
Калин Физическое материаловедение Том 6 Част 2 2008
.pdf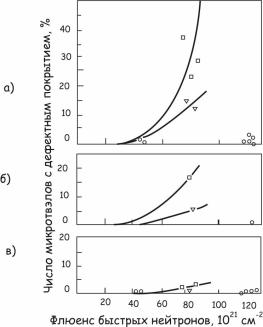
ного компонента является достаточной для компенсации анизотропного изменения размеров и объема высокоплотных мозаичной и слоистой составляющих (ОКСК = 1,05 1,35). Уменьшение содержания сажеподобного компонента снижает его пористость, но увеличивает долю МТ с дефектным покрытием при идентичных условиях облучения. В то же время, повышенное содержание сажеподобного компонента приводит к увеличению газопроницаемости, снижению характеристик и росту степени усадки материала.
Рис. 24.334. Зависимость доли микротвэлов с дефектным ПИУК-покрытием от условий облучения при следующих значениях плотности пироуглерода (г/см3) и Kа:
а – 1,75; 1,08; б – 1,76; 1,02; в – 1,85–1,95; 1,03; □, , ○ – температура в центре топливного стержня 1350, 1250, 1000 °С соответственно
Сравнивая свойства НТИ- и ВТИ-пироуглеродных покрытий МТ, следует отметить, что преимущества первых из них заключаются в лучшей размерной стабильности под облучением, более
541
низком уровне напряжений и меньшей загрязненности ураном и торием. В то же время слои ВТИ-пироуглерода, имеющие высокую плотность, лучше удерживают некоторые твердые ПД. Поэтому слои НТИ-пироуглерода предпочтительнее использовать ПИУКпокрытиях, которые содержат карбидный слой, являющиеся надежным диффузионным барьером для большинства твердых ПД. Слои ВТИ-пироуглерода являются более эффективными в ПИУпокрытиях.
Покрытия из карбида кремния. Карбид кремния (карборунд) SiС, бесцветные, а при наличии примесей – темно-серые, черные или зеленые кристаллы. Он известен в двух модификациях – и β.
-SiC имеет слоистую структуру с гексагональной (H) решеткой (пространственная группа Р63mc или P3ml, в ромбоэдрической (R) установке R3m); образует большое число политипов nН (или mR), где n – число слоев, повторяющихся по оси c в гексагональной ячейке политипа. Для гексагональной установки а = 0,3079 нм для всех политипов, кроме 2R, 4H, 6H, где а соответственно 0,3076, 0,3080, 0308065 нм; с ~ 0,2520 нм.
β-SiC имеет ГЦК решетку (а = 0,435 нм, пространственная группа F43m) и является метастабильным.
Выше 2100 °С происходит превращение β-SiC в -SiC. Обратный переход → наблюдается выше 1200 °С и давлении выше 3 ГПа.
Температура плавления 2830 °С. Плавление происходит инконгруэнтно с образованием графита и раствора углерода в кремнии.
Теплоемкость -SiC составляет 26,78 Дж/(моль∙К). Теплопроводность монокристаллов -SiC 490 Вт/(м∙К) при 300 К и 110 Вт/(м∙К) при 1000 K. Коэффициент линейного термического расширения при 250 – 2500 °С составляет 5,94∙10-6 1/К. Температура Дебая 1200 К.
Для -SiC модуль упругости равен 392 ГПа при 20 °С и 357 ГПа при 1200 °С, модуль сдвига 171 ГПа; модуль всестороннего сжатия 98 ГПа. Твердость по Кнупу при нагрузке 100 г для -SiC (грань
(001)) составляет 29,17 ГПа, а для β-SiC (грань (111)) – 28,15 ГПа.
В случае поликристаллического материала твердость находится в пределах 31 – 34 ГПа.
542
Карбид кремния не разлагается минеральными кислотами (кроме концентрированных HF, HNO3 и Н3РО4) и растворами щелочей. Разлагается расплавами карбонатов, сульфатов, гидроксидов щелочных металлов и множественных оксидов. Реагирует с СО и Сl выше 1200 °С, с F2 – выше 500 °С, парами воды – выше 1300 °С, N2
– выше 1400 °С. Окисляется О2 выше 1000 °С.
Карбид кремния получают при взаимодействии SiO2 с углем при 1600 – 2800 °С (по способу Ачесона – с добавкой NaCl). Возможно получение из составляющих элементов при температуре выше 1150 °С, а так же пиролизом газообразных соединений Si (например CH3SiCl3). Монокристаллы получают направленной кристаллизацией из металлических расплавов.
