
Учебное пособие 800399
.pdf2.3. Классификация затрат на качество: сравнительный анализ основных подходов
Экономические аспекты управления качеством уже довольно давно находятся в центре внимания как зарубежных, так и отечественных специалистов. Тем не менее, многие аспекты экономического обеспечения управления качеством остаются и на сегодняшний день актуальными для анализа и изучения.
Важной задачей экономики качества является систематизация (классификация) затрат на обеспечение качества и выявление среди них не создающих добавленной ценности для предприятия с целью их устранения (минимизации).
Классификация затрат на качество предполагает формирование на основе определяющего принципа структуры затрат по определенным признакам. При этом под структурой затрат понимается иерархическая зависимость групп и элементов, составляющих затраты на качество. Структура затрат на качество, в свою очередь, определяется составом затрат, представляющим собой совокупность расходов на все необходимые виды деятельности по обеспечению и улучшению качества объекта в соответствии с требованиями потребителей [126].
По мнению большинства исследователей проблем экономики качества, впервые законченная концепция, касающаяся классификации затрат, была разработана Дж. Джураном в 1951 году. В качестве основного принципа классификации затрат на обеспечение качества был использован принцип необходимого и излишнего. По мнению Джурана, затраты на обеспечение качества целесообразно группировать по двум основным категориям: затраты на обеспечение качества конструкции и затраты на обеспечение качества изготовления изделия. Позднее (в 1962 году) им были сформулированы следующие основные статьи затрат на качество:
1. Затраты на обеспечение качества конструкции: затраты на научно-исследовательские работы; затраты на разработку рабочего проекта;
затраты на планирование и технологическую подготовку производства.
50
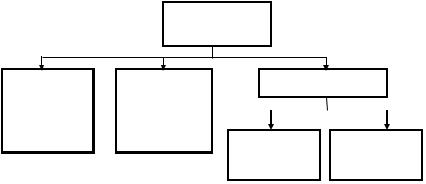
2. Затраты на обеспечение качества изготовления изделия: затраты на процесс производства; затраты на проведение анализа причин, вызывающих появ-
ление дефектов; административные затраты на разработку и проведение
программ по обеспечению качества [101].
Идеи Джурана впоследствии развил А. Фейгенбаум. Классификация затрат на качество, предложенная Фейгенбаумом еще в 1963 году в Америке, в период развития внутрифирменных систем управления качеством, широко используется и в настоящее время на предприятиях США и Европы.
А. Фейгенбаум предложил выделить четыре группы затрат в соответствии с тремя основными группами факторов, влияющих на качество (рис. 2.4).
Расходы на качество
Затраты на |
Затраты на |
Потери |
||
предупрежде- |
оценку каче- |
|
|
|
ние возникно- |
ства продукции |
|
|
|
|
|
|
||
вения дефек- |
|
|
|
|
тов |
Внутренние |
Внешние |
||
|
||||
|
затраты на |
затраты на |
||
|
дефект |
дефект |
Рис. 2.4. Классификация затрат на качество А. Фейгенбаума
Группа 1: затраты на предупреждение возникновения дефектов (превентивные затраты) — это расходы на разработку и планирование программ, направленных на улучшение качества, на достижение оптимального уровня контроля и предупреждение ситуаций, приводящих к возникновению дефектов (несоответствий).
Группа 2: затраты на оценку качества продукции — это стоимость оценки достижения требуемого качества работ, выполняемых на любой стадии, которая определяет путь последовательного
51
прохождения товара от его инженерного замысла до утилизации. Т. е. это расходы на проведение технического контроля и испытаний на всех этапах производства продукции (или процесса оказания услуг) с целью установления соответствия показателей качества изготовленной продукции (услуг) предъявляемым требованиям.
Группа 3: затраты, обусловленные внутренними и внешними отказами продукции. Издержки вследствие внутренних отказов — это издержки из-за несоответствий или дефектов, обнаруженных внутри организации на любой стадии петли качества до передачи изделия от поставщика к покупателю. Издержки вследствие внешних отказов — это издержки из-за несоответствий или дефектов, обнаруженных после поставки продукции заказчику (потребителю).
