
Калин Физическое материаловедение Том 6 Част 2 2008
.pdf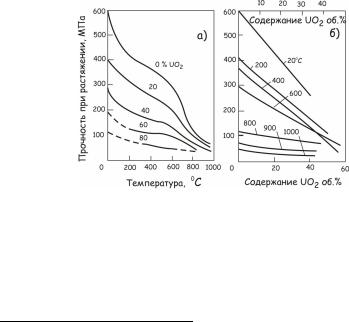
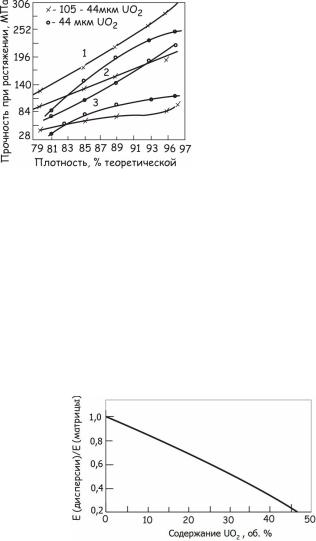
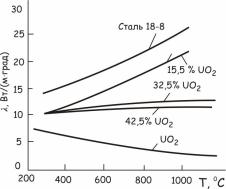
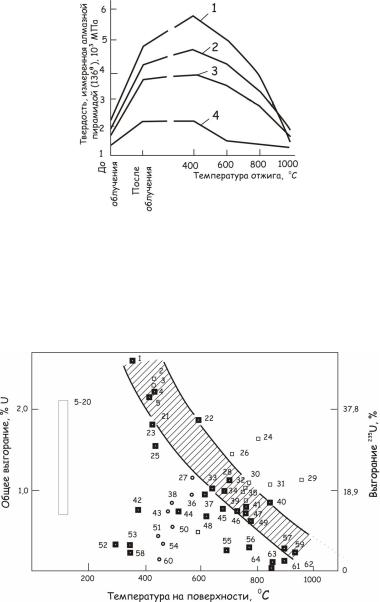
Рис. 24.298. Зависимость влияния облучения и нагрева после облучения на твердость композиции UO2–коррозионно-стойкая сталь от размера частиц:
1 – 7–11 мкм; 2 – 31–44 мкм; 3 – 88–105 мкм; 4 – оболочка
Влияние температуры и выгорания на радиационную стойкость дисперсных твэлов с сердечником 28–30 % UO2–коррозионно- стойкая сталь показано рис. 24.299, где широкая заштрихованная полоса разделяет области их стабильности и нестабильности.
Рис. 24.299. Радиационные характеристики твэлов с дисперсной композицией 18–30 мас.% UО2–коррозионно-стойкая сталь
484
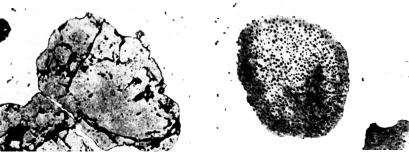
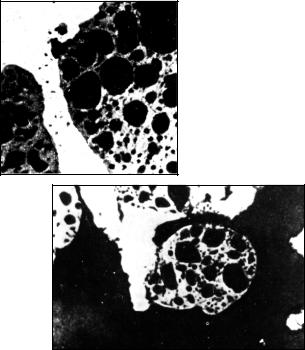
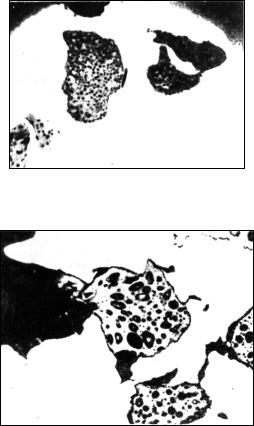
Рис. 24.304. Частицы UO2, облученные до выгорания 9 %. В процессе выгорания сохранялось постоянное сдерживающее влияние матрицы ( 500).
Шлиф не травлен
Рис. 24.305. Пластическое течение частицы UO2 по направлению к разорванной поверхности ( 250). Шлиф травлен
Отжиг облученных твэлов с сердечником UО2–коррозионно- стойкая сталь при 900 °С в течение 200 ч приводит возникновению вокруг частиц UO2 многочисленных трещин (рис. 24.306). Это обусловлено, по-видимому, тем, что отжиг создает значительное давление ГПД в местах их скопления (твэлы облучались, очевидно, при температурах ниже 900 °С), вызывающее растрескивание матрицы из стали.
Эксперименты по облучению твэлов с сердечниками из композиции UO2–коррозионно-стойкая сталь, содержащих специально
487
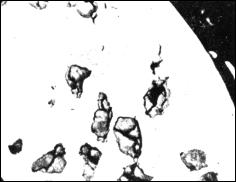
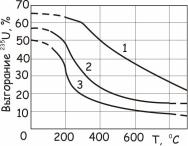
|
|
|
|
|
Таблица 24.47 |
|
Характеристики реакторов с дисперсной топливной композицией UO2–сталь |
||||
|
|
|
|
|
|
|
Параметры реактора |
SM-1, США |
PATHFINDER, США |
WBWR, США |
SPERT-3, США |
|
|
|
|
|
|
|
Назначение, тепловая |
Электростанция, |
Электростанция, |
Исследовательский, |
Исследовательский, |
|
мощность, Вт |
4·107 |
2·108 |
кипящий |
6·106 |
|
Максимальная плоность |
7,0·1013 (т.) |
В испарителе |
7,0·1013 (т.) |
7,0·1013 (т.) |
|
потока, нейтр./см2·с) |
3,8·1013 (т.), 1,1·1014 (б.) |
6,4·1014 (б.) |
||
|
|
|
|||
|
Тип твэла, его размеры, мм |
Прямые пластины, |
Кольцевые, |
Прямые пластины, |
Прямые пластины, |
|
|
559 63,5 0,5 |
l=1830 |
940 75 0,76 |
940 35,6 0,76 |
490 |
Число твэлов в сборке |
18 |
- |
38 |
38 |
|
|
|
|
|
|
|
Материал оболочки |
Сталь 304 |
Сталь 316 |
Сталь 304 |
Кор.-стойкая сталь |
|
|
|
|
|
|
|
Состав топлива (масс. |
-0,12% |
UO2 –кор.-стойкая |
UO2–кор.-стойкая |
UO2–кор.-стойкая |
|
содержание) % |
B4C – кор.-стойкая |
сталь |
сталь |
сталь |
|
Обогащение |
93 |
93 |
93 |
93 |
|
235U, % |
||||
|
|
|
|
|
|
|
Максимальн. темпер. |
230 |
440 |
285 |
340 |
|
теплоносителя, °C |
||||
|
|
|
|
|
|
|
|
|
|
|
|
|
Максимальный тепловой |
6,8·105 |
2,5·106 |
6,5·105 |
6,5·105 |
|
поток, Вт/м2 |
|
|||
|
|
|
|
|
|
|
Выгорание 235U, % |
33 |
20 |
60 |
Незначительное |
|
|
|
|
|
|