вдоль направления ее распространения на заданном расстоянии от вершины. Тогда критическое значение коэффициента интенсивности напряжений в случае плоского деформированного состояния называют вязкостью разрушения и
обозначают K1С, причем K1С ЕG1C , где G1C – работа образования
новой поверхности раздела, а Е – модуль нормальной упругости. С позиций оценки интенсивности напряжений в вершине тре-
щины считают, что эксплуатация конструктивного элемента (например, корпуса реактора) безопасна, если
K1C K1С], (16.12)
где [K1С] — допускаемое значение вязкости разрушения K1C. Допускаемые значения K1C могут быть получены экспериментально.
Рассмотренные критерии работоспособности важны для сталей, используемых для изготовления корпусов реакторов и других сосудов давления, так как они относятся к классу хладноломких материалов. При достаточно низкой температуре, например, в процессе гидравлических испытаний корпуса (20–100 °С) и расхолаживания реактора опасность хрупкого разрушения возрастает, и оно должно быть предотвращено соответствующим выбором состава стали, обеспечивающим необходимое сочетание величин Тхр, aк, K1С.
Таким образом, с точки зрения надежности и работоспособности конструктивных элементов (и материалов) ЯЭУ среди механических характеристик материала важное значение имеют пределы прочности, текучести, ползучести, длительной прочности и выносливости, модуль нормальной упругости, относительные удлинение и сужение сечения, удельная работа разрушения и вязкость разрушения, а также критическая температура хрупкости материала. Значения этих характеристик материалов в общем случае должны отвечать комплексу оптимальных требований.
57
Материал при рабочей температуре должен иметь максимально достижимые значения следующих параметров: кратковременной прочности, пластичности, длительной прочности, нестационарной и неизотермической ползучести, обеспечивающие непревышение предельно допустимого значения деформации ползучести, сопротивления усталости (выносливости), в том числе неизотермической, мало- и многоцикловой, сопротивления термической усталости и других механических свойств.
Физико-химические свойства. Физико-химические свойства конструкционных материалов – это совокупность свойств, характе-
ризующих степень химического взаимодействия материалов с ок-
ружающей технической средой, например с теплоносителями (водой, газами, жидкими металлами, солями металлов и др.), с газами (остаточным или нарабатываемым газом), с контактирующими материалами. Практический интерес представляет совместимость материалов, т.е. степень химического взаимодействия конструкционного материала со всеми его окружающими материалами.
Материалы считают совместимыми в конкретных температур- но-временных условиях, если химическое взаимодействие между ними отсутствует или настолько мало, что не изменяет заметно состав, структуру и свойства конструкционного материала. Обычно задача обеспечения совместимости материалов является комплексной, так как зависит не только от вида материалов, но и от конструкторского решения тех или иных элементов (узлов) установки, их назначения и режимов работы. Например, материал оболочки твэла ВВЭР снаружи омывается смесью воды и пара, а изнутри контактирует с ядерным топливом и продуктами деления топлива. Материал корпуса рабочей камеры ТЯР с одной стороны контактирует с разряженной средой (остаточное давление водорода 10–8–10–1 Па) и плазмой, а с другой стороны омывается теплоносителем.
Особо внимательно необходимо изучать систему «металл– водород» с позиций поглощения водорода, его проницаемости и влияния на свойства металлов. Водород в металлах образует твердые растворы, химические соединения (гидриды), комплексы «де- фект–водород», сегрегации в микропустотах, и поэтому поглоще-
58
ние и захват водорода – это многофакторный процесс. Применительно к ТЯР большое значение с точки зрения получения вакуума и загрязнения плазмы «холодным» газом играет реэмиссия (рециклинг) водорода, определяемая десорбцией водорода под действием излучения плазмы, протекающей одновременно с захватом, диффузией и молекулярной рекомбинацией водорода, его отражением от стенки рабочей камеры.
По поглощению и захвату водорода металлы делятся на группы по степени растворимости и характеру изменения теплоты растворения: 1) металлы с экзотермической реакцией растворения, имеющие высокую растворимость при относительно низкой температуре (Ti, V, Zr, Nb и др.); 2) металлы с эндотермической реакцией растворения, имеющие низкую растворимость водорода, возрастающую с ростом температуры (Мо, Al, Ni, Cu и др.). Практически все металлы поглощают, а при облучении захватывают водород.
Процесс поглощения водорода определяется его адсорбцией на поверхности и диффузией в объеме металла, зависит от температуры и степени радиационного повреждения, дислокационной структуры и других структурных особенностей металлов. Механизмами, контролирующими выход водорода из металла, наряду с термодесорбцией, могут быть рекомбинация хемосорбированных молекул на поверхности, разрушение комплексов типа Н–V, Н2–V и др. (здесь V – вакансия).
Проницаемость водорода через конструкционные материалы зависит от его растворимости и коэффициента диффузии. Увеличению проницаемости способствуют механические напряжения в упругой и пластической областях деформирования, повышение чистоты поверхности, воздействие на материал плазмы тлеющего разряда и облучения, увеличение температуры материала, его СФС. Эффективным барьером для проницаемости водорода являются многослойные покрытия. С точки зрения требований к материалам ТЯР важно иметь минимальные значения водородопроницаемости (на уровне 10–15–10–13 м2с–1Па1/2), что позволит получать высокий вакуум за реальное время.
Высокие химическая активность и диффузионная подвижность изотопов водорода могут вызывать значительные изменения
59
свойств конструкционных материалов. В инженерной практике хорошо известно водородное охрупчивание металлов и сплавов, работающих длительное время в водородсодержащих средах. Представляет интерес анализ влияния водорода на охрупчивание конструкционных материалов при так называемой водородной коррозии. Водородная коррозия как результат химического взаимодействия водорода с материалами, особенно сталями, может привести к нежелательным явлениям: обезуглероживанию сталей в результате образования углеводородов (типа СН4) при температуре Т > 450–500 °С; разложению карбидов, нитридов, оксидов; пони-
жению энергии образования дефекта упаковки и поверхностной энергии, что приводит к увеличению плотности дефектов упаковки и объема пустот, резкому снижению пластичности и охрупчиванию материалов.
Взаимодействие водорода с карбидами, например, по реакции Fe3C + 2Н2 ЗFе + СН4 при Т 450 °С идет с образованием метана, накопление которого из-за большого молекулярного объема (по сравнению с атомарным объемом железа) происходит в микропустотах и является одной из причин обезуглероживания и охрупчивания, может быть причиной образования блистеров при облучении ионами водорода углеродсодержащих материалов.
Охрупчивание материалов существенно зависит от температуры и растворимости водорода: чем выше растворимость, тем больше охрупчивание при снижении температуры. Вследствие этого охрупчивание ферритных сталей в несколько раз меньше, чем аустенитных. Растворимость водорода и охрупчивание сталей уменьшаются при легировании алюминием, кремнием и марганцем. Положительно влияют на водородную коррозию стали металлы V, Ti, Мо, Сг, т.е. карбидообразующие элементы. В целом, водородное охрупчивание материалов зависит от внешних (среда, температура, напряжения, скорость и характер деформации) и внутренних (структура, состав, растворимость водорода, присутствующие примеси) факторов, определяется количеством водорода в материале.
Для предотвращения водородного охрупчивания накладывают определенные ограничения на концентрацию водорода в материалах (табл. 16.2).
60