
Vladimirov_S.V._Mehanizats._pogruz.-razgruz.,_transport._i_sklad._rabot2010
.pdf
где А – амплитуда колебаний, см;
R – радиус коромысла, принимае-мый из условия оптимального размещения верхнего и нижнего грузонесущего элемента, см.
Углы закручивания, как центрального шарнира, так и крайних шарниров (верхнего и нижнего) в течение каждого периода колебаний равны между собой и составляют ±ρ.
Максимальная нагрузка на верхний или нижний шарнир от веса труб (желобов) и транспортируемого груза определяется для наиболее нагруженных шарниров, расположенных непосредственно у привода:
Pв Pн |
GT Gгр |
Gn ,кгс |
|
2nk |
|
||
|
4 |
(9.44) |
|
|
|
|
где GТ – собственный вес трубы со всеми присоединенными к ней деталями, кг;
Gгр – вес груза, транспортируемого в одной трубе, кг;
Gгр |
QL |
|
2 3,6 |
(9.45) |
Gп – вес привода, приходящийся на одну трубу, кг;
nк – количество опорных узлов на конвейере, каждый из которых имеет два коромысла.
Максимальная нагрузка на средний шарнир:
PC 2Pв |
Gкор |
,кг |
2nk |
||
|
|
(9.46) |
Gкор – вес опорных узлов коромысел и рессор.
Неучтенные нагрузки на шарниры оцениваются в расчетах путем снижения принимаемых допускаемых напряжений.
Расчет шарнира на кручение. При повороте на угол φ резина втулки шарниров скручивается. При этом максимальные напряжения сдвига при кручении будут возникать на внутренней поверхности крепления резины тех шарниров, которые имеют меньшие размеры.
Таким образом, проверке на сдвиг при кручении подлежат верхний и нижний шарниры:
|
2 |
Gr 2 |
|
|
max |
|
р 1 |
, кгс / см2 |
(9.47) |
r 2 |
r 2 |
|||
1 |
2 |
|
|
Из условия прочности τmax < [τ],
где φр – угол закручивания резины, в радианах;
r1 и r2 – соответственно наружный и внутренний радиусы втулки

шарнира, см (рис. 9.17); [τ] – допускаемое напряжение сдвига, кгс/см2 (см. табл. 9.8);
G – динамический модуль сдвига для шарниров (см. табл. 9.9).
Таблица 9.8. Допускаемые напряжения для резины, используемой для изготовления шарниров вибрационных конвейеров.
|
Допускаемое напряжение при дли- |
|
Вид деформации |
тельной динамической нагрузке, |
|
|
кг/см2 |
|
РАСТЯЖЕНИЕ |
5…10 |
|
Сжатие |
10…15 |
|
ПАРАЛЛЕЛЬНЫЙ |
3…5 |
|
СДВИГ |
||
|
||
Кручение |
3…5 |
Расчет шарнира на радиальную нагрузку. Под действием радиальной нагрузки на шарнир в резине втулки возникает сложное напряженное состояние, сочетающее в себе напряжения сдвига, сжатия и растяжения (см. рис. 9.18).
При действии на шарниры расчетных нагрузок, определяемых по формулам (9.46) и (9.47) радиальная деформация втулки будет определяться выражением:
|
Pln |
r1 |
|
|
|
|
|
||
|
|
|
|
|
|
||||
y0 |
|
|
r |
|
|
|
|
,см |
(9.48) |
|
2 |
|
|
|
|||||
|
|
|
|
|
|
|
|||
|
|
ф |
|
|
|
|
|
|
|
|
1,66E K |
|
|
2,53G |
|
l |
|
|
где Р – расчетная нагрузка на рассматриваемый шарнир;
Р=Рв=Рн или Р=Рс; l – длина шарнира, см (см. табл. 9.7);
Е′=6,5G, кг/см2 – модуль упругости при сжатии резины, привулканизированной к стальной арматуре. Значение G – по табл. 9.9.