Получение карбидных слоев. При производстве МТ покрытия карбида кремния наносят методом пиролиза метилтрихлорсилана CH3SiCl3, который пропускают через нагретый до высоких температур псевдоожиженный слой топливных МС с предварительно нанесенными на них пироуглеродными слоями. Качество покрытий SiC и их структура определяются главным образом степенью разбавления пиролизного газа, температурой и скоростью осаждения.
Использование чистого метилтрихлорсилана затрудняет получение качественных SiС-покрытий и регулирование их толщины. Поэтому его пары разбавляют с помощью газа-носителя, что дает возможность получать эффективное псевдоожижение и, следовательно, однородный слой SiC, наносимый с допустимой скоростью осаждения. В качестве газа-носителя обычно используют водород, который также служит восстановителем и увеличивает выход карбида кремния; концентрация в нем метилтрихлорсилана составляет около 4 об. %.
При использовании аргоно-водородной смеси в качестве газаносителя плотность и химический состав слоя SiС не связаны с концентрацией в газе метилтрихлорсилана, но зависят от температуры осаждения и отношения аргон/водород, так как эти характеристики определяют скорость, с которой атомы углерода и кремния образуют покрытия из карбида кремния на поверхности частиц. При температурах осаждения выше 1500 °С плотность покрытия не изменяется и имеет значение, близкое к теоретическому (3,21 г/см3); при возрастании концентрации аргона достигается критическое значение от-
543
ношения аргон/водород, выше которого плотность снижается. Это отношение уменьшается при повышении температуры. Соответственно, при низких температурах осаждения плотность SiC увеличивается с концентрацией аргона вплоть до достижения теоретического значения. Поэтому, регулируя отношение аргон/водород, можно осаждать пиролитический карбид кремния теоретической плотности в интервале температур 1200 ÷ 1700 °C.
Оптимальными свойствами обладают слои SiC с плотностью не менее 3,2 г/см3 , массовой долей свободного кремния не более 0,3 % и размером кристаллитов не менее 100 нм.
Структура карбидных покрытий. Рентгенографическое исследо-
вание слоев SiC показало, что основной фазой, которая в них присутствует, является кубический β-карбид кремния; содержание неупорядоченного α-карбида кремния обычно составляет менее 1 %.
Покрытия SiC состоят из радиально расположенных зерен, плоскости которых (111) ориентированы параллельно подложке. Их замеры и распределение изменяются при изменении параметров осаждения. Зерна содержат каналы, а на границах присутствуют микропоры, микротрещины и свободный кремний. Важную роль в удержании слоем SiC твердых ПД играет гомогенность его структуры. Количественно она характеризуется так называемым фактором негомогенности, который зависит от температуры и скорости осаждения. Слой SiC, полученный пиролизом метилихлорсилана при 1500 °С со скоростью 0,2 мкм/мин, состоит из крупных зерен, является изотропным, имеет стехиометрический став и незначительную пористость (плотность ~99 % ТП). Фактор негомогенности такого материала минимальный. Для пиролитического SiC, осажденного при более высокой температуре, характерны более высокие значения фактора негомогенности, образование пор по границам зерен и внутренних каналов, а также сличение размеров зерен. При более низких температурах осаждения (1300 ÷ 1400 °С) карбид кремния имеет слоистую структуру и невысокую плотность (~3,05 г/cм3); его фактор негомогенности возрастает, причем осаждается мелкокристаллический SiС, границы зерен которого содержат много свободного кремния (до 17 мас. %). Такой слой карбида кремния более проницаем для продуктов деления. Морфология по-
544
верхности SiC-осадка и ее изменение зависит от условий осаждения. Поверхность SiC-слоя может быть струйной, зернистой, или гладкой. Когда она является грубой струйной, первичные полосы искривляются. Эти особенности взаимосвязаны и топография поверхности отражает природу лежащих под ней первичных полос. При уменьшении скорости осаждения поверхность изменяется сначала от струйной к зернистой, а затем – к гладкой.
Свойства и радиационная стойкость покрытия SiC. Средний коэффициент линейного расширения SiC в интервале температур 20 – 1000 °С равен 4,9∙10-6 К-1 и практически изменяется при облучении. Коэффициент теплопроводности пиролитического SiC значительно выше, чем РуС, и при комнатной температуре составляет 30 ÷ 70 Вт/м∙К; он уменьшается с повышением температуры (20 ÷ 130 Вт/м∙К при 1200 °С), так и при облучении (~21 Вт/м∙К после облучения флюенсом быстрых нейтронов 2,7 ÷ 7,7∙1021 нейтр./см2
при 1100 °С).
