
- •Introduction to the Anchor Handling Course
- •Technical Specifications:
- •Winch Layout:
- •Power Settings / Bollard Pull
- •All operations on board must be performed in accordance with Company Procedures.
- •Risk Assessment
- •Planning
- •Planning:
- •Goal, example:
- •What to do:
- •Electrical winches
- •Winch operation
- •General Arrangement
- •A/H-Drum at full Capacity
- •Over speed
- •Water brake
- •Band brake
- •QUICK & Full Release
- •Hydraulic Winches
- •Lay out (B-type)
- •Hydraulic winch, “B-type”
- •TOWCON
- •Instruction for use of Wire Drums
- •Changing of Chain Wheels (Wildcats / Chain Lifter)
- •TRIPLEX - SHARK JAW SYSTEM.
- •Operation
- •Maintenance and inspections
- •Safety
- •2. OPERATION:
- •QUICK RELEASE:
- •EMERGENCY RELEASE:
- •CONTROL PANEL
- •Marks for Locked on Hinge Link
- •2.2- OPERATION OF THE "JAW IN POSITION ACCEPT" LEVER:
- •2.3 OPERATION OF THE CONTROL PANEL AT EMERGENCY POWER.
- •3. ELECTRIC AND HYDRAULIC POWER SYSTEM.
- •3. 1. ARRANGEMENT OF SYSTEM.
- •3.2. FUNCTIONING OF QUICK RELEASE - JAWS ONLY.
- •3.3. FUNCTIONING OF EMERGENCY RELEASE
- •4.2 Test without Load.
- •4.3 Test with Load.
- •5. General Maintenance
- •5.1 Accumulators Depressurising
- •5.2 Shark Jaw Unit
- •5.3 Guide Pins Units
- •5.4 Hydraulic System
- •5.5 Electric System
- •6. Control Measurements / Adjustments.
- •6.2 Adjustment of inductive proximity switches on lock cylinders.
- •6.3 Adjustment of Pressure Switches for Lock Pressure.
- •7. Test Program – Periodical Control
- •7.2 Checking List – Periodic Control Mechanical / Hydraulic.
- •7.3 Checking List – Periodic Control Electrical
- •7.4 Testing without Load – Yearly Testing.
- •7.5 Load Test – Emergency Release – 5 Year Control.
- •“Mark on line !”
- •“Double set of Jaws, Pins and Wire lifter”
- •View from the bridge.
- •“JAW READY FOR OPERATION”
- •“JAW LOCK POSITION ACCEPTED”
- •KARM FORK – SHARK JAW SYSTEM.
- •Wire and chain Stopper
- •Inserts for KARM FORK
- •Martensite:
- •Recommendations:
- •1. THE BASIC ELEMENTS OF STEEL WIRE ROPE
- •2. STEEL WIRE ROPE CONSTRUCTIONS
- •3. SPECIAL STEEL WIRE ROPES
- •4. USE OF STEEL WIRE ROPE
- •5. SELECTING THE RIGHT STEEL WIRE ROPE
- •6. ORDERING STEEL WIRE ROPE
- •7. STEEL WIRE ROPE TOLERANCES
- •8. HANDLING, INSPECTION AND INSTALLATION
- •9. INSPECTION AND MAINTENANCE
- •10. ELONGATION AND PRE-STRETCHING
- •11. OPERATING TEMPERATURES
- •12. MARTENSITE FORMATION
- •13. END TERMINATIONS
- •14. SOCKETING (WIRELOCK)
- •15. DRUM CAPACITY
- •16. CLASSIFICATION AND USE OF STEEL WIRE ROPE
- •17. ROPES
- •18. CHAINS AND LIFTING COMPONENTS
- •19. TECHNICAL CONVERSION TABLES
- •SWIVEL
- •MoorLink Swivel
- •Pin Extractor
- •Socket Bench
- •Chains and Fittings
- •STUD LINK MOORING CHAIN
- •OPEN LINK MOORING CHAIN
- •KENTER JOINING LINKS
- •PEAR SHAPE ANCHOR CONNECTING LINK
- •DETACHABLE CONNECTING LINK
- •D’ TYPE JOINING SHACKLES
- •‘D’ TYPE ANCHOR SHACKLES
- •SHACKLES
- •JAW & JAW SWIVELS
- •BOW & EYE SWIVELS
- •MOORING RINGS
- •FISH PLATES
- •PELICAN HOOKS
- •SLIP HOOKS
- •‘J’ CHASERS
- •PERMANENT CHASERS
- •DETACHABLE PERMANENT CHAIN CHASERS
- •PERMANENT WIRE CHASERS
- •‘J’ LOCK CHAIN CHASERS
- •The way to break the anchor loose of the bottom is therefore:
- •Table of contents
- •Introduction
- •General
- •Mooring systems
- •Mooring components
- •History of drag embedment anchors
- •Characteristics of anchor types
- •History of vryhof anchor designs
- •Criteria for anchor holding capacity
- •Theory
- •Criteria for good anchor design
- •Aspects of soil mechanics in anchor design
- •Soil classification
- •Fluke/shank angle
- •Fluke area
- •Strength of an anchor design
- •Anchor loads and safety factors
- •Anchor behaviour in the soil
- •Proof loads for high holding power anchors
- •Anchor tests
- •Soil table
- •Practice
- •Introduction
- •Soil survey
- •Pile or anchor
- •Setting the fluke/shank angle
- •Connecting a swivel to the Stevpris anchor
- •Chasers
- •Chaser types
- •Stevpris installation
- •Laying anchors
- •Retrieving anchors
- •Anchor orientation
- •Decking the Stevpris anchor
- •What not to do!
