
- •Introduction to the Anchor Handling Course
- •Technical Specifications:
- •Winch Layout:
- •Power Settings / Bollard Pull
- •All operations on board must be performed in accordance with Company Procedures.
- •Risk Assessment
- •Planning
- •Planning:
- •Goal, example:
- •What to do:
- •Electrical winches
- •Winch operation
- •General Arrangement
- •A/H-Drum at full Capacity
- •Over speed
- •Water brake
- •Band brake
- •QUICK & Full Release
- •Hydraulic Winches
- •Lay out (B-type)
- •Hydraulic winch, “B-type”
- •TOWCON
- •Instruction for use of Wire Drums
- •Changing of Chain Wheels (Wildcats / Chain Lifter)
- •TRIPLEX - SHARK JAW SYSTEM.
- •Operation
- •Maintenance and inspections
- •Safety
- •2. OPERATION:
- •QUICK RELEASE:
- •EMERGENCY RELEASE:
- •CONTROL PANEL
- •Marks for Locked on Hinge Link
- •2.2- OPERATION OF THE "JAW IN POSITION ACCEPT" LEVER:
- •2.3 OPERATION OF THE CONTROL PANEL AT EMERGENCY POWER.
- •3. ELECTRIC AND HYDRAULIC POWER SYSTEM.
- •3. 1. ARRANGEMENT OF SYSTEM.
- •3.2. FUNCTIONING OF QUICK RELEASE - JAWS ONLY.
- •3.3. FUNCTIONING OF EMERGENCY RELEASE
- •4.2 Test without Load.
- •4.3 Test with Load.
- •5. General Maintenance
- •5.1 Accumulators Depressurising
- •5.2 Shark Jaw Unit
- •5.3 Guide Pins Units
- •5.4 Hydraulic System
- •5.5 Electric System
- •6. Control Measurements / Adjustments.
- •6.2 Adjustment of inductive proximity switches on lock cylinders.
- •6.3 Adjustment of Pressure Switches for Lock Pressure.
- •7. Test Program – Periodical Control
- •7.2 Checking List – Periodic Control Mechanical / Hydraulic.
- •7.3 Checking List – Periodic Control Electrical
- •7.4 Testing without Load – Yearly Testing.
- •7.5 Load Test – Emergency Release – 5 Year Control.
- •“Mark on line !”
- •“Double set of Jaws, Pins and Wire lifter”
- •View from the bridge.
- •“JAW READY FOR OPERATION”
- •“JAW LOCK POSITION ACCEPTED”
- •KARM FORK – SHARK JAW SYSTEM.
- •Wire and chain Stopper
- •Inserts for KARM FORK
- •Martensite:
- •Recommendations:
- •1. THE BASIC ELEMENTS OF STEEL WIRE ROPE
- •2. STEEL WIRE ROPE CONSTRUCTIONS
- •3. SPECIAL STEEL WIRE ROPES
- •4. USE OF STEEL WIRE ROPE
- •5. SELECTING THE RIGHT STEEL WIRE ROPE
- •6. ORDERING STEEL WIRE ROPE
- •7. STEEL WIRE ROPE TOLERANCES
- •8. HANDLING, INSPECTION AND INSTALLATION
- •9. INSPECTION AND MAINTENANCE
- •10. ELONGATION AND PRE-STRETCHING
- •11. OPERATING TEMPERATURES
- •12. MARTENSITE FORMATION
- •13. END TERMINATIONS
- •14. SOCKETING (WIRELOCK)
- •15. DRUM CAPACITY
- •16. CLASSIFICATION AND USE OF STEEL WIRE ROPE
- •17. ROPES
- •18. CHAINS AND LIFTING COMPONENTS
- •19. TECHNICAL CONVERSION TABLES
- •SWIVEL
- •MoorLink Swivel
- •Pin Extractor
- •Socket Bench
- •Chains and Fittings
- •STUD LINK MOORING CHAIN
- •OPEN LINK MOORING CHAIN
