
681
.pdf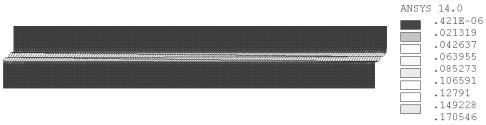
Рис. 5. Полные деформации по Мизесу при перемещениях 0,1911 мм, полученных при использовании модели разрушения PDMG
3. Испытание пластины с отверстием в центре на сжатие
Эксперимент на сжатие тонкой композитной пластины был проведен H. Suemasu [8]. Образец был изготовлен из материала T800/#8633, свойства которого приведены в табл. 3. Испытываемый образец имеет 16 слоев по толщине с толщиной одного слоя 0,13081 мм. Схема укладки слоев [(45/0/-45/90)2]s. Ориентация «0» соответствует расположению волокон углепластика вдоль длинной стороны образца. Длина образца составляет 118 мм, ширина 38,1 мм, диаметр отверстия 6,35 мм (рис. 6). На рис. 7 показана оснастка, использованная для проведения испытаний. В расчетах образцу были запрещены перемещения по нормали к одной из коротких сторон и к двум длинным сторонам. Перемещения прикладывались к противоположной короткой стороне по оси X. Также были запрещены перемещения по нормали к нижней грани. Были построены две конечно-элементные модели с различным числом и типом элементов. Для построения конечно-элементной модели с более грубой сеткой, где задается один элемент по толщине, были использованы элементы 2-го порядка с возможностью задания схемы армирования SOLID186. Для построения конечно-элементной модели с более точной сеткой, где задается 20 элементов по толщине, были использованы элементы 1-го порядка с возможностью задания схемы армирования SOLID185. Перемещения были приложены с шагом 0,001 мм до полного разрушения образца. Модель разрушения PDMG использовалась с сеткой в один и 16 элементов по толщине.
231
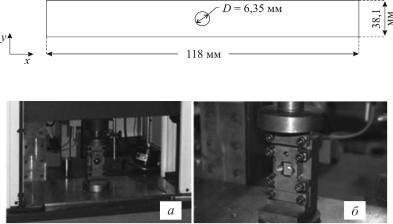
Свойства Т800/#8633 |
|
Таблица 3 |
|
|
|
||
|
|
|
|
Свойства материала |
|
Значение |
|
Продольный модуль Юнга |
E1 |
140 000 МПа |
|
Поперечный модуль Юнга |
E2, E3 |
9560 МПа |
|
Коэффициет Пуассона |
ν12, ν13 |
0,3 |
|
ν23 |
0,49 |
||
|
|||
Модуль сдвига |
G12, G13 |
4550 МПа |
|
G23 |
3170 МПа |
||
|
|||
Предел прочности на растяжение вдоль основы |
Xt |
2000 МПа |
|
Предел прочности на сжатие вдоль основы |
Xc |
1500 МПа |
|
Предел прочности на растяжение поперек основы |
Yt, Zt |
50 МПа |
|
Предел прочности на сжатие поперек основы |
Yc, Zc |
150 МПа |
|
Предел прочности на сдвиг |
S12, S13, S23 |
100 МПа |
Рис. 6. Геометрические размеры образца
Рис. 7. Аппаратура для испытания (а), закрепление образца (б)
Суммарная сила реакции измерялась на стороне, к которой прикладывались перемещения. На рис. 8 представлены графики зависимости силы реакции F (Н) от перемещений U (мм). Погрешность по максимальной нагрузке численного эксперимента с уточненной сеткой при использовании макроса FAIL_MOD относительно натурного эксперимента составила 12,04 %. Погрешность по максимальной нагрузке относительно натурного эксперимента для модели разрушения PDMG составила 26,33 %. Как видно из графиков, жесткости натурного эксперимента и численного решения не совпадают; это связано с тем, что в численном решении не учтена жесткость испытательной машины. Падение силы реакции происходит практически мгновенно, но кривая,
232
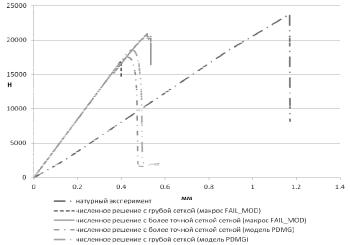
полученная с помощью модели разрушения PDMG, имеет более гладкий вид; это связано с тем, что модель разрушения PDMG по сравнению с макросом FAIL_MOD более чувствительна к шагу прикладываемых нагрузок. Также видно, что предельная нагрузка с сеткой в один элемент по толщине существенно ниже, чем предельная нагрузка с сеткой в 20 элементов по толщине, при использовании макроса FAIL_MOD. Последнюю предельную нагрузку следует считать более точной. На рис. 9 представлена конечно-элементная модель с разрушенными элементами при использовании макроса FAIL_MOD при перемещении 0,508 мм. Сравнение с рис. 13 показывает, что характер разрушения совпадает с натурным экспериментом. На рис. 10 показан характер распределения напряжений вдоль основы при перемещениях 0,418 мм, полученных при использовании макроса FAIL_MOD для модели с грубой сеткой. Видно, что в углах элементов, находящихся рядом с последними из разрушенных элементов, возникает концентрация напряжений. Фронт разрушения продолжает идти в сторону, где наблюдалась наибольшая концентрация напряжений. На рис. 11 показаны полные деформации по Мизесу при перемещениях 0,527 мм, полученных при использовании макроса FAIL_MOD для более точной сетки. На рис. 12 показаны полные деформации по Мизесу при перемещениях 0,48 мм, полученных при использовании модели разрушения PDMG. Как видно из рис. 11, 12, наибольшие полные деформации имеют разрушенные элементы.