- •Racking the Stevpris
- •Deploying Stevpris from the anchor rack
- •Boarding the anchor in deep water
- •Ballast In fluke
- •Chaser equilibrium
- •Deployment for permanent moorings
- •Piggy-backing
- •Piggy-back methods
- •Stevmanta VLA installation
- •Installation procedure
- •Stevmanta retrieval
- •Double line installation procedure
- •Stevmanta retrieval
- •Double line installation with Stevtensioner
- •The Stevtensioner
- •The working principle of the tensioner
- •Measurement of the tensions applied
- •Umbilical cable and measuring pin
- •Break - link
- •Duration of pretensioning anchors and piles
- •Handling the Stevtensioner
- •General tensioning procedures
- •Hook-up
- •Lowering
- •Tensioning mode
- •Retrieving
- •Supply vessels/anchor handling vessels
- •Product data
- •Introduction
- •Dimensions of vryhof anchor types
- •Proof load test for HHP anchors (US units)
- •Dimensions of vryhof tensioners
- •Proof load/break load of chains (in US units)
- •Chain components and forerunners
- •Connecting links
- •Conversion table
- •Mooring line catenary
- •Mooring line holding capacity
- •Shackles
- •Wire Rope
- •Wire rope sockets
- •Thimbles
- •Synthetic ropes
- •Mooring hawsers
- •Main dimensions chasers
- •Stevin Mk3 UHC chart
- •Stevin Mk3 drag and penetration chart
- •Stevpris Mk5 UHC chart
- •Stevpris Mk5 drag and penetration chart
- •Stevmanta VLA UPC chart
- •Introduction
- •Propulsion system
- •Propellers
- •Thrusters
- •Rudders
- •Manoeuvring
- •Current
- •Wind
- •Other forces
- •Turning point (Pivot point)
- •Ship handling
- •General layout Jack-Up drilling unit:
- •General information about a Semi Submersible drilling unit:
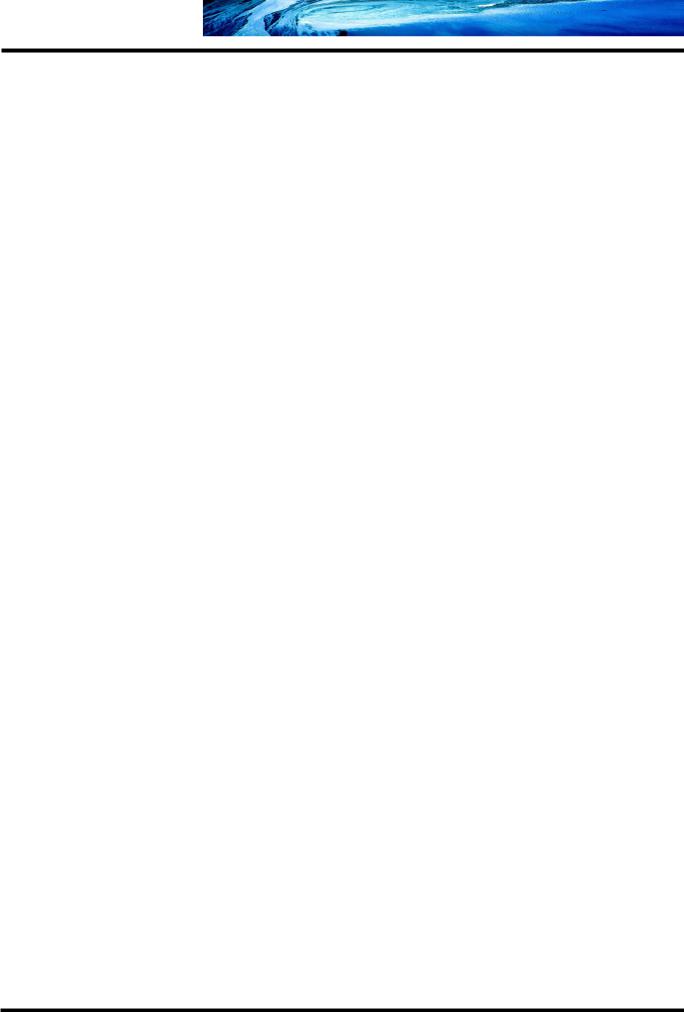
MTC
Anchor Handling Course
6.3Adjustment of Pressure Switches for Lock Pressure.
