
Калин Физическое материаловедение Том 5 2008
.pdf6. Методы финишного рафинирования собственно химических элементов, включающие: дистилляцию, зонную перекристаллизацию, многократную переплавку (например, дуговую, электроннолучевую, лазерную) в глубоком вакууме, выращивание монокристаллов.
Ниже будут рассмотрены важнейшие из этих методов, нашедшие широкое распространение в промышленности.
17.2.2. Жидкостная экстракция
Для разделения соединений и получения особо чистых веществ в крупномасштабных объемах одним из первых стал использоваться процесс жидкостной экстракции (от латинского extra-ctio – извлечение). Он основан на эффекте различия растворимости веществ в контактирующих фазах, объясняющемся неидеальностью реальных растворов. Исходной фазой обычно служит водный раствор минеральных солей. Извлекающими веществами (экстрагентами) являются какие-либо органические кислоты и/или основания. Например, в качестве органической фазы в промышленности широко используется раствор трибутилфосфата (ТБФ) в керосине.
Сущность экстракционного процесса состоит в том, что исходный водный раствор веществ А и В приводится в контакт с органической жидкостью – экстрагентом, и оба вещества по-разному перераспределяются между этими жидкими фазами. Процесс экстракции включает три последовательные стадии: смешение исходного раствора с экстрагентом; механическое разделение (расслаивание) двух образовавшихся фаз; удаление экстрагента и его регенерацию с целью повторного использования. После разделения получают раствор извлекаемого вещества в экстрагенте (экстракт) и остаток исходного раствора (рафинат). Выделение экстрагированного вещества из экстракта и одновременно регенерация экстрагента производится выпариванием, кристаллизацией, высаливанием и т. п. Достоинствами экстракции являются низкие рабочие температуры, возможность извлечения веществ из разбавленных растворов, способность эффективного разделения смесей близкокипящих компонентов и азеотропных смесей, простота аппаратуры. Недостатком экстракции является трудность в ряде случаев полного удаления экстрагента из экстрагированных веществ.
121
Экстракция оказалась весьма продуктивным процессом по разделению (очистке) для веществ, мало различающихся между собой по поведению в обоих растворах. Действенность жидкостной экстракции как средства для разделения металлов, близких по химическим свойствам, была открыта на примере разделения гафния и циркония. До 1923 г. гафний, который присутствует во всех естественных соединениях циркония, был совершенно не изученным элементом, поскольку обычные химические методы не давали возможности разделить эти два металла. Только после рентгеновских исследований, проведенных в 1923 г. и доказавших, что гафний действительно присутствует в цирконии, с трудом было осуществлено заметное их разделение фракционной кристаллизацией. А в 1947 г. определили, что растворы сульфата гафния могут быть эффективно отделены от сульфата циркония при применении эфира и воды в качестве несмешивающихся жидких фаз. Здесь исходный сульфат циркония, содержащий 2–3 % гафния, разделяется на водный раствор, содержащий менее 10–2 % гафния, и органический раствор гафния с единицами процентов циркония.
В настоящее время такие химически подобные элементы, как цирконий и гафний, ниобий и тантал, стронций и барий, редкоземельные элементы, их аналоги – скандий и иттрий, многие другие металлы, встречающиеся в рудах только совместно, разделяются с помощью жидкостной экстракции их соединений в промышленных масштабах.
Методы жидкостной экстракции, конечно, оказались очень полезны и для глубокой очистки веществ и металлов от примесей. В больших масштабах жидкостную экстракцию используют для очистки тория в виде нитрата, урана в виде раствора уранилнитрата.
В промышленности для повышения эффективности процесса экстракции две несмешивающиеся фазы приводят в контакт в экстракторах – устройствах, состоящих из серии дискретных (или непрерывных) экстракционных ступеней.
На рис. 17.2 схематически показаны наиболее распространненые типы вертикальных экстракторов. В них водный раствор (тяжелая фракция), содержащий интересующее нас растворенное вещество, поступает в экстрактор с одного конца устройства. Органическая фаза (легкая фракция – экстрагент), поступает с противоположного
122
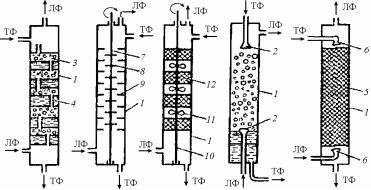
конца экстрактора и протекает в колонне в направлении, противоположном движению водной фазы.
