
Vladimirov_S.V._Mehanizats._pogruz.-razgruz.,_transport._i_sklad._rabot2010
.pdfЭлектропогрузчики небольшой грузоподъемности а высотой подъема до 1,8 м предназначены также для работы в крытых железнодорожных вагонах и трюмах судов.
Предельное рекомендуемое расстояние транспортирования тарно-штучных грузов до 100-200 м.
Для обеспечения широкой универсальности электропогрузчиков используются следующие сменные грузозахватные приспособления: многоштыревой захват, кантователь, боковой захват, вилочный захват, универсальный захват, штырь, стрела, ковш и прочие.
В зависимости от конструкции электроштабелера управление можетосуществляется водителем с пола, с сиденья или с площадки машины.
Недостатки: отсутствие централизованных, хорошо оснащенных ремонтных баз и зарядных станций.
Автопогрузчики являются универсальными машинами напольного транспорта и предназначены для погрузочно-разгрузочных работ с тарно-штучными и сыпучими грузами на площадках открытых и с навесом, в складских помещениях с твердым покрытием пола.
Автопогрузчики могут эксплуатироваться при температуре от -40 °С до +40°С. Рекомендуемая дальность транспортирования грузов до 200-300м.
Автопогрузчики, как правило, рекомендуются для работы на открытом воздухе или в хорошо проветриваемых крытых помещениях с грузами, для которых не опасны действия выхлопных газов.
В зависимости от характера перерабатываемых грузов, автопогрузчики могут комплектоваться различными сменными грузозахватными приспособлениями: вилами, стрелой безблочной и крановой, штырем, универсальным боковым захватом, ковшом, грейфером для сыпучих грузов и лесных материалов.
3. Машины для групповой укладки в транспортную тару упакованных пищевых продуктов
Одним из основных условий внедрения перевозок продукции в тареоборудовании является наличие механизмов для укладки мелкоштучных грузов в та- ру-оборудование. В связи с многообразием потребительской тары невозможно создание автоматов для каждого вида груза в отдельности, и поэтому при создании машин основными условиями являются их универсальность и возможность приспособления к различным типоразмерам грузов с минимальными затратами труда и материальных ресурсов (рис. 11.).
Например, разработаны укладочные автоматы нескольких типов. Один из них предназначен для укладки в контейнер готовой продукции в стеклянной таре (банок и бутылок), другой рассчитан на укладку грузов в пачках и мелких пакетах (фасованные мука, крупа, сахар-песок, сахар-рафинад и др.). Автомат для укладки продукции в стеклянной таре приведен на рис. 12. Штучные грузы поступают потоком с последней технологической операции на входной пластинчатый конвейер, где они формируются в ряды соответственно внутренним размерам контейнера. Сформированный порядно горизонтальный слой бутылок (банок) забирается групповым механическим захватом и переносится в зону, под которой находится контейнер. Захват движется по направляющим и опускает грузы либо на дно контейнера, либо на предыдущий ряд, на который предварительно уложена картонная прокладка.
Высота опускания захвата автоматически ограничивается при достижении грузом поверхности укладки. Подача порожних контейнеров и вывод загруженных осуществляется с помощью роликового конвейера и электропогрузчика или ручной тележки с подъемными вилами.
Производительность автомата 12000 единиц груза в час, мощность электродвигателей 4,5 кВт
Автомат для укладки в контейнеры грузов в пачках или пакетах показан на рис.
13.
Пачки или пакеты поступают от фасовочных автоматов по конвейеру, затем из них на конвейере 2 составляются сдвоенные ряды, которые поступают в укладочную головку, где формируются в горизонтальные ряды и вводятся в контейнер. Для укладки на нужную высоту контейнер поднимается и по мере загрузки пачек опускается. Порожние контейнеры подаются, а загру-женные отводятся с помощью конвейера 5. Производительность автомата до 120 пачек в минуту. Автомат обслуживает два оператора, один из которых подготавливает контейнеры.