1.Adjust pressure to 115 bar.
Use horizontal adjusting screw on pump pressure compensatory valve.
2.Adjust pressure switch until green lamp on control panel comes on. Use alternative voltmeter and measure on cables for pressure switches.
7.Test Program – Periodical Control
Triplex Shark Jaw Type H-700
Triplex Guide Pins Type S-300
7.1The Triplex system is installed and used under rough conditions. Due to mechanical stress, vibrations and aggressive atmosphere and the equipment needs to be maintained carefully for safe operation.
A functional dry run test is recommended before every anchor handling operation.
The owner is responsible for all maintenance on the Triplex equipment. He must perform his own routines and schedules after the following guidelines.
7.2Checking List – Periodic Control Mechanical / Hydraulic.
Procedure for Personal Safety See Section 1; Have to be Followed!
Recommended Regularity: |
MONTHLY |
1.Dismantle manhole cowers on Shark Jaw and Guide Pins.
2.Check H.P. hoses, pipes and fittings. Poor H.P. hoses to be changed.
3.Check that all bolts are properly tightened.
4.Check that link joints are over centre when jaws are in locked position. See drawing B-2209.
5.Check wears on jaws, rollers and bearings. Repair and change where necessary.
6.Movement of bolts and link joints to be controlled under the function test. Look carefully for cracks and deformations.
7.Check sea water drain pipes from Shark Jaw and Guide Pins.
8.Check oil lever in hydraulic oil tank.
9.Starts pump and check that hydraulic pressure raise to max. working pressure (175 bar).
10.Check accumulator nitrogen pressure: 35 Bar.
It’s important first to empty the accumulators for oil by opening the ball valve on the power unit. Then connect gas-filling equipment according to accumulator precharging procedure.
M:\ANCHOR HANDLING\Course Material\Training Manual New\Chapter 06\1.0 TRIPLEX-Shark Jaws.doc
Chapter 06 |
Page 18 |
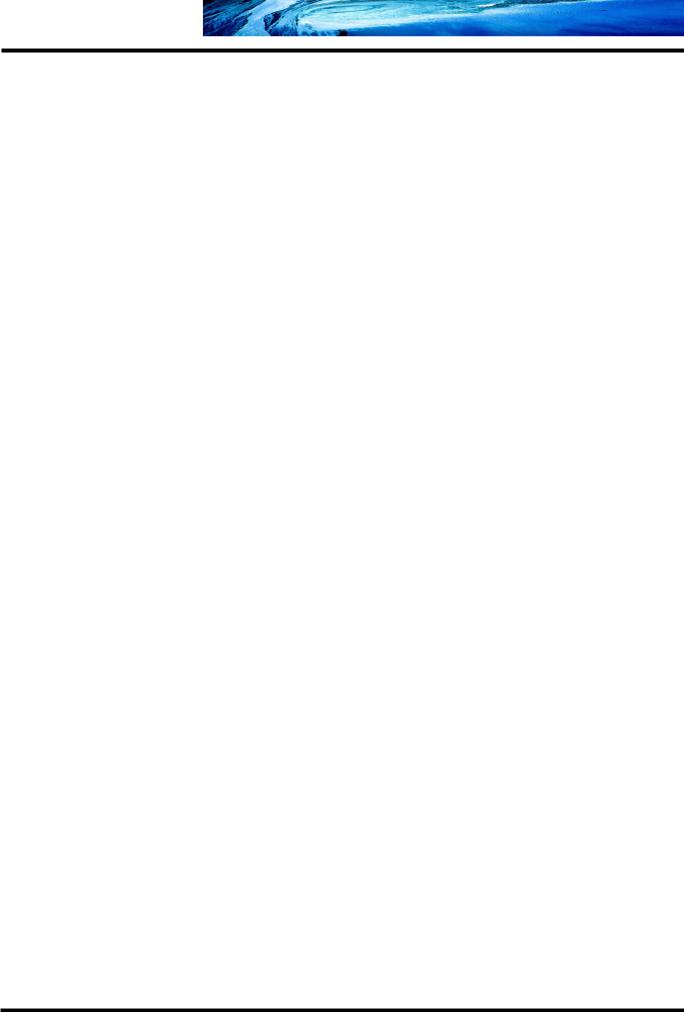
MTC
Anchor Handling Course
11.Auxiliary equipment as lubrication system to be checked according to the grease system manual. (LINCOLN)
12.Check that gaskets for manhole covers are in good condition.