η – коэффициент нелинейности, η ≈1,0; Кф – коэффициент формы:
Kф 1 4,67 |
|
|
|
r l |
|
|
|
|
|
|
2 |
|
|
|
|||
|
2r2 |
l r1 |
r2 |
|
||||
Условное напряжение сжатия: |
|
|
r1 r2 |
y0 |
|
|||
сж.усл. E K |
ф |
, |
||||||
r1 |
r2 y0 2 |
По результатам расчета необходимо обеспечить:
σсж усл ≤ [σсж]
кг
см2
(9.49)
(9.50)
(9.51)
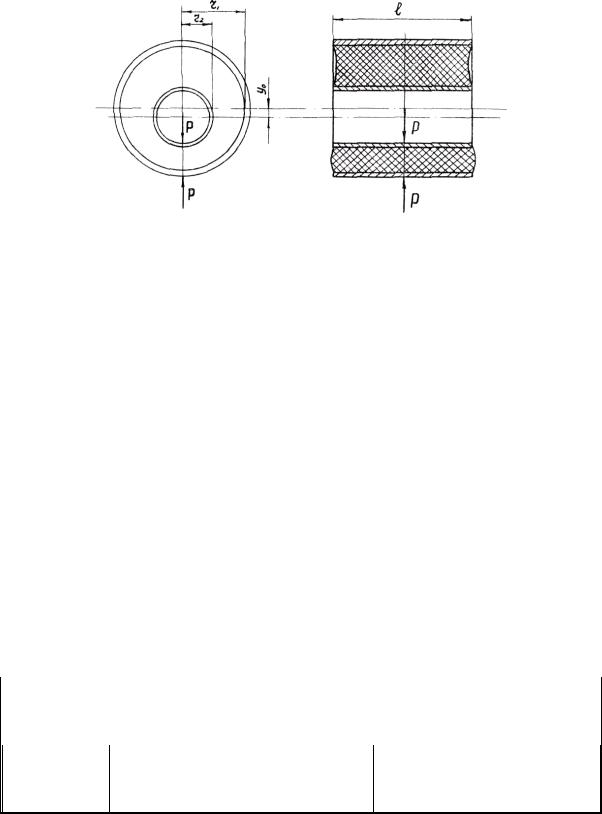
Рисунок 9.18. Схема для расчета резинометаллического шарнира на сжатие
Напряжения сдвига при радиальном сжатии:
|
|
y0 |
, |
кг |
(9.52) |
|
r1 |
r2 |
см2 |
||||
|
|
|
При этом должно быть обеспечено условие τmax ≤ [τ]. Значения допускаемых напряжений приведены в табл. 9.8.
Резиновая смесь, используемая при изготовлении шарниров, имеет, как правило, следующую характеристику:
твердость по Шору – 45…60 ед.;
предел прочности при разрыве – 160 кг/см2;
относительное удлинение при разрыве – 500%.
Коэффициенты угловой жесткости резинометаллических шарниров приведены в табл. 9.9.
Таблица 9.9. Динамические коэффициенты жесткости резинометаллических шарниров и расчетные динамические модули сдвига резины шарниров.
|
Тип |
Динамический коэффи- |
Динамический мо- |
|
циент угловой жесткости |
дуль сдвига резины шар- |
|
|
шарнира |
||
|
шарнира, Сугл, кг∙см/рад |
ниров, σ, кг/см2 |
|
|
1 |
2720 |
18,7 |
|
2 |
5332 |
14,0 |
|
3 |
16500 |
10,7 |
Коэффициенты жесткости системы. При резонансном режиме работы конвейера общий коэффициент жесткости упругих связей системы ∑С определяется произведением массы одной трубы со всеми находящимися на ней эле-
ментами m на квадрат круговой частоты колебаний ω2: |
|
||||||||||||||||||
|
1 |
|
|
1 |
|
|
∑С = mω2, кг/см, |
|
|
|
(9.53) |
||||||||
где m |
G |
|
G |
пр |
0,186 |
G |
кор |
|
|
G |
рес |
|
G |
|
, |
(9.54) |
|||
|
|
||||||||||||||||||
|
g |
T |
|
2 |
|
|
|
|
|
|
|
гр |
|
|
|||||
|
|
|
|
|
|
|
|
|
|
|
|
|
|
|
|
|

где GТ – вес трубы, кг; Gпр – вес привода, кг;
∑Gкор – суммарный вес коромысел (назначается ориентировочно); ∑Gрес – суммарный вес рессор (назначается ориентировочно);
Gгр – вес груза на одной трубе;
λ – расчетный коэффициент (см. рис. 9.10);
g=981 см/с2; 30n .