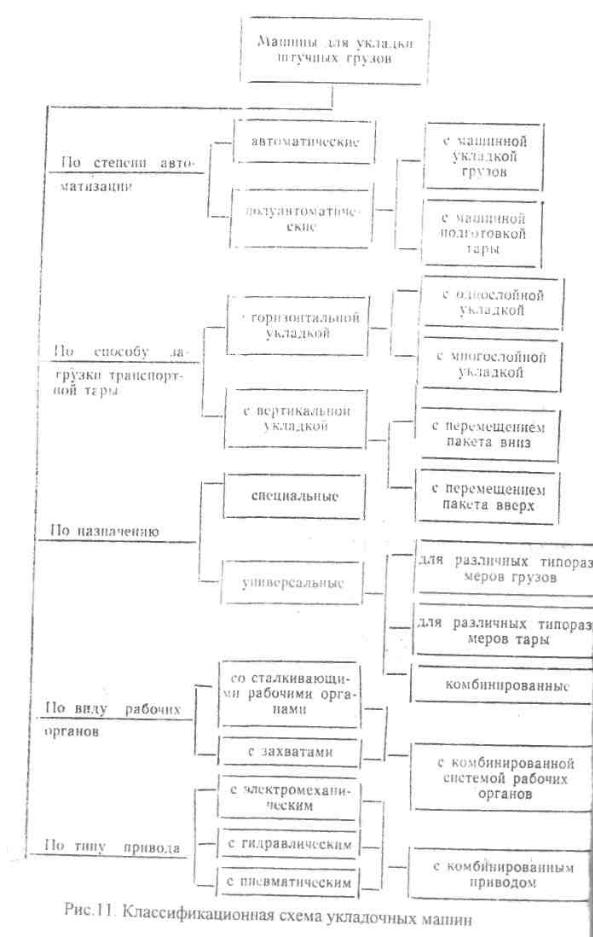
Перевозка продукции в таре-оборудовании требует взаимосвязанного рассмотрения всех вопросов у поставщиков, транспортников и потребителей. Автотранспорт для перевозок в таре-оборудовании должен быть таким же, как и для пакетных перевозок, т.е. пакетовозы с боковыми раздвижными дверями. Порядок выбора эффективного типоразмера тары-оборудования и организация перевозок следующие:
-выбирают грузы, перевозки которых следует осуществлять в тареоборудовании. Это должны быть в первую очередь наиболее массовые однородные грузы по возможности с короткими сроками реализации для того, чтобы количество тары-оборудования было наименьшим;
-изучают существующую схему товародвижения на транспортном процессе от цеха поставщика до торгового зала магазина;
-определяют условия выпуска продукции на производстве, доставки грузов автотранспортом и условия реализации в магазинах;
-отбирают варианты типоразмеров тары-оборудования, видов автотранспорта и способов организации движения для технико-экономического; сравнения;
-разрабатывают транспортно-технические карты (ТТК) по каждому из вариантов, делают технико-экономическое сравнение и выбирают наиболее эффективное решение по минимальным затратам и приведенным расходам суммарно у всех участников транспортного процесса.
Тема №12 «Классификация складов и оборудования»
1.Классификация и назначение складов
2.Склады сыпучих грузов. Склады штучных грузов.
3.Манипуляторы и роботы для механизации погрузочно-разгрузочных, транспортных и складских работ.
4.Система управления складами.
1. Классификация аккумулирующих устройств по их назначению Склад - это сложный комплекс строительных сооружений и устройств,
оснащенный высокопроизводительным подъемно-транспортным оборудованием и предназначенным для приема, переработки, складирования, отпуска грузов, а также для выполнения операций, предусмотренных технологией внутрискладской грузопереработки.
При выборе оборудования для склада его классифицируют по следующим показателям:
1.По виду груза - навалочные, тарно-штучные, наливные; 2.По номенклатуре поступающих грузов - однотипные и многоно-
менклатурные; 3.По готовому грузопотоку - мелкие (до 1 тыс. т в год); средние -1...25
тыс. т в год; крупные - свыше 25 тыс. т в год; 4.По типу строительной части - открытые, полузакрытые и закрытые.
От того, насколько рационально размещены склады, в существенной мере зависит общий объем грузопереработки, вид применяемых транспортных средств предприятия.