Рис. 8. График зависимости силы реакции (F, Н)
от перемещений (U, мм)
233

а |
б |
Рис. 9. Конечно-элементная модель с разрушенными элементами в начальном моменте разрушения (а) и при перемещении 0,527 мм (б) (уточненная сетка). Нагрузка прикладывалась вертикально. Разрушенные элементы показаны более темным цветом
Рис. 10. Характер распределения напряжений вдоль основы приперемещениях 0,418 мм, полученныхмакросом FAIL_MOD
Рис. 11. Полные деформации по Мизесу при перемещениях 0,527 мм, полученных при использовании макроса FAIL_MOD
Рис. 12. Полные деформации по Мизесу при перемещениях 0,48 мм, полученных при использовании модели разрушения PDMG
234

а |
б |
Рис. 13. С-Scan перед началом полного разрушения (а); увеличенный снимок при нагрузке 22,7 кН (штрих пунктиром отмечен отслоившийся слой) (б). Нагрузка прикладывалась вертикально
4. Испытание пластины с отверстием в центре на растяжение
Эксперимент на растяжение тонкой композитной пластины был проведен F.K. Chang и K.Y. Chang [9] и S.C. Tan [10]. Свойства мате-
риала приведены в табл. 4. Испытываемый образец имеет 20 слоев по толщине с толщиной одного слоя 0,13081 мм. Схема укладки слоев [0/(+-45)3/(90)3]s. Ориентация «0» соответствует расположению волокон углепластика вдоль длинной стороны образца. Длина образца составляет 203,2 мм, ширина 25,4 мм, диаметр отверстия 6,35 мм (рис. 14). Образцу были запрещены все перемещения по одной из коротких сторон, на противоположной короткой стороне были запрещены перемещения по другим осям и прикладывались перемещения по оси Y. Для построения конечно-элементной модели использовались элементы 1-го порядка с возможностью задания схемы армирования SOLID185. Число элементов по толщине пластины совпадает с числом слоев. Перемещения были приложены с шагом 0,001 мм до полного разрушения образца. Число элементов по толщине пластины при использовании модели разрушения PDMG совпадает с числом слоев.
Рис. 14. Геометрические размеры образца
235
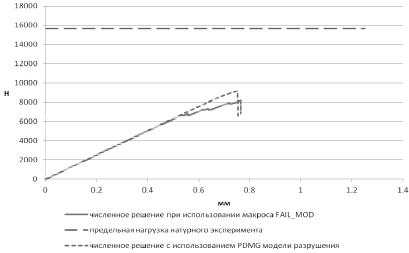
Свойства Т300/1034-С |
Таблица 4 |
||
|
|||
|
|
|
|
Свойства материала |
|
|
|
Продольный модуль Юнга |
E1 |
146800 МПа |
|
Поперечный модуль Юнга |
E2, E3 |
11400 МПа |
|
Коэффициет Пуассона |
ν12, ν13 |
0,3 |
|
ν23 |
0,5 |
||
|
|||
Модуль сдвига |
G12, G13 |
6100 МПа |
|
G23 |
3800 МПа |
||
|
|||
Предел прочности на растяжение вдоль основы |
Xt |
1730 МПа |
|
Предел прочности на сжатие вдоль основы |
Xc |
1379 МПа |
|
Предел прочности на растяжение поперек основы |
Yt, Zt |
66,5 МПа |
|
Предел прочности на сжатие поперек основы |
Yc, Zc |
268,2 МПа |
|
Предел прочности на сдвиг |
S12, S13, S23 |
58,2 МПа |
Суммарная сила реакции измерялась на стороне, к которой прикладывались перемещения. На рис. 15 представлены графики зависимости силы реакции F (Н) от перемещений U (мм). Погрешность по максимальной нагрузке относительно натурного эксперимента для модели разрушения PDMG составила 41,41 %, для макроса FAIL_MOD – 47,73 %. Падение силы реакции происходит практически мгновенно. Причина большого отклонения от максимального значения нагрузки не выявлена. На рис. 16 представлена конечно-элементная модель с разрушенными элементами в начальном и конечном моменте разрушения.
