
книги из ГПНТБ / Технология ремонта танков [учебник]
..pdfШейки валов проверяют на соосность путем определения вели чины биения. При проверке деталь укладывают на призмы, уста новленные на плите, или зажимают в центрах. После установки де тали к проверяемой поверхности подводят индикатор, укрепленный на штативе. Вращая вал, замечают величину суммарного отклоне ния стрелки индикатора за полный оборот вала. Эта величина ха рактеризует биение вала за счет прогиба и неравномерности изно са проверяемой поверхности. Если шейки вала имеют правильную
Рис. 35. Определение неперпендикулярности осей отвер стий
геометрическую форму, то величина биения будет равна удвоенно му прогибу вала.
Шатун двигателя В-2 может иметь остаточную деформацию в виде изгиба и скручивания. Поэтому при дефектовке шатуна про веряют непараллельность и скрещивание осей верхней и нижней головок, а также непараллельность и скрещивание осей нижней головки и отверстия под палец прицепного шатуна. Эти величины на длине 200 мм должны быть равны соответственно 0,15 и 0,25 мм. На рис. 36 приведена схема приспособления для проверки шатуна на параллельность и скрещивание осей.
В отверстия головок шатуна вводят разжимные оправки 1 и 2. После этого оправку, вставленную в нижнюю головку шатуна, укладывают на ножи 3. Стержень шатуна при этом должен опи раться на упор 5.
Непараллельность осей (изгиб шатуна) определяют по разно сти показаний индикатора 7, ножку которого поочередно подводят к концам оправки 1. Для определения величины скручивания ша туна пользуются индикатором 6, ножку которого подводят к кон цам той же оправки. Точно так же определяют положение оси под палец прицепного шатуна.
79
2 |
i |
Рис. 36. Приспособление для проверки шатуна на изгиб и скручивание:
1,2 — разжимные оправки; 3 — ножи; 4 — штифт; 5- — упор; 6Г 7 — индикаторы
I
80
о бн а р у ж е н и е т рещ и н и внутренних пороков в деталях
В практике ремонта для обнаружения трещин и других поро ков в деталях применяют следующие методы:
—гидравлического испытания;
—керосиновой пробы;
— красок; |
4 |
—люминесцентный;
—вихревых токов;
—намагничивания;
—ультразвуковой;
—просвечивания рентгеновскими и гамма-лучами.
Первые пять методов применяют только для обнаружения тре щин. Методы намагничивания, ультразвуковой и просвечивания гамма-лучами являются универсальными и позволяют обнаружить иа деталях не только трещины, но и внутренние пороки металла.
Ме т о д г и д р а в л и ч е с к о г о и с п ы т а н и я применяют при обнаружении трещин в полых деталях (баки, головки блока, радиаторы, трубопроводы и др.). При испытании полости деталей заполняют водой или дизельным топливом и создают в них давле ние в соответствии с техническими требованиями. О наличии тре щин судят по подтеканию жидкости. Трещины можно обнаружить также, заполнив полости деталей, погруженных в ванну с водой, сжатым воздухом. Выходящие из трещин пузырьки воздуха ука жут место нахождения дефектов.
М е т о д к е р о с и н о в о й п р о б ы состоит в следующем. Поверхность проверяемой детали смачивают керосином, после вы держки в одну-две минуты насухо протирают и покрывают мелом. Керосин, проникший в трещины, выступает на поверхность детали, четко определяя на меловом покрытии границы трещины. Этот метод очень прост, не требует специального оборудования и поэто му широко применяется. Однако при помощи такого метода невоз можно выявить мелкие трещины, шириной менее 0,03—0,05 мм.
М е т о д к р а с о к основан на способности красок к взаим ной диффузии. Для обнаружения трещины поверхность детали обезжиривают бензином и покрывают красной краской, которую через пять-десять минут смывают растворителем. После этого окра шивают деталь белой краской. Красная краска выступает из тре щины и окрашивает белое покрытие, четко обрисовывая границы трещины. Наша промышленность выпускает дефектбскопы ДМК-1, предназначенные для обнаружения трещин по методу красок. Ме тод красок позволяет обнаружить трещины шириной 0,01—0,03 мм и глубиной 0,01—0,04 мм.