В качестве исходных данных для рационального размещения складов являются: характеристика развития и размещения производительных сил рассматриваемого района; характеристика действующих материальных баз и их технико-экономические показатели; перечень потребителей; объемы потребления по видам продукции и пунктам (районам) потребителя; объем поставок груза на базы; пункты возможного размещения баз; состояние и развитие транспортной сети; расстояние перевозки грузов; нормативные и справочные материалы.
При выборе площадки для размещения аккумулирующего устройства в определенном пункте необходимо учитывать близость его расположения к пунктам примыкания железных дорог, а также развитой сети автомобильных дорог, удобного снабжения электропередачей, водой и пр.
2. Склады сыпучих грузов
Характеристика складов для сыпучих грузов
Тип скла- |
Хранение |
Продукт |
Оборудование для перемещения грузов |
|
да |
|
|
при подаче |
при выдаче |
|
|
|
|
|
Открытый |
В штабе- |
хранения |
Передвижные и стацио- |
Передвижные погрузочные |
|
лях |
овощного |
нарные разгрузочные ма- |
машины, краны, гидро- |
|
|
сырья, накап- |
шины, краны с грейдера- |
транспорт |
|
|
ливаемого в |
ми, ленточные конвейе- |
|
|
|
период заго- |
ры |
|
|
|
товок |
|
|
Закрытый |
Напольное |
Зерновое сы- |
Разгрузчики автомоби- |
Ленточные и скребковые |
|
|
рье |
лей и вагонов, ленточ- |
конвейеры, элеваторы, вин- |
|
|
|
ные и скребковые кон- |
товые конвейеры, аэ- |
|
|
|
вейеры, элеваторы |
рогравитационные кон- |
|
|
|
|
вейеры |
Закрытый |
В бунке- |
Зерновое сы- |
Разгрузчики автомоби- |
Ленточные и скребковые |
|
рах и си- |
рье |
лей и вагонов, ленточ- |
конвейеры, элеваторы, вин- |
|
лосах |
|
ные и скребковые кон- |
товые и аэрогравита- |
|
|
|
вейеры, элеваторы, вин- |
ционные конвейеры |
|
|
|
товые конвейеры, |
|
|
|
|
пневмотранс-портные |
|
|
|
|
установки |
|
Склады штучных грузов
Объем ПРТС работ со штучными грузами в различных отраслях промышленности составляет около 70% в общем объеме ПРТС работ, и большая часть всех работ сосредоточена в складах штучных грузов.
Склад можно представить в виде совокупности следующих основных элементов: фронт разгрузки внешнего транспорта (железнодорожного, автомобильного и др.); зона приемки, сортировки, подготовки к складированию прибывших грузов; зона хранения грузов; зона комплектации заказов по заявкам потребителей; зона погрузки заказов на внешний транспорт; зона хранения складской и транспортной тары; зона управления складом (контора склада и др. административные подразделения).
Компоновка склада определяется технологией переработки грузов на складе, видом груза, типом применяемых подъемно - транспортных машин и складского оборудования.
Наибольшее распространение получили склады, выполненные по тупиковой схеме. При такой компоновочной схеме повышается коэффициент использования оборудования и занятость обслуживающего персонала, увеличивается производительность подъемно - транспортного оборудования, упрощается переход на автоматизированный режим работы склада.
Недостатком такой схемы является совмещение грузопотоков прибытия и отправления на одной площадке. При небольших грузопотоках это отражается на работе склада незначительно. При больших грузопотоках (более 5 тыс. т в
год) рекомендуется верхний уровень использовать для приема груза, нижний - для отправления или наоборот.
Проходная схема используется для складов со стеллажами динамического хранения (гравитационными, роликовыми и т. д.).
В настоящее время применяются следующие схемы механизации: хранение в стеллажах или штабелях с транспортировкой и укладкой электропогрузчиками; в стеллажах с транспортировкой и стеллажи-рованием кра- нами-штабелерами; на стеллажах с загрузкой и выгрузкой кранамиштабелерами; на гравитационных стеллажах; в подвижных стеллажах с укладкой и выемкой краном-штабелером или электроштабелером.