13.Fit all manhole covers.
7.3Checking List – Periodic Control Electrical
Procedures for Personal Safety see Section 1. Have to be followed!
Recommended Regularity: |
MONTHLY |
1.Switch power off.
2.Perform Visual inspection for mechanical damage on:
-Junction boxes, control panels and cabinets.
-Cables.
-Indicators and switches.
-Electrical components mounted on the entire Triplex equipment / delivery.
3.Open every electrical cabinet, panel and boxes one by one, inspect for damage and heat exposure.
4.Control that all components are firm fastened, and relays are firm in their sockets.
5.Screw connections for every electrical termination to be carefully tightened.
6.Damages and other un-regularities must corrected immediately.
7.Power on, and perform complete functional test programs:
-Normal operation of all functions.
-Quick release.
-Emergency release.
8.Check emergency power (24 V) to junction box.
9.Remount all panels and doors / covers.
M:\ANCHOR HANDLING\Course Material\Training Manual New\Chapter 06\1.0 TRIPLEX-Shark Jaws.doc
Chapter 06 |
Page 19 |
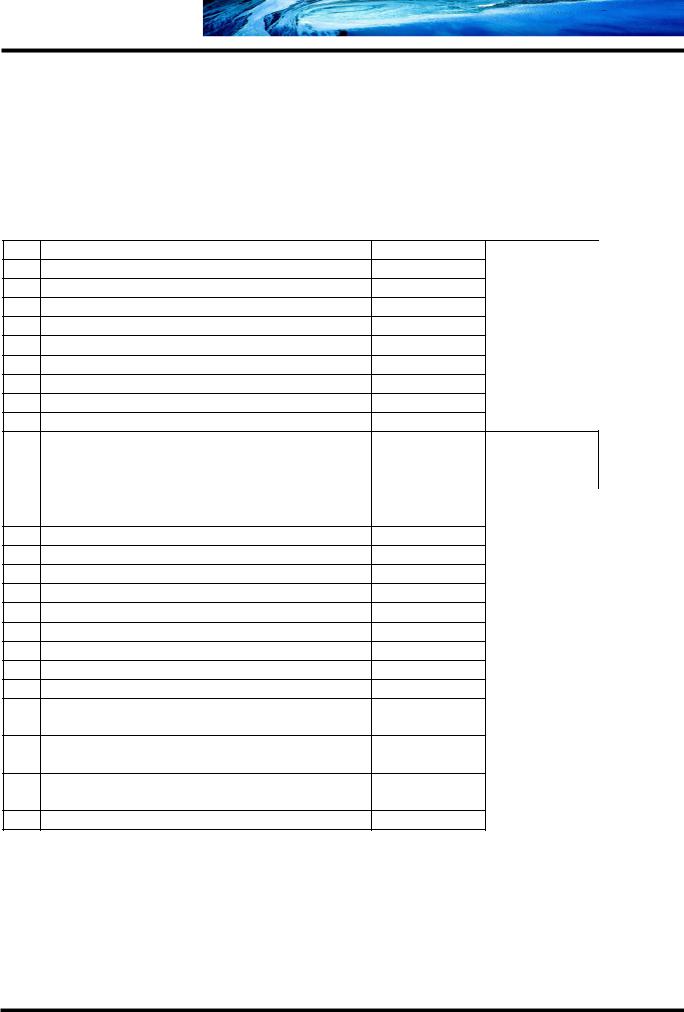
MTC
Anchor Handling Course
7.4 Testing without Load – Yearly Testing.
Checklist |
Control |
Motor/pump |
|
(Accept with OK) |
Panel Bridge |
starter |
|
1 |
Remote pump start |
|
- |
2 |
Remote pump stop |
|
- |
3 |
Local pump start |
- |
|
4 |
Local pump stop |
- |
|