- •KENTER JOINING LINKS
- •PEAR SHAPE ANCHOR CONNECTING LINK
- •DETACHABLE CONNECTING LINK
- •D’ TYPE JOINING SHACKLES
- •‘D’ TYPE ANCHOR SHACKLES
- •SHACKLES
- •JAW & JAW SWIVELS
- •BOW & EYE SWIVELS
- •MOORING RINGS
- •FISH PLATES
- •PELICAN HOOKS
- •SLIP HOOKS
- •‘J’ CHASERS
- •PERMANENT CHASERS
- •DETACHABLE PERMANENT CHAIN CHASERS
- •PERMANENT WIRE CHASERS
- •‘J’ LOCK CHAIN CHASERS
- •The way to break the anchor loose of the bottom is therefore:
- •Table of contents
- •Introduction
- •General
- •Mooring systems
- •Mooring components
- •History of drag embedment anchors
- •Characteristics of anchor types
- •History of vryhof anchor designs
- •Criteria for anchor holding capacity
- •Theory
- •Criteria for good anchor design
- •Aspects of soil mechanics in anchor design
- •Soil classification
- •Fluke/shank angle
- •Fluke area
- •Strength of an anchor design
- •Anchor loads and safety factors
- •Anchor behaviour in the soil
- •Proof loads for high holding power anchors
- •Anchor tests
- •Soil table
- •Practice
- •Introduction
- •Soil survey
- •Pile or anchor
- •Setting the fluke/shank angle
- •Connecting a swivel to the Stevpris anchor
- •Chasers
- •Chaser types
- •Stevpris installation
- •Laying anchors
- •Retrieving anchors
- •Anchor orientation
- •Decking the Stevpris anchor
- •What not to do!
- •Racking the Stevpris
- •Deploying Stevpris from the anchor rack
- •Boarding the anchor in deep water
- •Ballast In fluke
- •Chaser equilibrium
- •Deployment for permanent moorings
- •Piggy-backing
- •Piggy-back methods
- •Stevmanta VLA installation
- •Installation procedure
- •Stevmanta retrieval
- •Double line installation procedure
- •Stevmanta retrieval
- •Double line installation with Stevtensioner
- •The Stevtensioner
- •The working principle of the tensioner
- •Measurement of the tensions applied
- •Umbilical cable and measuring pin
- •Break - link
- •Duration of pretensioning anchors and piles
- •Handling the Stevtensioner
- •General tensioning procedures
- •Hook-up
- •Lowering
- •Tensioning mode
- •Retrieving
- •Supply vessels/anchor handling vessels
- •Product data
- •Introduction
- •Dimensions of vryhof anchor types
- •Proof load test for HHP anchors (US units)
- •Dimensions of vryhof tensioners
- •Proof load/break load of chains (in US units)
- •Chain components and forerunners
- •Connecting links
- •Conversion table
- •Mooring line catenary
- •Mooring line holding capacity
- •Shackles
- •Wire Rope
- •Wire rope sockets
- •Thimbles
- •Synthetic ropes
- •Mooring hawsers
- •Main dimensions chasers
- •Stevin Mk3 UHC chart
- •Stevin Mk3 drag and penetration chart
- •Stevpris Mk5 UHC chart
- •Stevpris Mk5 drag and penetration chart
- •Stevmanta VLA UPC chart
- •Introduction