3. МАНИПУЛЯТОРЫ И РОБОТЫ ДЛЯ МЕХАНИЗАЦИИ ПРТС РАБОТ
промышленные роботы Одной из основных причин создания ПР является экономия средств. При-
менение ПР обеспечивает большую гибкость технических и организационных решений .
Основные показатели, характеризующие технические возможности ПР: 1)номинальная грузоподъемность (кг); 2)размеры и форма рабочей зоны;
3)показатели степени подвижности: максимальное перемещение (мм, град.); время перемещения (с); максимальная скорость (м/с, град/с) ; максимальное ус-
корение |
(м/с2, град/с2); максимальная абсолютная погрешность позициониро- |
||||
вания |
(мм); |
число |
программируемых |
точек |
приl |
прямом и обратном перемещении; 4)показатели захватного устройства: усилие захватывания (Н); время захваты-
вания (с); время освобождения (с); максимальный и минималь-ный размеры объекта манипулирования (мм);
5)показатели устройства управления: число одновременно управляемых движений по степеням подвижности; число каналов связи (входе и выходов) с внешним оборудованием;
6)давление (МПа) и расход (м3/с) жидкости или воздуха (для ПР с гидроили пневмоприводом)
7)напряжение электропитания (В); 8)потребляемая мощность (кВт) ;
9)показатели надежности: наработка на отказ (час); срок службы (лет) до капитального ремонта и до списания;
10)масса (кг); 11)размеры (длина, ширина, высота) (мм).
Под грузоподъемностью ПР понимают наибольшую массу объекта манипулирования (масса захватного устройства в грузоподъемность не входит).
Под погрешностью позиционирования рабочего органа ПР понимают отклонение его положения от положения, заданного устройством передвижения (УП). Обычно ПР программируется методом обучения, эта погрешность определяется повторяемостью прихода звена ПР в заданную точку в течение цикла.
ПР классифицируют по следующим признакам: специализация, грузоподъемность, число степеней подвижности, возможность передвижения, способ установки на рабочем месте, вид системы координат; вид привода и управления, способ программирования.
По специализации ПР разделяют на специальные, специализиро-ванные и универсальные; по грузоподъемности - на сверхлегкие (до 1 кг), легкие (1...10 кг), средние (10...200кг), тяжелые (200... 1000кг) и сверхтяжелые (свыше 1000кг); по числу п степеней подвижности роботы разделяют на ПР с п = 2, ПР с п = 3, ПР с п = 4, ПР с п > 4; по возможности перемещения - на стационарные и передвижные; по виду систем координат - на работающие в декартовой системе (плоской, пространственной), в полярной системе (плоской, цилиндрической, сферической) и в сложной полярной системе (цилиндрической, сферической).
Промышленный робот-манипулятор состоит из манипулятора - исполнительного органа, несущего схват, устройства передвижения (УП), если робот не стационарный, устройства управления.
манипуляторы
Манипулятор - это управляемое устройство, оснащенное рабочим органом (захватным устройством) и предназначенное для выполнения двигательных функций, аналогичных функциям руки человека при перемещении объектов в пространстве. Манипуляторы могут иметь ручное, автоматическое или комбинированное управление. Промышленный робот (ПР) включает в себя манипулятор и перепрограммируемое устройство управ-ления.
Важной характеристикой манипулятора является погрешности позиционирования, который в современных ПР колеблется от + 4 до + 0,02 мм.
Скорость линейных перемещений рабочих органов манипуляторов 0,2...5м/с, а угловых перемещений 60 ... 180 рад/с. Наибольшим быстродействием обладают манипуляторы с пневмоприводом.
4. Система управления складом
.
В складском хозяйстве используются различные системы АСУ: с частичной автоматизацией управления, с дистанционным управлением, с программным управлением и с использованием управляющих машин. Выбор той или иной системы определяется характером и объемом работ складов и баз, принятой организацией и механизацией работ, системой учета и контроля за движением материальных ценностей.
Технологический процесс обработки информации, связанный с переработкой материалов на складах и базах в условиях АСУ, можно разделить на следующие четыре этапа: прием и регистрация входной информации; подготовка исходных данных; обработка информации; контроль, подготовка и регистрация выпуска выходных документов.
