
ТРАНСПОРТНО-ГРУЗОВЫЕ КОМПЛЕКСЫ. МЕХАНИЗАЦИЯ СКЛАДСКИХ РАБОТ С НАСЫПНЫМИ ГРУЗАМИ
.pdf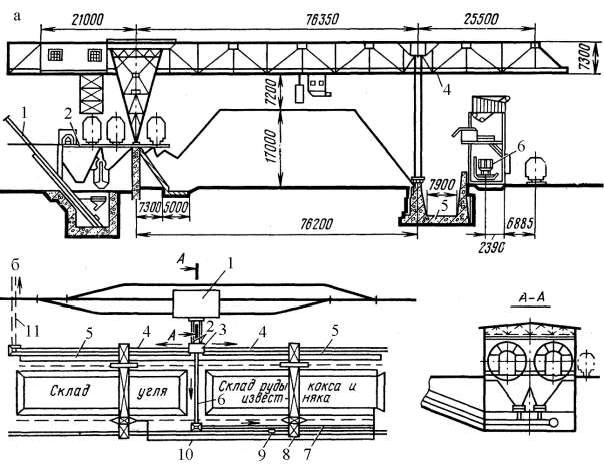
ми конвейерно-грейферными мостами 1 с приводными тележками и шаровыми опорами 5. На мосту расположены конвейеры 2, 4 и грейфер 3 вместимостью 5,3 м3. Подача угля на склад осуществляется конвейерами 7, 6, 4 и 2. Зависание и налипание угля в приемной воронке аккумулятора предотвращаются системой импульсного пневмооборудования (стреляющие сопла).
Руда и уголь в большом количестве поступают на теплоцентрали, обогатительные фабрики, металлургические заводы, где создаются технологические запасы. Для выгрузки угля и руды широко используются вагоноопрокидыватели. На рис. 2.29, а показан склад на рудном дворе металлургического завода.
Рис. 2.29. Склады угля и руды с использованием вагоноопрокидывателей: а – с башенным вагоноопрокидывателем: 1 – скиповый подъемник;
2 – доменная эстакада; 3 – штабель; 4 – кран; 5 – траншея; 6 – передвижные башенные вагоноопрокидыватели; б – со стационарными роторами:
1 – роторный вагоноопрокидыватель; 2, 4, 6, 7 – конвейеры; 3 – распределительное устройство; 5 – приемная траншея; 8 – кран;
9 – электровагон; 10 – бункер; 11 – конвейер топливоподачи
50
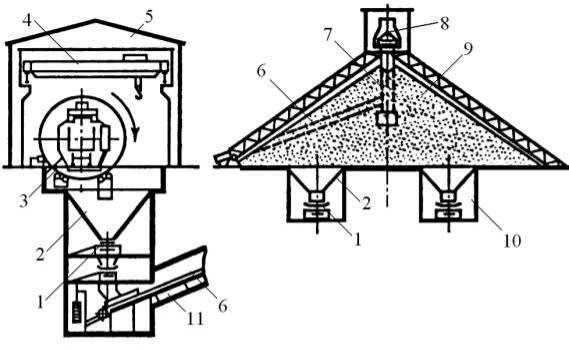
Выгрузка производится на башенном вагоноопрокидывателе в приемную траншею, расположенную вдоль склада. Штабелируется груз из траншеи двухконсольным мостовым перегружателем в доменную печь скиповым подъемником. Также для выгрузки используют роторные вагоноопрокидыватели. На рис. 2.29, б и рис. 2.30 показаны схемы использования стационарного роторного вагоноопрокидывателя в сочетании с ленточными конвейерами на эстакаде для приема и в тоннелях для выдачи со склада.
Рис. 2.30. Склад угля с использованием роторных вагоноопрокидывателей в сочетании с хребтовыми складами: 1, 6, 7 – конвейеры; 2 – приемный бункер; 3 – роторный вагоноопрокидыватель; 4 – мостовой кран;
5 – здание приемного устройства; 8 – разгрузочная сбрасывающая тележка; 9 – штабель; 10 – подштабельная галерея; 11 – конвейерная галерея
В местах выгрузки сыпучих грузов рациональным считается применение конвейерных погрузочно-разгрузочных машин (рекляймеров). Рекляймер – самоходная погрузочная машина на рельсовом или гусеничном ходу, у которой имеется ленточный штабелирующий конвейер, позволяющий отсыпать штабель значительной высоты (до 12 м) уступами (3, 6, 9, 12 м). При необходимости с помощью роторно-ковшового питателя, расположенного на хоботе конвейера, рекляймер может забирать материал из
51

штабеля и подавать на транспортные конвейеры (рис. 2.31). Производительность рекляймеров 0,2…10 тыс. т/ч.