При облучении быстрыми нейтронами в SiC образуются дефекты внедрения, вакансии и дислокационные петли Франка. Следствием этого процесса являются некоторое увеличение линейных размеров и сравнительно слабое изотропное объемное распухание. При температурах ниже 1000 °С распухание начинается при флюенсе быстрых нейтронов ~5∙1021 нейтр./см2. С увеличением флюенса распухание достигает максимума, после чего начинается усадка SiC даже в том случае, если температура облучения возрастает.
Отжиг облученного SiC при температуре облучения приводит к восстановлению исходных линейных размеров. Абсолютное значение скорости радиационного роста значительно меньше, чем РуС, и при 1000 °С составляет ~0,1 % на 1021 нейтр./см2 (для PyC оно находится в пределах от –2,0 до 3,0 % на 1021 нейтр./см2). Скорость распухания при 1250 °С выше, чем при 1500 °С, что, по-видимому, связано с процессе перемещения и укрупнения пор, который идет активнее при более высоких температурах.
Механические свойства покрытий SiC весьма чувствительны к температуре осаждения и несовершенствам поверхности, температуре облучения и флюенсу быстрых нейтронов. Прочностные свойства SiC, осажденного при температуре ниже 1400 °С, приблизительно в полтора раза ниже, чем SiС осажденного при температу-
545
рах выше 1500 °С. Предел прочности при изгибе пластин из карбида кремния при комнатной температуре составляет ~840 МПа, а модуль Юнга ~420 ГПа. Облучение флюенсом быстрых нейтронов ~12,2∙1021 нейтр./см2 в интервале температур 950 ÷ 1040 °С снижает предел прочности при изгибе до ~760 МПа, в то время как значение модуля Юнга практически не изменяется. Среднее напряжение разрушения покрытия из карбида кремния принимается равным ~100 МПа при разрушении одного МТ из тысячи при напряжении менее 20 МПа.
Скорость ползучести SiС при облучении незначительна, и ею в расчетах можно пренебречь.
Для улучшения защитных свойств ПИУК-покрытия в настоящее время ведутся работы по замене слоев из карбида кремния слоями из карбидов других металлов, имеющих малое сечение захвата нейтронов и лишенных недостатков, присущих карбиду кремния. Положительные результаты были получены, например, при нанесении из газовой фазы покрытий в виде карбидов циркония и ниобия в аппаратах кипящего слоя.
24.7.5. Выход продуктов деления из топлива ВТГР
Важнейшей задачей при конструировании, производстве и эксплуатации топлива ВТГР (МТ, твэлов и ТВС) является предотвращение поступления из него ПД в теплоноситель. Однако полностью решить эту задачу не представляется возможным, и по целому ряду причин, которые будут рассмотрены ниже, часть ПД выходит из топлива. Количественно этот процесс описывается равновесной и относительной утечками. Первая из них характеризует выход ПД с малыми периодами полураспада, таких, как изотопы Kr и Хе (за исключением 85Кr), йода, теллура и др., и выражается соотношением
F=R/B. (24.141)
Здесь R – скорость утечки изотопа ПД, а B Y Ф(ε)σf ρf dε – ско-
0
рость образования изотопа ПД, где Y – выход данного изотопа на деление, σf – сечение деления, ρf – плотность делящегося материала, Φ(ε) – поток нейтронов с энергией ε.
546
Многие нуклиды, такие, например, как 84Sr,90Sr и 137Сs, имеют большой период полураспада, и их выход из топлива со временем изменяется, вследствие чего в момент времени t он характеризуется относительной утечкой F(t), описываемой уравнением:
|
t |
λ(t ) |
|
|
|
|
R( )e |
d |
|
||
F(t) |
0 |
|
|
, |
(24.142) |
|
M(t) |
|
|||
|
|
|
|
|
где R(τ) – скорость утечки нуклида ПД, М(t) – его количество в момент времени t, λ – постоянная распада. Отношение R(τ)/B(τ) принято называть относительной скоростью утечки. Утечка ПД из твэлов и ТВС высокотемпературных реакторов не должна быть больше предельно допустимых значений, составляющих для ГПД < (10-5 ÷ 10-6), а для «твердых» ПД < (10-3 ÷ 10-4). Их превышение приводит к аварийной остановке реактора, а связанные с этим затраты могут существенно превышать расходы на изготовление топлива.