Перечень статей расходов, включаемых в каждую из категорий затрат на обеспечение качества, приводится в Прил. 1.
А. Фейгенбаум, отметив различия в динамике выделенных групп затрат с ростом качества, предложил распределять усилия между этими группами затрат и таким образом искать оптимальное соотношение между ними (искать минимум совокупных затрат этих групп).
Данному подходу к управлению затратами на качество присущ ряд недостатков:
1)предполагается возможность наличия в производстве экономически оправданного уровня брака;
2)затраты, необходимые для обеспечения качества (группы 1 и 2), приравнивают к потерям (группа 3), а это не позволяет сравнить затраты на повышение качества и потери и оценить экономическую эффективность управления затратами на качество (которая должна определяться путем сравнения затрат и потерь);
3)возникают затруднения с отнесением некоторых элементов затрат к тем или иным группам (с равным основанием ряд затрат можно отнести к любой из трех категорий);
4)распределение затрат по категориям имеет тенденцию отвлекать внимание от истинной цели учета и оценки затрат — их общего снижения (так, увеличение предупредительных затрат на качество должно приводить к снижению полных затрат, однако и они сами по себе должны в конечном итоге быть снижены).
Тем не менее, именно эта классификация, принятая Комитетом по затратам на качество (QCC) Американского общества по
52
контролю качества (ныне Американское общество качества — ASQ), лежит в основе международных стандартов в области экономики качества и сегодня является универсальной, т. е. применяемой (при соответствующей переработке) всеми компаниями, независимо от их отраслевой принадлежности или сферы деятельности. Она используется в промышленности, сфере услуг, деятельности административных органов и других областях экономики [96].
Впоследствии концепция затрат на качество Фейгенбаума, ориентированная на конечный результат (продукцию), получила свое применение и развитие в первой редакции Британского стандарта BS 6143 «Руководство по экономике качества. Модель предупреждения, оценки и отказов», принятой в 1981 году. С этого момента появилась первая стандартизованная классификация затрат на качество, получившая название «PAF-модель» (prevention — предупреждение, appraisal — оценивание, failure — дефект). Поскольку эта классификация практически повторяет классификацию А. Фейгенбаума, ей присущи те же недостатки, которые были отмечены ранее. Классификация затрат представлена на рис. 2.5.
Вновой версии Британского стандарта (1990 года), состоящей из двух самостоятельных частей, внесены существенные изменения в части классификации затрат на качество.
Так, в BS 6143. Часть 1: 1990 «Руководство по экономике качества. Модель стоимостного процесса» содержится метод применения оценки затрат на качество к любому процессу или услуге
ипризнается важность определения качества процесса. Затраты на качество группируются по двум основным категориям — затраты на соответствие и затраты вследствие несоответствия, что существенно упрощает классификацию затрат. Метод зависит от используемой модели процесса, приводятся рекомендации по использованию различных рациональных методов. Применение модели управления процессом совместимо с концепцией всеобщего (тотального) управления качеством [15]. Данный подход к классификации затрат более подробно будет рассмотрен нами позже.
ВBS 6143. Часть 2: 1990 «Руководство по экономике качества. Модель предупреждения, оценки и отказов» представлена пересмотренная (по сравнению с версией 1981 года) на основе приобретенного опыта версия традиционного метода оценки затрат на качество в производственных отраслях [14].
