
monomers-Платэ-книга
.pdf
581
участвующие в процессе окисления. Повышение температуры окисления выше 363 К нецелесообразно из-за увеличения концентрации гидропероксида. По этой же причине нежелательно возрастание рН выше 10, так как при рН 6-10 количество гидропероксида в сыром гидропероксиде составляет ~ 12%, а при рН 11-12 достигает 20-25%.
Концентрирование гидропероксидов. Разложение гидропероксида в прин-
ципе можно проводить без концентрирования – в этом случае фенолы можно выделить ректификацией или экстракцией щелочью непосредственно из реакционной массы. Однако разложение гидропероксида в присутствии большого избытка непрореагировавшего углеводорода неизбежно приведет к образованию продуктов взаимодействия с углеводородом и, в конечном счете, к большим потерям гидропероксида и увеличению выхода побочных продуктов.
Концентрирование гидропероксида осуществляют либо удалением непрореагировавшего углеводорода дистилляцией в вакууме, либо путем химических превращений гидропероксида. Дистилляция в вакууме – наиболее простой способ концентрирования, который находит наиболее широкое применение в производстве фенола. Обычно используются двухили трехступенчатые схемы дистилляции. В первом случае отгон углеводорода производится в системе последовательно расположенных колонн, причем последняя из них работает при остаточном давлении ~49 Па. При дистилляции главная задача – поддерживать в системе температуру не выше 373 К, чтобы уменьшить разложение гидропероксида.
При работе с гидропероксидом как в лаборатории, так и на производстве следует учитывать высокую взрывоопасность пероксидных соединений, которая возникает в связи с возможностью автоускоряющегося разложения в результате нагрева, механических воздействий, детонации. Ряд пероксидов образуют взрывоопасные смеси. Например, пероксид бензола может взорваться при перекристаллизации из хлороформа. Известны примеры аварий, вызванные образованием пероксидных соединений в простых эфирах. Низшие представители гомологических рядов органических пероксидных соединений каждого типа наиболее взрывоопас-
ны. Кислотное разложение гидропероксидов. Кислотное разложение гидропе-
роксидов протекает по следующей схеме:
OOH |
O |
|
C(CH3)2 |
|||
|
C(CH3)2 |
|
|
C(CH3)2 |
|
|
|
|
|
|
|
||
|
Н+ |
|
O |
|||
|
|
|||||
|
|
|
|
|
|
|
|
|
|
|
|
|
-Н2О
В зависимости от природы гидропероксида получают фенол и различные оксосоединения. Так, арилизопропилгидропероксиды образуют при разложении фенолы и ацетон, фенил-втор-бутилгидропероксид – фенол и метилэтилкетон; толилэтилгидропероксид – крезолы и ацетальдегид.
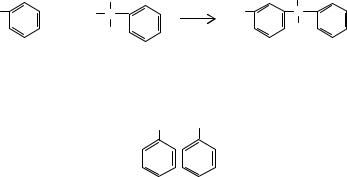
582
Выход фенолов в расчете на превращенный гидропероксид зависит от чистоты гидропероксида. При разложении гидропероксида 98-99%-й степени чистоты количественно образуются фенол и оксопроизводное. При концентрации гидропероксида 90-92% выход уменьшается до 94-97%, 87-88%-й гидропероксид дает 88- 90%-й выход фенола. При разложении технического гидропероксида, содержащего побочные продукты окисления, протекают побочные реакции, снижающие выход целевого продукта. Например, при взаимодействии фенола и диметилфенилкарбинола образуется кумилфенол:
|
|
CH3 |
|
CH3 |
HO |
+ |
HO C |
HO |
C |
|
|
CH3 |
||
|
|
CH3 |
-Н2О |
Диметилфенилкарбинол отщепляет воду с образованием -метилстирола, который, в свою очередь, может алкилировать фенол, а также полимеризоваться, и особенно димеризоваться, с образованием линейного димера
(CH3)2-C-CH=C-CH
Кроме этого, протекают реакции конденсации ацетона с образованием оксида мезитила, конденсации фенола и ацетона с образованием гидроксидифенилопропана, образование смолообразных продуктов.