Л ю м и н е с ц е н т н ы й м е т о д дефектоскопии основан на способности некоторых веществ излучать свет после воздействия на них ультрафиолетовых лучей.
6-1296 81
Для того, чтобы выявить трещины, на поверхность детали нано сят флуоресцирующее вещество — люминофор. После этого с дета ли удаляют излишки люминофора.
Люминофор, оставшийся в трещинах, в ультрафиолетовых лу чах будет ярко светиться. На рис. 37 приведена схема обнаружения трещин люминесцентным методом.
Рис. 37. Схема обнаружения трещин люминесцентным методом:
Контроль деталей на отсут ствие трещин производят при помощи специальных люмине сцентных дефектоскопов.
В качестве источника ульт рафиолетовых лучей в люмине сцентных дефектоскопах при меняют ртутно-кварцевые лам пы с дуговым разрядом. Лам па установлена в специальном кожухе, в который вмонтиро ван ультрафиолетовый свето фильтр из никелевого или морбалитового стекла.
В качестве люминофоров используют твердые или жидкие вещества. Из твердых лю-
1 — дет»ль; 2 — ультрафиолетовый светофильтр; |
МИНОФОПОВ |
Ч З Щ е ВСеГО |
ППИМе- |
3 — кожух лампы; 4 — ртутно-кварцевая лампа; |
|
и |
п р и т е |
5 - ультрафиолетовые лучи; 6 — дефект (тре- |
НЯЮТ ПОрОШКИ ОКИСИ |
МЭГНИЯ, |
|
шина)' |
углекислого |
магния |
или их |
|
смесь. При |
дефектовке |
детали |
протирают порошком люминофора. Порошок попадает в полость дефекта и после облучения ультрафиолетовым светом обнаружи вает его. ' ,
Наиболее распространены жидкие люминофоры, так как они легче проникают в полость дефекта. Хорошие результаты дает смесь из 15% трансформаторного масла и 85% керосина с добав кой 5% антраценового масла; она дает светло-голубое свечение.
Люминесцентный метод позволяет выявлять только дефекты, выходящие на поверхность деталей. Его применяют главным об разом для выявления трещин в деталях из немагнитных материа лов, так как для магнитных материалов предпочтительнее метод намагничивания, как более чувствительный. С помощью люмине сценции можно обнаружить трещины шириной более 0,01 мм и глубиной более 0,03 0,04 мм.
М е т о д в и х р е в ы х т о к о в применяют для обнаружения поверхностных и подповерхностных трещин, залегающих на глуби не до 0,3 мм или находящихся под слоем гальванических и других покрытий. Этот метод основан на том, что детали с поверхностны ми трещинами оказывают большее сопротивление вихревым то кам, чем детали без дефектов.
82
Для обнаружения трещин к поверхности проверяемой детали подносят датчик (рис. 38), представляющий собой индукционную катушку, которая является частью колебательного контура лам пового генератора токов высокой частоты. Высокочастотное маг нитное поле, созданное катушкой датчика, будет индуктировать в деталь вихревые токи.
Рис. 38. Датчик к |
прибору для обнаружения трещин |
методом вихревых токов: |
|
/ — защитный кожух; |
2 — корпус датчика; 3 —корпус катушки; |
|
4 —обмотка катушки |
Участок поверхности детали, содержащий трещины, имеет мень шую электропроводность, поэтому он будет вызывать меньшие по тери на вихревые токи. По величине этих потерь можно судить о наличии или отсутствии поверхностных трещин. В существующих дефектоскопах, работающих по методу вихревых токов, обычно оп ределяется не величина потерь на вихревые токи, а суммарная ве личина тока, протекающего через датчик, которая определяется как величиной напряжения генератора, так и магнитным полем, создаваемым вихревыми токами наведенными в детали.
