
Калин Физическое материаловедение Том 6 Част 2 2008
.pdf
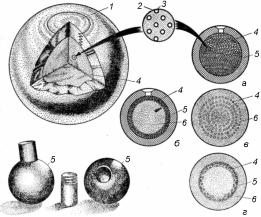
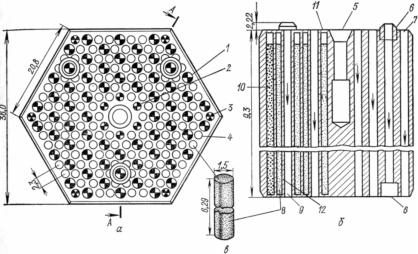
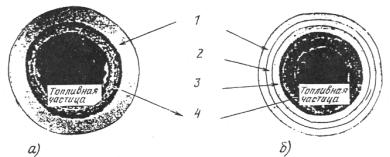
Рис. 24.316. Типы микротвэлов с пироуглеродным покрытием (а)
ис пироуглеродо-карбидным покрытием (б):
1– внешний плотный слой изотропного пироуглерода; 2 – барьерный слой из карбида кремния; 3 – внутренний плотный слой изотропного пироуглерода;
4 – буферный слой пористого пироуглерода
Для снижения утечки ПД были разработаны более сложные четырехслойные ПИУК-покрытия, содержащие наряду со слоями РyС промежуточный карбидный слой, например из карбида кремния SiС (рис. 24.316, б). Температура в центре МТ с таким покрытием не должна превышать 1500 °С, так как при более высоких температурах его удерживающие свойства оказываются неудовлетворительными.
В покрытиях первого типа пироуглеродный слой, непосредственно прилегающий к топливной МС и называемый буферный (слой PyC1), имеет низкую плотность ~0,9÷1,22 г/см3 (теоретическая плотность графита 2,27 г/см3) и аморфную структуру, которая практически не повреждается осколками деления. Функции буферного слоя весьма многообразны. Он воспринимает без передачи последующим слоям покрытия объемные изменения МС, обусловленные ее термическим расширением и распуханием. Буферный слой также защищает вышележащий слой плотного пироуглерода от воздействия осколков деления. В процессе выгорания топлива в порах буферного слоя происходит накопление вышедших из МС продуктов деления, что уменьшает давление газообразных и легколетучих ПД на покрытия МТ, снижая тем самым напряжения в его слоях.
510