Для разложения гидропероксидов применяют сильные кислоты. Слабые кислоты вызывают разложение гидропероксида только при длительном пребывании при 373-393 К и значительном расходе кислоты. В промышленности чаще применяют серную кислоту, но могут быть использованы также фенолдисульфокислота, алкилфенолсульфокислота и др.
При рассмотрении возможных вариантов технологической схемы разложения следует учитывать высокую экзотермичность этого процесса ( Н=309,6 кДж/моль гидропероксида).
Как правило, разложение гидропероксидов проводят в среде ацетона, при этом за счет его испарения отводится тепло реакции. Кислота в этом случае подается в виде раствора в ацетоне. Количество кислоты составляет 0,05-0,1% от реакционной массы, т. разл. ~ 348 К.
Общим недостатком всех технологических вариантов кислотного разложения гидропероксидов является необходимость нейтрализации реакционной массы и выведения из нее солей, чтобы исключить коррозию и выпадение осадков в ректификационной аппаратуре. При нейтрализации и промывке образуются сточные воды, содержащие фенол и соли.
Эти обстоятельства делают перспективным каталитическое разложение гидропероксида на твердых кислотах органического и неорганического происхожде-
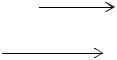
583
ния. В качестве твердых катализаторов могут использоваться сильные катиониты (смолы типа КУ-2), которые разлагают гидропероксиды при 323-333 К. Однако их недостатком является быстрое уменьшение каталитической активности при относительно длительной эксплуатации в результате окислительной деструкции.
Значительно более перспективно применение в качестве катализаторов твердых неорганических кислот. Они обладают высокой устойчивостью к действию окислителей. В качестве катализаторов могут быть использованы кислые природные глины (каолин, бентонит, мориллонит и др.), алюмосиликаты, кремнецирконевые катализаторы, цирконийфосфат.
Выделение фенола из продуктов разложения гидропероксида. Реакционная масса после разложения гидропероксида представляет сложную смесь фенола, ацетона, побочных продуктов превращения гидропероксида, смолистых веществ. Ректификация продуктов кислотного разложения кумилгидропероксида проводится в системе ректификационных колонн. Кроме ацетона и фенола выделяют - метилстирол, а фенольную смолу направляют на сжигание или переработку. Такая система очистки позволяет получить фенол высокой степени чистоты с выходом 97% от ресурсов в сырье.
Недостатки кумольного метода. Несмотря на прекрасно отлаженную технологию, кумольный метод имеет ряд недостатков. Прежде всего, это наличие взрывоопасного промежуточного соединения – гидропероксида кумила, а также многостадийность процесса. Так, при выходе целевого продукта 95% на каждой из трех стадий итоговый выход составляет лишь 86%.
Однако основным и принципиально неустранимым недостатком кумольного метода является образование в качестве побочного продукта ацетона. Это обстоятельство становится все более серьезной проблемой, поскольку ацетон не находит эквивалентного рынка сбыта. В 1990-х годах это стало особенно ощутимым после создания новых способов синтеза метилметакрилата путем окисления углеводородов С4, что резко сократило потребность в ацетоне.