Выход ПД в теплоноситель осуществляется за счет их миграции из герметичных и дефектных МТ, а также покрытия МТ, матрицы и компонентов твэлов и ТВС, загрязненных тяжелыми металлами. Наибольшей вероятностью утечки из топлива ВТГР обладают ПД, которые имеют достаточный выход при делении ядер урана, большой период полураспада и высокую диффузионную подвижность в материалах МТ матрицы, твэлов и ТВС, связанную их химическим состоянием.
Выход осколочных элементов при делении ядер урана и их свойства. Сведения о выходе ПД при делении ядер урана и некоторых их свойствах, влияющих на диффузионную подвижность (температура плавления, испарения и летучесть, оцененная по трехбальной шкале), приведены в табл. 24.51. Большая часть этих ПД удерживается в МТ, графитовой матрице, а также компонентах твэлов и ТВС, вследствие чего в контуре охлаждения ВТГР обнаружено сравнительно небольшое количество осколочных изотопов.
Это изотопы ПД (Xе и Кr), а также некоторые нуклиды твердых
ПД, такие, как 89Sr, 90Sr, 95Zr, 95Nb , 103,106Ru , 110mАg, 131I, 125Sb, 134Cs,
137Cs, 140Ba, 144Ce и 106Eu. Из табл. 24.51 видно, что большинство нуклидов твердых ПД относится к сильноили среднелетучим ПД,
хотя среди них имеются и слаболетучие, например 95Zr, 95Nb,
103,106Ru и 144Ce.
547
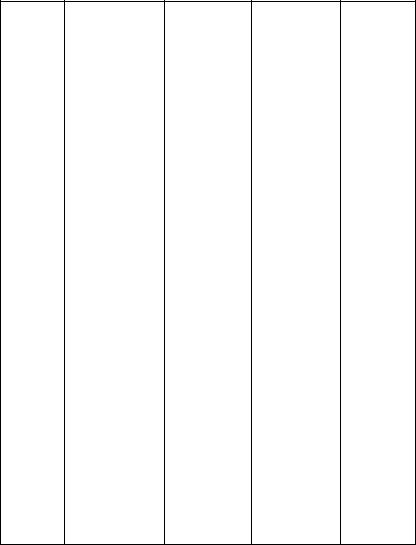
Таблица 24.51
Выход и некоторые другие свойства продуктов деления урана
Продукт |
Выход продукта |
Температура |
Температура |
Степень |
|
деления %, |
|||||
деления |
плавления, К |
кипения, К |
летучести* |
||
|
Σy=200 |
|
|
|
|
Ge |
0,0024 |
1210 |
3100 |
2 |
|
As |
0,0008 |
1081 |
866 |
1 |
|
Se |
0,485 |
494 |
958 |
1 |
|
Br |
0,14 |
266 |
331,4 |
1 |
|
Kr |
3,9 |
- |
119,75 |
1 |
|
Rb |
3,5 |
313 |
974 |
1 |
|
Sr |
9,4 |
1041 |
1640 |
2 |
|
Y |
4,8 |
1801 |
(3500) |
3 |
|
Zr |
31,0 |
2133 |
4650 |
3 |
|
Nb |
0 |
2750 |
5200 |
3 |
|
Mo |
24,5 |
2890 |
5100 |
3 |
|
Tc |
6,1 |
2473 |
4900 |
3 |
|
Ru |
10,9 |
2523 |
(4000) |
3 |
|
Rh |
3,0 |
2236 |
(4000) |
3 |
|
Rd |
1,55 |
1825 |
3400 |
3 |
|
Ag |
0,03 |
1234 |
2450 |
2 |
|
Cd |
0,067 |
594 |
1038 |
1 |
|
In |
0,010 |
430 |
2320 |
2 |
|
Sn |
0,085 |
505 |
2960 |
3 |
|
Sb |
0,058 |
904 |
1910 |
2 |
|
Te |
2,42 |
723 |
1260 |
1 |
|
I |
1,03 |
387 |
456 |
1 |
|
Xe |
21,8 |
- |
165,04 |
1 |
|
Cs |
19,2 |
302 |
958 |
1 |
|
Ba |
5,7 |
1002 |
1910 |
2 |
|
La |
6,6 |
1193 |
3640 |
3 |
|
Ce |
12,4 |
1071 |
3200 |
3 |
|
Pr |
6,0 |
1204 |
3290 |
3 |
|
Nd |
21,1 |
1289 |
3360 |
3 |
|
Pm |
2,4 |
1204 |
(3000) |
3 |
|
Sm |
1,93 |
1345 |
(1860) |
2 |
|
Eu |
0,20 |
1090 |
(1700) |
2 |
|
Gd |
0,022 |
1585 |
(3000) |
3 |
|
Tb |
0,0011 |
1630 |
(2800) |
3 |
|
Dy |
0,00008 |
1682 |
(2600) |
3 |
_______
* Степень летучести: 1 – температура плавления < 1500 К; 2 – промежуточная между 2 и 3; 3 – давление пара элемента < 10-2 Па при 1500 К.