Замеряя суммарную величину тока в катушке датчика, можно судить о величине потерь на вихревые токи, а следовательно, и о наличии поверхностных трещин. Величина тока в индукционной ка тушке после выпрямления его в детекторе (рис. 39) и усиления
И датчику
Рис. 39. Блок-схема прибора для обнаружения трещин методом вихревых токов:
Г — генерхтор; Д —детектор; У — усилитель; БП — блок питания; А —миллиамперметр
G* |
83 |
может быть замерена при помощи миллиамперметра. Стрелка мил лиамперметра обычно стоит на нуле, когда датчик поднесен к де тали без дефектов. При помещении датчика на деталь с поверх ностными трещинами, стрелка миллиамперметра отклонится от ну левого положения и, таким образом, покажет, что в детали имеют ся дефекты.
Метод вихревых токов позволяет обнаруживать трещины шири ной в 0,001 мм и глубиной в 0,1 мм.
М е т о д н а м а г н и ч и в а н и я . При проверке детали на от сутствие трещин методом магнитной дефектоскопии ее сначала на магничивают. Магнитные силовые линии, проходя через деталь и встречая на своем пути дефект, огибают его, как препятствие с малой магнитной проницаемостью, и образуют над ним поле рас сеяния (рис. 40). Чтобы обнаружить неоднородность магнитного
Рис. 40. Поле рассеяния магнитного потока около дефекта
поля, деталь поливают жидкостью, содержащей во взвешенном состоянии частицы магнитного порошка. Магнитный порошок будет втягиваться в поле рассеяния, образующееся около дефекта. Де фекты выявляются наиболее отчетливо в том случае, когда они располагаются перпендикулярно к направлению магнитных сило вых линий.
Метод магнитной дефектоскопии очень чувствительный и позво ляет выявлять треш.ины шириной до 0,001 мм, а также дефекты размером до 1 мм, расположенные под поверхностью детали на глубине до 15 мм.
При дефектовке деталей танков применяют следующие спосо бы намагничивания: циркулярное намагничивание, намагничива ние внешним полем и комбинированное намагничивание.
Циркулярное намагничивание применяется для выявления про дольных трещин. При этом переменный илщ постоянный ток боль шой силы (до 1000—4000 а) пропускают через деталь. На рис. 41 показана схема дефектоскопа циркулярного намагничивания пере менным током, предназначенного для деталей небольших разме ров.
Намагничивание внешним полем производится либо электро магнитом (рис. 42, а), либо соленоидом (рис. 42,6). Намагничи вание с использованием электромагнита применяют для выявле-
84 . •
8
Рис. 41. Схема дефектоскопа циркулярного намагничивания:
/ — медная плита; 2 —деталь; 3 —контактный диск; 4 —контактная головка; 5 — пусковая кнопка; 6 — кронштейн; 7 — понижающий трансформатор; 8 —маг нитный пускатель
|
й |
5 |
Рис. 42. Схема намагничивания внешним полем: |
||
а — электромагнитом; |
б — соленоидом; |
1 —выпрямитель (при намагничивании постоянным то |
ком); 2 —реостат; 3 |
— амперметр; 4 — электромагнит; 5 —деталь; 6 — амперметр; 7 —рео |
|
|
стат; |
8 —деталь; 9 —катушка |
85
ния поперечных трещин в деталях типа дисков, шестерен и т. п. Намагничивание соленоидом производится как переменным, так и постоянным током п применяется для обнаружения трещин в ва лах.
Комбинированное намагничивание применяют для обнаруже ния поперечных и продольных трещин. При этом создается вин товое магнитное поле. Оно получается от продольного постоянного поля электромагнита и циркулярного поля (рис. 43).
Рис. 43. Схема комбинированного намагничивания:
/ — электромагнит постоянного тока; 2—кон тактные пластины: 3 — деталь; 4 — пони жающий трансформатор
Ферромагнитный порошок для магнитной дефектоскопии полу чают путем восстановления железного сурика Fe203. Для этого су рик мелко размалывается, смешивается с керосином и загружается в тигель. Тигель замазывают глиной и помещают в печь, где про каливают при температуре 650—800СС. После такой обработки образуется магнетит Fe30 4 , который и используется для приготов ления суспензии. Суспензию приготавливают путем введения 50-у -т-100 г порошка на 1 л дизельного топлива.