В связи с проблемой утилизации ацетона в Японии разработана технология, предусматривающая его рецикл. С этой целью к традиционной кумольной схеме добавляют еще две стадии: гидрирование ацетона в изопропиловый спирт и дегидратация последнего в пропилена
O |
Ni |
OH |
||||
|
|
|
|
|
||
CH3—C—CH3 + H2 350K, 1,8 |
Па CH3—C—CH3 |
|||||
OH |
Al2O3 |
|
|
|||
|
|
|
|
|
||
CH3—C—CH3 |
CH3—C=CH2 + H2O. |
|||||
593K, 1,0 Па |
Образующийся пропилен снова возвращают на стадию алкилирования бен-
зола. В 1992 г. фирма "Мицуи" осуществила промышленную реализацию процесса

584
мощностью 200 тыс. т/год по этой пятистадийной кумольной технологии. В настоящее время ведутся интенсивные исследования, ориентированные на поиск новых путей синтеза фенола, которые основывались бы на прямом окислении бензола. Работы проводятся главным образом в следующих направлениях: окисление молекулярным кислородом, окисление моноатомными донорами кислорода и сопряженное окисление.
Окисление бензола
Окисление бензола молекулярным кислородом. Прямое окисление бен-
зола кислородом представляется наиболее привлекательным способом получения фенола:
OH
+ 0,5O2
Работы по окислению бензола кислородом начались еще до того, как в 1865 г. Кекуле предложил структурную формулу бензольного цикла. С тех пор многочисленные попытки найти эффективный путь для проведения этой реакции не прекращаются.
Наиболее успешные результаты получены при применении в качестве окислителей так называемых моноатомных доноров кислорода в виде различных кислородсодержащих молекул. Из таких молекул наибольшего внимания заслуживает пероксид водорода:
303-343 К |
|
|
|
|
|
OH |
|
|
|
|
|
|
|
+ H2O2 Комплексы металлов, |
|
|
|
|
|
+ Н2О. |
|
|
|
||||
Ti-силикаты |
|
|
Однако этот путь является мало перспективным из-за высокой стоимости пероксида водорода по сравнению со стоимостью фенола.
Более перспективным окислителем для бензола с практической точки зрения представляется азотная кислота, которая впервые была использована для этой цели в 1925 г. Эффективными катализаторами этой реакции являются оксидные системы на основе V2O5 и MoO3:
|
|
|
|
|
|
OH |
+ 2HNO3 |
|
|
|
|
|
+ 2NO2 + H2O. |
|
|
|
||||
|
|
|
|
|
|
|
Окисление протекает в газовой фазе в присутствии паров воды в при 600700 К. Степень конверсии бензола достигает 52% при селективности по фенолу
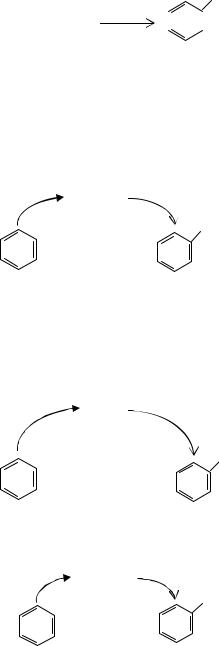
585
более 90%. Образующийся оксид азота (IV) может быть окислен до HNO3 и вновь применен для окисления бензола.
Представляет интерес способ окисления бензола сульфатом двухвалентной
меди в качестве окислителя:
OH
+ 2CuSO4 + H2O 573 K |
|
|
|
|
|
+ Cu2SO4 + H2SO4. |
|
|
|||||
|
|
|
Реакция протекает за счет восстановления Сu2+ в Cu+ или даже в Cu0. Интересным способом окисления бензола и других углеводородов является
использование пероксида водорода, образующегося в реакционной системе in situ. Применение пероксида по мере его образования из Н2 и О2 позволяет значительно увеличить селективность его использования. Это типичный пример сопряженного процесса:
H2 + O2 [H2O2]
H2O
OH
В данном случае первичной реакцией является окисление водорода в Н2О через промежуточное образование Н2О2, а вторичной – окисление бензола в фенол.
Помимо окисления водорода в качестве первичной реакции может выступать процесс окисления других молекул, например монооксида углерода:
CO + O2 [CO3]
CO2
OH
Сопряженный процесс может проводиться в сочетании с окислением вос-
становленной формы металла в растворах:
Mn + O2 [Mn+O2]
Mm+
OH
Реакция окисления бензола в фенол, вероятно, является рекордсменом по разнообразию подходов, количеству испытанных каталитических систем, а также по объему усилий, предпринимаемых исследователями для осуществления этой реакции.