53
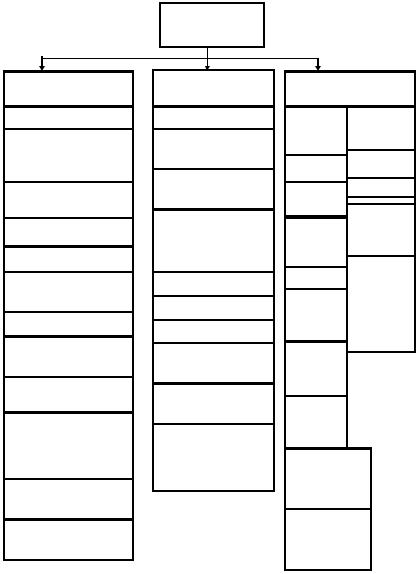
Все затраты в соответствии с этой частью стандарта руководство предприятия должно классифицировать на две группы:
Расходы на качество
Затраты на предотвращение ошибок
Планирование качества
Исследование пригодности к качественному производству
Оценка и консультация поставщиков
Планирование контроля
Заключение о качестве
Управление отделом обеспечения качеством
Управление качеством
Обучение по обеспечению качеством
Программы по мотивации качественного труда
Сравнение качественных показателей с конкурирующими показателями
Другие методы по определению ошибок
Уход за средствами контроля
Затраты на контроль
Входной контроль
Производственный
контроль
Контроль готовой продукции
Контроль качества при собственном проведении наружных монтажных работ
Приемочный контроль
Средства контроля
Экспертизы качества
Лабораторные исследования
Документация контроля
Другие меры и приобретаемые инструменты для осуществления контроля качества
Затраты на исправление ошибок
Внутри |
Вне произ- |
|
производ- |
водства |
|
ства |
|
|
|
Брак |
|
Брак |
||
|
||
|
Доработка |
|
Доработ- |
||
ка |
Гарантии |
|
Отклоне- |
||
изготови- |
||
ние в ко- |
теля |
|
личестве |
Другие |
|
Уценка |
||
расходы, |
||
Сортиро- |
возника- |
|
ющие вне |
||
вочный |
||
производ- |
||
контроль |
||
ства |
||
|
||
Повтор- |
|
|
|
||
ный кон- |
|
|
троль |
|
|
Исследо- |
|
|
вание |
|
|
проблем |
|
|
|
|
Простои из-за низкого качества производства
Другие расходы, возникающие на производстве
Рис. 2.5. Классификация затрат на качество по Британскому стандарту BS 6143:1981
54
1.Затраты на соответствие — это затраты на предупредительные меры по контролю качества и затраты на стандарты (нормы) по качеству для обеспечения их работы.
Предупредительные затраты являются достаточно весомы
ипроизводятся с тем, чтобы впоследствии снизить оценочные затраты и издержки вследствие отказов. Предупредительные затраты, по сути, представляют собой денежные средства, инвестированные в качество.
Оценочные затраты предприятие понесет при первоначальном установлении несоответствия изделия требованиям к качеству (рис. 2.6). Они не включают затраты из-за переделок или повторного контроля, которые следуют за отказом.
2.Затраты на отказы, ведущие к снижению прибыли, независимо от того, чем они вызваны. Эти затраты являются следствием внешних и внутренних отказов.
Издержки вследствие внутренних отказов возникают из-за неадекватного качества, обнаруживаемого до передачи изделия поставщиком покупателю.
Издержки вследствие внешних отказов возникают из-за неадекватного качества, обнаруживаемого после передачи продукции предприятием покупателю.
Полный перечень затрат, в соответствии с BS 6143. Часть 2: 1990 «Руководство по экономике качества. Модель предупреждения, оценки и отказов», представлен на рис. 2.6.
Позднее известный американский специалист в области качества Ф. Кросби внес существенные корректировки в концепцию А. Фейгенбаума. По сути, он перегруппировал затраты на качество Фейгенбаума, разделив их на две категории: «затраты на соответствие» и «затраты на несоответствие» [106].
Воснове такой классификации лежит принцип обеспечения
нулевого уровня дефектов в процессе производства продукции. В то время как А. Фейгенбаум придерживался принципа обеспечения оптимального уровня дефектов.
Это принципиальное отличие двух концепций привело к тому, что Ф. Кросби посчитал необходимым оценивать уровень затрат, требуемых для производства качественной продукции с первого предъявления (затраты на соответствие или «цена соответствия») и уровень затрат, вызванных необходимостью исправ-
55
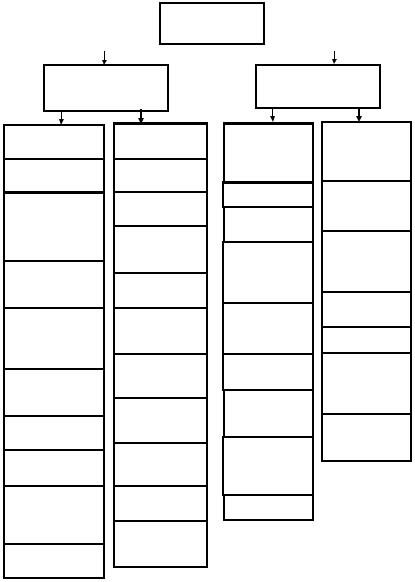
лять допущенный брак и несоответствия (затраты на несоответствие или «цена несоответствия»).