- •Propulsion system
- •Propellers
- •Thrusters
- •Rudders
- •Manoeuvring
- •Current
- •Wind
- •Other forces
- •Turning point (Pivot point)
- •Ship handling
- •General layout Jack-Up drilling unit:
- •General information about a Semi Submersible drilling unit:
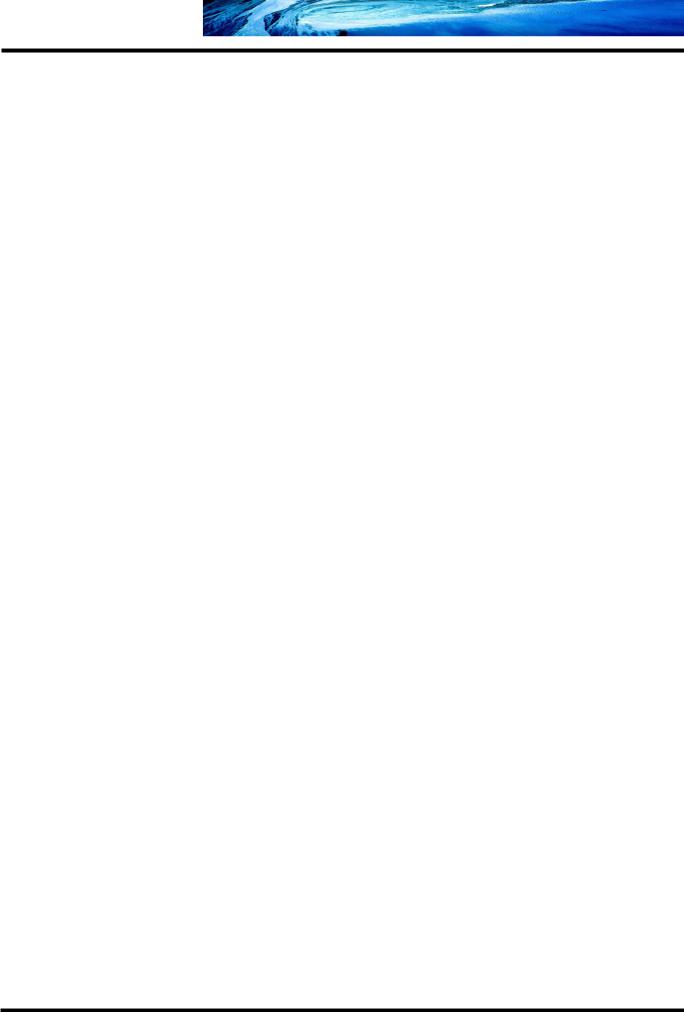
MTC
Anchor Handling Course
Propellers
A propeller can be a fixed propeller, which mean that the propeller blades are fixed, which again mean that changing from ahead and astern can only be done by stopping the rotation and then rotate the propeller the opposite way.
In our business we use propellers with variable pitch, where the propeller blades can turn, changing the pitch. From neutral where the propeller is rotating but without moving any water, to full pitch ahead or astern.
The variable pitch propeller will always rotate and can very fast go from full ahead to full astern.
If we look at the propeller seen from the aft and the propeller rotate clockwise when sailing ahead we call it a right-handed propeller and left-handed if rotating anti clockwise.
When the propeller rotate and special when we do not make any headway water flow to the propeller are less compared to when making headway. The water pressure on the top blades is lower compared with the blades in their lower position.
The lower blades will therefore have a better grip, and a right-handed propeller going ahead will push the stern towards starboard (ship’s heading turning port).
With a variable pitch propeller the propeller is always turning the same way and the movement of the stern will always be to port (rotation clockwise) whether we are going ahead or astern.
If we place the propeller inside a nozzle we eliminate this force and direct the water flow from the propeller in one direction.
The direction of the trust is determined by the direction of the water flow and by the direction the water flow pass the rudder.
Thrusters
Thrusters are propellers placed inside a tunnel in the ship or outside as an azimuth thruster.
The tunnel thruster can push the ship in two directions whereas the azimuth thruster can rotate and apply force in all 360°.
Most thrusters are constructed with an electrical motor inside the ship with a vertical shaft down to a gear in the thruster, which again rotate the propeller blades.
All thrusters do have variable pitch propellers.
Be aware of that your azimuth thruster can give full thrust in one direction and 15 -20 % less thrust in the opposite direction (because of the big gearbox).
And also remember that high speed through the water can empty the tunnel from water, and overheat the gear, if used.
Turbulence and air in the water can during powerful astern manoeuvre also result in air in the stern thruster.