а |
б |
в |
г |
д |
Рис. 17.2. Принципиальные схемы экстракционных колонн: |
||||
1 – колонна; 2, 6 – распылители; 3 –тарелка; 4 – переливная трубка; |
||||
5, 12 – насадка; 7, 10 – валы; 8 – плоский ротор; |
9 – кольцевые перегородки; |
11 – мешалки; ЛФ – легкаяфракция; ТФ – тяжелая фракция
Многоступенчатые экстракторы (рис. 17.2, а–в) обычно представляют собой вертикальные колонны, разделенные на ступени (секции) поперечными перфорированными тарелками, вращающимися дисками, мешалками и т. п. В каждой ступени происходит перемешивание взаимодействующих фаз и их расслаивание. Таким образом, в колонне исходный раствор и экстрагент многократно перемешиваются и расслаиваются.
Значительное распространение получили экстракторы ситчатые и с механическим перемешиванием. В ситчатых экстракторах (рис. 17.2, а) ступени разграничены перфорированными горизонтальными тарелками и сообщаются между собой переливными трубками. Одна из контактирующих жидкостей, проходя через отверстия тарелок, диспергируется, чем создается большая поверхность контакта с встречной жидкостью, протекающей по переливным трубкам в виде сплошной фазы.
Экстракторы с механическим перемешиванием делятся на ро- торно-дисковые (рис. 17.2, б) и с чередующимися смесительными и отстойными насадочными секциями (рис. 17.2, в). В роторнодисковых экстракторах вращающиеся диски перемешивают и дис-
123
пергируют жидкости, после чего они расслаиваются. В экстракторах со смесительными и насадочными секциями лопастные или турбинные мешалки размещены на общем вертикальном валу попеременно со слоями неподвижной насадки (кольца, спирали, пакеты сеток и пр.). Перемешанные жидкости, пройдя через слои насадки, расслаиваются.
Применяются также экстракторы с непрерывным контактом взаимодействующих фаз (распылительные, насадочные), не разделенные на отдельные ступени. Распылительные экстракторы (рис. 17.2, г) снабжены соплами, инжекторами и т. п. для диспергирования взаимодействующих жидкостей. Такие аппараты отличаются простотой и высокой производительностью, но сравнительно невысокой эффективностью. Более эффективны, но менее производительны насадочные экстракторы (рис. 17.2, д), наполненные насадкой в виде колец.
Ранее в качестве экстрагентов использовали только или органические кислоты, или основания раздельно. В настоящее время установлена высокая эффективность их нейтральных смесей, в которых образуются термодинамически устойчивые ионные пары из органических катионов и анионов металлов, распределяющиеся практически полностью в органическую фазу. В таких системах также существенно облегчается процесс реэкстракции, сокращается расход щелочей, минеральных кислот и комплексообразователей. Поскольку число бинарных сочетаний известных катионообменных и анионообменных экстрагентов велико, исследования в данном направлении являются весьма перспективными.
17.2.3. Дистилляционные методы
Экстракция основана на различном распределении компонентов смеси между двумя жидкими фазами; эффективность и глубина экстракции определяется различием в характеристиках неидеальности этих двух жидких растворов. Термодинамически более эффективными являются процессы очистки, основанные на различном распределении компонентов смеси между жидкой и паровой фазами. Здесь продуктивность разделения и очистки определяется величинами давления насыщенных паров компонентов, напрямую
124
связанных со значениями химических потенциалов самих индивидуальных веществ. Таким процессам можно дать название дистилляционных методов. Остановимся подробнее на важнейших схемах их технической реализации.
Собственно дистилляцией называется технологический процесс разделения компонентов жидкого раствора однократным его испарением с последующей конденсацией. Для твердых тел аналогом является сублимация – процесс разделения компонентов твердого вещества однократной возгонкой (испарением из твердой фазы).
Процесс однократной дистилляции или сублимации часто позволяет достигнуть хорошей очистки. При повторном проведении операции дистилляции результаты улучшаются, однако в таком виде этот процесс становится нетехнологичным и экономически неэффективным.
Разделение или очистка веществ через паровую фазу становятся более удобными в аппаратурном исполнении, если перегонку жидкостей проводить в форме непрерывного противоточного процесса, аналогично процессу экстракции. Процесс, в котором операции испарения и конденсации отдельных фракций многократно повторяются, носит название ректификации, а аппарат, в котором осуществляется процесс, называется ректификационной колонной.
При ректификации потоки пара и жидкости, перемещаясь в противоположных направлениях (противотоком), многократно контактируют друг с другом. Восходящие потоки пара непрерывно обогащаются более летучими компонентами, а стекающая жидкость – менее летучими. Для повышения степени очистки часть выходящей из аппарата жидкости возвращается обратно после конденсации. При затрате того же количества тепла, что и при дистилляции, ректификация позволяет достигнуть большего извлечения и обогащения.