|
|
Расходы |
||
|
|
на качество |
||
|
|
|
||
|
|
|
|
|
Предупредительные |
|
Отказы, ведущие |
||
меры по контролю |
|
к снижению прибыли |
||
качества |
|
|
|
Предупредительные затраты
Планирование
качества
Проектирование
иразработка оборудования для
контроля, испытаний и измерений
Рассмотрение качества и контроль проекта
Калибровка и ТО оборудования, используемого для оценки качества
Обеспечение
качества у поставщика
Обучение в области качества
Надзор за качеством
Получение и анализ информации о качестве, отчетность
Программа улучшения качества
Оценочные
затраты
Допроизводственные затраты
Входной
контроль
Лабораторные
приемочные
испытания
Контроль и испытания
Оборудование для контроля и испытаний
Материалы для контроля
и испытаний
Анализ результатов контроля и испытаний
Контроль эксплуатационных характеристик
Рассмотрение и одобрение
Оценка запасов. Хранение протоколов
Издержки
вследствие
внутренних
отказов
Лом
Замена, переделка, ремонт
Анализ неисправностей или дефектов/отказов
Повторный контроль и испытания
Дефекты у субподрядчиков
Разрешения на модификации и уступки
Понижение
категории (сортности) продукции
Простои
Издержки
вследствие
внешних
отказов
Рекламации в период гарантийного срока
Повторно
поставленные и возвращенные изделия
Уступки (отклонения)
Потеря продаж
Издержки, связанные с аннулированием (изъятием)
Ответственность за качество продукции
Рис. 2.6. Классификация затрат на качество по Британскому стандарту BS 6143:1990
56
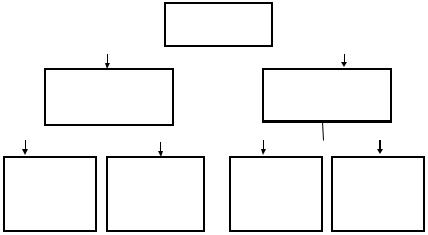
По мнению Ф. Кросби, производитель платит не за качество продукции, а за его отсутствие, т. е. прибыль снижается из-за потерь брака, переделок и ремонта [108].
В затраты на соответствие Ф. Кросби включил затраты, отнесенные А. Фейгенбаумом к группам 1 и 2 (рис. 2.7), в затраты на несоответствие были включены затраты, которые отнесены А. Фейгенбаумом к группе 3 (см. рис. 2.4).
|
|
|
|
|
Расходы |
|
|
||
|
|
|
|
на качество |
|
|
|||
|
|
|
|
|
|
|
|
||
|
|
|
|
|
|
|
|
|
|
|
Затраты на соответ- |
|
|
Затраты на несоот- |
|||||
|
ствие (на обеспечение |
|
|
ветствие (потери) |
|||||
|
качества) |
|
|
|
|
|
|||
|
|
|
|
|
|
|
|
||
|
|
|
|
|
|
|
|
|
|
Затраты на |
Затраты на |
|
|
|
|
|
|||
профилактику |
контроль и |
|
|
|
|
|
|||
|
брака |
оценку достиг- |
|
Внутренние |
Внешние |
||||
|
|
|
нутого уровня |
|
|
|
|
|
|
|
|
|
качества |
|
|
|
|
|
Рис. 2.7. Классификация затрат на качество Ф. Кросби
1. Затраты на соответствие включают в себя: 1.1. Затраты на профилактику брака:
1.1.1. Предупредительные действия: управление качеством; управление процессом; обеспечение качества поставок; аудит системы качества; программа улучшения качества; обучение вопросам качества.