M:\ANCHOR HANDLING\Course Material\Training Manual New\Chapter 14\Ship Handling Manoeuvring.doc
Chapter 14 |
Page 2 |
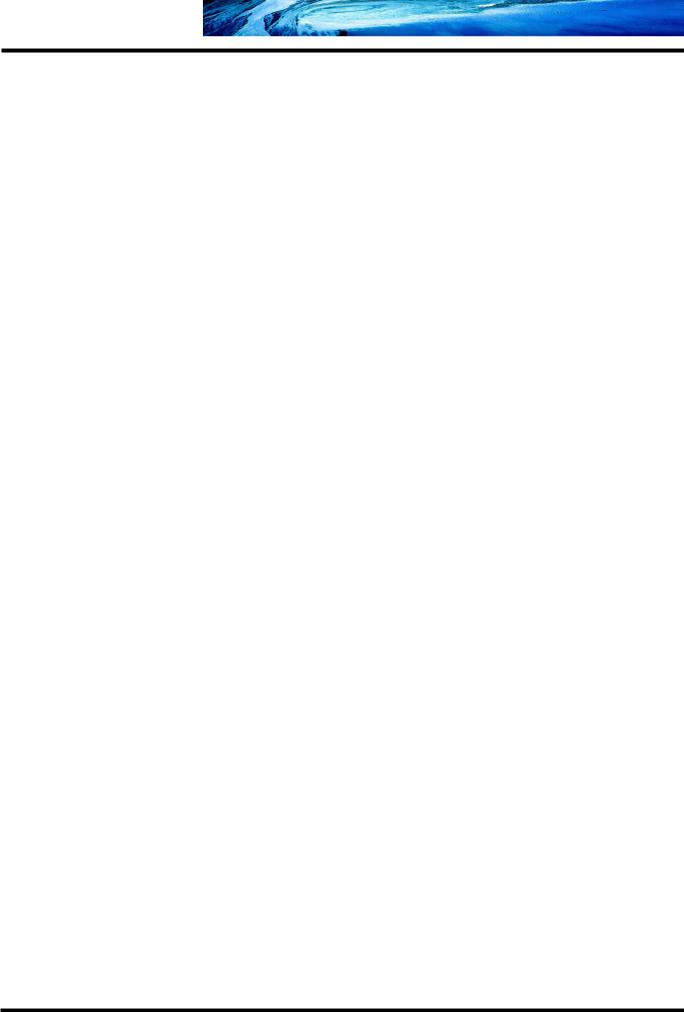
MTC
Anchor Handling Course
Rudders
The rudder is a passive steering system, which only can work if water is passing the rudder. The rudder is constructed like a wing on a plane, wide in the front and slim aft.
When turning the rudder the flow of water will on the backside create a low pressure and on the front a high pressure.
The low pressure or suction creates 75% of the turning force, whereas the high-pressure side only 25%.
That is why a traditional rudder looses steering moment when turned more than 40-50 degrees.
With high angles there will be turbulence on the backside killing the suction force.
The Becker rudder is constructed as a normal rudder, but with an extra small rudder flap on the edge. This flap turn twice the angle of the rudder, and the water on the high-pressure side will be directed more or less side wards creating big side wards thrust.
The Schilling rudder has a rotating cylinder built into the front of the rudder, rotating in a direction moving water towards the backside of the rudder.
A Shiller rudder can therefore turn up to 70 degree.
The Jastram rudder is an asymmetric constructed rudder designed special for the particular ship and propeller, and can also turn up to 70 degree.
If water do not pass the rudder, the rudder do not have any affect, which many navigators know from their experience with variable pitch propellers.
When the pitch is placed in neutral the rotating propeller stops the water flow, and the rudder can not be used.
When the propellers are going astern, the water passing the rudder is poor, and the effect from the rudder is very low.
But with a high speed astern the rudder will help, as there will be water passing the rudder.