Ректификация является одним из наиболее производительных и эффективных процессов глубокой очистки вобще, а не только среди дистилляционных методов. Она сравнительно несложна в аппаратурном оформлении, допускает непрерывное протекание процесса при практическом отсутствии потерь. Поэтому ректификация стала широко применяться в различных областях промышленности, в том числе при разделении изотопов и получения сверхчистых металлов и полупроводниковых материалов.
125
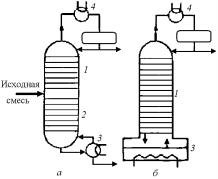
Ректификационные колонны (рис. 17.3) состоят из собственно колонны, где осуществляется противоточное контактирование пара и жидкости, и устройств, в которых происходит испарение жидкости и конденсация пара – соответственно куба и дефлегматора.
Рис. 17.3. Схемы потоков ректификационных колонн при непрерывной (а) и периодической (б) ректификации: 1 – укрепляющая секция;
2 – исчерпывающая секция;
3 – куб колонны; 4 – дефлегматор
Колонна представляет собой вертикально стоящий полый цилиндр, внутри которого или установлены так называемые тарелки (дискретные контактные устройства различных конструкций), или помещен дисперсный фигурный кусковой материал – насадка. Назначение тарелок и насадки – развитие межфазной поверхности и улучшение контакта между жидкостью и паром. Куб и дефлегматор – это обычно кожухотрубные теплообменники; находят применение также трубчатые печи и роторные испарители.
По способу проведения различают непрерывную и периодическую ректификацию. В первом случае разделяемая смесь непрерывно подается в среднюю часть ректификационнуой колонны, а из концов колонны непрерывно отводятся две фракции, обогащенные одним компонентом и обедненных другим. Схема потоков типичного аппарата для непрерывной ректификации показана на рис. 17.3, а. Колонна состоит из двух секций – укрепляющей и исчерпывающей. Исходная смесь подается в колонну, где стекает по контактным устройствам (тарелкам или насадке) исчерпывающей секции противотоком к поднимающемуся потоку пара.
Достигнув низа колонны, жидкостный поток, обогащенный тяжелолетучими компонентами, подается в куб колонны. Здесь жидкость частично испаряется, и пар снова поступает в исчерпывающую секцию. Выходящий из этой секции пар (так называемый от-
126
гонный) поступает в укрепляющую секцию. Пройдя ее, обогащенный легколетучими компонентами пар поступает в дефлегматор, где конденсируется хладагентом. Полученная здесь жидкость делится на два потока: дистиллят и флегму. Дистиллят является продуктовым потоком и выводится из колонны, а флегма возвращается в нее на орошение пара в укрепляющей секции. Отношение скорости орошения и скорости отбора продукта называется флегмовым числом. Чем выше флегмовое число, тем больше степень очистки, но меньше производительность.
При периодической ректификации (рис. 17.3, б) исходная жидкая смесь единовременно загружается в куб колонны, емкость которого соответствует желаемой производительности. Пары из куба поступают в колонну и поднимаются к дефлегматору, где происходит их конденсация. В начальный период весь конденсат возвращается в колонну, что отвечает так называемому режиму полного орошения. Затем конденсат делится на флегму и дистиллят. По мере отбора дистиллята (либо при постоянном флегмовом числе, либо с его изменением) из колонны выводятся сначала легколетучие компоненты, затем среднелетучие и т. д. Нужную фракцию (или фракции) отбирают в соответствующий сборник. Операция продолжается до полной переработки первоначально загруженной смеси.
Некоторые легкоплавкие элементы (например, ртуть, щелочные металлы, цинк, кадмий, йод, бром и др.) можно подвергать ректификационному разделению и очистке непосредственно. Однако в большинстве случаев этот процесс может быть осуществлен лишь с использованием летучих соединений нелетучих элементов; наиболее часто для этой цели применяют галогениды, карбонилы, гидриды или металлоорганические соединения. В настоящее время ректификация широко применяется в промышленности для очистки треххлористого мышьяка, тетрахлорида титана, тетрахлоридов германия и кремния, трихлорсилана, для разделения хлоридов циркония и гафния, а также для глубокой очистки металлоорганических соединений галлия, индия, алюминия, никеля, железа. Список можно продолжить практически неограниченно.
127
17.3.Получение сверхчистых металлов
17.3.1.Восстановление химических соединений
Высокочистые химические соединения находят свое самостоятельное применение в науке и промышленности. Однако наибольшее приложение на практике все же находят конструкционные материалы. Таковыми чаще всего являются сплавы металлов. Поэтому в технологии чистых веществ важнейшим направлением является получение свободных сверхчистых металлов, да и других элементов таблицы Д.И. Менделеева.