Рис. 2.31. Склад, оборудованный реклеймерами: а – схема приема-выдачи груза со склада: 1 – рекляймер; 2, 4 – штабеля груза; 3 – тележка; 5 – конвейер; б – схема формирования штабеля роторно-ковшовой
машиной, работающей в автоматическом режиме: 1, 2, 3, 4, 5 – порядок штабелирования в автоматическом режиме рекляймера
Склад (рис. 2.31, а) оборудован комбинированной машиной (рекляймером), объединяющей функции штабелера и перегружателя. Она имеет
52
специальную прицепную разгрузочную тележку, которая во время экскаваторного хода движется по рельсам вместе с машиной. В поперечном направлении машина может быть подана к любому штабелю. Эта схема обеспечивает сквозное транспортирование материала через склад даже при работе перегружателя. На рис. 2.31, б показано формирование штабеля угля роторно-ковшовой машиной, работающей в автоматическом режиме. Штабель формируется уступами 3, 6, 9 и 12 м.
Уголь и руда, добытые на шахтах, в рудниках или открытым способом на разрезах, загружают непосредственно в саморазгружающиеся полувагоны или с предварительным накоплением хранят в бункерах, полубункерах или в специальных складах.
Основными способами погрузки угля являются: бункерный (более чем на 500 пунктах); на 130 пунктах – безбункерный, т.е. непосредственно в вагоны и на около 80 пунктах – комбинированный. Современная технология погрузки угля и руды должна предусматривать непрерывный прием угля с шахты, обогатительной фабрики, руды из рудника при смене на пункте погрузки вагонов; возможность загрузки полувагонов различной грузоподъемности при любых возможных их сочетаниях в составе; полное использование подвижного состава по грузоподъемности и вместимости. На погрузочных путях шахт загружают как целые маршрутные составы, так и части маршрутов или группы отдельных полувагонов.
Бункерная погрузка угля в вагоны с одновременным взвешиванием и устройство поверхности шахты показаны на рис. 2.32.
Уголь из шахты 1 в секции бункеров 2 подается загрузочным распределительным конвейером 3. Из бункеров питателями 5 уголь подается в подбункерный ленточный конвейер 4, с которого поступает на погрузочную стрелу 8 и далее в полувагон, взвешиваемый на вагонных весах 9. На бункерной установке показан породоотборочный элеватор 6 и породоразделочная машина 7. Производительность такой установки 600 т/ч и более. Высоту падения угля в полувагоны измеряют подъемом и опусканием погрузочной стрелы, а подвижной состав при погрузке передвигают маневровой лебедкой или вагонотолкателем.
Для погрузки угля открытым потоком в периодически перемещаемые вагоны используют специальные углепогрузочные комплексы (КПУ) (рис. 2.33…2.35).
53
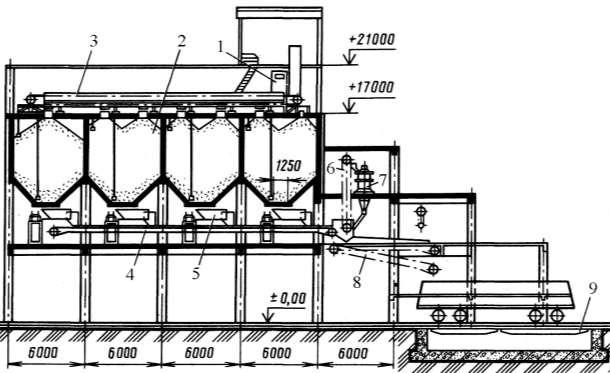
Рис. 2.32. Бункерная погрузка угля с предварительным накоплением: 1 – шахта; 2 – секция бункера; 3 – загрузочный распределительный конвейер; 4 – подбункерный ленточный конвейер; 5 – питатель;
6 – породоотборочный элеватор; 7 – породоразделочная машина; 8 – погрузочная стрела; 9 – вагонные весы
На шахте «Первомайская» производственного объединения «Кузбассуголь» организована погрузка угля (рис. 2.33) производительностью 600 т/ч непосредственно из скипов через приемные бункера 1, питатели 2, дробилки 3, ленточный конвейер 5. Поток угля с погрузочного конвейера 15 направляется двухрукавным поворотным желобом 16 в загружаемый вагон 14 или переключается в следующий вагон 17. При отсутствии порожних вагонов перекидной шибер 6 отклоняет поток на конвейер 7 для укладки в конусный штабель 8. Для подачи со склада используют питатели 9 и систему конвейеров 10 и 11, загружающих погрузочный конвейер 15. Для учета количества угля на конвейерах 5 и 7 установлены конвейерные весы 4 типа ЛТМ-1. Более точно определяют массу брутто груженого вагона вагонные весы 13. Передвижение вагонов обеспечивает маневровое устройство 12.