M:\ANCHOR HANDLING\Course Material\Training Manual New\Chapter 14\Ship Handling Manoeuvring.doc
Chapter 14 |
Page 3 |
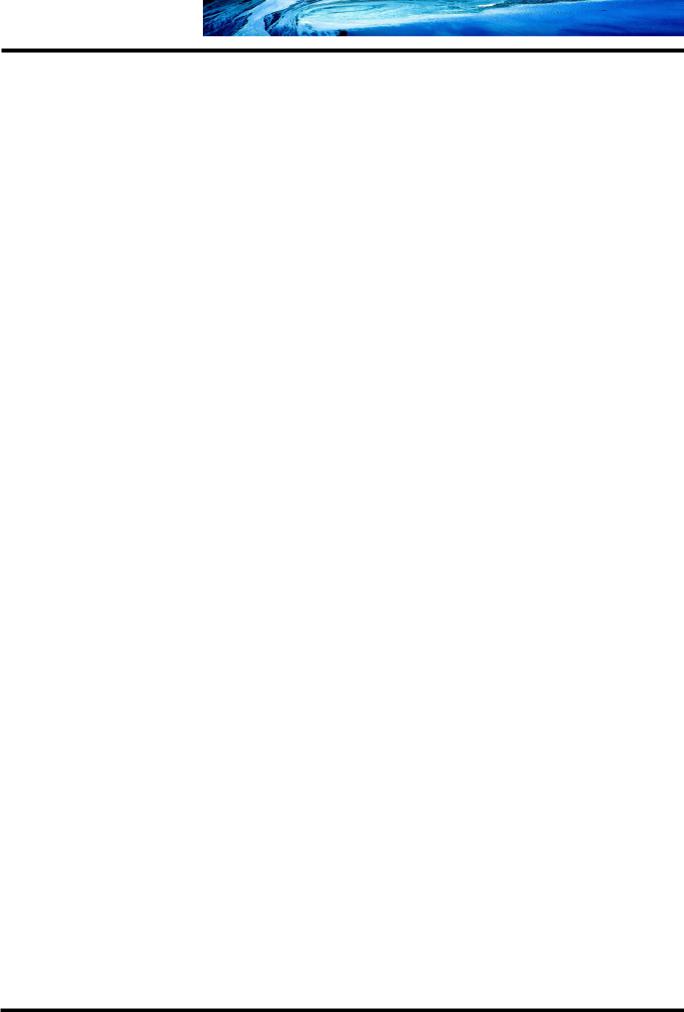
MTC
Anchor Handling Course
Manoeuvring
When talking about manoeuvring our ship, we need to look at how the ship is responding to different forces, and what happen when we apply forces as well.
A ship lying still in the water is exposed to forces from the current and wind. Swell and waves do not move the ship, but close to an offshore installation, swell and waves can push us into or away from the installation.
Current
The current moves the water we sail in and the ship will be set in the same direction and with the same speed as well.
We can calculate the force depending on the angle the current attacking the ship, where current abeam can be very high, special with water depth lower than twice the draft.
Turning a ship (80m long draft 8 meter) on a river with 2 knots current and water depth of 12 meter will when the ship is across the river give a force of 60 tons. If we have a lot of water below the keel the force will be 21 tons in above example, but when the water depth are lower the force will increase rapidly, and with only 2 meter below the keel the force will be 78 tons; a significant force.
Wind
We can do the same calculation with the wind, but the force from the wind moving the supply ship is not a considerable force, where big containerships, car-carriers, bulkers and tankers in ballast have to do their wind calculations.
The problem with wind in our business is the turning moment created by the wind.
With our big wind area in the front of the ship and none in the aft, the ship will turn up in the wind or away from the wind, depending on the shape of the hull and accommodation and the direction of the wind.
We can however use the force from the current and wind in an active way. Instead of fighting against the force, turn the ship and use the current or wind to keep you steady in a position or on a steady heading.
When operating close to FPSO, drill ships or other installations with a big underwater shape or hull, this can result in different forces and direction of the current and wind compared to observations done just 10 meters away.
Other forces
Forces between two ships passing each other can also be a considerable affect special if the speed is high. In front of a ship steaming ahead there is an overpressure, and along the sides a low pressure.
If a big ship pass us this pressure system can move or turn our ship, and if the big ship do have a high speed (30 knots) you can feel that effect up to ½ mile away.