Для вибрационных конвейеров рассматриваемой конструкции общий коэффициент жесткости системы может быть представлен суммой следующих слагаемых:
∑С = С1+ С2+ С3 , кг/см |
(9.55) |
где С1 – коэффициент жесткости всех рессор (или резинометалличе-
ских
пакетов); С2 – коэффициент линейной жесткости всех верхних резинометалли-
ческих шарниров; С3 – коэффициент линейной жесткости полусуммы всех средних рези-
нометаллических шарниров.
Определение коэффициента жесткости всей системы отдельных её элементов производится в следующей последовательности:
1.Определяется ∑С по формуле.
2.По табл. 9.9 принимается динамический коэффициент угловой жесткости Сугл для ранее выбранных шарниров.
3.Определяется коэффициент линейной жесткости одного верхнего шарнира и одного среднего шарнира.
C2 |
C2 угл |
|
C3 |
C3 угл |
|
|
|
(9.56) |
R2 |
R2 |
|
|
|||||
|
|
|
|
|
||||
где R – радиус коромысла, см. |
|
|
|
|
|
|
||
4. Коэффициент жесткости элементов системы: |
|
|||||||
C2 C2 nш |
С3 |
С3 |
nш |
|
(9.57) |
|||
2 |
|
|||||||
|
|
|
|
|
|
|
|
|
С1 = (С– С2 – С)3 , кг/см |
(9.58) |
где nш – общее число шарниров коромысел на одном из уровней, т.е. верхних или средних, равное удвоенному числу пар коромысел.
По полученному значению коэффициента жесткости С1 производится выбор и проверка упругих связей конвейера, которые выполняются из рессор или резинометаллических пакетов.
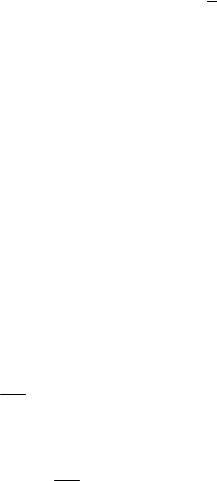
Стальные рессоры. Рессоры выполняются из высококачественной термически обработанной пружинной стали 55С2, 60С2, 60С2Н2А или из стеклопластика АГ-4С.
Рессоры аккумулируют кинетическую энергию колеблющихся масс, преобразовывая её в потенциальную энергию деформации при перемещении грузонесущего органа в одну сторону и снова в кинетическую при перемещении грузонесущего органа в другую сторону.
Расчетная схема и линия упругой деформации рессоры при крайнем положении шатуна эксцентрикового привода представлена на рис. 9.19.
Рессора рассчитывается на изгиб как консольная балка с вылетом: l0 2l , см
где l – длина незаделанной части рессоры, принимаемая по конструктивным соображениям соизмеряемой с удвоенным радиусом коромысел 2R.
Приближенно l ≈ (2R – 100).
Напряжение изгиба в месте заделки рессоры:
н |
P1l0 K зд |
, кг/см2 |
(9.59) |
|
|||
|
W |
|
где Кзд – коэффициент заделки рессоры (см. табл. 9.10); Р1 – сила, в результате действия которой рессора прогнется на
величину колебаний А.