После контроля детали размагничивают: при переменном токе путем постепенного вывода детали из соленоида, при постоянном
токе — путем чередования |
полярности с постепенным ослаблением |
||
магнитного поля. |
м е т о д |
обнаружения |
дефектов осно |
У л ь т р а з в у к о в о й |
|||
ван на способности ультразвука |
проходить через |
металлические |
изделия и отражаться от границы раздела двух сред, в том числе и от дефекта. В зависимости от способа приема сигнала от дефек
та различают два основных метода |
ультразвуковой |
дефектоско |
пии — метод просвечивания и импульсный метод. |
|
|
Метод просвечивания основан на появлении звуковой тени за |
||
дефектом. В этом случае излучатель |
ультразвуковых колебаний |
|
находится по одну сторону дефекта, |
а приемник — по другую, что |
|
не всегда удобно; поэтому наибольшее применение |
нашел метод |
86
ультразвуковой локации (импульсный). В этом случае нет необ ходимости иметь излучатель и приемник ультразвука. Вслед за посылкой импульса излучатель автоматически переключается в ре жим приема отраженных сигналов.
В качестве излучателей (приемников) ультразвуковых сигна лов используют пластинки из титаната бария (ВаТЮ3), у которо го пьезоэффект почти в 500 раз выше, чем у кварца.
На рис. 44 приведена схема импульсного ультразвукового де фектоскопа. При импульсном методе к детали подводят излуча тель (щуп). Если дефекта в детали нет, то ультразвуковой им пульс, отразившись от противоположной стороны детали, возвра’- тится обратно и возбудит электрический сигнал в приемнике; на экране электронно-лучевой трубки будут видны два всплеска: сле
ва — излученный импульс и справа — отраженный от противопо ложной стороны детали. Если в детали будет дефект, то ультра звуковой импульс отразится от дефекта и на экране трубки по явится промежуточный всплеск. Путем сопоставления расстояний между импульсами на экране электронно-лучевой трубки можно определить глубину залегания дефекта.
Ультразвуковой дефектоскоп обладает очень высокой чувстви тельностью и применяется для обнаружения внутренних дефектов
вметалле деталей. Внешний вид ультразвукового дефектоскопа
Рис. |
44. |
Схема |
импульсного ультразвукового дефектоскопа: |
|
1 — деталь; |
2 — излучатель (приемник) ультразвуковых сигналов; 3 — ге |
|||
нератор импульсов; |
4 — усилитель сигналов; |
5, 7 — отклоняющие пла |
||
стины; |
6 —излученный импульс; S — импульс, отраженный от дефекта; |
|||
р — донный импульс; |
10 — электронно-лучевая трубка; 11 — блок питания; |
|||
|
|
12 — развертывающее устройство; |
13 —дефект |
87
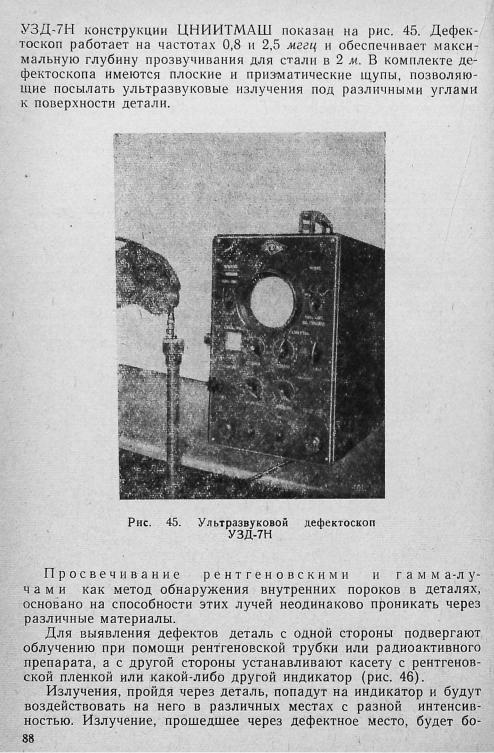