Любой метод получения элементарного металла из его соединения требует проведения некоторой химической реакции. Это может быть термическое разложение, электроосаждение или химическое восстановление. При термическом разложении летучего соединения оно разлагается с выделением свободного металла и другого газа. Этот метод дает хорошие результаты по чистоте, но не всегда экономически эффективен и экологически чист. Электроосаждение металла – результат электрохимической реакции между ионами металла и электронами, поступающими из нерасходуемого электрода. Метод нашел широчайшее распространение, но часто не обеспечивает сверхвысокую степень чистоты.
Химическое восстановление – процесс, в котором соединение металла реагирует с материалом (восстановителем) с образованием свободного металла и другого химического соединения. Метод очень широко применяется для получения сверхчистых металлов. Для обеспечения общей чистоты в ходе всего процесса необходимо использование высокочистых реагентов, защита получаемого металла от загрязнений, вносимых тиглем или реакционным сосудом. Эффективное использование химического восстановления при приготовлении высокочистых металлов требует, чтобы полученные в результате реакции металл и соединение находились в различных фазах.
При приготовлении металлов высокой чистоты наиболее часто в качестве восстановителей применяют водород, углерод, алюминий, натрий, магний, кальций, цинк, редкоземельные элементы.
128
Водород имеет много преимуществ перед другими восстановителями, так как легко доводится до очень высокой степени чистоты. Получаемый электролизом технический газ до глубокого уровня очищают, пропуская через нагретую до 400 °С мембрану из палладия.
Углерод высокой чистоты получают термическим разложением или неполным сжиганием предварительно очищенных газообразных углеводородов. Благодаря доступности углерод играет значительную роль в получении многих чистых металлов.
Такие металлы, как натрий, кальций и магний, могут быть получены электролизом расплавленных солей, а затем дополнительно глубоко очищены дистилляционными методами.
Так как практическое применение химических процессов восстановления очень обширно, то роль их на стадии приготовления высокочистых металлов будет иллюстрирована несколькими примерами.
Водородное восстановление. Из большого числа примеров восстановления различных соединений водородом можно привести промышленные процессы производства элементарных германия и кремния полупроводниковой чистоты.
Металлические германий и кремний приобретают свои полезные свойства, только находясь в состоянии высокой чистоты. Полупроводниковый германий получают восстановлением его твердого диоксида чистым водородом; до этого двуокись германия получается гидролизом дважды дистиллированной водой очищенного ректификацией тетрахлорида германия. Полученный таким путем металл не обладает максимальной чистотой, но он может быть дополнительно очищен зонной плавкой (см. п. 17.4).
Кремний был, есть и будет в обозримом будущем основным материалом микроэлектроники. Практически все интегральные микросхемы изготавливаются из эпитаксиальных структур на монокристаллических пластинах кремния. Пластины нарезают из монокристаллов кремния, выращиваемых в основном по методу Чохральского, или, для особо ответственных изделий или приборов специального назначения – методом бестигельной зонной плавки (БЗП). Описание методов выращивания крупных монокристаллов будет дано в п. 17.4.
129
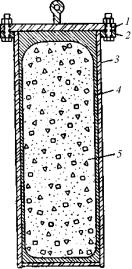
Исходным материалом для получения монокристаллов служит особо чистый поликристаллический кремний, который должен иметь плотную мелкокристаллическую структуру, без больших пор и с прочным сцеплением кристаллитов. Для БЗП исходным материалом служат круглые калиброванные стержни поликристаллического кремния с максимально гладкой поверхностью. Потребность мировой промышленности в поликристаллическом кремнии с указанными требованиями (а это десятки тысяч тонн в год), на 90% обеспечивает метод водородного восстановления трихлорсилана SiHCL3, предварительно глубоко очищаемого ректификацией.
Восстановление магнием и кальцием. Применимость как кальция,
так и магния для получения многих других металлов из их соединений была установлена много лет тому назад. Высокая реакционная способность этих металлов, высокая степень чистоты, с которой они могут быть получены, легкость обращения с этими металлами обусловили их применение при промышленном производстве большого числа редких металлов. Например, металлический уран высокой чистоты получают восстановлением его тетрафторида. Тетрафторид урана смешивают с гранулированным металлическим магнием и загружают в металлический цилиндр – химическую бомбу, футерованную изнутри огнеупорным материалом. Загрузку в бомбе также
накрывают слоем огнеупора, а саму бомбу закрывают металлической крышкой – фланцем, привинчивающимся болтами. Полностью собранная бомба схематически изображена на рис. 17.4.
Рис. 17.4. Поперечное сечение бомбы для магниетермического восстановления тетрафторида урана:
1 – крышка; 2 – фланец; 3 – стенка бомбы (стальная труба); 4 – огнеупорная футеровка; 5 – шихта (смесь UF4 и Mg)
130