Рис. 15. График зависимости силы реакции (F, Н) от перемещений (U, мм)
236
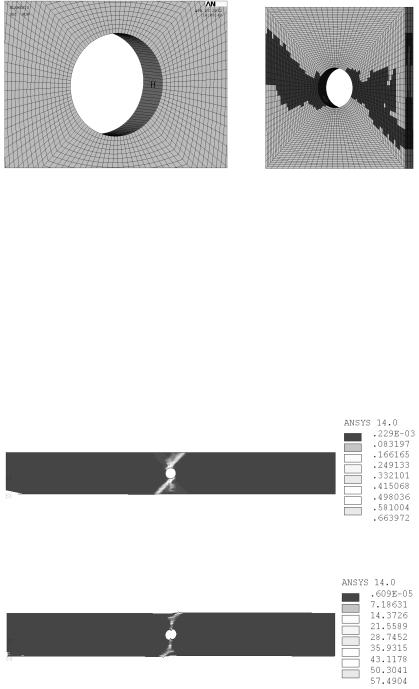
а |
б |
Рис. 16. Конечно-элементные модели с разрушенными элементами: а – при перемещениях 0,766 мм при использовании макроса FAIL_MOD; б– конечно-элементнаямодельсразрушенными элементамив начальный момент разрушения. Разрушенные элементы показаны более темным цветом
На рис. 17 показаны полные деформации по Мизесу при перемещениях 0,766 мм, полученных при использовании макроса FAIL_MOD. На рис. 18 показаны полные деформации по Мизесу при перемещениях 0,754 мм, полученных при использовании модели разрушения PDMG. Как видно из рис. 17–18, наибольшие полные деформации имеют разрушенные элементы.
Рис. 17. Полные деформации по Мизесу при перемещениях 0,766 мм, полученных при использовании макроса FAIL_MOD
Рис. 18. Полные деформации по Мизесу при перемещениях 0,754 мм, полученных при использовании модели разрушения PDMG
237
Заключение
Данные по полученным погрешностям в расчетах сведены в табл. 5.
|
|
|
Таблица 5 |
|
|
Погрешность в расчетах |
|
||
|
|
|
|
|
Название |
Методика |
Погрешность, % |
С чем сравнивалось |
|
эксперимента |
||||
|
|
|
||
|
FAIL_MOD |
6,72 |
по максимальной на- |
|
|
|
|
грузке относительно |
|
Расчет тонкой пласти- |
PDMG |
6,22 |
аналитического реше- |
|
|
|
ния |
||
ны на сдвиг |
|
|
||
FAIL_MOD |
10,63 |
по максимальной на- |
||
|
||||
|
PDMG |
11,16 |
грузке относительно |
|
|
натурногоэксперимента |
|||
|
|
|
||
Расчет пластины |
FAIL_MOD |
12,04 |
по максимальной на- |
|
с отверстием в центре |
PDMG |
26,33 |
грузке относительно |
|
на сжатие |
натурногоэксперимента |
|||
|
|
|||
Расчет пластины |
FAIL_MOD |
47,73 |
по максимальной на- |
|
с отверстием в центре |
PDMG |
41,41 |
грузке относительно |
|
на растяжение |
натурногоэксперимента |
|||
|
|
В расчете пластины с отверстием в центре на растяжение все модели разрушения подсказали заниженную предельную нагрузку. Это может быть связано с тем, что предельная нагрузка разрушения в натурном эксперименте не была подтверждена статистически или требуется применение более сложного критерия разрушения.
Отличия в результатах работы макроса FAIL_MOD и модели разрушения PDMG связаны с тем, что для определения коэффициентов запаса макрос FAIL_MOD анализирует напряжения в узлах, а в модели разрушения PDMG напряжения берутся из точек интегрирования элемента.
Ввиду того что все натурные эксперименты были проведении один-два раза, статистический разброс не был учтен.