5Pump lamp auto flicker
6Emergency stop
7Wire lift pin up
8Wire lift pin down
9Starboard jaw close
10Starboard jaw open
11Port jaw close
12Port jaw open
13Jaws close simultaneously
14Jaws open simultaneously
15 |
Alarm light jaws open |
|
JAW |
16 |
Lock pressure lights |
|
POSITION |
17 |
Jaw in position lights |
|
ACCEPTED |
18 |
Jaw in position accepted |
- |
|
19Jaws locked light
20Guide pins up
21Guide pins down
22Towing pins up
23Towing pins down
24Emergency release
25Quick release (Jaws only)
26Reset Quick release buttons
27Oil temperature high alarm light
28Oil level alarm light
29Emergency power supply junction box connection (193-194)
30Emergency power supply control panel bridge connection (77-78)
31Jaw in lock position marks in line check, starboard
32Jaw in lock position marks in line check, port
7.5 Load Test – Emergency Release – 5 Year Control.
Wire with required strength to be locked in the Shark Jaw. Make emergency release with a load of 90 tons on the wire (Jaws).
First test: |
With the pump running. |
Second test: |
With the pump stopped and accumulators fully loaded. |
M:\ANCHOR HANDLING\Course Material\Training Manual New\Chapter 06\1.0 TRIPLEX-Shark Jaws.doc
Chapter 06 |
Page 20 |
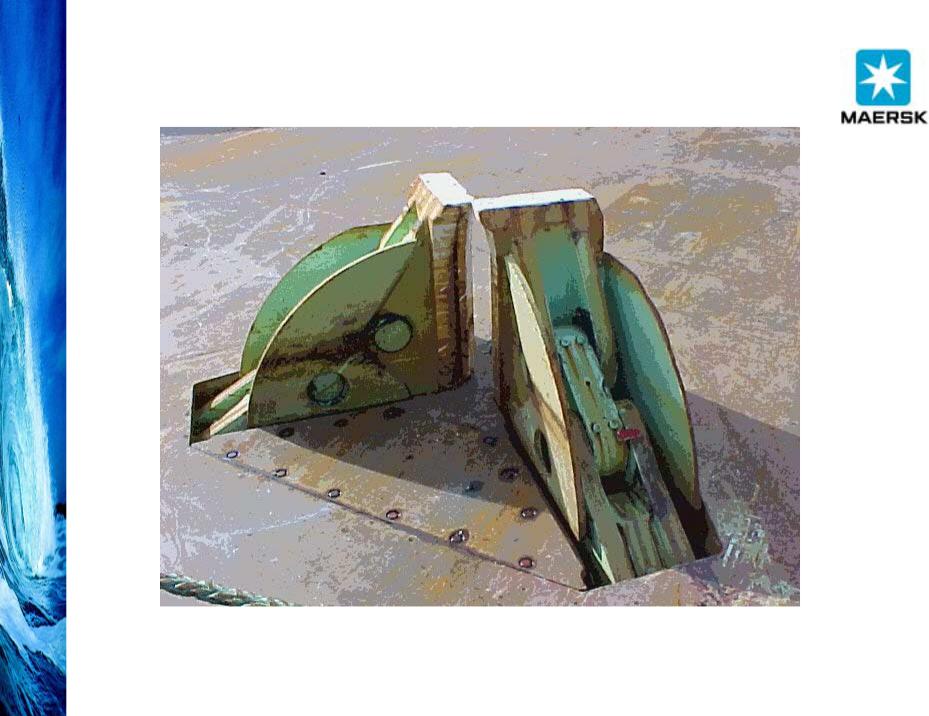
Maersk Training Centre A/S
“In closed / locked position” View from astern of Jaws.
Triplex Shark Jaw System
Anchor Handling Course, chapter 6