
Калин Физическое материаловедение Том 6 Част 2 2008
.pdf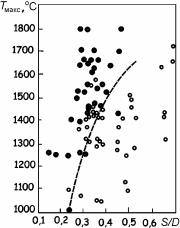
Рис. 24.317. Влияние максимальной температуры облучения и относительной толщины покрытия на стойкость микротвэлов с двух-и трехслойным пиророугперодным покрытием:
○– разрушений нет; ○ – разрушилось ~1 % МТ; ● – разрушилось более 1 % МT;
-– – – граница 1%-ного разрушения МТ при средней температуре облучений
Таким образом, при повышении температуры топлива требуется либо увеличение толщины покрытия, либо уменьшение диаметра МС. При постоянной относительной толщине покрытия для увеличения глубины выгорания топлива необходимо снижать температуру топлива (рис. 24.318).
В пористом буферном слое в соответствии с его функциональным назначением происходит торможение и полная остановка ПД в виде ядер отдачи, образующихся при делении ядер урана как в объеме, так и на поверхности топливной МС. Поэтому толщина этого слоя должна быть заведомо больше длины пробега осколка деления, которая, в свою очередь, зависит от его плотности (для буферного слоя РуС с пористотью 50 % длина пробега осколка деления составляет ~23 мкм). Влияние плотности на минимальную толщину буферного слоя, которая равна длине пробега осколка деления, показано в виде кривой на рис. 24.319.
На рис. 24.319 также представлена и кривая, построенная для буферного слоя с толщиной, составляющей 150 % от минимального значения (наиболее типичная толщина буферного слоя). Эти
513
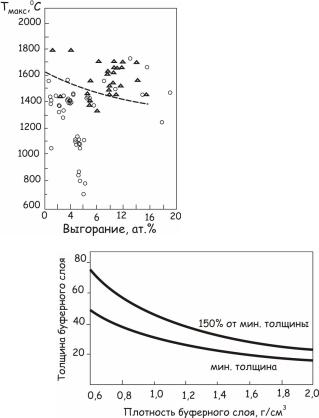
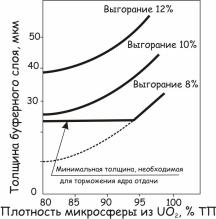
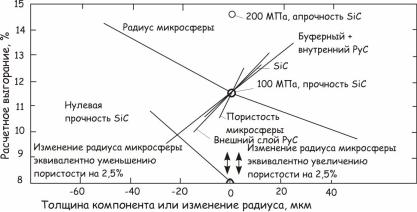