Исходя из этой предпосылки (считая амплитуду А равной прогибу консольной балки), будем иметь:
P1 |
|
3AEJ |
откуда |
A |
Pl3 |
|
|
1 0 |
|||||
l03 |
3EJ |
|||||
|
|
|
|
где J bh123 (см. рис. 9.19, в).
Е= 2,1∙106 кг∙с/см2 – модуль упругости для стали;
Е= 3,0∙105 кг∙с/см2 – модуль упругости для стеклопластика;
W bh62 (см. рис. 9.19, в).
После подстановки и преобразований уравнение может быть представлено в виде:
И |
6 AEKзд h |
, кгс/см2 |
(9.60) |
|
l 2 |
|
|
где h – толщина рессоры, обычно h = 0,4…0,65 см; l – см. формулу (9.59);
Кзд – см. табл. 9.10.
Таблица 9.10. Коэффициент заделки рессор Кзд .
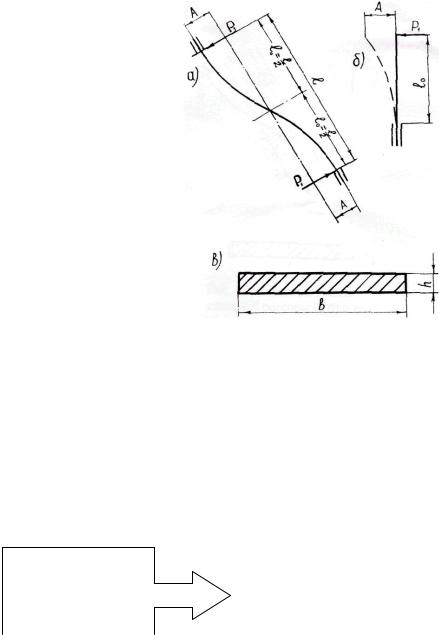
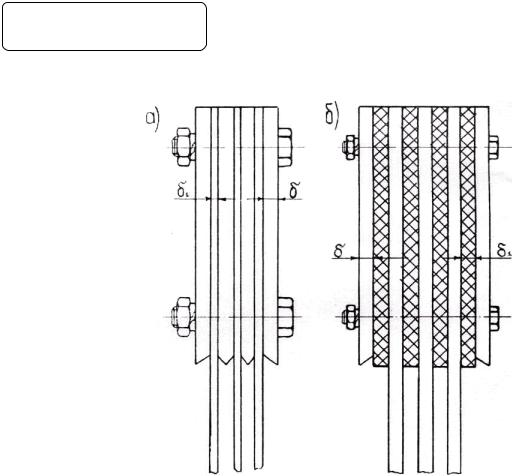
[σ]и = 1200 кг/см2
Стеклопластик АГ-4С: [σ]и = 800 кг/см2.
Рисунок 9.20. Схема крепления рессор конвейера:
а) стальные накладки и стальные прокладки со скосами δ=6 мм,
δ1=3 мм;
б) стальные накладки со скосами и резиновые прокладки δ=6 мм,
δ1=6 мм.
Коэффициент жесткости одной рессоры С1′ определяется по формуле:
C1 |
P1 |
|
K зд , |
кг с |
(9.61) |
||
A |
см |
|
|||||
|
|
|
|
||||
где Р1 и А – рассмотрены при анализе формулы (9.60). |
|
||||||
После преобразований: |
2EK здbh3 |
|
|
|
|||
С1 |
, |
кг с |
(9.62) |
||||
|
|
l 3 |
|
см |
|||
|
|
|
|
|
|
||
Необходимое количество рессор: |
C1 |
|
|
|
|
|
|
np |
|
|
|
|
(9.62) |
||
|
C |
|
|
|
|
|
|
|
1 |
|
|
|
|
|
|
Количество пачек рессор выбирается из условия nпач ≤ 4nк,
где nк – количество опорных узлов на конвейре, каждый из которых имеет 2 коромысла, таким образом, с каждой стороны одного коромысла устанавливается по пакету рессор.