Требуется дальнейшее исследование методик предсказания разрушающей нагрузки. Планируется провести подобные расчеты, но уже с использованием более сложных критериев разрушения Хашина, Па-
ка, LaRc03, LaRc04.
238
Библиографический список
1.Sleight D.W. Progressive Failure Analysis Methodology for Laminated Composite Structures. – Hampton: Langley Research Center, 1999. – 92 p.
2.Perillo G., Vedvis N.P., Echtermeyer A.T. Numerical application of three-dimensional failure criteria for laminated composite materials // SIMULIA Community Conference. – 2012. – URL: http://www.simuliachina.com/download/global/2012/Perillo_NTNU_final_2212012.pdf.
3.Pietropaoli E. Progressive Failure Analysis of Composite Structures Using a Constitutive Material Model (USERMAT) Developed and Implemented in ANSYS // Springer Science + Business Media B.V. – 2011. – URL: http://www.scribd.com/doc/74555060/Full-Text.
4.Chua H.E. Compressive failure of open-hole carbon composite laminates / National University of Singapore. – 2007. – URL: http://scholarbank.nus.edu.sg/bitstream/handle/10635/17550/%28Chua%20Hui%20Eng%29 CHE.pdf?sequence=1.
5.Patent No. AIAA Paper 81-0543. Postbuckling and Failure Characteristics of Selected Flat Rectangular Graphite-Epoxy Plates Loaded in Compression / J.H.Jr. Starnes, M. Rouse. – 1981.
6.Chang F.K., Chen M.H. The In Situ Ply Shear Strength Distributions in Graphite/Epoxy Laminated Composites // Journal of Composite Materials. – 1987. – Vol. 27. – P. 708–733.
7.Shahid I. Progressive Failure Analysis of Laminated Composites Subjected to In-Plane Tensile and Shear Loads: Ph. D. Dissertation / Stanford University. – 1993.
8.Suemasu H., Takahashi H., Ishikawa T. On the failure mechanism of composite laminates with an open hole subjected to compressive load // Composite Science and Technology. – 2006. – Vol. 66. – P. 634–641.
9.Chang F.K., Chang K.Y. A Progressive Damage Model for Laminated Composites Containing Stress Concentrations // Journal of Composite Materials. – September 1987. – Vol. 21. – P. 834–855.
10.Tan S.C. A progressive failure model for composite laminates containing openings // Journal of Composite Materials. – 1991. – Vol. 25, no. 5. – P. 556–577.
239
References
1.Sleight D.W. Progressive Failure Analysis Methodology for Laminated Composite Structures. Hampton: Langley Research Center, 1999, 92 p.
2.Perillo G., Vedvis N.P., Echtermeyer A.T. Numerical application of three-dimensional failure criteria for laminated composite materials. SIMULIA Community Conference, 2012, available at: http://www.simuliachina.com/download/global/2012/Perillo_NTNU_final_2212012.pdf.
3.Pietropaoli E. Progressive Failure Analysis of Composite Structures Using a Constitutive Material Model (USERMAT) Developed and Implemented in ANSYS, Springer Science + Business Media B.V., 2011, available at: http://www.scribd.com/doc/74555060/Full-Text.
4.Chua H.E. Compressive failure of open-hole carbon composite laminates, National University of Singapore, 2007, available at: http://scholarbank.nus.edu.sg/bitstream/handle/10635/17550/%28Chua%20 Hui%20Eng%29CHE.pdf?sequence=1.
5.Starnes J.H.Jr., Rouse M. Patent No. AIAA Paper 81-0543. Postbuckling and Failure Characteristics of Selected Flat Rectangular GraphiteEpoxy Plates Loaded in Compression, 1981.
6.Chang F.K., Chen M.H. The In Situ Ply Shear Strength Distributions in Graphite/Epoxy Laminated Composites. Journal of Composite Materials, 1987, vol. 27, pp. 708–733.
7.Shahid I. Progressive Failure Analysis of Laminated Composites Subjected to In-Plane Tensile and Shear Loads: Ph.D. Dissertation, Stanford University, 1993.
8.Suemasu H., Takahashi H., Ishikawa T. On the failure mechanism of composite laminates with an open hole subjected to compressive load.
Composite Science and Technology, 2006, vol. 66, pp. 634–641.
9.Chang F.K., Chang K.Y. A Progressive Damage Model for Laminated Composites Containing Stress Concentrations. Journal of Composite Materials, September 1987, vol. 21, pp. 834–855.
10.Tan S.C. A progressive failure model for composite laminates containing openings. Journal of Composite Materials, 1991, vol. 25, no. 5, pp. 556–577.
Получено 28.09.2012
240