54
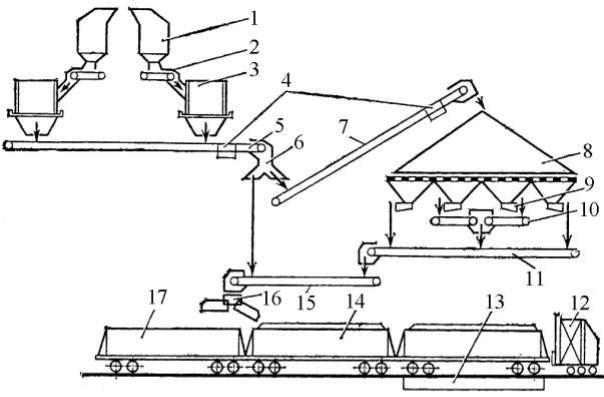
Рис. 2.33. Схема комплекса погрузки груза открытым потоком в периодически перемещаемый вагон: 1 – приемные бункера; 2, 9 – питатели; 3 – дробилки; 4 – конвейерные весы; 5, 7, 10, 11 – ленточные конвейеры;
6 – перекидной шибер; 8 – конусный штабель; 12 – маневровое устройство; 13 – вагонные весы; 14 – загружаемый вагон; 15 – погрузочный конвейер; 16 – двухрукавный поворотный желоб; 17 – следующий вагон
На разрезе «Холбоджинский» производственного объединения «Востсибуголь» применяют КПУ П-ЗМ, отгружающий уголь открытым потоком в непрерывно перемещаемые вагоны при периодическом движении погрузочного устройства (рис. 2.34). Уголь из штабеля 2 конвейером 1 подается в бункер 7. Два выпускных отверстия бункера с качающимися питателями 6 выдают уголь в поворотный погрузочный желоб 5. Состав вагонов непрерывно перемещается электротягачом 3. Когда порожний вагон 4 подходит к точке погрузки, желоб повернут ему навстречу. Включаются оба питателя 6, поток угля загружает начальный объем. По мере движения вагона поворачивается погрузочный желоб 5, причем скорость его задней грани совпадает со скоростью вагона. Таким образом, точка погрузки, перемещаясь, остается неподвижной относительно вагона, что обеспечивает заполнение его начального объема при производительности
55
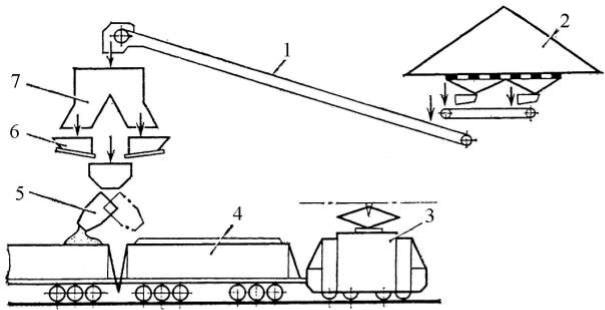
подачи угля 2000 т/ч. Необходимость согласования трех параметров – скорости движения вагона, производительности подачи угля питателями и угловой частоты поворота погрузочного желоба усложняет систему управления и затрудняет работу оператора.
Рис. 2.34. Схема углепогрузочного комплекса П-3М:
1 – конвейер; 2 – штабель; 3 – электротягач; 4 – порожний вагон; 5 – поворотный погрузочный желоб; 6 – питатели; 7 – бункер
Сочетание углепогрузочного комплекса П-4М с весовым дозированием подаваемого угля предусматривает погрузочный комплекс П-4В, внедренный на разрезах «Нерюнгринский» производственного объединения «Якутуголь» и «Сибирчинский» объединения «Кемеровоуголь» (рис. 2.35). Питатели 2 подают уголь из приемного штабеля 1 на наклонный конвейер 3 к распределительному устройству 4, которое поочередно направляет его поток в один из двух дозировочных бункеров 6, установленных на весах 7. Дозировочный бункер заполняется вначале на полном потоке (4000 т/ч), а затем на сниженном до 1000 т/ч. Это обеспечивает точность набора порций с отклонением, не превышающим 1 %. В это время 3/4 потока направляется во второй дозировочный бункер. Приготовленная порция груза через затворы 8 выгружается в накопительный бункер 10, который также установлен на весах 11 для контроля.