548
Присутствие последних обусловлено, по-видимому, недостаточной удерживающей способностью компонентов топлива ВТГР, высоким выходом этих нуклидов при делении ядер урана (за исключением Nb) и их большим периодом полураспада.
ГПД выделяются по мере выгорания топлива достаточно быстро, но они не оказывают существенного влияния на уровень радиоактивного заражения контура охлаждения ВТГР. Утечка твердых ПД происходит более медленно и после значительного выгорания
топлива. Наибольшую радиологическую опасность представляют ГПД Xе, Кr и тритий, а также твердые ПД 134Cs, 137Cs, 110mАg и 90Sr,
некоторые ядерно-физические характеристики которых представлены в табл. 24.52. Они имеют большой период полураспада и высокую диффузионную подвижность в материалах МТ, твэлов и ТВС, которая возрастает в следующем порядке: Sr, Cs и Ag.
Среди этих ПД особо следует отметить нуклид серебра 110mАg активность которого в пять раз выше активности 131I, 134Cs и 137Cs. Нуклиды 134Cs и 109Ag образуются по реакции (n,γ) на стабильных ядрах 133Cs и 109Ag соответственно. Однако 133Cs является дочерним изобаром высокоподвижного газообразного 137Xe с большим периодом полураспада (T1/2 = 129 ч), а 137Cs имеет своим предшественником короткоживущий 137Хе (T1/2 = 3,8 мин), вследствие чего
утечка 134Cs из МТ, твэлов и ТВС существенно отличается от утечки 137Cs. Что же касается 109Ag, то его образование во многом опре-
деляется используемым топливным циклом. Выход 109Ag на одно деление ядра урана составляет 0,03 %, тогда как на одно деление ядра плутония он равен ~1,2 %. Поэтому 109mAg особенно опасен при использовании уран-плутониевого топлива.
|
|
|
|
Таблица 24.52 |
||
Ядерно-физические характеристики некоторых твердых ПД |
||||||
|
|
|
|
|
|
|
Нуклид |
Период по- |
Реакция |
Долгоживущий |
|
Распад |
|
лураспада |
образования |
предшественник |
|
|
||
|
|
|
|
|||
134Cr |
2,062 года |
(n,γ) |
133Cs (стабильный) |
|
β–, γ |
|
137Cr |
30,174 года |
Деление |
- |
|
β–, γ |
|
110mAg |
250,4 сут. |
(n,γ) |
109Ag (стабильный) |
|
β–, γ |
|
549
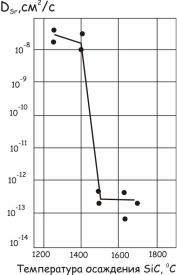
Диффузионная подвижность ПД в слоях PyC- и SiC-покрытий весьма чувствительна к их структуре и может изменяться в широких пределах в зависимости от технологии получения. Так, коэффициент диффузии Sr в PyC, осажденном из метана, в 10 раз ниже, чем в PyC, полученном из пропилена, а в SiC, полученном выше 1500 °С, приблизительно на пять порядков меньше, чем в SiC, полученном ниже 1500 °С, что обусловлено присутствием свободного кремния в низкотемпературном SiC-слое и неравновесным состоянием его структуры (рис. 24.335). Поэтому при описании диффузионной подвижности ПД в слоях покрыт МТ необходимо давать точные характеристики этих слоев. Обычно это не делается, что
сильно затрудняет сравнение и интерпретацию приводимых данных. В этой связи миграцию ПД нельзя объяснить простой диффузией, вследствие чего коэффициенты диффузии принято считать «эффективными».
На диффузию твердых ПД в матричном графите, а также графитовых компонентах твэлов и ТВС влияет тип графита, концентрация твердых ПД, температура облучения быстрыми нейтронами, давление гелия и окисление графита. Удерживающая способность. графита определяется, в свою очередь, диффузией твердых ПД в объеме графита, а также их сорбцией на поверхности, включая поверхность пор.
Химическое состояние продуктов деления. Способность топ-
лива удерживать ПД во многом определяется характером их физи- ко-химического взаимодействия с компонентами топлива или с ураном (торием) и между собой. Так, ПД растворяющиеся в топливе или образующие самостоятельные тугоплавкие оксидные или
550