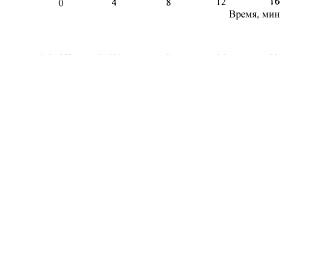
587
На рис. 15.4 приведена кинетическая кривая низкотемпературного разложения N2О в статической установке.
Рис. 15.4. Изменение парциального давления N2 (1), N2O (2) и O2 (3) при разложении оксида азота (I) на цеолите FeZSM-5 при 523 К
Видно, что протекание реакции сопровождается выделением в газовую фазу только N2, тогда как образующийся кислород заполняет каталитические центры и
остается полностью связанным на поверхности. До температуры 600 К -кислород термически устойчив. Выше этой температуры он необратимо десорбируется в газовую фазу и реакция разложения N2О приобретает характер обычного каталитического процесса.
Процесс получения фенола окислением бензола закисью азота (I) разработан совместно Институтом катализа Сибирского отделения Российской Академии Наук совместно c американской фирмой "Монсанто", которая принадлежит к числу крупнейших в мире производителей адипиновой кислоты (полупродукт для синтеза полиамида-6,6), что в значительной мере и определило ее первоначальный интерес к новому процессу получения фенола.
Схема получения адипиновой кислоты (cхема 15.3) включает следующие стадии: гидрирование бензола в циклогексан, окисление циклогексана кислородом воздуха в смесь циклогексанола и циклогексанона и, наконец, дальнейшее окисление этой смеси в адипиновую кислоту с помощью азотной кислоты. На последней стадии выделяется большое количество отходов оксида азота (I), который образуется (в мольном соотношении 1:1) одновременно с адипиновой кислотой. Поэтому идея использования таких отходов для окисления бензола в фенол как стадии в модифицированной схеме получения адипиновой кислоты является привлекательной.
Оксид азота (I) уже не рассматривается как безобидный "веселящий газ". Он обладает сильным парниковым эффектом, который (в расчете на г/моль) в 160 раз превосходит эффект СО2, главного "парникового газа". Кроме того, имея большое

588
время жизни, N2О достигает верхних слоев атмосферы, где способствует разрушению озонового слоя Земли.
Схема 15.3
|
|
OH |
O |
COOH |
|
|
3H2 |
O2 |
+ |
HNO |
+ N2O |
||
COOH |
||||||
|
|
|
||||
|
OH |
|
|
|
|
|
N2O |
|
2H2 |
|
|
|
П р и м е ч а н и е. Обычная схема – сплошные стрелки, модифицированная – штриховые.
В процессе получения фенола окислением бензола оксидом азота (I) используют железосодержащие цеолиты ZSM-5. Ниже приведены типичные технологические показатели процесса на пилотном заводе, построенном в г. Пенсакола
(США).
Т, К ……………………………………….. |
673-723 |
Время контакта, с …………………………………….. |
1-2 |
Степень превращения, % (мол.): |
|
бензола в фенол …………………………………... |
97-98 |
бензола в СО ……………………………………… |
0,2-0,3 |
бензола в двухатомные фенолы …………………. |
1 |
N2O в фенол ………………………………………. |
85 |
Производительность катализатора в расчете на фенол, |
0,4 |
кг/кг(кат.) ч ……….
Таким образом, вместо расходования средств на нейтрализацию оксида азота (I) в новом процессе его используют как ценное химическое сырье. По результатам пилотных испытаний фирмой принято решение о строительстве крупного промышленного завода мощностью 140 тыс. т фенола/год.