Переменные программы составляют при проектировании автоматизированных складов, и их содержание должно отражать принятую технологию ПРТС работ на складах. При составлении алго-
ритмов работы кранов все движения крана, выполняемые в течение цикла, разбиваются на отдельные операции, управляемые при помощи программного устройства.
Устройство программного (логического) управления составляют из унифицированных блоков, используемых для кранов-штабелеров как мостового, так и стеллажного типов. Адрес ячейки стеллажа состоит из номера стеллажа, номера ячейки по длине стеллажа и номера яруса.
Для поиска ячейки в стеллажах автоматическим краном-штабелером используют следующие методы:
-позиционный - грузозахват устанавливают датчиком, расположенным у данной ячейки, при воздействии на него элемента грузозахвата;
-позиционно - кодовый - грузозахват в данной позиции устанавливают по особому коду, отличному от кодов других ячеек;
-счетный (наиболее распространенный) -грузозахват в заданной позиции устанавливают по отсчету числа позиций, которые прошел кран и захват в сравнении с заданным числом.
Точность установки автоматического крана-штабелера + 4мм. Автоматизированная система управления (АСУ) позволяет решать сле-
дующие задачи:
по планированию - поступление продукции от поставщиков; отгрузка продукции потребителям;
по учету - поступление продукции и тары; реализация продукции и тары; остаток продукции; денежные расчеты с поставщиками и потребителями;
по контролю - выполнение плана поставки продукции поставщиками и отгрузка потребителям;
по управлению складскими процессами - определение адреса размещения продукции; определение места хранения продукции;
по управлению запасами - выявление дефицитной, сверхнормативной и излишней продукции; установление норм запаса продукции;
по отчетности - поставка продукции; остатки продукции.
Автоматизированная система управления складскими процессами дает возможность комплексно и ритмично организовать процесс снабжения, снизить совокупный запас продукции в районе деятельности базы или склада, ускорить оборачиваемость материальных ресурсов, снизить издержки обращения и т.д.

Тема 13. Комплексная механизация ПРТС работ.
1.Бестарной перевозки грузов
2.Механизация погрузочно-разгрузочных, транспортных и складских работ на предприятиях, разливают пищевые жидкости
3.Механизация ПРТС работ с продукцией предприятий хлебопекарной промышленности;
4.Механизация ПРТС работ по затаренных грузами в различных отраслях пищевой промышленности.
1.Бестарные перевозки грузов
Вгруппу бестарно перевозимых и хранимых грузов входят мука, зерно, са-
хар, овощи, соль, молочные продукты, вино, пиво и т.п. Наибольший объем бестарных перевозок приходится на долю муки.
Бестарные перевозки и хранения муки. Перевозка муки россыпью осуществляется в основном автомобильным транспортом (реже железнодорожным) с мелькомбинатов на хлебопекарные и кондитерские предприятия, расположенные в радиусе до 200 км от мелькомбината.
Как на мелькомбинате, так и на хлебозаводе для внутрипроизводственного перемещения муки имеются аэрозольтранспортные установки При горизонтальном транспортировании муки применяются скребковые и аэрогравитационные конвейеры.
Устройства для хранения муки различны. На мелькомбинатах, где запасы рассчитывают на размещение 6-8 суточного запаса, строят железобетонные силосы квадратного сечения 3x3 м, высотой до 15 м. При меньших запасах строят силосы круглыми металлическими диаметром 2..2,5 м высотой до 20 м. Стальные силосы в 1,5...2 раза дешевле, чем железобетонные. Следует отметить, что хранение муки в стальных силосах, особенно при низких температурах, требует дополнительных исследований.
Рис.73. Схема движения муки при бестарной доставке от мелькомбината до хлебозавода:
1 - контрольный рассев; 2- энтолейтор; 3 - автоматические весы; 4 - магнитное заграждение; 5 - питатель аэрозолътранспортной линии; 6 - силосы на мелькомбинате; 7 - разгрузители винтовые; 8 - конвейеры (аэрожелоба); 9 - автомуковозы; 10 - силосы на хлебозаводе; 11 - разгрузитель с фильтром; 12 - автовесы; 13