M:\ANCHOR HANDLING\Course Material\Training Manual New\Chapter 14\Ship Handling Manoeuvring.doc
Chapter 14 |
Page 4 |
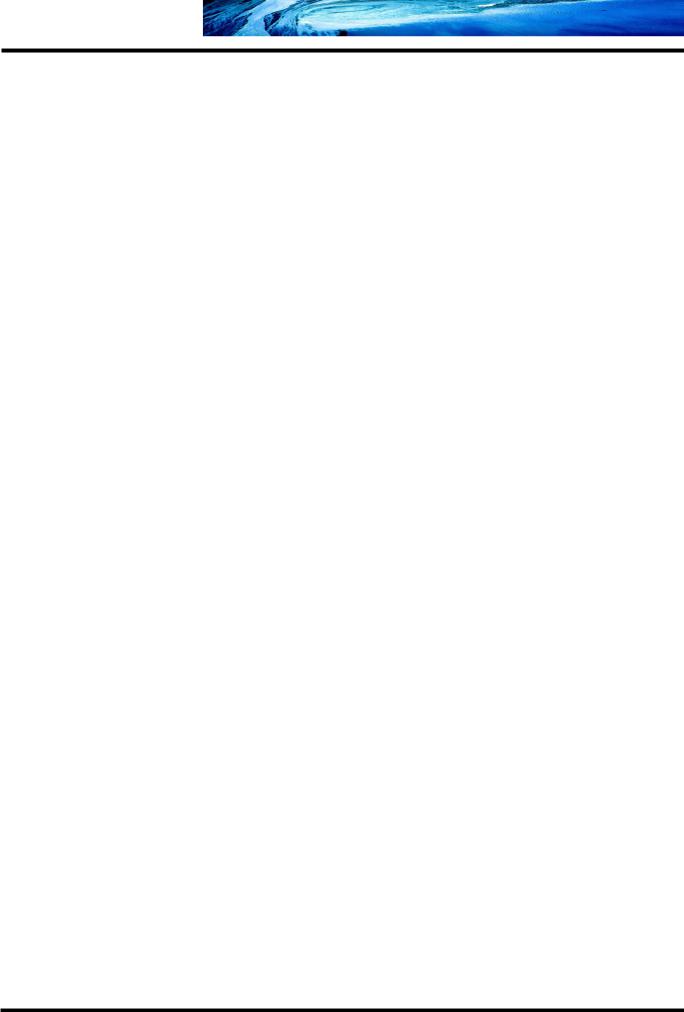
MTC
Anchor Handling Course
Turning point (Pivot point)
When a ship is stopped in the water and we use our thrusters to turn the ship, it will normally turn around the Centre of the ship, depending on the underwater shape of the hull.
When sailing this point will move ahead and the ship will turn around the Pivot point now approximately 1/3 to 1/6 from the front.
Our bow thruster will therefore loose some of the turning moment as it must now move the hole ship in the desired direction, whereas the stern thruster, and also the rudders, do have a long arm and thereby giving a big turning moment of the stern of the ship.
It will be the opposite when going astern, the pivot point moving aft and in this case our bow thruster having a long arm and a very big moment.
The Pivot point must not be confused with the turning point we can choose on our Joystick; this is a computer-calculated turning point. But think about it, when you next time have chosen turning point aft and you are sailing ahead with 5 knots and the ship seems reluctant in retrieving a high turning rate.
Forces from cable lying, wire/chain from tow and anchor handling, special if there is a big force in the system, will also have a significant effect on our ship. Some times it can be very difficult to turn a ship as the Pivot point can move outside the ship.
As the pull from these systems mostly is very big, we need to use high engine/thruster power to obtain the desired movement.
Ship handling
With a basis knowledge of the different forces acting on our ship. Special whether it is a big or a small force, knowledge of how our propellers, rudders and thrusters are working and how the ship react on above, we can gain a better and quicker experience in ship handling of the particular ship we are on right now.
You will see experienced navigators using split-rudder, where one rudder have one angle and the other rudder having another angle. Going for and back on the engine you can control the aft end of the shipside wards without moving ahead or astern. But again other navigators will get the same result by using the rudders in parallel drive and turn the rudders from side to side, and still use the engine to control the movement side wards and ahead or astern.
The best way is like mentioned in the beginning of this chapter, to practice manoeuvring of your particular ship, using the information mentioned in this chapter.
M:\ANCHOR HANDLING\Course Material\Training Manual New\Chapter 14\Ship Handling Manoeuvring.doc
Chapter 14 |
Page 5 |