56
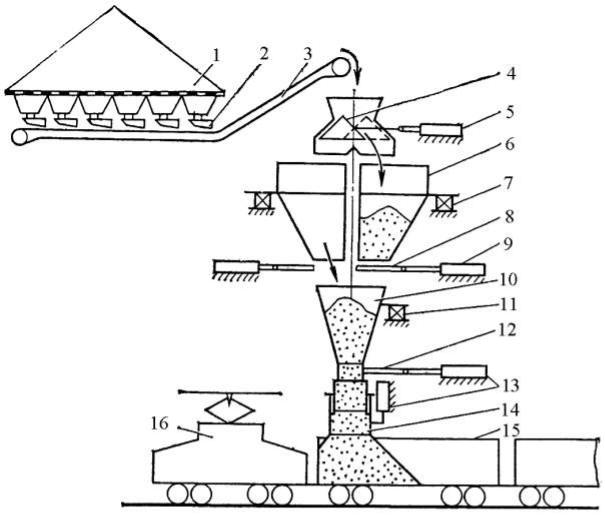
Рис. 2.35. Технологическая схема углепогрузочного комплекса П-4В:
1 – штабель; 2 – питатели; 3 – наклонный конвейер; 4 – распределительное устройство; 5, 9, 13 – гидроприводы; 6 – дозировочные бункера; 7 – весы дозировочные; 8, 12 – затворы; 10 – накопительный бункер; 11 – весы контрольные; 14 – телескопический желоб; 15 – вагон; 16 – электротягач
Вагоны непрерывно передвигаются электротягачом 16, скорость которого регулирует дистанционно с пульта управления оператор или автоматика в зависимости от параметров процесса погрузки. При подаче под погрузку очередного вагона 15 выдвижной телескопический желоб 14 устанавливают на высоту, определяемую типом загружаемого вагона, после чего открывается затвор 12 и порция груза с подпором загружается в непрерывно перемещаемый вагон. Гидроприводы 5, 9, 13 обеспечивают достаточную быстроту срабатывания затворов и опускание – подъем желоба, что необходимо для обеспечения точного дозирования и качественного заполнения вагонов. При отсутствии дозирующих емкостей стабильность
57
работы этого комплекса обеспечивается использованием ЭВМ, реализующей несложный алгоритм управления.
Безбункерная погрузка вагонов производится при использовании роторных и многоковшовых экскаваторов.
Роторные экскаваторы используются в карьерах для добычи и погрузки угля, рудных и нерудных ископаемых из уступов, расположенных как выше, так и ниже уровня установки механизмов. Ход – гусеничный или рельсошагающий. Накоплен опыт применения роторных экскаваторов при транспортно-отвальной системе и с непосредственной погрузкой в железнодорожные вагоны.
Цепные многоковшовые (многочерпаковые) экскаваторы характеризуют высокая производительность (до 15 млн. м3 в год) и чистота выемки забоя. Передвигаются они по рельсовой колее или на гусеницах. Недостаток этих машин в большом износе деталей черпаковой цепи и расходе электроэнергии.
Как правило, железнодорожные полувагоны при использовании отвальных конвейеров экскаваторов загружают непосредственно с ленты. На разгрузочном конце конвейеры оборудованы воронками с затворами или клапанами для перекрытия потока в момент прохода межвагонного промежутка.
Также для карьерных, шахтных, погрузочно-разгрузочных работ, складских операций с насыпными грузами используют карьерные экскаваторы, оснащенные основными ковшами прямой и обратной лопаты емкостью 2 до 15 м3.
2.4Разгрузочные фронты для смерзающихся грузов
2.4.1Особенности перевозки
иразгрузки смерзающихся насыпных грузов
Ксмерзающимся относятся перевозимые насыпью грузы, которые при температурах наружного воздуха ниже 0 °С теряют свои обычные свойства сыпучести вследствие смерзания частиц груза между собой и примерзания их к полу и стенкам кузова вагона. Краткий перечень смерзающихся грузов следующий:
– агломерат (влажный);
58
–балласт;
–барит (кусковой);
–бокситы;
–глина (каолиновая, огнеупорная, простая);
–гравий;
–известняк (мытый);
–камень (гипсовый, известняковый, строительный);
–кокс;
–клинкер (цинковый, цементный);
–колчеданы (железные, медный и серные);
–концентрат вермикулитовый;
–мелочь коксовая (размером частиц до 10 мм);
–мергели;
–мука (доломитовая) известняковая;
–огарки пиритные;
–песок (кварцевый, строительный, формовочный);
–руда (железная, марганцевая, медная, никелевая, свинцовая, цинковая);
–сланцы горючие;
–соль (каменная, техническая);
–уголь (бурый и каменный);
–флюсы;
–шлаки гранулированные;
–щебень мытый.
Правила перевозок грузов железнодорожным транспортом предусматривают, что до предъявления к перевозке грузов, подверженных смерзанию, грузоотправитель должен принять меры к уменьшению их влажности до безопасных в отношении смерзания пределов, установленных ГОСТами и техническими условиями на продукцию.
Для каждого насыпного груза существует нижний предел влажности, зависящий от строения материала, его химического состава и других свойств, определяющих влагоемкость, при котором его частицы не смерзаются даже при самых низких температурах наружного воздуха. Эта влажность называется безопасной (табл. 2.4).
59