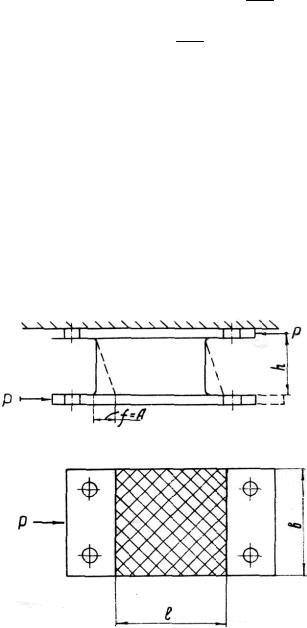
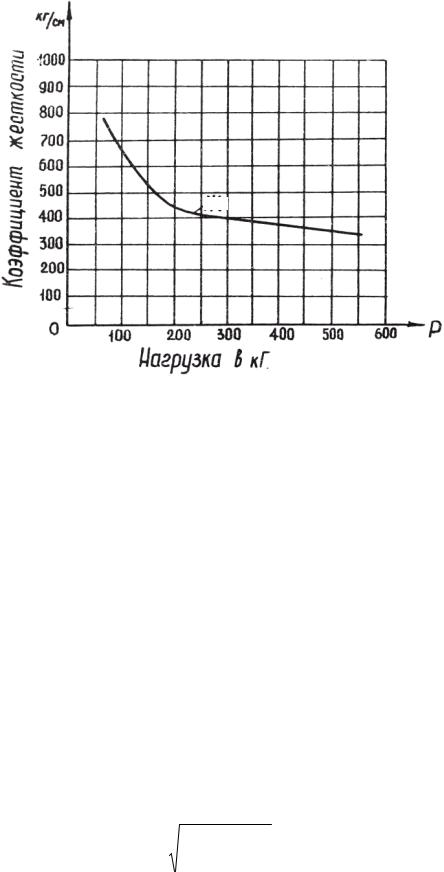
С
Рисунок 9.22. Экспериментальная зависимость коэффициента жесткости резинометаллического амортизатора от нагрузки.
При использовании резинометаллических пакетов-амортизаторов в расчет уравновешенного двухмассного конвейера вводятся изменения, вызванные заменой коромысел и рессор на резиновые амортизаторы.
Характер этих изменений показан на примере расчета конкретного конвейера, выполненного в конце данной главы для двух вариантов упругих связей.
Вариант 1: используются коромысла и рессоры. Вариант 2: используются резиновые амортизаторы.
Усилия в шатунах привода. Эксцентриковый привод двухмассных вибрационных конвейеров всегда имеет два шатуна. В приведенных ниже формулах дается общее усилие, действующее в двух шатунах. Для получения усилия в одном шатуне полученные по формулам нагрузки должны быть поделены пополам.
Максимальное возмущающее усилие в шатунах при установившемся режиме движения грузонесущих элементов конвейера определяется формулой:
P |
A C |
|
1 |
|
2 |
|
2 |
(9.65) |
|
2 |
|
||||||
ш |
|
|
|
|
|
0 |
|
|
|
|
|
|
0 |
|
|
|
где ∑С – общий коэффициент жесткости системы; ω и ω0 – соответственно, круговая частота вынужденных и собствен-
ных колебаний системы;0 – общий коэффициент сопротивлений от внутреннего трения в упру-
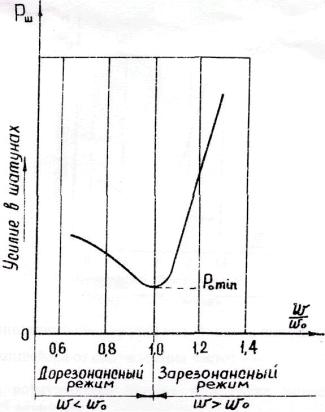