1.1.2. Корректирующие действия (предотвращение повторения выявленных дефектов).
1.2. Затраты на контроль:
1.2.1. Проверка и испытания (выявление дефектов после изготовления).
57

1.2.2.Контроль процесса (выявление дефектов в процессе производства).
1.2.3.Аудит (контроль входных объектов).
2. Затраты на несоответствие включают в себя: 2.1. Потери на внутренние дефекты:
2.1.1. Переделки и ремонт.
2.1.2. Повторная проверка и испытание. 2.1.3. Анализ потерь.
2.1.4. Уступки (допуск к применению тех материалов, которые не отвечают техническим требованиям).
2.1.5. Снижение сорта. 2.1.6. Отходы.
2.2. Потери на внешние дефекты: 2.2.1. Переделки и ремонт.
2.2.2. Повторная проверка и испытание. 2.2.3. Снижение сорта.
2.2.4. Анализ потерь.
2.2.5. Гарантийные обязательства.
2.2.6. Юридические споры и выплаты компенсации.
По мнению Ф. Кросби, в результате осуществления затрат на соответствие должен быть обеспечен выпуск продукции с нулевым уровнем дефектов (с первого предъявления). В этом случае затраты на несоответствие возникать не будут [108]. Соотношение между затратами на соответствие (З) и потерями (П), связанными с несоответствиями, Ф. Кросби предложил использовать для диагностики состояния СМК организации. Для этого он разработал «решетку зрелости» (табл. 2.1).
|
|
Таблица 2.1 |
|
Диагностика СМК предприятия по критерию Ф. Кросби |
|||
|
|
|
|
Стадии развития |
Критерии диагно- |
Показатели соответствия |
|
стики стадий |
|
||
СМК |
СМК стадиям развития |
|
|
развития СМК |
|
||
|
|
|
|
|
|
|
|
1. Контроль |
З « П |
1.2.1 > 1.2.2 + 1.2.3 |
|
качества |
|
||
|
|
|
|
2. Управление |
|
1.1.1 < 1.1.2; |
|
З < П |
1.2.2 > 1.2.1; |
|
|
качеством |
|
||
|
1.2.2 > 1.2.3 |
|
|
|
|
|
58
|
|
Окончание табл. 2.1 |
|
|
|
|
|
1 |
2 |
3 |
|
3. Обеспечение |
З > П |
1.1.1 > 1.1.2; |
|
качества |
1.2.1 < 1.2.2 + 1.2.3 |
|
|
|
|
||
4. Совершен- |
|
Циклически изменяются, |
|
ствование каче- |
З » П |
последовательно повторяя |
|
ства |
|
соотношения стадий |
|
Само понятие «затраты на качество» имеет некий негативный оттенок, в значительной мере отражая подходы, доминировавшие в 50-е годы, когда бытовало мнение, что чем выше качество продукции, тем выше и затраты на ее производство. Но по мере того, как изменялось отношение менеджеров к концепции «затраты на качество», изменялось и само содержание этого понятия. Поскольку приоритетная задача системы экономики качества состоит в снижении затрат предприятия, обусловленных плохим качеством продукции или услуг, суть такой системы более точно отражает термин «затраты на неудовлетворительное качество»
(poor-quality cost, PQC) [91].
Концепция PQC является непосредственным развитием идей Дж. Джурана – А. Фейгенбаума, но в то же время имеет целый ряд специфических особенностей:
1.Для того чтобы задача выявления и отслеживания затрат на качество была воспринята менеджментом предприятий (в том числе — и непроизводственной сферы), термин «дефект», преимущественно относящийся к производству, был заменен на термин «ошибка».
2.Смысл понятия «оптимальные затраты на качество», ориентированного на производственную деятельность, расширен таким образом, чтобы концепция отражала экономические преимущества безошибочности всех направлений деятельности предприятия, а не только связанных с изготовлением продукции. Процесс улучшения качества рассматривается как «непрерывное движение в сторону совершенствования».
3.Принимаются во внимание затраты, понесенные клиентом из-за неудовлетворительного (плохого) качества продукции или услуги.
59