15.1.2. Получение бромфенолов и их производных – антипиренов
Несмотря на успехи, достигнутые в создании трудносгораемых пластиков, проблема пожароопасности полимерных материалов остается актуальной. Удельный вес галогенсодержащих соединений в общем объеме потребляемых в мире антипиренов довольно высок и непрерывно возрастает. Около трети производимого брома используется для производства огнестойких материалов и антипиренов. Практическое значение нашли одно- и двухатомные фенолы с различной степенью
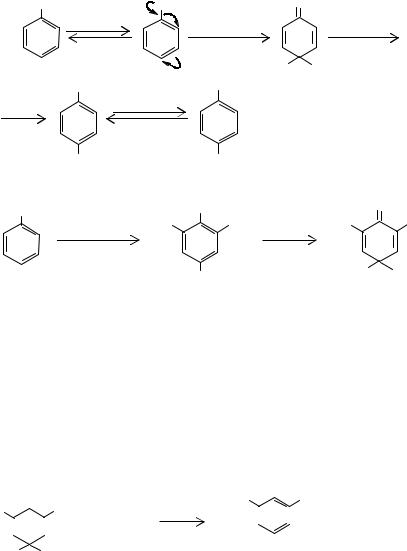
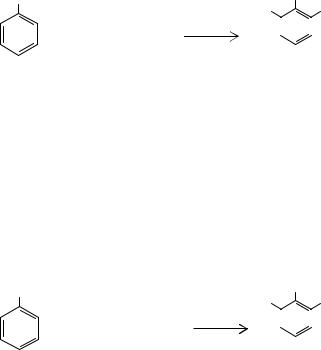
590
OH |
Br |
OH |
|
Br |
+ 1,5Br2 + 1,5Cl2 |
|
|
|
|
+ 3HCl . |
|
|
||||
|
|
|
|
||
|
|
Br |
Основным бромирующим средством в промышленности является молекулярный бром или молекулярный бром в смеси с молекулярным хлором. Хлор вводят потому, что бром - дефицитное сырье. В отсутствие хлора улавливание выделяющегося HBr и его утилизация в виде бромоводородной кислоты не решают проблемы, так как потребность в этой кислоте не велика. Эффективным решением данной задачи является применение окислителей для перевода бромида водорода в бром. В качестве окислителя в процессах бромирования фенолов обычно используют пероксид водорода.
2,4,6–Трибромфенол может быть получен таким образом:
OH |
Br |
OH |
|
Br |
+ 1,5Br2 + 1,5H2O2 |
|
|
|
|
+ 3H2O . |
|
|
||||
|
|
|
|
||
|
|
Br |
Выход целевого продукта достигает 85% при селективности ~ 90%.
15.2. МОНОМЕРЫ ДЛЯ КАРБАМИДО-АЛЬДЕГИДНЫХ ПОЛИМЕРОВ
Карбамидо-альдегидные полимеры (мочевино-формальдегидные олигомеры, смолы) - синтетические термореактивные продукты поликонденсации карбамида с формальдегидом. Эти полимеры бразуются в результате поликонденсации первичных продуктов присоединения карбамида и формальдегида – метилкарбамидов Н2NCОNНСН2ОН и СО(NНСН2ОН)2 - друг с другом, карбамидом и формальдегидом и содержат повторяющуюся группу —NH—С(О)—NH—.
Карбамидо-формальдегидные полимеры - смесь олигомеров различной молекулярной массы линейного, разветвленного или циклоцепного строения, содержащих реакционноспособные NH2- и ОН-группы. Получают и применяют карбамидо-формальдегидные олигомеры в виде водных растворов (преимущественно 40-70%-х) и порошков. Твердые сетчатые олигомеры бесцветны, светостойки, устойчивы в органических растворителях и маслах, легко окрашиваются. Однако они характеризуются пониженной водостойкостью, хрупкостью, низкой устойчивостью к деструктивным воздействиям, выделением свободного формальде-